
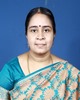
- Open Access
- Authors : Dr.S. Subasree, Dr.N.K. Sakthivel, L.Dhinesh, R.Shathiyapriyan, K.S.Chandru, M.Karthik
- Paper ID : IJERTV13IS040096
- Volume & Issue : Volume 13, Issue 04 (April 2024)
- Published (First Online): 24-04-2024
- ISSN (Online) : 2278-0181
- Publisher Name : IJERT
- License:
This work is licensed under a Creative Commons Attribution 4.0 International License
Sensory Detector of Hazardous Gases in Poultry Farms
Dr.S. Subasree Professor and Head, Department of CSE
Nehru Institute of Engineering and Technology
Coimbatore, India
R.Shathiyapriyan
Department of CSE
Nehru Institute of Engineering and Technology
Coimbatore, India
Dr.N.K. Sakthivel
Dean(Academics),
Nehru Institute of Engineering and Technology
Coimbatore, India
K.S.Chandru
Department of CSE
Nehru Institute of Engineering and Technology
Coimbatore, India
L.Dhinesh
Department of CSE
Nehru Institute of Engineering and Technology
Coimbatore, India
M.Karthik
Department of CSE
Nehru Institute of Engineering and Technology
Coimbatore, India
Abstract The production of poultry is essential to meeting the world's demand for animal protein. However, as chicken production intensifies, it becomes more critical than ever to manage the associated health and environmental problems. Poultry houses contain hazardous gasses that pose a serious threat to the wellbeing of the birds as well as the health of surrounding residents and farm laborers. Concentrations of harmful gases, such as carbon dioxide, hydrogen sulfate, ammonia, and others, can accumulate and result in respiratory issues, reduced revenue, and even death. It is necessary to create contemporary sensory gas detection systems for chicken farms in order to lessen these risks and ensure the security and well-being of both humans and animals. These detectors employ modern technology to continuously monitor gas concentrations and provide real-time data and alarms to farm operators. By promptly detecting and reacting to rising gas levels, these devices provide proactive intervention activities, such as improved ventilation and waste disposal to guarantee perfect air quality beneath the chicken buildings. A complex combination of hardware and software modules, such as high- sensitivity gas detection mechanisms, microcontrollers and information-processing techniques, graphical user interfaces, and alarm systems, make up the sensory detector for hazardous gasses in chicken farms. Together, these elements enable accurate gas concentration detection, data evaluation, and stakeholder sharing of useful information. Additionally, developments in technologies for wireless communication make it possible for farm managers to monitor and control operations remotely. This enhances operational effectiveness as well as security by enabling them to promptly check gas levels from any location.
Keywords Hazardous gases, Real-time data, Respiratory issues, Poultry production
-
INTRODUCTION
An essential part of supplying the world's animal protein needs is the production of poultry. But as chicken production increases, it becomes more and more important to deal with the related environmental and health issues. Hazardous gasses found in poultry houses not only threaten the health of
nearby populations and farmworkers, but also the welfare of the birds themselves. Gases like ammonia, hydrogen sulfide, and carbon dioxide can build up and cause respiratory problems, financial losses, and even death. In order to reduce these hazards and guarantee the wellbeing and safety of people as well as animals, modern sensory gas detection equipment are essential for chicken farms. These devices use contemporary technology to continually monitor gas concentrations and give farm operators real-time data and alarms. These devices ensure optimal air quality in poultry operations by quickly detecting and responding to rising gas levels. They also enable proactive actions such as improved ventilation and waste management. These sensory detectors, which consist of an intricate combination of both software and hardware modules, such as microcontrollers, machine learning algorithms, user interfaces with graphics, alarm systems, and high-sensitivity detection of gases mechanisms, allow for accurate detection of gas concentrations, data analysis, and the communication of critical information to relevant parties. Furthermore, improvements in technology for wireless communications enable farm managers to oversee and manage activities from a distance, improving operational effectiveness and safety by facilitating quick gas level assessments from any location. In light of this, this study investigates the creation and application of sensitive gas detection equipment designed especially for chicken farms, emphasizing the critical role that these systems play in protecting human health and animal welfare while also improving operational efficiency.
-
LITERATURE REVIEW
-
Detection of Sewer Gases
Sewer gas is a complex combination of harmful and harmless gases that are created and gathered in sewage systems as a result of the breakdown of common sewage components, such as organic domestic or industrial waste. Hydrogen sulfide, ammonia, methane, also sulfur dioxide,
and carbon monoxide, and nitrogen oxides are examples of sewer gases. The goal of this project is to provide a system that can identify and warn the user of potentially harmful gases that have developed inside the sewer system before they are exposed to them. The measurement of these identified gases is done in "parts per million (ppm)". The values for thresholds that were previously put into the controller are then compared with it. The user receives a warning along with the ppm readings if the detected values exceed the threshold value. The user is only shown the ppm readings without any warnings if the recorded values are less than the threshold value. Low concentrations of the compound can irritate the pupils and induce a sore throat or cough, shortening of breath, and lung fluid buildup. Extended low-level exposure can lead to dizziness, exhaustion, migraines, pneumonia, appetite loss, irritability, and poor memory. Oxygen sulfide at high quantities (>150 ppm) can cause olfactory tiredness, which makes the aroma unnoticeable. Higher amounts of hydrogen sulfide (>300 ppm) might result in unconsciousness and even death. After just one breath, very high doses (>1000 ppm) can cause an instantaneous collapse.
For these harmful gases, the NIOSH suggested Exposure Limit (REL) is:
-
The average ammonia level during an eight-hour workday is 25 ppm.
-
There are 350 ppm of carbon dioxide.
-
Over the course of an eight-hour workday, methane levels average 1,000 ppm.
-
After 15 minutes on average, the concentration of hydrogen sulfide is 15 ppm.
-
-
Electronic Nose for Monitoring Odor
With the ability to pinpoint the source of odors and track the spread of odors throughout the surrounding area in real time, e-nose technology has proven beneficial in addressing a range of unpleasant issues. The temperature and humidity sensors are two of the eight metal oxide semiconductors (MOX) gas sensors used in the lab-developed electronic nose system. The primary volatile chemicals released by the cattle farms were taken into consideration when choosing the gas sensors. Principal Component Analysis, or PCA, was employed in conjunction with data analysis approaches to identify distinct odor samples through classification algorithms. Additionally, each poultry farm's e-nose has been used to investigate the sources of the malodor. Poultry farms with inadequate building management and manure hanling systems were found to have high quantities of odor. In conclusion, the agricultural and cattle industries may benefit from the monitoring capabilities that e-nose technology offers. It is advised that e-nose devices be used on animal farms in order to lower the risk to the health and safety of employees as well as neighborhood complaints.
-
-
EXISTING SYSTEM
In the current system, poultry farmers rely on periodic manual inspections to evaluate air quality and detect hazardous gas accumulation within the poultry house. This process often involves visual observation, where farmers
look for signs such as unusual odors, surface discoloration, or condensation on walls or equipment. However, this manual approach poses risks to farm workers, who may be exposed to hazardous gases during inspections or while responding to gas-related incidents. Without continuous monitoring and early warning systems, workers may not detect dangerous gas levels until symptoms of exposure manifest. Moreover, the existing system lacks automation and remote monitoring capabilities, making it challenging for farmers to monitor gas levels consistently and implement timely corrective measures. To address these limitations, the development of a sensory detector for hazardous gases in poultry farms offers a promising solution, enabling real-time monitoring, proactive intervention, and enhanced safety for both poultry and farm workers.
-
PROPOSED SYSTEM
The proposed solution involves the development of an automatic sensor model to address emissions of ammonia (NH3), hydrogen sulfide (H2S), carbon dioxide (CO2), and nitrogen (N2) gases from bird litter in poultry farms. The methodology begins with the careful selection of suitable electrochemical sensors, strategically placed in areas prone to gas emissions. These sensors continuously collect real- time data, which is processed to identify patterns in gas concentrations. The system incorporates predefined threshold levels for NH3 and H2S, triggering an alarm system when these levels are exceeded. Additionally, a communication module facilitates remote monitoring and alerts, providing farm personnel with timely information. And the machine learning algorithm implemented in this solution helps to identify the data corresponding to the time as hazardous or not. By leveraging advanced sensor technology and data analysis capabilities, the system empowers poultry farmers to proactively manage gas-related risks and optimize poultry farming operations. This integrated approach enhances safety, improves air quality, and enhances overall efficiency in poultry farming practices.
Figure 1 Proposed System Model
-
System Working
-
-
HAZARDOUS GAS MONITORING SYSTEM
Figure 2 Overall Proposed System Architecture
The proposed solution involves the development of an automatic sensor model to address emissions of ammonia (NH3), hydrogen sulfide (H2S), carbon dioxide (CO2), and nitrogen (N2) gases from bird litter in poultry farms. The methodology begins with the careful selection of suitable electrochemical sensors, strategically placed in areas prone to gas emissions. These sensors continuously collect real- time data, which is processed to identify patterns in gas concentrations. The system incorporates predefined threshold levels for NH3 and H2S, triggering an alarm system when these levels are exceeded. Additionally, a communication module facilitates remote monitoring and alerts, providing farm personnel with timely information. By leveraging advanced sensor technology and data analysis capabilities, the system empowers poultry farmers to proactively manage gas-related risks and optimize poultry farming operations. This integrated approach enhances safety, improves air quality, and enhances overall efficiency in poultry farming practices.
Figure 3 Flow Diagram of Hazardous Gas Detection System
This flow statement provides a structured approach to deploying a comprehensive sensory gas detection system, integrating data collection, processing, machine learning, and data sharing to enhance safety and efficiency in poultry farm operations. The hazardous gases can be detected using gas sensor that is been used for the particular gas such as MQ136 and MQ137 to identify key gases from the poultry farm and also other sensor to collect the data from the other surrounding gas. Also uses this data to create a dataset to create a report and use the system wisely. The microcontroller paired with IoT module also allows us to share data to the cloud source and use the data to feed the data to the machine learning model and display the data over to the webpage and allow the user to access the data and the place remotely.
-
Sensors
We make use of a variety of sensors that are intended to identify gasses that are frequently present in poultry farming settings. These sensors are deliberately chosen for their exceptional sensitivity and dependability in detecting gases such as carbon dioxide, also known as CO2, hydrogen sulfide (H2S), & ammonia, which (NH3). Examples of these sensors are the MQ series (such as MQ2, MQ8, MQ136,
MQ135, MQ137). The MQ series detectors are well-known for their dependability and capacity to deliver precise real- time readings, which makes them perfect for ongoing gas concentration monitoring in chicken houses. These sensors are arranged in a deliberate manner throughout the building to provide thorough coverage and efficient risk identification. Through the incorporation of these types of sensors into the sensory detector for gases system, our goal is to improve farm worker safety and health by anticipating and addressing any gas-related risks.
Sensor No
Gas Sensors
Sensor name
Part Per
Million (PPM)
MQ2
Methane & Butane Gas Sensor
200 ~
10000ppm
MQ8
Hydrogen Gas Sensor
100 ~ 1000ppm
MQ135
Air Quality Gas Sensor
10 1000ppm
MQ136
Hydrogen Sulfide Gas Sensor
1 ~ 200ppm
MQ137
Ammonia Gas Sensor
5 ~ 500ppm
PM 2.5
Dust Smoke Particle Sensor
500g/m3
-
Microcontroller and IoT
Arduino : Our sensory gas identification system's Arduino microcontroller functions as its main processing unit, reading sensor data, running data processing algorithms, and managing the system's general functioning. Our selected gas detectors and other hardware elements can be seamlessly integrated with the Arduino microcontroller thanks to its extensive variety of input and output, or I/O, pins and support for many communication protocols. Furthermore, the Arduino platform provides an intuitive programming environment that enables us to create and use unique algorithms that are suited to our particular application needs. We can improve our sensory gas identification system's performance and expand its possibilities for accurate and on time gas monitoring in chickens farming conditions thanks to its versatility.
ESP32 : ESP32 is a single 2.4 GHz Wi-Fi-and-Bluetooth combo chip designed with the TSMC low-power 40 nm technology. It is designed to achieve the best power and RF performance, showing robustness, versatility and reliability in a wide variety of applications and power scenarios. Overall, the ESP32 plays a central role in our project, facilitating seamless communication, data processing, and system control to ensure the safety and well-being of poultry and farm personnel.
-
Gps Module
This is a third generation POT (Patch Antena On Top) GPS module. This POT GPS receiver providing a plution that high position and speed accuracy performances as well as high sensitivity and tracking capabilities in urban conditions & provides standard NMEA0183 strings in "raw" mode for any microcontroller. The module provides current time, date, latitude, longitude, speed, altitude and travel direction / heading among other data, and can be used in a host of
applications, including navigation, tracking systems, fleet management, mapping and robotics. This is a standalone GPS Module and requires no external components except power supply decoupling capacitors. It is built with internal RTC Back up battery. It can be directly connected to Microcontroller's USART. The module is having option for connecting external active antenna if necessary. The GPS chipsets inside the module are designed by MediaTek Inc., which is the world's leading digital media solution provider and largest fab-less IC company in Taiwan. The module can support up to 51 channels. The GPS solution enables small form factor devices. They deliver major advancements in GPS performances, accuracy, integration, computing power and flexibility. They are designed to simplify the embedded system integration process.
-
Voice Module
The APR9600 device offers true single-chip voice recording, non-volatile storage, and playback capability for 40 to 60 seconds. The device supports both random and sequential access of multiple messages. Sample rates are user- selectable, allowing designers to customize their design for unique quality and storage time needs. Integrated output amplifier, microphone amplifier, and AGC circuits greatly simplify system design. the device is ideal for use in portable voice recorders, toys, and many other consumer and industrial applications. APLUS integrated achieves these high levels of storage capability by using its proprietary analog/multilevel storage technology implemented in an advanced Flash non-volatile memory process, where each memory cell can store 256 voltage levels. This technology enables the APR9600 device to reproduce voice signals in their natural form. It eliminates the need for encoding and compression, which often introduce distortion.
-
Machine Learning
The naive Bayes classifier algorithm is a supervised ML algorithm that leverages probabilistic computations for classification. It is a fast and efficient classifier that works on a set of independent features to predict and classify a binary output. Initially, a frequency table is created when the data set is input to the naive Bayes trainer node. The posterior probability for each class is then calculated using the obtained frequency table using the Bayes formula
(|)()
(|) = ()
-
P(A|B) is Posterior probability: Probability of hypothesis A on the observed event B.
-
P(B|A) is Likelihood probability: Probability of the evidence given that the probability of a hypothesis is true.
-
P(A) is Prior Probability: Probability of hypothesis before observing the evidence.
-
P(B) is Marginal Probability: Probability of Evidence
-
This formula is applied to every independent occurring feature, and the class with the highest posterior probability would be assigned as the outcome. The naive Bayes trainer node displays 2 outputs: (1) statistical table of the data set and (2) Parametric mixture models naive Bayes table.
-
-
EXPERIMENTAL RESULT
hazardous Gas from Poultry Farm is one major concern and a challenge always.
This paper thus put forth a new proposed system which is microcontroller based application of Detection of hazardous Gas from Poultry Farm using IOT. The sensor used in this model can sense and detect the formation of the gas, and the user gets notification regarding to gas in the area as well certain action can be taken to locate the area location without any barrier. This unit can be easily integrated into an alarm unit, and the mobile display for an earlier awareness for further benefits. This proposed system can be useful in agriculture sectors like poultry, livestock farm etc. This has the potential to revolutionize air quality management practices in poultry farming, leading to healthier environments, increased productivity, and improved sustainability within the industry. The main intention of this work is to ensure safe and easier way detecting the formation of the gas in the environment to avoid disasters that may occur due to negligence and long term exposure of the gas to workers.
Figure 4 Prototype model of the Hazardous Gas Detection System
The prototype of projected system is shown in the Figure 4. This proposed system is developed to detect and monitor the Hazardous Gas in Poultry Farm ,when a small amount of gas is brought near the MQ sensor, it display the message in LCD i.e Air Contamination Found at the time of spreading of the gas and the system monitors the gas level and displays the message i.e, Air Contamination Found MQ. As in recent times, the problems that are faced by the workers of the poultry farm such as respiratory problems and eye irritation has been observed, the developed system will be helpful to the workers. It helps them to upgrade their safety norms and aids to prevent the major disaster. It also helps in protecting life and property from apparent accidents. The primary aim of this proposed system is therefore to detect the gas formation which is detected though gas sensor and user should be notified to prevent injure or outburst. The secondary aim is to remotely monitor and also help the worker to identify the easier working environment and focus on the major source of the problem and also maintain the farm easier.
-
CONCLUSION
Internet of Things has gained its wide popularity in recent days due to its various streams of applications which has paved way for smooth, safe and easier mode of living style for human beings. One such area of applications includes Detection of hazardous Gas from Poultry Farm for both domestic and commercial purposes. Though, several techniques is existing for the same, yet Detection of
REFERENCES
-
MUHAMMAD SHOAIB FAROOQ, OSAMA OMAR SOHAIL,
ADNAN ABID, (Member, IEEE), AND SAIM RASHEED A
Survey on the Role of IoT in Agriculture for the Implementation of Smart Livestock Environment IEEE ACCESS VOLUME 10,2022 Pp:5
-
Dr. G. S. Uthayakumar, F. Albinus Sagay Tomson and R. Ashwin Remote Detection for the Presence of NH3, CO2, CH4, H2S, CO and Other Toxic Gases at Various Locations in a Sewer to Alert the User International Journal of Advanced Research in Science, Communication and Technology (IJARSCT) VOLUME -4 April 2021 Pp:3-5.
-
Wandee Aunsa-Ard, Theerapat Pobkrut, Teerakiat Kerdcharoen, Nathamanee Prombaingoen, Olarn Kijpreedaborisuthi Electronic Nose for Monitoring of Livestock Farm Odors (Poultry Farms) IEEE ACCESS VOLUME -1 2021 IEEE Pp:2-3.
-
Wandee Aunsa-Ard, Theerapat Pobkrut, Teerakiat Kerdcharoen, Satetha Siyang, Nathamanee Prombaingoen Development of lntelligent Electronic Nose for Livestock Industries 7th International Conference on Engineering, Applied Sciences and Technology (ICEAST) VOLUME-1 2021 Pp:2.
-
M. Chernyshev, Z. Baig, O . Bello, S. Zeadall, Internet Of Things (Iot): Research, Simulators, And Testbeds, Iot-2488-2017.
-
Punit Rathore, Aravinda S. Rao, , SutharshanRajasegarar, ElenaVanz,JayavardhanaGubbi, And MarimuthuPalaniswami, Fellow, IEEE, Real-Time Urban Microclimate Analysis Using Internet Of Things, IEEE Internet Of Things Journal,2017.
-
Sony Shrestha; V. P. Kishna Anne; R. Chaitanya, "IoT Based Smart Gas Management System," 2019 3rd International Conference on Trends in Electronics and Informatics (ICOEI),
DOI:10.1109/ICOEI.2019.8862639
-
Arpitha, T and Kiran, Divya and Gupta, VSN Sitaram and Duraiswamy, Punithavath, FPGA-GSM based gas leakage detection system, India Conference (INDICON), 2016 IEEE Annual.
-
Fraiwan, Luay and Lweesy, Khaldon and Bani-Salma, Aya and Mani, Nour A wireless home safety gas leakage detection system, Biomedical Engineering (MECBME), 2011 1st Middle East Conference on IEEE
-
Kesavan, G., P. Sanjeevi, and P. Viswanathan A 24 hour IoT framework for monitoring and managing home automation, Inventive Computation Technologies (ICICT), International Conference on. Vol. 1. IEEE, 2016.