
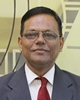
- Open Access
- Authors : Atul D. Dhale
- Paper ID : IJERTV11IS120066
- Volume & Issue : Volume 11, Issue 12 (December 2022)
- Published (First Online): 19-12-2022
- ISSN (Online) : 2278-0181
- Publisher Name : IJERT
- License:
This work is licensed under a Creative Commons Attribution 4.0 International License
Use of vibration Monitoring and Analysis for Fault Diagnosis of Rotating Machines – Some Case Studies
Atul D. Dhale*
*Professor, Mechanical Engineering Department,
-
J. Sanghvi college of Engineering, Mumbai, India-400056
Abstract:- In modern process industry it is not uncommon to find various rotating machines like cutters, crushers, pulverizes, pumps, centrifuges, ID fans, FD fans, steam turbines etc. linked together in continuous process of manufacturing. Unexpected failure of one of these machines can lead to unwanted down time and disrupt an entire process with staggering losses in terms of production, manpower, and money. Even a failure of single bearing or coupling of steam turbine can produce catastrophic results. Replacement of single bearing or coupling of steam turbine in power plant costs more than one lakh and takes at least 6 hrs. of down time. These facts together with increasing cost of new machines have placed increased demand on preventive maintenance of rotating machine to keep existing machines operating efficiently and reliably.
Vibration monitoring and analysis is one of the most effective ways to judge the health condition of rotating machines. Vibration frequency analysis (spectrum analysis) and phase analysis. In the event abnormal condition of machine greatly help to identify the mechanical faults. Authors have come across many types of vibration problems where they have tackled the problems by using vibration monitoring and analysis.
The present paper deals with the application vibration monitoring and analysis for fault diagnosis of some critical machines in process industries. Steps involved in vibration monitoring and analysis are discussed as well as three case studies are presented.
Keywords: – Vibration monitoring, Vibration frequency analysis, Fault diagnosis, Process industry, Rotating machines
-
INTRODUCTION
Process industry consists of variety of rotating machines; these machines are linked together to perform a continuous process of manufacturing. Most of these machines are heavy in weight. Their operating speeds lie in the range of 10 to 6000 rpm. A catastrophic failure of just one of these machines disrupts an entire process of manufacturing and leads to downtime of few hours to few days. Sever failure of critical machines like ID fan and steam turbine etc. require two to three days for repairs.
By monitoring vibration level of these machines periodically and analyzing the vibration levels, one can plan the scheduled maintenance for these machines. Analysis of vibration along with phase analysis helps to diagnose the malfunction in the machines.
A large variety of instrumentation and techniques are available for the measurement and analysis of machinery vibration, which have been successfully used to avert catastrophes in process industries. However, because of lack of understanding about the suitability of this technique for machines in process industry and due to lack of properly trained personnel missing link is still existing in most of process industries. In this decade a few process industries started to make use of vibration monitoring to access the condition of some of the machines. The present work has been undertaken to delve in to field of vibration monitoring, analysis and diagnosis of critical machines in process industries. The technique of vibration monitoring and analysis is aimed at to apply for different machines effectively.
-
METHODOLOGY
Case 1: I.D. Fan of Boiler, Sahyadri starch and Auxiliary Chem. Industries Pvt. Ltd. Miraj. Motor H.P. – 30Kw
Motor RPM – 1440 RPM Fan RPM – 1200 RPM
Boiler capacity – 10 ton
Figure 1 Layout of I.D. Fan of Boiler
In the course of the trial it was observed that even on NO LOAD the vibration level on both the bearings of the fan were very high which are shown in the Table 1. As the vibrations levels were severe at both bearings of I.D. Fan, it was decided to carry out frequency spectrum analysis. Frequency spectrum taken on bearings shown in Figure 2 and 3. Vibration analysis with IRD 350 Av revealed that the predominant frequency was at 1x RPM. A little marked vibration was also observed at 2x RPM. The vibration at 1x RPM with steady phase occurs due to unbalance. So it was concluded that there was unbalance.
It was decided to carry out single plane In-situ balancing of fan. As usual procedure, initial vibration level was tuned condition at 1x RPM and phase were measured they were found to 500 microns and 250 degrees respectively. Trial weight of 95 gms was added on shroud plate of the fan. With this trial weight vibration level and phase were observed and they found to be 420 microns and 260 degrees respectively. Vector diagram was drawn and value of balance weight to be added with respect to trial weight, location was calculated. They were 120 gms, and 95 degrees with respect to the position of trial weight in opposite direction of rotation.
After adding the balance weight at same radius as that of trial weight at calculated position, the fan was restarted. It was found to run smoothly. Figure 4 shows the vibration spectrum after rectification which reveals substantially reduced peak at 1x RPM.
Table 1: Before Balancing
Pick up
Position
A
B
C
D
DIS
µm
VEL
mm/s
DIS
µm
VEL
mm/s
DIS
µm
VEL
mm/s
DIS
µm
VEL
mm/s
V
350
42
300
30
200
18
220
14
H
900
42
600
50
200
17
260
18
A
1300
84
1300
90
—
—
—
—
Table 2: After Balancing
Pick up Position
A
B
C
D
DIS
µm
VEL
mm/s
DIS
µm
VEL
mm/s
DIS
µm
VEL
mm/s
DIS
µm
VEL
mm/s
V
180
16
160
13
140
09
140
13
H
280
24
220
24
150
10
180
13
A
250
20
—
—
—
—
—
—
Figure 2: Frequency Spectrum at Bearing A Figure 3: Frequency Spectrum at Bearing B
Figure 4: Frequency Spectrum at Bearing A
Case 2: – Scalper Machine
Company Name Indian aluminum Ltd Kalwa, Thane
Motor H.P.: – 160kw Motor RPM: – 985rpm Rotor RPM: -985rpm
As per ISO 10816-1, class of equipment Class 3
Permissible overall vibration level 18.0 mm/sec, due to flexible mounting condtion.
Figure 5: layout of scalper machine
When machine was running in the load condition it was observed that there were very high axial readings on A and B bearings (motor side) also very high vertical reading on C and D (Crusher side) as shown in Table 3. As the vibration level were severe, it was decided to carry out frequency spectrum analysis. Figure 4 shows the frequency spectrum at A axial, in that 1x, 2x, 3x rpm and 1x rpm was predominant and so it was concluded that there might be unbalance. At B vertical and axial, got almost same frequency spectrum (Figure 6). Also at C and D vertical from frequency spectrum (Figure 7) it was found that 1x rpm was dominant and so concluded that there was an unbalance on rotor side.
As we had suggested then to replace the blades with equal mass distribution and suggested to align rotor shaft to motor. After rectification by mounting equal weight blades exactly apposite in each plane vibration drastically came down and then they are almost acceptable except on D horizontal are still higher than permissible overall vibration level. From the frequency response at D vertical 1x rpm was predominant and so there were still minor unbalance in rotor assembly on NDE side. After few days it was observed that there was increase in vibration level, especially at bearing A and B axial and bearing C vertical and D vertical horizontal. Again observed the frequency spectrum and there were found 1x, 2x, 3x rpm and so it was concluded that there was misalignment and it was checked and found 0.2 microns range which was permissible for 985 rpm.
After thinking so much and with carefully observation it was seen that the anti-vibration pads were worn out and so there was uneven deflection of anti-vibration pads this leads to misalignment of crusher and motor also creates oscillation because of this axial vibration on motor side are more therefore it was advisable to check anti-vibration pads for loading in such a way that deflection of all pads was same, which helps to keep level of machine horizontal
It was found that anti-vibration pads were worn out we asked to replace the pads but unavailability they couldn't replace, so as a temporary solution, we had tried out In-situ balancing of assembly of flywheel. After addition of approximate 220gms. Vibration on bearing D vertical dropped down to 33mm/sec @ 240 degrees. However, after restarting of machine without any further addition, vibration on bearing D vertical rose to 57 mm/sec @ 240 degrees. these readings rose to 154 mm/sec @ 277 degrees after restating machine.
This showed that characteristics of rotating hammer changes angular distribution of weights in each run as such satisfactory results in balancing could be achieved. The main cause of vibration was eccentric mounting of rotor with respect to shaft and loss of damping properties of anti-vibration pads. Rotors were thoroughly checked for eccentric fitment was dynamically balanced, without hammers and with flywheel especially on balancing machine. (Off-site).
Then hammers were mounting with equal weight distribution uniformly to attain better results. Also shaft was rubbed out and so it was materialized and then it was assembled with rotors also anti-vibration pads change. After that the vibrations were reduced drastically as shown in Table 4.
Table 3: Before Rectification Table 4: After Rectification
Pick up Position
A
B
C
D
V
16.24
34.54
59.48
72.18
H
12.96
17.3
12.71
23.98
A
61.83
57.4
18.85
19.22
Pick up Position
A
B
C
D
V
3.05
4.16
4.94
7.01
H
3.86
2.65
1.55
3.17
A
4.63
3.04
1.83
2.51
Figure 6: Frequency Spectrum at Bearing B Axial Figure 7: Frequency Spectrum at Bearing A Axial
Figure 8: Frequency Spectrum at Bearing C Vertical
Case 3: Dryer Circulation Fan
Company Name- National Organic Chemical India Ltd. (Rubber Division) Thane
Motor RPM- 2900rpm Rotor RPM- 4200rpm Motor H.P. 7.5 H.P.
Permissible overall vibration level – 7.1 mm C D
Fan
Motor
A B
Belt
Figure 9: Layout of Dryer Circulation Fan
From the readings shown in Table 5 found that vibration levels were much higher than the permissible value as per ISO 10816-1 STD. So it was decided to carry out the frequency spectrum analysis. From the frequency spectrum (Figure 9 to Figure
11) it was seen that there were high radial vibration and 1x rpm is predominant, so there might be eccentric pulley also there might be misalign.
Because of flexible motor mounting causes high motor vibration due to that resonating type of condition occurred, therefore it was recommended to change the motor mounting structure and make it more stiffened. Also at 'D' observed the bearings frequencies and therefore bearing might be deteriorating, so it was recommended also to check the fan shaft surface for scoring marks at the bearings mounting area.
At bearings 'C' and 'D' show the increased clearances and so recommended to replace the bearings. After rectification in alignment again we had taken readings and frequency spectrum it was observed that there was minor misalignment between both pulleys, also there was no proper fitment of both the pulleys.
After realign we observed that there was drastically reduction in vibration as shown in Table 6. After realigning of pulleys, the overall vibration levels were acceptable.
Table 5: Before Rectification Table 6: After Rectification
Pick up Position
A
B
C
D
V
10.71
13.72
4.77
4.8
H
9.58
8.89
6.6
7.1
A
5.58
8.69
10.4
10.3
Pick up Position
A
B
C
D
V
4.8
4.8
2.37
3.5
H
5.9
5.7
4.37
4.5
A
6.7
4.1
4.6
3.0
Figure 10: Frequency Spectrum at Bearing A Vertical Figure 11: Frequency Spectrum at Bearing B Vertical
Figure 12: Frequency Spectrum at Bearing C Axial Figure 13: Frequency Spectrum at Bearing D Axial
-
CONCLUSION: –
-
The technique of using vibration measurement to determine the Health Condition of rotating machine and vibration analysis in the event of abnormal condition to detect incipient failure has considerable potential for process industries.
From the above three cases, it was observed that vibration analysis from the frequency spectrum is a very complex process, but still it is very useful to detect the cause of vibration and so we can maintain the good condition of rotating machines specifically in process industries.
REFERENCES: –
[1] Manish Vishwakarma, Rajesh Purohit, V.Harshlata, P.Rajput, Vibration Analysis & Condition Monitoring for Rotating Machines: A Review,Materials tday : Proceedings, Volume 4, issue 2, Part A, 2017, pages 2659-2664
[2] Chhaya H. M. Vibration and Analysis for Preventive Maintenance. Journal of Vibration, Acoustics, stress and Reliability in Design, December 1989. [3] Micani D. Vibration Control in Industrial Plant: A Methodological Approach, Journal of vibration, Acoustics, stress, and Reliability in Design,october 1987, vol. 109/335.
[4] IRD Mechanalysis,Inc Columbus-Ohio. [5] Andrew k. costain and Michael Robichaud practical methods for vibration control of industrial Equipment. www.bretech.com [6] Randy Fox,Dynamic Absorbers For Solving Resonance Problems. Google.com [7] Collacot R.A. Mechanical fault diagnosis and preventive maintenance [8] Rao S.S. Fundamentals of vibration, Addison- Wesley publishing company. [9] Norton M. & Karczub D. Fundamentals of noise and vibration analysis for engineers [10] Willams J.H., Davis a., Drake P.R. Condition based maintenance and machine diagnostics [11] Steve Goldman, Vibration Spectrum Analysis a practical approach Industrial Press Inc.