
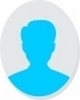
- Open Access
- Authors : Vigneshwara K B , Yugendheran K T , Justin Joseph , Adithya N
- Paper ID : IJERTV11IS100038
- Volume & Issue : Volume 11, Issue 10 (October 2022)
- Published (First Online): 27-10-2022
- ISSN (Online) : 2278-0181
- Publisher Name : IJERT
- License:
This work is licensed under a Creative Commons Attribution 4.0 International License
Performance Analysis of Tidal Turbine Blades for Different Composite Materials
Vigneshwara K B
Department of Mechanical Engineering Chennai Institute of Technology Chennai, India
Yugendheran K T
Department of Mechanical Engineering Chennai Institute of Technology Chennai, India
Justin Joseph
Department of Mechanical Engineering Chennai Institute of Technology Chennai, India
Adithya N
Department of Mechanical Engineering Chennai Institute of Technology Chennai, India
Abstract:- In recent times, tidal turbines have been massively cutting-edge in using the dynamic energy of water flows to deliver electrical energy. The edge has consistently been the principal censuring portion of the tidal turbines as well. The design of the chord, the aerofoil, and the twist distribution over the blade are such that the turbine has perpetual conduction across a vast period. Tidal turbine blades are exposed to an enormous thrust and torsional loading due to the high density of the seawater in which they perform. These thrust loadings result in high bending moments at the blade root, which can end up being a genuine design requirement for these gadgets and can have suggestions regarding cost- economic and adaptability. The tidal turbine blade materials have to be chosen correctly to attenuate the deterioration of the material. This chapter presents the degradation of tidal turbine blades as well as finite element analysis of FRP composites such as CFRP, GFRP, and AFRP in a hydrothermal setting using Ansys Tools. We conclude that degradation affects the tidal turbine blades after accounting for the unavoidable uncertainties and thus the foremost suitable materials for the manufacture of blades are the engineered materials like the FRP composite, among which, CFRP is endorsed by most turbine developers.
KeywordsCAE Analysis, Composites Finite Element Analysis Hydrothermal, Tidal Turbinenent
-
INTRODUCTION
The tidal turbine is the most emerging way of renewable power generation. A tidal stream is a quick streaming waterway made by tides. A turbine is a machine that takes energy from a progression of liquid in which the fluid can be liquid (water) or air (wind) [1]. Since water is notably denser than air, tidal energy is more prominent than wind energy. Unlike wind, tides are predictable and stable. While we use the flow of water to run the turbine, it might raise some ruckus to the propeller, and the perennial interaction between the water and propeller causes layers of greenery on the propellers which causes extra load on the propeller. And due to this supplementary load, the productivity of electrical energy reduces [2]. The significant obstacle to the advancement of tidal ranches is their expense of upkeep. To decrease the development of greenery on the propeller, we need to select the material accordingly. As they have less resistance, tidal turbines ought to be conveyed at destinations with solid conditions (high flows, choppiness, waves, and tempests). Besides, the tidal turbine components
will be exposed to different marine animosities, for example, biofouling, disintegration, and consumption. Therefore, selecting the aptest material for tidal turbine blades in such a critical environment is vital to reduce the risks of error, minimize the costly maintenance load, and prolong their service periods (by more than 25 years) [3]. FRP has many potentials such as light weight, weakness obstruction, high elasticity, hostility to erosion, and warm protection. FRP should be the most adequate material for the propeller cutting edge to be erosion liberated from moss. In this chapter, we will examine the consumption of greenery on the propeller cutting edges, the harm brought about by them, and the investigation of quality will be shown. We will discuss the FRP (Fiber-Reinforced Polymer) composites on the propeller, and then the improvements brought by the FRP composites [4]. After the investigation of both, we will analyze the FRP composites on the sharp edges of the tidal turbine using the Ansys analysis software. The FRP composites include Carbon Fiber-Reinforced Polymer (CFRP), Graphite Fiber-Reinforced Polymer (GFRP), and Aramid Fiber-Reinforced Polymer (AFRP). The recorded composite materials are examined and the visits underneath will clarify the contrast between each composite and between structural steel, and we will settle for the best material for the propeller in the turbine.
-
LITERATURE SURVEY
-
ZhaoCheng Sun et al (2021). This paper discusses the Performance optimization and investigation of flow phenomena on tidal turbine blade airfoil considering cavitation and roughness, the submerged pollutant and cavitation that could fundamentally affect the streamlined exhibition of flowing turbine edge airfoil As a result, it is important to consider both harshness and cavitation during the time spent on optimization plan
.
-
Emadelddin Hassan, Lasones Zekos et al. (2021). This paper explains the Use of glass fiber reinforced polymer used in turbine blades, and its ability to harness the energy from tidal sources.
-
Christophe Floreani, Colin Robert, Parvez Alam et al. (2021). This paper discusses the Advantages of using powder epoxy composites and its ability to carry out separate melting and curing operations. This paper also highlights the risk of delamination when powder epoxy structures are manufactured.
-
Mitchell G. Borg, Qing Xiao, Steven Allsop et al. (2021). This paper explains The design and evaluation of turbine rotors in hydrodynamic conditions by means of numerical analysis with an analysis of Distinct Fiber-composite internal blade designs to establish the structural response.
-
Hassan Gonabadi, Adrain Oila, Arti Yadav et al. (2021). This paper discusses The use of glass fiber composite rather than carbon fiber composite blade of similar design in order to maintain the safety factor. Finite element analysis is conducted to conclude the research.
-
Guisser, Meryem et al. (2021). This paper discusses Composite materials used in turbine blades and study of structures behavior in unsteady environments. The fatigue behavior of each material is analyzed.
-
Jelle Joustra, Bas Flipsen, Ruud Balkenende (2021). This paper states that composite materials, in particular fiber-reinforced polymers, present a challenge when reaching their end of life. Current recycling processes are unable to attain high-end material quality, thus challenging the (re)use of composite materials in a circular economy.
-
ImadShakirAbbood et al (2020). This paper explains the Properties evaluation of fiber reinforced polymers and their constituent materials used in structures. Rivalry in structural designing business sectors typically forces minimal effort, low-thickness, and naturally safe materials with least upkeep and stretched-out assistance life highlights to withstand the undesired cut-off stacking and forceful ecological conditions. Subsequently, utilizing progressed composite materials as building up for various constructions have grown acceptably in past many years through new development and recovery applications. Fiber supported polymers as composite materials are incredible fortifying strategies for different underlying applications and have been the primary concentration for some analysts in the most recent years due to their previously mentioned properties.
-
Indraneel R. Chowdhury, Noel P. ODowd et al. (2021). This paper discusses Non-crimp fibre (NCF) based reinforced composite materials with e-glass nd carbon fibres used as main materials for blades.
-
William Fillnegen, Ronan Allen, Conor Glennon, James Maguire et al. (2021). This paper describes how, after wind and sun oriented energy, flowing energy presents the most noticeable chance for producing energy from inexhaustible sources. Nonetheless, because of the harsh climates that flowing turbines are exposed to, various plan and production challenges are introduced to engineers.
-
Mitchell G. Borg et al (2020). The paper depicts the unique investigation of A numerical performance analysis of a ducted, high-solidity tidal turbine three blade even flowing turbine in approval of three particular boundaries: power and torque coefficient. Thrust coefficient and wake velocity profiles – the mathematical results of the principle execution variables of the full-scale ducted turbine, depicting a peak power coefficient of 0.34 with a thrust coefficient of 0.97 at an ostensible tip-speed ratio of 1.75 – were found out to legitimize the pertinence of the full-scale examination.
-
H.M. Su (2020). In their work titled Reliability analysis of composite wind turbine blades considering material degradation of blades, a bunch of logical strategies were proposed to assess the unwavering quality of composite wind turbine blades after material aging and to improve the blade structure solidarity to upgrade its reliability. The dependability assessment technique utilized in this investigation is the immediate mix strategy, which can rapidly assess the dependability of blades corrupted by materials. The impact of time on the material is thought of, and the relationship between time-material strength and time-material constant is tentatively.
-
J.S. Walker et al (2020). They investigate The effect of a barnacle-shaped excrescence on the hydrodynamic performance of a tidal turbine blade section. Proficient flowing turbine plans depend upon the hydrodynamic presentation of the turbine's sharp edge areas. A significant thought for the probable power age limit of a flowing turbine is the impact of biofouling on the sharp edge execution. This paper considers the instance when a barnacle connects to the upper (pull) surface of the sharp edge segment.
-
William Finnegen, Edward Fagan, Thomas Alanagan et al. (2020). This paper explains The study which uses advanced computational fluid dynamics and needs to explore a model for operational fatigue loads induced on tidal turbine blades.
-
Colin Robert, Toa Pecur, James M. Maguire et al. (2020). This paper explains The powder-epoxy towpregging process for both carbon and basalt
fibres and testing of two basalt fibres compared to glass fibre composities.
-
-
MATERIALS
The blades play a major role in the efficiency of the tidal turbine. Therefore, the material using which the blades are manufactured can be amended in order to improve its performance drastically. Here, we compare four materials, namely structural steel, CFRP, GFRP, and AFRP to determine the best alternative to structural steel.
-
STRUCTURAL STEEL
It is also one of the other broadly utilized building materials in the construction sector, as well as the most learned and best acknowledged. Structural steel is 100% recyclable and perhaps one of the many highly reused materials around the globe [5]. Steel can be various such as carbon steel, heat-treated carbon steel, high-strength low- composite steel, and warmth-treated constructional combination steel. Structural steel below the sustained effect of operational aspects such as temperature, cyclic loads, pressure, radiation, and the surrounding can precede embrittlement as an outcome of thermal aging and corrosion damage as well as fatigue.
-
CFRP
CFRP is a tremendously solid, profoundly conductive, and light-weight FRP. There are no limitations to its application. The common applications are in the field of Automotive, Aerospace, Robotics, Civil Engineering, Sports and Leisure Sector, and Wind and Tidal Energy for Turbines [6]. CFRP is one of many composites using which strengthening of concrete structures as well as repairing can be done. Environmental effects such as humidity and temperature have intense effects on the FRP composites.
-
GFRP
Graphite fibers have the advantage of high surface area. Because of a high surface area, it can generate a maximum power of 68.4 W/m cubes and it has low ohmic resistance which improves the efficiency of the turbine [7]. Graphite fiber-reinforced metal has been developed with a combination of properties like stiffness, strength, thermal conductivity, and electrical conductivity. This improves the underlying attributes.
-
AFRP
Aramid fibers are most commonly known as Kevlar fibers. Aramid fibers are more expensive compared to glass fibers. Impact-resistant structural products such as body armor are usually manufactured with these materials [8]. The excellence of AFRP is its advanced impact properties, significantly lower fiber elongation, high firmness, higher tensile strength, high rigidity, high modulus, low gauge, and thickness, as well as good high-temperature properties. Long Aramid fibers bonded with resins are anticipated to be applied as concrete reinforcement displacing steel.
-
-
METHODOLOGY
With the help of the CAD software, the tidal turbine blade is drawn and is used as a modeling part in different analyses in Ansys software, where the turbine blade is researched for different tests like stress, strain, equivalent stress (von misses) and fatigue [9]. The modal analysis is also done for the turbine blade. The behavior of the turbine blade is analyzed for structural steel, CFRP, GFRP, and AFRP after observing the reaction of the blade to the given input parameters in the Ansys software [10]. A comparative study is made between these materials about how they would react to the same environment when tested under the same properties and conclusions are drawn.
-
Von Mises Stress
von Mises pressure is a worth used to decide whether a given material will yield or crack. The von Mises yield basis expresses that if the von Mises pressure of a material under load is equivalent to or more prominent than the yield furthest reaches of a similar material under straightforward strain, then the material will yield. Table 1 shows the von Mises stress for various materials.
S
. N
o
Mat erial
Analysis Result
Von Mises Stres s
1
Struc tural Steel
1.079
3e+10
2
GPF P
1.084
8e+10
Table I. Von Mises Stress for Various Materials
3
CRP F
1.081
9e+10
3
CRP F
0.056
366
4
ARF P
1.083
7e+10
4
ARF P
0.066
066
-
Total deformation
Total deformation The behavior of the structural steel and CFRP under a cantilever load of 5000 N is given below. The maximum and minimum effects of the force can be seen in the image. Table 2 shows the Total deformation for various materials.
Table II. Total deformation for Various Materials
-
Normal Stress
A typical pressure is a pressure that happens when a part is stacked by a hub power. The estimation of the ordinary power for any kaleidoscopic segment is basically the power partitioned by the cross-sectional region [11]. An ordinary pressure will happen when a part is under strain or pressure. Table 3 shows the Total deformation for various materials.
Table III. Normal Stress for Various Materials
S
.N
o
Mate rial
Analysis Result
Total defor matio n
1
Struc tural Steel
0.020
517
2
GPF P
0.020
571
S
. N
o
Mate rial
Analysis Result
Norm al Stres s
1
Struc tural Steel
1.000 e+00
2
GPF P
1.000 e+00
3
CRP F
1.000 e+00
4
ARF P
1.000 e+00
3
CRP F
33.30
3
4
ARF P
38.88
9
-
Modal Analysis
A modular investigation is the investigation of the unique properties of frameworks in the frequency domain. Table 4 shows the Total deformation for various materials.
Table IV. Modal Analysis for Various Materials
-
Safety Factor
In designing, the safety factor or Factor of Safety (FOS) communicates how much more grounded a framework is than it should be for an expected burden [12]. Security factors are frequently determined by utilizing point-by-point investigation since extensive testing is unfeasible on numerous tasks, like scaffolds and structures; however, the constructions capacity to convey a heap should be resolved to a sensible precision. Table 5 shows the Safety factor for various materials.
Table IV. Saftey Factor for Various Materials
S
. N
o
Mate rial
Analysis Result
Moda l Freq uency
1
Struc tural Steel
16.63
4
2
GPF P
31.83
2
S
. N
o
Mate rial
Analysis Result
Facto r of Safet y
1
Struc tural Steel
15
2
GPF P
15
3
CRP F
15
4
ARF P
15
-
Fatigue Sensitivity
Ansys Workbench is utilized to examine the pressure and the exhaustion strength of the injector body, getting the consequences of the most extreme worth of stress and the base worth of weakness strength if the fuel stacks and dumps quickly [13]. It was additionally used to track down pressure fixation. The graph in Figure 1 shows the fatigue behavior of the turbine blade when different loads are applied to it.
Fig.1. When 2000 N Load is applied
Fig.2. When 5000 N Load is applied
-
Normal Stress Vs Elastic Equivalent Strain
The stress-strain diagram provides valuable information about how much force a material can withstand before permanent deformation or failure occurs. Engineering stress and strain data are commonly used because it is easier to generate the data and the tensile properties are adequate for engineering calculations.
A normal stress is a stress that occurs when a member is loaded by an axial force. The value of the normal force for any prismatic section is simply the force divided by the cross-sectional area. A normal stress will occur when a member is placed in tension or compression. The equivalent plastic strain is the total strain energy of this plastic deformation value on a material. Figure 3 shows the relationship between normal stress and elastic equivalent strain.
Fig.3. Relationship between normal stress and
elastic equivalent strain.
Fig.4. Shear Stress Vs Percentage of Count.
Fig.5. Shear Stress Vs Percentage of Volume.
Fig.6. Principal Stress 1 Vs Percentage of Volume.
Fig.7. Principal Stress 3 Vs Percentage of Volume.
-
-
RESULT AND DISCUSSION
-
Von Mises Stress
Von Mises pressure is a worth used to decide whether a given material will yield or crack. The von Mises yield rule expresses that if the von Mises pressure of a material under load is equivalent to or more prominent than the yield
furthest reaches of a similar material under basic strain, then the material will yield. The von misses is equivalent for the four materials and its underneath the yielding point which shows that anybody material can be supplanted. In any case, hen the structural distortion is viewed as the GFRP and AFRP is more disfigured than CFRP which demonstrates that it is the most ideal alternative. A graph chart is also drawn between the principal stress and the percentage of volume.
-
Total Deformation
We can see that the all out misshapening esteem is practically same for the power applied on structural steel and CFRP, GFRP, and AFRP. At the point when the yield of the four investigations is thought about, clearly, CFRP is the nearest to the estimation of the structural steel which shows that it will be the correct substitute. For example, the strength and hardness given by the steel can be accomplished by supplanting it with the CFRP than GFRP and AFRP, hence, decreasing the weight and cost in this manner and improving the effectiveness of the sharp edge.
-
Normal Stress
Mechanical strain is a mathematical proportion of deformity addressing the general relocation between particles in a material body. Strain is brought about by outside requirements or burdens. Warm strains are strains created at the point when a material is warmed or cooled.They can be the most despicable aspect of an architects presence in the event that they are not thought of as materials that fit impeccably at one temperature and can crack or drop out when their ecological temperature changes. A visual representation is given in this chapter.
-
Modal Analysis
The modular examination empowers the plan to predict the full vibration or to vibrate at a particular recurrence and gives designs a thought of how the plan will react to various unique load types. From our analysis, it is clear that the CFRP materialized blade will deform less at a particular frequency when compared to structural steel blades, GFRP, and AFRP.
-
Safety Factor
It is noticed that for a similar power applied to the four materials, the CFRP fabricated cutting edge affect its construction and plan in view of its advanced properties and adaptable nature. In spite of the fact that the GFRP and AFRP look like CFRP, when inspected intently, the impact applied because of power is significantly less on the underlying surface of the CFRP. The FOS is essentially used to ensure the essential arranging doesnt lead to any alarming disillusionment or presence of deformation or blemish.
-
-
CONCLUSION
The water that goes through the turbine creates some uproar and produce layers of greenery on the propeller which diminishes the productivity of the turbine. Subsequent to testing various materials, CFRP can be supplanted rather than steel in the turbine when contrasted with various materials like GFRP and AFRP. The motivation behind why CFRP stands out from the rest is that it has a low deformity rate and it is adaptable in nature. The water that goes through the turbine creates some uproar and produce layers of greenery on the propeller which diminishes the productivity of the turbine. Thus, a substitute material is required. FRP is a substitute material to steel. It has properties like high flexibility, resistance to disintegration, light weight, sortcoming hindrance, etc. The improvement of utilizing FRP composites on the sharp edge of the propeller is shown and demonstrated via Ansys analysis software.
-
REFERENCES