
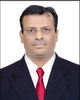
- Open Access
- Authors : Nilesh Kumar Popatlal Kankariya , Shailesh S. Pimpale , Dr. Subim N. Khan
- Paper ID : IJERTV9IS060750
- Volume & Issue : Volume 09, Issue 06 (June 2020)
- Published (First Online): 07-07-2020
- ISSN (Online) : 2278-0181
- Publisher Name : IJERT
- License:
This work is licensed under a Creative Commons Attribution 4.0 International License
Finite Element Analysis of Variable Thickness Disc Wheel Rim for Weight Optimization
Published by : http://www.ijert.org
International Journal of Engineering Research & Technology (IJERT)
ISSN: 2278-0181
Vol. 9 Issue 06, June-2020
Nilesh Kumar Popatlal Kankariya (1) ME (Design) Mechanical Engineering JSPMs R.S College of Engineering, Pune, Maharashtra.
Prof. Shailesh S. Pimpale (2) Mechanical Engineering Department JSPMs – R.S. College of Engineering, Pune, Maharashtra.
Dr. Subim N. Khan (3) Mechanical Engineering Department JSPMs R.S College of Engineering,
Pune, Maharashtra.
Abstract – The objective of this paper is to introduce light weight wheel rim by opting variable wall thickness of wheel disc without affecting its key functions and life. Wheel rim 3D model prepared in Pro-E software. Linear static structural analysis of wheel rim were performed in FEM – ANSYS software to determine stress level at various loading conditions, given boundary conditions to optimize disc thickness, weight, cost of wheel rim. The results of the FEA analysis to validate with the experimental test results.
Keywords Wheel rim; Wheel rim disc; Variable thickness; Pro-E design; FEA.
-
INTRODUCTION
A wheel rim is a highly stressed component in an automobile that is subjected to bending and torsional loads. Since it is subjected to high stresses and demand of long life, light in weight, which it becomes very important to select right material and manufacturing process in rim design. There are competitions among materials and manufacturing processes due to cost performance and weight. The main components of the wheels & tire system aggregates is the wheel rim. Performance of wheel rim directly affects the vehicle performance and safety. Wheel rim size selection is based on tire size used in vehicle, It has standard catalogue
– JATMA which recommends standard wheel rim size accordingly.
Tata 1109 ILCV Vehicle recommended wheel rim size is
-
x 20 is as per JATMA standard for 8.25R20-14PR tire size. Wheel rim was taken for weight optimization analysis and experimental study purpose refer below three piece wheel rim figure no.1
Fig. 1 : Three piece wheel rim nomenclature
In this perspective expecting wheel rim design with significant mass reduction without compromise in its function and performance. The above wheel rim weight can be reduced by recognizing various stress regions and corresponding changes in wheel rim design. Rim material can be removed wherever is lower stress region and has low vehicle load effect.
-
-
PROBLEM STATEMENT
Currently Tata 1109 ILCV vehicles recommended wheel rim size has higher weight, cost which need to be analyze and optimized under finite element analysis. Analysis of wheel rim to determine the material removal area, changes in von misses stresses and deformation for current and modified rim design within given boundary condition to gain significant advantages for lighter mass vehicle wheels.
-
METHODOLOGY
The methodology involves technology for performing the designing and analyzing of the object.
-
Design and modeling of three piece wheel rim
-
Dimension specification
-
Analysis by ANSYS
-
Analysis to perform at various load condition on existing and modified rim design.
-
Analysis of wheel rim under boundary condition to obtain deformation and von misses stresses of model.
-
Obtained optimized wheel rim and compare with existing model.
-
-
CAD DESIGN
Design Input parameters of TATA 1109 ILCV Vehicle
Existing Three Piece Wheel Rim Design:
-
Vehicle Tire size : 8.25 R20 – 14 PR
{Front – 2, Rear – 4, Spare – 1}
-
Wheel rim mass per wheel 42.5 kg
Published by : http://www.ijert.org
-
Recommended Wheel rim as per ITTAC : 6.5 x 20
-
Load on each wheel (rated and overload condition) : 2300 kg, 2650 kg, 3000 kg
-
Material : Rim Rst 37 & Disc Yst 38
-
Wheel rim disc manufacturing process – Press forming
-
Mass of Vehicle 3960 kg
-
Payload on vehicle 8710 kg
Existing wheel rim CAD design prepared using Pro-E Software.
-
Sketcher
-
Part design
-
Assembly design
-
Wireframe and surface design
-
Meshing & analysis by ANSYS software
Fig 2 : Existing Wheel Rim 2D Drawing
Fig 3 : Existing Wheel Rim 3D Model
International Journal of Engineering Research & Technology (IJERT)
ISSN: 2278-0181
Vol. 9 Issue 06, June-2020
Table 1: Existing Wheel Rim Specification
-
-
OPTIMIZATION SCOPE
-
Three Piece Wheel Rim Optimization Scope – Design The following are the design changes incorporated to reduce the wheel rim weight, cost and improve its performance:
-
Increase in nave thickness to avoid crack initiation in the region due to fretting.
-
Variable disc thickness to reduce weight and cost of rim.
-
Increased cold working effect on the product.
-
Optimized brake drum clearance thru variable thickness.
-
Wheel rim flow forming manufacturing process.
Specification
Existing Design
Modified Design
Wheel Size
Same as existing
Same as existing
Rim Thickness in mm
6
Optional
Rim Material
Rst 37-2
Optional
Bolt hole Diameter in mm
Ø24
Same as existing
Bolt hole Numbers
8
Same as existing
Bolt hole PCD in mm
275
Same as existing
Vent hole Numbers
8
Same as existing
Total Ventilation Area in cm2
144
Minimum 144
Disc Thickness in mm
11
Optional
Disc Material
Yst 38
Yst 38
Wheel Offset
134
134
Wheel Load in Kg
3000
Same as existing
Wheel Weight in Kg
42.4
Target 36 kg / Per wheel
Table 2: Wheel Rim Design Optimization Scope and Space
Published by : http://www.ijert.org
International Journal of Engineering Research & Technology (IJERT)
ISSN: 2278-0181
Vol. 9 Issue 06, June-2020
-
-
Three Piece Wheel Rim Optimization Scope -Process
-
The goal is to flow form and optimize disc weight.
-
Increase disc material yield strength
-
Process compress disc material to increase its hardening by cold working, hence we can get higher yield, tensile strength and thinner thickness
-
Reduce the rim weight without compromising the performance.
Fig 4: Wheel Rim Process Optimization Scope
-
-
OPTIMIZED CAD DESIGN
Modified Three Piece Wheel Rim Design
As per above table no. 2 and igure no. 4 where wheel rim design changes and process improvement were done for optimization, cad data has been modified in Pro-E.
Fig 5: Modified Wheel Rim 2D Drawing
Fig 6: Modified Wheel Rim 3D Model
Table 3: Wheel Rim material Specification
Table 4: Modified Wheel Rim Specification
Optimized wheel rim design proposal made based on Finite element analysis (FEA). Wheel disc thickness increased at the region identified to have higher stress and gradual reduction of material thickness at lower stressed regions.
The modification in the design is shown in the Fig. 5 and 6.
Following design changes to be incorporated to reduce rim weight and also simultaneously improve its performance:
-
Increase in nave thickness to avoid crack initiation in the region due to fretting
-
Variable disc thickness to reduce weight, cost of the product and new process of variable disc increased cold working effect on the product.
-
Improvement in brake drum clearances.
-
Adaptation of Rim Flow Forming manufacture process
-
Flange Shape Optimization
-
-
ANALYSIS
TATA 1109 ILCV wheel rim specification 6.5×20 design and modeled in 3D using Pro-E software. 3D model imported to ANSYS Workbench for further analysis such as cornering effect thru FEA and compare stress analysis at different loading condition.
Published by : http://www.ijert.org
-
Geometry of Three Piece wheel rim
Fig 7: Three Piece Wheel Rim Geometry
-
Boundary Condition
-
Wheel, adaptor, bolts modeled, assembled.
-
Tetrahedral mesh used for the wheel and hub.
-
Cornering load applied.
-
Rim flange fixed in all DOF.
-
Results viewed in the post processor.
Fig.8 : Boundary Condition
-
Meshing and Boundary Condition for Wheel rim
Meshing and boundary condition applied in ANSYS
to reduced degree of freedom from infinite to finite with the help of discretization or meshing (Nodes & Elements).
Wheel rim flange were fixed and cornering load applied.
International Journal of Engineering Research & Technology (IJERT)
ISSN: 2278-0181
Vol. 9 Issue 06, June-2020
Fig. 9: Meshing and Boundary Conditions
-
Wheel Rim Stress Distribution and Analysis
The wheels were loaded due to cornering and lateral effect and same was simulated at various test conditions and accordingly results are obtained. FEA evaluated displacement at each node of wheels according to the initial boundary conditions from which the strain can be calculated and then using Hookes law the stress at that point can be calculated using the Youngs modulus of the material of the wheel.
-
Equivalent Stress Results
10a 10b
Fig 10 (a) Stress plot with uniform thickness wheel disc at 30KN Fig 10 (b) Stress plot with variable thickness wheel disc at 30KN
-
-
-
RESULTS
The following table no. 5 shows comparative stress analysis results of existing as well as modified three piece wheel rim design with various load cases & boundary conditions.
-
Comparative Stress Analysis Results
Table 5: Comparative Stress Analysis Results
Published by : http://www.ijert.org
International Journal of Engineering Research & Technology (IJERT)
ISSN: 2278-0181
Vol. 9 Issue 06, June-2020
-
-
SUMMARY
-
The FEA comparative results shown in table no. 5 that the variable thickness disc had lower or equivalent stresses value as than existing wheel rim with uniform thickness.
-
Analysis shows the uniform thickness disc had a stress value of 170 MPa whereas the variable thickness disc wheel had a stress value of 162 MPa.
-
Peak stress is at the vent hole region for existing wheel rim with the thickness of 11 mm, by introducing variable thickness about 10 mm at same location the stress level can be brought down to 5 %.
-
Variable disc thickness achievable with an advanced manufacturing technique called the flow form / spinning process. This process facilitated the vent hole position in a single plane with adequate ventilation area and the reduction in stresses was also noticed.
-
With modified wheel rim design weight is reduced from 42.4 kg to 36 kg per wheel, which is approximately 16 % without affecting functional requirement.
REFERENCES
-
S.Chaitanya and B.V.Ramana Murty Mass Optimization of Automobile Wheel Rim, IJETT, 2015, 26 (3), pp 169-173.
-
Sourav Das Design and Weight Optimization of Aluminium Alloy Wheel, IJOSRP, 2014, 4(6), pp1-12
-
R. Muthuraj, R.Badrinarayanan and T.Sundararajan, Improvement in the wheel Design using realistic Loading Conditions FEA and Experimental Stress Comparison, SAE Technical Paper Series 2011-28-0106
-
R. Muthuraj and Dr.T.Sundararajan, The Forged Hybrid Wheel for Commercial Vehicles, A Robust Design for Augmented Product Service and Performance, SAE Technical Paper Series 2015-26-0068.
-
Haruo Nagatani & Tsuyoshi Niwa Application of Topology Optimization and Shape Optimization for Development of Hub- Bearing Lightening, TN Technical Review 73, 2015, pp14-19
Reference Standard
-
IS: 9438-Performance Requirements and Methods of test for Wheels/Rims for Trucks and Buses standard, 2000.
Reference Book
-
Reference Manual ITTAC, 2014