
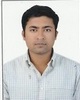
- Open Access
- Authors : Kunal D. Gadgil , Keshav U. Kulkarni , Hrishikesh V. Tupkari
- Paper ID : IJERTV10IS020040
- Volume & Issue : Volume 10, Issue 02 (February 2021)
- Published (First Online): 10-02-2021
- ISSN (Online) : 2278-0181
- Publisher Name : IJERT
- License:
This work is licensed under a Creative Commons Attribution 4.0 International License
Potential use of Passive Cooling Technique in Evaporative Cooler
Prof. Kunal D. Gadgil
(Assistant Professor)
Dept. of Mechanical Engineering
Shri Sant Gajanan Maharaj College of Engineering Shegaon, Maharashtra, India
Keshav U. Kulkarni
Dept. of Mechanical Engineering
Shri Sant Gajanan Maharaj College of Engineering Shegaon, Maharashtra, India
Hrishikesh V. Tupkari Dept. of Mechanical Engineering
Shri Sant Gajanan Maharaj College of Engineering Shegaon, Maharashtra, India
AbstractEnergy consumption in buildings shares a major chunk of the energy demand pie throughout the globe. The majority of the energy consumption in buildings is contributing to thermal comfort to individuals. Thermal comfort is vital for human life as it related to the health, performing ability of an individual. There is an exponential rise in the use of air conditioners in the last few decades which in turn provided many environmental adversities like an increase in global temperature due to global warming and ozone layer depletion. Thus, it is a timely need to develop a sustainable, eco friendly, economical, and energy viable solution to satisfy the thermal comfort needs of occupants. An evaporative cooler is one such technology. Although this method has the advantages of being an ideal cooling system it has certain limitations of lower heat transfer rates, uses in specific climatic conditions, and a large amount of water consumption associated with it. To address the issue of lower heat transfer rate Passive cooling method of incorporating surface roughness like dimples and protrusions on the surface where heat transfer takes place can prove a milestone. In the present study, experimental analysis and analytical study using computer simulation software ANSYS are carried out on terracotta tubes of conical shape which are to be used in Evaporative Cooler. These studies are carried out on three kinds of tubes viz. plain tube, dimpled tube, and protrusion tube. The tubes are checked for variation in heat transfer rate, percent temperature drop, Reynolds number, Nusselt number, and pressure drop due to the incorporation of dimples and protrusion on the inner wall of tubes. It is found that heat transfer and percent temperature drop increase with the use of protrusions by about 39.17% and 17.2% respectively. It is also observed that flow characteristics like Reynolds number, Nusselt number increase with the use of dimples and protrusions without any significant pressure drop. It is also concluded that the input air should be administered at lower velocities to get maximum temperature drop. The tubes with protrusion proved more useful in Evaporative cooler application when used with lower input air velocities.
Keywords: Passive Cooling, Evaporative Coolers, Terracotta Tubes, Dimples, Protrusions, Net temperature drop
I.INTRODUCTION
The construction sector, which includes domestic buildings, mercantile, civil services, agriculture, etc. attribute for around 35% of the entire global energy requirements [1]. Heating, cooling, air conditioning, and ventilation applications form the major components of energy
consumption in the building sector. It is also argued that globally around 40% of total building energy is consumed for space heating or cooling applications in both residential and commercial sectors [1]. Room air conditioners are mostly used worldwide as air cooling appliances. However, the rise in the use of air conditioners has led to serious environmental issues associated with global warming and ozone layer depletion. Consequently, it becomes necessary to provide environment friendly, energy viable solutions to obtain a proper thermal environment in buildings. Evaporative cooling (Evaporative Coolers) is one such widely employed effective passive cooling technique that can provide a satisfactory degree of comfort [2]. Deki Cooling installation is one such architectural installation at Noida which made an application of evaporative cooling. It is an elaborate arrangement of hundreds of cone-shaped terracotta tubes into a beehive patterned circle. The porous terracotta tubes (baked earthen tubes) absorb water, and as hot air passes through them, its turned into cool air. It is an innovative solution for cooling workplaces involving heat rejection in the surrounding environment through machinery. The cooling efficiency of this installation can be enhanced with some changes made to the surface structure of terracotta tubes.
The effect of using the passive method of incorporating the surface roughness (like dimples, protrusions) on the inner surface of these terracotta tubes, in increasing heat transfer rate is illustrated in this paper with the help of results obtained through experimental testing and two-dimensional analysis on Ansys software.
-
LITERATURE REVIEW
It is found in the literature that thermal comfort for humans is vital. For a reason, people pass about 8090% of the day functioning in offices and living in residents, thus it becomes crucial to keep the good indoor environmental quality (IEQ). [3,4]. The report named The Future of Cooling published by IEI in May 2018 depicted an immense need to develop an energy-efficient and environment-friendly cooling technique predicting that effectual measures can increase cooling efficiency averagely by double and bring down energy requirement for cooling by about 45%. The review by et.al Dnyandip K. Bhamare, 2019 shows how passive cooling can be an option to develop such cooling systems. He depicts that passive cooling techniques are capable of maintaining a
comfortable indoor environment and also lower the cooling energy load [5]. Yifan Yang, 2019 establishes Evaporative cooling as a potential energy-saving passive cooling method along with classification, recent developments, and applications of different enhanced evaporative cooling technologies [2]. An air conditioning technology, named Evaporative Cooler uses the water evaporation phenomenon to cool the temperature of air [6]. Evaporative Coolers are categorized into three types viz. direct, indirect, and indirect- direct evaporative coolers [7]. Air conditioning devices of these types are energy-saving [8] and environmentally-sound [9]. Even though such cooling units are energy-efficient and green, there are certain restrictions to their absolute use. Its performance is good only in hot and arid climates. The performance of the device also varies depending on the inlet air conditions. By Performance evaluation of Indirect Evaporative Cooler et al. Aftab Ahamad quoted that the indirect evaporative cooler is suitable for hot and dry climatic conditions, as in most of the regions of India [10]. Also, passive technologies mainly consist of surface shape modications to expand the heat transfer area or to escalate the turbulence of flow [11-13]. This approach involves surface roughening, such as ribs, ns, dimples, and protrusions [14,15]. Ibrahim et al, 2003 stated that the cooling effect was enhanced by a high porosity of the evaporator, increased water supply pressure [16]. Hemant Pisal, Avinash Ranaware demonstrated that the heat transfer rate increases for the metal plate with dimple [17]. Also, presented a fact that the rate of heat transfer and drop in pressure inside dimples rise with the increase in flow rate and with increases in Reynolds number.
From the detailed and sequential literature survey, it is understood that to cope up with the ever-increasing demand for energy for thermal comfort or cooling purpose there is a dire need to develop an energy-efficient, economical, and environment-friendly coolig technology. Passive cooling especially, Indirect Evaporative Cooling can be the best option to provide thermal comfort in dry and arid regions since it provides an advantage of avoiding direct contact with the cooling medium and thus facilitating control over humidity. Also, it is understood that the three-dimensional roughness like dimples and protrusions cause the enhancement in heat transfer and this is ruled by various input factors like input temperature, surface temperature, flow velocity, etc. Thus, Evaporative coolers along with the passive cooling method of surface roughness may prove effective in providing necessary thermal comfort with low energy consumption.
-
EXPERIMENTAL WORK
-
Objective
The objective is to check the effect on heat transfer rate by incorporating patterned irregularities (dimples or protrusions) over the inner surface of the terracotta tubes which are to be used in the Evaporative Cooler.
Fig. 1. Test Tubes (a) Plain Tube, (b) Dimpled Tube, (c) Protrusion Tube
-
Materials
To satisfy the objective the Experimental Testing is carried out over three kinds of terracotta tubes at three different velocities.
Plain Tube: Baked conical clay tube open at both end plain on the inner wall
Dimpled Tube: Baked conical clay tube open at both tubes with dimples on the inner wall of the tube and plain outer wall.
Protrusion Tube: Baked conical clay tube open at both ends with protrusions of clay of identical size and shape are attached on the inner surface of the tube and smooth outer surface.
All the tubes are identical in shape, size, and dimensions except for their inner wall surface structure.
Specifications of Tubes:
Inner Diameter of bigger end of Tube (D1) = 100 mm Inner Diameter of the smaller end of Tube (D2) =50 mm Length of Tube (L) = 400 mm
Diameter of Dimple (d) = 10 mm
Distance between two consecutive dimples (l) = 8 mm The material of Tube: Potters Clay
Fig. 1 shows the cross-sectional view of different kinds of tubes to be used in the experiment. A well suitable test Rig is developed to ensure the process experimentation under controlled conditions. Fig. 2 presents the diagram of the experimental test rig. All the elements of the test rig are listed in order.
-
Experimentation
In the present work, the three tubes are tested for heat transfer rate at three different velocities. The individual test tubes are placed one by one in a test section i.e., between two steel boxes. The suction fan is turned ON and the air is channelized through the test tube. The air is made to flow from the bigger end to the smaller end of the tube. The velocity of air passing through the test tube is regulated with the aid of a regulator. After the airflow is set at a constant velocity, the pumps in the water reserve are turned ON. These pumps draw the water from the water reservoir to the top tray. The water sprays fall on the clay test tube through perforations made on the top tray. Thus, the test tube gets wet in turn providing constant surface temperature (25 0C). The remaining water gets
A. Inlet Section
E. Bottom Tub Water Reservoir
I. Perforations
B. Outlet Section
F. Test Tube
J. Temperature sensor with data logger
C. Top tray
G. Speed Regulator
K. Suction Fan
D. Base Tray
H. Pumps
Fig. 2 Diagrammatic view of the experimental test rig.
collected back in the water reservoir through holes made on the base tray. The temperature of the air at the inlet and outlet section is determined at regular intervals with the help of a temperature sensor and data logger. In this way, an individual test tube is tested for three different velocities (constant value until changed with regulator) by altering the velocity with help of a regulator. The velocity of air at the inlet and outlet is measured using an anemometer. The same procedure is adopted for all test specimens.
-
Sample Calculations for experimental test:
Let,
= Density of air (kg/m3)
µ = Dynamic Viscosity of air (kg/m.s)
k = Thermal Conductivity of air (W/m. K)
Pr = Prandtl Number
Q= Heat transfer rate (W) ti = Inlet Temperature (K) to = Outlet temperature (K)
dT = Change in temperature = (ti-to)
H = Height of frustum of cone tube
Now, we have
The cross-sectional area of the bigger end,
1 = r12
The cross-sectional area of smaller end,
2 = 22
The average cross-sectional area of flow,
1 + 2
v1 = Minimum Velocity of air (m/s)
v2 = Intermediate Velocity of air (m/s)
Total Surface area,
=
2
v3 = Maximum Velocity of air (m/s)
r1 = Radius of bigger end of frustum of cone tube (m) r2 = Radius of smaller end of frustum of cone tube (m) h = Convective heat transfer coefficient (W/m2K)
= (1 + 2)(12 22) + 2
Area of convection or Wetted Perimeter of the cross-section,
= (1 + 2)
Hydraulic Diameter,
= 4/
temperature drop at outlet against different inlet temperature keeping velocity of air at inlet and wall surface temperature constant for a particular case. It is important to note that air is made to pass from the bigger end to the smaller end of a frustum of the earthen tube. Furthermore, similar to experimentation all three kinds of tubes are analyzed for three different input velocities. Thus, the output temperature drop is studied against input parameters used are various inlet temperatures at various input air velocities.
Input air temperature values used are 40 0C,41 0C, 42 0C,43 0C, 44 0C
Input air velocities values used are 2.5 m/s, 5 m/s, 10 m/s Wall Surface temperature = 25 0C
Now, Reynolds number is given by,
=
µ
For forced convection,
i.e., for Re 10000, 0.6 Pr 160 and L/D 10 as per the Dittus-Boelter equation,
= 0.0230.80.3
Also, Nusselt number is given by,
.
=
Therefore, convective heat transfer coefficient is given by,
.
=
So, the heat transfer rate can be calculated by,
= . ( ).
The rate of heat transfer for three tubes at a particular constant velocity is calculated for all three tubes and is
B. Sample Calculations for Analytical study:
Let,
tin = inlet temperature for the nth case ton = outlet temperature for the nth case Percent drop in outlet temperature,
100
Percent drop in outlet temperature,
100
Let,
P1n = percent drop in outlet temperature for plane tube for the nth case,
P2n = percent drop in outlet temperature for a tube with dimples for the nth case,
P3n = percent drop in outlet temperature for a tube with protrusions for nth case
Percent change in temperature drop for a tube with dimples,
compared to the select best tube. Similarly, all three tubes are checked at various values of velocities. Table 1 and Table 2 depict the observations and calculations made for
2 1
1
100
experimentation respectively.
-
-
COMPUTER SIMULATION STUDY
A. Details about Analytical study
In the present work along with experimental studies, analytical studies through computer simulation software are also carried out. The software used for the purpose is ANSYS 2020 R1 Student version. For geometry creation Fusion 360 software is used. This study is carried out on 2-dimensional
models of the three terracotta tubes identical to the one used in experimental work. The dimensions and shape of the test tubes are discussed earlier in the experiment section. Thee models of test tubes are analyzed to get average percentage
Percent change in temperature drop for a tube with
protrusions,
3 1
100
1
Fig. 3 and Fig. 4 represent the contours of static temperature and static pressure respectively obtained through ANSYS software analysis. Table 3 shows the variations of percent change in temperature drop at an outlet for dimpled and protrusion tube concerning plain tube.
Fig. 3 Counters of Static Temperature for (a) plain tube, (b) protrusion tube, (c) dimpled tube.
Fig. 4 Contours for static pressure for (a) plain tube, (b) protrusion tube, (c) dimpled tube.
TABLE I. INLET TEMPERATURE, MINIMUM OUTLET TEMPERATURE, AND MAXIMUM CHANGE IN TEMPERATURE FOR EACH TUBE AT EACH VELOCITY OBTAINED THROUGH EXPERIMENTATION
Velocities
V1 = 2.7 m/s
V2 = 3.7 m/s
V3 = 4.9 m/s
Temperatures (0C)
Ti
To
dT
Ti
To
dT
Ti
To
dT
Tubes
Plain Tube
24.33
20.2
4.13
24.33
20.8
3.53
24.33
21.4
2.93
Dimpled Tube
23
20.1
2.9
23
20.2
2.8
23
20.3
2.7
Protrusion Tube
24.3
19.7
4.6
24.3
20.2
4.1
24.3
20.6
3.7
TABLE II. VARIATION OF FLOW CHARACTERISTICS, AND HEAT TRANSFER RATE, Q (W) FOR INPUT VELOCITY V1 = 2.7 M/S
Tube
Reynolds Number
Nusselt Number
Heat Transfer Rate, Q1 (W)
% change in Heat Transfer Rate
Plain tube
41238.29
103.01
3.98
Dimpled tube
44183.88
108.86
2.95
-25.87
Protrusion tube
47129.47
114.62
4.94
+24.12
TABLE III. VARIATION OF FLOW CHARACTERISTICS, AND HEAT TRANSFER RATE, Q (W) FOR INPUT VELOCITY V2 = 3.7 M/S
Tube
Reynolds Number
Nusselt Number
Heat Transfer Rate, Q2 (W)
% change in Heat Transfer Rate
Plain tube
55966.25
131.52
4.18
Dimpled tube
58911.84
137.02
3.59
-14.11
Protrusion tube
61857.43
142.48
5.47
+30.86
TABLE IV. VARIATION OF FLOW CHARACTERISTICS AND HEAT TRANSFER RATE, Q (W) FOR INPUT VELOCITY V3 = 4.9 M/S
Tube
Reynolds Number
Nusselt Number
Heat Transfer Rate, Q3 (W)
% change in Heat Transfer Rate
Plain tube
73639.80
163.81
4.34
Dimpled tube
76585.39
169.63
4.27
-1.61
Protrusion tube
79530.98
174.21
6.04
+39.17
TABLE V. VARIATION OF THE PERCENTAGE CHANGE IN TEMPERATURE DROP FOR DIMPLED TUBE AND PROTRUSION TUBE OBTAINED THROUGH EXPERIMENTAL STUDY
Heat Transfer Rate (W)
Tubes
Plain Tube
% change in Heat Transfer Rate
Dimpled Tube
% change in Heat Transfer Rate
Protrusion Tube
% change in Heat Transfer Rate
Q1
3.88
.
2.72
-25.87
4.33
+24.12
Q2
4.10
.
3.37
-14.11
4.95
30.86
Q3
4.28
.
4.07
-1.61
5.59
39.17
TABLE VI. VARIATION OF HEAT TRANSFER RATE FOR ALL THREE TUBES OBTAINED THROUGH COMPUTER SIMULATION
Test Tube
Dimple Tube
Protrusion Tube
Percentage Change in temperature drop at the outlet
Percentage Change in temperature drop at the outlet
Velocity
2.5m/s
5 m/s
10 m/s
2.5 m/s
5 m/s
10 m/s
Inlet Temperature
40 0C
-10
-5.50
-5.59
10.8
18.92
17.37
41 0C
-9
-5.50
-5.59
10.9
16.47
17.31
42 0C
-9
-5.50
-5.59
10.92
16.45
17.52
43 0C
-10
-5.50
-5.59
11.2
16.51
17.62
44 0C
-9
-5.50
-5.59
11.09
16.6
17.72
Fig. 5: Rate of Heat Transfer against Velocity
Fig. 6: Variation of Nusselt number
Fig. 7: Variation in Outlet temperature w.r.t. time obtained through Experimental work for (a) Plain Tube, (b) Dimpled Tube, (c) Protrusion Tube
-
RESULTS AND DISCUSSION
-
Results from Experimental work
The experimental data is used to tabulate the flow characteristics like Reynolds number and Nusselt number along with heat transfer rate as shown in table 2,3 and 4 for different test tubes at different velocities. Further, it is used to plot various thermal and flow characteristics. Fig. 3 shows the contours of static temperature for all three tubes and depicted that as the air flows from the bigger end to the smaller end of the tube it gets cooled along the boundary of tubes. It is clear from Fig. 4 that static pressure drops at a minimum in the case of dimpled tube and protrusion tube as compared to plain tube. Thus, tubes with dimples and protrusions offered no significant drop in pressure. Fig. 7 shows the variation in the temperature
Fig. 8: Variation in percent drop in outlet temperature obtained through Computer Simulation for input temperature (a) 40 0C, (b) 42 0C, (c) 44 0C
at outlet concerning the time at three different velocities. It shows that temperature difference increases with time but decreases with an increase in velocity. It is seen from Tables 2, 3, and 4 that the heat transfer rate increases with an increase in velocity due to an increase in Reynolds number. But it is seen earlier that we get the maximum cooling effect for the lower velocity of incoming air despite increased heat transfer rate. This might be because as the velocity of air increases turbulence increases resulting in more molecular friction between air molecules.This friction between air molecules rises the temperature of the air. Also, contact of air with tube wall for more duration due to lower velocity increases the cooling effect. Thus, the resultant temperature coming out of the tube decreases. It means the lower the input velocity higher the cooling effect. Fig. 5 is a plot for heat transfer rate against
velocity for all three tubes. It is clear from the plot that the heat transfer rate is maximum (6.04 W) for a tube with protrusion followed by plain tube (4.34 W) and lastly by dimpled tube (4.27 W). The percent change in heat transfer for dimpled and protrusion tube is depicted in table 5. The negative value in the case of the dimpled tube shows that for dimpled tube heat transfer rate is less than the plain tube of identical dimensions. The positive percent change in heat transfer rate denotes the superiority of the protrusion tube over the plain tube in heat transfer. Therefore, a protrusion tube with air administered at a lower velocity is the best option to obtain the optimum cooling effect. Also, it is seen from Fig. 5 that the graph for the plain tube is flatter than steeper graphs of dimple and protrusion tube indicating that for plain tube there is not much effect of velocity on heat transfer in case of the plain tube. Fig. 6 shows the flow characteristic for all three tubes.
-
Result and Discussion for Computer Simulation
The data obtained through computer simulation on Ansys software is used to tabulate table 6 which shows the variation of the percentage change in temperature drop for dimpled tube and protrusion tube. Further, it is used to plot a graph as shown in Fig. 8. From Fig. 8 it is clear that a drop in temperature at the outlet is maximum for protrusion tube followed by plain tube and lastly by dimpled tube. It is also seen that when input air is administered at lower velocity temperature drop is maximum in terms of giving more cooling. The causes of this phenomenon are already discussed in results and discussion of experimental work.
-
-
CONCLUSIONS:
The study concludes that protrusion tube is more suitable for evaporative coolers followed by plain tube and lastly by dimpled tube. It is found that heat transfer and percent temperature drop increase with the use of protrusions by about
-
% and 17.2 % respectively as compared to plain tube. It is also observed that flow characteristics like Reynolds number, Nusselt number increase with the use of dimples and protrusions without any significant pressure drop. Reynolds number increases in case of dimpled tube and protrusion tube primarily because of irregularities present on the inner surface of the tube and further due to conical shape of a tube. Reynolds number increase in the case of plain tube primarily because of the conical shape of a tube. The rate of heat transfer increases with an escalated Reynolds number and input temperature of the inlet flow of air. Though, higher input velocities increase the heat transfer it also led to more intermolecular frictions between air molecules and offer less contact with the wall surface of the wet tube resulting in a lower net temperature drop at the outlet. Thus, it is also concluded that the input air should be administered at lower velocities to get maximum temperature drop. Thus, to get maximum cooling effect protrusion tubes are to be used with lower input air velocities for Evaporative cooler applications like Deki cooling installations. Also, it is clear that simulation results support the experimental results and are in line with each other.
ACKNOWLEDGMENT
The authors thankfully acknowledge the financial support provided by The Institution of Engineers (India) for carrying out Research and Development in this subject.
REFERENCES
-
IEA Online Data Services. Available at, http://data.iea.org/ieastore/statslisting. asp.
-
Yifan Yang, Gary Cui, Christopher Q. Lan, Developments in evaporative cooling and enhanced evaporative cooling – A review, Elsevier Journal – Renewable and Sustainable Energy Reviews 113 (2019) 109230
-
Chenari B, Dias Carrilho J, Gameiro da Silva M, Towards sustainable, energy- ecient and healthy ventilation strategies in buildings: a review, Renew Sustain Energy Rev 2016;59:142647. http://dx.doi.org/10.1016/j.rser.2016.01.074.
-
Zomorodian ZS, Tahsildoost M, Hafezi M, Thermal comfort in educational buildings: a review article, Renew Sustain Energy Rev 2016;59:895906. HTTP:// dx.doi.org/10.1016/j.rser.2016.01.033.
-
Bhamare, D., Rathod, M. and Banerjee, J., 2019. Passive cooling techniques for building and their applicability in different climatic zonesThe state of the art. Energy and Buildings, 198, pp.467-490.
-
M.J. Moran, H.N. Shapiro, D.D. Boettner, M.B. Bailey, Fundamentals of engineering thermodynamics, John Wiley & Sons, 2010.
-
S.K. Wang, S.K. Wang, Handbook of air conditioning and refrigeration vol. 49, (2000) 49.
-
Kabeel, A., Bassuoni, M. and Abdelgaied, M., 2017. Experimental study of a novel integrated system of the indirect evaporative cooler with internal baffles and evaporative condenser. Energy Conversion and Management, 138, pp.518-525.
-
Lin, J., Wang, R., Kumja, M., Bui, T. and Chua, K., 2017. Multivariate scaling and dimensional analysis of the counter-flow dew-point evaporative cooler. Energy Conversion and Management, 150, pp.172-187.
-
Aftab Ahmad, Shafiqur Rehman, Luai M. Al- Hadhrami (2013), Performance evaluation of an indirect evaporative cooler under controlled environmental conditions, Energy and Buildings, vol. 62, pp. 278285
-
S. Alzahrani, S. Usman, CFD simulations of the eect of in-tube twisted tape design on heat transfer and pressure drop in natural circulation, Thermal Sci. Eng. Progress11 (2019) 325333.
-
S.P. Nalavade, C.L. Prabhune, N.K. Sane, Eect of novel ow divider type turbulators on uid ow and heat transfer, Elsevier Journals – Thermal Sci. Eng. Progress 9 (2019) 322331.
-
Y. Liu, X. Ma, X. Ye, Y. Chen, Y. Cheng, Z. Lan, Heat transfer enhancement of annular nned tube exchanger using vortex generators: The eect of oriented functional circumferential arrangement, Elsevier Journals – Thermal Sci. Eng. Progress 10 (2019) 2735.
-
A.E. Bergles, H.L. Morton, Survey and evaluation of techniques to augment convective heat transfer, 1965, Cambridge, Mass.: MIT Dept. of Mechanical Engineering.
-
F.A. Kulacki, S. Acharya, Y. Chudnovsky, R.M. Cotta, R. Devireddy, V.K. Dhir, M.P. Mengüç, J. Mostaghimi, K. Vafai, Handbook of Thermal Science and Engineering, Springer, 2018.
-
R. Boukhanouf, A. Alharbi, O. Amer, H. Ibrahim, Experimental and numerical study of a heat pipe-based indirect porous ceramic evaporative cooler, Int. J. Environ. Sci. Dev. 6 (2015) 104110.
-
Hemant C. Pisal, Avinash A. Ranaware, Heat Transfer Enhancement using Dimpled Surface, IOSR Journal of Mechanical and Civil Engineering (IOSR-JMCE) ISSN: 2278-1684, PP: 07-15
-