
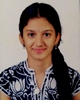
- Open Access
- Authors : N. Netrika , N. Bhanupriya , D. Nagateja , K. Sai Priyanka, D. Govardhan
- Paper ID : IJERTV10IS050455
- Volume & Issue : Volume 10, Issue 05 (May 2021)
- Published (First Online): 07-06-2021
- ISSN (Online) : 2278-0181
- Publisher Name : IJERT
- License:
This work is licensed under a Creative Commons Attribution 4.0 International License
A Review on Design and Analysis of Shape Memory Alloy Actuator for Drone Parachute
N. Netrika1, N. Bhanupriya2, D. Nagateja3, K. Sai Priyanka4, D. Govardhan5
Research student1, Research Student2, Research Student3, Assistance Professor4, Head of the Department5, Department of Aeronautical Engineering, Institute of Aeronautical Engineering, Telangana, India.
Abstract: The objective of this paper is to review the performance of the actuators and rigging lines present in drone parachutes which are fabricated with Shape Memory Alloy (SMA) materials with some standard improvements compared to traditional way of operative. This is to analytically observe the change in the degree of control that can be enhanced by replacing rigging lines of a parachute with shape-memory alloy material. A parachute drone with rigging lines and spring in actuators which are made up of NiTiNol shape memory alloy will be steered by changing temperature by operating with thermostats. Electrical current will be passed through NiTiNol in order to change their lengths for controlling the parachute which is similar to AGAS. The purpose of analysis of parachute is to safely land the payload without damage by continuously steering it effectively. These cargo parachutes are used for varies purposes in the field of agriculture, military cargo parachute are used widely by steerable parachute which also meet the requirements like to track the flight path using mission planner, to ensure the controlling of drone parachute in terrain precision areas.
Keyword: SMA, Actuator, Parachute drone, Steerable parachute.
-
INTRODUCTION
Parachute and drone combination is extending significantly in the aircraft industries with a wide range of applications of payload drop in Military, Agriculture, surveillance and commercial needs. However, notably in the recent past, an increase in use of unmanned aerial vehicles (UAS) has increased the demand for ease of operation of UAVs. To perform effectively there must be advanced components, materials to make it sustainable for a longer period as well as to protect the payload from damage. These unmanned cargo parachutes should have controlled parachute systems that improve the accuracy of unmanned airdrop that is precise landing as parachutes can be disintegrated by severe meteorological conditions, which in turn results in damage of payloads.
The stability and controllability in steering the parachute are observed and made changes to solve the problems that are faced in a traditional way. The idea behind this paper is to replace the rigging lines and actuators with Shape Memory Alloy (SMA) material. The SMA material has a peculiar property, which undergoes mechanical shape change when heated above a certain conversion temperature moreover, it is a lighter and cheaper material to meet the industrial needs. As there are various materials come under SMA material like copper-zinc-aluminium, nickel-titanium, copper-
aluminium-nickel, and many more; however, Nickel- Titanium (NiTiNol) is used to replace rigging lines as it has remarkable electrical and mechanical properties with long fatigue and high corrosion resistance. NiTiNol can contort 10-30 times as much as ordinary metals and return to its initial shape and this multi-functional smart alloy can have shape returning force of 30000 PSI (Pounds per square inch) so this property is helpful in building strings in actuators that have potential for steering the parachute.
To steer the parachute with maximum control, the rigging lines need to be moved through actuators made up of SMA material and that requires heating of the material. The process of heating them is by passing a flow of electric current which is generated by battery which allow SMA alloy to change its shape along with change in length there by changing the direction of parachute
-
SMA OVERVIEW
SMA materials as termed it remembers the previously defined shape after applying a force by changing external parameter like temperature. The crystal structure inside SMA material will change from Martensite to Austenite on heating and again Austenite to Martensite on cooling this phenomena is known as Shape Memory Effect (SME) and also it has an another feature called Super elasticity (SE). They can be shaped into bars, wires, springs, plates and rings which are useful in various fields from aerospace engineering to medical devices. An SMA material is used because of the following reasons:
-
They have high force to weight ratio and noiseless operation.
-
SMA can be activated at 70°C.
-
SMA materials are able to expand large forces and to recovery large deformation and then they have an enormous capacity in low frequency applications.
-
SMA alloy has tremendous electrical and mechanical properties with the long fatigue and a great corrosion resistance.
-
They are cheap and easily available material which meets the industrial requirements.
-
-
Types of SMA alloys
There are more than 15 alloys that exhibits the property of shape-memory effect. Some of them are Fe-Mn-Si, Co-Ni-
Al, Ni-Ti-Cu, Co-Ni-Ga, Fe-Mn-Si, Ni-Mn-In-Co, Ni-Ti- Pd, Ni-Mn-Ga, Ni-Fe-Ca.
The typical SMA compositions commonly used are Ni-Ti, Ni-Ti-Cu, Ni-Mn-Ga, Ni-Mn-In-Co, Ni-Cu-Al, among all these varieties of SMA alloys the Ni-Ti alloy is more efficient and more easily available in the market. It is also known as NITINOL (Nickel Titanium Naval Ordnance Laboratory) which they have termed by the combination of the composition and the place it has been discovered i.e. US Naval Ordnance Laboratory in White Oak, Maryland in 1963. The properties of Ni-Ti alloy are having high corrosion resistive, higher memory strain and a very good electrical and mechanical properties and have long life. This NiTi alloy is having a unique property like it can act as an actuator, sensor and heater all in a one material for different purpose.
-
Operation
SMA Actuator can operate in two ways based on shape memory effect (SME) either one-way or two-way process. One-way processing will be in the form of single SMA piece with low yield stress at martensitic stage and return to high yield stress at austenite stage while heating and can allows the force or displacement only in one direction. To obtain two-way processing there are two methods (figure 1) and these have been categorized as:
-
Bias type SMA Actuator
This type of actuator is compiled of a SMA element and a bias spring which can be any other materials like steel, but it has a slow response because of the speed which is determined by cooling process.
-
Differential type Actuator This type of actuator is comprised of antagonistic which is SMA elements and which has faster response speed then the bias actuator but the disadvantage in this type of actuator is it consume more power and the angle is constrained by the state SMA elements.
SMA Linear Joint with Differential SMA Bias Spring Linear Joint
Source: Sylvain Toru
Figure 1. Types of SMA actuators operations
-
-
applications
-
There are several applications of SMA material
-
Biomedical applications
In particular, NiTi SMAs have been found in many biological applications due to their excellent compatibility. Studies have shown that Nickel alone is toxic and any contact with Nickel can lead to a variety of medical problems but, in the event of Niti alloys merging, the bond
between Ni and Ti is stronger (as in ceramic material) as compared to nickel bonding with steel and other things.
-
Civil engineering applications
In social engineering applications large voice cords of SME springs and beams are used as offenders in bridge structures and in similar axis systems due to their good energy dissipation and this energy intrusion. The use of SMA components as reinforcement in reinforced concrete (RC) has been more effective in blocking lateral column displacement even at high levels of strong loading similar to model earthquakes compared to their counterparts such as RC steel columns.
-
Aerospace and automotive applications
SMA components are used as thermal actuators in various temperature regimes depending on the type of applications in the automotive industry The use of SMA actuators finds many applications before selling concepts such as smart automatic light systems fuel control climate mirrors adjustment locking system suspension such as semi-ropes, beams, torque tubes used to rescue the entry and direction, amplifying/lowering the nozzle, wing vibrations in various aerospace applications.
-
SMA AS ACTUATOR
Considering the actuator, a shape memory alloy actuator is the most provident actuator type as it has self-monitoring, high alloy material features, excellent in anti-corrosion properties and available totally consistently in high-quality shape memory alloy or available in different forms as spring, wire or rods in actuator therefore SMA Actuators offers the best cost and technical advantages in every field. By using SMA actuators there is no need of any extra components for the movement of spring in the actuator. With evidence shown in the table 1 and figure 2, choosing SMA material will be best in overall performance and for displacement and output forces in actuators. The SMA material is one of the form from the smart materials which encompassed of different materials which are used in many domains which are grouped as
-
Shape memory alloy
-
Piezoelectric
-
Thermoelectric material
-
Thermochromic
-
Photochromic, etc.
As listed above there are different types of smart materials which can be used as a actuators but this paper chooses shape memory alloy because of the properties that it exhibits, can be used as a actuator without failing. Compared to conventional actuators such as electrical, hydraulic and pneumatic actuators, SMA actuators have the advantages, biocompatibility, negligible size, and unadorned mechanical design and quiet operations. SMA actuators perform in unidirectional actuation so it requires an upturn force like weight, spring or any other antagonistic SMA wire to release by bidirectional moment. The actuator in parachutes are used for steering the parachute in different directions which should not fail during the mid-air operations. The use of
SMA actuator in parachute will increase the length and displacement which in turn moves the parachute in desired direction without losing the control. The following figure 2 indicates the displacement versus force for different actuators.
Actuat or Type
Ni Ti S M A
Piezo- cera maic
Single crystal piezoele ctric
Hum an Mus cle
Hydra ulic
Pneum atic
Stress (MPa)
20
0
35
300
0.00
7
0.8
20
0.7
Strain (%)
10
0.2
1.7
1 –
100
50
50
Efficie ncy (%)
3
50
90
35
80
90
Bandw idth (Hz)
3
5000
5800
2 –
173
4
20
Work per Volum e (J/cm3)
10
0.035
2.55
0.03
5
5
0.175
Power per
30
175
15000
0.35
20
3.5
Source: Jaronie mohd jani et al. (2014)
Table 1: Comparison of properties of different actuator
Source: Kinitics Automation
Figure 2. Comparison between SMA actuator and other actuator technologies.
-
-
REVIEW ON PERFORMANCE AND DESIGN OF SMA ACTUATOR FOR LANDING GEARS OF UAV.
-
The purpose of this paper is to compare the main performance of the SMA Actuator system reference with traditional servo-actuator and developed the design of actuator for extension and retraction of landing gears with SMA material. The selection of NiTiNol material have
shown to activate and deactivate at room temperature (20°C) for the applied preload also the SMA Technology was introduced for two sub-systems of UAV, the Deployment and Locking Subsystem. The blocking subsystem is introduced to rise the stability to the retracted and the deployed configuration apart from oscillations along with the static and dynamic behaviour of the SMA based subsystems was defined. The values of Weight, Volume, Activation time and Power are compared for the performance of conventional servo-Actuator, SMA subsystems. The working principle of landing gear system was perceived for overall progress of UAVs arms during take-off and landing and also to ensure full retardation throughout missions like all other flight missions like cruise, loitering etc. by using SMA actuation system. This data will be used for saving the cargo from damage by rotating the arm 90° around the pivots which is produced by SMA actuation system there is an issue regarding lateral stability which is also sorted by SMA actuator. The landing gear comprise of two subsystems and both are grounded on SMA technology they are 1) the deployment-retraction 2) the blocking system.
-
The deployment-retraction
The SMA springs are linked by shaft, the springs are parallel which is connected to fuselage body and a mass is placed at centre of gravity for balancing the weight of the arm-wheel system. The antagonistic spring increases the internal stress to achieve the same balance by activating the SMA spring(blue sketch, figure 3) landing gears is deployed as shown in the figure 3.
They will be pre-stressed around the arm pivot and reach stability once the landing gear is retarded because of SMA spring has super elastic (SE) behaviour. The SMA spring used here is NiTiNol alloy with some specific characters enumerated in table 2
Spring Diameter (mm)
4.5
Wire Diameter (mm)
0.55
Wingdings
38
Length Without Loads (mm)
27.8
Material (See load and unload cycles in)
NiTiNol
Austenite Youngs Modulus (GPa)
103.3
Martensite Youngs Modulus (GPa)
57.7
Density (kg/m3)
6450
Source: Salvatore Ameduri et al. (2016)
Table 2. Characteristic of shape memory alloy spring.
-
Locking system of landing gears
This system proposes to increase the ability to deployed configuration without oscillations. Here also there are two SMA Springs(green sketch, figure 3), one is fixed and connected to hub and another is actuated by two SMA antagonistic spring with they are pre-stressed so that brake components are pushed against the rotation components to clutch it. Landing a rotation around pivot is avoided through the connection fiction force, between two aluminium elements, namely a circular straight connect to the gear arm and of friction element, having some length and connected to two pasive springs (Figure 4a). In the blocked condition, the springs undergoes a displacement, force by your initial slide layout. The stimulation of the right spring produces a further displacement, generating a gap between the two elements and then permitting the arm rotation (Figure 4b).
Source: Salvatore Ameduri et al. (2016)
Figure 3. (a) Before deployed of landing gear (b) after deployed of landing gear.
The working springs process two actions, one the response due to the antagonistic spring and the regular action due to the contract at 20C temperature. Since these forces have opposite sense, if the extending of the working spring is low, it risk working in compression; however, the extending cannot overcome a certain level, for a material shear stress limitation. The curve drawn between force and spring displacement in various conditions like spring reaction at room temperature (20°C), Spring when fully activated, Force level in lock the condition and unlock the condition, and the path followed during locking and unlocking in conditions are shown in graph (figure 5).
Source: Salvatore Ameduri et al. (2016)
Figure 4. (a) Unlocking condition (b) Locking condition
Source: Salvatore Ameduri et al. (2016)
Figure 5. Force displacement curve present in locking subsystem.
-
INTEGRATION WITH UNMANNED AERIAL SYSTEM
As we say, SMA spring actuator is widely used in unmanned aerial vehicles (UAV) for the stability and direct arrival purpose. The requirements and design of the SMA spring used in actuator is shown below figure 6 which is designed in CATIA
Source: Salvatore Ameduri et al. (2016)
Figure 6. (a) Computer aided design details of deployment and locking system, (b) attitude in retracted and (c) deployed configuration.
-
REVIEW ON PERFORMANCE OF SMA RIGGING LINES OF PARACHUTE
They have discussed the new application that is Guided parachute systems from existing technology that has been developed through major research work. Adequately an experiment is set up to test actuator made-up of NiTiNol, an SMA material which can steer a parachute more effectively as an actuator for unmanned parachute by heating them with electricity. The properties of SMA are observed by changing the length of the riser of parachute. Finally data is taken for each drop test using Excel and the numerical analysis will be performed by MATLAB. If the data have met the required results for controllability, a new generation actuator will be
developed. Many researchers have put their efforts in developing the control of the parachute system to have efficient accuracy of unmanned airdrops. Since years researchers was concentrating in guidance and navigation system while avoiding the actual function of actuator which can be used and controlled for an airdrop systems.
4.1 Objective
The researchers of this paper got a plan of experimenting a new type of actuator with a new method for autonomous guided parachute system that uses light and cheaper actuators made from shape memory alloy SMA. The experiment outlined in this paper will execute how well an SMA actuator made up of NiTiNol material which can steer a parachute by changing the length of the shape memory alloy woven into its risers of a parachute. One system of raising the temperature of SMA is by operating a higher amount of electric current through the material or a battery can be used to provide the current required to effect a change in shape of an SMA and by using these methods a simple actuation system can build by powering a SMA alloy wires with electric current which in straight changes the length of the ringing lines call rises of the parachute. They used NiTiNol wires which has been woven into the suspension or ringing lines (figure 7) of scale-down prototype of parachute with electrical circuit for control and sensing. Before conducting experiments they have tested the following parameters:
-
Testing the NiTiNol actuators on stationary parachute for the control on the length of the ringing lines.
-
There should be no damage for the payload or container by means of ground impact.
-
They have repeated the test to determine the effect of actuator and electronic system for cycling loading.
The real testing of an actuator rely on combination of outside temperature that is ambient temperature and payload weight to return to their initial state, so the test must has conducted in a wind tunnel which avoided outside parameters like:
-
The gravitational force pulling on the payload which has opposite direction of SMA wires.
-
The gravitational force that pull parachute in horizontal direction that is sideway displacement.
4.2 Experiment details
This experimental set up was performed at parachute drop facility US Army Natick soldier systems Centre in Natick, MA. They have set up in this particular area because of the wind condition that should not affect the parachute actuator efficiency.
They have mention three different ways for changing the signals which will be sent to actuators. The first method involves varying the voltage level of the signal, the second varies the width of the pulse of the signal, and the third varies the total time for which signal is sent to the actuators and all these independent variables alter the amount of current supplied to the actuator as the amount of heat.
The design included in this experiment are the parachute consist of 18 ringing lines which are made up of para-cord. The Dimensions that is length of each ring line is 100 in (2.54 m). The canopy of parachute is already connected with rigging lines further, the NiTiNol wires are woven into these rigging lines by hand and martensitic and austenite final temperatures are taken as 25°C and 35°C respectively. The data collected from the thermal model developed at Mide technology Corp which determines the type of NiTiNol wire can be used based on requirements like for this 1.2 mm diameter NiTiNol wire is required in actuators. They strained the material in the low-temperature Martensitic phrase by the weight of the payload before combining the NiTiNol wires with rigging lines of parachute, upon heating the material above transition temperature it will undergoes a phase change that is austenite stage this shape memory effect will decrease the length of the NiTiNol wire by 3%. This decrease in length of SMA wire will steer the parachute in the desired direction. The time difference between heating and cooling is observed to be about half a second in an actuator to be actuated. The MATLAB program of implementation of thermal model is found in reference paper [2].
The Focus of this paper is to Control and steer the unmanned parachute without the damage of the payload, with the use of SMA actuator so, there are some dependent and independent variables that are key in the controlling of parachute. Firstly, dependent variables which directly impact on the parachute such as horizontal velocity and change in path for vertical drop of 10 m/s and these para- metres are used to determine how effectively an actuator work for a specific parachute. Secondly, the independent variables are the different variables for applying the amount of current to SMAs to change its shape in the actuator. They are: voltage, the potential difference enforced to actuators; pulse width, the length of the pulse of current applied to actuators; length of the perturbations. By altering all the dependent and independent variables the experiment is conducted successfully by safety precautions and eliminating the systematic errors and random errors which are caused in by manual errors, gross errors or human error. This in turn would have an impact on the overall performance of the parachute.
Source: Brian Wong (2002)
Figure 7. Experimental Setup of Parachute with Payload.
-
-
-
REVIEW ON COMPARISON OF SMA ACTUATOR
They have introduced a differential SMA actuator integrating two antgonistic SMA wires and a torsion spring. The purpose of these two things in actuator is to allow the more effective angular motion compared to a conventional SMA actuator. They have inspired by the biological structure of the human elbow joint which is actuated by antagonistic skeletal muscles (biceps and triceps) which are connected to the bone through the tendon so this inspiration has led to a new SMA based differential actuator which is composed of a SMA wire, a torsion spring and two cylindrical couples. By evaluating Heat Dynamics and Heat transformation model, the rate of temperature change due to change in voltage of wire and the heat loss to the environment is discussed. Using MATLAB/ SIMULINK, stiffness and output angle parameters are compared and also to observe the functioning in terms of pursuing accuracy and settling time. The greatest speed of response of the new actuator largely varies on the input current/voltage through the SMA wires and SMA wires rigidity, inflexibility and they also stated that there should be a limit of increase in current for the protection of wires.
-
Comparison of SMA actuators
Here they have compare three different types of actuator using the same mechanical approach. The basic experiment test bench was used The model consist of two couplers, one is fixed on the axis and the second one is free to rotate about the axis and encoder is also coupled to the axis by a coupling which is used to measure the rotational angle of the axis.
-
Working process
-
The coupler 1 starts to rotate as the upper SMA wire activates by heating due to its reduction force
of SMA wire thereby, the force is transferred from coupler 1 to couple 2 when torsion spring start to twist.
-
The lower SMA wire will be extended and it will control the rotation when this lower SMA wire is heated, the force is transferred in opposite direction.
By following this principle, we can heat the antagonist wire and cool the opposite one intensify the speed of the actuator.
Source: Z.Guo et al. (2015)
Figure 8. (a) CAD model and (b) experimental bench
The three actuators is compared with each other using the same source of external parameters like voltage, current, mechanism as shown in the figure 9. (a) Bias SMA actuator which consist of a coupler 1 are linked to SMA wire and coupler 2 is fixed by iron wire and torsion spring is used for recovery force. (b) Differential SMA actuator consist of two SMA wires which are linked to only one coupler that is coupler 1. (c) Compliant differential SMA actuator consist of two SMA wires and they are connected to two coupler respectively and the torsion spring will be concealed inside. All the wires generate tensile force with some stiffness ki and damping factor bi. This experiment was conducted to showcase the performance of two aspects one is stiffness and other is output angle. By using a software call Matlab or Simulink a model is developed for all the three distinct SMA actuators with similar load and similar input voltage in open loop. The results were shown in the graph (figure 10).
Source: Z.Guo et al. (2015)
Figure 9. (a) Bias SMA actuaor, (b) Differential SMA actuator and (c) Compliant differential SMA actuator CAD models respectively.
The maximum response speed of actuator mainly depends on input current, the strength of voltage across the SMA Cable, and SMA wire strength. Larger current can rise their response field, while currency should be restricted to safeguard the SMA wire. Investigation on this experiment was done and found that differential SME actuator will have
the faster response then other actuators within its working range and also by limiting increasing stiffness. There are limitations like strain of SMA wire i.e. long wire was used in large rotational angles in traditional SMA actuators but this method has increase the angle of rotational for same actuator which can be used to reduce the length of SMA wire.
Source: Z.Guo et al. (2015)
Figure 10. Stiffness of upper SMA wire during heating process BS: bias SMA actuator, DI: differential SMA actuator, CD: compliant differential SMA actuator.
-
REVIEW ON ANALYSIS OF SMA SPRING
They conducted an experiment with SMA spring in actuator to analyse the output force. The output force increases as temperature increases and the graph drawn between the force and temperature is almost linear. Experiment is conducted with NiTiNol which composed of TI 49.8% Ni with some specific start and end temperature. The main aim to conduct this experiment is to show how a SMA material can display length with the rise in temperature subsequently, contrasting an element which can be either way weight, any force that is constant or a conventional spring i.e. steel spring (Figure 11). After the data is collected they stated that increase in temperature on SMA actuator, the output displacement has increased proportionally.
Source: Jianzuo Ma et al. (2013)
Figure 11. The operation of SMA (helical spring) actuator.
The outcome of this paper are mainly focusing on two parts, one the yield displacement of SMA spring with changed temperature; two the yield force of SMA spring with changed temperatures. For both the aspect to be tested two experiment set-ups are stated and performed by changing the measurements of respective sensors.
-
The output force of SMA spring under different temperatures:
The scehmatic diagram for this experiment is shown in figure 12. During this testing they have mentioned few specifications of the material; martensitic and austentic phase temperatures at starting and ending of the experiment, Ms = 78°C , Mf = 50°C, As = 74°C and Af = 95°C
respectively; share moduli are GM = 7.5 GPa and GA = 25 GPa; the diameter of SMA spring is 1 mm ; angle of inclination = 6° and the number of turns are seven. The result is shown in the figure 12 below which express the relation between output force and the temperature of SMA Spring; the experimental and calculated values are plotted. By looking into the graph we can say that as the temperature increases the output force of the SMA spring gradually increases.
Source:Jiansuo Ma et al. (2013)
Figure 12. Schematic diagram of testing SMA spring experiment.
Source: Jianzuo Ma et al. (2013)
Figure 13. Graph between output force and temperature.
-
The output displacement of sma spring under different temperature:
The schematic diagram of this experiment is shown in figure 14.
Source: Jianzuo Ma et al. (2013)
Figure 14. schematic diagram of the experiment for output displacement.
Source: Jianzuo Ma et al. (2013)
Figure 15. Graph between displacement and temperature.
this experiment was led when the maximum shear stress is 2% according to the graph shown in the figure 15. The experimental and theoretical are almost matched and also we can accomplish that as the temperature increases the displacement of the SMA spring will increase.
-
The output displacement of sma actuator under varying temperature.
Two springs are used, one is SMA spring to actuate and the second spring that is biasing spring which will move and
corespondingly used to test the displacentment of SMA spring as shown in figure 16 and results in figure 17.
Source: Jianzuo Ma et al. (2013)
Figure 16. Schematic diagram of a SMA actuator experiment.
Source: Jianzuo Ma et al.(2013)
Figure 17. The graph between displacement and temperature of SMA actuator.
-
-
CONCLUSION
In this paper, the discussion on what actually is SMA alloys do and its properties and applications. Further, a review was made on how an SMA actuator is effective than other actuators by using different methods. Comparatively from all the actuators only SMA based actuator and rigging lines made up of SMA can be used in drone parachute for steering purpose and also for avoiding the cargo damage. Ths review article also reveals that documents publish by the SMA research community for past decade has focused in medical applications although SMA actuator are gaining in scope applications for actuators and this paper reviews noted that their participation in non-medical setting is also high. Problems caused by SMA actuators used in various drone parachutes fought for the right choice modelling techniques control strategies and feedback sensors. SMA actuator also suffer in terms of resistance to fatigue however, magnetic SMA also have good fatigue resistance produce higher
throughput capacity. Document review too confirmed resistance to SMA regulatory response the elements are suitable for drone parachute as it eliminates the need of supplementary sensors although accuracy is narrow because increase degree of freedom for drone parachute, the number of actuators also needs to be improved, creating complex control problems. An additional cooling system is needed to maximize frequency of actuation, which can set limit as such makes the device even bigger.
-
REFERENCES
-
-
-
-
Salvatore Ameduri et al., A Shape memory alloy application for compact Unmanned Aerial Vehicle, May 2016.
-
Brian Wong, Assessment of shape memory alloy actuator for steered parachute, December 2002.
-
Z.Guo, H. Yu, Liang B. Wee, Design and control of novel compliant differential shape memory alloy actuator, January 2015.
-
Jianzuo Ma et al., Characteristics Analysis and Testing of SMA Spring Actuator, September 2013.
-
Jaronie Mohd Jani et al., A review of SMA research, applications & opportunities, 17 December 2013.
-
Ashwin Rao et al., Design of Shape Memory Alloy (SMA) Actuator, 2015.
-
R. Andrew Rusell, Improving the Response of SMA actuator.
-
Y. H. Teh, R. Featherstone, An Architectue for fast and accurate control of SMA Actuator.
-
C. Liang, C. Rogers, Design of shape memory alloy actuators, J. Intell. Mater. Syst. Struct., 8(4) (1997) 303-313.
-
A. Nespoli et al., The high potential of shape memory alloy in developing miniature mechanical devices: A review on shape memory alloy mini-actuators, sensors and actuators.
-
K. Wada and Y. Lin, Shape recovery of NiTi shape memory alloy under various pre-strain and constrain conditions, 2015.
-
J. K. Paik, R. J. Wood, A bidirectional shape memory alloy folding actuator, 2012.
-
Jagadeesan Jayender et al., modelling and control of shape memory alloy actuators.
-
Awad Khidir Elawaleed et al., A new concept of linear smart actuator, 2007.