
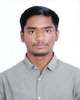
- Open Access
- Authors : Pradnesh Mokal , Tanvesh Patil , Aniruddh Pawar , Siddhesh Jadhav, Dr. Nitin Panaskar
- Paper ID : IJERTV12IS040112
- Volume & Issue : Volume 12, Issue 04 (April 2023)
- Published (First Online): 24-04-2023
- ISSN (Online) : 2278-0181
- Publisher Name : IJERT
- License:
This work is licensed under a Creative Commons Attribution 4.0 International License
An Investigation of Lean Six Sigma Barriers in Electric Vehicle Assembly
Pradnesh Mokal, Tanvesh Patil, Aniruddh Pawar, Siddhesh Jadhav Department of Mechanical Engineering MCTs Rajiv Gandhi Institute of Technology Mumbai, Maharashtra
Dr. Nitin J. Panaskar
Assistant Professor Department of Mechanical Engineering
MCTs Rajiv Gandhi Institute of Technology Mumbai, Maharashtra
Abstract:- Lean and Six Sigma integration will reduce errors by removing non-value-added activities from the production chain. In the latter scenario, the manufacturing and assembly companies are facing intense competition in the market as the demands of the customers to develop high quality products are increasing day by day. In this situation, the manufacturing and assembly organizations apply strategies that improve the organization and deliver high-quality products within the stipulated time to meet customer demand. Successful implementation of the LSS framework using a combination of DMAIC tools and techniques can reduce errors and eliminate waste while reducing non-value-added activities in the supply chain. The study focuses on developing a solution that uses LSS to overcome identified barriers and reduce non-value-added activities with improved profitability.
Keywords: Six Sigma, DMAIC, Lean Six Sigma, Lean manufacturing, TOPSIS, Business process improvement
OBJECTIVES
-
To investigate the obstacles to implementing LSS (Lean Six Sigma) at various levels of the electrical assembly.
-
To examine the challenges in the manufacturing of electrical vehicles
-
To implement a Lean Six Sigma (LSS) methodology to help an automotive component assembly company reduce defects and improve bottom-line outcomes.
-
INTRODUCTION
-
Working of Electric vehicles
The controller takes energy from the batteries and transfers it to the motor. The accelerator pedal is connected to several potentiometers (variable resistors), and these potentiometers provide a signal that tells the controller how much power to deliver. The controller can provide power (while the vehicle is stationary), full power (while the driver is pressing the accelerator), or any level of power in between.
Electric cars, often referred to as battery electric vehicles (BEVs), are powered by an electric motor rather than an internal combustion engine. The electric motor is powered by a large traction battery that needs to be plugged into an outlet. Electric vehicle power supply equipment, often referred to as plug or polarity charging (EVSE). Because it runs on electricity, there are no exhaust fumes from the tailpipe, and it doesn't have standard liquid propulsion components like a fuel pump, power cord, power pack, or energy tank. [1] [2]
-
Six Sigma
Six Sigma is a management strategy which was originally introduced by Bill Smith of Motorola in United States of America in 1986 to reduce variations in manufacturing process. Motorola during that time was in trouble as their quality of products started declining, and which ultimately hampers their profit. 40 companies who have successfully implemented Six Sigma in some form or another. Another company General Electric implemented and adopted Six Sigma through proper Six Sigma training from Motorola. [1] [3]
As of today, many business and manufacturing sectors uses this to improve the overall quality of process by identifying and eliminating the root cause and minimizing the variability in process. Six Sigma is structured, data driven approach to eliminate or reduce defects from any process whether it is manufacturing or service. [4]
-
-
LITERATURE REVIEW
-
TOPSIS
It is a compensatory aggregation method that compares a set of alternatives by identifying weights for each criterion, normalising scores for each criterion, and calculating the geometric distance between each alternative and the ideal alternative, which is the alternative with the best score in each criterion.[5] TOPSIS makes the premise that the criteria increase or decrease monotonically. In multi-criteria issues, normalisation is commonly essential since the parameters or criteria are frequently of discordant dimensions.[6] TOPSIS and other compensatory approaches allow for trade-offs between criteria, where a bad outcome in one criterion might be offset by a good result in another.[7] Non-compensatory approaches, which include or exclude alternate solutions based on hard cut- offs, give a more realistic type of modelling.
-
Why TOPSIS in Multiple-Choice Decision-Making
TOPSIS is favoured in multiple-choice decision-making because it can handle both quantitative and qualitative criteria, which is critical when making judgements involving many elements that are difficult to quantify or represent statistically.[8] It also provides for customizable criterion weighting, which implies that decision-makers may give varying degrees of priority to each criterion based on their individual needs.[9]
TOPSIS also considers the relative relevance of criteria and the trade-offs between them.[10] It examines each alternative's positive and negative influences on each criterion and assigns a score to each alternative based on its
proximity to the ideal answer, which is a combination of the greatest possible values for each criterion.[11]
TOPSIS is also reasonably easy to use and may be employed in scenarios with a large number of choices and criteria. It gives a clear and visible ranking of options, which can assist decision-makers in making informed judgements and understanding the reasoning behind their selections.
-
Paper Referred
1] This study examines the problems and possibilities presented by electric automobiles. According to market experts, IC transportation will be replaced by EV in the future. EV sales are expected to increase by 24% on average throughout the projected period. There are several hurdles in the initial investment and market adoption, but the EV industry will grow owing to the prospects.[12]
2] The engineering and manufacture of an electric car alters the OEM-supplier relationship dramatically. To begin with, an electric motor has just roughly 200 separate components, but an internal combustion engine has at least 4000 parts. Manufacturers benefit greatly from the substantial decrease in part number. On the one hand, this can result in huge cost savings. Not only are the parts less expensive to acquire, but manufacturing EVs allows for economies of scale since OEMs get their parts from fewer sources. Having fewer parts also as ramifications for maintenance and total ownership costs. It is significantly simpler to replace a single component. [13]
Parameters
1
2
3
4
5
Time-Efficient
O
O
O
O
O
Cost-Efficient
O
O
O
O
O
Effort-Efficient
O
O
O
O
O
Table 1:- Parameter for Survey
3] Six sigma approaches are mostly used to eliminate faults and enhance oprational efficiency. It seeks to reduce flaws by eliminating variances, which will eventually lead to better efficiency. Lean technique aids in the elimination of waste resulting from unnecessary analysis. The combination of the Lean and Six Sigma techniques results in even more precise identification and elimination of process faults.[13] [14]
4] More robots will be employed to assemble smaller parts and subassemblies, in addition to the full motor, as OEMs and suppliers speed up EV manufacturing. Tight tolerances provide various issues in rotor assembly, which is a great choice for automation. Robots are used in rotor and stator assembly applications to choose, wind, and shape coils or windings. Robots can also be employed to attach parts, push the rotor shaft, weld and glue, and bolt the body together. Precise, automated injection of glue into magnet housings is required to assure magnet retention, even at rotating rates of 15,000 rpm or higher.[15]
5] Six Sigma framework proposed. The proposed framework was used in small and medium-sized businesses (SMEs). The implementation framework in this study was designed to meet the demands of SMEs and was completed after a lengthy research period. Data for the framework
were gathered via a manufacturing organization consultant, a questionnaire, a semi-structured interview, and several papers. The Six Sigma methodology was implemented in SMEs using a five-phase strategy. The Six Sigma deployment framework was evaluated in three SMEs in this study. Following a successful deployment, they discovered the true need for a framework in SMEs. Upon completion, they changed the framework based on expert advice and team member suggestions.[16]
-
-
METHODOLOGY
Table 2:- Figure depicts the overall flow of the suggested technique. Each flow stage is detailed in depth here
-
Data Collection Categorised For Further Processing. (The Identified Variables Are Grouped Into Several Levels)
-
Experts Opinion
The acquired and summarised data is then displayed to a group of specialists from the same field. The data was compiled and organised into a set of questions for the specialists to review. To make data collection easier, the questionnaires were created in Google Forms.
-
Expected Outcomes
The planned study's findings would aid in improved Six Sigma implementation and would help to identify issues faced during the development of electrical cars. Identifying and addressing impediments to the assembly of electric vehicles will thereby enhance and develop sustainable production. This support will be beneficial for both the environment and the economy. The organisation as a whole must be willing to shift its perspective and adapt to the new practises and cultural changes necessary for a successful assembly strategy based on lean six sigma models.
-
-
BARRIERS IDENTIFIED
-
Today, all assembly processes are within reach of attaining a world-class level of electric car delivery, and the industry's automation is to blame. However, human involvement remains a crucial aspect. For automated and technologically complex equipment, skills above the usual
supervisor or worker are essential, as is a suitable and successful assembly strategy. Time, money, labour, resources, and commitment from all stakeholders are necessary for implementing assembly plans employing lean six sigma in industries. In businesses, there are several hurdles to Lean Six sigma Assembly. The following sections explore and summarise the major hurdles identified in the literature.
Table 3:- Barriers to Lean six sigma EV assembly process
-
Battery Pack Transportation from Battery Manufacturer to EV Manufacturer
Because of the vast size and weight of battery packs, as well as the dangerous components they contain, transporting battery packs from a battery production unit to an electric vehicle (EV) manufacturing facility is a difficult and time-consuming process.[17] To guarantee safe and effective transit, this procedure necessitates careful handling and shipment, and there are several technological and logistical difficulties to overcome. Battery technology, battery pack size and weight, mode of transportation, regulatory requirements, scheduling, documentation, labelling, communication, and teamwork are some of these.[18] To limit the danger of accidents or incidents during transportation, effective communication, safety standards, and procedures are required. Overall, moving battery packs from a battery manufacturer's unit to an EV manufacturer's unit necessitates meticulous planning, coordination, and execution to guarantee the batteries reach safely and on schedule.[19]
-
Battery Pack Transportation within the EV Plant Affect the Final Assembly of Electric Vehicle
Battery pack movement inside an electric vehicle (EV) facility can have a substantial influence on the final assembly process.[20] This is due to the fact that battery packs are critical components of electric vehicles, and delays or faults in their transportation may lead to delays and pauses in the assembly process.[21] To solve these concerns, EV producers must adopt a carefully designed and efficient transportation system that includes defined
routes, supply dates, and methods for carrying battery cells inside the plant.[22] To lessen the risk of delays or mistakes, robots or automation can be deployed.[23] Furthermore, the structure of the battery pack building facility may be adjusted to decrease the time and distance required to transport battery packs between stages of the production process.[24]
-
Manual assembly line
The manufacturing industry is confronted with a number of issues linked to assembly line production. To begin with, adjusting to new surroundings might be challenging owing to assembly line inflexibility and a lack of required equipment. Second, many assembly lines lack the equipment required to isolate problems and assess the whole process from a single place.[25] Finally, an uneven task allocation on the manufacturing line can lead to bottlenecks and inefficiency. Lastly, labourers' perspectives contribute to assembly line manufacturing problems such as low salaries, minimal instruction, and repetitive duties with limited chance for critical thinking. Addressing these issues may necessitate investments in new technology, improved training, and the development of methods to balance the burden on assembly lines.[26]
4. Rigid Automated Assembly Lines to Change Due To New Battery Designs
New battery designs for electric cars are projected to have an influence on the current design and operation of automated assembly lines.[27] [28] This is due to the fact that new battery designs may necessitate the use of different assembly techniques, equipment, and materials than those currently in use.[29] [30] Nevertheless, due to many reasons such as compatibility concerns, time limits, cost considerations, worker training needs, and the complexity of producing the new batteries, altering inflexible automated assembly lines to incorporate new battery types may be a substantial task.[31] Manufacturers must carefully consider these aspects in order to decide the optimal way for implementing the necessary adjustments.[32] [33] Workarounds or interim solutions may be required to keep production functioning while adjustments are implemented.[34] Finally, how effectively manufacturers solve these difficulties will determine the effectiveness of introducing new battery designs.[35]
-
Assembly Of Electric Vehicles into The Current Conventional IC Engine
Incorporating the assembly of electric cars into a traditional ICE-based vehicle manufacturing line might be a big difficulty.[36] When compared to ICE cars, electric vehicles have different components, manufacturing procedures, quality control measures, and safety issues, necessitating considerable adjustments to the existing ssembly line.[37] The assembly line has been reconfigured, new tools and equipment have been integrated, quality control processes have been updated, and new safety needs have been accommodated. [38] To effectively integrate the manufacture of electric cars into a
current assembly line, proper planning and execution are required.[39]
=
Xij
X
n 2
-
Integrate Inline Inspection and Testing into the Current Conventional IC engine
We have examines numerous issues and technology linked to electric drives, electric automobiles, and quality standards in the EV business. The first point underlines the significance of precisely matching the moving rotor and stationary stator in electric drives in order to achieve high efficiency and minimal wear.[36] The second point discusses the usage of locator sensors to ensure appropriate adhesive bead application in electric vehicles. The third point emphasises the EV industry's dynamic and complicated character, as well as the need of assuring the quality and dependability of electric power trains.[40] The fourth point highlights insulation evaluation as a significant issue in EVs, and typical testing may fail to discover concealed faults. The fourth argument emphasises the significance of field evidence and experience in developing globally accepted quality standards for EV production.[41]
-
Qualified Human Resource Working In The EV Industry
In the electric vehicle (EV) business, a lack of qualified human resources can have an influence on the development, cost, quality, and workload of designing, constructing, and maintaining EVs.[41] A lack of
i=1 Xij
Step 3: Create the weighted normalised matrix using
elements.
Vij = × Wj
Xij
Step 4: Finding the greatest and minimum values of
weighted normalised components in each column to get the positive and negative ideal solutions.
Step 5: Calculate the Euclidean distance from ideal best alternative
m 0.5
2
Si+ = [(Vij Vj+ ) ]
j=1
Step 6: Calculate the Euclidean distance from the ideal
worst alternative
m 0.5
2
Si = [(Vij Vj ) ]
j=1
Step 7: Rank the possibilities in preference order of
closeness ratio (Pi). The best option is the one with the
shortest distance to the optimal answer. The shortest
distance to the ideal answer represents the greatest distance from the negative ideal solution.
Si
Pi = S + + S
i i
competent staff can stymie EV development, raise labour
costs, reduce product quality, and strain current workers with additional workloads.[42] Furthermore, competition for elite people can spark a talent war, driving up salary and perks even higher.[38] Companies may need to engage in training and education programmes, partner with universities and research institutes, or investigate outsourcing possibilities to replenish their staff to handle this issue.[43]
-
Qualified Human Resource Working In The Area Of Statistics
Electric vehicle manufacturing necessitates a wide variety of skills and experience, including statistical analysis, to guarantee the production process is efficient and the cars satisfy quality requirements.[44] Without trained statistics workers, the manufacturing process may be hampered, resulting in inefficient production, poor quality control, and erroneous predictions. Manufacturing businesses may address this difficulty by investing in training and employing competent workers, or by collaborating with universities and research organisations to establish specialised training programmes for the current workforce.[45] This will guarantee that the production process runs smoothly and that the electric vehicles satisfy the necessary quality requirements.[32]
-
Procedure Followed For TOPSIS
Step 1: On the basis of m alternative and n criteria, a
matrix with elements Xij is made
Step 2: The normalised matrix is now computed using
elements.
-
Implementation of TOPSIS
Table 4:- Survey Results and Weightage
Weightage [STEP 1]
0.34
0.33
0.33
Cost
Time
Effort
1. Battery Pack Transportation From Battery Manufacturer To EV Manufacturer
3.46
3.17
3.32
2. Battery Pack Transportation Affect The Final Assembly Of Electric Vehicle
3.42
3.17
3.25
3. Manual Assembly Line
3.60
3.21
3.35
4. Rigid Automated
Assembly Lines To Change Due To New Battery Designs
3.42
3.39
3.60
5. Assembly Of Electric Vehicles Into The Current Conventional IC Engine
3.39
3.42
3.57
6. Integrate Inline Inspection
3.39
3.25
3.25
7. Integrate Inline Testing
3.71
3.25
3.50
8. Qualified Human Resource Working In The EV Industry
3.57
3.35
3.60
9. Qualified Human Resource Working In The Area Of Statistics
3.60
3.4
3.46
10. Enough Qualified Experts Working In The Field Of Lean Six Sigma
3.5
3.35
3.42
STEP 2
Cost
Time
Effort
1. Battery Pack Transportation From Battery Manufacturer To EV Manufacturer
0.3495
0.3406
0.3406
2. Battery Pack Transportation Affect The Final Assembly Of Electric Vehicle
0.3465
0.3406
0.3334
3. Manual Assembly Line
0.3647
0.3438
0.3447
Table 5:- Normalized matrix
Vehicles Into The Current Conventional IC Engine
6. Integrate Inline Inspection and Testing into the Current Conventional IC engine
0.1188
0.1124
0.1124
0.0102
7. Qualified Human Resource Working In The EV Industry
0.1178
0.1124
0.1100
0.0028
8. Qualified Human Resource Working In The Area Of Statistics
0.1240
0.1134
0.1137
0.0059
4. Rigid Automated Assembly Lines To Change
Due To New Battery Designs
0.3465
0.3631
0.3703
5. Assembly Of Electric Vehicles Into The Current Conventional IC Engine
0.3424
0.3674
0.3662
6. Integrate Inline Inspection and Testing into the Current Conventional IC engine
0.3586
0.3481
0.3467
7. Qualified Human
Resource Working In The EV Industry
0.3606
0.3599
0.3703
8. Qualified Human
Resource Working In The Area Of Statistics
0.3586
0.3631
0.3539
Table 9:- Distance from the negative ideal solution Si-
Barriers
Parameter
Step 6
Cost
Time
Effort
Si-
1. Battery Pack Transportation From Battery Manufacturer To EV Manufacturer
0.118
8
0.112
4
0.112
4
0.003
2. Battery Pack Transportation Affect The Final Assembly Of Electric Vehicle
0.117
8
0.112
4
0.11
0.001
3. Manual Assembly Line
0.124
0.113
4
0.113
7
0.008
4. Rigid Automated Assembly Lines To Chan ge Due To New Battery Designs
0.117
8
0.119
8
0.122
2
0.014
5. Assembly Of Electric Vehicles Into The Current Conventional IC Engine
0.116
4
0.121
2
0.120
8
0.014
6. Integrate Inline Inspection and Testing into the Current Conventional IC engine
0.118
8
0.112
4
0.112
4
0.007
7. Qualified Human Resource Working In The EV Industry
0.117
8
0.112
4
0.11
0.015
8. Qualified Human Resource Working In The Area Of Statistics
0.124
0.113
4
0.113
7
0.011
Table 6:- Weighted normalised matrix
Barriers
Step 3
Cost
Time
Effort
1. Battery Pack Transportation From Battery Manufacturer To EV Manufacturer
0.1188
0.1124
0.1124
2. Battery Pack Transportation Affect The Final Assembly Of Electric Vehicle
0.1178
0.1124
0.1100
3. Manual Assembly Line
0.1240
0.1134
0.1137
4. Rigid Automated Assembly Lines To Change
Due To New Battery Designs
0.1178
0.1198
0.1222
5. Assembly Of Electric Vehicles Into The Current Conventional IC Engine
0.1164
0.1212
0.1208
6. Integrate Inline Inspection and Testing into the Current Conventional IC engine
0.1219
0.1148
0.1144
7. Qualified Human
Resource Working In The EV Industry
0.1226
0.1187
0.1222
8. Qualified Human Resource Working In The Area Of Statistics
0.1219
0.1198
0.1168
Table 10:- Summary of closeness ratio and Ranking of barriers
Barriers
Step 7
RANK
Pi
1. Battery Pack Transportation From Battery Manufacturer To EV Manufacturer
0.1923
7
2. Battery Pack Transportation Affect The Final Assembly Of Electric Vehicle
0.0778
8
3. Manual Assembly Line
0.4248
5
4. Rigid Automated
Assembly Lines To Change Due To New Battery Designs
0.6932
2
5. Assembly Of Electric Vehicles Into The Current Conventional IC Engine
0.6455
4
6. Integrate Inline Inspection and Testing into the Current Conventional IC engine
0.4209
6
7. Qualified Human Resource Working In The EV Industry
0.8419
1
8. Qualified Human Resource Working In The Area Of Statistics
0.6575
3
Table 7:- Summary of +ve ideal solution and ve ideal solution
Step 4
Cost
Time
Effort
Positive ideal solution (v+)
0.1240
0.1212
0.1222
Negative ideal solution (v-)
0.1164
0.1124
0.1100
Table 8:- Distance from the positive ideal solution Si+
Barriers
Parameter
Step 5
Cost
Time
Effort
Si+
1. Battery Pack Transportation From Battery Manufacturer To EV Manufacturer
0.1188
0.1124
0.1124
0.0141
2. Battery Pack Transportation Affect The Final Assembly Of Electric Vehicle
0.1178
0.1124
0.1100
0.0162
3. Manual Assembly Line
0.1240
0.1134
0.1137
0.0114
4. Rigid Automated Assembly Lines To Change Due To New Battery Designs
0.1178
0.1198
0.1222
0.0063
5. Assembly Of Electric
0.1164
0.1212
0.1208
0.0076
-
RESULTS AND DISCUSSION
Barriers are rated on a scale of 1 to 5. (1-Very low, 5- Very high). Table 6 shows a weighted normalised decision matrix created in steps 2 and 3. Positive and negative ideal solutions are obtained using step 4, as shown in table 7. Step 5 determines the differentiation of each CSF from the positive and negative ideal solutions, as indicated in tables 8 and 9. Now, using step 6, the relative proximity of each barrier to the ideal solution (closeness ratio) is determined, displayed in table 10, and the relative order of these barriers is presented in table 10.
The development of innovative battery technologies for electric vehicles is likely to have a substantial influence on present automated assembly line design and operation. Different assembly procedures, equipment, and materials may be required, and manufacturers must carefully evaluate compatibility problems, time constraints, price considerations, worker training requirements, and the difficulty of making the new batteries. The EV industry also faces a shortage of competent human resources. It is a complex and time-consuming procedure to transport batteries form a battery manufacturer to an electric vehicle manufacturing plant. To ensure safe transportation, seamless interaction, regulations, and procedures are essential.
The mobility of battery packs inside an EV factory may also have a significant impact on the assembly phase of the procedure. Integrating electric vehicle assembly into a standard ICE-based vehicle production process might be difficult. A variety of difficulties related to production on assemblies confront the manufacturing business, which may necessitate investments for new technology, greater training, and the creation of strategies to balance the pressure on assembly lines. The article looks at a variety of topics and technologies related to electric moves, electric autos, and quality guidelines in the EV industry. Overall, the electrical car manufacturing business has numerous and complicated obstacles, and practical solutions are necessary to assure efficient production as well as reliability and quality of electrically powered trains.
Transporting batteres safely from battery producers to EV makers. Incorporation of electric vehicle production into conventional ICE-based vehicle production lines necessitates careful planning and execution, which includes restructuring the assembly line, merging new machinery and tools, updating quality control methods, and adapting new safety requirements. A further problem confronting the EV business is a shortage of competent people materials, which might be tackled through training and educational initiatives, collaboration with institutions and other academic organizations, or exploring outsourcing options. Furthermore, novel battery design for electric vehicles can have a substantial influence on the layout and operation of automatic assembly lines, necessitating the use of alternative assembly processes, equipment, and materials. Finally, to assure the reliability and excellence of electric power trains, manufacturing must address challenges connected to manufacturing on assemblies, such as money in new technology, increased training, and the invention of techniques to balance the pressure on assembly lines.
-
CONCLUSION
-
To summarize, the challenges that the electric car manufacturing business faces are considerable and complicated. These include problems with transport for battery packs, the integration of electric cars into existing ICE-based vehicle production lines, a shortage of qualified workers, and the discovery of novel battery technologies that necessitate changes to automation assembly lines. When adopting new designs, designers must carefully examine compatibility problems, time constraints, cost considerations, employee educational requirements, and the involved process of producing new batteries.
To guarantee the safe delivery of battery assemblies from battery makers to EV manufacturers, seamless interaction, security regulations, and processes are essential. Inclusion of electric vehicle manufacturing operations into typical ICE-based vehicle production lines necessitates careful strategy and execution. To meet these problems, investments in emerging technologies, enhanced instruction, and the establishment of strategies to balance the pressure on production lines will be required. This will assure the dependability and reliability of electrically powered trains.
To ensure the safe transportation and installation of the battery packs, the electric car (EV) assembly entails a complicated and automated procedure that calls for trained people and careful planning. The literature has highlighted a number of obstacles that may prevent the effective application of Lean Six Sigma assembly procedures.
BIBLIOGRAPHY
[1] Padhi and Manas Ranjan, ELECTRIC VEHICLES, CENTURION UNIVERSITY OF TECHNOLOGY AND MANAGEMENT,ODISHA, [Online]. Available: https://courseware.cutm.ac.in/wp- content/uploads/2020/06/Notes-on-Electric-Vehicles.pdf
[2] https://afdc.energy.gov/vehicles/how-do-all-electric-cars-work. [3] Application of Lean Six Sigma to Improve Service in Healthcare Facilities Management: A Case Study | Journal of Facility Management Education and Research. https://meridian.allenpress.com/jfmer/article/1/1/9/131363/Applicati on-of-Lean-Six-Sigma-to-Improve-Service (accessed Feb. 24, 2023). [4] I. web studio, Six Sigma, qcc.ge. [Online]. Available: http://qcc.geen/insight/34. http://qcc.geen/insight/34 (accessed Feb. 24, 2023). [5] F. R. Lima Junior, L. Osiro, and L. C. R. Carpinetti, A comparison between Fuzzy AHP and Fuzzy TOPSIS methods to supplier selection, Appl. Soft Comput., vol. 21, pp. 194209, Aug. 2014, doi: 10.1016/j.asoc.2014.03.014. [6] I. Beg and T. Rashid, Modelling Uncertainties in Multi-Criteria Decision Making using Distance Measure and TOPSIS for Hesitant Fuzzy Sets, J. Artif. Intell. Soft Comput. Res., vol. 7, pp. 103109, Apr. 2017, doi: 10.1515/jaiscr-2017-0007. [7] R. M. Zulqarnain, M. Saeed, N. Ahmad, F. Dayan, and B. Ahmad, Application of TOPSIS Method for Decision Making, vol. 7, pp. 7681, Apr. 2020. [8] (PDF) Implementation of TOPSIS Method for Multi Criteria Decision Making of Supplier Selection. https://www.researchgate.net/publication/343657614_Implementatio n_of_TOPSIS_Method_for_Multi_Criteria_Decision_Making_of_S upplier_Selection (accessed Feb. 24, 2023). [9] S. Corrente and M. Tasiou, A robust TOPSIS method for decision making problems with hierarchical and non-monotonic criteria, Expert Syst. Appl., vol. 214, p. 119045, Mar. 2023, doi: 10.1016/j.eswa.2022.119045. [10] M. Hanine, O. Boutkhoum, A. Tikniouine, and T. Agouti, Application of an integrated multi-criteria decision making AHP- TOPSIS methodology for ETL software selection, SpringerPlus, vol. 5, no. 1, Art. no. 1, Dec. 2016, doi: 10.1186/s40064-016-1888-z.
[11] A. Kolios, V. Mytilinou, E. Lozano-Minguez, and K. Salonitis, A Comparative Study of Multiple-Criteria Decision-Making Methods under Stochastic Inputs, Energies, vol. 9, no. 7, Art. no. 7, Jul. 2016, doi: 10.3390/en9070566. [12] M. Kalita and G. I. Hussain, Opportunities and Challenges of Electric Vehicles in India, Int. J. Eng. Res. Technol., vol. 9, no. 11, Jul. 2021, doi: 10.17577/IJERTCONV9IS11033. [13] Siemens Smart Expert Partner of NX CAD Design, Manufacturing Simulation and Industry 4.0 Software. https://www.ddsplm.com/ (accessed Feb. 24, 2023). [14] Deploying Lean Six Sigma framework in an automotive component manufacturing organization | Emerald Insight. https://www.emerald.com/insight/content/doi/10.1108/IJLSS-06- 2015-0023/full/html (accessed Feb. 24, 2023). [15] Assembling Electric Vehicle Motors | 2021-05-20 | ASSEMBLY. https://www.assemblymag.com/articles/96393-assembling-electric- vehicle-motors (accessed Feb. 24, 2023). [16] M. Kumar, J. Antony, R. K. Singh, M. K. Tiwari, and D. Perry, Implementing the Lean Sigma framework in an Indian SME: a case study, Prod. Plan. Control, vol. 17, no. 4, pp. 407423, Jun. 2006, doi: 10.1080/09537280500483350. [17] R. Bisschop, O. Willstrand, and M. Rosengren, Handling Lithium- Ion Batteries in Electric Vehicles: Preventing and Recovering from Hazardous Events, Fire Technol., vol. 56, no. 6, pp. 26712694, Nov. 2020, doi: 10.1007/s10694-020-01038-1. [18] M. Slattery, J. Dunn, and A. Kendall, Transportation of electric vehicle lithium-ion batteries at end-of-life: A literature review, Resour. Conserv. Recycl., vol. 174, p. 105755, Nov. 2021, doi: 10.1016/j.resconrec.2021.105755. [19] Policies to promote electric vehicle deployment Global EV Outlook 2021 Analysis, IEA. https://www.iea.org/reports/global- ev-outlook-2021/policies-to-promote-electric-vehicle-deployment (accessed Apr. 06, 2023). [20] A. Sharma, P. Zanotti, and L. P. Musunur, Robotic Automation for Electric Vehicle Battery Assembly: Digital Factory Design and Simulation for the Electric Future of Mobility.. [21] J. A. Sanguesa, V. Torres-Sanz, P. Garrido, F. J. Martinez, and J. M. Marquez-Barja, A Review on Electric Vehicles: Technologies and Challenges, Smart Cities, vol. 4, no. 1, pp. 372404, Mar. 2021, doi: 10.3390/smartcities4010022. [22] S. Arora, A. Kapoor, and W. Shen, Application of Robust Design Methodology to Battery Packs for Electric Vehicles: Identification of Critical Technical Requirements for Modular Architecture, Batteries, vol. 4, no. 3, p. 30, Jul. 2018, doi: 10.3390/batteries4030030. [23] PRODUCTIVITY IMPROVEMENT OF A MANUAL ASSEMBLY LINE.pdf. [24] S. Arora and A. Kapoor, Mechanical Design and Packaging of Battery Packs for Electric Vehicles, in Behaviour of Lithium-Ion Batteries in Electric Vehicles, G. Pistoia and B. Liaw, Eds., in Green Energy and Technology. Cham: Springer International Publishing, 2018, pp. 175200. doi: 10.1007/978-3-319-69950-9_8. [25] E. Popp, 3D Smart Sensors for Inline EV Battery Inspection, Nov. 18, 2022. https://lmi3d.com/blog/smart-3d-laser-profiling-for-inline-ev-battery-inspection/ (accessed Apr. 06, 2023).
[26] Adantages and Disadvantages of Assembly Line Manufacturing.pdf. [27] R. DSouza, J. Patsavellas, and K. Salonitis, Automated assembly of Li-ion vehicle batteries: A feasibility study, Procedia CIRP, vol. 93, pp. 131136, 2020, doi: 10.1016/j.procir.2020.04.111. [28] Lithium-ion battery demand forecast for 2030|McKinsey.https://www.mckinsey.com/industries/automotive-and- assembly/our-insights/battery-2030-resilient-sustainable-and- circular#/ (accessed Mar. 24, 2023).
[29] From ICE to EV How EV Manufacturing is Changing the Game, STANLEY® Engineered Fastening. https://www.stanleyengineeredfastening.com:443/en/News-and- Stories/From-ICE-to-EV-How-EV-Manufacturing-is-Changing-the- Game (accessed Mar. 24, 2023). [30] Automated battery manufacturing, E-Mobility Engineering, Nov. 09, 2022. https://www.emobility-engineering.com/automated-battery-manufacturing/ (accessed Mar. 21, 2023).
[31] A. Beck, Challenges of Changing Battery Suppliers on an Existing Design. https://blog.epectec.com/challenges-of-changing-battery- suppliers-on-an-existing-design (accessed Mar. 24, 2023). [32] Improving BEV market profitability through reduced structural costs | McKinsey. https://www.mckinsey.com/industries/automotive-and- assembly/our-insights/improving-battery-electric-vehicle- profitability-through-reduced-structural-costs (accessed Mar. 24, 2023). [33] J. C. and L. Ice, Charging into the future: the transition to electric vehicles: Beyond the Numbers: U.S. Bureau of Labor Statistics. https://www.bls.gov/opub/btn/volume-12/charging-into-the-future- the-transition-to-electric-vehicles.htm (accessed Mar. 24, 2023). [34] E. Ayerbe, M. Berecibar, S. Clark, A. A. Franco, and J. Ruhland, Digitalization of Battery Manufacturing: Current Status, Challenges, and Opportunities, Adv. Energy Mater., vol. 12, no. 17, p. 2102696, 2022, doi: 10.1002/aenm.202102696. [35] A. Masias, J. Marcicki, and W. A. Paxton, Opportunities and Challenges of Lithium Ion Batteries in Automotive Applications, ACS Energy Lett., vol. 6, no. 2, pp. 621630, Feb. 2021, doi: 10.1021/acsenergylett.0c02584. [36] Testing Electric Vehicle Components | 2021-09-21 | ASSEMBLY. https://www.assemblymag.com/articles/96623- testing-electric-vehicle-components (accessed Apr. 06, 2023). [37] J. Cao, X. Chen, R. Qiu, and S. Hou, Electric vehicle industry sustainable development with a stakeholder engagement system, Technol. Soc., vol. 67, p. 101771, Nov. 2021, doi: 10.1016/j.techsoc.2021.101771. [38] The challenges of a transition from ICE to EV production for automotive manufacturers and the implications for assembly plants | Article | Automotive Manufacturing Solutions. https://www.automotivemanufacturingsolutions.com/voice/the- challenges-of-a-transition-from-ice-to-ev-production-for- automotive-manufacturers-and-the-implications-for-assembly- plants/41723.article (accessed Feb. 24, 2023). [39] Trends and developments in electric vehicle markets Global EV Outlook 2021 Analysis, IEA. https://www.iea.org/reports/global- ev-outlook-2021/trends-and-developments-in-electric-vehicle- markets (accessed Mar. 24, 2023). [40] Electric vehicle makers rethink assembly processes | 2019-11-06 | ASSEMBLY. https://www.assemblymag.com/articles/95294- electric-vehicle-makers-rethink-assembly-processes (accessed Mar. 21, 2023). [41] M. Griffin, The future of work in the automotive industry: The need to invest in peoples capabilities and decent and sustainable work. [42] Electric Vehicles Should Be a Win for American Workers, Center for American Progress, Sep. 23, 2020. https://www.americanprogress.org/article/electric-vehicles-win- american-workers/ (accessed Mar. 24, 2023). [43] S. Z. Rajper and J. Albrecht, Prospects of Electric Vehicles in the Developing Countries: A Literature Review, Sustainability, vol. 12, no. 5, Art. no. 5, Jan. 2020, doi: 10.3390/su12051906. [44] R. Bohnsack, J. Pinkse, and A. Kolk, Business models for sustainable technologies: Exploring business model evolution in the case of electric vehicles, Res. Policy, vol. 43, no. 2, pp. 284300, Mar. 2014, doi: 10.1016/j.respol.2013.10.014. [45] R. S. Schuler and S. E. Jackson, Linking Competitive Strategies with Human Resource Management Practices, Acad. Manag. Perspect., vol. 1, no. 3, pp. 207219, Aug. 1987, doi: 10.5465/ame.1987.4275740.