
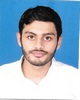
- Open Access
- Authors : Ahmed Shah , Dev Shah, Mohammed Ahsan Shaikh , Pawankumar Shelar, Bhushan Shrirame , Sachin Komble
- Paper ID : IJERTV10IS010088
- Volume & Issue : Volume 10, Issue 01 (January 2021)
- Published (First Online): 20-01-2021
- ISSN (Online) : 2278-0181
- Publisher Name : IJERT
- License:
This work is licensed under a Creative Commons Attribution 4.0 International License
Automated Cleaning Tracking and Cooling System (ACTCS) for Solar Panel
Ahmed Shah
Department of Mechanical Engineering, Student, Vishwakarma Institute of Technology Pune, India
Pawankumar Shelar, Bhushan Shrirame Department of Mechanical Engineering Students, Vishwakarma Institute of Technology Pune, India
Dev Shah, Mohammed Ahsan Shaikh Department of Mechanical Engineering Student, Vishwakarma Institute of Technology Pune, India
Sachin Komble
Department of Mechanical Engineering Assistant Professor, Vishwakarma Institute of Technology
Pune, India
Abstract Due to the increase in demand for power in India and the move towards sustainability, it has become very important to move to renewable sources of energy. Solar energy is one of the most common and easy to adopt a renewable source of energy on a large scale. As it can be installed anywhere not only limiting to the solar farms but also at the roofs of private establishments as well as public establishments. The operating efficiency of a solar panel is 15-22% and due to various factors, such as shadows, snow, high temperatures, dust, dirt, bird droppings, pollen and sea salt, the efficiency is hampered to a larger extent. The problem of dust and dirt is overcome by installation of a cleaning system. In traditional solar panel instalment, the 100% efficiency would only be possible for hardly 2 to 3 hours due to the angle of incident. The addition of the cooling system ensures that the temperature of the solar panel never exceeds above 50oC which is the optimum operating temperature. By incorporation of all the three systems, the operating efficiency of the solar panel can be increased by almost 45 to 85%.
Keywords Efficiency, renewable, solar panel, incident ray.
-
INTRODUCTION
Power generation from renewable sources has grown drastically in recent years, thanks to increasing energy demand and environmental & economic concerns with fossil fuels. Renewable energy sources are getting more and more popular, due to the pollution and non-sustainability of traditional sources of energy. With the increasing human population, an issue arises, what is getting to be subsequent reliable energy source after the disappearance of fossil fuels? The best solution to fossil fuel would by any renewable source of energy. One of the most abundant resources is solar energy. The rise in solar energy has been drastic as compared to other forms of renewable sources of energy this is because the initial investment for a solar panel is lower than that of a windmill.
The electrical energy can be produced by using photovoltaic (PV) cells which solar panel is made from. The solar panel converts the incident solar rays to electricity. The efficiency of a solar panel is low and due to various factors, the operating efficiency of the solar panel is reduced to a much larger extent. The major factors that reduce the efficiency of the solar panel are shadows, snow, high temperatures, dust, dirt, bird droppings, pollen, and sea salt. To meet the requirement, it necessary that the solar panel works on 100% of the operating efficiency.
-
CLEANING SYSTEM
-
Need for Cleaning System
The efficiency of the solar panel depends upon the amount of solar irradiation on the PV cell. Over time dust settles on the surface of the solar panel resulting in improper irradiation of the solar rays. The dropping of birds also causes improper irradiation of solar rays. The dust can be easily cleaned with the help of a brush. But the bird dropping tends to stick on to the surface of the solar panel. By using the cleaning system, the operating efficiency of the solar panel can be increased by 10 to 15%.[1]
Currently, the existing methods which are widely used is manual labour. The problem associated with the cleaning of solar panels on a large scale such as in the case of solar farms, the required manpower is very high for the cleaning purposes. But the main limitation is that it is not feasible to clean large solar farms using humans as the efficiency of the cleaning process is limited. There is some automated system available which are costly for the application on a personal level. There has been an increase in the use of solar panels on personal property. The number of solar panels is less as compared to a solar farm. Hence a feasible solution which not only limits to personal but also solves the commercial application needs to be developed.
-
Literature Review of Cleaning System
Various technologies were developed by various individuals and cooperation over a period of time to assist in the cleaning of the solar panel. A review has been done through which would help in the designing of a better system.
-
Heliotex Technology
Heliotex is an automatic cleaning system that the surface of the solar panel. The cleaning system can be programmed according to the necessity, depending on the environmental conditions. It does not require any further attention except that of replacement of the water filter that may be clocked due to sand and the occasional refilling of the soap concentrate. The system uses the water from the reservoir via a piping system connected to the pump and attached to nozzles on the solar panel surface without causing rubbing. This system can be installed for any size or number of solar panels.
Fig. 1. Heliotex Technology
The disadvantage of this system is the amount of water consumed for cleaning is very high which is not a sustainable model of cleaning is by using solar panels the main objective is to move towards an eco-friendly source of energy.
-
Electroststics Cleaning
Electrostatics cleaning technology is named Harvesting electricity. This cleaning technology was first developed by scientists to unravel the matter of dust deposits on the surfaces of the solar panel. This technology also can be used in areas where the humidity is low, and the chances of rain are limited. Electrostatic charge material is employed on a transparent plastic sheet or glass that covers the solar panels. Sensors monitor dust level sand activates the system into cleaning mode. The dust is shaken off the solar panels when an electrically charged wave breaks over the surface material. In two minutes, this system can remove up to 90% of the dust from the surfaces of the PV panels by sending electrical dust deterring waves that cause the dust to fall off onto the ground. This system cannot remove dust when it is wet, or the dust is in a moist condition. The movement of the wave mechanism requires only a small amount of electricity which makes it a power-efficient system however at present; the worldwide usage of the harvesting system is only 4% this is
as the system is costly and difficult to maintain.
-
Ecoppia E4 Cleaning System
Fig. 2. Ecoppia E4 Cleaning System
This system consists of a three-frame assembly. The first frame consists of the cleaning brush along with the nozzle system which is used to provide water for the cleaning operations which is optional. The second frame is the support frame for the first one, the first frame travels inside the
second frame along with the vertical orientation. The second frame travels on the third frame and is used for the horizontal movement of the cleaning system.
The disadvantage of this system is that it consists of many moving parts that require lots of regular maintenance as there is lots of friction between the frames. The system uses less water as compared to Heliotex technology. The maintenance cost is high as there are a lot of moving parts.
-
-
Selection of Cooling System
The development of the cleaning system was done by taking a hybrid approach by combining Heliotex Technology & the Ecoppia E4 Technology. The cleaning system was optimized by reducing the number of moving parts. This was done by reducing the number of frames to a single cleaning unit along with a guide provided on the solar panel mounting frame.
-
-
TRACKING SYSTEM
-
Need for Tracking System
The efficiency of the solar panel depends upon the amount of solar irradiation on the PV cell. In most cases, the solar panel is fixed at a particular angle that would receive the most irradiation throughout the day. Due to this, the solar panel operates at 100% of operating efficiency of 2 to 4 hours depending on the season and location.
The amount of output mainly depends on the cosine angle of incidence i.e., the angle between the sunray and horizontal surface. The minimum incidence angle gives the maximum power output. In the case of the fixed panel except for noontime the angle is maximum for the movement of the sun. An efficient solar tracker can be used to correct this problem. By taking readings for 6 days from morning 8 AM to 6 PM at an hour interval it was found that the efficiency of the single- axis tracking system over that of the static panel is calculated to be 32.17% and the dual-axis tracking system over that of the static panel is calculated to be 81.68%.[2].
-
Literature Review of Tracking System
Type of System
Efficiency
Capabilities
Restrictions
Single-Axis Solar tracking system
Horizontal Single Axis Tracker (HSAT)
68%
Less complicated, expensive.
More Rigid and stable.
Less likely to be damaged during storms
Requires More Space as there is arranged horizontally
Vertical Single Axis Tracker (VSAT)
62%
Less complicated, expensive.
Easily affected by wind force. so, support should be taken care
Tilted Single
Axis Tracker (TSAT)
69%
More suitable for smaller Latitudes (Places near to equator)
The inclination should be calculated Accurately to Avoid losses due to shading and wind.
Polar Aligned Single Axis Trackers
Development Phase
More suitable for larger latitudes (Places far from
Still, experiments are going on.
Type of System
Efficiency
Capabilities
Restrictions
Single-Axis Solar tracking system
Horizontal Single Axis Tracker (HSAT)
68%
Less complicated, expensive.
More Rigid and stable.
Less likely to be damaged during storms
Requires More Space as there is arranged horizontally
Vertical Single Axis Tracker (VSAT)
62%
Less complicated, expensive.
Easily affected by wind force. so, support should be taken care
Tilted Single
Axis Tracker (TSAT)
69%
More suitable for smaller Latitudes (Places near to equator)
The inclination should be calculated Accurately to Avoid losses due to shading and wind.
Polar Aligned Single Axis Trackers
Development Phase
More suitable for larger latitudes (Places far from
Still, experiments are going on.
TABLE I. TABLE OF LITERATURE REVIEW OF TRACKING SYSTEM [3]
(PASAT)
the equator)
Dual Axis Solar tracking system
Tiptilt dual-
axis Tracker (TTDAT)
78%
Track the sun in both directions (East-West & North-South).
Able to minimize the up-sun shading.
Attached on a long pole so wind forces do not affect the system.
Azimuth altitude dual- axis tracker (AADAT)
82%
Suitable for the greater latitude where substantial Seasonal variation in suns height and arc.
The weight of the array is
distributed over a portion of the ring
Pivoting mechanism rests on the ground hence occupies a large space and these are not suitable for northern climates with snow build up.
Passive tracking system
Passive tracking system
40%
Use of passive materials like SMA (Shape Memory Alloy), parts can be eliminated.
The cost of the materials acting as
actuators are very high and Scarcity in availability.
Also sluggish in moving cold temperature
-
Selection of Tracking System
Fig. 3. TIPTILT DUAL-AXIS TRACKER (TTDAT) SCHEMATIC
Fig. 4.
The tracking system selected was Tiptilt dual-axis Tracker (TTDAT) system was selected as it has a higher efficiency than the other types of the tracking system. And the construction is comparatively simpler. In A tip-tilt dual-axis tracker has the panel array mounted on the top of a pole. Normally the east-west movement is driven by rotating the array round the top of the pole. The vertical azimuth axis is fixed to allow great flexibility of the payload connection to the ground-mounted equipment because there is no twisting of the cabling around the pole. Tip-tilt trackers can make to attenuate up-sun shading and thus maximize the entire power being collected.
irradiance to electricity. The solar irradiation falls on the surface of the solar panel a small part of the solar irradiance is converted to electricity while the remaining part of the solar irradiation is converted into heat, which increases the temperature of the cells and reduces the performance of the PV module. The most commonly used cooling methods can be distinguished as active cooling, which consumes energy (pump, fan, etc.), and passive cooling, which uses natural convection/conduction to enable heat extraction.
The main methods that are used for cooling are active and passive cooling and there are many other methods used for the cooling. Both types of colling can further be divide into two parts which are air cooling and water cooling.
In air passive cooling most commonly, a fin is used which has increased the efficiency by 6.97 to 7.55%. [4]. In the case of water passive cooling, the solar panel is submerged into water and it increases the operating efficiency by 11%. The main disadvantage of this method is the chance of the solar panel to get defective.[5]
In the case of air active cooling and fan is used along with the fin arrangement which enables us to force the air and increases the circulation of air. This method increases operating efficiency by 8 to 15%. In case of water active cooling water is sprinkled on to the surface of the panel and is cooled by this method. This method increases the operating efficiency of the solar panel by 9 to 22%. [6]
A. Selection of Cooling System
The cooling system selected for cooling is an Active Water Type cooling as it has a higher amount of efficiency than the other methods of cooling and would utilize the same infrastructure as required by the cleaning system.
Headings, or heads, are organizational devices that guide the reader through your paper. There are two types: component heads and text heads.
V. AUTOMATED CLEANING TRACKING & COOLING SYSTEM (ACTCS)
-
Motor Selection
-
Motor for Movement of Cleaning System
The motor selection for the movement of the cleaning system was one by calculating the torque required at the top end as well at the bottom end.
The Torque was calculated using the formula. Force required at the lower side,
(1)
The torque required at the lower part,
(2)
Force required at the upper side,
(3)
The torque required at the upper side,
(4)
The mass of the cleaning system was considered to be 17 kg.
IV. COOLING SYSTEM
The electrical energy is produced by using photovoltaic (PV) cells. The solar panel directly converts the incident solar
Fig. 5. Graph of Torque Requirement Comparision
The motor was selected to be placed at the bottom end. As there was a continuous movement of the frame due to the tracking system. The motor was selected with a torque of 45 kg-cm
-
Motor for Tracking System
The required torque for movement of the tracking system was found by conducting a motion analysis on solid works. Through which the required torque was found out which was around 2100 Kg-cm. The motor if selected for this torque would have been too costly. Hence, a combination of a motor coupled to a gearbox was selected.
Fig. 6. Torque Output
Torque of Motor: 160 kg-cm Gear Box: Worm Gear Box 15:1
Torque output of Gear Box: 2400 Kg-cm
-
-
Construction
The system construction can be divided into two parts being the Mechanical or structural and Electrical.
-
Mechanical
The mechanical or structural part can be divided into two parts.
-
Cleaning System
The cleaning system mainly consists of three components.
-
Frame
-
Cover Piece
-
Brush
Fig. 7. Cleaning System
The frame consists of two MS sheet of 5mm thickness on both sides with the motors mounted on one sheet and the other sheet consisting of bearing to allow smooth rotation of the brush. Three wheels are attached on both sides which move on the track for the cleaning operation. The brush is placed in between the two MS Plates. Two MS Tubes that provide support to the assembly are welded to the MS Plates. The cover piece is used to protect the motors from various environmental factors lie dust and water. The material used for the cover piece is Poly (methyl methacrylate) which is also known as Plexiglass.
-
-
Structural Assembly
The Structural Assembly consists of three sub-assembly and the subassemblies consist of various parts and other smaller sub-assemblies.
-
Frame
The frame sub-assembly consists of various components and sub-assemblies like Solar Panel, Solar Panel Mounting, Support Frame, Drain and Sensors
The solar panel is mounted on the Solar panel mounting which is an Aluminum L- Angle. The solar panel mounting is then bolted on the Support Frame. The Support Frame is made of MS Square Tubing. The shaft is mounted on the support frame on which a sprocket is mounted which is used for transmitting power and torque the movement of the solar panel is done about the X-axis using this arrangement. In addition to this, the is a square tubing on the top and bottom ends of the frame which is used as a track for the movement of the cleaning system.
Fig. 8. Frame Assembly
-
Connection Piece
The Connection Piece Sub-Assembly Consists of Journal Bearings, Gear Box and Coupling.
The Coupling is used to transmit the motion about the Y- axis. The coupling is mounted on an MS plate om which the Journal Bearings are also mounted. An MS square tubing is welded on the MS Plate. The Gearbox is bolted on the square Tubing. The shaft of the frame subassembly passes through the journal bearing. The movement about the X-axis is done using this arrangement.
Fig. 9. Connection Piece and Base and Pillar Assembly
-
Base and Pillar
This assembly consists of an MS square tubing in which a motor is mounted which controls the movement of the solar panel about the Y-Axis. The MS Square tubing is welded onto a plate which acts as a base which will be bolted to a concrete foundation and provide stability to the structure. The pillar is and the base is provided with additional supports with the help of ribs on all the 4 sides.
Fig. 10. Complete Assembly
-
-
-
Electrical
The Arduino Mega is the heart of the System it is a versatile microprocessor that is used in the system. The Wi-Fi Module (ESP 8266), sensors, and actuators are connected to the Arduino. There is 4 LDR sensor which is the place at the four ends of the Frame. The 2-rain sensor is mounted on the top side of the frame. Two thermocouples are mounted on the backside of each Solar panel at equal distance. The limit switch is mounted on the ends of the track of the cleaning system. Three solenoid valves are connected to the relay used to ensure the water supply. The ammeter is used to track the output of the solar panel. The Wi-Fi module is used to send & track and also to operate the system wirelessly as the solar farms are usually in a remote location.
Fig. 11. Circuit Diagram of System
The cleaning system comprises of four limit switch which controls the functioning of the cleaning system which are mounted in pairs on both ends of the track. The Limit switches which are at the starting side of the track are used in NC setup while the Limit Switch which is used at the end side is used in NO setup. In addition to this, there is a relay which is used to control the feed of water which is required for the cleaning purpose. A stepper motor is also used for the movement of the cleaning system which is connected to a wheel. while a Johnson Motor is used for the rotation of the brush abut its axis. The rain sensor is also used for the cleaning system.
-
Cleaning System
The cleaning system comprises of four limit switch which controls the functioning of the cleaning system which are mounted in pairs on both ends of the track. The Limit switches which are at the starting side of the track are used in NC setup while the Limit Switch which is used at the end side is used in NO setup. In addition to this, there is a relay which is used to control the feed of water which is required for the cleaning purpose. A stepper motor is also used for the movement of the cleaning system which is connected to a wheel. while a Johnson Motor is used for the rotation of the brush abut its axis. The rain sensor is also used for the cleaning system.
-
Tracking System
The tracking system consists of four LDR Sensors which are placed at the four ends of the frame. The Rain sensor is also used for the tracking system. The motor which is used for transmission of the motion about the Y-axis is placed inside the pillar. While the motor which is used to transmit the motion about the x-axis is attached to the gearbox which is mounted on to the connection piece
-
Cooling System
The cooling system mainly consists of thermocouples which are mounted on the backside of the solar panel. In addition to this, the solenoid valve is also used to provide the water for cooling purposes.
-
-
-
Working
-
Cleaning System
The cleaning system is a time actuated system that does the cleaning operations according to the pre-determined schedule. The relay which controls the solenoid valves is used to control the flow of water. The Johnson Motor is used to rotate the cylindrical brush and the stepper motor is used for the movement of the cleaning system. A pair of limit switches attached at both ends of the track.
During the cleaning operation, the cleaning robot moves from the start point or the initial position to the endpoint at a uniform speed. The brush is also rotating at a constant speed in a clockwise direction to ensure that the solar panel gets rid of all the dust as well as bird droppings on the surface. The sprinkler system used for washing of the dirt is connected to a solenoid valve which is programmed in such a way that the flow of water is done according to the movement of the
cleaning robot. The water stops as soon as the cleaning system is done with the cleaning of that panel.
Fig. 12. Cleaning System Flow Chart
Once the cleaning system reaches the end of the track and hits the either of the limits switches in a pair it will completely stop the water from the sprinklers and the rotation of the brush would change from clockwise to anti-clockwise and the cleaning robot would start to return to its starting point till either of the limit switches in the pair gets triggered. The cleaning operation should at least be done once in 40 hours and not more than once in 22 hours. In case of rain to save water, the system can perform the cleaning operation if the cleaning has not been conducted in the last 22 to 40 hours. The same can also take place for cooling of the solar panel as the water would be used for the cooling of the solar panel the same water can also be used for the cleaning
purpose.
-
Tracking System
The system works on the principle of high intensity of light. The LDR Sensor is a device that is used to measure the intensity of light. The LDR sensor which has the highest
intensity of light acts as a point of action. The LDR sensor sends the data to the Arduino which in turn converts the data and according to the maximum intensity, it sends a signal to the motor. The motor helps the solar panel to adjust according to the intensity of the light.
Fig. 13. Tracking System Flow Chart
Considering the time required for the solar panel to adjust according to the intensity of light and to avoid the malfunction of the motors the adjustment of the solar panel is done once in 25 minutes.
-
Cooling System
-
The system works on the principle of sensing and actuation. Two thermocouples are attached to the backside of a solar panel at equidistance to one another. When the temperature of the solar panel reaches above 45OC the performance of the solar panel starts to deteriorate. When the solar panel reaches a temperature above 45OC a signal is sent to the Arduino which in turn sends a signal to the relay to which a solenoid valve is connected.
Fig. 14. Cooling System Flow Chart
The solenoid valve opens, and the water starts to flow through the valve. The water acts as a medium to transfer heat. The water is let to flow until the temperature of the solar panel is reduced by 15 to 20OC.
As three solenoid valves are used this makes the system very efficient. This is as the cooling is done only to the solar panel which is above the optimum working temperature.
-
IOT INTEGRATION
The integration of the Internet of Things into the system has a vital role as the main objective of the system is to increase the efficiency of the solar panel. This can only be achieved if the losses in the efficiency of the solar panel are known. To understand this, there is a requirement of data from the various aspects like the intensity of sunlight in a particular section, the power output of the solar panel, the temperature of the solar panel, the number of times in a day adjustment of the solar panel is required, etc. The data is collected throughout the day.
To store this data the use of a free service known as ThingSpeak which is an open-source Internet of Things (IoT) application. The data form sensor and actuators are stored and retrieved by using the HTTP and MQTT protocol over the Internet or LAN. ThingSpeak enables the creation of sensor logging applications, location tracking applications, and a lot of things with status updates. The data from the sensor is sent to an individual made ThingSpeak server through the Arduino via Wi-Fi Module (ESP-8266) This collected data can be accessed by anyone who has access to the channel. This data can be used for monitoring the temperature, the output of the solar panel, Sunlight intensity, rain in the area or can be used in analysis and R&D in improving the efficiency of the solar panel. The analysis can be done using ThingSpeak as it has integrated support from the numerical computing software MATLAB, allowing us to perform analysis and visualize the data using Matlab without requiring the purchase of a Matlab.
-
CONCLUSION
Automizing the Cleaning process helped in eliminating the requirement of manual labour which in turn provide with higher efficiency and the operating cost was reduced as the cleaning would require electricity which would be available from the solar panel. Due to the presence of Arduino (microcontroller) in the system, System gets full proofed and chances of error get minimized. Using the cleaning system, the efficiency of the system is increased by 10 to 20 %.
Trackers generate more electricity than their stationary counterparts in roughly the same amount of space required this is due to increased direct exposure to solar rays. The increase in operating efficiency can be between 10 to 25% depending on the geographic location of the tracking system. Due to the tracking system, the vibrations in the system are high. The cost is slightly higher than other types of tracking system this is due to the more complex technology and moving parts necessary for their operation. This is usually around a 5.8 7.3/W increase depending on the size and location. The cost of maintenance is higher as compared to a traditional fixed rack, though the quality of the solar tracker
plays an important role in how much and how often this maintenance is needed.
Using the cooling System increases the energy yield. This is due to the efficiency of the solar panel starts to get effected once the temperature reaches above 50OC. Incorporation of the cooling system ensures that the solar panel will always remain at the desired temperature which will increase the operating efficiency by 10 to 15%. Water active cooling is more efficient than air cooling. This system can easily be self-sustaining and eliminate the cost of power to run various systems as the power would be available through the solar panel. The maintenance cost is the only cost which would remain and no further investment would be required. The initial investment cost can easily be paid off in the long run (within 3 years of use).
-
FUTURE SCOPE
-
To improve the design of the product and increase strength.
-
To further reduce cleaning time.
-
Improving the commercial viability of the product.
-
Using IoT technology to optimize the working of the system by analyzing the data sent to the server by using Matlab through Thinkspeak.
-
The maintenance of the system would also become easy due to this incorporation.
ACKNOWLEDGMENT
The success and final outcome of this project required a lot of guidance and assistance from many people and we are extremely privileged to have got this all along with the completion of our project. All that we have done is only due to
such supervision and assistance and we would like to thank them.
We are glad to present this project report and we express our gratitude to all who directly and indirectly helped us to execute this project – Automated Cleaning Tracking Cooling System (ACTCS) For Increasing Efficiency of Solar Panel. Thus, the success of our project group is a blend of cooperation, dedication, and commitment of staff members during the project work.
We express our deepest gratitude and heartfelt thanks to our project guide Professor S. P. Komble (Mechanical Department) for his expert guidance, constant encouragement, constructive criticism, and inspiring advice throughout this course of the project.
REFERENCES
-
Kimber, A., L. Mitchell, S. Nogradi, and H. Wenger. "The Effect of Soiling on Large Grid-Connected Photovoltaic Systems in California and the Southwest Region of the United States." 2006 IEEE 4th World Conference on Photovoltaic Energy Conference (2006): n.pag. Print.
-
Dhanabal.R., Bharthi.V., Ranjitha.R., Ponni.A., Deepthi.S., and Mageshkannan.P. 2013. Comparison of efficiencies of solar tracker systems with static panel single axis tracking system and dual axis tracking system with fixed mount. International Journal of Engineering and Technology (IJET) 5:1925-1933.
-
K, RAJAN. (2016). SOLAR TRACKING SYSTEM- A REVIEW. International Journal of Sustainable Engineering. 10.1080/19397038.2016.1267816.
-
C.G. Popovici, S.V. Huditeanu, T.D. Mateescu, N.C. Chereche, Energ. Procedia, 85 (2016)
-
El-Seesy, I. E., Khalil, T., Ahmed, M. T., Experimental Investigations and Developing of Photovoltaic/Thermal System, World Applied Sciences Journal 19(9), 1342-1347, 2012.
-
Grubii-abo, Filip & Nizetic, Sandro & Tina, Giuseppe. (2016). Photovoltaic panels: A review of the cooling techniques. Transactions of FAMENA. 40. 63-74.