
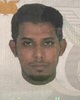
- Open Access
- Authors : Thamer Saeed Balubaid , Abdulrahman Basahel
- Paper ID : IJERTV12IS030053
- Volume & Issue : Volume 12, Issue 03 (March 2023)
- Published (First Online): 08-04-2023
- ISSN (Online) : 2278-0181
- Publisher Name : IJERT
- License:
This work is licensed under a Creative Commons Attribution 4.0 International License
Assessing the Occupational Safety and Health Management System based on Plan-Do-Check-Act Approach – A Case Study of the Saudi Cargo Sector
Thamer Saeed Balubaid Department of Industrial Engineering, Faculty of Engineering
King Abdulaziz University
PO Box 24581, Jeddah 21456, KSA
Prof. Abdulrahman Basahel Department of Industrial Engineering, Faculty of Engineering
King Abdulaziz University
PO Box 24581, Jeddah 21456, KSA
Abstract:- Major accident occurred in the cargo field due to many reasons such as not following the health and safety procedures, fatigue, lack of report the workplace hazard, nor attending the health and safety training, poor supervision therefore, the quality evaluation for the occupational health safety management system of an organization is crucial. The main aim of this study is to assess the occupational safety and health management in the Saudi cargo industry from a prospective Plan-Do-Check-Act model and identifying the root causes of major accidents in Saudi Arabian logistic company. A questionnaire was established to assess the data and measure the occupational safety and health management system in the company as well questionnaire developed in four parts as per the Plan-Do-Check-Act model. One-hundred twenty participated in the present study across main SAL hub stations Riyadh, Jeddah, Dammam and Medina. The key finding of the study was poor training of health and safety of employee, health and safety procedures are not followed, poor environment workplace and management practice, lack of communication, employee are not aware of the HSE policy, management is not considering safety of employee is important and tools and equipment are not inspected regularly. Some of the proposed KPIs are listed such as HSE team should communicate the HSE policy to all employee, top management should listen to employee suggestions, introduce the workplace hazard to the employee, proving high-quality of personal protective equipment to the employee and HSE team should evaluate the corrective action before implementing. By implementing these KPIs and involving the management to health and safety will improve the health and safety performance and culture of the company.
-
INTRODUCTION:
Saudi Arabian Logistic, SAL is offering a variety of secure and convenient Logistics Services through the main hubs. Being strategically located in the Kingdom of Saudi Arabia, SAL is uniquely positioned to provide a bridge between East and West via the hubs, thus giving SAL increased flexibility to use the capacity efficiently and move the customer cargo.
Occupational safety and health is important to focus on preventing the hazards at workplace. As well, Plan-Do-Check-Act is very important to any management system to provide simple approach for solving problems. Following points are some of the advantage of Plan-Do-Check-Act model: It stimulates continuous improvement of people and processes, It test possible solutions on a small scale and in a controlled environment and It prevents the work process from recurring mistakes.[1]
Some researcher say about safety culture, large amount of research has focused on the safety culture within high-risk industries for insight into the causation of industrial accidents (Martyka and Lebecki, 2014). Cox and Flin (1998) have indicated that an organisation's safety culture can be related to accident and incident performance. In fact, after the Chernobyl accident, the safety culture was considered in investigations into the causes of major atastrophes (Martyka and Lebecki, 2014). Some scholars have paid more attention to the function of the safety culture during the process of analysing the cause of accidents (Cox and Flin, 1998). A positive safety culture can help prevent work-related injuries and major disasters (Frazier et al., 2013). With the goal of improving both occupational and process safety, various industries are exploring the approaches and means to create a fine safety culture. Some scholars have considered that culture might concretely refer to the way employees approach their work, in which the creation of a positive safety culture ultimately means improving on-the-job behaviour (Geller, 2005; Krause et al., 1999). [30]
Safety is one of SAL core business functions. SAL is committed to developing, implementing, maintaining and constantly improving strategies and processes to ensure that all SAL aviation activities meet the safety requirements of its safety management system (SMS). This system is considering various safety national and international standards so, it is aimed to achieve the highest level of safety performance and meet standards while delivering the services. At SAL we strive to be leaders in safety, by identifying and managing risks to the operations to levels which are low and deemed unacceptable. SAL is committed to enhancing the safety standards, exceeding regulatory compliance by the application of best industry practices.
SAL SMS safety components are:
-
Safety policy and objectives:
-
Safety accountabilities.
-
Appointment of key safety personnel.
-
SMS documentation. 2- Safety risk management:
-
Hazard identification.
-
Risk assessment and mitigation. 3- Safety assurance:
-
Safety performance monitoring and measurement.
-
Continuous improvement of the SMS. 4- Safety promotion:
-
Training and education.
-
Safety communication.
-
-
-
METHODOLOGY:
This part aims to describe the research methods, approaches and tools of the study to find out the goals and objectives of the study. Explanation of the methods of data collection, sample size and survey that were used in the study. Survey used based on Plan- Do-Check-Act model. In addition, the current chapter illustrates the data that was collected from SMS of SAL to complete the accidents analysis process as a part of this study.
This study was distributed in several parts to get the aims. Researcher selected SAL Company for this study to improve the safety management system and reduce the major accidents at the workplace. Researcher used the Plan-Do-Check-Act model and classified the accidents at workplace into minor and major. Researcher was shoes the repetitive accident to find the root causes by using the fishbone diagram and fault tree analysis. Finally, researcher will recommend a new KPIs base on the weakness in each stage of Plan-Do-Check-Act model and find the root causes of the repetitive accident to reduce it at workplace. These aims will be achieved in next 6 months
The researcher collected the data for the minor and major accidents from 2020 to 2022 for all main hub stations Riyadh, Jeddah, Dammam, Madinah including the date, type, causes, detailed of accident . As well as number of training record of safety at the workplace, cost of the accident, number of safety committee meeting, emergency response drill conducting.
-
Study Questionnaire:
A questionnaire was used to collect the data and measure the occupational safety and health management system in the company. Questionnaire was developed in four parts as per Plan-Do-Check-Act model.
The survey consists of multiple-choice questions in five parts, which are:
Part I: General information: contains the details used for classification, such as the name of employee, main job, age, level of experience and name of the employee was optional because of the confidentiality of participation when completing the survey. Part II: Plan stage: contains of severa questions that measure did the organization aims and objectives are achieved?. In this stage there are nine questions and four multiple choice, for example, Did the HSE policy communicating at the workplace? participants can select, strongly agree, agree, disagree, strongly disagree.
Part III: Do stage: contains several questions that measure the implementation of employee toward organization aims and objectives. In this stage there are there are eight questions and four multiple choice, for example, Did the employees believe that safety is very important at the workplace? participants can select, strongly agree, agree, disagree, strongly disagree.
Part IV: Check stage: contains several questions that measure the organization monitoring towards aims and objectives. in this stage there are ten questions and four multiple choice, for example, Did the employees use all necessary safety equipment to do the task? participants can select, strongly agree, agree, disagree, strongly disagree.
Part V: Act stage: contains several questions that measure did the organization review and act according to the loss target?. In this stage there are seven questions and four multiple choice, for example, Did the company follow up on the action taken? participants can select, strongly agree, agree, disagree, strongly disagree.
Questionnaire of Plan-Do-Check-Act model has four choices to measure the aim of the study each choice has a grade as follows:
(25%)
(50%)
(75%)
(100%)
-
Strongly disagree
-
Disagree
-
Agree
-
Strongly agree
-
-
Sample Size:
To determine the sample size for the study, the observation was held for three weeks to calculate the population, which has been found to be 800 manpower at the main hub station. The sample size was calculated as per the following formula:
Main stations
Manpower
RUH
270
JED
320
DMM
130
MED
80
Sample size =
Where N is the population size, p population proportion p= 0.5, e margin of error e=0.1, z critical value at 95% confidence level Z= 1.96, after taking the previous numbers of population proportion, margin of error and confidence level, sample size equal to 100 as per the previous formula.
-
Data Analysis:
-
Statistical Analysis:
Researcher used the week points in each stage of questionnaire of Plan-Do-Check-Act model and suggested a new KPIs to control the safety management system, in addition to the accident frequency rate and total accident frequency rate. The correlation between the Plan-Do-Check-Act model is to involve the management to health and safety of employee, reporting the hazard of the workplace, proving health and safety training to the employee and communicate the HSE policy to the employee to improve the health and safety performance and culture.
-
Root Cause Analysis:
This study focusing on the major accident at the workplace to find the most common accident, then finding the root causes of these accident by using the fishbone diagram and fault tree analysis to identify the main causes of accident. Researcher using these methods depend on the available document. Major accidents that are considered in this research are property damage, equipment accidents and damage of dangerous goods shipments.
Root causes method will depend on some required data such as:
-
Time of the accident.
-
Witness records.
-
Training records.
-
Toolbox talk records.
-
Previous accident records.
-
-
-
-
RESULT AND DISCUSSION
This chapter represents the major findings of the occupational safety and health management system by analyzing all the collected data from the questionnaire and the relationship between the finding of Plan-Do-Check-Act model of the questionnaire and the findings of fault tree analysis and fishbone diagram.
SMART technique was implemented in some research as a result of appropriate calculations, a following vector of SMART weights was obtained: [S = 0.0822; M = 0.2529; A = 0.1448; R = 0.4384; T = 0.0817]. The highest significance (ca. 44%) has been attributed to the Relevant criterion i.e. the relevance of the indicator to the actions performed in a given area of OSH MS, and to the adequacy thereof within the context of the contribution to the achieving of overall objectives for a given area of activity as well as the entire system. The second highest significance (ca. 25%) was attributed to the Measurable criterion, thus emphasising that KPI should have such characteristics as to allow for technical measurement of the indicators value, and that the data should be identifiable and relatively readily available to persons involved in the measurement.[29]
Persentage
One of the research introduce the important of safety culture Safety culture is an organisational factor in safety cases, and it is also the root cause of accidents. Safety culture plays an important role in antecedents of enterprise safety conditions, of which defects may cause various industrial accidents.[30]
Plan stage
40%
35%
30%
25%
20%
15%
10%
5%
0%
Strongly agree
Agree Disagree
Strongly disagree
P1 P2 P3
P4 P5 P6
Questions
P7
P8
P9
Figure 1: Plan stage questions diagram
50%
40%
30%
20%
10%
Persentage
As shown in figure 1, most of the participants disagree and strongly disagree in the plan stage questions due to several reasons such as employee are not understanding of the company HSE policy, HSE policy are not committed by top management, employee are not participating in the risk assessment, HSE programs and objectives are not announce to the employee, employee are did not know to whom to report the workplace hazard, top management are not consider safety is important as production.
Do stage
Strongly agree
Agree Disagree
Strongly disagree
D1
D2
D3
D4
D5
D6
D7
D8
Questions
0%
Figure 2: Do stage questions diagram
As shown in figure 2, 75% of participants are having fire drill exercise in the workplace twice a year. On the other hand, most of the participants are disagree with questions due to several reasons such as HSE team are not brief the employee for the hazard at the workplace, tools and equipment are not inspected regularly, HSE team are not review all the suggested solution to substitute or eliminate the hazards, employee are not believe that safety is important at the workplace, top management are not promote their employee for attending the HSE training, company are not proving sufficient personal protective equipment to their employee
Check stage
40%
35%
Persentage
30%
25%
20%
15%
10%
5%
0%
C1 C2 C3 C4 C5 C6 C7 C8 C9 C10
Questions
Strongly agree Agree Disagree
Strongly disagree
Figure 3: Check stage questions diagram
As shown in figure 3, many participants disagree with the questions due to internal audit is not implementing correctly to measure the system, activity records and control system are not based on HSE requirements, employee are not involved in the accident investigation process, accident lesson and learn is not implemented, investigation results and corrective action are not announced to the employee, HSE team are not analyze the minor and major accidents, employee are not reporting th workplace hazards, suggested solutions are not improve employee task, employee are not use the correct personal protective equipment to their task, HSE rules and procedure are not followed by employee.
Act stage
40%
35%
30%
25%
20%
15%
10%
5%
0%
Strongly agree
Agree Disagree
Strongly disagree
A1 A2 A3
A4
Questions
A5
A6
A7
Persentage
Figure 4: Act stage questions diagram
As shown in figure 4, most of the participants disagree with the question due to HSE team are not acting on the failed suggested solutions, top management are not involved in the hazard review meeting, HSE team is not following up with the concerned department for the action taken, employee are not rewarding for reporting the hazard at the workplace.
Researcher consider following KPIs to improve all stages, HSE team should communicate the HSE policy, HSE awareness through toolbox talk, HSE meetings and distribute the policy in the boards, HSE policy should be very simple to the employee, involve the top management to the HSE policy and HSE committee meeting, providing the HSE basic training to the employee, participate the employee in the risk assessment, top management should listen to employee suggestions, introduce the workplace hazards to all employee, implement regular tools and equipment inspection, HSE team must listen and review the employee suggested solutions, HSE team need to find the causes of repetitive accident for implementing additional control, proving a high quality of personal protective equipment, implementing internal audit to measure the HSE system, employee should follow the safe job analysis for their task, involving the employee for accident investigation, employee should report the hazard at the workplace, accident corrective action should be announced to the employee, HSE team should react on failure corrective action, HSE team should follow up with the concerned corrective action, HSE team must evaluate the corrective action before implementing and rewarding the employee for reporting the workplace hazard.
-
CONCLUSION:
This study aims to evaluate the occupational safety and health management system by using the Plan-Do-Check-Act model and identifying the root causes of major accidents furthermore suggesting control measures to enhance the safety culture in the workplace.
Most of the study showed that enhancing the occupational safety and health management system through involving the high management through health and safety committee meeting by presenting the effectiveness of the safety and health management system and new plans of the workplace, participating and discussing with the employee of the hazard at the workplace through toolbox talk and training session, rewarding the employee for safe behavior, involving them in the risk assessment task, inspect their equipment and tools regularly to make sure it is safe to use, distribute the safety signs through the workplace, provide good and welfare facilities to the employee.
Research found that some of the findings in the study which need to improve such as lack of high management involvement in the workplace health and safety, employee are not aware of health and safety policy, lack of health and safety employee training, not reporting the hazard or near miss nor accident cases in the workplace, root causes of the incidents are not implemented, no procedure for inspect the workplace equipment and tools, internal audit is not implemented in the field.
Major accidents such as fatalities or lost time cases are one of the biggest issues in the airport filed. For avoiding these accidents should implement the health and safety management system, reporting the hazards of workplace, finding the root causes of the workplace accident to prevent the repetitive, introduce the hazards of the new tasks or equipment to the employee before starting the new task or using the equipment.
-
REFERENCES:
<https://www.hsa.ie/eng/topics/managing_health_and_safety/safety_and_health_management_systems/> [Accessed 4 October 2022]. [3] Phelpstead. J, (2020) management of health and safety. London: Rapid results college limited.
[4] Safety management system . [online] Available at: <https://en.wikipedia.org/wiki/Safety_management_system> [Accessed 7 March 2022]. [5] How can effective safety management system safe money. [online] Available at: <https://www.upkeep.com/answers/facility-management/how-can- effective-safety-management-actually-save-money> [Accessed 22 February 2022]. [6] Safety management system. [online] Available at: <https://en.wikipedia.org/wiki/Safety_management_system> [Accessed 22 February 2022]. [7] Accident. [online] Available at: < https://en.wikipedia.org/wiki/Accident> [Accessed 22 February 2022]. [8] Safety management system. [online] Available at:<https://www.faa.gov/about/initiatives/sms/explained/components#:~:text=SMS%20is%20composed%20of%20four,Safety%20Assurance> [Accessed 22 February 2022].
[9] International labour organization . [online] Available at: <https://www.ilo.org/global/standards/introduction-to-international-labour-standards/the- benefits-of-international-labour-standards/lang–en/index.htm> [Accessed 6 October 2022]. [10] ISO 45001 Occupational Health & Safety Management. [online] Available at: <https://www.qmsuk.com/iso-standards/iso-45001 > [Accessed 26 February 2022]. [11] Common warehouse accidents and how to avoid them. [online] Available at: <https://www.thompsons.law/support/legal-guides-and- resources/common-warehouse-accidents-and-how-to-avoid-them> [Accessed 26 February 2022]. [12] Health and safety issues in the warehouse. [online] Available at:<https://www.newcastlesys.com/blog/top-10-health-and-safety-issues-in-the- warehouse?msclkid=577689bdae8a11ecb8d806c232099f87> [Accessed 28 March 2022]. [13] How to prevent accident at workplace. [online] Available at:<https://mmannlofts.com/how-to-prevent-accidents-in-the- warehouse/?msclkid=48cae7c8b0b911eca4884d214a444d97> [Accessed 31 March 2022]. [14] OSH WIKI networking knowledge . [online] Available at: <https://oshwiki.eu/wiki/Accident_investigation_and_analysis > [Accessed 9 October 2022]. [15] Tochi. U, Eucharia. N, Chinemerem. P, (2021) Evaluation of safety performance of nigerian construction industry: Acase study of the niger deltaregion.
[16] Impact of safety culture to organization. [online] Available at:<https://www.ipl.org/essay/Internal-And-External-Factors-That-Influence-Safety- FJZRED4NSU?msclkid=77d57632ae6211ecb7fb7f69a7d0bf2c> [Accessed 28 March 2022]. [17] Impact of health and safety training to organization. [online] Available at:<https://www.hse.gov.uk/treework/training-is- important.htm?msclkid=92fe0f6cae6f11ecadd672555d61f4bf> [Accessed 28 March 2022]. [18] Effective workplace inspection. [online] Available at:<https://www.ccohs.ca/oshanswers/prevention/effectiv.html?msclkid=b099e0c2ae7111ecba32e1395bcab285> [Accessed 28 March 2022]. [19] Root cause analysis. [online] Available at: <https://en.wikipedia.org/wiki/Root_cause_analysis> [Accessed 7 March 2022]. [20] Five whys. [online] Available at:<https://buffer.com/resources/5-whys-process/?msclkid=855e4865ab6d11ec9e67f49c79a3767b> [Accessed 24 March 2022]. [21] Five whys. [online] Available at:<https://en.wikipedia.org/wiki/Five_whys?msclkid=85600b5bab6d11eca03ef2a75c9cadde> [Accessed 24 March 2022]. [22] Five whys. [online] Available at:<https://www.isixsigma.com/tools-templates/cause-effect/determine-root-cause-5- whys/?msclkid=b4747d9eab7511ec870f93d54f615797> [Accessed 24 March 2022]. [23] Ishikawa diagram. [online] Available at:<https://en.wikipedia.org/wiki/Ishikawa_diagram?msclkid=98defd28ab7711ecafc09611117e9e2b> [Accessed 24 March 2022]. [24] Pareto analysis. [online] Available at:<https://en.wikipedia.org/wiki/Pareto_analysis?msclkid=27b73f70ab7a11ec836d28c1225f207d> [Accessed 24 March 2022]. [25] Fault tree analysis. [online] Available at:<https://en.wikipedia.org/wiki/Fault_tree_analysis#:~:text=Fault%20tree%20analysis%20(FTA)%20is,series%20of%20lower%2Dlevel%20events.> [Accessed 7 March 2022].
[26] Fault tree analysis. [online] Available at: <https://www.edrawsoft.com/what-is-fault-tree- analysis.html?msclkid=8a0c4013ab6611ecafa7cb5463b7bae0> [Accessed 24 March 2022]. [27] Accident analysis. [online] Available at:<https://en.wikipedia.org/wiki/Accident_analysis#:~:text=Accident%20analysis%20is%20carried%20out,accident%20investigation%20or%20incident
%20investigation%20> [Accessed 7 March 2022].
[28] Accident analysis. [online] Available at: <https://ehscenter.com/accident-analysis-report-sample?msclkid=95c82834ab6b11ec94633bc579c99b2a> [Accessed 24 March 2022]. [29] Dniel, P 2014, Measuring operational performance of OSH management system A demonstration of AHP-based selection of leading key performance indicators, Elsevier Ltd, vol. 7, no 1, pp. 6, 11 [30] Jiangshi, Z, Jing, F, Hongyu, H, Gui, F, Fangchao, N, Wenyue, Z, Process Safety and Environmental Protection, Elsevier Ltd, vol. 7, no 1, pp. 2, 3 [31] Anna, S 2014, Assessing the impact of processes on the Occupational Safety and Health Management Systems effectiveness using the fuzzy cognitivemaps, Elsevier Ltd, vol. 7, no 1, pp. 72, 77
[32] Ahmet, T, Ercan, Y, Emre, A, Ozcan, A, Probability-based extensive quantitative risk analysis: collision and grounding case studies for bulk carrier and general cargo ships, Australian Journal of Maritime & Ocean Affairs, vol. 15, no 1, pp. 93,96-97