
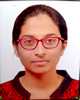
- Open Access
- Authors : Pallavi R. Sakharkar , Dr. Milind S. Yadav , Dr. Supriya N. Bobade
- Paper ID : IJERTV10IS030264
- Volume & Issue : Volume 10, Issue 03 (March 2021)
- Published (First Online): 03-04-2021
- ISSN (Online) : 2278-0181
- Publisher Name : IJERT
- License:
This work is licensed under a Creative Commons Attribution 4.0 International License
Vibration Analysis of Twin Cylinder Diesel Engine Fueled with Blends of Cottonseed Oil in Comparision with Diesel at Fixed Compression Ratio and Injection Time
Pallavi R. Sakharkar1
Mechanical Engineering
Finolex Academy of Management and Technology, Ratnagiri, India
Dr. Milind S. Yadav2
Associate Professor
Finolex Academy of Management and Technology Ratnagiri, India
Dr. Supriya N. Bobade3
Research head
Indian biodiesel corporation, Baramati
Abstract:- Diesel engine is critical equipment because its failure has high consequences on cost. Engine body vibration signals are rich in information about its operating parameters and physical condition. Due to the shortage of conventional fossil fuels there is need to use alternative environment friendly biodiesel blends like cottonseed oil blends. This paper represents comparative study of vibration signals of cylinder head of diesel engine for pure diesel and blends of cottonseed oil B5, B10, B15 and B20 respectively by studying effects on statistical parameters like kurtosis, skewness, RSM, crest factor and peak amplitude. Using LabVIEW setup vibration signals are collected through data acquisition system by attaching accelerometer on cylinder head of internal combustion engine. This experimentation was done on no load condition as well as on 3 to 12 kg loading condition in steps of 3 in three different direction for cylinder head. After experimentation it is observed that blend B20 shows maximum reduction of 24.94 % at no load condition for average kurtosis value which means reduction in peackedness of signal. Kurtosis seems to be more sensitive to change of fuel blends. Significant drop in crest factor has been recorded for almost all blends. Maximum reduction in average crest value has been recorded for Blend B20 at 3kg loading condition which is 55.13%. Blend B20 recorded highest drop of average peak amplitude of vibration signals which is 58.1% at 9kg loading condition. Blend B20 gives effective reduction in vibration signals.
Keywords Cottonseed oil, vibration, internal combustion engine, kurtosis, skewness. RSM. Crest factor, peak amplitude, accelerometer, lab VIEW Introduction (HEADING 1)
-
INTRODUCTION
Internal combustion engine find wide spread automobile and industrial application. In automobile and industrial application internal combustion engine is considered as critical mechanical component. Engine knocking is unfavorable engine operating condition which causes vibrations [1]. According to Uludamar E, Tuccar G, Aydin K, Ozcanli M [2], engine can generate forces at different frequencies and cause passenger discomfort. The defect and vibration in internal combustion engine, unless detected in
time, will cause malfunctioning and may lead to catastrophic failure of the machine or system [3]. Emissions from diesel engine seriously threatened the environment and are considered one of the major sources of air pollution [4]. Regarding the reduction in exhaust emission and vibration signals study has been done by Abdulkadir Yasar, Ali Kekin, Erinc Uludamar[5], by adding metallic based nanoparticles in diesel fuel, where significant reduction in NOx emission and decreased in sound pressure level of engine block has been seen. Zhi Cho Ong, Mohd Bakar Mohd Mishani, Wen Tong Chong [6] studied the advanced vibration analysis techniques like time domain, frequency domain and motion visualization analysis to identify an optimum fuel blend with minimum engine vibration. It has been seen that commonly used fuels such as petrol and diesel have definite energy values, there is increase in demand of energy and rapidly depletion of fossil fuels brings interest to derive alternative fuel from renewable resources [7, 8]. Pankaj Shelke, Nitin M. Sakhare, Subhash Lahane [8] stated that among all the different alternative fuels vegetable oil has potential to substitute traditional diesel fuels. The concept of using vegetable oil as fuel dates back to 1895 [9]. The cottonseed crop is fast growing plant and even sustain in drought and poor soil [8]. According to the Md. Nurun Nabi, Md Mustafizur Rahman, Md. Shamin Akhter [10], Transesterification is a process which is suitable to produce biodiesel as it has good potential to reduce engine problems associated with vegetable oil. Also from the study done by T. Eevera and K. Pazhanichamy [11] it is concluded that, cottonseed oil biodiesel blends can be mixed very well with diesel and can be used in diesel engine without any modification. The study of effect of cottonseed oil biodiesel blends on engine performance and exhaust emission is already done by Md. Nurun Nabi, Md Mustafizur Rahman, Md. Shamin Akhter [10.] and satisfactory reduction in exhaust emission and engine performance has been seen. Duple Sinha, S, Murugavelh [12], also concluded that use of cotton seed oil biodiesel blends showed reduction in exhaust emission of carbon monoxide and hydrocarbon. The vibration analysis of diesel engine is done by Milind Yadav, Suresh M.
Sawant [13.] by studying the changes in the behavior of statistical parameters like skewness, kurtosis, crest factor, RSM value and peak amplitude. With reference to above information it would be interesting to study effect of addition of cottonseed oil biodiesel in diesel on the vibrations of internal combustion engine by observing changes in statistical parameters.
-
MATERIAL AND METHOD
-
Fuel preparation:
Biodiesel fuel was produced by using transesterification process from cotton seed oil. Transesterification is the process which is used to obtain biodiesel from vegetable oil or animal fat subjected to chemical reaction in the presence of a catalyst. It is a reversible reaction and carried out by mixing reactant- fatty acid, alcohol and catalyst. Basically biodiesel is the mono-alkly-esters of long chain fatty acids such as vegetable oil or animal fat for using in compression ignition engine [10]. The filtered cottonseed oil is heated up to desired temperature and catalyst and alcohol solution is added to it. After the preset reaction time the stirring and heating is stop. After the overnight settling of this mixture we obtain two distinct layers of crude ester phase at the top which is washed by de-ionized water and bottom glycerol phase respectively [11]. The chemical reaction is as follow-
Fig .1 Transesterification process [23]
After getting cottonseed oil biodiesel from transesterification process, this biodiesel is mixed with conventional diesel fuel on volume basis to get blends B5 (5% cottonseed oil biodiesel & 95% diesel ), B10 (10% cottonseed oil biodiesel & 90% diesel), B15 (15% cottonseed oil biodiesel & 85% diesel) and B20 (20% cottonseed oil biodiesel & 80% diesel) respectively.
Table 1: Properties of fuel
Sr. No.
Test Description
Ref. Std. ASTM6751
Reference
Diesel
Cottonseed oil biodiesel blends
Unit
Limit
B00%
B05%
B10%
B15%
B20%
1
Density
D1448
gm/cc
0.800-0.900
0.830
0.831
0.833
0.835
0.838
2
Calorific Value
D6751
MJ/Kg
34-45
42.50
42.46
42.41
42.0
42.18
3
Cetane No.
D613
–
41-55
49.00
49.09
49.22
49.31
49.40
4
Viscosity
D445
Mm2/sec
3-6
2.700
2.79
2.88
2.90
2.94
5
Moisture
D2709
%
0.05%
NA
NA
NA
NA
NA
6
Flash Point
D93
o C
–
64
79
88
92
103
7
Fire Point
D93
o C
–
71
91
99
99
111
-
Engine test set up and methodology:
(b)
Fig.2 (a) Experimental test setup and (b) position of accelerometer on cylinder head
(a)
Table 2: Engine specifications
Make
Comet
Type
Twin cylinder, four stroke compression ignition engine
Stroke
110 mm
Bore
87.5 mm
Compression ratio
18:1
Rated output
9.7 kw (13 HP)
Rated speed
1600 rpm
Dynamometer
Water brake dynamometer
Fig. 3: Block diagram for signal extraction and analysis using Lab VIEW
For the experimentation the piezoelectric accelerometer is used which is mounted on cylinder head of diesel engine. Vibrations are recorded for three different directions X, Y and Z respectively with the use of Lab VIEW setup. By varying load form 0 to 12kg in the steps of 3 the vibration analysis is done for no blend condition and then for blends B5, B10 B15 and B20 respectively.
-
-
RESULT AND DISCUSSION:
-
Effect of cottonseed oil blend on kurtosis of vibration signals
The normalized fourth moment, kurtosis, is the ratio of the fourth moment to the square of the second moment (commonly known as variance).It is the indication of the degree of flatness or peakedness of the distribution. High Kurtosis indicates a peaked distribution and low kurtosis indicates flat distribution near the mean value. There are three types of distribution- leptokurtic, platykurtic and mesokurtic. Normal distribution posses kurtosis value equal to 3 and the one with more than three is called leptokurtic. Platykurtic has value less than 3 and mesokurtic possess value equal to 3. Higher kurtosis value shows irregular engine
performance [18]. Mathematically kurtosis is defined as the ratio of fourth moment to the square of variance [17]
Kurtosis=
-
Comparison of average values of kurtosis for different loading condition for no blend with blends of cottonseed oil biodiesel for x-direction is as follow-
Fig.4 : Recorded average Kurtosis of acceleration signals from cylinder head in X-direction
The above graphs shows recorded average kurtosis value of acceleration signals from cylinder head in x-direction with respect to various blends of diesel and cottonseed oil biodiesel for different loading conditions. The recorded average kurtosis values shows leptokurtic nature. The above graph shows reduction in kurtosis value for every loading condition and for every blends as compre to pure diesel. Blend B20 shows maximum reduction of 24.94 % at no load condition which means reduction in peackedness of signal. As blend B20 posses maximum cetane number among all the fuel, which is 49.90, it causes reduction in probablity of generation of periodic impulse with large amplitudes in cylinder head.
-
Comparison of average values of kurtosis for different loading condition for no blend with blends of cottonseed oil biodiesel for Y-direction is as follow-
Fig.5 : Recorded average Kurtosis of acceleration signals from cylinder head in Y-direction
The above graph shows increase in the average kurtosis value for blend B5 at every loading condition as compare to pure diesel. Blend B10 shows maximum reduction in kurtosis value as compare to other fuels, at 9kg loading condition the reduction is of 53.40%. As calorific value of B15 blend is higher than B20 blend, B15 blend shows rise in average values of kurtosis. At 12 kg load rise of 9.12% is recorded for B15 blend as compare to pure diesel. For 12kg load reduction of 14.83% in value of kurtosis for blend B20 has been recorded.
-
Comparison of average values of kurtosis for different loading condition for no blend with blends of cottonseed oil biodiesel for Z-direction is as follow-
Fig.6 : Recorded average Kurtosis of acceleration signals from cylinder head in Z-direction
Above graph shows maximum reduction of kurtosis value for blend B20, for 9 kg load there is 18.06% drop of average kurtosis value. Blend B5 shows maximum kurtosis value for all loading conditions, highest value is recorded at no load condition. Blend B5 posse minimum cetane number, which is 49.09, than other biodiesel blends which refers to higher ignition delay. Blend B10 shows 10.15% reduction of average kurtosis value at 12kg load as compare to pure diesel.
-
-
Effect of cottonseed oil blend on skewness of vibration signals
Skewness is a indicator used in distribution analysis as a sign of asymmetry and deviation from normal distribution.
Mathematically skewness is defined as the ratio of averaged cubed deviation from mean and cube of standard deviation [17]
Skewness =
It is the cube of deviation from arithmetic mean, N is the number of observations and is the standard deviation. Skewness is dimensionless number and ideally has a zero value [13].
-
Comparison of average values of skewness for different loading condition for no blend with blends of cottonseed oil biodiesel for X-direction is as follow-
Fig.7 : Recorded average Skewness of acceleration signals from cylinder head in X-direction
Fig. shows variation in average skewness value of acceleration signals from cylinder head for variour blends of cottonseed oil biodiesel and pure diesel in X-direction at different loading conditions . For blend B15 the distribution is negatively skewed. For no load condition the average skewness value for B5 blend is increased by 28.80% and then again reduction in average skewness values of other blends is seen as compared to no blend condition. for blend B20 the average skewness value approaches to zero with drop of 49.41% with respect to pure diesel.
-
Comparison of average values of skewness for different loading condition for no blend with blends of cottonseed oil biodiesel for Y-direction is as follow-
Fig.8 : Recorded average Skewness of acceleration signals from cylinder head in Y-direction
Fig. shows distribution of average skewness of acceleration signals from cylinder head with respect to various blends at different loading conditions for Y-direction of cylinder head. For no load condition there is drop of average skewness value for every blend as compare to no blend condition. Blend B15 shows negatively skewed distribution for every loading condition. At 9kg load blend B5 shows maximum drop of 86.79%. At every loading condition the average skewness valus for blend B20 suddenly rises but still reamain less than no blend condition.
-
Comparison of average values of skewness for different loading condition for no blend with blends of cottonseed oil biodiesel for Z-direction is as follow-
Fig.9 : Recorded average Skewness o acceleration signals from cylinder head in Z-direction
Fig. shows variation in average skewness value of acceleration signals from cylinder head for various blends of cottonseed oil biodiesel and pure diesel in Z-direction at different loading conditions. For every loading condition blend B5 shows sudden rise in average skewness value. Then reduction in values is recorded for blend B10 and blend B15. For blend B20 at 6kg loading condition drop of 56.52% is recorded. Blend B20 recorded average skewness values which approaches to zero.
-
-
Effect of cottonseed oil blend on RMS value of vibration signals-
The RMS (root mean square) value of the vibration acceleration can be used for the primary health investigation of the machine. The RMS of variant X is the square root of the mean squared value of x. It is a powerful tool to estimate the average power of a discrete signal and is proportional to area under the envelope waveform of discrete signal [13].
With increase in RMS value vibrations increases [18]. Therefore, in vibration RMS is a suitable parameter to evaluate the vibration of internal combustion engine.
RMS=
-
Comparison of average values of RMS value for different loading condition for no blend with blends of cottonseed oil biodiesel for X-direction is as follow-
Fig.10 : Recorded average RMS of acceleration signals from cylinder head in X-direction
Fig. shows comparison of average RMS value of acceleration signals from cylinder head for various blends of cottonseed oil biodiesel with pure diesel in X-direction at different loading conditions. From figures it is seen that there is drop of RMS values for every loading condition for all the blends as compare to no blend condition. This reduction in RMS value reduces the power from vibration signals of cylinder head. Maximum power drop of vibration signal is observed for blend B20 at loading condition of 9kg which is of 70.39%. As B20 posse maximum cetane number 49.40 it results in reduction of ignition delay which results in reduction in rate of pressure rise.
-
Comparison of average values of RMS value for different loading condition for no blend with blends of cottonseed oil biodiesel for Y-direction is as follow-
Fig.11 : Recorded average RMS of acceleration signals from cylinder head in Y-direction
Fig. shows comparison of average RMS value of acceleration signals from cylinder head for various blends of cottonseed oil biodiesel with pure diesel in Y-direction at different loading conditions. RMS value indicates energy of vibration signal. Maximum RMS value will result in maximum vibration signals. By observing all the above figures it is clearly understood that RMS value for every blend reduces as compare to no blend condition. RMS value for blend B5 rises from no load condition to 12kg loading condition but still it remains lesser than no blend condition. For blend B10 at 9kg loading condition maximum drop of 26.92% as compared to no blending condition is observed.
-
Comparison of average values of RMS value for different loading condition for no blend with blends of cottonseed oil biodiesel for Z-direction is as follow-
Fig.12 : Recorded average RMS of acceleration signals from cylinder head in Z-direction
Fig. shows comparison of average RMS value of acceleration signals from cylinder head for various blends of cottonseed oil biodiesel with pure diesel in Z-direction at different loading conditions. Like X and Y-direction, in Z-direction also there is reduction in values of RMS of all the blends for every loading condition as compare to no blend condition. Maximum reduction of RMS value is seen for blend B10 at 3kg loading condition which is of 39.73 %. For blend B20 at 12kg loading condition drop of RMS value is of 29.07%.
-
-
Effect of cottonseed oil blend on crest factor of vibration signals-
Crest factor of vibration signal is often used to indicate difference in vibration. However the RMS level may not show appreciable changes in the vibration signal. A better measure is to use crest factor which is defined as ratio of the peak level of the vibration signal to the RMS level. Therefore peak in the time series signal will result in an increase in the crest factor value. Crest factor gives a quick idea about how much impacting is occurring in waveform [13]. Higher value of crest factor indicates strong impacting [19].
Crest factor =
-
Comparison of average values of crest factor for different loading condition for no blend with blends of cottonseed oil biodiesel For X-direction is as follow-
Fig.13 : Recorded average Crest Factor of acceleration signals from cylinder head in X-direction
Fig. shows comparision of average crest factor value of acceleration signals from cylinder head for variour blends of cottonseed oil biodiesel with pure diesel in X-direction at different loading conditions. From the above figure it is clear that the crest facor is much higher than ideal value 1.4144. Which results in strong impacting of vibration signals from cylinder head. Recorded values of crest value indicates that addition of cottonseed oil biodiesel in pure diesel reduces the impacting of vibration signals for all loading conditions, as blends reduces the average crest factor values. Maximum reduction in average crest value is redcorded for Blend B20 at 3kg loading condition which is 55.13%. As calorific values of blends are less than pure diesel, reduction in peak pressure is occured which significantly results in reduction of impacting of vibration signals.
-
Comparison of average values of crest factor for different loading condition for no blend with blends of cottonseed oil biodiesel For Y-direction is as follow-
Fig.14 : Recorded average Crest Factor of acceleration signals from cylinder head in Y-direction
Fig. shows comparison of average crest factor value of acceleration signals from cylinder head for various blends of cottonseed oil biodiesel with pure diesel in Y-direction at different loading conditions. Above figures shows reduction in crest factor for all loading condition. 42.32% maximum drop in average crest factor is recorded for blend B20 at 9kg loading condition. Blend B10 shows minimum reduction of 17.93% at no load condition as compare to other fuels. Blend B20 has maximum cetane number which assure smooth running of engine and less RMS value means less impacting of vibration signals.
-
Comparison of average values of crest factor for different loading condition for no blend with blends of cottonseed oil biodiesel for Z-direction is as follow-
Fig.15 : Recorded average Crest Factor of acceleration signals from cylinder head in Z-direction
Fig. shows comparison of average crest factor value of acceleration signals from cylinder head for various blends of cottonseed oil biodiesel with pure diesel in Y-direction at different loading conditions. Reduction in RMS value is recorded for al loading condition as compare to pure diesel. That means Cottonseed oil biodiesel blend reduces the impacting of vibration signals. For no load condition the reduction in crest factor of blend B10 is recorded of 16.01%. Blend B15 recorded maximum reduction in crest value at 9kg load which is 22.37%. At 12kg loading condition drop in crest value for blend B20 is 19.06%. Like X and Y-direction of cylinder head, in Z-direction also drop in values of average crest factor is observed.
-
-
Effect of cottonseed oil blend on peak amplitude of vibration signals
Fourier analysis breaks up a signal into sine waves of different frequencies and phases. This transform is used for frequency domain analysis. The information regarding the vibration signals in IC engine can be obtained with the help of FFT. The abnormal working of sydtrm is recognized by sudden peak in the frequency spectrum than normal behavior. The amplitude obtained in the frequency spectrum of the system using FFT is nothing but the amplitude of vibration and it is used for analysis.
-
Comparison of average values of peak amplitude for different loading condition for no blend with blends of cottonseed oil biodiesel for X-direction is as follow-
Fig.16 : Recorded average Peak Amplitude of acceleration signals from cylinder head in X-direction
Fig. shows variation in average peak amplitude of acceleration signals from cylinder head for various blends of cottonseed oil biodiesel and pure diesel in X-direction at different loading conditions. These figure shows that there is definite reduction in amplitude of vibration signals from cylinder head. Cottonseed oil biodiesel blends shows reduction in average peak amplitude for every loading condition as compare to non-blending condition. Blend B5 shows reduction in average peak amplitude up to 6kg loading condition and then again rise in values is recorded for 9kg and 12kg loading condition. But still this rise is less than the values of average peak amplitude of non-blending condition. Blend B20 recorded highest drop of 58.1% at 9kg loading condition. As blend B20 has least calorific value it assures less peak pressure inside the cylinder of diesel engine which results in highest drop in average peak amplitude of vibration signal.
-
Comparison of average values of peak amplitude for different loading condition for no blend with blends of cottonseed oil biodiesel for Y-direction is as follow-
Fig.17 : Recorded average Peak Amplitude of acceleration signals from cylinder head in Y-direction
Fig. shows variation in average peak amplitude of acceleration signals from cylinder head for various blends of cottonseed oil biodiesel and pure diesel in y-direction at different loading conditions. Recorded values of average peak amplitude for cottonseed oil biodiesel blend shows reduction in values as compare to pure diesel. 63.80% is the highest drop of average peak amplitude is recorded for Blend B20 at 09kg loading condition. For every loading condition drop of values is observed for blend B05, B10, B15 and blend B20 as compared to pure diesel. Which results in reduction in amplitude of variation signals. Blend B20 shows highest reduction in average peak amplitude because it posse highest cetane number 49.40 which results in reduction in ignition delay and ultimately gives smooth running of engine
-
Comparison of average values of peak amplitude for different loading condition for no blend with blends of cottonseed oil biodiesel for Z-direction is as follow-
Fig.18 : Recorded average Peak Amplitude of acceleration signals from cylinder head in Z-direction
Fig. shows variation in average peak amplitude of acceleration signals from cylinder head for various blends of cottonseed oil biodiesel and pure diesel in Z-direction at different loading conditions. As compare to all loading condition for blend B5 highest drop of average peak amplitude is 62.91% at no load condition as compare to no blend condition. At 12 kg loading condition highest drop of 71.75% is observed for blend B20. Blend B20 shows highest drop in amplitude of vibration signal as it has lowest calorific value 42.18MJ/kg which gives less peak pressure inside the cylinder head of internal combustion engine.
-
-
CONCLUSION
Following conclusions can be drawn from the analysis:
-
As blending of cottonseed oil with diesel increases the reduction in vibration signals as compare to pure diesel has been recorded
-
Blend B20 shows maximum reduction of 24.94 % at no load condition for average kurtosis value which means reduction in peackedness of signal. Kurtosis seems to be more sensitive to change of fuel blends.
-
For blend B20 at 6kg loading condition in Z-direction of cylinder head drop of 56.52% in average skewness value is recorded.
-
RMS values of recorded vibration signals did not get significantly affected by blending of cottonseed oil biodiesel with pure diesel.
-
Significant drop in crest factor has been recorded for almost all blends. Maximum reduction in average crest value has been recorded for Blend B20 at 3kg loading condition which is 55.13%.
-
Blend B20 recorded highest drop of average peak amplitude of vibration signals which is 58.1% at 9kg loading condition. As blend B20 has least calorific value it assures less peak pressure inside the cylinder of diesel engine which results in highest drop in average peak amplitude of vibration signal.
Overall it is observed that addition of cottonseed oil biodiesel blends in pure diesel reduces the vibration signal from cylinder head of diesel engine. Blend B20 gives effective reduction in vibration signals.
-
-
REFERENCES
-
Bergthorson JM, Thomson MJ, (2015), A Review of the Combustion and Emissions Properties of Advanced Transportation Biofuels and their Impact on Existing and Future Engine, Renewable and Sustainable Energy Reviews, 42, 1393-1417.
-
Uludamar E, Tuccar G, Aydin K, Ozcanli M, (2016), Vibration Analysis of Diesel Engine Fuelled with Sunflower and Canola Biodiesel, Adv Automo Enf, 137, 2167-7670
-
Taghizadeh-Alisaraei A, Ghobadian B T, Tavakoli-Hashjin S M (2012), Vibration analysis of a diesel engine using biodiesel and petrodiesel fuel blends, Fuel, 102, pp. 414422.
-
Rao PV & Rao B V (2011), Performance Emission and Cylinder Vibration studies of DI-Diesel Engine with COME – Triacetin Additive Blends, International Journal of Thermal technologies, 1, pp. 100-109.
-
Abdulkadir Yasar, Ali Kekin, Erinc Uludamar (2019),Emission and vibration analysis of diesel engine fuelled diesel fuel containing metallic based nanoparticles, Fuel, 239, pp. 1224-1230.
-
Zhi Cho Ong, Mohd Bakar Mohd Mishani, Wen Tong Chong(2017), Identification of optimum Calophyllum inophyllum bio-fuel blend in diesel engine using advance vibration analysis technique, Renewable energy,109,295-304.
-
Talebian-Kiakalaieh A, Amin NAS, Mazaheri H, (2013), A Review on Novel Processes of Biodiesel Production from Waste Cooking Oil. Applies Energy, 104, 683-710
-
Pankaj Shelke, Nitin M. Sakhare, Subhash Lahane (2016), Investigation of Combustion Characteristic of a Cottonseed Biodiesel Fuelled Diesel Engine, Elsevier Ltd, Procedia Technology 25, pp. 1049-1055.
-
A Murugesan, C, Umarani, R. Subramanian, N. Nedunchezhian (2009), Bio-diesel a an alternative fuel for diesel engines- A review, Renewable and Sustainable Energy Reviews 13, pp. 653- 662.
-
Md. Nurun Nabi, Md Mustafizur Rahman, Md. Shamin Akhter (2009), Biodiesel from cotton seed oil and its effect on engine performance and exhaust emissions, Applied Thermal Engineering 29, pp. 2265-2270.
-
T. Eevera and K. Pazhanichamy (2015), Cotton Seed oil: A Feasible Oil Source for Biodiesel Production, Taylor and Francis Group.LLC, ISSN: 1556-7036, pp. 1118-1128.
-
Duple Sinha, S, Murugavelh (2016), Biodiesel production from waste cotton seed oil using low cost catalyst: Engine performance and emission characteristics, Perspective in Science 8, pp.237-240.
-
Milind Yadav, Suresh M. Sawant (2018), Analysis of Vibration Signals from Cylinder Head of a Diesel Engine Fueled with Blends of Diesel and Oxy-Hydrogen Gas, International Journal for Research in Applied Science and Engineering Technology (IJRAET) vol. 6, issue 3, ISSN: 2321-9653, pp. 33-41.
-
Shaikh M F and Sudhakar U (2014), Noise and Vibration Analysis of Diesel Engine Using Diesel and Jatropha Biodiesel, International Journal of Engineering Trends and Technology, 12(5), pp. 228-231.
-
Sastry GRK, Kumar INN, Prasad SC and Rao BVA (2005), Comparative Performance Study of MAHUA METHYL ESTER as Diesel Fuel Substitute on DI Diesel Engine with Emphasis on
Vibration & Noise as Potential Engine Parameters, Power and energy systems (PES), Marina del Rey USA ISSN: 1482-7891, pp 492-036.
-
Asif A H & Suryakumari TSA (2016), Vibration Analysis of two Cylinder Diesel engine using Biodiesel Blends, Journal of Chemical and Pharmaceutical Sciences, ISSN: 0974-2115, pp. 355- 359.
-
Gupta SP (1997), Statistical Method, 28th edition, S Chand publications, pp. E-914 E-925.
-
Taghizadeh-Alisaraei A & Rezaei-Asl A (2016), The effect of added ethanol to diesel fuel on performance vibration combustion and knocking of a CI engine, Fuel, 185, pp. 718-733
-
Nortan MP and Karczub DG (2003), Fundamental of noise and vibration analysis for engineers, Second edition, Cambridge University press, pp. 496.
-
Dipak Pawar (2017), Vibration Studies of Defective and Non Defective Deep Groove Ball Bearing Using FFT Analyzer International Journal for Science and Advance Research in Technology (IJART) vol-3, issue 10, ISSN: 2395-1052.
-
Sarthak Nag, Priybrat Sharma, Arpan Gupta, Atul Dhar (2019), Combustion, vibration and noise analysis of hydrogen-diesel dual fuelled engine, Fuel, 241, pp. 488-494.
-
Hariram Venkatean, Godwin John and Seralathan Sivamani (2017), Cotton Seed Biodiesel as Alternative fuel: Production and its Characterization Analysis using Spectroscopic Studies, International Journal of Renewable Energy Research, vol. 7, No. 3, pp. 1333-1339.
-
Sandeep Singh, Sumeet Sharma and S.K. Mohapatra (2015), A production of biodiesel from waste cotton seed oil and testing on small capacity diesel engine, International Journal of Advance Research in Science and Engineering (IJARSE), vol. no. 4, ISSN: 2319-8354, pp. 172-178.
-
Supriya Chavan, Reena Singh, Meena Yadav and Veena Singh (2017), Production of biodiesel from three indigenous feedstock: Optimization of process parameters and assessment of various fuel properties, Environmental Progress & Sustainable Energy (Vol.00, No.00) DOI 10.1002/ep.
-
Chavan Supriya Baburao, R. Rohith Renish, Shinde Chandrakant Anna and Kumbhar Rajendra Rayappa (2015), Application of an Ecofriendly Heterogeneous Catalyst (CaO) for Synthrses of Biodiesel and its Characterization on VCR Engine, International Review of Mechanical Engineering, Vol. 9, N. 3 ISSN 1970-8734.
-
Santosh kumar Dash, Pradip Lingfa & Supriya B. Chavan, An experimental investigation on the application potential of heterogeneous catalyzed Nahar biodiesel and its diesel blends as diesel engine fuels (2018), Energy Sources, Part A: Recovery, Utilization, and Environmental Effects ISSN: 1556-7036.