
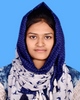
- Open Access
- Authors : Ameena A , Hazni Nizam
- Paper ID : IJERTV10IS060112
- Volume & Issue : Volume 10, Issue 06 (June 2021)
- Published (First Online): 12-06-2021
- ISSN (Online) : 2278-0181
- Publisher Name : IJERT
- License:
This work is licensed under a Creative Commons Attribution 4.0 International License
Respone Reduction of Highrise Buildings using Friction Dampers
Ameena A
-
ech in Structural Engineering Dept. of Civil Engineering
Younus College of Engineering and Technology Kollam, India
Smt. Hazni Nizam
Assistant Professor, Dept of Civil Engineering Younus College of Engineering and Technology Kollam, India
Abstract The present scenario in the construction industry demands lighter and taller structures having high strength and maximum flexibility. This is facilitated by the advancements in the construction technology and material science. From the serviceability point of view, the increase in failure possibly provides a threat to this. The main theme in civil and mechanical structural design is the vibration control techniques relating to the structures subjected to environmental dynamic loads. Different policies have been proposed in this field which considers the structural safety and the random natural vibrations caused by natural or artificial loads such as sea waves, traffic vibrations, earthquakes etc. The alleviating responses of civil engineering structures to environmental loads such as winds and seismic has fascinated many researchers in recent years. Passive, semi active and active vibration control devices have been developed. Friction dampers is one of the simplest and the most reliable passive control devices among the available ones. This study deals with the efficacy of friction dampers as a passive device in controlling vibration of structures. Typical multistoried composite buildings consisting of normal, braced frame building and FD building were considered. Braced frame building and FD building are connected by eight different configurations. These buildings were analysed using the software MSC.PATRAN/NASTRAN to find out the dynamic characteristics and response of the buildings. The effective configuration formed by the addition of friction dampers, and percentage reduction of forces were also determined. Energy efficiency of friction dampers on effective configuration were also calculated. The wind force acting on the building is calculated as per design code IS 875; [part 3]. Ground acceleration were taken according to seismic zone which is used for seismic analysis of the building. Two main analysis namely Normal Mode Analysis and Modal Frequency Response Analysis have been performed in this thesis. From the Normal Mode Analysis, natural frequencies and corresponding mode shapes of the buildings were obtained. From Modal Frequency Response Analysis displacement and acceleration response of the buildings to base excitation and wind excitation have been procured. This study proves that FDs equipped on building structure can reduce the displacement of the building to a considerable extend and thus the safety and comfort of the occupants can be ensured.
Keywords Seismic analysis, Friction damper, High rise building, Modal frequency response analysis, MSC.PATRAN/NASTRAN
-
INTRODUCTION
The most feasible and effective solution for the housing needs of rapidly increasing urban population are the high-rise buildings. It is possible to construct high rise building with the development in the construction technology and use of different type of construction material. The major engineering
concern is the safety of high rise building against the environmental forces such as wind and earthquakes. Ductility, strength and stiffness are the major factors which depends on the response of these high rise building structures. The overall lateral response is affected by the structural used in tall buildings. The vibrations produced by the seismic and wind forces can cause failure for the building and produce discomfort to the occupants. This can be controlled by the enhancement of damping, mass, shape, rigidity of the structure.
DAMPING
Damping is the process by which mechanical energy is dissipated in dynamic systems. It reduces the structural response on buildings. Vibration amplitude, materials used in the construction, fundamental periods of vibration, mode shapes and structural configurations are the parameters that depends the damping of the structure. Vibration control technique depends on many factors like efficiency, compactness and weight, capital cost, operating cost, maintenance requirements and safety. The damage produced on the structural system can be reduced by dissipation of input energy due to earthquake and wind through special devices which can be replaced if necessary after the occurrence of earthquake. Three types of external dampers that can be added to a mechanical system to enhance its energy dissipation characteristics. They are
-
Active control devices
An active system uses a power source to produce an additional force between the dampers and the structure, and still uses a damper to dissipate energy. This system includes a smaller mass but contains large amounts of energy. However, another major problem with active control system is that they can only be used on smaller buildings due to economic impact of the huge amount of energy consumption; the power needed to dampen the oscillations of huge structures is enormous. This high amount of energy not only has a negative consequence on overall operational charges, but it also produces a gigantic mark on the environment; active control devices do not conserve energy resources and emit exhaust that convert to environmental pollution. Examples of active control devices comprises of tuned mass damper and tuned liquid damper [4].
-
Passive control devices
A passive system is the frequently used vibration control technique. This method is not only the inspected and most acknowledged but is also the age oldest configurations of
vibration control technique and it is presently the productive devices in high-rise buildings. Passive control devices dissipate the energy with no external power source. This system simply comprises of a mass, a damper and a spring. The force that act on the building due to the external force is directed through this device and thus dissipated takes place with the help of damping device. Examples of passive control devices comprises of viscous fluid dampers, viscoelastic solid dampers, friction dampers, and metallic dampers [4].
-
Semi Active control devices
Semi-active control devices are hopefully the most promising devices, with lower performance costs and more energy efficient components. Semi-active control devices can be potentially activated fully by batteries if needed making them superior to active systems in the area of power interruption. The prime idea of a semi-active system is the amalgam of a passive and active system. The basic passive system operates as it always does, but in between outward disturbance force intakes, a valve is turned on. This valve sends a signal to a computer, which in exchange gives the active part of the system a bump of energy. This added energy then builds on to the dampening effect of the passive component of the system. Though this is a rather systematic method of dampening structural oscillations, the actuality remains that an external power supply is still needed in the semi-active tuned mass damper's performance. The totality of environmental impact caused by this power source may be much lesser than that of an active tuned mass damper system, but semi-active tuned mass dampers still rank below passive systems with regards to its sustainability. Passive control methods are quite usual vibration control method in tall building structures. Among numerous passive control devices, tuned mass dampers are used systmatically to bring down the dynamic response of structures due to wind or seismic induced excitations. Some models of semi-active dampers include variable-orifice dampers, magneto rheological dampers, and electro rheological dampers [4].
It is apparent that passive control devices are most productive in reduction of response of high-rise buildings from profitable and natural view point. This is where the friction damper, the subject matter of this study comes into play.
-
-
FRICTION DAMPERS
Friction dampers [FD] are devices that use dry friction to dissipate energy of a system in order to limit its vibratory response. They work by keeping in contact two surfaces that move relative to each other in order to generate friction. When compared to other means to attenuate vibration, friction dampers stand out by their noteworthy advantages. To name a few, they work in harsh environments and in the absence of electric or hydraulic power they adapt to a wide excitation bandwidth without tuning; and they can act simultaneously along multiple directions. Consequently, they are used in a variety of applications. Their most common use is in buildings, as a means to prevent damage caused by earthquakes. Their use is also common in the transportation sector, such as for truck and train damping of road-induced vibrations. Friction damping is also extensively used in
turbomachinery, especially on turbine blades and bladed disks.
Friction damping can be referred to as frictional damping or Coulomb damping. When the damping comes from the material itself or from a system about which no clear information of the inner dynamics is known, the terms hysteretic damping, complex stiffness, and structural damping may refer to the same phenomenon of dissipation by friction. The friction damper consists of 3 steel plates rotating against each other and in between these plates, there are two circular friction pad discs, in order to have dry friction lubrication in the unit, ensuring stable friction force and reducing noise of the movements [1].
The damper main parts are the central plate and two side plates. The central plate holds and connects the damper device to the girder of frame structure by a hinge in order not to introduce moment in the girder. The hinge connection will increase the amount of relative rotation between the central and side plates, which in turn increases the amount of energy dissipation in the system. The two side plates connect the damper to the bracing system and in this work, inverted V- bracing was used. This bracing consists of pretension bar members in order to avoid compression forces and therefore buckling. The bracing bars are pin-connected at both ends to the damper and to the column bases [18].
Fig. 1. Details of the FD device [20]
The reason for using two side plates instead of one was to increase the frictional surface area and to provide the necessary symmetry in to obtain plane behaviour of the device. The bolt connects the three plates of the damper to each other. This adjustable bolt is used to control the normal force applied on the friction pad discs and the steel plates. In order to keep a constant clamping force, several discs spring washers (Belleville washers) are used. Hardened washers were placed between these springs and steel plates to prevent any marks on steel plate due to the disc springs when they were in compression.
When a lateral external force excites a frame structure, the girder starts to displace horizontally due to this force. The bracing system and the frictional forces developed between the frictional surfaces of steel plates and friction pad materials will resist the horizontal motion. This process of moving from phase to phase is repeated upon reversal of the direction of the force application.
Pall Friction Dampers are simple and fool proof in construction. Basically, these consist of series of steel plates, which are specially treated to develop very reliable friction. These plates are clamped together and allowed to slip at a predetermined load. Decades of research and testing have led to perfecting the art of friction. Their performance is reliable, repeatable and they possess large rectangular hysteresis loops with negligible fade. Pall Friction Dampers are passive energy dissipation devices and, therefore, need no energy source other than earthquakes to operate it. Pall Friction Dampers are available for long slender tension-only cross bracing, single diagonal tension-compression bracing and chevron bracing. The damper for cross bracing is a unique mechanism. When the brace in tension forces the damper to slip, the damper mechanism forces the other brace to shorten and, thus avoid buckling. In this manner, the other brace is immediately ready to slip the damper on reversal of cycle. These dampers have been used in 22 meter (65 feet) long slender bracing. To avoid pounding at the expansion joints, Pall Friction Connectors are custom made to accommodate bi-directional movements.
The damping of typical structures is about 1- 5% of critical, while, the damping of structures that have been built by friction damper devices is easily about 20-30% of critical. Pall Friction Dampers are available for long slender tension only cross bracing, single diagonal tension compression bracing and chevron bracing Another attractive feature of friction dampers is that they offer stiffness in conjunction with supplemental damping. While supplemental damping is beneficial in reducing the earthquake forces and amplitudes of vibration, added stiffness is beneficial for stability. For a given force and displacement in a damper, the energy dissipation of friction damper is the largest compared to other damping devices. Therefore, fewer friction dampers are required to provide a given amount of supplemental damping. Unlike other devices the maximum force in a friction damper is pre defined and remains the same for any future ground motion [18].
characteristic shape, and fundamental shape. Each mode shape is correlated with corresponding natural frequency are the functions of the boundary conditions and structural properties. Boundary condition applied here is that the support nodes of the structure was made fixed by assigning all translational and rotational degree of freedom to zero. Modal frequency response analysis method uses the mode shapes of the structure to uncouple the equations of motion (when no damping or only modal damping is used) and, depending on the number of modes calculated and retained, reducing the problem size. These twin factors are likely to make modal frequency response analysis calculatingly more efficient than direct frequency response analysis. It is used for large models where a large number of solution frequencies are defined. This method supersedes the physical degrees of freedom (DOF) with a reduced number of modal degrees of freedom. Fewer degrees of freedom intend a faster solution. Because modal frequency response analysis utilizes the mode shapes of the structure, modal frequency response analysis is a natural extension of normal modes analysis.
Modal frequency response analysis was done with base excitation and wind excitation along X axis. Base excitation was taken as per IS 1893[part 1];2002 based on seismic zone. It was applied on all the base nodes of the structure. Zone factor was taken as 0.24g. Wind excitation was calculated as per IS 875;1987 Part 3. The basic wind speed was taken as 44 m/s. It was provided at top nodes 5164, 5170, 5180, 5190,
5200, 5210, 5220. The risk factor, terrain factor, topographic factor was calculated as per code. The following table gives the value of wind force calculated for the building.
IV. MATHEMATICAL FORMULATIONS
To run a modal frequency response, it is necessary to transform the physical coordinates to modal coordinates. The natural frequencies and eigen vectors are a good way to do this because of their property of orthogonality. As such, we can replace the physical coordinates u with the modal coordinats. So first, a transformation is defined
Eq. [1]
This is substituted into the equations of motion (temporarily ignoring the damping term):
Fig. 2. Friction Damper in tension-only cross brace [21]
-
DYNAMIC ANALYSIS OF HIGH-RISE BUILDING A high-rise building structure design are affected by lateral
Resulting in the following: Now pre-multiply by:
Eq. [2]
Eq. [3]
Eq. [4]
loads especially sway produced due to two main lateral forces; wind and seismic forces. Normal mode analysis determines the natural frequencies and mode shapes of the structure with damping neglected. These results indicate the basic dynamic behaviour of the building and shows how the building will react to dynamic loading. The natural frequencies of the building are the frequencies at which the structure naturally prone to vibrate if it is exposed to a disturbance. The deformed shape of the building at a particular natural frequency of vibration is designated as normal mode of vibration. Different terms used to depict the normal mode are mode Shape,
These terms are replaced with the uncoupled generalized
components that are easily handled:
= modal or generalized mass matrix
= modal or generalized stiffness matrix
= modal load vector
Resulting in an uncoupled series of equations that are easily solved:
Eq. [5]
And once the modal displacements are found, the physical displacements can be found from the sum of the modal displacements:
Eq. [6]
This approach will yield the exact same answer as the direct approach, provided that all modal degrees of freedom are included in the transformation. However, the strength of the approach comes about because an answer that is very close to exact can usually be obtained with significantly fewer modal degrees of freedom than there are physical degrees of freedom. With fewer DOF, the solution can proceed much faster. This can be especially efficient for large models and for models with large numbers of frequencies [22].
-
CASE STUDY
In this study a 20-storied commercial composite building situated at zone 4 is considered. The buildings were modelled as a normal plane frame structure, a braced frame structure and friction damper structure. Modelling was done with the help of the software MSC.PATRAN. Points and curves were used to create the geometry of the building. Once the geometry of the building was created, finite element discretization was done followed by meshing. Material of the structural elements like beams, columns, bracings, FD were assigned as steel whose modulus of elasticity was given by 2.1e+11 N/m2. Beams and columns were created as ID bar element and dimensions of beams and columns were specified. Bracings and FD were created as 1D bush element and dimensions were specified. Slabs were made of concrete whose modulus of elasticity is 2.2e+10 N/m2 and was created as 2D plates of thickness 150 mm. Beams are of I section [ISLB 250], columns of hollow square box section [2 ISA 200 x 200 x 25 mm], bracings are of angle section [ISA 200 x 200 x 15 mm] were specified. Bracings type is X- bracings provided at periphery of the structure. The X- type Pall friction damper is modelled with stiffness 5.4e+7 N/m, damping force 6000 KN. It is attached to X- braces of section ISMB 200. The bracings and Pall friction dampers are provided on the structure at 8 different configurations.
The usual first step in performing a dynamic analysis is determining the natural frequencies and mode shapes of the structure. The deformed shape of the structure at a specific natural frequency of vibration is termed its normal mode of vibration. Here the building can be considered analogous to a cantilever beam (fixed at one end and free at the other). The normal building modelled using MSC.PATRAN is as shown below.
Fig. 3. Model of the normal building in MSC.PATRAN
The natural frequency of the normal building was obtained as 0.226 Hz. The first mode shape of normal building obtained from normal mode analysis using MSC.NASTRAN is as shown below.
Fig. 4. First Mode shape of the normal building
After Normal mode analysis, Modal frequency response analysis were conducted considering base excitation and wind excitation. The results obtained from Modal frequency response analysis were displacement and accelerations. For normal building results obtained from modal frequency response analysis were normalized to 1.
Fig. 5. Normalized displacement response for normal building at natural frequency
Fig. 6. Normalized acceleration response for normal building at natural frequency
Braces and FD where added on this building in eight different configurations and two analyses where conducted. The eight different configurations where shown below.
Fig. 7. Configuration I Fig. 8. Configuration II
Fig. 9. Configuration III Fig. 10. Configuration IV
Fig. 11. Configuration V Fig. 12. Configuration VI
Fig. 13. Configuration VII Fig. 14. Configuration VIII
-
RESULTS AND DISCUSSIONS Following table shows the natural frequencies for braced framed building in all configurations.
-
-
TABLE. 1. NORMAL MODE ANALYSIS RESULTS OF BRACED FRAME BUILDING
Configurations |
Natural frequency [Hz] |
I |
0.34 |
II |
0.46 |
III |
0.24 |
IV |
0.42 |
V |
0.32 |
VI |
0.32 |
VII |
0.32 |
VIII |
0.32 |
Configuration II shows maximum value of natural frequency
0.46 Hz for braced frame building.
TABLE. 2. MODAL FREQUENCY RESPONSE ANALYSIS RESULTS FOR BRACED FRAME BUILDING
Configurations |
Displacements |
Accelerations |
I |
0.51 |
2.30 |
II |
0.28 |
2.40 |
III |
0.91 |
2.06 |
IV |
0.32 |
2.36 |
V |
0.55 |
2.20 |
VI |
0.57 |
2.31 |
VII |
0.57 |
2.31 |
VIII |
0.55 |
2.38 |
Configuration II shows minimum displacement value of 0.28 in braced frame building.
Following table shows the natural frequencies for FD building in all configurations.
TABLE. 3. NORMAL MODE ANALYSIS RESULTS OF FD BUILDING
Configurations |
Natural frequency [ Hz] |
I |
0.29 |
II |
0.36 |
III |
0.23 |
IV |
0.33 |
V |
0.28 |
VI |
0.27 |
VII |
0.27 |
VIII |
0.28 |
Configuration II shows maximum value of natural frequency
0.36 Hz for FD building.
TABLE. 4. MODAL FREQUENCY RESPONSE ANALYSIS RESULTS FOR FD BUILDING
Configurations |
Displacements |
Accelerations |
I |
0.45 |
1.52 |
II |
0.23 |
1.25 |
III |
0.85 |
1.94 |
IV |
0.29 |
1.32 |
V |
0.51 |
1.59 |
VI |
0.53 |
1.63 |
VII |
0.53 |
1.64 |
VIII |
0.50 |
1.66 |
Configuration II shows minimum displacement value of 0.23 in FD building.
Following figure is a chart representing comparison of values of natural frequency for braced frame building and FD building.
Fig. 15. Comparison of natural frequency for braced frame building and FD building
From Normal mode analysis it was observed that FD building gives lesser value of natural frequency when compared to braced frame building in all configurations. This is because of higher stiffness on braces of braced frame building than FD on FD building.
Fig. 16. Comparison of displacement on different configurations for braced frame building and FD building
Comparing the displacement results obtained from modal frequency response analysis it is observed that the reduction of displacement in FD building is higher than in braced building. This is because of the energy dissipation efficiency of FD than stiffness of bracings. Thus, the use of FD is effective in reducing the lateral response of high rise building.
Fig. 17. Comparison of accelerations on different configurations for braced frame building and FD building
Comparing the acceleration results obtained from modal frequency response analysis it is observed that FD building have least acceleration when compared to braced building. This is because acceleration is directly proportional to natural frequency. Since FD building have least values of natural frequency it shows least accelerations.
From the above comparison it is concluded that FD building is more effective than braced building when subjected to lateral forces. Following chart will gives the percentage reduction of displacement on different configurations of FD building.
Fig. 18. Percentage reduction of forces on FD building
From the chart it is observed that addition of FD on building can reduce the lateral forces to a maximum of 77 % on configuration II and 71 % on configuration IV. Since configuration IV have half the amount of materials when compared to configuration II and shows 71% reduction of lateral forces. So, from economic view point, Configuration IV can be considered as the effective configuration of FD.
To study the energy dissipation efficiency of FD, the configurations II having maximum response reduction [77 %] is again analysed with 0 damping force on MFRA. Following table gives the analysis results.
TABLE. 5. COMPARISON OF DISPLACEMENT RESULTS FOR FULL DAMPING FORCE AND 0 DAMPING FORCE
Configuration |
Natural frequency [] |
Displacement [full damping force] |
Displacement [0 damping force] |
II |
0.36 |
0.23 |
0.43 |
Energy dissipation efficiency of friction dampers
= x 100
= 46.51%
From this study it is concluded that buildings equipped with friction damper is effective tan building equipped with bracings. FD buildings can reduce a maximum of 77 % of lateral response when excited by lateral forces. Configuration IV gives most economic location of addition of friction dampers with 71% reduction of forces. Energy dissipation efficiency of friction damper alone is found to be 46.51%.
VI. CONCLUSIONS
From this study, it can be concluded that for 20-storied building, the incorporation of FD on buildings dissipate a greater amount of energy and thus reduces the lateral response more compared to braced frame building, hence considered as an effective solution. The energy dissipation of friction damper varies depending on its location in the building structure. Maximum percentage reduction of forces was shown by configuration II and the percentage reduction is 77
%. Configuration IV shows a percentage reduction of 71%, with less no of dampers and materials usage than configuration II, hence configuration IV is considered as the effective configuration of addition of friction dampers. Energy dissipation efficiency of friction damper with maximum percentage reduction of forces is 46.51 %. Thus, it is clear from the study that a Pall type FD attached to a high-rise building can be considered as a means with which its response to lateral loading can be significantly reduced leading to better scope to the construction of super tall buildings to meet the increasing living space requirements.
REFERENCES
-
Louis Gagnon, Marco Morandini & Gian Luca Ghiringhelli. [2020]A review of friction damping modeling and testing. Archive of Applied Mechanics volume 90, pages107126
-
T. Roy and V. Matsagar. (2020). Probabilistic assessment of steel buildings installed with passive control devices under multi hazard scenario of earthquake and wind. Structural Safety, vol. 85, Article ID 101955.
-
R. Rupakhety, S. Elias, and S. Olafsson. (2020). Shared tuned mass dampers for mitigation of seismic pounding. Applied Sciences, vol. 10, no. 6, p. 1918.
-
Prof. Yogesh Ravindra Suryawanshi. (2012). Study or Tuned Mass Dampers System as Vibration Controller in Multistoried buildings. ISSN: 2278-7844.
-
S. Chapain and A. M. Aly. (2019).Vibration attenuation in high-rise buildings to achieve system-level performance under multiple hazards. Engineering Structures, vol. 197, Article ID 109352.
-
S. Elias, R. Rupakhety, and S. Olafsson. (2019). Analysis of a benchmark building installed with tuned mass dampers under wind and earthquake loads. Shock and Vibration, vol. 2019, Article ID 7091819.
-
Roy and V. Matsagar. (2019). Effectiveness of passive response control devices in buildings under earthquake and wind during design life. Structure and Infrastructure Engineering, vol. 15, no. 2, pp. 252268.
-
Chi-Chang Lin, Lyan Ywan Lu, Ging-Long Lin, Ting Wei Yang Vibration control of seismic structures using semiactive friction multiple tuned mass dampers.
-
K. S. Numayr, S. T. Mesmar, and M. A. Haddad. (2018). Dynamic analysis of tapered thin-walled masts. Journal of Engineering Science and Technology, vol. 13, no. 7, pp. 21062124.
-
S. Elias. (2018). Seismic energy assessment of buildings with tuned vibration absorbers. Shock and Vibration, vol. 2018, Article ID 2051687.
-
M. Anoushehei, F. Daneshjoo, S. Mahboubi, and S. Khazaeli. (2017).Experimental investigation on hysteretic behavior of rotational friction dampers with new friction materials. Steel And Composite Structures, vol. 24, no. 2, pp. 239248.
-
F. Fathi and O. Bahar. (2017). Hybrid coupled building control for similar adjacent buildings. KSCE Journal of Civil Engineering, vol. 21, no. 1, pp. 265273.
-
T. Roy and V. Matsagar. (2017). Multi-hazard assessment of steel buildings retrofitted with passive control devices. in 16th World Conference On Earthquake Engineering (16WCEE), Santiago, Chile.
-
B. He, H. Ouyang, S. He, and X. Ren. (2017). Stick-slip vibration of a friction damper for energy dissipation. Advances in Mechanical Engineering, vol. 9, no. 7, pp. 113.
-
L. F. F. Miguel, L. F. F. Miguel, and R. H. Lopez. (2016). Failure probability minimization of buildings through passive friction dampers.
Be Structural Design of Tall and Special Buildings, vol. 25, no. 17, pp. 869885.
-
J. Kim and S. An. (2016). Optimal distribution of friction dampers for seismic retrofit of a reinforced concrete moment frame. Advances in Structural Engineering, vol. 20, no. 10, pp. 15231539.
-
B. Chen, S. Weng, L. Zhi, and D. Li. (2016). Response control of a large transmission tower-line system under seismic excitations using friction dampers. Advances in Structural Engineering, vol. 20, no. 8, pp. 11551173.
-
Mualla IH (2000) Experimental and computational evaluation of a novel friction damper device. PhD thesis, Department of Structural Engineering and Materials, Technical Uiversity of Denmark. Google Scholar
-
Seyed Mehdi Zahraei, Alireza Moradi and Mohammadreza Moradi. (2000) Using Pall_Friction Dampers for Seismic Retrofit of a 4-Story Steel Building. Google Scholar
-
https://www.google.com/url?sa=i&url=https%3A%2F%2Fwww.resear chgate.net%2Ffigure%2FDetails-of-the-friction-damper- device_fig1_267717939&psig=AOvVaw2- hb2qWw8Qobj9YJhPI5LU&ust=1623327021757000&source=images &cd=vfe&ved=0CAIQjRxqFwoTCLC3t8bCivECFQAAAAAdAAAA ABAD
-
https://www.google.com/url?sa=i&url=https%3A%2F%2Fwww.seman ticscholar.org%2Fpaper%2FPERFORMANCE-BASED-DESIGN- USING-PALL-FRICTION-DESIGN-Pall- Pall%2F409602a398dc5a8e536d9ee107f742b9395d3618&psig=AOvV aw3LpQjAEpV88B8vlRZAclit&ust=1623327205812000&source=ima ges&cd=vfe&ved=0CAIQjRxqFwoTCOi72Z7DivECFQAAAAAdAA AAABAD
-
Endrita MULLETI. (2014). Seismic Response Of High Rise Buildings Using Friction Damper. Epoka University Faculty Of Architecture And Engineering Civil Engineering Department
-
Avtar PALL and R. Tina PALL. (2004). Performance-based design using pall friction dampers – an economical design solution. 13th World Conference on Earthquake Engineering Vancouver, B.C., Canada
-
D. Wang, T. K. T. Tse, Y. Zhou, and Q. Li. (2015). Structural performance and cost analysis of wind-induced vibration control
schemes for a real super-tall building. Structure and Infrastructure Engineering, vol. 11, no. 8, pp. 9901011,
-
Y. Fukumoto and I. Takewaki. (2015). Critical earthquake input energy to connected building structures using impulse input. Earthquakes and Structures, vol. 9, no. 6, pp. 11331152.
-
S. Mahmoud, A. Abd-Elhamed, and R. Jankowski. (2013). Earthquake- induced pounding between equal height multi-storey buildings considering soil-structure interaction. Bulletin of Earthquake Engineering, vol. 11, no. 4, pp. 10211048.
-
H.-S. Chung, B.-W. Moon, S.-K. Lee, J.-H. Park, and K.-W. Min. (2009). Seismic performance of friction dampers using flexure of RC shear wall system. Be Structural Design of Tall and Special Buildings, vol. 18, no. 7, pp. 807822.
-
H. Mualla and B. Belev. (2002). Performance of steel frames with a new friction damper device under earthquake excitation. Engineering Structures, vol. 24, no. 3, pp. 365371.
-
R. Chandra, M. Masand, S. K. Nandi, C. P. Tripathi, R. Pall, and A. Pall. (2000). Friction-dampers for seismic control of la gardenia towers south city, Gurgaon, India. in 12th World Conference On Earthquake Engineering (12WCEE), Auckland, New Zealand.
-
IS 875(Part 1):1987- Code of practice for design loads (other than earthquake) for buildings and structures Part 1 Dead loads – Unit weights of building material and stored materials (second revision) (Incorporating IS:1911-1967)
-
IS 875(Part 2):1987- Code of practice for design loads (other than earthquake) for buildings and structures: Part 2 Imposed loads (second revision)
-
IS 875(Part 3):1987- Code of practice for design loads (other than earthquake) for buildings and structures: Part 3 Wind loads (second revision)
-
IS 800:2007- Code of practice for general construction in steel (third revision)
-
IS: 800 : 2007 – Code of Practice for general construction in Steel
-
IS: 808 : 1989 – Dimensions for Hot Rolled Steel Beam, Column, Channel and Angle Sections