
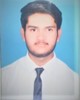
- Open Access
- Authors : Raja Ram Dadhich , Prachi Goswami
- Paper ID : IJERTV11IS100055
- Volume & Issue : Volume 11, Issue 10 (October 2022)
- Published (First Online): 21-10-2022
- ISSN (Online) : 2278-0181
- Publisher Name : IJERT
- License:
This work is licensed under a Creative Commons Attribution 4.0 International License
Review on Improving Coil Tubing Life using Nano Coating Technology
Raja Ram Dadhich, Prachi Goswami
Oil Field Warehouse services Pvt. Ltd.
Abstract:- Most mechanical losses in engineering materials are caused via fatigue failure, corrosion, erosion and manufacturing defects. In order to examine the effect of nano coating layers on steel coiled tubing life, this study aimed to coat steel bars using the nano-coating techniques. In the most of nanotechnology labs, titanium dioxide TiO2, silica dioxide (SiO2), graphene-, and carbon nanotube (CNT)-based nanocoating systems are used., The coating process is carried out at various coating times to produce coating layers of varying thickness. The outcomes of fatigue testing on coated samples strongly imply that samples with long-lasting coatings (a thick layer of coat) have a better fatigue life, which may be up to four times longer than that of uncoated samples.
Keywords: Fatigue, Fatigue Life, Steel Bars, Nano-Coating Technology
INTRODUCTION
The working life of the CT may be defined as the duration of service for the continuous-tubing string when subjected to the following conditions:
-
Bend-cycle fatigue
-
Corrosion
-
Mechanical damage
The concept of fatigue is the collapse of a component during cyclic loading before its ultimate stress. Theories of failure describe the factors that contribute to failure. The element will fail when external stress is greater than the component's allowable maximum value for tensile, compressive, or shear stress. In the occurrence of a fatigue failure, the failure will take place significantly earlier than the design stress's maximum value. Fatigue describes the characteristics that can change in a metallic substance as a necessary consequence of repetitive application of stress and strain, particularly to those changes which lead to failure or cracking. (Shine
U. et al)
The bend-cycle fatigue life of a CT string is also sensitive to surface damage, such as: Scars, Scratches, Gouges, Dents. These types of mechanical damage serve as localized stress-strain concentrations where repeated bend cycling can cause cracks to develop in the tube body.
Unpredictable coiled tubing (CT) service life is not acceptable in the CT industry and is not tolerated by the customer. Experience shows that service life becomes unpredictable without adequate tubing maintenance programs that include corrosion prevention. Therefore, monitoring and maximizing CT service life requires effective corrosion control on both inside and outside CT surfaces from the time the tubing string is milled until it is retired.
Masao Kikuch et al. observed that shot pining with surface structural anomalies (internal oxides precipitated along the grain boundaries and accompanying non-martensitic morphology near the surface) increased the fatigue durability of carburized steels (Masao Kikuchi. Et al.).
On type 304 stainless steel, Xu Chen et al. conducted low-cycle fatigue tests with axial/torsional, torsional/axial, in phase /90o- out of phase, and 90o-out of phase /in phase loading cycles. In accordance with the results, cross hardening occurs during axial/torsional loading but not when axial/axial loading (Xu Chen et al.).
Using gas-carburized, modified Brugger, and genuine ring and pinion gears, Jason J. SPICE et al. assessed three methods to increase the life of bending fatigue. For high cycle fatigue, the gaz-carburized did not provide any improvement in fatigue life, whereas other techniques did. (Jason J Spice. Et al. Optimized Carburized Steel Fatigue Performance as Assessed with Gear and Modified Brugger Fatigue Tests).
Yasir, Ali S. studied When the influence of cooling rate on the fatigue life of heated steel bars was studied, it was discovered that samples that cooled with a medium cooling rate (by oil) had the best fatigue life, while samples that cooled with a high cooling rate had the lowest fatigue life (by water and brine). (Ali S. Yasir & Vol.3).
NANO COATING TECHNOLOGY
Nanotechnology is the manipulation or self-assembly of individual atoms, molecules, or molecular clusters into structures to create materials and devices with novel or vastly different properties. Nanotechnology can operate from the top down (reducing the size of the smallest structures to the nanoscale, as in photonics applications in nanoelectronics and nanoengineering) or from the bottom up (which involves manipulating individual atoms and molecules into nanostructures and more closely resembles chemistry biology). (Jayanta Kumar Behera).
Nanocoating is one of the most important topics in the field of nanotechnology, as it involves the nanoscale engineering of surfaces and layers. Many synthesis techniques for producing nanostructure coatings have been developed, including sputtering, laser ablation, sol/gel technique, chemical vapour deposition, gas condensation, plasma spraying, and electrochemical deposition. (Abdel-Karem R. et al).
A.Mubarak et al. use the physical vapour deposition method to investigate the effect of coating thickness on the properties of (TiN) on tool steel (high speed steel H.S.S). The hardness of highspeed steel was increased by this coating. (Mubarak. A. et al.) L.Ipaz et al. improved the mechanical and tribological properties of AISI D3 steel surfaces by coating them with a multilayer system of (Ti-Al/Ti-Al-N). The results show an increase in steel hardness, toughness, and elastic modulus. (Ipaz. L. et al).
Ms. Jennifer Hay, When Titanium-nitride coating is applied to tool steel to improve mechanical properties, the surface hardness and modulus of elasticity improve (Jennifer Hay).
Shiva Rama Kreshna, D. Using a stainless steel (TiO2) coating to improve the tribological and corrosion properties of austenitic stainless steels. The results show an increase in hardness, an increase in corrosion resistance, and an improvement in wear resistance. (Siva D. et al.)
COATING METHOD
Coating Method Another factor affecting the corrosion properties of the nanocoating is the coating method. Nanocoating can be obtained with one of the thin film deposition methods. The coating method defines the surface topography, which greatly influences the nanocoating properties. Nanocoating can be prepared by different methods, and electrodeposition is the most used technique for metallic nanocoating so far. Electrodeposition is the deposition of a metal or alloy coating over a conducting surface by means of electrolysis from a well-formulated electrolyte, which is known as bath. Dense and pores-free coating is produced with this technique compared to other methods, which would create lots of pores and grain boundaries. Electrodeposition can be performed with either a direct or pulse current. Pulse electrodeposition was shown to enhance deposit properties such as porosity, ductility, hardness, and surface roughness. Nano crystalline zinc deposits that were pulse electrodeposited were more homogenous; they also had a finer-grained surface and a higher number of the lattice imperfections compared to the direct current electrodeposition. This was due to the higher and instantaneous current density during pulse deposition, which increased the nucleation rate and thus led to the formation of finer grains. Figure (1ad) shows that direct current had a higher size of grains and agglomerated crystals, while an optimal current density of 0.2 A/cm2 produced the lowest size of agglomerated particles, which was tested to produce good corrosion behaviour (e). Moreover, nanocrystalline NiCu alloy coating also obtainedbetter corrosion resistance through pulse electrodeposition compared to direct electrodeposition, both in aerated and deaerated environments.
fig.1(ad) shows that direct current had a higher size of grains and agglomerated crystals, while an optimal current density of 0.2 A/cm2 produced the lowest size of agglomerated particles, which was tested to produce good corrosion behaviour (e)."Materials | Free Full-Text | A Review on the Corrosion Behaviour … – MDPI." 10 Jan. 2019, https://www.mdpi.com/1996-1944/12/2/210.
TYPES OF NANO COATING SYSTEMS (Weiwei Bao, 2019)
In this review, we will introduce mainstream nanocoating, its challenges, and applications, including the silica dioxide (SiO2), titanium dioxide (TiO2), graphene, and carbon nanotube (CNT)-based nanocoating systems.
Nanocoating Based on SiO2
Silicon dioxide, one of the most complex and abundant families of materials, exists as a synthetic product as well as a mineral compound. In 2002, the first commercial-grade surface-modified silica nanoparticles with a very narrow particle size distribution were introduced into epoxy resin via a modified sol-gel process. Many metal-O-Si bonds were formed on the surface of the substrate, which not only supplemented the good physical barrier effect, but also improved the adhesion force between the coating and the substrate. Silica's inherent hardness and chemical resistance, as well as its alteration characteristics, enable nanoSiO2 particles in coatings to improve properties such as modulus, stiffness, toughness, scratch resistance, and anticorrosion. Conradi et al. applied a 0.5 kg load to the surface of pure epoxy and a 130 nm SiO2/epoxy coating separately, and found that the indents in the epoxy coating were significantly larger than those in the SiO2/epoxy coating, and the hardness was increased by nearly 40%. (Conradi et al., 2013). The incorporation of Nano-SiO2 into the coatings significantly influenced the morphology, with the area roughness parameters Sa ranging from 16 to 329 nm. This influenced the surface hydrophobicity with the WCA ranging from
84.6 to 94.2. Surface roughness may affect hydrophobicity by trapping air between the surface and the water droplet, which can reduce contact area by creating micro/nano structures. The nano-SiO2/epoxy coating with enhanced anti-corrosion properties resulted from improved hydrophobicity. As discussed in the section ZnO-Based nanocoating, coating hydrophobicity plays an important role in anti-corrosion; thus, modifying nano-SiO2, resulting in a nanocoating with super hydrophobicity and improved compatibility, can significantly increase the nanocoating corrosion resistance. Ye and colleagues recently compared the performance of various nano-SiO2 based coating systems, including electrodeposited oligoaniline modified silica/epoxy coating (E-M-SiO2) and electrodeposited pure silica coating/epoxy coating (E-P-SiO2) (E-SiO2). The E-M-SiO2 coating demonstrated super hydrophobicity with a WCA of 167, whereas E-SiO2 demonstrated hydrophobicity with a WCA of 143.5. (Ye et al., 2018). Because super hydrophobicity could inhibit the diffusion of corrosive medium, E-M-SiO2 coating provided better corrosion protection than E-SiO2. The author also compared the performance of E-M-SiO2 with sol-gel oligoaniline modified silica/epoxy coating (M-SiO2), finding that E-M-SiO2 performed better in terms of hydrophobicity and corrosion protection. This could be because most silica coating obtained by sol-gel approach has low surface roughness, which severely limits coating thickness, and thus the physical barrier of pre-process coating was weak. When a conventional coating is damaged, there is no protective effect; protection only lasts for the first damage. Kongparakul's group reported incorporating self-healing microcapsules, such as perfluorooctyl triethoxysilane-urea-formaldehyde (POT-UF) shell, ethanolamine-polystyrene (ETA-PS) shell, or diethanolamine- polystyrene (DEA-PS) shell, into the modified nano-silica/epoxy nanocoating and improving the coating anti-corro (Kongparakul et al., 2017). The POT-UF shell microcapsules performed the best corrosion prevention of the three systems due to the increased length of the diffusion pathways and decreased oxygen permeability of the coating. Other methods, such as using nanocontainers, self-healing additives, layer-by-layer deposition, and so on, could also be used to create self-healing nanocoating (Shchukin et al., 2006; Li et al., 2013). The hydrophobic coating is unstable and easily loses its ability to repel water (Zhang et al., 2006). As a result of its long-term protection properties, self-healing coatings combined with superhydrophilicity behaviour are promising. TiO2 Coating
Titanium dioxide, one of the most common oxides of titanium, has received a lot of attention due to its readily available, relatively inexpensive, chemical stability, and harmless nature, which has been widely applied in a variety of fields such as paints, coatings, inks, and so on (Munaf et al., 2015). Incorporating nano-TiO2 into coating systems can improve the nanocoating's protection and even endow it with self-cleaning properties. Shen et al. reported that coating the surface of 316L stainless steel with uniform TiO2 nanoparticle films could significantly improve its corrosion resistance, with corrosion resistance increasing by three orders of magnitude (Shen et al.,2005). The protection mechanism of TiO2-based nanocoating is that when nano-TiO2 is exposed to UV- irradiation, electrons are generated in the coating and transferred to the metal substrate, making its electrode potential more negative than its corrosion potential, while TiO2 is not consumed. A nano-TiO2-based coating with anti-corrosion properties is promising. The protection mechanism, however, suggests that pure TiO2 nanocoating cannot be used in low-light conditions due to the photo effect. Furthermore, once small defects appear in the nanocoating, the nanocoating is no longer able to protect the exposed zone, implying that the nanocoating only works until its surface is intact. Several studies have attempted to address this issue by modifying nano-TiO2 coatings with noble metal deposition, doping of metallic and non-metallic ions, and so on (Hoffmann et al., 1995; Park and Choi, 2004). Yun et al. (2007) reported TiO2-nanocoating without photo-effect using doped TiO2 with N, S, and Cl. For the various coating systems, electrochemical polarisation was performed in 0.5 M NaCl solution under dark conditions.
When compared to bare 316L, the pure TiO2-nanocoating slightly improved corrosion resistance, whereas the dopant-modified TiO2 coating significantly improved corrosion resistance. This could be because the modified nano-TiO2 coating eliminates the photo effect.
Other studies on nano-TiO2 particle modification to improve nanocoating corrosion resistance have been reported, such as polypyrrole/Sn-doped TiO2, thermal oxidation, and introducing polyaniline into the coating system (Krishna and Sun, 2005; Radhakrishnan et al., 2009; Mahmoudian et al., 2011).
Normally, TiO2 is hydrophobic. However, when exposed to UV light, it becomes both oleophilic and hydrophilic, decreasing the organic liquid angle or WCA until organic liquids or water droplets on the surface are almost completely flattened. This property prevents external dirt from directly contacting the coating surface, making stain removal easier. Spraying the nano-TiO2 product
directly on the stone surface with different amounts resulted in a single-layer (SL) and three-layer (ML) treatment nanocoating (Goffredo et al., 2013). Under UV illumination, there was no significant degradation of stains on untreated surfaces, whereas photocatalytic degradation of the strain was very rapid for the SL and ML coatings, with the rhodamine B losing nearly 50% of its original colour after 4 hours. Because TiO2-based nano coatings are transparent, they can be applied directly to architectural surfaces for protection without changing their appearance. Severa studies on the incorporation of TiO2 nanoparticles into various coating systems to improve self-cleaning performance have been published (Kaplani et al., 2015; Crupi et al., 2018). The system investigated the relationship between self-cleaning and the size or amount of nano-TiO2, but further optimization of the nano- TiO2 particles and extending the coating's lifepath remain a challenge.
Carbon (Graphene and Carbon Nanotube)-Based Nanocoating
Because of their inherent properties, such as high stiffness and conductivity capacity, nanoscale carbon, graphene, and CNT have the potential to be useful as nano coatings in materials protection (Hu et al., 2014). Chen et al. successfully used as-grown graphen for the first time to protect the surface of a metallic growth substrate of Cu or Cu/Ni alloy from air oxidation (Chen et al., 2011). The covered graphene resulted in metal pass0069vation beneath, providing an inserted block between the reactants and the protected metal. Aside from oxidation resistance, graphene-based nanocoating could also significantly improve thermal stability and corrosion resistance. Kwon et al. used graphene and metal-chloride-doped graphene over layers on 25 um thick copper foil, where chlorine evaporation was almost completely blocked, and the doped state was maintained even after thermal annealing (Kwon and Kim, 2014). Yu and colleagues applied graphene, typically metronidazole-modified graphene oxide, to the metal surface, which demonstrated greater corrosion resistance than bare metal (Yu et al., 2016).
It should be noted that graphene provides an excellent oxidation barrier in the short term; however, on larger scales, graphene promotes metal corrosion rather than preventing it. Under ambient conditions, Schriver et al. compared the sample surfaces of bare Cu and graphene-coated Cu for up to 2 years (Schriver et al., 2013). The results showed that after two years, the bare Cu's colour changed slightly. Within one week, the graphene-protected Cu was shiny and oxide-free. However, after 1 month, the surface began to tarnish unevenly with small patches, resulting in high oxide after 5 months. Finally, at 18 months, heavy oxidisation was observed on nearly all of the surface. Non-uniform oxidation or defects in graphene cause stress and cracking of the oxidation layer, which frequently opens a new path for corrosion. Furthermore, wetting transparency was frequently observed in monolayer graphene (Hu et al., 2014). As a result of these characteristics, monolayer graphene has poor protection properties. To address this issue, multi-layered graphene or nanocomposite materials, such as epoxy mixtures, were used, and they demonstrated good protective performance (Rafiee et al., 2012; Tang et al., 2013).
The irregular microstructure formed by randomly stacked fluorographene was attributed to the super hydrophobicity of this nanocoating. CNT, graphene allotropes, was used in coating effect protection performance, typically on anti-oxidation and corrosion resistance. According to recent research, CNT-based nano coatings perform similarly to graphene-based nano coatings in terms of protection (Janas and Koziol, 2013). In many cases, the CNT not only acts as a physical barrier to the corrosion process, but it also improves the electrochemical properties to anti-oxidation (Ates, 2016). Frankel's group reported epoxy composite coatings filled with different multiwalled CNT contents, indicating that multiwalled CNT can influence coating performance such as improving adhesion strength, increasing wear resistance, and increasing total impedance (Khun et al., 2013). Nano coatings containing modified CNT composites should be on the rise.
CONCLUSION
Strength
The improving in fatigue life of rotating steel bar/coil may be reached to more than couple of times as nano-coat will reduce the ability to initiation and growing of micro cracks on the steel bar surface that may causes the fatigue failure.
Heat Insulation
The surface temperature of nano heat insulation sheet is about 40 °C and the indoor temperature is about 33.5 °C. Because the spectral reflective film can reflect 85% of the ultraviolet rays, both outdoor and indoor temperatures of the nano thermal insulation board are much lower.
Corrosion Resistance
The anti-aging protective film on the surface of the nano anti-corrosion sheet is intact. Nano steel has super acid, alkali, and corrosion resistance. It is suitable for chemical plants, oil and gas, and other harsh use environments. Nanoparticle materials have specific physical, chemical and physicochemical properties so it is improved corrosion protection compared with bulk size substances.
REFERENCES
[1] "(PDF) Next-Generation Composite Coating System: Nanocoating – ResearchGate." 17 Apr. 2019, https://www.researchgate.net/publication/332467920_Next-Generation_Composite_Coating_System_Nanocoating. [2] "(PDF) ON THE IMPROVEMENT OF THE FATIGUE BEHAVIOUR OF AUSTENITIC …." 04 Aug. 2008,https://www.researchgate.net/publication/233856101_ON_THE_IMPROVEMENT_OF_THE_FATIGUE_BEHAVIOUROF_AUSTENITIC_STAI NLESS_STEELSDUE_TO_SURFACE_RESIDUAL_STRESSESPRODUCED_BY_LOW_TEMPERATURE_CARBURIZING.
[3] "A Review on the Corrosion Behaviour of Nano coatings on Metallic Substrates." https://www.academia.edu/48835577/A_Review_on_the_Corrosion_Behaviour_of_Nano coatings_on_Metallic_Substrates. [4] "Biosorption of Pb(II) And Zn(II) from aqueous solutionusing langsat …." https://www.jocpr.com/articles/biosorption-of-pbii-and-znii-from-aqueous- solutionusing-langsat-lansium-domesticum-corr-fruit-peel.pdf. [5] "Boardman, B. (1990) Fatigue Resistance of Steels. In ASM Handbook …." https://www.scirp.org/reference/referencespapers.aspx?referenceid=2666228. [6] "Conducting polyanilinenano-TiO 2 composites for smart corrosion …." 30 Jan. 2009, https://www.researchgate.net/publication/244154163_Conducting_polyaniline-nano-TiO_2_composites_for_smart_corrosion_resistant_coatings. [7] "Dowell-Handbook CT CLIENT SCHOOL.pdf – COILED TUBING CLIENT…." https://www.coursehero.com/file/30992779/Dowell-Handbook-CT- CLIENT-SCHOOLpdf/. [8] "EFFECT OF COATING THICKNESS ON THE PROPERTIES OF TiN COATINGS DEPOSITED …." 25 Sept. 2019,https://www.worldscientific.com/doi/10.1142/S0218625X08011524.
[9] "Electrochemical corrosion behavior of pulse and DC electrodeposited Co …." 15 Jan. 2012, https://www.sciencedirect.com/science/article/abs/pii/S0257897211009601. [10] "Fatigue Failure – an overview | ScienceDirect Topics." https://www.sciencedirect.com/topics/engineering/fatigue-failure. [11] "Fatigue Failure of Structural Steel – Analysis Using Fracture Mechanics." 01 Jan. 2008, https://www.researchgate.net/publication/242569600_Fatigue_Failure_of_Structural_Steel_-_Analysis_Using_Fracture_Mechanics. [12] "Fatigue Failure of Structural Steel Analysis Using Fracture Mechanics." https://citeseerx.ist.psu.edu/viewdoc/download?doi=10.1.1.307.3692&rep=rep1&type=pdf. [13] "Fatigue life prediction of type 304 stainless steel under sequential …." 01 Mar. 2006, https://www.sciencedirect.com/science/article/abs/pii/S0142112305000976. [14] "Improved corrosion behavior of nanocrystalline zinc produced by pulse …." 01 Jan. 2004, https://www.sciencedirect.com/science/article/abs/pii/S0010938X03001422. [15] "Improvement of mechanical and tribological properties in steel surfaces …." 01 Feb. 2012, https://www.sciencedirect.com/science/article/pii/S0169433211019246. [16] "M.R. Hoffmann, S.T. Martin, W. Choi, D.W. Bahnemann, Environmental …." http://www.sciepub.com/reference/301166. [17] "Nano Coated Steel | Heat Insulation | Anti-corrosion Metal." https://wzppgi.com/nano-coated-steel/. [18] "NanoTech Coatings – Metal Coating." https://www.nanotechcoatings.com/proucts/metal-coating/. [19] "Nanotechnology | NIOSH | CDC." https://www.cdc.gov/niosh/topics/nanotech/default.html. [20] "Optimized Carburized Steel Fatigue Performance as Assessed with Gear …." 04 Mar. 2002, https://www.sae.org/publications/technical- papers/content/2002-01-1003/. [21] "Publications – Assistant Professor Suwadee Kongparakul – Google." https://sites.google.com/site/skongparakul/publica. [22] "Search Petrowiki: Coiled tubing fatigue | SPE." https://search.spe.org/i2kweb/SPE/search?filters=store%3APetrowiki&sort=score+desc&q=Coiled+tubing+fatigue. [23] "Study the Effect of Cooling Rate on Fatigue Strength and Fatigue Life …." https://www.academia.edu/18179220/Study_the_Effect_of_Cooling_Rate_on_Fatigue_Strength_and_Fatigue_Life_of_Heated_Carbon_Steel_Bars. [24] "SYNTHESIS AND CHARACTERIZATION OF ZnO NANO-PARTICLES." http://ethesis.nitrkl.ac.in/182/1/final_final_jayanta_thesis.pdf. [25] "What Is Nanotechnology? | National Nanotechnology Initiative." https://www.nano.gov/nanotech-101/what/definition. [26] "Mechanical Evaluation of Titanium Nitride Coated Tool Steel – KLA." https://www.kla.com/wp-content/uploads/KLA_AppNote_TiN_on_Steel.pdf. [27] "Simple fabrication of zinc oxide nanostructures." https://www.researchgate.net/profile/Fadong- Yan/publication/248841463_Simple_fabrication_of_zinc_oxide_nanostructures/links/0deec524c5b12c75a1000000/Simple-fabrication-of-zinc-oxide-nanostructures.pdf.
[28] "Thermally oxidised rutile-TiO2 coating on stainless steel for …." 15 Nov. 2005, https://www.sciencedirect.com/science/article/abs/pii/S0169433205002679. [29] "Machine Design – DocShare.tips." 01 Mar. 2010, http://docshare.tips/machine-design_5a85fc7d08bbc59a11718c8c.html. [30] "(PDF) Nano coatings – ResearchGate." 22 May. 2013, https://www.researchgate.net/publication/300623340_Nano coatings.