
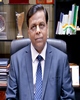
- Open Access
- Authors : Anoop Kumar Kanaujia , Narendra Mohan
- Paper ID : IJERTV10IS050435
- Volume & Issue : Volume 10, Issue 05 (May 2021)
- Published (First Online): 05-06-2021
- ISSN (Online) : 2278-0181
- Publisher Name : IJERT
- License:
This work is licensed under a Creative Commons Attribution 4.0 International License
Bio-Energy from Indian Sugar Industry: A Sustainable Renewable Energy Future
¹Narendra Mohan & ²Anoop Kumar Kanaujia
National Sugar Institute, Kanpur, Uttar Pradesh, India
Abstract India is the world's second largest sugar producer during 2019-2020, narrowly losing the top spot to Brazil. India produced 28.9 million metric tons of sugar which is about 17% of the world's total sugar production of 166.18 million metric tons. Also, the country expects sugar production to rise by around 17% for 2020-2021. However, the Indian sugar industry lacks in sustainability due to imbalances in demand-supply of sugar. The Indian sugar industry is faced with a reality that sugar, molasses and bagasse can no longer be regarded as final product from sugar industry and thus, value additions, diversifications and transformations to be vigorously investigated as possible routes to new market and making sugar industry less dependent on single commodity i.e. sugar. The future of the sugar industry, as a whole, lies in development of sugarcane bio-refineries i.e. bio-electricity, bio-ethanol, bio-gas/ bio-CNG, bio-manure, bio-plastic and chemicals etc.
Keywords Biomass, Bio-ethanol, Bio-electricity, Bio-gas, Bio- CNG.
INTRODUCTION
Conventional sugar factories process sugarcane to obtain crystal sugar, molasses and energy co-products from bagasse. At present, only about 50% of the Indian sugar factories are carrying out power export to national grid, whereas, the number of ethanol units attached to sugar factories is bit higher. Hence, the potential of value addition through better utilization of by-products even in the most common manner is not fully harnessed. Utilization of by-products even in the most generalized manner, thus, can not only perk up the financial health of the sugar industry but also in meeting the
scarcity of power and ethanol for EBP programme, the bio- energy in either case.
Moving further, a bio-refinery includes the sustainable processing of sugarcane into range of valuable products (including food, feed, molasses and chemicals) and energy (including power, fuels and heat) and thus, offers great potential for improving profitability and sustainability of the Indian sugar industry [1].
The sugar industry across the globe is also required to work on the mandate developing Wealth from Waste or converting Waste to Resource utilizing anything which is available with sugarcane or is generated in one or other form of processing. Thus, for sustainability of the Indian sugar industry or sugar industry as a whole, it includes improvement in the sugarcane and sugar productivities, conversion from single-product to multi-product factory, optimizing cost of sugarcane processing, integration with food processing industry, utilization of huge infrastructure during off-season, adoption of hybrid system for power generation i.e. biomass: solar: wind power and finally conversion of existing sugar factories to bio-refineries. (Fig.1)
In terms of bio-energy, the major sugarcane energy chains/ sources are;
-
Bagasse for heat & bio-electricity generation.
-
Molasses for conversion to bio-ethanol.
-
Press mud and spent wash for conversion bio-gas.
Biocomposites Tableware Particle Board Pulp
Lignin
Ethanol/Bio-crude Chemicals
Chemical Bio-plastics
Baking/ Candy Making
Cattle Feed
Bio-fuels Pharmaceuticals Industrial Products
Fertilizers
Bio-gas/ Bio-CNG
Wax
Proteins
Plant made products
High Value Chemicals
Renewable Electricity
Fig.1 Bio-Refinery Concept
Bio-Electricity
Sugarcane is one of the most promising agricultural sources of biomass energy in India and elsewhere. In sugarcane plant the overall % by weight of dry matter and the energy content is given in Table 1.
Table 1 Dry Matter in Sugarcane Plant
S. No. |
Part of the Sugarcane Plant |
Dry Matter by Weight % |
% Energy Content |
1 |
Roots |
2 |
1.23 |
2 |
Stalk |
58 |
62.63 |
3 |
Leaves |
14 |
24 |
4 |
Top |
26 |
12.14 |
At present, only sugarcane stalk is processed to extract juice and bagasse, the fibrous residue left over after the milling. The balance 37.37 % of energy of the sugarcane plant remains unutilized. This energy needs to be used efficiently. It is fact that for the soil conditioning and its fertility improvement, part of the Sugarcane Plant Residue (SPR) should be used in mulching. Even, if 50% of the SPR is left for mulching, the balance 50% of SPR is a huge source of bio-energy and efficient utilization of the same may enhance the revenue of the sugar industry to a greater extent. The revenue generation for a 5000 TCD Plant in respect to utilization of 50 % SPR is given in Table 2.
Table 2 Revenue from SPR
S.No. |
Particulars |
Unit |
Quantity |
1 |
Cane crushed per day |
TCD |
5000 |
2 |
Season Days |
Days |
160 |
3 |
SPR (dry) |
MT |
196960 |
4 |
50% SPR (dry) |
MT |
98480 |
5 |
Steam Produced at 125 ata /540 deg |
MT |
364376 |
6 |
Power Produced |
Lakh Units |
958.9 |
7 |
Sale Price @ Rs 5/- per unit |
Lakh |
4794.4 |
8 |
Cost of SPR (dry) |
Lakh |
2462 |
9 |
Cost of Conversion |
Lakh |
1438.3 |
10 |
Net saving |
Lakh |
894.1 |
11 |
Sugar Production at 10 % Recovery |
MT |
80000 |
12 |
Revenue/ MT sugarcane |
/MT Cane |
111.8 |
Bagasse is usually combusted in boiler furnaces to produce steam for power generation but now is also being considered as an emerging and attractive feedstock for 2G bio-ethanol production. It is also utilized as the raw material for production of paper, particle board and tableware etc.
Bagasse based co-generation is one of the most attractive and successful power projects that have already been implemented in many of sugar factories in India. Combined heat and power from sugarcane in the form of power generation offers renewable energy options that promote sustainable development, take advantage of domestic resources, increase profitability and competitiveness in the industry, cost-effectively address climate mitigation and other
environmental goals. For efficient utilization of biomass, bagasse based co-generation in sugar mills have been promoted by co-generation programme under Ministry of New and Renewable Energy (MNRE), Government of India.
Most of the sugar factories in India, cogeneration units work at very low cycle efficiency. For 67 ata and 87 ata pressure, the cycle efficiency is as low as15 to 18% only whereas it is between 21 to 25% for 110 ata and 125 ata pressure. Power plants operate at cycle efficiencies as high as
35 to 45%. To improve upon, the working pressure and temperature needs to increase up to 140 ata and 560 deg C so as it may reach up to 35% of the efficiency. Another factor which needs to be improved for increasing the pressure and temperature is the moisture content of bagasse. Moisture of bagasse is to be brought down to as low as possible by use of waste heat going out of chimney. Details of cycle efficiency and power generated is given in the Table 3.
Table 3 Cycle Efficiency at Different Pressure
Boiler Pressure |
ata |
67 |
87 |
110 |
125 |
140 |
160 |
225 |
Cane crushed per hour |
MT |
1 |
1 |
1 |
1 |
1 |
1 |
1 |
Bagasse Produced |
MT |
0.3 |
0.3 |
0.3 |
0.3 |
0.3 |
0.3 |
0.3 |
Steam Produced |
MT |
0.7 |
0.7 |
0.7 |
0.81 |
0.84 |
0.87 |
0.96 |
Power Potential |
MW |
0.14 |
0.17 |
0.2 |
0.23 |
0.28 |
0.32 |
0.4 |
PP Efficiency |
% |
18 |
21 |
24 |
29 |
35 |
40 |
50 |
Advantages of Bio-Electricity
Generating bio-electricity offers numerous benefits as;
-
A rich & renewable source and of high potential to substitute fossil fuels to meet energy demands of the country. It is also less expensive than fossil fuels.
-
It provides clean and green energy because of neutral emission of carbon dioxide (CO2) [2].
-
Decentralized power generation results minimal transmission and distribution costs [3].
-
It enables diversification in electricity generation, thus, increasing energy security.
-
Significant reduction of environmental pollution in relation to use of fossil fuels [3].
-
It helps sugar mills to meet 100% of their energy needs and drastically reduce their operational costs. Furthermore, the opportunity to sell surplus electricity to electric power grid [4].
-
Additional revenue generation through sale of carbon credits in terms of Clean Development Mechanism (CDM) [5] and Renewable Energy Certificate (REC).
-
Improved gross Station Heat Rate (SHR) of 5500 Kcal/ kWh with high pressure boiler/ turbine combination.
-
Assists in modernizing the rural areas by promoting sustainable rural growth.
Indian Electricity Sector Scenario
The utility electricity sector in India had an installed capacity of about 382.0 GW as on March 2021. Renewable power plants constitute 94.4 GW i.e. about 25% of total installed capacity, out of which, contribution of biomass based
% Contribution
% Contribution
cogenerated power is 10.0 GW i.e. 11.0% of total installed Renewable Energy Sources (RES) capacity. RES includes Small Hydro Projects, Biomass Power, Urban & Industrial Waste Power, Solar and Wind Energy. (Fig.2)
61.4%
61.4%
60.0
50.0
40.0
30.0
20.0
60.0
50.0
40.0
30.0
20.0
12.1%
10.3%
10.5%
12.1%
10.3%
10.5%
10.0
10.0
1.8%
1.3%
2.7%
1.8%
1.3%
2.7%
0.0
0.0
Thermal
Nuclear
Hydro
Wind
Solar
Small Hydro Biomass
Thermal
Nuclear
Hydro
Wind
Solar
Small Hydro Biomass
Fig. 2 Installed Power Capacity in India as on March, 2021 Source: CEA Data March 2021
During last five years, the installed biomass power capacity has increased by about 130% and achieved targeted capacity of 10.0 GW in early 2020, in which the bagasse based co-generated power played a vital role. (Fig.3)
The current exportable energy from excess bagasse in sugar factories is about 3500 MW, which is 1.0% of the national electricity generation, with only part of the sugar factories undertaking power export and also as only about one-third sugar factories out of 275 co-generating sugar factories have high pressure co-generation system. With the availability of advanced co-generation technologies, sugar factories can harness the onsite bagasse resource to go beyond meeting their own energy requirements and produce more surplus electricity for sale to the national electric power
commercially proven co-generation technologies. New technologies like steam parameters with extra high pressure and temperature configuration, modified design of fuel handling system and furnaces, higher blending of other biomass along with bagasse, improvements in pollution control devices and water treatment plants etc. have to be made to increase the potential to this level. The exportable power potential may be further increased by around 15% i.e. to 14.0 GW after installation of bagasse drying system [6].
Table 4 Power Export Potential in Different Models of Co-Generation
MMT Million metric tonnes
Pressure (ata) |
Cane Crushed (MMT) |
Bagasse Available (MMT) |
Exportable Power (MW) |
Power from Cane Trash (MW) |
Total Exportable Power (MW) |
67 |
300 |
87.0 |
5093 |
800 |
5893 |
125 |
300 |
87.0 |
11111 |
1500 |
12611 |
Presently direct-combustion technology to generate steam for production of electricity through condensing-extraction steam turbine (CEST) system is dominant, but the future is focused on the introduction of high-efficiency gasification combined-cycle systems [7]. In this system gas turbines fuelled by gas produced by thermo-chemical conversion of biomass. The exhaust is used to raise steam in heat recovery systems used in expanding through a steam turbine to boost power output and efficiency in a gas turbine/steam turbine combined cycle (GTCC). Gas turbines, unlike steam turbines, are characterized by lower unit capital costs at modest scale, and the most efficient cycles are considerably more efficient than comparably sized steam turbines. (Fig.4)
Flue Gases
9.88
9.88
grid.
10.15
10.15
Biomass
Dryer Gasifier Gas Cleaning
10.00
10.00
9.10
9.10
8.70
8.70
8.00
8.00
Insatalled Capacity (GW)
Insatalled Capacity (GW)
Gas G Turbine
6.00
6.00
Heat Recovery
Steam Generator
Steam G Turbine
4.80
4.80
4.42
4.42
4.01
4.01
4.00
4.00
3.60
3.60
Fig. 4 Simplified Schematic of a Biomass Integrated- Gasifier/ Gas Turbine
Combined Cycle (BIG/GTCC) System
2.00
2.00
0.00
0.00
2014
2015
2016
2017
2018
2019
2020
2021
2014
2015
2016
2017
2018
2019
2020
2021
Fig. 3 Biomass based Installed Power Generation Capacity in India Source: MNRE Data 2021
Potential of Power Export from Sugar Industry
Keeping in view the average cane crush of 300 MMT during a crushing season, the potential of the sugarcane industry nationwide is estimated as around 12.5 GW that can be exported to the grid on the basis of power generation @ around 150 kWh per tonnes of cane processed using the latest
The potential of power generation in such case may as high as 225-250 kWh per ton of cane as compared to 120-150 kWh through CEST system.
Bio-Ethanol
Increase on worlds energy demand and the progressive depletion of oil reserves motivate the search for alternative energy resources, especially for those derived from renewable materials such as biomass. Global concern about climate change and the consequent need to diminish greenhouse gases emissions have encouraged the use of bio-ethanol as a gasoline replacement or additive. Bio-ethanol may also be
used as raw material for the production of different chemicals, thus driving a full renewable chemical industry.
In recent years, energy consumption and global carbon intensity (the ratio between carbon emissions and energy supplied) have increased worldwide, reinvigorating worries about potential depletion of fossil fuel reserves. Such increase, accompanied by growing political instability in oil- producing regions, has instigated many countries to search for alternative forms of energy [8].
In most cases, this alternative source is renewable, since the CO2 emitted into the atmosphere is recaptured by the growing crop in the next growth cycle. Ethanol from sugarcane is one of the most promising bio-fuels because its energetic balance is generally positive, meaning that the growing sugarcane absorbs more carbon than is emitted when the ethanol is burned as fuel.
Ethanol (EtOH) may be produced using sugarcane bagasse as raw material through the organosolv process with dilute acid hydrolysis, thus increasing ethanol production with the same cultivated sugarcane area [9]. The area, however, requires in intensive study before adopting it on commercial scale with respect to economics of production and comparative advantages between power generation vis-a- vis EtOH production.
U.S. Environmental Protection Agency (EPA) classified that sugarcane ethanol as capable of reducing green house gas (GHG) emissions by at least 50% compared to gasoline [10].
Roughly, one ton of sugarcane biomass based on sugar, bagasse and ethanol output has an energy content equivalent to one & half barrel of crude oil [10]. The sugarcane plant, therefore, takes on special significance as the worlds most economically significant energy crop and presents exciting opportunities as well as challenges if it is to reach its potential as a bio-energy resource.
Overview of Indian Alcohol Industry
India is a fast-growing economy and is facing the challenge of increasing energy demand which is usually met by fossil fuels. Indias domestic production of crude oil since been inadequate to cope up the requirement, this huge gap between demand and supply is met by imports at the cost of foreign exchange draining out. Ethanol is such a fuel which can partially or fully replace fossil fuels. In India, at present, for the proposed 10% blending approximately 3500 million litres of ethanol is required. Ethanol in India is mainly produced by the fermentation/ distillation of final molasses i.e. C- molasses, the by-product and B-Heavy molasses of cane sugar industry.
The production of C-molasses in India, under normal circumstances is about 12 to 13 million tonnes per year which can produce alcohol to an extent of around 2800-3000 million litres, out of which the produce is also utilized by potable and industrial sector. As a result of it, the blending targets of about 5% could be achieved with the amount of available ethanol obtained through the conventional i.e. C-molasses route.
India, at present, targeting ethanol blending @ 10% in petrol, produces it mainly by molasses route. The installed capacity of about 6500 million litres per annum (3/4th molasses and 1/4th grain based) is grossly underutilized due to shortage of raw material i.e. molasses. Statistically, India
produces about 3% and 1% of the world alcohol and fuel alcohol respectively. However, many policy interventions viz. financial assistance for setting up new ethanol plants/expansion of existing plants and differential pricing policy for ethanol made out of various feed stocks from sugar factories i.e. C-molasses, B heavy molasses, cane juice/syrup/sugar have been made to ensure higher availability of ethanol in future.
Table 5 Molasses and Estimated Alcohol Production Potential Considering 5% diversion of molasses for export, cattle feed, other uses and wastage/deterioration etc. and assuming an average realistic yield of alcohol
@ 235 litres/ton of molasses (considering average Total Reducing Sugar Content as approx. 47.5)
Sugar Season |
Total Molasses Production (million tons) |
Molasses Available for Alcohol Production (million tons) |
Estimated Alcohol Production Potential (million litres) |
2015-16 |
10.87 |
10.33 |
2427.4 |
2016-17 |
9.03 |
8.57 |
2015.1 |
2017-18 |
14.06 |
13.36 |
3139.6 |
2018-19 |
13.79 |
13.10 |
3078.2 |
2019-20 |
11.53 |
10.95 |
2573.2 |
Table 6 Target for Ethanol Blending Programme
Particulars |
2018-19 |
2019-20 |
2020-21 |
2021-22 |
Petrol sale projection @ 8.38% CAGR |
32415 |
35131 |
38075 |
41226 |
Ethanol requirement @ 5% blending |
1621 |
1757 |
1904 |
2063 |
Ethanol requirement @ 10% blending |
3241 |
3513 |
3808 |
4127 |
Ethanol requirement @ 20% blending |
6483 |
7026 |
7615 |
8253 |
All figures in million litres
It is pertinent to mention that during 2020-21, the potential of alcohol production from sugar industry is about 2800 million litres through C-molasses route and about 1200 million liters through sugar cane juice and B-Heavy molasses diversion route. The requirements for potable liquor industry and other industrial uses is about 1500 and 500 million litres respectively. Even if the 500 million litres of alcohol production is considered from grain based distilleries, 2500 million litres of ethanol shall be available for national Ethanol Blending Programme (EBP), which shall be sufficient for about 6.5% of the blending target. Keeping this in view, to achieve the blending target of 10%, there is need to encourage more utilization of alternative feed stocks available with the sugar industry viz. B-Heavy molasses, sugarcane juice and sugar syrup may be considered to cope up with the requirement.
Under the situation of excess sugar production, lower sugar prices and favorable market economics, diversion of sugarcane juice or diversion of other intermediate molasses (B-Heavy molasses) holds promise considering the relative economics of ethanol vis-a-vis sugar production. The ethanol production from cane juice and B-Heavy molasses is reported to be about 70-75 litres/ton and 300-330 litres/ton respectively. The diversion shall result into:
-
Better capacity utilization of the distilleries.
-
Variation on the ratio of sugar and ethanol produced according to the market, resulting in sugar price
stabilization and coping up with the requirement of EtOH for EBP.
-
Sugar of better quality no need o recycle molasses or juices of low purity and thus price premium over the produce.
Carbohydrates
Fats
Sugars
Fatty Acids
Carbonic Acids & Alcohols
Hydrogen Carbon
Hydrogen Acetic Acid Carbon Dioxide
Methane Carbon Dioxide
In addition to this, the conventional distilleries may beProteins
Amino Acids
Dioxide
Ammonia
converted to SMART distilleries utilizing other alternate feed stocks available in different regions of the country. The potential of EtOH production may be harnessed by utilizing Cassava, Sugar Beet and Sweet Sorghum as available in different agro-climatic zones. As discussed earlier, more work shall be required to develop a cost effective, indigenous technology for production of EtOH from Lignocellulosic material including bagasse.
Apart from the above, considering the ample amount of available grains which is not found suitable for human consumption may be utilized for production of ethanol by converting the existing molasses based distilleries into dual feedstock based distilleries. The Government of India has already announced policy in this regard and it is expected that more Dual Feed Stock based ethanol units shall be set up in future.
A holistic approach on the above will result into integration of more distilleries with the sugar factories, optimal capacity utilization of the existing distilleries and increased availability of alcohol for all sectors, resulting into a win-win situation for all the stakeholders.
Bio-Gas and Bio-CNG
Conventionally, handling of the filter cake in the sugar industry is considered to be a troublesome area and whatever utilization is made is in making the bio-compost. However, in pursuit of generating higher revenues, the unharnessed potential of filter cake has been exploited by utilizing for generating bio-gas or bio-CNG/ CBG. Filter cake contains appreciable proportion of biodegradable organic matter which has very good potential for the production of bio-gas from it. Bio-gas from filter cake can be produced by anaerobic digestion which is a biochemical degradation process wherein organic matter is decomposed by bacteria in the absence of oxygen [11]. The anaerobic digestion is low-cost method and the byproducts of this process are methane, CO2 and H2S. It is a complex process and divided into four categories: Hydrolysis, Acidogenesis, Acetogenesis or dehydrogenation and methanation. (Fig.5) The use of bio-gas or compressed biogas/bio CNG will not only help to preserve the non- renewable energy resources but will also decrease dependence on scarce fossil resources and will also lead to decrease in green house emission and earning additional revenue in case of sugar factories. In addition to that, in our day-to-day life we come across different types of waste such as municipal solid waste, food waste, industrial waste, sewage sludge, animal manure and agricultural residue etc. having the good energy potential may be converted into bio- gas/bio-CNG.
Hydrolysis Acidogenesis Acetogenesis Methanogenesis
Fig. 5 Anaerobic Digestion Process
It has been estimated that 1 tonne of press mud generates between 85 to 120 m³ of bio-gas i.e. 25-30 kgs of filter cake yields about 1 kg of bio-CNG and thus looking to the prices of filter cake and bio-CNG being about 250 per MT and about 48 per kg respectively, utilization of filter cake in such a manner appears lucrative for value addition and for providing green energy.
Potential of Compressed Bio-Gas (CBG) from Indian Sugar Inductry
% Contribution
% Contribution
The graphical presentation at Fig.6 provides an idea of total compressed bio-gas potential in the country estimated to be about 62 million metric tonnes per annum out of which spent wash/ filter cake (press mud) can contribute to the extent of about 2 million metric tonnes.
45
45
25 MMT
40%
25 MMT
40%
40
40
35
20 MMT
32%
35
20 MMT
32%
30
25
20
10 MMT
16%
30
25
20
10 MMT
16%
15
10
5 MMT
8%
15
10
5 MMT
8%
5
2 MMT
3%
5
2 MMT
3%
0
0
Surplus Agri-residue Recoverable Cattle Dung Spent Wash/ Press Mud Municipal Solid Waste Sewage Treatment Plant Chicken Litter
Surplus Agri-residue Recoverable Cattle Dung Spent Wash/ Press Mud Municipal Solid Waste Sewage Treatment Plant Chicken Litter
Fig. 6 Compressed Bio-Gas Potential
Bio-Energy from Spent Wash (Vinasse)
It may not be out of place to mention that vinasse/ spent wash, the effluent of ethanol production may turn out to be a key source of bio-energy either by transforming it into biogas (methane), which can be used as boiler fuel or after concentrating it in multiple effect evaporators (MEE) and then to incinerate along with bagasse/coal/other bio-mass in an incineration boiler integrated with turbine to produce the bio-electricity [12].
Potential of Bio-Energy from Spent Wash
Keeping in view the average alcohol production of 3000 million liters during an alcohol year, the potential of the alcohol industry nationwide is estimated around 500 MW power as reflected in Table 7, that can be utilized for own process uses and surplus energy may be exported to the national grid, using the latest commercially proven incineration technologies.
Discussion
The optimal utilization of resources with exploring new horizons besides facilitating bio-energy in the form of biomass power, bio-ethanol and bio-gas/ bio-CNG shall also help in maintaining the health of the sugar industry even under adverse sugar-sugarcane price scenario, thus, making possible in time payments for the sugarcane prices to the 50 million sugarcane farmers and others directly or indirectly associated with the Indian sugar industry, which has frequently remained a volatile issue for the Indian sugar industry. The judicious utilization of the three vital by- products i.e. bagasse for bio-electricity, molasses for bio- ethanol and press mud for bio-gas/ bio-CNG can bring a turn around the situation as reflected from Table 8 and Table 9 respectively as besides rendering green energy, it renders the most desired value addition by the most convenient route. The potential of bio-ethanol shall be further increased by diversion of sugarcane juice or B-Heavy molasses considering the relative economics of ethanol.
Table 8 Revenue through Sale of Primary By-product (Standalone Sugar Units- Conventional Route)
By-product |
Quantity (ton) |
Rate ( per ton) |
Revenue () |
Bagasse saved @ 7.0% on cane* |
0.070 |
1700 |
119 |
Molasses @ 4.5% on cane |
0.045 |
4000 |
180 |
Press Mud @ 3.5% on cane |
0.035 |
250 |
8.75 |
Total Revenue = 307.75 per ton of sugarcane
*Average bagasse % cane- 30 and considering installation of low to medium pressure boilers of 32 kg/cm² g to 45 kg/cm² g working pressure having bagasse: steam generation ratio as 2.2 to 2.3 only.3
Table 9 Revenue through Value Addition (Integrated Sugar Complexes considering high pressure Co-Generation)
turbines to meet sugar plant requirements and surplus for sale to national grid.
Pressure (ata) |
Table 7 Po Alcohol Production (Million Liters) |
wer Generatio Spent Wash Available (Million Liters) |
n Potential usin SW to Supplement Fuel Ratio |
g Spent Wash Steam Generation Potential (MT) |
Power Generation Potential (MW) |
45 |
3000 |
3000 |
70:30 |
3500 |
500 |
Pressure (ata) |
Table 7 Po Alcohol Production (Million Liters) |
wer Generatio Spent Wash Available (Million Liters) |
n Potential usin SW to Supplement Fuel Ratio |
g Spent Wash Steam Generation Potential (MT) |
Power Generation Potential (MW) |
45 |
3000 |
30000 |
70:30 |
3500 |
500 |
**Considering an average yield of 235 litres of ethanol per ton of molasses.
***Considering 25-30 kgs of filter cake yields about 1 kg of bio-CNG.
CONCLUSION
Production of bsio-energy is one of the most proficient ways to achieve sustainable development. Increasing its share in the world vide matrix will not only help prolong the existence of fossil fuel reserves, address the threats posed by climate change, but also enable better security of the energy supply on a global scale. Most of the new renewable energy sources are still undergoing large-scale commercial development, but some technologies are already well established. These include bio-electricity and bio-ethanol, in particular, which, is a global energy commodity that is fully competitive with motor gasoline and appropriate for replication in many countries.
In the near future, the bio-energy concept of complete utilization of sugarcane biomass, molasses and press mud will become a pivotal element for a sustainable sugarcane industry. An industry that produces bio-electricity, bio-fuels and bio-gas /bio-CNG fuels from a renewable source should be considered a fascinating vision.
From the perspective of sustainable energy development, renewables are widely available, ensuring greater security of the energy supply and reducing dependence on oil imports from politically unstable regions. Renewable are less polluting, both in terms of local emissions (such as particulates, sulphur and lead) and green house gases (carbon dioxide and methane) that cause global warming.
Hence, there is abundant opportunity for the wider use of bagasse/spent wash for generation of bio-electricity, molasses for production of bio-ethanol and press mud for production of bio-gas/bio-CNG in sugarcane producing countries. Even, this potential remains by and large unexploited.
REFERENCES
-
L. A. Edye, W. O. S. Doherty, and J. A. Blinco et al., The Sugarcane Bio-Refienry: Energy Crops And Processes For The Production Of Liquid Fuels And Renewable Commodity Chemicals, in Proc. Aust. Soc. Sugar Cane Technol., 2005, vol. 27, pp. 922.
[2] S. Jenjariyakosoln, B. Sajjakulnukit, and S. Garivait, Energy and
By-product
Quantit y (ton)
Value Added Product
Rate ()
Reve nue ()
Addl. Cost of Conver
sion
Net Reve nue
()
Bagasse saved @
9.0% on cane
0.090
Power: 43.3
units*
5 per unit
216.
5
1.5
per unit
i.e.
64.95
151.5
Molasses
@ 4.5% on cane
0.045
Ethanol: 10.6
litres**
45
per liter
477
10 per liter
i.e.
106
371.0
Press Mud
@ 3.5% on cane
0.035
Bio- CNG: 0.001
ton***
4800
0 per ton
48
15 per kg
i.e.
15
33
By-product
Quantit y (ton)
Value Added Product
Rate ()
Reve nue ()
Addl. Cost of Conver
sion
Net Reve nue
()
Bagasse saved @
9.0% on cane
0.090
Power: 43.3
units*
5 per unit
216.
5
1.5
per unit
i.e.
64.95
151.5
Molasses
@ 4.5% on cane
0.045
Ethanol: 10.6
litres**
45
per liter
477
10 per liter
i.e.
106
371.0
Press Mud
@ 3.5% on cane
0.035
Bio- CNG: 0.001
ton***
4800
0 per ton
48
15 per kg
i.e.
15
33
Greenhouse Gas Emissions Reduction Potential of Sugarcane Field Residues Power Generation in Thailand, in International Journal of Environmental Science and Development, 2013, vol. 4, no. 2, pp. 182186.
-
T. C. Cannavam, W. F. Molina, and M. L. Cunali, Energy Potential Of Sugar Cane Biomass In Brazil, in Scientia Agricola, 2000, vol. 57, no. 4, pp. 677681.
-
Anonymous, Using Bagasse for Bioenergy, in Clean Energy Council https://www.cleanenergycouncil.org, 2010.
-
Anonymous, Bio-Ethanol As Major Source Of Energy, in National Development and Reform Commission (NDRC) http://www.hedon.info/docs, 2007, pp. 115.
-
A. K. Kanaujia and D. Swain, Bagasse Drying – A Green & Efficient Solution To Significantly Meet Out Power Deficit In India, in Proceedings of 11th Joint Convention of STAI & DSTA, 2015, pp. 390398.
-
N. Mohan, J. P. Srivastava, and A. K. Kanaujia, Bagasse Gasification – An Energy Efficient Option, in Proceedings of 11th
Total Revenue = 555.55 per ton of sugarcane
*Average bagasse % cane – 30 and considering installation of high-pressure boilers of 87 kg/cm² g to 110 kg/cm² g working pressure having bagasse: steam generation ratio as 2.5 to 2.6 only. Power generation through Condensing/ Condensation-Extraction or in combination with back pressure
Joint Convention of STAI & DSTA, 2015, pp. 399405.
-
L. A. Martinelli and S. Filoso, Expansion Of Sugarcane Ethanol Production In Brazil: Environmental And Social Challenges, in Ecological Applications, 2008, vol. 18, no. 4, pp. 885898.
-
M. O. S. Dias, A. V. Ensinas, and S. A. Nebra et al., Production
Of Bioethanol And Other Bio-based Materials From Sugarcane Bagasse: Integration To Conventional Bioethanol Production Process, in Chemical Engineering Research and Design, 2009, vol. 87, pp. 12061216.
-
Anonymous, Renewable Energy Brazil, in PWC https://brazilianchamber.org, 2013.
-
S. Awasthi, S. Paroha, and N. Mohan, Bio-Energy from Filter
Cake, in Proceedings of National Seminar on Bio-energy from Sugar Industry- A way forward for sustainability at SNSI, 2019, pp. 16.
-
P. Patel and S. Gaikwad, Spent Wash Incineration Technology For Sugar & Distillery Sector To Achieve Zero Liquid Discharge, in Proceedings of 11th Joint Convention of STAI & DSTA, 2015, pp. 788798.
-