
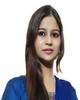
- Open Access
- Authors : Shaik Mehamuda Afsari
- Paper ID : IJERTV10IS100021
- Volume & Issue : Volume 10, Issue 10 (October 2021)
- Published (First Online): 22-10-2021
- ISSN (Online) : 2278-0181
- Publisher Name : IJERT
- License:
This work is licensed under a Creative Commons Attribution 4.0 International License
Evaluation of Steerability and Handling Characteristics of An Automotive Vehicle using Multi Body Dynamics (MBD) Simulation
Shaik Mehamuda Afsari
Lead Engineer,
HCL Technologies, Bangalore, India
Abstract:- In this research work, mechanical behavior of steerability and handling characteristics of the vehicle have become major aspects. Providing comfort to the driver by reducing steering effort without any compromise in steerability and handling of the vehicle is a major concern for automakers. Evaluating handling and steering characteristics of a vehicle in a virtual environment with the help of multi-body system packages saves product development time and cost. The main intention is to improve the steerability and handling of the vehicle by avoiding the steering pull and wheel wandering problems.
Keywords Vehicle Dynamics, Steering Geometry, Steering Drift, Vehicle Pull
1. INTRODUCTION
-
Introduction to Vehicle Dynamics of a SUV
Vehicle dynamics is the study concerned with the dynamics of vehicles mainly on the ground surface. Vehicle dynamics is a part of engineering primarily based on classical mechanics. Vehicle dynamics is determined by different kinds of forces, such as aerodynamic force, gravitational force and forces coming from the tires, acting on the vehicle. Detailed study of all these forces imposed and their influence on stability and handling of the vehicle are part of vehicle dynamics. In order to study the parameters contributing to handling and stability of the vehicle, the approach used is to first create an approximate vehicle model and then later in virtual simulated through different straight lines courses and related conditions environment.
Vehicle steering response that plays a key role both in manoeuvrability and vehicle handling, is one of the major feature in vehicle dynamics. The two major factors that aid in understanding the vehicle steering are Wheel Geometry and Tire behaviour. Tire is the primary source of various forces and moments that administer the control and provide stability to the vehicle. Interaction between tires and road generates various forces like tractive, braking and other cornering forces for controlled manoeuvring. Hence, proper alignment of the wheels help in achieving better grip and handling of the vehicle.
-
MULTIBODY SYSTEMS APPROACH TO VEHICLE DYNAMICS
Vehicle Dynamics texts by and Milliken and Gillespie are great references for someone looking for a brief introduction to this subject. A great reference on vehicle dynamics modelling and multibody systems (MBS) approach was presented by Blundell
and Harty. They first introduce the theory on kinematics and dynamics of rigid bodies to get a better understanding before dwelling deep into the MBS simulation software that is related to vehicle dynamics design. The text gives common information related to most multibody dynamics software, but uses Adams for specific examples and demonstrations.
Many concepts like parts, joints, degrees of freedom, forces and bushings are also included for building MBS models. A brief Introductions to the concepts of solving linear and nonlinear equations are also covered.
Suspension systems that are discussed by elevating the need for such systems to allow for wheel load variations, body isolation, handling control, etc. Different styles of suspension systems are described through screen captures of templates in Adams-Car software. The quarter vehicle modelling approach, covered briefly the Suspension analysis, introducing how to concluded suspension characteristics, and suspension calculations. The chapter finally concludes with several case studies using Adams-Car simulations in order to demonstrate the different theories that are available in the field of Vehicle Dynamics.
In similar fashion, tire modeling and full-vehicle assemblies are covered as well. Understanding of simulation outputs are also discussed intricately, and it finally finalizes with a chapter that is related to active vehicle systems such as brake-based systems brakes, active dampers, and active torque distribution
.
The text could theoretically be used in designing a Vehicle Dynamics course around MBS modeling, however, the text does not include problems to be worked by students similar to those in the Gillespie and MillikeSntex.
2.1 Wheel Geometry Parameters Affecting Vehicle Steering
Wheel geometry is an important aspect which contributes a lot to the steerability of a vehicle. Even a slightest misalignment creates problems like steering pull and vehicle drift. The wheel geometry parameters that affect the steerability of the vehicle are camber, caster, Steering Axis Inclination (SAI), scrub radius and toe.
Caster is the angle that is formed between the steering axis and vertical axis when observing the vehicle normal to one of the sides. Positive caster means there is a tilt towards the rear
of the vehicle in the steering axis. Camber is the angle that is formed between the vertical axis and a line parallel to the wheel when viewed on its vertical axis. Negative camber means there is an inward tilt of the top of the wheel towards the vehicle. Toe that is denoted as angle between the longitudinal axis of the wheel and a line that is parallel to the longitudinal sides of the wheel. Negative toe (or Toe In) means there is a slight inward tilt in the tires towards the centreline of the vehicle.
Positive caster and negative camber and toe are preferred for predictable behavior both during straight line motion and in cornering. Negative camber aids the outside tire in producing higher lateral forces during cornering, and negative toe adds stability since suspension components are much stronger in compression than in tension. If positive toe were used, the tires would generate forces away from the center of the vehicle during straight forward motion, adding unwanted stresses and possible steering instability. Suspension systems must control these parameters during deflection and rebound to preserve vehicle stability over obstacles or rough terrain.
Proper control of any vehicle requires a improved steering subsystem. A proper steering system must link the front two wheels, preserve a proper amount of toe, and produce correct steer angles when corning. Gillespie illustrates the key geometry of a turning vehicle, as depicted.
As the vehicle completes a turning it should be noted that, the inside steer angle should be larger than the steer angle outside to follow the turn radius without resulting in the excessive side slip of the tire and a premature wear of the tire. Better geometry of steering provides better feedback of steering to the the driver, where the steering torque rises the steer angle. A parallel nature of front wheels during a turn may cause an initial increase in steering torque before dropping off and possible becoming negative with the increase of steer angles. Further steer torque which is negative would cause an automatic steer into a turn, creating a loss of control i.e. is dangerous.
There are different styles of steering systems that exist in this field, but the two most common steering systems that are very popular are Pitman Arm and the other one is Rack-and-Pinion designs. Pitman arms, as shown in Fig 3-9, are generally used in heavy trucks and also in the pickups with straight axles, while Rack-and-Pinion systems are used everywhere else. Both designs can be equipped with either hydraulic or more recently offered electric power assist systems.
Steering box transfers driver inputs to the Pitman arm through an arc to move te draglink, which is attached/entangled near one end of the tie rod. Each end of the tie rod is entangled to the knuckles to control steering geometry. A steering stabilizer is typically added in larger pickups for added control in the system. Since the steering box has the capability to be mounted to the frame above the axle, the Pitman design lends itself well to use in straight front axle suspensions. Conversely, the rack- and-pinion design utilizes a central rack that must be mounted
to a subframe in line with the tie rods and much closer to the ground.
Steering inputs turn a pinion gear against the steering rack which moves a rack left or right. Tie rods connect to the rack via ball joints and transfer steering forces to the knuckles. Since sub frames required to mount the lower control arms provide appropriate mounting locations for the fixed rack housing, rack-and-pinion steering designs are mainly used along with independent suspensions. The major components of the Adams-Car rack-and-pinion steering system are illustrated.
Nearly all normal driving forces applied to a vehicle, with only the exception of aerodynamic drag, are generated by the interaction between the tire contact patch and the ground. Thus, wheels and tires directly affect handling, ride, braking, and accelerating characteristics.
Increase in lateral slip angle results in creation of Tire lateral forces, as depicted in Figure 3-12. At small slip angles, the relationship between slip angle and the lateral force is linear, and is characterized by the cornering stiffness, C, i.e mainly the slope of the lateral force curve vs. slip angle at = 0 (or small slip angles). As shown in Figure 3-12, a negative slip angle produces a positive lateral force (to the right). Cornering stiffness is defined by the negative of the lateral force slope, based on the SAE convention, thus C is positive.
The greater impact on the lateral force is caused by the normal loads vs. slip angle behavior of tires, so it is important to also introduce the cornering coefficient, CC, which is the cornering stiffness divided by the normal tire load. In general, the cornering coefficient has an inverse association with load (Fz). Typical values for CC at 100% rated load is around 0.2 (lby-lbz/deg ).
Making up the largest portion of the tire, the tread is designed to influenceively retain grip with the ground under varying situations. Much design work goes into creating tread patterns specialized to shed water, grip on mud, ice, or snow, or maximize adhesion to dry roads. The strength of tires is increased by the steel belts that are moulded into the tire beneath the tread. The sidewall is aptly named as it makes up the distance between the rim and the tread. The material here can be made softer for better ride quality, or stiffer for less lateral distortion and better handling. Strength and Flexibility is provided by the Cords, typically made of nylon or steel, that are moulded deep into the sidewall. A steel-cable-reinforced bead secures and seals the tire to the wheel. Wheels (rims) are generally made of either steel or aluminium. They come in different variety of sizes for various applications. Lug nuts hold the wheel to the knuckle, spindle, or hub, depending on the application.
Making up the largest portion of the tire, the tread is designed to influenceively retain grip with the ground under varying situations. Much design work goes into creating tread patterns specialized to shed water, grip into the tire beneath the tread. The sidewall is aptly named as it makes up the distance between the rim and the tread.
The material here can be made softer for better ride quality, or stiffer for less lateral distortion and better handling. Strength and Flexibility is provided by the on mud, ice, or snow, or maximize adhesion to dry roads. The strength of tires is increased by the steel belts that are moulded Cords, typically made of nylon or steel, that are moulded deep into the sidewall. A steel-cable-reinforced bead secures and seals the tire to the wheel. Wheels (rims) are generally made of either steel or aluminium. They come in different variety of sizes for various applications. Lug nuts hold the wheel to the knuckle, spindle, or hub, depending on the application.
-
Creation of Subsystems
A subsystem is a mechanical model which references the template and tailors it by supplying the parameters, including properties of the components like spring, tire etc. Subsystems also allow new point positions can be defined. The respective templates from the database were imported and all the subsystems required for the SUV were created.
-
Full-Vehicle Assembly
To create the full vehicle model, the subsystems were imported in a single environment and assembled properly.
-
-
PROBLEM DEFINITION
Based on the literature survey, various problems related to
-
Steering subsystem
-
Front wheel subsystem
steering, like steerability under limit handling condition, Rear wheel subsystem steering drift because of improper alignment, have be Body subsystem identified. The work reported in this paper concerns the effect
of different wheel parameters on steerability and development Brake subsystem
of a computer model and carrying out virtual simulations to Powertrain subsystem
study the effect of different wheel geometry parameters on vehicle steering.
-
-
MODELING OF SUV IN ADAMS/CAR
To study the behaviour of an SUV for different wheel geometry parameter, a multi-body model of Honda-CRV, the vehicle selected for this study, was built in ADAMS/CAR. Different sub-systems of an SUV, such as suspension system, steering system, wheels, brakes and chassis were built according to the specification and assembled together to carry out the simulations.
Three major steps involved in the construction of multi-
-
RESULTS AND DISCUSSIONS
The SUV modelled in ADAMS/CAR was used to study the steering wheel returnability, steering effort and other steering related parameters. Using this model, maneuvres for different values of wheel geometry parameters, were simulated.
-
SINGLE LANE CHANGE (SLC) ANALYSIS:
In SLC, full vehicle analysis was carried out to study the impact of different wheel geometry parameters mainly Steering Angle Inclination ( SAI), caster angle, and Toe angle, its influences on
body model of SUV are
-
Creation of templates
-
Creation of sub-systems
-
Creation of full vehicle assembly
-
4.1 Creation of Templates
In the simulation software, a template is the basic level multi-body model that contains the geometry and topological data. Template defines the geometric parts, joints (to enable the connection between different geometric parts), forces and other modelling elements that constitute an aggregate sub-assembly of a vehicle. It also includes how the parts connect together through the joints and how the force will be transmitted from one part to another and so on. The template also contains communicators to achieve the communication between different sub-assemblies of the vehicle.
To create the simulation model of the selected SUV, the coordinates of hard points were changed to match those in the selected vehicle. Similarly, the templates of steering, front and rear suspension, front and rear wheels, powertrain and brakes were modified according to the specification of selected SUV and saved in the database.
-
steering effort, (pinion torque)
-
steering wheel returnability and(aligning torque)
-
Steering assistance angle(steering Angle)
In single Lane Change full vehicle simulation test was carried out, vehicle speed was kept at 70 kmph and steering angle of 15 degrees was given as an input to steering wheel for lane change with vehicle speed of 80 km/h. For path change, steering angle of 1 ° was given as an input to steering wheel. Simulations were carried out to recognise the effect on handling behaviour, steering effort and steering wheel returnability by changing the different wheel geometry parameters.
5.2. Caster Angles influence on Vehicle Behaviour
Figure 2 depicts the difference of pinion torque acting at the pinion and pinion of rack steering system for numerous values of caster angles. The caster angle was varied from – 5° to +5° to observe its control on the change of steering effort. It can be concluded that the torque acting at the pinion, i.e a amount of steering effort, is directly proportional to the caster angle and increases with the caster angle.
Fig. 2 Time variation of pinion torque for different caster angles
A completely opposite movement is observed for the aligning torque. Aligning torque, is a instant produced at the boundary of the road and tire, have a tendency to align the wheels back to the conventional ahead position without any major determination from the driver. It is inversely proportional to the caster angle and decreases as the caster value increases.
For caster angles that are negative, the aligning torque, thrusts the wheels beyond away from it, instead of annoying to push the wheels to straight ahead position, as this dislocates the wheel path, giving rise to wheel wandering problems. Therefore, it is always desired to have positive caster angles to ignore wheels going beyond away from it.
Fig. 3 Time variation of aligning torque for different caster angles
Figure 4 depicts the difference of steering assistance angle, which is a amount of return ability of steering wheel back to its original position after the track changeover, with numerous caster angle. After changing the path, as the vehicle starts moving in the straight lane, the steering angle residues constant.
Fig. 4 Time variation of steering assistance angle for different caster angles
Fig. 5 Time variation of steering assistance angle for different caster angles
-
Effect of SAI Angles on Vehicle Behaviour
Figure 6 depicts the difference of torque acting at the pinion for numerous values of Steering angle inclination angles in an SLC manoeuvre. When SAI angle is varied and the values are plotted across time. The results can be concluded that drivers effort is decreased with increasing Steering Angle Inclination.
Fig. 6 Pinion Torque for different SAI angles vs Time
Fig. 7 Aligning Torque for different SAI angles vs Time.
Fig. 8 Steering Assistance Angle for different SAI angles vs Time
Figure 7 depicts the difference of aligning torque for various SAI angles. The aligning torque about the steering axis is lower for 15° SAI the angle and Rises as the SAI angle decreases. This type of difference is because increase in SAI angle r e s u l t s i n t h e i n c r e a s e o f the lateral forces at tires. With moment arm residual the same, it results in increase in aligning torque. Higher aligning torque increases steering return ability and results in wheels to align to straight forward position faster.
Figure 8 depicts the difference of steering assistance angle, which is a amount of return ability of steering wheel back to its original position after the path changeover, with numerous SAI angles for an SLC manoeuvre. After fluctuating the path, as the vehicle starts affecting in the straight path, the steering angle remains constant.
Details of the difference in the enclosed area is shown in Fig. 9. There, it can be seen that a vehicle with SAI angle of 8° returns back to the initial position slower than vehicles with larger SAI angle. This observation validates the difference of self-aligning torque shown in Fig.7.
In order to improved recognize the movement there is another way to understand this result and it is as follows. SAI angle effects in the front end of the car to increase as the wheels are steered. This stimulating results gives better steering return ability. Larger the SAI angle, more is the lift, and more is the self-centring influence, as seen from Figure 9.
Fig. 9 Steering assistance angle for different SAI angles vs Time
-
Toe Angles Influence on Vehicle Behaviour
Figure 10 depicts the lateral forces that are acting on the tires for numerous toe-in angles during SLC manoeuvre. In this case, lateral force is directly proportional to toe- in angles but the range of difference of the force decreases.
However, with increasing steering response comes the propensity of the vehicle to enter a turn. This concessions the straight line immovability of the vehicle. So, even though non-zero toe-in vehicles have steering reaction lower to zero toe-in vehicles, some toe-in must be kept to confirm straight line stability.
6.1 Constant Radius cornering (CRC) Simulation
6.1.1 Camber Angles Influence on Vehicle Behaviour CRC (Constant Radius Cornering) simulations, for different camber angles, were carried out in order to study the influence of camber thrust and slip angles on handling behaviour of a vehicle and wear and tear of the tire. For this study, vehicle was travelling at a speed 20 km/h initially and progressively accelerating to a speed 80 km/h on round test track of 3.5 m radius and was simulated. The camber angles were varied from (0° to ±4°) in steps of ±1°.
Figure 13 depicts the distribution and difference of lateral forces in CRC test for various positive camber angles. Lateral forces are like inverse proportional relationship and decrease as the camber angle increases because of higher camber thrust produced by the camber angles which are positive.
Fig. 13 Tire Lateral Force for positive camber angles vs Time
Reduction in the net lateral force at the tires generally increases vehicles like hood to understeer. And in order to reduce this behaviour, lower positive camber should be used so that vehicle doesnt understeer.
Fig. 15 Later Force vs Slip Angle for various negative camber values
Figure 15 depicts the difference of lateral force in direct relative with slip angle for numerous values of camber
angles in a CRC test simulation. The highest lateral force increases as the camber value increases from negative to zero a n d t h e n to positive. From Figure. 15, it is also clear that the slip angle produced by positive camber is maximum and decreases as camber reduces to zero and then finally goes to negative. This describes why wheels with positive cambers wear/tear out as soon as possible. Generally there is a preference for negative camber as it provides or ensuresbetter cornering and manoeuvrability and also consequences in less slip and tire wear.
-
Study the Effect Scrub Radius by Simulation of Brake-in-turn Analysis
In this analysis, the vehicle is made to run with lateral acceleration of 0.30 g with scrub radius of 30 g around the path then applied brakes. Through brakes, 3g deceleration was noticed to the wheels to stop the vehicle Fig 18 portrays the plot of time difference of steering angle for three different, positive, zero and negative, values of scrub radii. The steering input used is to sanctuary the vehicle on course on road after the brakes are functional.
Fig. 19 steering assistance angle vs Time for different Scrub radii
To offer more info of the steering input, enflamed view of the enclosed portion in Figure 18 is shown in Figure.19. It depicts that when scrub radius is positive, maximum/highest steering input is preferred to keep the vehicle on course. This effort is less for zero and negative scrub radii, but only slightly. This means the unbalanced steering torque created is less for the negative scrub radius during braking. Hence, the steering input given by the driver to preserve the vehicle on desired path is also less. Therefore, negative scrub radius is preferable. Though the zero scrub radius produces least steering disturbance, it is not preferred because the driver will not have the steering feel
CONCLUSIONS
-
Negative caster angle diminishes the effort of the steering due to the lack of adequate aligning torque, However it results in the wandering problem of the wheel
-
Larger Steering Axis Inclination (SAI) angle rises the steering wheel return ability and in addition it also diminishes the overall steering effort
-
Positive camber angle lessens the overall lateral force i.e. the net force produced in the tires due to the counter acting thrust of camber and hence enriches the tendency of a vehicle to demonstrate understeer characteristics.
-
Negative camber angle results in increased cumulative lateral force i.e. net force at the tires, the camber thrust that acts in the direction similar to the lateral force in the tire. Therefore, the negative angle of the camber enriches the vehicle handling behaviour and facilitates sharp cornering of the vehicle
-
Increase in the angle of Toe-in is directly proportional to the straight-line stability i.e. Toe-in rises results in enhanced straight line stabilization, but it results in lack of proper sharp cornering ability.
-
Increase in the angle of Toe-out is directly proportional to the cornerabilty of the vehicle i.e. Toe-out increase results in enhances cornerability of the vehicle but results in bad straight line stability.
-
Even though zero radius of the scrub permanently removes the production of unbalanced torque of steering, it is generally not preferred. The feel of the steering will vanish if there is zero scrub radius.
-
Scrub radius with negative value generates less disturbance in the steering and hence it results in greater improvement in the stabilising influence.
REFERENCES
-
Milliken, F.W. and Milliken, D.L., Race Car Vehicle Dynamics
-
Fundamentals of Vehicle Dynamics, Thomas Gillespie.
-
Blundel, M. and Harty, D., The Multibody Systems Approach
-
Finite Element Model of Chevy Silverado, Model Year 2007,
Version2, FHWA/NHSTA National Crash Analysis Center, 2009
-
< http://www.ncac.gwu.edu/vml/archive/ncac/vehicle/silverado- v2.pdf>
-
Cosin Scientific Software, <http://www.cosin.eu/prod_FTire> accessed October 2012.
-
Jayakumar, P., Alanoly, J., and Johnson, R., "Three-Link Leaf-Spring Model for Road Loads," SAE Technical Paper 2005-01-0625, 2005, doi:10.4271/2005-01-0625.
-
Deakin, A., Crolla, D., Ramirez, J., and Hanley, R., The Influence of Chassis Stiffness on Race Car Handling Balance, SAE Technical
Results generated from the simulation of SUV with various values of parameters of wheel geometry the following insights are drawn
-
-
Increment of positive caster angle enhances the mechanical trail, which further rises the self-aligning torque that improves/enhances the steering wheel return ability. Since the self-aligning torque acts in an opposite direction to the torque of the steering, the effort of the driver rises in managing the steering.
Paper 200-01-3554, 2000, doi:10.4271/2000-01-3554.
-
Mohan, P., Marzougui, D., Arispe, E., and Story, C., Component and Full-Scale Tests of the 2007 Chevy Silverado Suspension System, FHWA/NHSTA National Crash Analysis Center Report, July 2009.
-
MD R2 Adams-Car: ADM740 Course Notes, MSC.Software Corp., Santa Ana, CA, June 2007.
-
MSC.Software Case Studies,
-
<http://www.mscsoftware.com/Solutions/Success- Stories/?tid=2&apid=&inid=&pid=3&lid=>, accessed November 2012.