
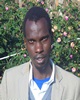
- Open Access
- Authors : Clement Kiprotich Kiptum , Steve Ochieng Ochieng , Victor Muroki Mwirigi
- Paper ID : IJERTV9IS070681
- Volume & Issue : Volume 09, Issue 07 (July 2020)
- Published (First Online): 06-08-2020
- ISSN (Online) : 2278-0181
- Publisher Name : IJERT
- License:
This work is licensed under a Creative Commons Attribution 4.0 International License
Cost and Waste Evaluation of Expanded Polystyrene (EPS) Model House in Kenya
Clement Kiprotich Kiptum, Steve Ochieng Ochieng, Victor Muroki Mwirigi
Department of Civil and Structural Engineering University of Eldoret
Eldoret, Kenya
Abstract Expanded polystyrene panels is a recent construction material in Kenya used for construction of walls and floors. However, its usage like most building materials generates wastes. Moreover, being less than six years since its introduction in the Kenyan market means that very few people understand the cost of building a residential house using EPS in Kenya. The aim of the study was to determine the cost and wastes generated during construction of an EPS model house. The methodology involved construction of a 3.6 m by 3.6 m house using EPS, measurement of wastes generated and costing several elements of the building. The results showed that the model house costs Ksh. 37 858/m2 and generated 11% wastes. EPS house was more expensive than stone house and is therefore not a cheaper construction material.
KeywordsCost;expanded polystyrene; house; waste
-
INTRODUCTION
It is expected that by the year 2030, two-thirds of world population will be living in urban areas and will require adequate housing if Goal number 11 of the United Nations Sustainable Development Goals is to be met [1]. House affordability is not only a problem to the unemployed persons but also a problem to those employed who spend more than 50% of their income in paying rent [2]. UN-HABITAT defines affordable housing as one that is adequate in quality, location and its cost does not interfere with an occupants capacity in meeting other needs or his or her enjoyment of other basic human rights [3]. Affordable housing is one of the Big Four ambitious social programmes that the Kenyan government hopes to deliver for Kenyans [4]. This ambition is similar to Indias slogan of Housing for All by 2022 [5]. Indeed, house affordability in Kenya is a challenge and as a consequence, 40% of urban dwellers particularly those in low income areas live in mud walled houses [6] despite the availability of other walling materials like concrete blocks, stones, bricks and timber. Kenyan urban population is more than 33% of the total population and majority of these urban dwellers live in low income areas renting houses. In fact 40% of Kenyans live in rented houses as per the census of 2019. The census further revealed that the leading walling material was mud/cow dung at 27.5% following by stone at 16.5% and thirdly, concrete blocks at 16.3% [7]. In the census report, there was no mention of expanded polystyrene (EPS) panels despite the construction of EPS factory in Mlolongo, Kenya, in 2012. According to the National Housing Corporation in Kenya, the use of EPS reduces both direct and indirect costs in construction by 30 % while shortening the construction
time by 50% [8] and therefore this is ideal building material for low income earners. This contradicts what the Indian manual (Indian manual) that showed that EPS construction is 12.9% cheaper than reinforced concrete building. Apart from walling EPS panels can be used for floor, stairs, partitions and roofs according to EPS Indian manual [5]. Walling constitutes more than two-thirds of the outer surface area of any building. Therefore, any cheap material that is used for walling has a great influence in reducing the overall cost of the building. It was in this in mind that this study was conceived and conducted with the aim of determining the costs and wastes which will go a long way in creating awareness and promoting use of EPS in other parts of Kenya away from Nairobi. In this study, a model house was constructed to give information to inform the governments agenda on affordable housing.
-
METHODOLOOGY
-
Construction of Model House
The location of the model house was near the school of engineering workshop, University of Eldoret. The dimensions of the model house were 3.6 m by 3.6 m and 2.7 metres high. The cost of each item was noted and photos taken as the work was progressing which helped in the determination of the cost per square metre.
-
Determination of Wastes
The total number of EPS panels used to construct walls was counted. The areas of each panel as well as pieces of wastes were measured using a steel tape measure. The total area of EPS panels used was found by multiplying the number of panels used by the area of one panel whose dimensions were 1.2 m by 2.7 m. For the roof slab, the total number of roof slab panels used was noted and multiplied by the area of one panel that measured 1.2 m by 3.0 m. During construction, the wastes generated as a result of cutting EPS panels at the door, window spaces and construction of canopy for roof were measured by taking the length and the width of each piece that remained. This was done for both wall and roof floor panels.
-
-
RESULTS AND DISCUSSION
-
Cost of Model house
Walling of the model house (Fig.1) constituted 50% of the outer surface area of the building. The total surface area
included; floor, roof and the walling. A plaster known as shotcrete of more 40 mm was done on the EPS panels both inside and outside of the house. The plastering of the outside makes the EPS house look the same as a house made of blocks or stones when plastered. This denies EPS house the aesthetics and the beauty that goes with usage of bricks or bush stones that have different shades of colours and therefore this could be one of the disadvantages of EPS house.
Fig. 1. Walling of model house using EPS Panels
Labour cost was 22% of the total cost while the cost of transporting EPS panels from Nairobi was 8% (Table I). Purchasing of EPS panels represented 34% of the total cost. Considering that the roof as well as the walls were made of EPS panels, meant that the cost would have been lower if the factory prices of EPS can be reduced. Cost of materials was around 78% of the total cost which is higher than 50-60% observed [9] when they were studying affordable housing in fifteen African countries. The cost of transportation can be reduced if factories are located near major towns like Eldoret. Bringing factories closer to many developers will create more awareness which has direct influence of increasing uptake of EPS panels in Kenya. If one has many projects the cost of timber can be reduced by recycling timber from one project to another. From Table I, it can be seen that the cost of the model house was Ksh. 490,640 and if it is divided by the floor area of 12.96 m2, the cost translates to Ksh. 37 858/ m2, using exchange rate of 1USD to Ksh. 107, it was found that the cost was USD 354 /m2. According to Indian standard [5] the cost in India in Indian rupees is 5545/m2, using exchange rate of 1USD to 75 Indian rupees, it was found that the cost becomes USD 74 /m2. This shows that the cost of constructing EPS house in Kenya is five times that in India. The reason is because in India, they have factories close to where houses are being constructed. In Afghanistan the cost of EPS house is 96 USD/m2 [10]. This cost is in between Kenya and India because Afghanistan is not as industrialized as India and is more developed than Kenya.
Description
Cost (KSh.)
Labour
110100
EPS Panels
168000
Transport of EPS
40000
Reinforcement
19000
sand (10+4)
16800
Quarry dust(6+4)
12000
Ballast(2+3)
8000
Timber
18000
Description
Cost (KSh.)
Labour
110100
EPS Panels
168000
Transport of EPS
40000
Reinforcement
19000
sand (10+4)
16800
Quarry dust(6+4)
12000
Ballast(2+3)
8000
Timber
18000
TABLE I. COST OF MODEL HOUSE
Door and windows
18000
Electrical
16940
Nails and bind wire
3000
Welding
6600
Cement
43200
Painting and glazing
11000
Total
490640
The cost of the model house was more than Ksh. 25,000 per square metre of stone wall houses, and also higher than Ksh. 5000/ m2 for iron sheet walled houses as observed by [6] in Kenyan low income areas. In addition, EPS model house costs more than Ksh. 30,000 /m2 observed by [11] in 2018 for concrete block houses. This means that an EPS house is a little bit expensive and might not be affordable to many Kenyans.
-
Percentage waste generated
The area of one wall panel was 3.24 m2. Since the house consumed on the one hand 13 panels, their cumulative area was found to be 42.12 m2. On the other hand, the house consumed 4 floor panels with a cumulative area of 14.4 m2 considering that each floor panel had an area of 3.6 m2 There were ten pieces of waste generated with nine of them from wall panels and the remaining one from roof floor panel. The area of each piece is shown in Table II.
TABLE II. AREAS OF WASTES
Description
Length (m)
Width (m)
Area (m2)
Wall Panel pieces
Piece 1
2.70
0.60
1.62
Piece 2
2.70
0.30
0.81
Piece 3
1.08
0.45
0.49
Piece 4
0.93
0.44
0.41
Piece 5
1.20
0.30
0.36
Piece 6
0.90
0.37
0.33
Piece 7
0.89
0.29
0.26
Piece 8
1.04
0.24
0.25
Piece 9
0.62
0.17
0.11
Total for wall pieces
4.64
Floor Panel
Piece 10
1.24
0.30
0.37
The percentage wastes were 11% and 2.6% for wall and floor panels, respectively. Wall panels had high percentage because in the wall panels there were wastes due to openings for windows and doors. In the roof there were no openings. The longer pieces of 2.7 m of wastes were the pieces that remained when constructing the canopy for the roof. These wastes need not be thrown to the dust pin but can be recycled to make light weight block as demonstrated by [12].
-
-
CONCLUSION
The study found that constructing a model house using EPS costs Ksh. 37 858/m2 and generates wastes of 11%. There is no much difference between the cost of EPS house and that of cement blocks when plastered.
ACKNOWLEDGMENT
The researchers would like thank the University of Eldoret for awarding them research funds for the project.
REFERENCES
-
https://sustainabledevelopment.un.org/content/documents/197282018_ background_notes_SDG_11_v3.pdf. accessed on 26 June, 2020.
-
World Economic Forum. Making affordable housing a reality in cities. Cities urban development and urban services platform in collaboration with with PwC.pp.1-60, June, 2019.
-
UN-HABITAT, 2011. Affordable land and housing in Asia.
-
State Department for Housing and Urban Development. Development framework guidelines. Kenya Affordable Housing programme pp. 1- 41, October, 2018.
-
Central Building Research Institute Roorkee. Manual for Expanded Polystyrene (EPS) core panel system and its field application. Ministry of Housing and Urban Poverty Alleviation, Governmnet of India, pp 1- 152, June, 2017.
-
C.K. Kiptum, S.O. Ochieng, and V.M. Mwirigi, Affordable walling materials used in low income estates in Eldore, Kisumu and Nakuru towns in Kenya, American Journal of Science, Engineering and Technology, Vol. (2), pp.56-60, March 2020.
-
Republic of Kenya, 2019 Kenya Population and housing census volume
4. Distribution of population by socio-economic characteristics. Kenya National Bureau of Statistics, pp. 1-498, December, 2019.
-
https://www.constructionkenya.com/1698/nhc-eps-technlogy/ accessed 29 June, 2020 at 11.20 am
-
Centre for affordable housing finance in Africa. Benchmarking Housing using CAHFs housing cost benchmarking methodoloogy to analsyse housing costs in fifteen African countries, pp. 1-55, May 2019.
-
J.A. Lee, H. Kelly, A. Rosenfeld, E. Stubee, J.Colaco, A. Gadgil, H. Akbari, L. Norford and H. V. Burik, Affordable, safe housing based on expanded polystyrene (EPS) foam and a cementitious coating, Springer, J Mater Sci 41, pp.110-117,2014.
-
Association of retirement benefit scheme ARBS. 2018. 500,000 Affordable House Programs.
-
C.K. Kiptum, S.O. Ochieng, and V.M. Mwirigi, Comparing compressive strengths of layered and random placement of expanded polystyrene wastes in quarry dust blocks , Journal of Civil Engineering Science and Technology, Vol.11 (1), pp.57-63, April 2020.
Is there a known company doing these kinds of houses in the Juja region, Kiambu county? I am looking for an alternative method of construction for a 3-bedroomed family house.