
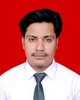
- Open Access
- Authors : Harshit Bansal , Abhiraj Kumar Gupta , Dr. Ashok Madan
- Paper ID : IJERTV10IS100068
- Volume & Issue : Volume 10, Issue 10 (October 2021)
- Published (First Online): 21-10-2021
- ISSN (Online) : 2278-0181
- Publisher Name : IJERT
- License:
This work is licensed under a Creative Commons Attribution 4.0 International License
Wire ARC Additive Manufacturing Process for Higher Deposition Rate and Mechanical Strength
Harshit Bansal1, Abhiraj Kumar Gupta1, Dr. Ashok Madan2
1 Research scholar, Department of Mechanical engineering, Delhi Technological University, Delhi, India
2 Professor, Department of Mechanical engineering, Delhi Technological University, Delhi, India
Abstract:- Wire Arc Additive manufacturing also known as WAAM is always been economical and highly efficient technology which is very suited for producing large and complex shaped metallic components using the process of 3D printing. In past few years, it is widely studied in various fields such as automotive, marine as well as aerospace industries. As WAAM has advantage of higher metal deposition rate, lesser machining cost, higher Buy-to-fly ratio and very lesser lead time in comparison to any other powder Additive Manufacturing processes. WAAM had always been noticed topic by many of the industrial engineers and researchers. If we compare WAAM process over any other traditional manufacturing methods, considering the complex shapes and high buy to fly ratio (BTF), WAAM is always proved to be best of them. Therefore, having an advantage of comparatively lesser manufacturing cost, better quality and a higher efficiency WAAM became highly used technique for fabricating a component with a much higher metal deposition rate and least material wastage/least scrap. This paper provides a detailed overview of 3D printing of metallic object by inheriting WAAM technique as manufacturing method. At first, the review introduces metal wire and WAAM technique of 3D printing, followed by WAAM systems that are being used to manufacture 3D component, and analyzing which aims to study metal deposition rate and mechanical properties.
Key Words: Direct Energy Deposition(DED); Buy To Fly ratio(BTF); Additive Manufacturing; WAAM ; High Deposition Rate; CMT; GTAW; Plasma Arc Welding(PAW); LMD
-
INTRODUCTION
Wire Arc Additive Manufacturing (WAAM) is a process of manufacturing which combines continuous metal feeding in the form of wire and arc-welding technique for 3-D printing. Although this idea is not new, in last few decades several researchers were working over the use of various arc welding techniques on layer by layer deposition of weld bead to production of 3D parts. Therefore, welding techniques such as Cold Metal Transfer (CMT), Gas Metal Arc Welding(GMAW), Gas tungsten arc welding (GTAW) or Plasma arc welding (PAW) have been implemented for Additive manufacturing of various metal/alloys such as steel, aluminium, nickel superalloys and Titanium alloys.
WAAM on the other hand adds to typical Additive manufacturing processes with further more advantages such as lesser welding equipments cost, easily available standard metal wires, virtual and non-limited part sizes and a higher deposition-rates. In this way, for steels Selective Laser Melting (SLM) attains metal deposition rates of 0.1 kg/hr welding that marked its applicability limited. In this work three types of welding processes are used which are Plasma
whereas Laser Metal Deposition (LMD) was being able to deposition of 1 Kg/hr, but WAAM technology has achieved a higher deposition rate reaching up to 5-6 Kg/hr.
Then again, WAAM showed a few disadvantages when contrasting it with SLM or LMD. In WAAM heat input is higher, that prompts to high residual stresses and bending/distortion, hence fabricated part accuracy and roughness is lower than that of any other Additive Manufacturing advancements and there is always a need of machining step. In addition, the low accuracy causes difficulty in redesigning by the use of geometry optimization algorithms.
Therefore, WAAM technique is adequate for manufacturing of large size parts which are manufactured by high cost materials and requires a high amount of machining.
It was proven to be nothing that most of the previously done work were been completed over single bead multilayer arrangement with or without torch waving or lateral oscillation. Single bead layer was able to produce a wall thickness of about 2 mm to 10mm.
For manufacturing walls with a more thickness then this requires overlapping of multiple weld beads adjoining each other. In such kind of overlapping, the center distance between the joining weld beads have a great effect on the surface finish and layer flatness. Previously done researches over multi bead overlapping showed a result that it is not possible to get an ideal smooth any flat overlapping surface. Various researchers now discovered a new multi bead overlapping model that determines an optimal center distance for ensuring a stable overlapped bead. In WAAM applications, non-uniform deposited beads can cause cumulative errors along direction of bead deposition that can cause a unstable process. Along with this, this issue can be solved by real time monitoring by controlling welding current and arc length, that can result in a better surface quality and lesser material wastage. Up to now, GTAW and PAW arc welding techniques were described as more reliable and most suitable processes for WAAM with much lesser problems like excessive heating, porosity and distortion in GMAWtechnique. But in both of the techniques the metal wire was not fed coaxially which thereafter resulted in process variations on altering the direction of weld deposition and sensitivity to arc length. And the fact is that many of the welding system implementing robots requires rotary axis for the positioning of nozzle and matching it with the position of
welding (PAW), Cold Metal Transfer (CMT), Gas Tungsten Arc Welding (GTAW). In this PAW is the conventional
welding technique whereas CMT and Top-TIG are advancement of GMAW and GTAW welding techniques respectively. The 1st reduces the heat input and variations in process by traditional GMAW technique and the 2nd is the GTAW (coaxial) that improves all over metal deposition
rate of the WAAM process. The outcome of the work not only includes capabilities of all the implemented processes to generate high quality parts. Moreover, mechanical properties were also studied and analyzed for the AISI 316L stainless steel.
-
LITERATURE REVIEW
S.No.
TITLE
Author & Year
Publication
Findings
1.
A review on wire and arc additive manufacturing of titanium alloy
Zidong Lin , Kaijie Song ,
Xinghua Yu (2021)
ELSEVIER
This paper gives knowledge of 3D metallic printing of titanium alloy using WAAM process for metal deposition [1].
2.
A multi-bead overlapping model for robotic wire and arc additive manufacturing (WAAM)
Donghong Ding,Zengxi Pan, Dominic Cuiuri,Huijun Li (2015)
ELSEVIER
This paper shows a vastly improved guess to the exploratory estimations when compared with flatl top overlapping model (FOM).This is basic in measure intending to accomplish better geometry, accuracy and material effectiveness in additive manufacturing [2].
3.
Preliminary development of a Wire and Arc Additive Manufacturing Engineering
J.L. Prado-Cerqueiraa, J.L.
Diéguezb, A.M. Camachoa (2017)
ELSEVIER
The primary target of this work is to show the principal encounters in the advancement of a practical metal added substance producing framework based on gas metal arc welding [3].
4.
Additie manufacturing using WAAM with AA5183 wire [7]
Erikssonb, O.M. Akselsen (2018)
ELSEVIER
The current review tends to wire arc additive manufacturing of AA5183 aluminum alloy utilizing regular gas metal arc welding deposition on 20mm thick AA6082-T6 plate as support material [4].
5.
A review of wire arc additive manufacturing and advances in wire arc additive manufacturing of aluminium
K .S DEREKAR (2018)
ELSEVIER
This paper is an audit of WAAM technology including a brief of WAAM history, status, benefits, and limitations of the WAAM field. A focus is given including the endeavors coordinated towards the decrease of porosity, malleable properties, microstructural examinations, and other important headway in the field of WAAM of aluminium [5].
6.
Effect of heat input on microstructure and mechanical properties of Al-Mg alloys fabricated by WAAM
Chuanchu Su, Xizhang Chen, Chuang Gao,
Yangfan Wang (2019)
ELSEVIER
From this paper, it is obvious that parts produced by WAAM-CMT have a preferable exhibition over the 5356 regular casting alloys [6].
7.
Development of low-cost production process for prototype components based on Wire and Arc Additive Manufacturing (WAAM)
Nataliia charnabol, Bert Lauwers, Patrick Van rayment (2020)
ELSEVIER
This paper centers around the various strides to be taken to adapt existing GMAW innovation into a moderate and effective WAAM innovation [7].
8.
Investigating the generation process of molten droplets and arc plasma in the confined space during compulsively constricted WAAM
Meng Guo, Chuanbao Jia, Jihui Zhou, Wenqiang Liu,
Chuansong Wu (2020)
ELSEVIER
The paper uncovered that arc behaviors and beads transfer were truly unstable at low-level electrical boundaries with the features that the beads transfer measurements were huge (1.85.3 mm), the beads transfer frequencies were low (223 Hz) [8].
-
Horgara, H. Fostervollb,
-
Nyhusb, X. Renb, M.
9.
Thermal management in WAAM through the CMT Advanced process and an active cooling technique.
Fernando Matos Scottia, Felipe Ribeiro Teixeiraa, Leandro João da Silvaa,Douglas Bezerra de Araújoa, Ruham Pablo Reisa,*, Américo Scotti (2020)
ELSEVIER
This paper gathered that the chance of influencing the thermal cycles and geometries of the resultant preforms with two autonomous thermal administration instruments grows the windows for discovering ideal affidavit boundaries in WAAM [9].
10.
Wire Arc Additive Manufacturing (WAAM) process of nickel based superalloys A review
T. Sathish , B. Stalin (2020)
ELSEVIER
This paper infers that the broad utilization of WAAM actually shows many difficulties, and these may should be engaged and settled in explicit manners for various materials to create a functional framework in an acceptable time span [10].
11.
Wire arc additive manufacturing (WAAM): A new process to shape engineering materials
Sudhanshu Ranjan Singh ,
Pradeep Khanna (2021)
ELSEVIER
This paper expects to portray the different stagewise advancements and capabilities of WAAM tech, with an outline on the materials that can be worked upon and some knowledge on the future possibilities of the technology [11].
12.
Ultracold-Wire and arc additive manufacturing (UC-WAAM)
Tiago A. Rodrigues *, Valdemar R. Duarte , R.M. Miranda , Telmo G. Santos
, J.P. Oliveira (2021)
ELSEVIER
By eliminating the electric flow through the substrate and separating the electric arc from the liquid pool, this new WAAM variation can diminish the process temperatures and increment in cooling rates, without compromising the trustworthiness or deposition pace of the as-fabricated parts [12].
13.
A review on process planning strategies and challenges of WAAM
Sagar Singh, Satish kumar Sharma , Dinesh W.
Rathod (2021)
ELSEVIER
The nuts and bolts and essentials of WAAM methods, different significant stages and key interaction getting ready for WAAM have been explained. Moreover, the difficulties and cutting- edge developments in this conspicuous field of WAAM are engaged for the better comprehension of processes and technologies [13].
14.
Metal transfer modes for Wire Arc Additive Manufacturing Al-Mg alloys: Influence of heat input in microstructure and porosity
Aldalur a,*, A. Su´arez a,b,
F. Veiga a (2021)
ELSEVIER
In this paper, aluminum alloy 5356 is analyzed in the Gas Metal Arc Welding (GMAW)- based WAAM innovative cycle. From among the different suggested working methods of various makers, three working modes for aluminum alloy are analyzed: pulsed GMAW mode, Cold arc mode and pulsed AC mode [14].
15.
Investigation of the WAAM processes features based on an indirect arc between two non- consumable electrodes
Jihui Zhou, Chuanbao Jia
*, Meng Guo, Maoai Chen, Jinqiang Gao, Chuansong Wu
(2021)
ELSEVIER
This paper confirmed that the solid burning arc kept continuously melting the steel cord. Because there is no modern-day flowing thru the droplets and molten pool, the crucial manner function of low warmth input became revealed [15].
16.
Hot forging wire and arc additive manufacturing (HF-WAAM)
Valdemar R. Duartea,*, Tiago A. Rodriguesa, N. Schellb, R.M. Mirandaa,
J.P. Oliveiraa, Telmo G.
Santosa (2020)
ELSEVIER
The paper showed that this new version refines the solidification microstructure and reduce texture consequences, as decided via high power synchrotron X-ray diffraction experiments, without interrupting the additive production procedure [16].
17.
Recent developments and challenges associated with wire arc
S. Srivatsav, V. Jayakumar,
M. Sathishkumar
ELSEVIER
This paper overviews the imminent studies and traits on WAAM
-
Dhinakaran , J. Ajith ,
-
Fathima Yasin Fahmidha , T. Jagadeesha ,
-
additive manufacturing of Al alloy: A review
(2021)
techniques and frequently used materials for the equal. Common errors which arise at some stage in WAAM were mentioned in this paper, together with the advantages of WAAM. Alloys of aluminium play a key function in the marine, aerospace and car industries [17].
18.
Oxidation in wire arc additive manufacturing of aluminium alloys
Tobias Hauser a,d,*, Raven
T. Reisch b,d, Philipp P.
Breese c,d, Yogesh Nalam d, Kaivalya S. Joshi d, Katharina Bela d, Tobias Kamps d, Joerg Volpp a, Alexander F.H. Kaplan a (2021)
ELSEVIER
It became located that the arc interacts with the prevailing amorphous oxide layer of the formerly deposited layer and turns it right into a white duplex (crystalline and amorphous) oxide layer. In addition to the analysis of the white surface oxidation, oxidation anomalies, which occur at low protecting from the environment, have been investigated [18].
/td>
19.
Robot Based Wire Arc Additive Manufacturing System with Context- Sensitive Multivariate Monitoring Framework
Raven Reischa,b,*, Tobias Hauserb, Tobias Kampsb,
Alois Knolla (2020)
ELSEVIER
A WAAM machine is divided into 4 elements (welding supply, kinematic structure, control gadget, tracking system) and a evaluation is performed for every. Requirements are described based totally on those evaluations and further desires and a robot primarily based WAAM setup is proposed [19].
20.
Continuous three-dimensional path planning (CTPP) for complex thin parts with wire arc additive manufacturing
Adama Diourt´e a,*, Florian Bugarin a, Cyril Bordreuil b, St´ephane Segonds
(2021)
ELSEVIER
The manufacturing of those elements with CTPP and numerous numerical critiques have proven the reliability of this method and its ability to produce complex new shapes with an excellent geometrical restitution, difficult or not possible to attain these days the use of 2.5D with WAAM generation [20].
21.
Arc Behaviour in Wire Arc Additive Manufacturing Process
Pranjal Shuklaa, Balaram Dasha, Degala Venkata Kirana*, Satish Bukkapatnam
(2020)
ELSEVIER
It changed into determined that the bead width step by step multiplied from the first layer to the fourth layer and remained about the same from 5th to the tenth layer [21].
22.
Weld Bead Modeling and Process Optimization in Hybrid Layered Manufacturing
Suryakumar S, Karunakaran KP, Bernard A, Chandrasekhar U, Raghavender N, Sharma D 2011
ELSEVIER
According to previous researches, the multi globule or bead overlapping models have claimed that it is difficult to accomplish an optimal flat surface with overlapped molten metal beads [22].
-
-
EXPERIMENTAL PROCEDURE
The tests took place in a robotic cell in there was two cartesian machines (Fig. 1). And 3 different power sources were used:
-
Fronius Transplus Synergic 4000-CMT R, power source was connected to Robacta drive torch from Fronius.
-
Top-TIG 220-DC source and patented torch from the Air Liquide.
-
Praxair-EWM TETRIX 400-Synergic Plasma source coupled to Plasmatechnik PWM 350A torch.
Mechanical properties were calculated by tensile test specimens which were produced by electron discharge machining (EDM) having a geometry according to ASTM E8-16-standard (Fig. 2). A specimens was tested for studying mechanical properties of the specimen walls in 2 directions: PL(bead generation direction) and PT(bead vertical overlapping direction) . AISI-316L specimen was tested as the built conditions.
Tensile tests were performed in a model Z100 ZWICK/Roell at ambient temperature by applying a displacement rate of 1.6 mm/min and by the use of an extensometer with gauge length of 25 mm.
Fig -1: WAAM Facilities. Left- IK-4 Lortek (CMT & TopTIG). Centre-TECNALIA (PAW). Right- ADDILAN
(CMT&PAW)
Table 1. Deposition Rates and Shielding gasses
Material
Process
Shielding Gas
Deposition Rate
AISI 316L
CMT PAW
TopTIG
25% CO2 75% Ar
5% H2 95% Ar
100% Ar
1.51 kg/hr
Material
Process
Shielding Gas
Deposition Rate
AISI 316L
CMT PAW
TopTIG
25% CO2 75% Ar
5% H2 95% Ar
100% Ar
1.51 kg/hr
for each material
Fig. -2: Tensile test specimens taken from thick-walled WAAM
samples.
-
CMT process in WAAM
3.1.1 CMT – AISI 316L
Cold metal transfer (CMT) process is a welding method optimized for lowering the heat input into the metal substrate and it is very common to use it in industrial welding of many steel alloys. Moreover, this work only showed the results obtained for deposition rate of 2,5 kg/h and compared them with those which were obtained by all the other processes, CMT process showed very good results of upto 5 kg/h metal deposition rates with AISI 316L.
Though, CMT process produces the bead with a relatively higher aspects ratios (relationship b/w bead height and the width) that could make the process difficult for overlapping and it may cause defects in the component like pores or voids.
Regarding the mechanical properties, results showed that properties were dependent clearly over the test direction (Fig.3). While longitudinal specimens (PL) were close to the least value fixed by the standards, transversal ones (PT) not reaches these limits, which shows lowering yield strength and elongation at break that demonstrates a much more rigid behavior over the traverse direction.
Fig.-3: CMT mechanical tests results for AISI 316L stainless steel
Therefore, for the tensile strength tests 3 types of gases were studied: 100% of Ar (single bead wall), 50% Ar- 50%He and 100% of He. It was worth nothing to increase the percentage suppose an increase of the price of the gas.
Fig.-4: Simple and overlapped beads for different shielding gases.
-
Top-TIG process in WAAM
3.2.1 Top-TIG AISI 316L
4 Top-TIG is a TIG technology that allows the coaxial feeding of wire that increases the metal deposition rate and providing a high quality TIG process. The major limitation of Top-TIG technology is that it has a lower deposition rates when compared with CMT or PAW. The results showed this limit in 1.5 kg/h for AISI 316L and the current equipment (Fig. 8). This limit resulted from a lesser heat input of the process which was unable to melt the wire when the feed rate increased. Moreover, it is very necessary to care of the aspect ratios that could make difficult for horizontal overlapping.
Fig.-5: Beads obtained by Top-TIG on AISI 316L. Left) 1 kg/h.
Centre) 1.5kg/h. Right) 1.6 kg/h.
On the other hand, the mechanical results obtained from Top-TIG were situated over the least required and show high homogeneity in both the directions (Fig. 6).
Fig.-6: Top-TIG mechanical tests results for AISI 316L stainless steel.
-
Plasma Arc Welding process in WAAM
-
PAW AISI 316L
PAW constricts the arc within the pilot arc increasing the energy density so, beads produced by this process were shorter and wider, which means they had a lesser aspect ratio. The fact eases the horizontal overlapping, avoiding pores and voids. Mechanical tests were done on the wall generates at
1.5 kg/h metal deposition rate, moreover 3.5 kg/h values could be reached with suitable quality.
Test results (Fig. 11) shows a high anisotropy between the directions. PL specimens crosses both Yield and Ultimate strength limits, while for the PT it reaches the limit only for the Ultimate strength. In both of the cases, values of Elongation at breaking were below the limited values.
Fig. -7: PAW mechanical tests results for AISI 316L stainless steel
-
-
-
RESULTS
The result section shows the obtained results that we get from the use of the three processes for Additive Manufacturing. Results includes, not only mechanical properties of the specimen, but also the capability of each accomplished process that to be applied in Higher metal Deposition Rate for Additive Manufacturing.
Results are classified by WAAM technologies (CMT, PAW and Top-TIG) and a material (AISI 316L).
4. CONCLUSIONS
The work studies various 3 welding processes (Plasma Arc Welding (PAW), Cold Metal Transfer (CMT) and AirLiquide Top-TIG for the Wire Arc AM in the term of acceptability and the obtained properties. The material that had been studied: an AISI 316L stainless steel.
From the results obtained, following things can be concluded:
-
WAAM technique, without considering welding technology used, achieving a good quality manufactured component with a deposition rates of as high as 5 kg/hr in the AISI 316 L.
-
The obtained results show that, although WAAM technology was able to obtain the mechanical requirements, the only matter that was important is the choice of the correct welding technique depending over the material properties.
-
CMT achieves the highest metal deposition rates in stainless steel but shows anisotropy in the mechanical properties. And hence, it can be
concluded that the CMT process is best for bigger size Stainless steel components with a lesser or medium mechanical requirement.
-
Top-TIG achieves the most suitable properties for the stainless steel and showed a good homogenous behavior without consideration of the directions. Although, its lower energy efficiency didnt allows high deposition rates (1.5 kg/h max.) and made it necessary for the usage of an active shielding gases mixture. Therefore, Top-TIG method can be used for the small or medium size Stainless steel parts that have medium or high mechanical requirements.
-
PAW achieves a intermediate metal deposition rates for the stainless steel (3.5 kg/h) with a better properties in both of the directions. Therefore, PAW method is recommended for the medium or large size Stainless steel parts that have medium or high mechanical requirements.
-
Regardless of the welding methods, parts that were manufactured by WAAM process had shown the anisotropy in the properties that should be taken into account in the duration of design procedure or be-heat or mechanically treated during the 3D- printing.
REFERENCES
-
Zidong Lin, Kaijie Song, Xinghua Yu, A review on Wire and Arc Additive Manufacturing of Titanium alloy.
-
D. Ding, Z. Pan, D. Cuiuri, H. Li, A multi-bead overlapping model for robotic wire and arc additive manufacturing (WAAM), Robot. Comput. Integrated Manuf. 31 (2015) 101110.
-
J.L. Prado-Cerqueiraa, J.L. Diéguezb, A.M. Camachoa, Preliminary development of a Wire and Arc Additive Manufacturing Engineering, Procedia Manufacturing 00 (2017) 895-902.
-
A. Horgar, H. Fostervoll, B. Nyhus, X. Ren, M. Eriksson, O.M. Akselsen, Additive Manufacturing using WAAM with AA5183 wire, J. Mater. Process. Tech. 259 (2018) 6874.
-
K.S. Derekar, A review of wire arc additive manufacturing and advances in wire arc additive manufacturing of aluminium, Mater. Sci. Technol. 34 (2018) 122.
-
Chuanchu Su, Xizhang Chen, Chuang Gao, Yangfan Wang, Effect of heat input on microstructure and mechanical properties of Al-Mg alloys fabricated by WAAM, Applied Surface Science 486 (2019) 431-440.
-
Nataliia charnabol, Bert Lauwers, Patrick Van rayment, Development of low-cost production process for prototype components based on Wire and Arc Additive Manufacturing (WAAM), CIRP 95 (2020) 60-65.
-
Meng Guo, Chuanbao Jia, Jihui Zhou, Wenqiang Liu, Chuansong Wu, Investigating the generation process of molten droplets and arc plasma in the confined space during compulsively constricted WAAM, Journal of Materials Processing Tech. 275 (2020)116355).
-
Fernando Matos Scottia, Felipe Ribeiro Joao da Silvaa, Thermal management in WAAM through the CMT Advanced process and an active cooling technique, Journal of Manufacturing Processes 57 (2020) 23-35.
-
V. Dhinakaran , J. Ajith , A. Fathima Yasin Fahmidha , T. Jagadeesha , T. Sathish , B. Stalin, Wire Arc Additive Manufacturing (WAAM) process of nickel based superalloys A review, Materials Today : Proceedings 21 (2020) 920-925.
-
Sudhanshu Ranjan Singh , Pradeep Khanna, Wire arc additive manufacturing (WAAM): A new process to shape engineering materials, Materials Today : Proceedings 44 (2021) 118-128.
-
Tiago A. Rodrigues *, Valdemar R. Duarte , R.M. Miranda , Telmo
G. Santos , J.P. Oliveira, UltracoldWire and arc additive manufacturing (UC-WAAM), , Journal of Materials Processing Tech. 296 (2021) 117196.
-
Sagar Singh, Satish kumar Sharma , Dinesh W. Rathod, A review on process planning strategies and challenges of WAAM, Materials Today: Proceedings (2021).
-
Aldalur a,*, A. Su´arez a,b, F. Veiga a, Metal transfer modes for Wire Arc Additive Manufacturing Al-Mg alloys: Influence of heat input in microstructure and porosity, Journal of Materials Processing Tech. 297 (2021) 117271
-
Jihui Zhou, Chuanbao Jia *, Meng Guo, Maoai Chen, Jinqiang Gao, Chuansong Wu, Investigation of the WAAM processes features based on an indirect arc between two non-consumable electrodes,
Vacuum 183 (2021) 109851
-
Duarte, V.R., Rodrigues, T.A., Schell, N., Miranda, R.M., Oliveira, J.P., Santos, T.G., 2020. Hot forging wire and arc additive manufacturing (HF-WAAM). Addit. Manuf., 101193
-
S. Srivatsav, V. Jayakumar, M. Sathishkumar, Recent developments and challenges associated with wire arc additive manufacturing of Al alloy: A review, Materials Today 2021
-
Tobias Hauser a,d,*, Raven T. Reisch b,d, Philipp P. Breese c,d, Yogesh Nalam d, Kaivalya S. Joshi d, Katharina Bela d, Tobias Kamps d, Joerg Volpp a, Alexander F.H. Kaplan a, Oxidation in wire arc additive manufacturing of aluminium alloys, Additive Manufacturing 41 (2021) 101958
-
Raven Reischa,b,*, Tobias Hauserb, Tobias Kampsb, Alois Knolla, Robot Based Wire Arc Additive Manufacturing System with Context- Sensitive Multivariate Monitoring Framework, Procedia Manufacturing 51 (2020) 732-739
-
Adama Diourt´e a,*, Florian Bugarin a, Cyril Bordreuil b, St´ephane Segonds, Continuous threedimensional path planning (CTPP) for complex thin parts with wire arc additive manufacturing, Additive Manufacturing 37 (2021) 101622
-
Pranjal Shuklaa, Balaram Dasha, Degala Venkata Kirana*, Satish Bukkapatnam, Arc Behavior in Wire Arc Additive Manufacturing Process, Procedia Manufacturing 48 (2020) 725-729
-
S. Suryakumar, A. Bernard, K.P. Karunakaran, U. Chandrasekhar,
D. Sharma, N. Raghavender, Weld Bead Modelling and Process Optimization in Hybrid Layered Manufacturing. Computer Aided Design, Vol. 43, no. 4, pp. 331-344, 2011
-
N. Shamsaei, A. Yadollahi, L. Bian, S.M. Thompson, An overview of Direct Laser Deposition for additive manufacturing; Part II: mechanical behavior, process parameter optimization and control, Addit. Manuf. 8 (2015) 1235.
-
J. Ding, P. Colegrove, J. Mehnen, S. Ganguly, P.M.S. Almeida, F. Wang, S. Williams, Thermomechanical analysis of wire and arc additive layer manufacturing process on large multi-layer parts, Comput. Mater. Sci. 50 (2011) 33153322.
-
A. Horgar, H. Fostervoll, B. Nyhus, X. Ren, M. Eriksson, O.M. Akselsen, Additive manufacturing using WAAM with AA5183 wire, J. Mater. Process. Technol. 259 (2018) 6874.
-
P. Henckell, K. Günther, Y. Ali, J.P. Bergmann, P. Foret, The influence of gas cooling in context of wire arc additive manufacturinga novel strategy of affecting grain structure and size, TMS 2017 146th, in: Annual Meeting & Exhibition Supplemental Proceedings vol. 146, 2017, pp. 147156.
-
D. Herzog, V. Seyda, E. Wycisk, C. Emmelmann, Additive manufacturing of metals, Acta Mater. 117 (2016) 371392.
-
C. Zhang, Y. Li, M. Gao, X. Zeng, Wire arc additive manufacturing of Al-6Mg alloy using variable polarity cold metal transfer arc as power source, Mat. Sci. Eng. A. 711 (2017) 415423.
-
Wang F, Williams S, Rush M. Morphology investigation on direct current pulsed gas tungsten
-
Arc welded additive layer manufactured Ti6Al4V alloy. Int J Adv Manuf Technol 2011;57:597603>
-
Z. Pan, D. Cuiuri, et al., Bead modelling and implementation of adaptive MAT path in wire and arc additive manufacturing, Rob. Comput. Integr. Manuf. 39 (2015) 3242.
-
Bambach, M., Sizova, I., Sydow, B., Hemes, S., Meiners, F., 2020. Hybrid manufacturing of components from Ti-6Al-4V by metal forming and wire-arc additive manufacturing. J. Mater. Process. Technol. 282, 116689.
-
Cunningham, C.R., Flynn, J.M., Shokrani, A., Dhokia, V., Newman, S.T., 2018. Invited review article: strategies and processes for high quality wire arc additive manufacturing. Addit. Manuf. 22, 672686.
-
Kazanas, P., Deherkar, P., Almeida, P., Lockett, H., Williams, S., 2012. Fabrication of geometrical features using wire and arc additive
manufacture. Proc. Inst. Mech. Eng. Part B J. Eng. Manuf. 226, 10421051.
-
L. chao, 2018b. Wire and arc additive manufacture of high-building multi-directional pipe joint. Int. J. Adv. Manuf. Technol. 96, 2389 2396.
-
Wang, X., Wang, A., Li, Y., 2019b. A sequential pathplanning methodology for wire and arc additive manufacturing based on a water-pouring rule. Int. J. Adv. Manuf. Technol. 103, 38133830. F. Martina, P.A. Colegrove, S.W. Williams, J. Meyer, Microstructure of interpass rolled wire + arc additive manufacturing Ti-6Al-4V components, Metall. Mater. Trans. A 46 (2015) 61036118.
BIOGRAPHIES
Harshit Bansal received his B.Tech degree from Noida Institute of Engg. & Technology, Noida, India and M.Tech in Production Engg. from Delhi Technological University, Delhi, India. |
|
Abhiraj Kumar Gupta received his B.Tech degree from ABES Engg. College, Ghaziabad, India and M.Tech in Production Engg. From Delhi Technological University, Delhi, India. |