
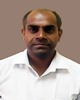
- Open Access
- Authors : Venkat , Dr. S. R. Ranganatha
- Paper ID : IJERTV9IS110025
- Volume & Issue : Volume 09, Issue 11 (November 2020)
- Published (First Online): 11-11-2020
- ISSN (Online) : 2278-0181
- Publisher Name : IJERT
- License:
This work is licensed under a Creative Commons Attribution 4.0 International License
Vibration Analysis of Rectangular Solid Plates and Plates with Surface Cracks
Venkat
Microwave Tube Research and Development Centre
DRDO, Bangalore, India
Dr. S.Ranganatha
Mechanical department
Universuty Visvesvaraya College of Engineering Bangalore University, Bangalore, India
Abstract— Plate members are used in automobile and aerospace structures. These structures are subjected to dynamic forces with variable frequencies due to engines used for propelling. These variable frequencies of dynamic forces cause resonance of plate elements in the structure. The resonance phenomenon leads to the fatigue of plate structures thus the instability of the flight in space.
In the present investigation an attempt has been made to characterize dynamic response, which controls the fatigue phenomenon of rectangular plates and plate with surface cracks oriented in different directions. The clamped-clamped-free-free (CCFF) boundary condition is incorporated. The vibration shaker is used to introduce exciting forces. The frequency of the exciting force is varied from 20 Hz to 2000 Hz. The amplitude, modal frequency, phase angle and damping factor are monitored at various resonant frequencies.
It is found from the experimental results that, amplitude of vibration, modal frequency, phase angle and damping factor are dependent on surface crack with longitudinal axis and its orientations.
Keywords— Surface crack, modal frequency, amplitude, damping factor,phase, vibration.
I. INTRODUCTION
An aerospace and automobiles engineering industry utilize a system in which major sub components are plate structured elements. More specifically in aerospace, plate panels are used to a large extent. These plate elements are subjected to different frequencies and of varying range due to high speeds of aero engines. The large range of variable speeds of aero engines introduces forced excitation on plate panels. The plate experience response at specific frequencies called modal frequencies. The modal frequencies at higher modes in engineering structure, results in fatigue failure of the components.
Both experimental and numerical attempts are made by researchers to understand the dynamic response of plate structure.
IVO Senjanovic made an attempt for estimating the natural frequency of free thin rectangular plate based on Rayleigh quotient method. The analytical estimated natural frequencies are compared with numerical obtained natural frequencies (1). Viswas and Ranjith studied both analytically and numerically methods to characterize free vibration of plates. Parameters like boundary conditions and plate thickness were considered for characterizing the dynamic response of the plate. The experimental method results were compared with results of numerical methods (2).Ibearugbulem and Owus studied the dynamic response of plate using energy method. The natural frequency was obtained by using Taylor’s series shape function and Ritz energy method. The results were compared with experimental work (3). Ilook Park and Usik lee studied dynamic response of plate using frequency dynamic spectral elements modeling and analysis method. The results were compared with exact solutions and numerical solutions (4). Khiem and Lien made an attempt in obtaining natural frequencies of beam with arbitrary number of cracks. The new method analyzed the effect of crack and boundary condition on natural frequencies (5). Zarza and Naimi made an attempt dynamic characteristic of isotropic and orthotropic cracked plate using energy approach. The results were comparable with numerical methods (6). Asif Israr et al., attempted a analytical modeling vibration analysis of partially cracked plate with different boundary condition. The method of multiple scales an approximate method was applied for solving the problem of cracked plate. The results were analyzed for both cracked length and plate thickness (7). Gharaibeh and Obeidat studied analytically the dynamic response of the rectangular plates. Rayleigh-Ritz method was used to calculate the first natural frequency. They used the results to characterize dynamic response in the presence of extra masses on the rectangular plates (8). Joshi et al., made analytical an attempt in characterizing, the dynamic response of internally cracked rectangular plate. They found that natural frequencies are more affected when cracks are internal and symmetrical about the mid plate of the plate. The influence was found that orientation of cracks with respect to longer edge of the crack was found to be more effective (9). Tushar choudary and Kumar made analytical attempts in predicting dynamic response of plate with circular hole. The results show that the natural frequency of the plates decreased with increased hole diameter (10). Ali and Atwal made analytical attempts to characterize the dynamic response of the rectangular plates with rectangular cut outs. They used the Rayleigh-Ritz method for finding the natural frequency. The results were compared with numerical methods (11). Ramamurthy et al., made attempts experimental attempt to find damping ratio. Such found damping ratio was used in numerical analysis (12). Maruyama and Ichinomiya conducted experiment for characterizing the dynamic response of clamped rectangular plates with straight narrow slits. Real time technique of the average interferometery was used to find the natural frequencies and mode shapes. The effect of the length of slit, position and inclination angle of slit on dynamic response was evaluated. They found that the above said parameters alter the dynamic response (13). Yin and lam developed analytical method for characterizing dynamic response of rectangular plates with two parallel cracks. The energy method was used for calculating natural frequencies
and also concluded that time domain response of the plate can be calculated using mode super position method (14). Gade and Khatode made analytical attempts for predicting dynamic response of beams with open edge crack. Parameters like varying crack, depth and location of the cracks were incorporated and studied the dynamic response of the beam. The result showed that the above parameter affects the dynamic response of the beam (15).
II. EXPERIMENTAL SETUP
The experiments are conducted using a 4-channel vibration controller, vibration shaker with accelerometer. The schematic experimental setup is shown Fig. 1.
Fig. 1. Schematic of electrodynamics vibration set up
The details of the equipment/instruments used are shown in Table I. The solid rectangular plate and plate with surface cracks are shown in Fig. 2. The fixture used for obtaining clamped-clamped-free-free boundary condition is shown in Fig. 4 and Fig. 5.
TABLE I. SPECIFICATION OF SHAKER AND SUBSYSTEM
Subsystem
Model
Parameter
Specification
Electro dynamic Shaker
SEV 060
Rated force
600 Kgf (Peak Sine)
Digital
power amplifier
DAS 3K6
Operating frequency
5 Hz to 3000 Hz
Vibration controller
Spandon
Stroke
30 mm (p-p)
Piezo electric accelerometers
M353B04 (2 no’s)
Acceleration bare table
75 g
RSTD package
Maximum velocity
1.5 m/sec
Moving platform diameter
180 mm
Fig. 2. Solid plate
Fig. 3. Surface crack at 0° with longitudinal axis
Fig. 4. Assembly fixture with specimen
Fig. 5. 2 D drawing of vibration fixture
Fig. 6.
IMG_20200702_160416.jpg
Fig. 7. Vibration shaker with plates for CCFF boundary condition
The experiments are conducted with different orientation direction of the surface cracks. The different orientations of the crack with longitudinal axis used in experiments are
1. Solid plate
2. Surface crack at 00 with longitudinal axis
3. Surface crack at 200 with longitudinal axis
4. Surface crack at 400 with longitudinal axis
5. Surface crack at 600 with longitudinal axis
6. Surface crack at 800 with longitudinal axis
7. Surface crack at 900 with longitudinal axis
III. RESULTS AND DISCUSSION
A. Solid plate
Rectangular plate with clamped-clamped-free-free (CCFF) boundary condition was subjected to forced vibration. The experiment was repeated for three times and average values of parameters; modal frequency, amplitude, phase angle and damping factor were estimated. A typical plot of experimental results is shown in Fig. 8.
Fig. 8. Experimental results for solid plate for CCFF condition
The Fig. 8 shows different magnitude of amplitude, modal frequencies and phase angle at resonance. All the details regarding resonance frequencies, amplitude at resonance, phase angle and Q-factor s are also shown in Fig. 8. These data are used for drawing Fig. 9 which shows detailed information inclusively dependence of amplitude with exciting frequency.
Fig. 9. Dependency of amplitude with excitation frequency for solid plate
The data of phase angle dependency on excitation frequencies are extracted from the Fig. 8 and drawn a new figure shown in Fig. 10 for the detailed information on phase angle of vibration.
Fig. 10. Dependency of phase angles with modal frequency for solid plate
The experimental data in Fig. 8 are rounded off to nearest number. The amplitude is rounded up to full number, phase angle rounded up to full number. The frequencies are rounded up to full number and Q-factor rounded up to full number. The rounded off data of frequencies, amplitudes, phase angles and Q-factors are tabulated and shown in Table II. The damping factor (ξ) was found from the tabulated Q-factor values in the Table II. The damping factor (ξ) was estimated using formula: ξ=1/2Q the estimated damping factors (ξ) are tabulated in Error! Reference source not found..
TABLE II. AMPLITUTE, MODAL FREQUENCY, PHASE, Q-FACTOR AND DAMPING FACTOR FOR SOLD PLATE
Solid plate
Mode
No.
Amplitude
(g/g)
Modal
Frequency (Hz)
Phase angle (0)
Q-Factor
Damping
factor (ξ)
1
70
188
-90
49
0.02
2
2
292
-165
55
0.02
3
1
522
171
24
0.04
4
49
661
67
63
0.02
5
3
715
-129
148
0.01
6
5
954
119
14
0.07
7
25
1065
61
25
0.04
8
30
1132
-60
89
0.01
B. Surface crack at 00 with longitudinal axis
A typical plot of experimental results is shown in Fig. 11.
Fig. 11. : Experimental results for surface crack at 00 for CCFF conditions
The Fig. 11 shows different magnitude of amplitude, modal frequencies and phase angle at resonance. All the details regarding resonance frequencies, amplitude at resonance, phase angle and Q-factor are also tabulated in Fig. 11.
The data of amplitude dependency on excitation frequencies are extracted from the Fig. 11. These data is used for drawing Fig. 11 which shows information inclusively on dependency of amplitude with exciting frequency.
Fig. 12. : Dependency of amplitude with excitation frequency for surface crack at 00
The data of phase angle dependency on excitation frequencies are extracted from the Fig. 11 and drawn a new figure shown in Fig. 13 for the detailed information on phase angle of vibration.
Fig. 13. Dependency of phase angles with excitation frequency for surface crack at 00
The experimental data of table in Fig. 11 are rounded off to nearest number. The amplitude is rounded up to first number, phase angle rounded up to full number. The frequencies are rounded up to full number and Q-factor rounded up to full number. The rounded off data of frequencies, amplitudes, phase and Q-factors are tabulated and shown in Error! Reference source not found.. The damping factor (ξ) was found from the tabulated Q-factor values in the Error! Reference source not found.. The damping factor (ξ) was estimated using formula: ξ=1/2Q. The estimated damping factors (ξ) are tabulated in Error! Reference source not found..
TABLE III. AMPLITUDE, MODAL FREQUENCY, PHASE AND Q-FACTOR FOR SURFACE CRACK AT 00
Surface crack at 0
Mode
No.
Amplitude (g/g)
Modal
Freq.(Hz)
Phase (0)
Q-Factor
Damping
Factor (ξ)
1
103
186
-86
41
0.01
2
3
276
141
45
0.01
3
22
634
77
89
0.01
4
7
666
-72
89
0.01
5
17
1109
-74
45
0.01
6
6
1319
-70
44
0.01
7
26
1434
-96
63
0.01
8
48
1824
-162
32
0.02
The Error! Reference source not found. shows the highest magnitude of amplitude 70g/g at resonance frequency was found in first mode which is 188 Hz. Other lesser magnitude of amplitude was found 49, 25 and 30 g/g at the resonance frequencies of 661, 1065 and 1132 Hz in mode 4, 7 and 8 respectively. The other minimum magnitude of amplitude were found 2, 1, 3 and 5 g/g at the resonance frequencies 292, 522, 715 and 954 Hz in modes 2, 3, 5 and 6 respectively.
The Error! Reference source not found. shows highest magnitude of amplitude 103g/g at resonance frequency was found in first mode which is 186 Hz. Other lesser magnitude of amplitude was found 22, 17, 26 and 48 g/g at the resonance frequencies of 634, 1109, 1434 and 1824 Hz in mode 3, 5, 7 and 8 respectively. The other minimum magnitude of amplitude was found 3.2, 6.9 and 5.8g/g at the resonance frequencies 276, 666 and 1319 Hz in modes 2, 4 and 6 respectively.
The Error! Reference source not found. shows the phase angles at the resonance modes. The phase angles at the resonance modes were found to be 141 and 770 at the modes 2 and 3respectively. The response during these modes is lagging to forcing disturbance. The lagging found to be maximum in mode 2 and minimum in mode 2. The mode angles were found to be -86, -72, -74, -70, -96 and -1620 at the modes 1, 4, 5, 6, 7 and 8 respectively. The response of the system during negative phase angle represents the leading of the system with respect to disturbing force. The leading was found to be highest in mode 8 and leading of the system gets reduced in modes 1, 4, 5, 6 and 7
The Error! Reference source not found. shows damping factor (ξ) varies from 0.01 to 0.02. The maximum damping factor was found 0.02 in mode 8 and minimum damping factor 0.01 were found in mode 1 to 8.
C. Surface crack at 200 with longitudinal axis
A typical plot of experimental results is shown in Fig. 14
Fig. 14. : Experimental results for surface crack at 200 for CCFF conditions
The Fig. 14 shows different magnitude of amplitude, modal frequencies and phase angle at resonance. All the details regarding resonance frequencies, amplitude at resonance, phase angle and Q-factor are also tabulated in Fig. 14. The data of amplitude dependency on excitation frequencies are extracted from the Fig. 14. These data is used for drawing Fig. 15 which shows information inclusively on dependency of Amplitude with exciting frequency.
Fig. 15. Dependency of amplitude with excitation frequency for surface crack at 200
The data of phase angle dependency on excitation frequencies are extracted from the Fig. 14 drawn a new figure shown in Fig. 16 for the detailed information on phase angle of vibration
Fig. 16. Dependency of phase with excitation frequency for surface crack at 200
The experimental data of table in Fig. 14 are rounded off to nearest number. The amplitude is rounded up to first digit, phase angle rounded up to full number. The frequencies are rounded up to full number and Q-factor rounded up to full number. The rounded off data of frequencies, amplitudes, phase and Q-factors are tabulated and shown in Error! Reference source not found. . The damping factor (ξ) was estimated using formula: ξ=1/2Q. The estimated damping factors (ξ) are tabulated in Error! Reference source not found..
TABLE IV. AMPLITUDE, MODAL FREQUENCY, PHASE AND Q-FACTOR FOR SURFACE CRACK AT 200
Surface crack at 20
Mode
No.
Amplitude (g/g)
Modal Freq.(Hz)
Phase (0)
Q-Factor
Damping
factor (ξ)
1
77
177
-112
50
0.01
2
6
610
99
74
0.01
3
1
661
135
50
0.01
4
2
672
94
89
0.01
5
10
888
91
21
0.02
6
14
1077
-50
28
0.02
7
152
1414
-159
74
0.01
8
22
1644
-128
17
0.03
The Error! Reference source not found. highest magnitude of amplitude 77g/g at resonance frequency was found in first and magnitude of 152g/g at resonance frequency was found in seventh mode which is 1414 Hz. Other lesser magnitude of amplitude was found 6, 10, 14 and 22 g/g at the resonance frequencies of 610, 888, 1077 and 1644 Hz in mode 2, 5, 6 and 8 respectively. The other minimum magnitude of amplitude was found 01 and 2g/g at the resonance frequencies 661and 672 Hz in modes 3 and 4 respectively.
The Error! Reference source not found. shows the phase angles at the resonance modes. The phase angles at the resonance modes were found to be 99, 135, 94 and 910 at the modes 2, 3, 4 and 5 respectively. The response during these modes is lagging to forcing disturbance. The lagging found to be maximum in mode 3 and minimum in mode 5. The mode angles were found to be -112, -50, -159and -1280 at the modes 1, 6, 7 and 8 respectively. The response of the system during negative phase angle represents the leading of the system with respect to disturbing force. The leading was found to be highest in mode 7 and leading of the system gets reduced in modes 1, 4, 5, 6 and 8.
The Error! Reference source not found. shows damping factor (ξ) varies from 0.01 to 0.03. The maximum damping factor was found 0.03 in mode 8 and minimum damping factor were found in mode 1 to mode 4, 7 and also damping factor was found 0.02 in mode 5 and mode 6 respectively.
D. Surface crack at 400 with longitudinal axis
A typical plot of experimental results is shown inError! Reference source not found.
Fig. 17. Experimental results for surface crack at 400 for CCFF
The Fig. 17 shows different magnitude of amplitude, modal frequencies and phase angle at resonance. All the details regarding resonance frequencies, amplitude at resonance, phase angle and Q-factor are also tabulated in Fig. 17.
The data of amplitude dependency on excitation frequencies are extracted from the Fig. 17. These data is used for drawing Fig. 18 which shows information inclusively on dependency of Amplitude with exciting frequency.
Fig. 18. Dependency of amplitude with excitation frequency for surface crack at 400
The data of phase angle dependency on excitation frequencies are extracted from the Fig. 17 and drawn a new figure shown in Fig. 19 for the detailed information on phase angle of vibration.
Fig. 19. Dependency of phase with Excitation frequency for surface crack at 400
The experimental data of table in Fig. 17 are rounded off to nearest number. The amplitude is rounded up to full digit, phase angle rounded up to full number. The frequencies are rounded up to full number and Q-factor rounded up to full number. The rounded off data of frequencies, amplitudes, phase and Q-factors are tabulated and shown in Error! Reference source not found. . The damping factor (ξ) was estimated using formula: ξ=1/2Q . The estimated damping factors (ξ) are tabulated in Error! Reference source not found. .
TABLE V. AMPLITUDE, MODAL FREQUENCY, PHASE AND Q-FACTOR FOR SURFACE CRACK AT 400
Surface crack at 400
Mode No.
Amplitude (g/g)
Modal Freq.(Hz)
Phase (0)
Q-Factor
Damping
factor (ξ)
1
89
168
-84
26.35
0.02
2
5
259
111
74.25
0.01
3
3
606
142
49.67
0.01
4
6
649
94
55.69
0.01
5
14
862
96
21.09
0.02
6
11
1044
-49
24.86
0.02
7
6
1206
-37
31.82
0.02
8
36
1424
-156
63.57
0.01
The Error! Reference source not found. shows highest magnitude of amplitude 89g/g at resonance frequency was found in first mode which is 168 Hz. Other lesser magnitude of amplitude was found 14, 11 and 36 g/g at the resonance frequencies of 862, 1044 and 1424 Hz in mode 5, 6 and 8 respectively. The other minimum magnitude of amplitude was found 5, 3, 6 and 6g/g at the resonance frequencies 259, 606, 649 and 1206 Hz in modes 2, 3, 4 and 7 respectively.
The Error! Reference source not found. shows the phase angles at the resonance modes. The phase angles at the resonance modes were found to be 111, 142, 94 and 96 at the modes 2, 3, 4 and 5 respectively. The response during these modes is lagging to forcing disturbance. The lagging found to be maximum in mode 3 and minimum in mode 4. The mode angles were found to be -84, -49, -37and -1560 at the modes 1, 6, 7 and 8 respectively. The response of the system during negative phase angle represents the leading of the system with respect to disturbing force. The leading was found to be highest in mode 7 and leading of the system gets reduced in modes 1, 4, 5, 6 and 8.
The Error! Reference source not found. shows damping factor (ξ) varies from 0.01 to 0.02. The maximum damping factor was found 0.02 in mode1, 5, 6 and 7 and minimum damping factor were found in mode 2, 3, 4 and 8 respectively.
E. Surface crack at 600 with longitudinal axis
A typical plot of experimental results is shown in Fig. 20.
Fig. 20. Experimental results for surface crack at 600 for CCFF boundary
The Fig. 20 shows different magnitude of amplitude, modal frequencies and phase angle at resonance. All the details regarding resonance frequencies, amplitude at resonance, phase angle and Q-factors are also shown in Fig. 20.
The data of amplitude dependency on excitation frequencies are extracted from the Fig. 20. These data is used for drawing Fig. 21 which shows information inclusively on dependency of amplitude with exciting frequency.
Fig. 21. dependency of amplitude with excitation frequency for surface crack at 600
The data of phase angle dependency on excitation frequencies are extracted from the Fig. 20 and drawn a new figure shown in Fig. 22 for the detailed information on phase angle of vibration.
Fig. 22. Dependency of phase angles with excitation frequency for surface crack at 600
The experimental data of table in Fig. 20 are rounded off to nearest number. The amplitude is rounded up to first full number, phase angle rounded up to full number. The frequencies are rounded up to full number and Q-factor rounded up to full number. The rounded off data of frequencies, amplitudes, phase and Q-factors are tabulated and shown in Error! Reference source not found. . The damping factor (ξ) was estimated using formula: ξ=1/2Q. The estimated damping factors (ξ) are tabulated in Error! Reference source not found..
The Error! Reference source not found. highest magnitude of amplitude 95.6g/g at resonance frequency was found in first mode which is 190 Hz. Other lesser magnitude of amplitude was found 27.9, 27.8 and 17.8 g/g at the resonance frequencies of 654, 1051 and 1411Hz in mode 4, 7 and 8 respectively. The other minimum magnitude of amplitude was found 4.9, 1.7, 2.4 and 5.4g/g at the resonance frequencies 291, 523, 707 and 946 Hz in modes 2, 3, 5 and 6 respectively
TABLE VI. AMPLITUDE, MODAL FREQUENCY, PHASE AND Q-FACTOR FOR SURFACE CRACK AT 600
Mode
Amplitu
Modal
Phase (0)
Q-Factor
Damping
1
96
190
-82
49
0.01
2
5
291
-127
63
0.01
3
2
523
141
37
0.01
4
28
654
74
89
0.01
5
2
707
-104
89
0.01
6
5
946
120
11
0.04
7
28
1051
52
21
0.02
8
18
1411
-76
89
0.01
.
The Error! Reference source not found. shows the phase angles at the resonance modes. The phase angles at the resonance modes were found to be 141, 74, 94,120 and 52 at the modes 3, 4, 6 and 7 respectively. The response during these modes is lagging to forcing disturbance. The lagging found to be maximum in mode 6 and minimum in mode 7. The mode angles were found to be -82, -127, -104and -760 at the modes 1, 2, 5 and 8 respectively. The response of the system during negative phase angle represents the leading of the system with respect to disturbing force. The leading was found to be highest in mode 2 and leading of the system gets reduced in modes 1, 5 and 8.
The Error! Reference source not found. shows damping factor (ξ) varies from 0.01 to 0.04. The maximum damping factor was found 0.04 in mode 6 and minimum damping factor was found 0.01 in mode 1, 2, 3, 4 and 5 respectively and also damping factor 0.02 found minimum in mode 7.
F. Surface crack at 800 with longitudinal axis
A typical plot of experimental results is shown in Fig. 23.
Fig. 23. Experimental results for surface crack at 800 for CCFF boundary conditions
The Fig. 23 shows different magnitude of amplitude, modal frequencies and phase angle at resonance. All the details regarding resonance frequencies, amplitude at resonance, phase angle and Q-factor are also tabulated in Fig. 23.
The data of amplitude dependency on excitation frequencies are extracted from the Fig. 23. These data is used for Fig. 24 which shows information inclusively on dependency of amplitude with exciting frequency.
Fig. 24. Dependency of amplitude with excitation frequency for surface crack at 800
The data of phase angle dependency on excitation frequencies are extracted from the Fig. 23 and drawn a new figure shown in Fig. 25 for the detailed information on phase angle of vibration.
Fig. 25. Dependency of phase angles with excitation frequency for surface crack at 800
The experimental data of table in Fig. 23 are rounded off to nearest full number. The amplitude is rounded up to first number, phase angle rounded up to full number. The frequencies are rounded up to full number and Q-factor rounded up to full number. The rounded off data of frequencies, amplitudes, phase and Q-factors are tabulated and shown in Error! Reference source not found. . The damping factor (ξ) was estimated using formula: ξ=1/2Q. The estimated damping factors (ξ) are tabulated in Error! Reference source not found..
TABLE VII. : AMPLITUDE, MODAL FREQUENCY, PHASE AND Q-FACTOR FOR SURFACE CRACK AT 800
Mode
Amplitude
Modal
Phase (0)
Q-Factor
Damping
1
89
168
-84
26
0.02
2
5
259
111
74
0.01
3
3
606
142
50
0.01
4
6
649
94
56
0.01
5
14
862
96
21
0.02
6
11
1044
-49
25
0.02
7
6
1206
-37
32
0.02
8
36
1424
-156
64
0.01
The Error! Reference source not found. shows highest magnitude of amplitude 89g/g at resonance frequency was found in first mode which is 168 Hz. Other lesser magnitude of amplitude was found 14, 10 and 36 g/g at the resonance frequencies of 862, 1044 and 1424Hz in mode 5, 6 and 8 respectively. The other minimum magnitude of amplitude was found 5, 3, 6 and 6 g/g at the resonance frequencies 259, 606, 649 and 1206 Hz in modes 2, 3, 4 and 7 respectively.
The Error! Reference source not found. shows the phase angles at the resonance modes. The phase angles at the resonance modes were found to be 111, 142, 94 and 960 at the modes 2, 3, 4 and 5 respectively. The response during these modes is lagging to forcing disturbance. The lagging found to be maximum in mode 3 and minimum in mode 4. The mode angles were found to be -84, -49, -37and -1560 at the modes 1, 6, 7 and 8 respectively. The response of the system during negative phase angle represents the leading of the system with respect to disturbing force. The leading was found to be highest in mode 8 and leading of the system gets reduced in modes 1and 2.
The Error! Reference source not found. shows damping factors (ξ) varies from 0.01 to 0.02. The maximum damping factor was found 0.04 in mode 1, 5, 6 and 7 and minimum damping factor was found 0.01 in mode 2, 3, 4 and 8respectively.
G. Surface crack at 900 with longitudinal axis
A typical plot of experimental results is shown in Fig. 26
Fig. 26. Experimental results for surface crack at 900 for CCFF
The Fig. 26 shows different magnitude of amplitude, modal frequencies and phase angle at resonance. All the details regarding resonance frequencies, amplitude at resonance, phase angle and Q-coefficients are also tabulated in Fig. 26.
The data of amplitude dependency on excitation frequencies are extracted from the Fig. 26. These data is used for drawing Fig. 27 which shows information inclusively on dependency of Amplitude with exciting frequency.
Fig. 27. Dependency of amplitude with excitation frequency for surface crack at 900
The data of phase angle dependency on excitation frequencies are extracted from the Fig. 26 and drawn a new figure shown in Fig. 28 for the detailed information on phase angle of vibration.
Fig. 28. Dependency of phase on excitation frequency for surface crack at 900
The experimental data of table in Fig. 26 are rounded off to full number. The amplitude is rounded up to full number, phase angle rounded up to full number. The frequencies are rounded up to full number and Q-coefficient rounded up to full number. The rounded off data of frequencies, amplitudes, phase and Q-coefficients are tabulated and shown inError! Reference source not found.. The damping coefficient (ξ) was estimated using formula: ξ=1/2Q. The estimated damping factors (ξ) are tabulated in Error! Reference source not found..
TABLE VIII. AMPLITUDE, MODAL FREQUENCY, PHASE AND Q-COEFFICIENT FOR SURFACE CRACK AT 900
Surface crack at 90
Mode
No.
Amplitude
(g/g)
Modal
Freq.
(Hz)
Phase
(0)
Q-Coefficient
Damping
coefficient (ξ)
1
77
174
-90
37
0.01
2
4
279
-132
74
0.01
3
1
587
178
6
0.08
4
9
661
72
63
0.01
5
5
888
104
20
0.02
6
20
1072
26
20
0.02
7
4
1184
-18
34
0.01
8
7
1225
-28
23
0.02
H. Estimated average magnitude of amplitudes
The Error! Reference source not found. shows estimated average values of magnitude of amplitude from the three different trials for different modes of solid plates and plates with surface cracks oriented in different direction with longitudinal axis of the plates are tabulated in Error! Reference source not found..
TABLE IX. AVERAGE AMPLITUDE RESPONSE OF SOLID & ARBITRARY ORIENTED SURFACE CRACKS
Average Amplitude (g/g)
Solid plate
Surface cracks
Mode No
–
00
200
400
600
800
900
1
92
96
72
52
98
74
77
2
1
3
3
3
3
3
2
3
4
8
1
13
6
2
1
4
34
15
2
13
15
20
4
5
4
16
12
10
1
6
22
6
2
2
10
5
3
5
7
7
10
9
8
3
12
4
2
8
5
18
1
3
7
14
5
The average magnitudes amplitudes tabulated in Error! Reference source not found. are used for drawing bar chart and shown in Fig. 29.
Amplitude (g/g)
Modes
Surface cracks-Amplitude
Solid plate
Surface crack at 0 Degree
Surface crack at 20 Degree
Surface crack at 40 Degree
Fig. 29. Average magnitude of amplitude with modal number of solid & arbitrary oriented surface cracks
The average values magnitude of amplitudes in mode1 for solid plate and plate with surface cracks oriented differently with longitudinal axis of the rectangular plate lies between 92 and 52 g/g. The average magnitude of amplitude in mode 4 for solid plate and plate with surface crack oriented differently with longitudinal axis of the plate lies 34 and 2 g/g. The average value magnitude of amplitudes in mode 2, 3, 5, 6, 7, 8 for solid plate and plate with surface cracks oriented differently with longitudinal axis of the rectangular plate lies between 22 and 1.
In general the fluctuations in magnitude of average amplitudes of vibration of solid plate and plate with surface cracks oriented differently with longitudinal axis of the rectangular plate fluctuates larger extent in mode1 and mode 4. The extent of fluctuation, the magnitude of average amplitude in mode2, 3, 5, 6, 7 and 8 is found to be narrow down compared to the mode1 and mode 4.
The presence of surface crack and its orientation with respect longitudinal axis was found to alter the amplitude of vibration in first mode compared to solid plate. The magnitudes of amplitude in first mode for surface cracked plate were found to be less than solid plate except for 00 and 600 oriented surface crack. This could be attributed to alter the potential energy of the plate due to surface crack. Such generalization not found at higher modes
I. Estimated average magnitude of amplitude
The Error! Reference source not found. shows estimated average values of magnitude of amplitude from the three different trials for different modes of solid plates and plates with surface cracks oriented in different direction with longitudinal axis of the plates are tabulated in Error! Reference source not found..
TABLE X. AVERAGE MODAL FREQUENCIES OF SOLID & ARBITRARY ORIENTED SURFACE CRACKS
Average Modal frequency
Solid plate
Surface cracks
Mode No
–
00
200
400
600
800
900
1
188
183
175
169
191
170
176
2
303
282
397
390
313
281
281
3
504
460
436
432
606
535
412
4
651
649
554
707
670
647
558
5
696
819
733
800
724
741
720
6
835
894
807
929
847
869
816
7
1004
1013
938
1011
1056
1023
926
8
1110
1319
1025
1114
1247
1145
1058
The average magnitudes of modal frequencies tabulated in Error! Reference source not found. are used for drawing bar chart and shown in Fig. 30.
Fig. 30. Average magnitude of modal frequency of solid & arbitrary oriented surface cracks
The average values magnitude of modal frequencies in mode1 for solid plate and plate with surface cracks oriented differently with longitudinal axis of the rectangular plate in the range 169 and 191Hz. The average values magnitude of modal frequencies in mode2 for solid plate and plate with surface cracks oriented differently with longitudinal axis of the rectangular plate in the range 281and 390Hz. The average values magnitude of modal frequencies in mode3 for solid plate and plate with surface cracks oriented differently with longitudinal axis of the rectangular plate in the range 412 and 606Hz.The average values magnitude of modal frequencies in mode4 for solid plate and plate with surface cracks oriented differently with longitudinal axis of the rectangular plate in the range 554 and 707Hz. The average values magnitude of modal frequencies in mode5 for solid plate and plate with surface cracks oriented differently with longitudinal axis of the rectangular plate in the range 554 and 707Hz. The average values magnitude of modal frequencies in mode6 for solid plate and plate with surface cracks oriented differently with longitudinal axis of the rectangular plate in the range 807-and 869Hz. The average values magnitude of modal frequencies in mode7 for solid plate and plate with surface cracks oriented differently with longitudinal axis of the rectangular plate in the range 926 and 1056Hz. The average values magnitude of modal frequencies in mode8 for solid plate and plate with surface cracks oriented differently with longitudinal axis of the rectangular plate in the range 1025and 1319Hz respectively.
The modal frequencies in general increased with mode numbers irrespective of surface crack its orientation. This could be attributed to storing the potential energy due to mode configuration.
J. Estimated average magnitude of Phase angle
The Error! Reference source not found. shows estimated average values of magnitude amplitude from the three different trials for different modes of solid plates and plates with surface cracks oriented in different direction with longitudinal axis of the plates are tabulated in Error! Reference source not found..
TABLE XI. AVERAGE PHASE ANGLE OF SOLID & ARBITRARY ORIENTED SURFACE CRACKS
Average phase angles
Solid plate
Surface cracks
Mode No
–
00
200
400
600
800
900
1
-87
-85
-114
-91
-87
-90
-95
2
-56
49
-59
-61
-154
-75
132
3
39
27
-69
-92
123
-35
-165
4
5
-11
-46
88
49
89
138
5
-93
-13
80
-64
59
-8
65
6
111
-23
-49
112
125
59
-88
7
112
-31
21
100
77
53
112
8
32
-52
39
31
14
0
74
The average magnitudes of modal frequencies tabulated in Error! Reference source not found. are used for drawing bar chart and shown in Fig. 31.
Fig. 31. : Average magnitude of phase angles of solid & arbitrary oriented surface cracks
The average values magnitude of phase angles in mode1 for solid plate and plate with surface cracks oriented differently with longitudinal axis of the rectangular plate lies between -85 and -900. The average magnitude of amplitude in mode 4 for solid plate and plate with surface crack oriented differently with longitudinal axis of the plate lies 5 and 1380. The average value magnitude of amplitudes in mode 2, 3, 5, 6, 7, 8 for solid plate and plate with surface cracks oriented differently with longitudinal axis of the rectangular plate lies between 0 and -1650.
The system irrespective orientation of surface crack was found to lagging in first mode. The phase angle was found to be positive and negative in higher modes. Such behavior also could be attributed to storage of potential energy due to configuration of the plate.
K. Estimated average magnitude of damping factor
The Error! Reference source not found. shows estimated average values of magnitude damping coefficient from the three different trials for different modes of solid plates and plates with surface cracks oriented in different direction with longitudinal axis of the plates are tabulated in Error! Reference source not found..
TABLE XII. AVERAGE MAGNITUDE OF DAMPING COEFFICIENT OF SOLID & ARBITRARY ORIENTED SURFACE CRACKS
Average Damping coefficient
Solid plate
Surface crack
Mode No
–
00
200
400
600
800
900
1
0.01
0.01
0.01
0.02
0.01
0.01
0.01
2
0.04
0.01
0.01
0.01
0.02
0.02
0.01
3
0.01
0.01
0.02
0.01
0.01
0.01
0.04
4
0.01
0.01
0.01
0.02
0.01
0.01
0.02
5
0.01
0.01
0.01
0.01
0.01
0.01
0.01
6
0.02
0.01
0.01
0.01
0.02
0.01
0.01
7
0.01
0.01
0.01
0.01
0.02
0.04
0.01
8
0.03
0.04
0.03
0.04
0.01
0.02
0.03
The average magnitudes of damping coefficient in different modes of vibration are used for drawing bar and shown in TABLE XII. .
Fig. 32. Average magnitude of damping coefficient of solid & arbitrary oriented surface cracks
The average values magnitude damping factor in mode1 for solid plate and plate with surface cracks oriented differently with longitudinal axis of the rectangular plate lies between 0.01 and 0.02. The average magnitude of amplitude in mode 4 for solid plate and plate with surface crack oriented differently with longitudinal axis of the plate lies 0.01and 0.02. The average value magnitude of amplitudes in mode 2, 3, 5, 6, 7, 8 for solid plate and plate with surface cracks oriented differently with longitudinal axis of the rectangular plate lies between 0.01 and 0.04.
The damping coefficient found to be in the order of 0.01 except in the case of in mode 2 of solid plate and surface crack with arbitrary oriented 900 in mode 3 and surface crack with arbitrary oriented 40 in mode 4 and surface crack with arbitrary oriented 400 and 900 in mode 4 and surface crack with arbitrary oriented 600 in mode 6 and surface crack with arbitrary oriented 800 in mode 7 and surface crack with arbitrary oriented 00 and 400 in mode 3
IV. CONCLUSION
❖ The amplitude of vibration was found to be influenced by the surface cracks and its orientation with respect to longitudinal axis.
❖ The modal frequencies, irrespective of cracks and its orientations, in general increased with mode number.
❖ The system was found to be lagging in mode 1and both lagging and leading in other modes,
❖ The redistribution of potential energy which depends on the mode configuration was found to be a factor influencing the dynamic response.
REFERENCE:
[1] Vibration analysis of plates with one free edge using energy method (CCCF plate). Ibearugbulem et al. s.l. : International journal of engineering and technology, 2014, Vols. 4, No.1.