
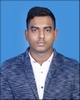
- Open Access
- Authors : Injarapu Kamal Kumar , Varun Chebrolu , Gudapuvalasa Ramana
- Paper ID : IJERTV9IS100092
- Volume & Issue : Volume 09, Issue 10 (October 2020)
- Published (First Online): 14-10-2020
- ISSN (Online) : 2278-0181
- Publisher Name : IJERT
- License:
This work is licensed under a Creative Commons Attribution 4.0 International License
Reduction of Dent and Cost in Manufacturing Industry using Statistical Process Control Techniques
Injarapu Kamal Kumar1, Varun Chebrolu2, Gudapuvalasa Ramana3
1 PG Student, Dept. of Mechanical Engineering, MVGR College of Engineering (A), Vizianagaram, AP, India.
2 Assistant professor, Dept. of Mechanical Engineering, MVGR College of Engineering (A), Vizianagaram, AP, India.
Abstract:- Dent is a shallow misshapening in the outside of an item, created by an effect. Reduction of defects produced while manufacturing in an industry is still critical and on-going. An attempt has been made to analyse on the rejections, Dents are contributing 14% of total rejections out of 30 different types of defects in the company which resulting in reworks, delivery failure and increase in cost of pure quality. Cost of Such defect incurring a loss of 5 Lakhs / Month approximately 60 Lakhs /Annum to the Organisation.
So, we took a Challenging task to reduce the Dent Rejections.
Keywords: Dents, Check sheet, Pareto chart, histogram, Fishbone diagram
1. INTRODUCTION
An off-Highway vehicle segments fabricating organization in Visakhapatnam is spent significant time in creating Three-Point Linkage (TPL), Precision Machined Parts (PMP). Seven Quality control tools are utilized for tackling the Dents and Damages in the organization and due to this present organization's creation cost, creation time is expanding and there might be a postponement in the conveyance. In every industry defects are commonly seen. Dents are the most common defect seen in most of the industries which result in loss of material, price and cost to the industry. In this industry on analysing total rejections of all Precision Machined Parts, We found that dents are contributing major quantity of the total rejections which is huge loss to the company. The scrap of the components has been increasing due to these defects. We focussed to reduce the dents on top and bottom face majorly by problem solving technique like Statistical Process Control [1].
1.1 Statistical Process Control
Seven fundamental devices of value or seven quality control apparatuses appeared in Japan during the 1950s by Kaoru Ishikawa. These are simple graphical and factual instruments utilized for tackling indispensable issues in any stage from the inception of the creation to the conveyance. As demonstrated by Kaoru Ishikawa, ninety-five percent of the issues can be unwound using these instruments. These region units alluded to as fundamental because of it very well may be utilized with least mindfulness. Seven quality control instruments consist of:
-
Flow chart: It is utilized to decipher groupings of tasks or exercises of a procedure utilizing images. It tends to be utilized in executing any undertaking, regulatory part, producing process, and so on [4].
-
Check sheet: It is utilized to document the predominance of an event in pre-characterized exercises. It'll be incredible with histogram and Pareto diagrams.
-
Pareto chart: It has been presented by a financial master, Vilfredo Pareto and that is moreover alluded to as 80-20 guideline. In an association or procedure, there might be a few deformities or issues and it will be hard to focus on all the imperfections or issues, Pareto outline assists with looking through the premier imperfections or issue affecting the overall deformities [4].
-
Fishbone outline: It was carried with the guide of Kaoru Ishikawa to find the association between the deformities and the components or to discover the underlying drivers of the imperfections. At first, the difficult explanation is characterized and the primary variables are ordered like man, machine, technique, material, condition, and so forth, where the reasons for these are recorded by perception.
-
Control chart: Walter A. Shewhart has been created to speak to process variety in graphical structure to dissect whether the procedure is in charge or not. In case the examples are inside the upper control limit (UCL) and lower control limit (LCL), by then we can confirm that the procedure is progressing nicely or, no doubt, the strategy ought to be assessed to make it fit.
-
Histogram: It is a pictorial depiction of accumulated repeat dissemination data of a time period in a visual graph structure that is recorded during the view of a methodology [4]
-
Scatter chart: It is utilized to discover the connection between the needy factors on Y-hub and free factors on X-pivot graphically by joining the basic purposes of the X-Y set, which is to discover the circumstances and logical results connection. On the off chance that their zone unit comparable qualities, at that point they depict with an alternate picture.
-
BACKGROUND
-
Company overview
Uniparts is an Indian based overall creator of built frameworks and arrangements. With salaries of USD 190 million, the Gathering is the greatest exporter of frameworks and segments for the off-expressway market and works out of 9 regions in 4 countries like India, North and South America, Europe, and Japan.
Uniparts Gathering is the world's driving maker of 3-point association frameworks for ranch hardware. In 1996 the gathering started to gracefully worldwide OEMs. It is affirmed by administrators, for example, John Deere, Mahindra and Mahindra, CNH, Kubota and Yanmar. Uniparts Gatherings are providers of the development part with PMP (accuracy machined segments). Worldwide OEMs, for example, Catamount, Caterpillar, and John Deere have been affirmed providers. In 2007, the Uniparts Gathering entered the pressure driven field and has water powered frameworks and chamber producing abilities.
-
Process of a product
Purchase Order (PO) will be gotten from the client depending on the sort of items and amount required. Utilizing Undertaking Asset Arranging programming PO will be changed over into Deals Request. Material requirement planning (MRP) is created with the assistance of data sources, for example, an ace calendar which characterizes the sort of items, the quantity of items, and the period required for shipment of the items, stock that characterizes the crude material open for the assembling and. Bill of Materials (BOM) characterizes the amount of the crude material, sort of congregations required for the assembling of an item. Purchase Order (PO) will be transmitted to the providers of crude materials. Gained products will be investigated, on the off chance that it is far inside the detail, it will be acknowledged in any case merchandise will be en route to the providers. Bring the creation solicitation of the Creation Request and will be managed to the shop floor. Dependent upon the creation demand crude material will be figured out how to the shop floor. The crude material will begin picking up its shape to create the item and it will be investigated. In the event that it fulfills the client's prerequisite, at that point a receipt will be created by the Sales Order (SO) and the item will be dispatched. On the off chance that it doesn't meet the details it will be rejected or sent for revise [9].
Figure 1: Product Process flow chart
-
Problem statement
In the hour of Data Innovation (IT), the correct information at the right an ideal opportunity for the perfect individual transforms into the key for progress. Recently gathered information from April 2019 to October 2019 has been utilized to recognize the commitment of various deformities in the organization. Pareto diagram was utilized to recognize the significant deformities and
minor imperfections that are influencing the creation cost, creation time, delay in conveying the items to the clients, and so forth.,
1600
Over All Defect wise Pareto Analysis
98.9088.9796.39100
1400
1200
1000
1346
1289
898
779
91.9726.9838.9846.9757.9666.9570.32
86.8073.8993.9305.59 90
79.8417.8846.03 80
70
70
71.7349.7370.07
60
60
62.6450.6484.42
58.44
Rej Qty
Rej Qty
800
600
686 52.34 50
455.1862 40
37.00
400
200
Rusty part
Rusty part
Blade Cut
Blade Cut
Tap Broken
Tap Broken
0
27.59
14.10
379
290284284278264230228207191
18113611811210794 87 85 80
30
20
78 73 65 60 58 10
Crack
Crack
0
Face Unclean
Face Unclean
material not match
material not match
Position not ok
Position not ok
OD Unclean
OD Unclean
NO go gauge
NO go gauge
Perpendicularity
Perpendicularity
Drill Broken
Drill Broken
Setting Rejection
Setting Rejection
Sales Return
Sales Return
Wrong operation
Wrong operation
Dents/Damage
Dents/Damage
Rej.
Figure 2: Pareto chart for overall defects in the company
From figure 2, it was found that Dents damage is contributing 14.10 % of overall defects which is resulting in a revenue loss of 60 lakhs / annum to the company.
-
-
METHODOLOGY
-
Statistical Process Control Techniques are used for solving the dent damages in the company. Following approach was to study, gather, and analyze for best results:
-
Historical data were used for plotting the Pareto chart which helps in finding the problem statement.
-
Dent(s) damages relating to the batch were recorded in stratified check sheet.
-
Pareto chart was used for finding the overall damages using required information.
-
Fishbone diagram for utmost dent damages to find the connection between damages and factors.
-
By brainstorming plausible cures were actualized.
-
After implementing corrective measures again, the dent damages are recorded in a stratified check sheet.
-
Histogram was utilized to look at the information when the counteraction steps were presented.
Problem identification: a) Collect historical data
b) Pareto chart
Experiment: a) Flow chart
b) Stratified check sheet
Analysis: a) Histogram
-
Fishbone diagram
-
Implemented remedies
-
Result: a) Stratified check sheet
b) Histogram
Figure 3: Flow chart of the methodology
-
EXPERIMENT
-
Machining process in the industry
Get the creation solicitation of the purchase Request and will be managed to the shop floor. Dependent upon the creation demand crude material will be figured out how to the shop floor. Part boundaries are set up according to the details of the client necessity. After the achievement of the Turning, Penetrating, Grinding machining process, parts will be sent for audit where the Quality Control engineer examines the segment. In the event that the segment is according to the prerequisite, it will be acknowledged and they can begin the cluster creation in any case the segment will be dismissed and this pre-batch production assessment consistent till the part is acknowledged. At the point when the cluster creation is begun each part will be outwardly investigated by the administrators and for additional affirmation, they will counsel the specialists. On the off chance that the segment is without imperfection it will be sent for the further activities else it will be sent for scrapped.
Figure 4: Flow chart of the production process
-
Data recording using a check sheet
There are child wip inspection tables are for inspecting the Precision Machined Parts (PMP) it is inspected manually using man power. There by observing each and every part during the inspection, if there are any dents, damages, and scratches by visual inspection relating to the dents damage was recorded in a stratified check sheet [6].
Month
Nov-19
Dec-19
Jan-20
Feb-20
Total
Batch
3725
2372
3089
3027
12213
Rejected
1737
1241
1346
1287
5611
Table 1: Check sheet of DENT damages concerning the child wip inspection Overall 45% of the dents on the components which are rejected from inspection department.
Figure 5: Dents on different components
-
-
ANALYSIS
5.1 Histogram of dents location wise
182 |
||||||||||||
180 |
165 |
|||||||||||
160 |
||||||||||||
140 120 100 |
95 |
117 |
108 |
|||||||||
80 |
||||||||||||
60 |
42 |
|||||||||||
40 |
25 |
26 |
||||||||||
20 |
2 |
0 |
1 |
5 |
||||||||
0 |
||||||||||||
LNK |
SPN |
TPN |
Others |
|||||||||
TOP |
95 |
165 |
2 |
25 |
||||||||
MID |
42 |
108 |
0 |
5 |
||||||||
BOTTOM |
117 |
182 |
1 |
26 |
||||||||
182 |
||||||||||||
180 |
165 |
|||||||||||
160 |
||||||||||||
140 120 100 |
95 |
117 |
108 |
|||||||||
80 |
||||||||||||
60 |
42 |
|||||||||||
40 |
25 |
26 |
||||||||||
20 |
2 |
0 |
1 |
5 |
||||||||
0 |
||||||||||||
LNK |
SPN |
TPN |
Others |
|||||||||
TOP |
95 |
165 |
2 |
25 |
||||||||
MID |
42 |
108 |
0 |
5 |
||||||||
BOTTOM |
117 |
182 |
1 |
26 |
||||||||
Histogram was plotted for all the dent locations of the component that are used for rework of PMP, where type of components will be on the X-axis, the number of the defective locations will be on the primary Y-axis.
200
Figure 6: Histogram for dents in different component locations
From the figure 6, we observed that SPN component having high number of dents in its location are the major defective parts producing and should be focused on these area to minimize the dents.
Histogram of dents in percentage
Histogram chart was plotted for dent defects that encountered during the child wip inspection, where the type of components will be on the X-axis, dent defect percentage will be on the primary Y-axis.
70.0 60.0 50.0 40.0 30.0 20.0 10.0 0.0 |
59.2 |
||||||
33.1 |
7.3 0.4 |
||||||
LNK |
SPN |
TPN |
Others |
||||
% of Dents |
33.1 |
59.2 |
0.4 |
7.3 |
Figure 7: Histogram of dents in percentage
From figure 7, we observed that SPN are the major defects and should be focused on these defects for minimization, and reduction of dents in the component.
-
Concerns of dents
Dent is the topmost defect that was encountered during the analysis of defects in the industry. Fishbone diagram for dents was used to find the connection between the defects, factors, even to find the root cause.
-
Causes of man factor
-
When the component is in machining process the rough handling of the components by the operator can cause damage to the component and dents can be seen.
-
After every machining process the component is thrown into the storage pallet from a certain height by the operators and the hitting to other components can cause components to get dents.
-
Some operators dont have knowledge of systematic arrangement of components into the pallet and are not capable of high targets.
-
-
Causes of the method factor
-
Giving higher production targets to the operators irrespective to their capability.
-
Due to inappropriate speed, feed, depth of cut of the components can cause concern to method factor.
-
Due to improper storage methods the components may get dents, scratches, rust etc.
-
-
Causes of machine factor
-
If the component is not fixed properly during the time of machining there is a chance of falling of component while in machining process.
-
When the power supply is interrupted it will terminate the process in between the operation.
-
-
Causes of material factor
-
Improper handling of the components can lead to damaging of edges of parts which cannot be used for further operations as the surface becomes uneven due to dents.
-
Some components have threading for assembling if the thread damage occurs the component is not recommended for the assembling to other components as the thread got damaged.
-
If the material fall/thrown for a certain height the material gets impact to the ground, due to that impact the material gets damaged and irregular surfaces can be seen.
Figure 8: Fishbone diagram for DENTS
-
-
Preventive measures for dents
By brainstorming feasible remedies of dents are implemented to reduce the undesired events during the process.
-
Remedies for man factor
Operators had undergone a training season to understand the production process. And damages caused during handling of material and improper arrangement of components in the crates. Based on capacity of the operators production targets has to be given. Proper handling of components while placing in crates after every machining operation.
-
Remedies for machine factor
The work piece was clamped uniformly, the worktable ought to be checked for flatness and rigid to the ground and electrical generators were used for uninterrupted power supply.
-
Remedies for method factors
Maintaining appropriate speed, feed, depth of cut gives the better output without any scratches and damages to the components and it is stored in a proper way without getting impact to any other surface as the impact can cause damage.
-
Remedies for material factor
After manufacturing of component, it should be inspected whether it satisfies the end-user specification or not. If not, it should be rejected. Proper storage of components was maintained to avoid dents.
-
-
Action plan
-
Implementing the conveyor system to reduce material handling and human errors.
-
Usage of Netlons on threaded parts.
-
Usage of Polythene/ Sheets in between layers.
-
Implementation of Netlons on all soft and external Threaded parts.
-
Packaging Instructions needs to adhere strictly @ Supplier End.
-
Material handling Improvements from finishing shop.
-
Listing of Soft Parts and display in all Work Centres.
-
Material Handling Visuals – Family Wise Packaging Process in Bins / Trolleys.
-
Implementation of material handling trolleys for LNK"S and Soft parts.
-
Material handling improvements for asymmetrical parts.
-
Repairing the existing trolleys.
-
Manufacturing the trolleys for CLAAS parts.
-
Manufacturing the trolleys for LNKS.
-
Wooden planks need to get prepared to place it in the bottom of the bin for Chrome LNKS and for Bigger LNKs and for asymmetrical parts.
-
-
Implementations
-
Conveyor System
Conveyor system are tough and reliable utilized in mechanized dispersion and warehousing, this takes into account more proficient retail and assembling circulation. It is a labour saving system that allows large material to move rapidly through a process. Allows industry to receive and ship higher volumes with small storage space and less labour expenses [3].
Basing on the plant layout a conveyor system has been designed to reduce material handling and labour errors which finally resulting in dents on components. Where the components are moved from one machining operation to another machining operation and finally to inspection department. The components which are accepted there will be sent to packing and dispatch. Design has been suggested and yet to implement.
Figure 9: conveyor system based on plant layout.
-
Pallets for components to place on conveyor system
A Catia 3D design has been suggested to the industry for placing of the components into pallets to reduce physical contact between each component. This is used to place on the conveyor system. And still to implement.
Figure 10: Design of multi parts pallet in catia.
Figure 11: Design of single part pallet.
-
Placing Netlons to parts
Figure 12: Netlons for parts.
-
Usage of Polythene/ Sheets in between layers.
Figure 1: usage of sheet layers.
Usage of sheets in between every layer while placing parts reduces the contact of parts to one another and can reduce dents.
-
-
RESULT AND DISCUSSION
After implementing the preventive measures, the process was ascertained and every part was examined. The occurrences of the sort of dents have been recorded in a check sheet.
Month |
Nov-19 |
Dec-19 |
Jan-20 |
Feb-20 |
Mar-20 |
Batch |
3725 |
2372 |
3089 |
3027 |
3387 |
Rejected |
1737 |
1241 |
1346 |
1287 |
656 |
Percentage |
46.63087248 |
52.31871838 |
43.57397216 |
42.5173439 |
19.36817242 |
Table 2: Check sheet of DENT damages concerning the child wip inspection after implementing remedies.
-
Histogram of Parts Produced, Defects and Rejection Percentage
2372
2372
PMP
PMP
1737
1737
1241
1241
1346
1346
1287
1287
Histogram was used to compare the data before and after the remedies implemented.
4000
3500
3000
2500
2000
1500
1000
500
0
3725
3089
3027
3387
4000
3500
3000
2500
2000
1500
1000
500
0
3725
3089
3027
3387
Nov-19 Dec-19 Jan-20 Feb-20 Mar-20
Nov-19 Dec-19 Jan-20 Feb-20 Mar-20
46.6
46.6
52.3
52.3
43.5
43.5
42.5
42.5
656
19.3
656
19.3
Figure 14: Comparison of parts produced, defects and rejection percentage of dents.
From the figure 14, we can observe that the rejection quantity is reduced and percentage of rejected components reduced to 19%.
-
Scope of Project
In this project, components are inspected at a macro level, which restricts in finding the dents on the surface. To overcome this drawback micro-level inspection such image processing can be employed.
-
CONCLUSION
In an off-highway vehicle components manufacturing company, dents are contributing 14.10 % of overall defects. Seven Quality Control tools were used as a problem-solving technique in which various tools were used in different phases:
-
Using previously collected data Pareto chart of Figure. 2 were used to identify the major defects and minor imperfections that are affecting the production cost, production time, delay in conveying the products to the customers, etc.
-
The flow chart of Figure. 4 were employed to interpret sequences of the production process. And in Figure 5 dents are seen in different components.
-
By observing every part during the production process, if there are any undesired encounters by visual investigation the sort of dent(s) was recorded in a check sheet as tabulated in Table.1.
-
Using the histogram chart of Figure. 6, it was found that major location of dents in different components, and from Figure. 7, histogram of dents percentage among the different components.
-
Fishbone diagrams for dents are drawn as shown in Figure. 8 to identify the root causes of various factors that are affecting the dents.
-
Using brainstorming remedies for the causes was identified and feasible remedies were implemented.
-
After implementing the remedial measures, the process was observed and defects corresponding to the dents were recorded in the check sheet as tabulated in Table. 2. Histogram was used to compare before and after implementing preventive measures. From Figure. 14, it was found that the components rejection percentage was reduced to 19.3%.
REFERENCES
-
DH Bester field 2004 quality control 7th edition (2006) published by Pearson education.
-
Mitra, Amitava fundamentals of quality control and improvement 4th edition (2016).
-
Matthew p. Stephens Manufacturing facilities design & material handling 6th edition (2013).
-
Varsha M. Magar, Dr. Vilas B. Shinde, Application of 7 Quality Control (7 QC) Tools for Continuous Improvement of Manufacturing Processes International Journal of Engineering Research and General Science Volume 2, Issue 4, June-July, (2014), ISSN 2091-2730.
-
Aichouni, M. Quality Control The Basic Tools and their Applications in Manufacturing and Services, ISBN 6690-75-688-2, Dar Al-Asshab, Book Publishing, Riyadh, (2007).
-
Walker, H. F and Levesque, J. 'The Innovation Process and Quality Tools', Quality Progress, Vol. 40, No. 7, July (2007), pp. 18/22.
-
Pyzdek, T., Quality Engineering Handbook, Second Edition, Marcel Dekker, Inc., New York, (2003).
-
Quality Assurance Handbook (Products) 1 Volume 1 General Instructions – Group Level Rev.1.11.2018
-
Joseph M. Juran, Joseph A. De Feo, Jurans Quality Handbook 6th edition ISBN: 978-0-07-162973-7
-
ESS handbook for quality reports (2014 )edition. ISBN 978-92-79-45487-5, doi: 10.2785/983454.
-
Mitra, Amitava. Fundamentals of quality control and improvement / Amitava Mitra. 3rd edition (2008).
-
Brian B. Mansir & Nicholas R. Schacht. Total quality management (1989).
-
Joseph M. Juran, A. Blanton Godfrey, Jurans Quality Handbook 5th edition.
-
Graeme Knowles, Quality Management, study guide (2011).
-
Arthur Langford Jr. Park, Quality Assurance/Quality Control, Section 00 14 00.
-
Western Electric Company, Inc. statistical quality control handbook. 1st Edition (1956), 2nd Edition (1958).
-