
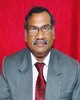
- Open Access
- Authors : K. L. Ratnakar , Dr. B. Rajesh Kamath
- Paper ID : IJERTV9IS090481
- Volume & Issue : Volume 09, Issue 09 (September 2020)
- Published (First Online): 06-10-2020
- ISSN (Online) : 2278-0181
- Publisher Name : IJERT
- License:
This work is licensed under a Creative Commons Attribution 4.0 International License
Comparison of Partial Discharges Occurring in The SF6 – N2 (10:90) Gas Mixture Between Uniform Electrodes
K. L. Ratnakar, Dr. B. Rajesh Kamath, Professors in Electrical and Electronics Engineering, Sri Siddhartha Institute of Technology, Tumakuru,
Karnataka.
Abstract: Partial discharge (PD) is an electric discharge that does not completely bridge the space between the two conducting electrodes. In all the high voltage operating devices, normally partial discharge activity will be present. The usage of spacers in between the electrodes will increase the insulation strength and reduces the intensity of PD provided the spacer material happened to be healthy without any leakage paths either through the material or through the surface discharges. As the time prolongs the PD activity inside the insulation media leads to breakdown of insulation. The study of PD is necessary to understand the performance of Insulator operating at high voltages and gives the idea to improve its performance. The usual cause of PD activity is the presence of any conducting metal particles on the electrodes or on the spacers. If the spacers are defective then also there will be conductive path either through the material or surface discharge. Another possible reason for PD is having voids of any shape in the insulating spacers creates the weak zone in the insulating material and responsible for the occurrence of PD. The PD activity inside an insulator needs to be monitored continuously. Though the PD discharges in the magnitude of micro coulombs, but their continuous presence makes the progressive deterioration of insulation and may lead to failure of insulation. In this work experiments have been conducted on plane plane electrodes with insulating spacers Polymethylmethacrylate (PMMA) of cylindrical shape of different thicknesses have been used as dielectric between the electrodes when the chamber is filled with SF6-N2 gas mixture with varying pressure. The following data has been taken while performing the PD test.. The discharge current (ID), Discharge Power (PDis) and number of PD events per second with respect to the phase angle .are noted in this paper. To plot the PD graphs of 2D and 3D the Omicron MPD 600 software and hardware are employed.
Keywords: Discharge Current (ID), Discharge Power (PDis), number of events per second (n), Spacer.
-
INTRODUCTION:
The partial discharges are generated due to local electric field concentrations inside the insulation material or in its outer surface. The surface discharges in a gaseous media are called as corona partial discharges usually produce a voltage or current signals with duration less than 1s. The high voltage operating devices and the generating stations operate at very high voltages. When the high voltage is applied to a electrode gap filled with a dielectric, PD may occur that do not lead to the loss of insulating properties of the dielectric as a whole. At this time the pulses of current are registered in the discharge circuit. The number and intensity of which can predict the probability of a breakdown of the gap. PD
normally occurs at the defected sites within the insulation system because of higher breakdown strength of insulation material than the defect site. Even if the insulator is perfect there may occur the surface discharge or corona discharge when the voltage between the electrodes was increased beyond the inception voltage [1-3]. The added advantage of the electrode setup in the gaseous chamber indicates that the breakdown voltage will be high because of the presence of insulating gas and spacers in between the electrodes [4-6]. The PD may occur due to the voids which were filled with gas during the manufacturing. The breakdown of insulation system causes the need for the costly and time consuming maintenance as the whole unit of insulation need to be replaced. To avoid this PD measurement and PD data analysis are essential to assess the performance and condition of the insulation system in order to avoid the unwanted breakdown [7-11]. The PD is measured at variable frequency of the applied voltage. The added advantage of this method is that local conditions at defects in the insulation change with the varying frequency. As a result with the change in the frequency the PD activity also changes. An added advantage of the variable frequency phase resolved Partial Discharge analysis at low frequency is possible with low power consumption.
-
EXPERIMENTAL PROCEDURE:
The arrangement of electrodes in the chamber for the desired gap length keeping the same thickness spacer of PMMA in between the electrodes is made. Then the chamber as shown in figure 1 is made air tight and then filled with gas of SF6 N2 gas of (10:90) at different pressures. After filling the gas in the chamber it is connected in the PD circuit and the voltage is applied gradually and the PD is recorded. The SF6
N2 Gas pressure is varied from 0.1Mpa to 0.3MPa and the change in PD with respect to the increase in gas pressure is studied.
Before starting the experimentation the MPD 600 measuring system is first calibrated by connecting a PD calibrator across the test object. The PD measuring system is calibrated for voltage measurement as well as capacitance calibration by applying a certain known voltage much below the inception voltage, across the test object.. The calibrator is disconnected and the sample is connected to a PD free, HVAC source across the test object, through a RC divider. After calibration the software is shifted to expert mode and made the selection of settings of frequency, charge and voltage. The voltage is
then increased gradually until it reaches a value 20% above the discharge inception level and reduced gradually to zero to record the extinction voltage. The setup of the electrodes with spacer for different electrodes is considered at a time with variation in the gas pressure from 0.1MPa to 0.3MPa. For all the sets of the readings the histogram of 3D and PD graph of 2D plots have been captured and presented in this paper.
-
RESULTS AND DISCUSSIONS:
The experimental results of Plane Plane Electrode setup with PMMA spacer with variation in spacer thickness at different gas pressures are as shown in figures 2 to figure 10. The chamber with electrode arrangement has the provision to fill the insulating gas of SF6-N2 gas mixture of 10:90 is filled and maintained at different pressures. The 3D PD graphs show the variation of number of PD pulses/sec, and magnitude of charge with respect to phase angle. The gas chamber is filled with gas and maintained its pressure at 0.1MPa and the PD is recorded. Similar recordings are made for 0.2MPA and 0.3MPa pressures. Two variables have been considered in the experimentation, variation in gap and variation in pressure.
Figure 1: Gas chamber to house the Electrodes, filled with gas and maintain at different pressures.
Figure 2: 3D PD graph of 5mm gap at 0.1MPa pressure
Figure 3: 3D PD graph of 5mm gap at 0.2MPa pressure
Figure 4: 3D PD graph of 5 mm gap at 0.3MPa pressure
It is observed that with the increase in the gas pressure from 0.1MPa to 0.3MPa the number of PD pulses per second decreased from 1455 PD/s to 537 PD/sec. The discharge current has decreased from 21.8 nC/sec to 8.98 nC/sec. The discharge power also decreased from 78.8 W to 29.95 W. It is observed that PD is more predominant in negative half cycle at the angle of 2880 to 3240 and in the positive half cycle in between 00 to 360. As the gas pressure increases there is decrease in the PD activity. All this data we get from 2D PD graphs. Similarly the fllowing graphs of 3D PD for 10mm and 15mm gap lengths have been shown.
Figure 5: 3D PD graph of 10 mm gap at 0.1MPa pressure
Figure 6: 3D PD graph of 10mm gap at 0.2MPa pressure
Figure 7: 3D PD graph of 10 mm gap at 0.3MPa pressure th.
The PD activity gets reduced due to increase in the thickness of the spacer. It is obeserved that the number of PD pulses/sec, the discharge current and discharge power is decreased and the values have been given in the table 1.The variation of PD pulses per second is between 918 to 643.8PDs/sec. Similarly the current and Power discharge are varying from 13nC/sec to 8.69nC/sec and discharge power from 48.64W to 16.18 W.
Figure 8: 3D PD graph of 15 mm gap at 0.1MPa pressure.
Figure 9: 3D PD graph of 15 mm gap at 0.2MPa pressure.
Figure 10: 3D PD graph of 15 mm gap at 0.3MPa pressure
The two 2D graphs of PD indicate the Discharge Current, Discharge Power, Number of PD events per second against the phase angle of the voltage waveform. The data has been recorded in the tables 1 to 3 for different gap lengths and different gas pressures. The colour variation in the PD graph indicates the variation in the PD activity over the phase angle variation of the appled voltage.
Figure 11: 2D PD graph of 5mm gap at 0.1MPa pressure
Figure 12: 2D PD graph of 5mm gap at 0.2MPa pressure.
Table1 shows the values of number of PD pulses per second, Table 2 shows the value of Power discharge and table 3 shows the values of discharge current due to PD for different combinations of gas pressure and gap lengths for uniform electrodes.
Table 1: Number of pulses (n) in PDs/sec
Gap/Pressure
0.1MPa
0.2MPa
0.3MPa
5mm
1455
982
537
10mm
918
720
644
15mm
584
514
465
Table 2: Power Discharge(PDis in W)
Gap/Pressure
0.1MPa
0.2MPa
0.3MPa
5mm
78.81
46.57
29.95
10mm
48.64
40.60
16.12
15mm
38.62
35.55
24.14
Table 3: Current Discharge(ID in nC/s)
Gap/Pressure
0.1MPa
0.2MPa
0.3MPa
5mm
21.18
14.07
8.98
10mm
13.12
10.48
8.69
15mm
9.24
7.63
5.96
-
CONCLUSIONS:
-
The numbers of PD pulses are decreasing with increase in gap length at constant voltage and it is 37% at 10 mm gap, and 60% at 15mm gap with respect to the 5mm gap length.
-
The numbers of PD pulses are decreasing with the increase in the gas pressure from 0.1MPa to 0.3MPa. and it is 33% at 0.2MPa, 63% at 0.3MPa gap lengths with respect to the 0.1MPa pressure.
-
The power discharge is decreasing with increase in the gap length at constant pressure of 0.1MPa and it is 38% at 10 mm, 51% at 15mm gap with respect to the 5mm gap length.
-
The power discharge is decreasing with the increase in the gas pressure at constant gap length of 5mm, it is 41% at 0.2MPa, and 62% at 0.3MPa with respect to the 0.1MPa pressure.
-
The current discharge in between the electrodes is decreasing with increasing in the gap at constant pressure, it is 33.6% at 10mm, 68% at 15mm gap lengths with respect to 5mm gap length.
-
The current discharge also decreasing with increase in gas pressure at constant gap length, and it is 33.5% at 0.2MPa, 57.6% at 0.3 MPa with respect to the 0.1MPa gas pressure.
-
Thus we can increase the operating range of the given circuit breakers by increasing the gap or by increasing the pressure of the insulating media or both.
5. REFERENCES:
-
Evgeni Volpov, Dielectric Strength Coordination and generalized Spacer Design Rules for HVAC/DC SF6 gas insulated system, IEEE Transactions on Dielectrics and Electrical Insulation, Vol 11, No. 6, pp. 949-963, December 2004.
-
Edward Gulski, Digital Analysis of Partial Discharges, IEEE Transactions on Dielectrics and Electrical Insulation, Vol 2, No. 5, pp. 822-837, October 1995.
-
E. Gulski, Diagnosis of HV Components by Digital PD Analyzer, IEEE Transactions on Dielectrics and Electrical Insulation, Vol. 2, pp. 630-640, 1995.
-
H. Edin, Partial Discharges Studied with Variable Frequency of the Applied Voltage, Ph.D. Thesis, KTH, Stockholm, Sweden, 2001.
-
T. Yamada, T. Ishida, N. Hayakawa et.al., Partial Discharge and Breakdown Mechanisms in Ultra-dilute SF6/N2 Gas Mixtures, IEEE Transactions on Dielectrics and Electrical Insulation, Vol. 8, pp. 137-142, February 2001.
-
L. Niemeyer, A Generalized Approach to Partial Discharge Modeling, IEEE Transactions on Dielectric. and Electric Insulation., Vol. 2, pp.510-528, 1995.
-
S.A. Boggs, Partial Discharge: Overview and Signal Generation, IEEE Electrical Insulation Magazine, Vol. 6, No. 4, pp. 33-42, July/August 1990.
-
Shuhei Kaneko, Shigemitsu Okabe, Electromagnetic Wave Radiated from an Insulating spacer in Gas Insulated Switchgear with PD Detection, IEEE Transactions on Dielectrics and Electrical Insulation, Vo.16, No 1, PP, 60-68, September 2009.
-
S. Okabe, S. Kaneko, M. Yoshimura, H. Muto, C. Nishida and M. Kamei: Partial Discharge Diagnosis Method Using Electromagnetic Wave Mode Transformation in Gas Insulated Switchgear IEEE
Transactions on Dielectrics and Electrical Insulation, Vo.14, PP, 702-709, 2007.
-
J. S. Pearson, B. F. Hampton and A. G. Sellers: A continuous UHF monitor for gas-insulated substation, IEEE Trans. Electr. Insul., Vol. 26,, pp. 469-478, 1991.
-
B. Rajesh Kamath, Member, IAENG , J. Sundara Rajan, K. A. Krishnamurthy, M. Z. Kurian, PD Characteristics of 10:90 SF6- N2 Gas Mixtures with Particle and Dielectric Coating of Metal Electrodes, Proceedings of the World Congress on Engineering and Computer Science 2012 Vol II, WCECS 2012, October 24-26, 2012, San Francisco, USA
BIOGRAPHIES
Prof. K.L.Ratnakar got his B.Tech and M.Tech degrees in the year 1983 and 1985 from JNTU college of Engineering Kakinada. He has joined as Lecturer in Sri Siddhartha Institute of Technology, Tumkur in the year 1985 and he has grown in his profession along with his service to the height of Professor in Electrical and Electronics Engineering. He has authored a text book on Electrical Power Transmission and Distribution for third year B.E. students. He was a life member Indian Society for Technical Education MISTE and Institution of Engineers (India) M.I.E., professional bodies. He has presented 20 papers in national and international conferences. He has visited BRISBANE, Australia to present a technical paper in the International Conference in the year 2007. In 2019 his text book has become an International publication by New Academic Science, of New Age International (UK) Ltd.
Dr. B. Rajesh Kamath is a senior faculty of Sri Siddhartha Institute of Technology, Tumkur, and served as Dean Academic and Head of the Department of Electrical and Electronics Engineering. He has presented many technical papers in national and International conferences. He had been to San Francesco of USA, Dubai, Singapore for presentation of his research papers. He was Fellow of Institution of Enginers (India) F.I.E., life member of Indian Society for Technical Education MISTE. He also chaired many technical sessions in the national and International conferences. At present he was a senior Professor in the Department of Electrical and Electronics Engineering.