
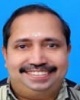
- Open Access
- Authors : Dr., Narayanan N I, Archana T A
- Paper ID : IJERTV13IS040161
- Volume & Issue : Volume 13, Issue 04 (April 2024)
- Published (First Online): 24-04-2024
- ISSN (Online) : 2278-0181
- Publisher Name : IJERT
- License:
This work is licensed under a Creative Commons Attribution 4.0 International License
Glass Fiber Composite Materials
Dr.,Narayanan N I, Archana T A
Department of Civil Engineering, Government College of Engineering Kannur Kerala, India
Abstract Glass fiber composite materials have become indispensable in various industries due to their exceptional mechanical properties and versatility. This comprehensive review paper explores the advancements, properties, fabrication techniques, and applications of these materials. It begins with an introduction to the basic constituents and structure of glass fiber composites, followed by an in-depth discussion of the different types of glass fibers and their suitability for various applications. Fabrication processes such as hand lay-up, filament winding, and resin transfer molding are elucidated, along with their advantages and limitations. The paper also examines the mechanical properties of glass fiber composites, including tensile and flexural strength, as well as factors influencing their behavior such as fiber orientation and interfacial bonding. Additionally, thermal, electrical, and chemical properties are discussed, highlighting their significance in specific applications. Diverse applications across industries such as aerospace, automotive, marine, construction, and sporting goods are presented to showcase the widespread adoption of glass fiber composites. Finally, challenges and opportunities in the field, including recyclability and sustainability, are addressed, offering insights for future research and development. This review serves as a valuable resource for researchers, engineers, and practitioners seeking a comprehensive understanding of glass fiber composite materials and their potential applications.
Keywords Fabrication techniques, composites, glass fiber, glass fiber material, polymer-reinforced concrete, natural fiber, hybrid composite, polymer-matrix composites (PMCs), mechanical properties.
-
INTRODUCTION
Glass fiber composite materials are becoming an essential class of materials in many industries because of their remarkable mechanical qualities, low weight, and adaptability in terms of design and fabrication. Made up of glass fibers embedded in a polymer matrix, these composites are ideal for a variety of applications due to their exceptional strength, stiffness, and resistance to corrosion. A summary of the fundamental components and structure of glass fiber composites is given in this introduction, which also establishes the background for the discussion that follows on the developments, characteristics, manufacturing processes, and uses of these materials.
The reinforcement phase, which consists of glass fibers, and the matrix phase, which is often a polymer resin, are the two main components of glass fiber composites. The material's strength and stiffness come from the reinforcement phase, which is mainly made of glass fibers based on silica. The matrix phase, on the other hand, binds the fibers together, transfers loads, and protects the material from outside
elements like moisture and chemicals. When these two phases are combined, a material is produced that has better mechanical qualities than conventional materials like metals or plastics.
Glass fiber composites have advanced to the point where different kinds of glass fibers designed for particular uses have been developed. They include S-glass fibers, which are valued for their exceptional tensile strength and modulus, E- glass fibers, which are renowned for their high electrical insulation qualities, and specialty fibers like AR-glass and C- glass, which are made to meet particular performance specifications. Selecting the best material for a particular application requires an understanding of the qualities and attributes of these fibers.
Glass fiber composites' ultimate characteristics and functionality are largely determined by their fabrication methods. Different advantages exist in terms of cost, complexity, and production rate for techniques like resin transfer molding, filament winding, and hand lay-up. Manufacturers can attain desired mechanical, thermal, and electrical properties that are suited to the demands of particular applications by streamlining these procedures.
When choosing and designing glass fiber composites, it is crucial to take into account properties other than just mechanical ones, like chemical resistance, electrical conductivity, and thermal stability. These characteristics affect the material's performance and endurance in a variety of settings, such as marine applications exposed to saltwater corrosion and aerospace structures subjected to high temperatures and vibrations.
The fact that glass fiber composites are so widely used in the construction, automotive, marine, aerospace, and sporting goods industries points out how important they are to contemporary engineering and manufacturing. These materials provide unmatched design flexibility and performance advantages, fostering innovation and efficiency through a variety of sectors, from lightweight aircraft components to strong automotive body panels.
Still, there are problems with glass fiber composites, such as those pertaining to environmental impact, sustainability, and recycling. Researchers, engineers, legislators, and industry stakeholders must work together to develop more environmentally friendly manufacturing and recycling techniques in order to address these issues.
This review paper, in summary, attempts to give a thorough overview of glass fiber composite materials, addressing developments, characteristics, manufacturing processes, uses, obstacles, and prospects in the industry. In order to facilitate future breakthroughs and innovations and ensure the growth and evolution of glass fiber composites in the years to come, researchers, engineers, and practitioners must have a
thorough understanding of the fundamentals and potential of these materials.
Fig 1: fiber reinforced composite.
Fig 2: (a) Woven structure and (b) microscopy image of unidirectional glass fiber fabric.
-
CONSTITUENTS OF GLASS FIBER
COMPOSITE
Glass fiber reinforcement, which is made up of glass fibers, and the matrix phase, which is usually made of a polymer resin, are the two main parts of glass fiber composites. The mechanical qualities, stiffness, and general performance of the composite material are all significantly influenced by each component.
-
Matrix Phase: Polymer Resin
The matrix phase is essential to glass fiber composites because it holds the reinforcement fibers together, offers support, and distributes loads among them. Because of their adaptability, compatibility with glass fibers, and ease of processing, polymer resins are the most widely used matrix materials. The following describes the main characteristics and uses of polymer resins in glass fiber composites:
-
Adhesion
Interfacial bonding is the process by which the matrix material creates a strong connection with the glass fiber surface. Effective load transfer between the fibers and the matrix depends on this adhesion, which also prevents delamination and improves the composite material's overall mechanical qualities.
-
Flexibility
Because of their ductility and flexibility, polymer resins enable composite materials to deform under load without failing catastrophically. The material's impact resistance and fatigue performance are enhanced by its flexibility, which qualifies it for use in applications with dynamic loading cnditions.
-
Processing Characteristics
Polymer resins can be processed through a variety of methods, including casting, molding, and infusion, and customized for particular uses. This adaptability gives designers more creative freedom when creating and manufacturing complex forms and structures.
-
Environmental Resistance
Polymer matrix materials have outstanding resistance to UV light, chemicals, and moisture. This resistance keeps the reinforcement fibers safe from deterioration and guarantees the composite material's long-term performance and durability, even under demanding operating circumstances.
-
Durability
Polymer resins protect glass fiber composites from corrosion, wear, and abrasion, increasing their durability. Because of their durability, they can be used in a variety of industries, such as the building, automotive, marine, and aerospace sectors.
-
Weight Reduction
Lighter and more fuel-efficient structures can be achieved by using polymer matrix composites instead of more conventional materials like metals, which offer substantial weight savings. In aerospace and automotive applications, where reducing weight is essential for performance and efficiency, this weight reduction is especially helpful.
-
Mechanical Strength
Because glass fibers have a high tensile strength, they can withstand heavy loads without breaking. In applications like aerospace and automotive components, where structural integrity is critical, this property is essential.
-
Stiffness
The overall rigidity of the composite material is influenced by the glass fibers' inherent stiffness. The material performs better in structural applications due to its stiffness, which also
helps to maintain dimensional stability and inhibits excessive deformation under load.
-
Impact Resistance
Good impact resistance is offered by glass fibers, which absorb and release energy during abrupt loading events. This characteristic increases the material's toughness and damage resistance, which makes it appropriate for uses like armor panels and protective helmets where impact resistance is essential.
-
Chemical Inertness
-
The chemical inertness of glass fibers makes them immune to deterioration, corrosion, and exposure to the elements. This characteristic makes the composite material stable and long-lasting, even under challenging operating circumstances.
-
-
TYPES OF GLASS FIBERS
There are several varieties of glass fibers that are used in composite materials, and each has special qualities and uses. It is essential to comprehend the distinctions between these kinds of glass fibers in order to choose the best material for a given engineering application. The following describes the features and uses of common types of glass fiber:
-
E-Glass (Electrical Glass)
The most popular kind of glass fiber in composite materials is called E-Glass. Fibers made mostly of silica-based glass with boron oxide and alumina added, E-Glass is prized for its adaptable qualities.
Fig 3: E-Glass fiber
-
High Tensile Strength
E-Glass fibers are a good choice for applications that need load-bearing capacity and structural integrity because of their exceptional tensile strength. Construction, automotive, and aerospace are among the industries that benefit greatly from their capacity to bear heavy loads without breaking.
-
Electrical Insulation Properties
Because of their superior electrical insulation qualities, e- glass fibers are perfect for use in the electronics and electrical sectors. The safety and dependability of electronic parts and gadgets are guaranteed by their capacity to insulate against electrical currents.
-
Chemical Resistance
The chemical corrosion resistance of E-Glass fibers increases their robustness in abrasive conditions. Because of their resistance, they can be used in corrosive environments such as chemical processing plants, marine structures, and other places where it's crucial to prevent chemical degradation.
-
Applications
Due to their unique blend of strength, electrical insulation, and chemical resistance, E-Glass fibers are used extensively in a wide range of industries. They are used in aerospace for parts of aircraft, automotive for lightweight body panels and interiors, in construction for fiberglass and concrete reinforcement, and in electronics for electrical devices and circuit board insulation.
-
summary
The balancing of mechanical strength, electrical insulation, and chemical resistance that e-glass fibers provide makes them indispensable in a wide range of industries and applications. This balance is essential to the performance of composite materials.
-
-
S-Glass (Structural Glass)
E-Glass fibers comprise a class of sophisticated glass fibers that are characterized by their remarkable composition and mechanical attributes. S-Glass fibers, which are mainly made of silica-based glass with additional components like alumina and magnesia, have a number of important characteristics.
Fig 4: S-Glass fiber
-
High Tensile Strength and Modulus
The superior modulus and tensile strength of S-Glass fibers over traditional E-Glass fibers are two of their distinguishing qualities. Since S-Glass fibers have a higher strength, they can bear large loads without buckling or failing, which makes them perfect for high-performance uses that call for extraordinary mechanical qualities. S-Glass fibers provide the robustness required to meet demanding performance requirements, whether they are used in high-performance sporting goods, ballistic armor, or aerospace components.
-
Stiffness
S-Glass fibers are not only much stronger than E-Glass fibers, but they are also much more rigid. This increased stiffness offers composite structures improved dimensional stability and stiffness, resulting in less deformation or deflection under load. S-Glass fiber composites are therefore well suited for applications where stability and precision are crucial because they can retain their structural integrity and shape even in the most adverse circumstances.
-
Applications
S-Glass fibers are widely used in demanding applications in many different sectors of the economy. S-Glass fiber composites are utilized in aerospace for crucial structural elements like engine components, wings, and fuselages of aircraft. Their strength and stiffness combination enhances overall performance and safety in these applications. S-Glass fibers are also used in ballistic armor systems to offer better defense against ballistic threats without sacrificing lightweight design. The remarkable mechanical qualities of S-Glass fibers also benefit high-performance sporting goods, like golf clubs, tennis rackets, and racing bicycles, allowing athletes to perform at their best.
-
summary
Providing superior tensile strength, modulus, and stiffness over traditional glass fibers, S-Glass fibers are the epitome of advanced materials engineering. In high-performance applications where precision, dependability, and durability are critical, their exceptional qualities render them indispensable.
-
-
AR-Glass (Alkali-Resistant Glass)
Alkali-resistant glass fibers, sometimes referred to as AR- Glass fibers, are designed with special tolerance for the abrasive alkaline conditions typical of concrete applications. AR-Glass fibers, made of calcium-alumino-silicate glass, have a special set of qualities designed to improve the functionality and longevity of reinforced concrete structures:
Fig 5. S-Glass fibers
-
Alkali Resistance
AR-Glass fibers are primarily distinguished by their remarkable ability to withstand alkalis found within concrete. Fiber breakage and loss of structural integrity can result from the gradual degradation of conventional glass fibers caused by alkalis like hydroxides and carbonates. But AR-Glass fibers are designed specifically to withstand alkali attack, guaranteeing long-term performance and durability in alkaline-exposed reinforced concrete structures.
-
Enhanced Mechanical Properties
AR-Glass fibers offer concrete substantial reinforcement in addition to their resistance to alkali, which improves the material's mechanical qualities. AR-Glass fibers improve the material's impact resistance, flexural strength, and tensile strength by evenly dispersing throughout the concrete matrix. This reinforcement increases the overall durability, strengthens the structure, and reduces cracking in concrete components.
-
Applications
In many different applications where improved mechanical properties and durability are needed, AR-Glass fibers are widely used in the construction industry. AR-Glass fibers help precast concrete elementslike panels, beams, and columnsperform better structurally and have a lower chance of cracking during handling and transportation. Similarly, AR-Glass fibers are used in short-create applications, such as tunnel linings, underground structures, and slope stabilization, to improve the sprayed concrete's tensile and flexural strength and resistance to shrinkage cracking. Addition of AR-Glass fibers enhances the durability and extends the service life of fiber-reinforced concrete structures, including pavements, buildings, and bridges.
-
summary
The performance and longevity of concrete structures in alkaline environments can be improved with the help of AR- Glass fibers. When it comes to a variety of construction applications where long-term durability and structural integrity are crucial, their outstanding alkali resistance and capacity to enhance mechanical properties make them the obvious choice.
-
-
C-Glass (Chemical-Resistant Glass)
C-Glass fibers, which are well-known for their remarkable resistance to chemicals and high temperatures, are designed to perform well in challenging conditions where exposure to corrosive agents and high temperatures is common. The robust set of properties that make up C-Glass fibers, which are composed of calcium-alumino-silicate glass with elevated levels of boron oxide, are specifically designed for demanding applications.
Fig 6: C-Glass fiber
-
Chemical Resistance
Strong resistance to a wide range of chemicals, such as acids, alkalis, and corrosives, is one of the distinguishing qualities of C-Glass fibers. Because of their innate chemical resistance, they are excellent choices for use in settings where exposure to strong chemicals is a concern. C-Glass fibers ensure long-term durability and performance in corrosive environments, whether in chemical processing plants, wastewater treatment facilities, or industrial manufacturing settings.
-
High Temperature Resistance
C-Glass fibers have exceptional resistance to high temperatures in addition to their outstanding chemical resistance. Both their mechanical and structural integrity are unaffected by high operating temperatures. Because of their high temperature tolerance, C-Glass fibers are ideal for use in oil and gas refineries, industrial furnaces, and high- temperature processing operationsall settings where heat exposure is a factor.
-
Applications
The exceptional combination of chemical resistance and high temperature tolerance found in C-Glass fibers makes them highly valuable in a broad range of industries and applications. In the chemical processing sector, C-Glass fibers are used in structures and equipment like reaction vessels, piping systems, and storage tanks that are exposed to corrosive chemicals. Utilizing C-Glass fiber-reinforced composites, wastewater treatment plants can withstand the corrosive effects of wastewater and chemicals in their digesters, filtration systems, and clarifiers. Furthermore, C- Glass fibers are utilized in the oil and gas sector to provide reinforcement in harsh environments with high temperatures and corrosive fluids in offshore platforms, pipelines, and downhole equipment.
Table 1: Properties of Glass Fibers
Table 2: properties of different glass fibers
-
summary
For uses where resistance to chemicals and high temperatures is necessary, C-Glass fibers provide a dependable option. In sectors where dependability and longevity are critical, like chemical processing, wastewater treatment, and oil and gas, their exceptional resistance to chemicals and high temperature tolerance make them indispensable.
-
-
-
FABRICATION TECHNIQUES
Different fabrication techniques, each with specific benefits and drawbacks, are used in the production of glass fiber composites. To maximize the manufacturing process and obtain the appropriate material properties, one must comprehend these techniques. Here, we examine several typical fabrication methods that are applied in the creation of glass fiber composites:
-
Hand Lay-Up
Among the earliest and most flexible methods of fabricating glass fiber composites is hand lay-up. This technique involves hand-applying layers of glass fiber mats or fabrics that have been saturated with resin onto a mold surface. To remove air pockets and guarantee adequate resin impregnation, these layers are subsequently consolidated and compacted using hand tools or rollers. There are numerous noteworthy benefits to hand lay-up:
Fig 7: hand layup process.
-
Flexibility
For producing complex shapes and prototypes, hand lay-up is a highly versatile method that offers unmatched flexibility in both design and manufacturing. Manufacturers can experiment with creative designs without being constrained by inflexible production procedures thanks to this flexibility.
-
Low Cost
Hand lay-up is a cost-effective method, especially for small- scale production runs or the creation of one-of-a-kind, one- off parts, because of its simplicity, which equals lower equipment and labor costs. Hand lay-up operations are affordable and accessible to a diverse range of businesses and artisans due to the minimal investment required.
-
Suitability for Large Parts
Even though hand lay-up is manual, it can be used to fabricate large components efficiently and with little equipment. Because of its scalability, manufacturers can create large
structures without investing in costly machinery or specialized facilities.
Fig 8: Composites processes.
Fig 9: final product of composite after hand layup process.
-
limitations
-
Hand lay-up can take a lot of time and effort, particularly when working with large or complicated components. The manual application process may lengthen production times and increase expenses since it requires specialized labor and close attention to detail.
-
Based on the operator's experience and skill level, hand lay-up products can have different quality levels. Differences in mechanical properties and surface finish can result from irregularities inmaterial distribution, resin impregnation, and compaction. It might take a lot of training and quality control procedures to achieve consistency and repeatability in hand lay-up production.
Products made by hand lay-up artists can vary in quality depending on their background and degree of expertise. Inconsistencies in material distribution, resin impregnation, and compaction can lead to variations in mechanical properties and surface finish. Achieving consistency and repeatability in hand lay-up production may require extensive training and quality control procedures.
-
-
-
Filament Winding
Filament winding is a highly automated fabrication technique that is mainly used to create glass fiber composite pipes, tanks, and pressure vessels, among other cylindrical or tubular structures. Using a rotating mandrel, continuous glass fiber rovings are precisely wound in a predetermined pattern. Applying resin either during the wet winding process or after the winding process is finished is known as dry winding. Winding filaments has a number of clear benefits.
-
High Production Rate
Filament winding has an efficient high-speed production process that can produce large numbers of parts with reliable quality. It is especially well-suited for industries needing high-volume output, like infrastructure, automotive, and aerospace, because of its quick production rate.
-
Tailored Properties
Filament winding allows for precise customization of the winding pattern and fiber orientation to maximize mechanical properties and performance. Manufacturers can tailor the properties of the resultant composite structure to match particular application needs by carefully modifying the winding parameters, which will increase the structure's strength, stiffness, and longevity.
-
Material Efficiency
Because filament winding precisely controls resin content and fiber placement throughout the fabrication process, it excels at minimizing waste. This careful oversight guarantees the best possible material use, which reduces waste and increases efficiency relative to conventional manufacturing techniques.
-
despite these advantages, filament winding also presents certain limitations:
-
Filament winding is more difficult for small-scale or low-volume production operations to implement because it requires specialized tools and knowledge. Because of the intricacy of the winding process, smaller businesses may find it difficult to hire qualified technicians who understand how to operate and maintain the complex machinery involved.
-
Filament winding is very good at producing cylindrical or tubular parts with high accuracy and efficiency, but it works best with these particular geometries. Other fabrication methods that are better adapted to handle a variety of geometries may be necessary when manufacturing components with complex designs or non-cylindrical shapes.
-
-
conclusion
A high-speed, effective way to create cylindrical or tubular structures out of glass fiber composites with customized properties and little material waste is by filament winding. For industries that need to produce large quantities of consistently high-quality parts, filament winding is still the preferred method even though it requires specialized equipment and expertiseespecially in applications where cylindrical shapes are common.
-
-
Pultrusion
One notable continuous manufacturing process for creating profiles and structural shapes with consistent cross-sections out of glass fiber composites is pultrusion. Examples of these shapes include beams, channels, and rods. The following are the essential steps in this method:
-
Resin Impregnation
After being drawn through a resin bath, continuous glass fiber reinforcements are fully impregnated with resin. In order to achieve uniform mechanical properties throughout the composite structure, it is imperative that the fibers be uniformly saturated with the resin matrix.
-
Heating and Forming
The resin-impregnated fibers then pass through a heated die, where the resin undergoes curing and the composite material takes its final shape. The die imparts the desired cross- sectional profile to the pultruded part, ensuring dimensional accuracy and uniformity along its length.
-
Pultrusion offers several notable advantages
Superior Strength-to-Weight Ratio: Pultruded components have outstanding strength-to-weight ratios, which make them perfect for structural lightweight applications where strength and longevity are crucial. Because of the pultrusion process's efficiency and the inherent strength of glass fiber reinforcements, composite components can withstand significant loads while maintaining their lightweight nature.
Dimensional Stability: The mechanical properties of pultruded parts remain constant throughout their length, exhibiting outstanding dimensional stability and uniformity. Because of their ability to maintain precise tolerances and consistent performance, pultruded components are an excellent choice for applications that demand strict dimensional control and structural integrity.
Automation: Pultrusion is a highly automated process with minimal labor requirements and continuous production. Setting the pultrusion parameters allows the process to operate continuously, producing consistent results without requiring ongoing manual intervention. Compared
-
to conventional fabrication techniques, this automation lowers manufacturing costs and increases production efficiency.
-
-
pultrusion does present certain limitations:
-
Limited to Constant Cross-Sections: Pultrusion is best used to create parts like rods, beams, and channels that have constant cross-sections. This constraint limits the applicability to specific geometries and might require the use of different fabrication methods for components whose cross- sectional profiles vary.
-
High Equipment Cost: The specialized tools needed for pultrusion, such as dies and pultrusion machines, can be costly to buy and maintain. For some manufacturers, especially smaller ones or ones with lower production volumes, the initial investment in pultrusion equipment may be a barrier to entry.
-
-
summary
High-strength, lightweight structural components with outstanding dimensional stability can be produced economically and effectively with pultrusion. Pultruded parts, though restricted to constant cross-sections, are widely used in many industries where cost-effectiveness and performance optimization depend on lightweight, strong materials.
-
-
Autoclave Molding
The best technique for creating high-performance glass fiber composite parts with intricate shapes and precise tolerances is autoclave molding. The following crucial steps are involved in this intricate process:
-
Autoclave molding is the most effective method for producing high-performance glass fiber composite parts with complex shapes and exact tolerances. This complex process involves the following essential steps.
-
Mold Preparation: The prepreg materials are meticulously arranged in a mold according to the intended lay-up order and part geometry. To help with resin flow and part removal after cure, the mold may include features like vacuum ports and release agents.
-
Autoclave Curing: After the mold is ssembled, it is placed in an autoclave to cure under high pressure and temperature. Excellent dimensional accuracy, surface finish, and mechanical properties are produced by the autoclave's combination of heat and pressure, which thoroughly impregnates, consolidates, and cures the composite laminate.
-
Advantages
-
High Quality: Parts made by autoclave molding are recognized for their remarkable mechanical qualities, surface finish, and dimensional accuracy. High-quality composite laminates are produced by precisely controlling the autoclave environment's temperature, pressure, and curing cycles, which guarantees uniform resin distribution and consolidation.
-
Complex Geometries: Autoclave molding is a good method for creating structural parts, aerodynamic components, and other complex shapes because it can easily handle complex part geometries and features. The molding process's flexibility enables the production of parts with exact curves, contours, and details, satisfying the exacting specifications of demanding applications.
-
Tailored Properties: The resin flow, fiber orientation, and laminate thickness can all be precisely controlled during the curing process in an autoclave, which makes it easier to optimize the mechanical properties and performance. Strength, stiffness, and impact resistance are just a few of the attributes that manufacturers can improve in composite laminates to meet the demands of particular applications.
-
-
limitations
-
High Cost: Autoclave molding requires specific tools and equipment, such as autoclaves, which can have a significant initial cost. Furthermore, the upkeep and operation of autoclave facilities may necessitate large investments in personnel, infrastructure, and energy use, raising the total cost of production.
-
Long Cycle Times: An autoclave's curing cycle can take a long time, which could result in longer lead times for production and higher manufacturing costs. The requirement for exact control over temperature and pressure during the curing process could result in longer cycle times, which could affect the efficiency and throughput of production.
-
-
summary
When it comes to manufacturing high-performance composite parts with unmatched quality and accuracy, autoclave molding is the ultimate method. The outstanding qualities and capabilities of autoclave-molded parts make them indispensable for applications requiring the highest levels of performance, dependability, and durability from glass fiber composites, despite their higher costs and longer cycle times.
-
-
-
MECHANICAL PROPERTIES
Renowned for their remarkable mechanical characteristics, glass fiber composites possess tensile strength, flexural strength, and impact resistance. To maximize the performance of composite materials in a variety of applications, it is essential to comprehend these qualities and the variables that affect them. Here, we examine the mechanical characteristics of glass fiber composites and the variables influencing their behavior:
-
Tensile Strength
The maximum stress that a material can bear before failing under tension is known as its tensile strength. Tensile strength in glass fiber composites is impacted by matrix characteristics, volume fraction, and fiber orientation. A crucial factor is fiber orientation: fibers with an orientation parallel to the applied load have a higher load-bearing capacity than those with a direction perpendicular to the load. When there are more fibers in a composite structure, load transfer is improved and tensile strength is generally increased. Furthermore, by altering stress distribution and the interaction between the fibers and matrix, the stiffness and adhesion of the matrix material can have a substantial impact on the tensile strength.
-
Flexural Strength
The greatest stress a material can bear before breaking under bending is measured by its flexural strength, commonly referred to as its bending strength. Because the reinforcing fibers have a high tensile strength and can distribute and withstand bending loads, glass fiber composites have excellent flexural strength. Just like with tensile strength, flexural strength is largely determined by matrix properties, volume fraction, and fiber orientation. Optimizing flexural performance requires proper fiber alignment and distribution because improper fiber alignment or clustering can lead to stress concentrations and weaken the composite structure. Furthermore, flexural strength is determined by the matrix material's stiffness and toughness, which control the composite's resistance to deformation and fracture under bending loads.
-
Impact Resistance
Impact resistance is the capacity of a material to bear high- energy, abrupt impacts without breaking or deforming. Because of the strong and durable reinforcing fibers and their capacity to release energy through matrix deformation and fiber pull-out, glass fiber composites are well known for their exceptional impact resistance. By influencing the distribution and absorption of impact energy, variables like fiber orientation, volume fraction, and matrix characteristics affect a composite's ability to withstand impact. Because they stop delamination and fiber breakage under impact loading, proper fiber alignment and interfacial bonding are essential for improving impact resistance. Moreover, the composite structure's overall impact resistance is improved by the toughness and ductility of the matrix material, which are crucial in absorbing and dissipating impact energy.
5.4. summary
Fiber orientation, volume fraction, and matrix characteristics are some of the variables that affect the mechanical properties of glass fiber composites, such as tensile strength, flexural strength, and impact resistance. Manufacturers can adjust the mechanical properties of glass fiber composites to meet the unique needs of a variety of applications, from the automotive and aerospace to the marine and construction industries, by comprehending these factors and optimizing composite design and processing parameters.
-
-
THERMAL, ELECTRICAL, AND CHEMICAL PROPERTIES
The diverse range of thermal, electrical, and chemical properties exhibited by glass fiber composites renders them appropriate for a multitude of industrial applications. It's critical to comprehend these attributes and how they depend on elements like fiber type, matrix composition, and environmental circumstances when choosing the right composite material for a given set of engineering needs. The thermal stability, electrical conductivity, and chemical resistance of glass fiber composites are examined here:
-
Thermal Stability
The term "thermal stability" describes a material's capacity to tolerate high temperatures without experiencing appreciable deterioration or loss of mechanical characteristics. Because glass fibers have a high melting point and are heat resistant, glass fiber composites often show excellent thermal stability. However, a number of variables, including the type of fiber, the resin matrix, and the processing conditions, can affect how thermally stable a composite is. Some glass fiber types, like S-Glass, are more thermally stable than regular E-Glass fibers, which makes them appropriate for high-temperature applications. Some glass fiber varieties, like S-Glass, are more thermally stable than regular E-Glass fibers, which makes them appropriate for high-temperature applications. Thermosetting resin matrices, like epoxy or phenolic resins, offer superior thermal stability in comparson to thermoplastic matrices. The required thermal stability of glass fiber composites can be ensured for particular applications, such as automotive parts, aerospace components, and thermal insulation systems, by carefully selecting the fiber type and matrix material and paying close attention to processing parameters.
-
Electrical Conductivity
The electrical conductivity of glass fiber composites is primarily influenced by the type of glass fibers and the matrix material used in their fabrication. Because glass is a non- conductive material, glass fibers themselves are electrically insulating. Thus, glass fiber composites have a generally low electrical conductivity. Nonetheless, the composite may acquire varied levels of electrical conductivity if conductive fillers or additives are present in the matrix material. The electrical conductivity of glass fiber composites, for instance, can be increased by adding carbon fibers or conductive fillers like metallic particles or carbon nanotubes to the resin matrix.
These conductive additives fit the bill for applications requiring electromagnetic shielding, static dissipation, or electrical grounding because they open up channels for electrical conduction within the composite.
-
Chemical Resistance
The term "chemical resistance" describes a material's capacity to endure exposure to acids, solvents, and corrosive substances without degrading or coming under chemical attack. Because thermosetting resin matrices are resistant to chemical attack and glass fibers are inert, glass fiber composites are well known for their exceptional chemical resistance. Particularly E-Glass fibers show good chemical resistance to a variety of corrosive substances, which makes them appropriate for use in wastewater treatment, chemical processing, and marine environments. However, elements like fiber type, resin matrix, and environmental conditions can have an impact on how chemically resistant glass fiber composites are. A few strong chemicals or solvents have the potential to weaken the resin matrix or induce delamination in the composite structure, which could result in diminished mechanical qualities and impaired functionality. Assuring the long-term chemical resistance of glass fiber composites in demanding applications requires careful consideration of environmental exposure conditions, resin matrix, and protective coating selection.
6.4. summary
Crucial characteristics of glass fiber composites that affect their suitability for different industrial applications are their chemical resistance, electrical conductivity, and thermal stability. Glass fiber composites can be customized by manufacturers to meet the unique performance requirements of a variety of applications, from structural components to electrical insulation and chemical-resistant structures, by knowing the factors that influence these properties and choosing the right fiber type, matrix material, and processing conditions.
-
-
APPLICATION
Glass fiber composites' remarkable mechanical qualities, adaptability, and lightweight design have transformed a number of industries. This section examines the diverse applications of glass fiber composites in the construction, automotive, marine, aerospace, and sporting goods industries, highlighting their adaptability and benefits in terms of performance:
-
Aerospace
Glass fiber composites are essential to the aerospace sector because of their excellent stiffness, high strength-to-weight ratio, and resistance to fatigue. The fuselages, wings, empennage parts, and interior panels of aircraft are among the many structures made of these materials. For instance, carbon fiber reinforced composites are used in vital aerospace parts
like airplane wings and fuselages where weight reduction is crucial. Additionally, glass fiber composites find application in unmanned aerial vehicles (UAVs), rocket fairings, satellite components, and other aerospace applications where their robust and lightweight design enhances performance and reduces fuel consumption.
Fig 10: Components made of FRPs used in airbus
-
Automotive
Glass fiber composites are used in the automotive industry to reduce weight, increase fuel economy, and improve crashworthiness of vehicles. Body panels, chassis reinforcements, interior trims, and structural elements are just a few of the automotive components that use these materials. Because of their improved strength and stiffness, carbon fiber reinforced composites are being used in high-performance automobiles more and more. To lighten and increase the range of batteries in electric and hybrid vehicles, glass fiber composites are also utilized. Additionally, glass fiber composites provide corrosion resistance, which helps car parts last longer and be more durable in challenging operating conditions.
Fig 11: hybrid vehicles
-
Marine
Glass fiber composites are widely used in the marine industry to make masts, decks, boat hulls, and other structural parts. Because of their exceptional strength, resistance to corrosion, and dimensional stability, these materials are perfect for use in maritime environments. The exceptional water resistance and durability of glass fiber composites based on epoxy resin make them especially popular in maritime settings. Because carbon fiber reinforced composites are stiff and lightweight, they improve speed and maneuverability and are used in luxury and high-performance racing boats. In marine infrastructure, such as docks, bridges, and offshore platforms, glass fiber composites are also used because of their corrosion resistance and durability.
Fig 12: Marine ship
-
Construction
Glass fiber composites are employed in the construction sector for many different purposes, such as building facades, cladding panels, roofing materials, reinforcement bars, and structural elements. Because of their great strength, resilience to weather, and durability, these materials can be used in both indoor and outdoor settings. Because of their lightweight, ease of installation, and resistance to corrosion, glass fiber reinforced polymer (GFRP) composites are gradually taking the place of more conventional building materials like steel and concrete. For instance, to stop corrosion and increase the lifespan of infrastructure and buildings, GFRP rebar is used in concrete structures.
Fig 13: glass fiber in construction
-
Sporting Goods
Glass fiber composites are employed in the construction sector for many different purposes, such as building facades, cladding panels, roofing materials, reinforcement bars, and structural elements. Because of their great strength, resilience to weather, and durability, these materials can be used in both indoor and outdoor settings. Because of their lightweight, ease of installation, and resistance to corrosion, glass fiber reinforced polymer (GFRP) composites are gradually taking the place of more conventional building materials like steel and concrete. For instance, to stop corrosion and increase the lifespan of infrastructure and buildings, GFRP rebar is used in concrete structures.
7.6. summary
Glass fiber composites are used in many different sectors of the economy, including construction, sporting goods, marine, and automotive. They are essential materials for producing a wide range of products due to their lightweight design, high strength, durability, and resistance to corrosion. This helps to promote sustainability, innovation, and improved performance across a number of industries.
-
-
CHALLENGES AND OPPORTUNITIES
Although there are many benefits to glass fiber composites in many different industries, there are certain obstacles that must be overcome in order to move the technology forward. This section looks at the main obstacles that the glass fiber composites industry must overcome as well as the chances for advancement and expansion they offer:
-
Recyclability and Sustainability
Glass fiber composites' limited capacity for recycling and their environmental impact present one of their main problems. Because of the bonding between the fibers and resin matrices in traditional composite materials, such as glass fiber composites, it is challenging to recycle them. End- of-life disposal therefore poses a number of difficulties and raises questions about waste management and the environment. To tackle this obstacle, inventive recycling techniques and environmentally friendly production methods must be developed. To recover valuable materials from composite waste streams and lessen their environmental impact, researchers are investigating a variety of strategies, including mechanical recycling, chemical recycling, and pyrolysis. Additionally, there are chances to improve sustainability and lessen dependency on materials derived from fossil fuels by utilizing natural fibers and bio-based resins in composite manufacturing.
-
Cost-Effectiveness
Finding cost-effective solutions without sacrificing performance is a problem in the field of glass fiber composites. Although glass fiber composites have many benefits over traditional materials like steel and aluminum, such as good strength-to-weight ratios, lightweight designs, and resistance to corrosion, the initial cost of materials and manufacturing processes can be somewhat high. Manufacturers must streamline their production procedures, cut down on material waste, and increase output to reach economies of scale in order to overcome this difficulty. Automated lay-up, filament winding, and additive manufacturing are examples of advanced manufacturing techniques that can streamline production and save costs without sacrificing or lowering product quality. Furthermore, through pooling resources, transferring technology, and collaborating on research and development, strategic alliances and supply chain collaboration can help reduce costs.
-
Performance Optimization
Scientists and engineers are always trying to find ways to improve the performance of glass fiber composite materials. Despite the great mechanical properties of glass fiber composites, careful design, material selection, and manufacturing optimization are needed to achieve reliable and consistent performance in a variety of uses. Composite materials' mechanical, thermal, and chemical properties can be influenced by a variety of factors, including fiber orientation, resin matrix formulation, processing conditions, and environmental exposure. A multidisciplinary strategy
integrating mechanical engineering, materials science, and manufacturing technologies is needed to address these issues. Experiments validated by modeling and simulation combined with advanced modeling techniques can yield important insights into how composite materials behave in various environments and loading situations. The performance and adaptability of glass fiber composites can also be further improved for a variety of applications through continued research into innovative fiber reinforcements, resin systems, and composite architectures.
8.4. summary
Researchers, manufacturers, and policymakers must work together to find creative solutions to address the problems of recyclability, sustainability, cost-effectiveness, and performance optimization in the field of glass fiber composites. The glass fiber composites industry can overcome these obstacles and open up new avenues for growth, innovation, and sustainability in the years to come by utilizing developments in materials science, manufacturing technologies, and recycling procedures.
-
-
CONCLUSION
The present thorough review has yielded significant insights regarding the developments and uses of glass fiber composite materials. We have discussed the basic characteristics, manufacturing processes, mechanical, thermal, electrical, and chemical properties, as well as the wide range of applications in numerous industries, throughout this paper. Because of their extraordinary mechanical qualities, low weight, and adaptability, glass fiber composites have become essential materials in a variety of industries, including construction, automotive, marine, aerospace, and sporting goods. Glass fiber composites have shown their ability to improve performance, durability, and sustainability across a wide range of applications, from aircraft components to automotive body panels, boat hulls to building facades.
Researchers, manufacturers, and policymakers must work together to address issues like recyclability, sustainability, cost-effectiveness, and performance optimization. The development of glass fiber composites will not be possible without cutting-edge material optimization techniques, inventive recycling technologies, environmentally friendly production procedures, and economical production techniques.
Given the aforementioned obstacles and prospects, it is apparent that further investigation and creativity are essential to realizing the complete capabilities of glass fiber composite materials. We can open up new avenues for the development and use of glass fiber composites and pave the path for improved performance, sustainability, and competitiveness in the global market by utilizing developments in materials science, manufacturing technologies, and interdisciplinary collaborations.
Finally, for those looking for a thorough understanding of glass fiber composite materials and their possible uses, this review paper is an invaluable tool for researchers, engineers, and practitioners. In order to advance progress and prosperity in the years to come, we hope that the insights offered here
will stimulate additional research, creativity, and cooperation in the field of glass fiber composites.
REFERENCES
-
Dini, A., Ripeanu, R. G., Ilinc, C. N., Cursaru, D., Matei, D., Naim, R. I., Tnase, M., & Portoaca, A. I. (2024). Advancements in Fiber-Reinforced Polymer Composites: A Comprehensive Analysis. Polymers, 16(1), 2.
https://doi.org/10.3390/polym16010002.
-
Singh, J., Kumar, M., Kumar, S., & Mohapatra, S. K. (2017). Properties of Glass-Fiber Hybrid Composites: A Review. Volume 56, 2017 – Issue 5, 455-469.
https://doi.org/10.1080/03602559.2016.1233271.
-
Kulhan, T., Kamboj, A., Gupta, N. K., & Somani, N. (2022). Fabrication methods of glass fiber compositesa review. Functional Composites and Structures, 4(2). https://doi.org/10.1088/2631-6331/ac6411.
-
Kiron, M. I. (2012). Glass Fiber Composites: Properties, Manufacturing, and Applications. The Fracture and Strength of Glass, Volume 3, Issue 2, 122-136.
https://doi.org/10.1111/j.2041-1294.2012.00090.x
-
Bilal, M. (2022). Composite Formation by Hand-Layup Process. Engineering and Applied Sciences.
-
Kim, S.-Y., Shim, C. S., Sturtevant, C., Kim, D. (Dae-Wook), & Song, H. C. (2014). Mechanical properties and production quality of hand-layup and vacuum infusion processed hybrid composite materials for GFRP marine structures. International Journal of Naval Architecture and Ocean Engineering, 6(3), 723- 736. https://doi.org/10.2478/IJNAOE-2013-0208.
-
Raji, M., & Abou el kacem Qaiss. (2020). Modern Manufacturing Processes.
-
Ou, Y., Zhu, D., Zhang, H., Huang, L., Yao, Y., Li, G., & Mobasher, B. (2016). Mechanical Characterization of the Tensile Properties of Glass Fiber and Its Reinforced Polymer (GFRP) Composite under Varying Strain Rates and Temperatures. Polymers, 8(5), 196. https://doi.org/10.390/polym8050196.
-
Farzana, M., Haque, M. M., Sonali, S. M., Mollah, M. Z. I.,
Amin, M. A., Khan, S. A., Islam, F., & Khan, R. A. (2023). Thermo-Mechanical Properties and Applications of Glass Fiber Reinforced Polymer Composites. Modern Concepts in Material Science, ISSN: 2692-5397. DOI: 10.33552/MCMS.2023.05.000614.
-
Harle, S. M. (2024). Durability and long-term performance of fiber reinforced polymer (FRP) composites: A review. Structures, Volume 60, 105881.
https://doi.org/10.1016/j.istruc.2024.105881.
-
Sawpan, M. A., & Beg, M. D. H. (2024). Long-term residual properties and durability of glass fiber reinforced polymer composite exposed to alkaline
solution and natural weather for a decade. Polymer Composite, Volume 45, Issue 2, 1096-1106.
https://doi.org/10.1002/pc.27838.
-
Harle, S. M. (2024). Durability and long-term performance of fiber reinforced polymer (FRP) composites: A review. Structures, Volume 60, 105881.
https://doi.org/10.1016/j.istruc.2024.105881.
-
Harle, S. M. (2024). Durability and long-term performance of fiber reinforced polymer (FRP) composites: A review. Structures, Volume 60, 105881.
https://doi.org/10.1016/j.istruc.2024.105881.
-
Hariz, H. M., Sapuan, S. M., & Ilyas, R. A. (2021). Advanced composite in aerospace application: A review on future aspects of fiber-reinforced polymer (FRP) in the aerospace industry. In Seminar on Advanced Bio- and Mineral based Natural Fibre Composites (SBMC2021).