
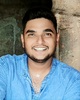
- Open Access
- Authors : Pratik Goel , Aditi Sharma
- Paper ID : IJERTV11IS070005
- Volume & Issue : Volume 11, Issue 07 (July 2022)
- Published (First Online): 13-07-2022
- ISSN (Online) : 2278-0181
- Publisher Name : IJERT
- License:
This work is licensed under a Creative Commons Attribution 4.0 International License
Use of Alternative Materials in Manufacturing of Concrete Paver Blocks: A Review
Pratik Goel
M.tech, Geotechnical Engineering IIT Bhubaneswar, India
Aditi Sharma
-
tech, Geotechnical Engineering IIT Bhubaneswar, India
Abstract- Roads have been the backbone of infrastructure. Different materials have been used for the construction of roads like bitumen, concrete, WBM etc. Concrete block adds to this list as they are easy to install and have proved to be cost effective in low volume roads. This paper outlines the desired properties of concrete blocks according to Indian standards. Cement manufacturing utilizes lime which is a limited resource thus materials alternative to cement are a constant topic of research. This paper further highlights the alternative materials used by different researchers in the manufacturing of concrete blocks.
Keywords:- Concrete block, Red mud, Fly ash, Compressive strength
-
INTRODUCTION
Paver blocks are being in use in transportation industry for a long. They have proved to be an adequate replacement of bitumen and concrete as wearing course in many types of pavement design. Paver blocks use a simple design methodology and its design is in accordance with design of flexible pavements (Ahmed & Singhi, 2013). Paver blocks have been found to be most advantageous in low volume roads however researches are going for their effective use in high volume roads also. The paver blocks find its application in footpaths, toll plazas, taxiways, etc. (IRC: SP: 63-2004). The major advantage of using paver blocks according to most of the literatures is the easy access to underground utilities after construction of the pavement which is an issue of serious concern in conventional pavement practices. Paver block pavements are found to have less maintenance cost than conventional pavement design and thus despite of higher initial construction cost, they prove to be cheaper than conventional pavements for low volume traffic. Various researches are going in transportation industry to find alternative materials in manufacturing of concrete blocks. The major advancement that is occurring in this field is the use of earth materials and some additives as a replacement of cement for construction of block pavements. The most commonly used earth material in most of the literatures is the locally available soil with additives like fly ash, rice husk ash, etc. as binder.
-
MATERIALS USED IN MANUFACTURING
OF CONCRETE BLOCKS
The materials used in construction of concrete blocks are aggregates (6mm to 20 mm), Stone dust (crushed), Ordinary Portland Cement, Water, Admixtures, Colors, Coating required to make the surface glossy.
-
PROPERTIES OF CONCRETE BLOCK
Compressive Strength
For light traffic conditions the compressive strength of paver block should be 25Mpa and for more severe conditions it should be 35Mpa for loading greater than 30KN (SABS 1058-2002). The compressive strength should be greater than 30Mpa for single block (IRC: SP: 63-2004).
Thickness
According to Ahmed and Singhi, 2013 the thickness of block should be decided on basis of traffic conditions prevailing which are as follows-
-
60mm- Light traffic condition
-
80mm- Medium traffic condition
-
100mm-Heavy traffic condition
This was however also confirmed by Mascio et.al, 2018 who found suitable thickness of block between 80-100mm. Increase in block thickness results in reduction of deflection and therefore increasing the number of safe load cycles. This is attributed to the fact that the load spreading capacity of the block depends on its thickness thus if block thickness increases the elastic deformation decreases and hence less stress is transmitted to lower layers.
-
Shape and Size
Complex shaped blocks are found to work better than rectangular blocks this is due to the fact that the vertical surface area is higher in complex shaped blocks and higher vertical surface area results in higher load spreading capability and also aid in developing larger frictional forces that is responsible for transfer of load to the adjacent block. Larger size blocks are found to work better than small blocks; this is due to the fact that as the block size increases the number of blocks per unit area decreases which results in reduced translation and rotation. However the length should not exceed certain limiting value which will otherwise result in excessive deflection of the block.IRC: SP: 63-2004 has classified the blocks depending upon the shapes in three categories. This division is attributed to number of curved faces present in the block.
According to Reddy et.al, 2015 the plan area of the complex is calculated as-
-
The block is placed on the cardboard and perimeter of its face is traced on the cardboard.
-
The shape is cut and weighed, let its weight be
msp. (kg)
-
A rectangle (200mm ×100mm) is cut from same cardboard, and weighed, let its mass be mstd (kg)
-
Then, plan area Asp is given as-
-
These materials give the properties like compressive strength, water absorption etc. within the safe limits prescribed by code.
-
They economize the overall process.
=
a) The cost of conventional concrete paver block made of M20 grade concrete is Rs.
12 per block. The cost of paver block
-
-
NEED FOR REPLACEMENT OF CEMENT
AND AGGREGATES IN PAVER BLOCKS
The needs for the replacement of cement and aggregates in concrete blocks are highlighted in the following points.
-
The production of cement is an energy intensive process and thus requires a huge amount of energy in all process of its production.
-
The production of cement results in emission of carbon dioxide which is a serious threat to environment.
-
The manufacturing of cement requires lime however the availability of lime is limited and thus sustainable use lime is an issue of serious concern.
-
The aggregates are quarried however their stock is limited thus there is an urgent need to find out alternatives in transportation industry that can replace natural aggregates without compromising the standards.
-
-
BENEFITS OF USING ALTERNATIVE
MATERIALS
-
The alternative materials to cement and aggregates used in various literatures are present in abundance.
-
According to Tanu et.al, 2020, large amount of agricultural and industrial waste is produced and is simply burnt or dumped resulting in release of harmful gases and conversion of valuable lands into dumping sites.
-
According to Anupriya et.al, 2021, about 56 lakh tons of plastic waste is generated in India per year whose handling is an issue of serious concern.
-
According to Piloneta et.al, 2021, Steel production in 2017 has resulted in generation of 120 to 240 tons of slag.
-
According to Jayakumar et.al, 2013, the urbanization and industrialization has catalyzed the growth of waste generation whose handling has forced the researchers to find their alternative uses.
-
According to Anupriya et.al, 2021, the world at present produces about 2378 tons of municipal solid waste ash.
-
-
According to Jangid and Darade, 2017, Infrastructure development using earth materials is a way of judicious use of the Earths valuable resources. Earth infrastructure avoids pollution and deforesation.
made from fly ash and M20 grade
concrete of is Rs. 10 per block. The cost of paver block made from solid waste is found to be as Rs. 6 per block (Anupriya et.al, 2021).
-
The cost of construction of flexible pavement per kilometer is found to be 77,69,000 INR but similar pavement paved with bagasse paver blocks costs 58,93,000 INR (Rajkumar et.al, 2016)
-
The average cost of plastic paver block pavement is found to be about 35.39% less than conventional concrete paver block pavement.
-
-
-
ALTERNATIVES USED FOR CEMENT AND
AGGREGATES
There are various alternatives to be used as partial or total replacement of cement and aggregates few of them are listed below.
Rice husk ash
-
Rice husk is the outer hard protective covering of rice crop which is a waste generated during harvesting of rice crop.
-
About 200 kg of rice husk is produced per ton of rice production which reduce to 40 kg on burning. (Zareei et.al, 2017)
-
The ash is prepared by burning the rice husk burning at about 800 oC and then cooling it.
-
The coarse ash is then transferred to grinded to obtain finer ash.
-
It is used as the replacement of cement.
-
It contain about 85 to 90% amorphous silica and about 5% alumina which imparts pozzolonic property to rice husk ash.
-
The burning of rice husk requires huge energy and also results in carbon emissions in environment thus a proper methodology should be adopted in order o get max sustainable development.
Fly ash
-
Fly ash is the ash generated after the combustion of coal.
-
At present India produces about 180 million tons of fly ash every year which is used in a small amount in construction and other industries and the rest is simply dumped in ponds.
-
It used as replacement of cement in construction industry due to its pozzolonic properties.
-
Fly ash contains silicon dioxide (SiO2) both in crystalline and amorphous state, aluminum oxide
(Al2O3) and calcium oxide (CaO) which imparts pozzolonic properties to it.
-
Use of fly ash results in slower strength gains.
-
Class C fly ash is temperature sensitive and thus do not give desired strength in case of mass concreting very temperature is high.
-
Fly ash affects the color of concrete.
Recycled asphalt
-
Recycled asphalt is obtained from removal of asphalt from the old pavement.
-
It is used as the replacement of coarse and fine aggregates in concrete industry.
-
It reduces the specific gravity of the concrete due to presence of aged bitumen.
Plastic material
-
Burning of plastic waste results in huge emission of toxic gases resulting in environmental pollution.
-
To be used in concrete the plastic waste is first shredded and melted.
-
Plastic consist of variety of synthetic and semi synthetic organic that can be melt and can be mould desired solid shapes.
-
Plastic is basically polymer formed from carbon chain monomers or with addition of oxygen, nitrogen and Sulphur.
-
Using plastic also have certain disadvantages those are like plastic in presence of chlorine emits Hcl gas, toxics present in plastic start leaching during first rain.
Municipal solid waste
-
MSW on combustion generates methane gas which is highly toxic gas and results in degradation of environment and many severe health issues.
-
India uses 256 million tons of MSW in construction activities.
-
MSW ash contains SiO2, Al2O3, and CaO which imparts pozzolonic properties to it.
Steel and iron slag
-
Only 10% of slag produced in India is being utilized.
-
Slag is the byproduct obtained during extraction of iron from its ore.
-
Slag is rich in silica and alumina and thus acts as source material for the formation of geopolymer.
-
It is also used as replacement of aggregates.
-
-
MANUFACTURING OF PAVER BLOCKS BY PARTIAL REPLACEMENT OF CEMENT
OR AGGREGATES
-
Reddy et.al, 2015 used rice husk ash and nylon fiber with cement concrete and found good to be used in paver blocks. He added nylon fiber as
reinforcement in varying proportion of 0.1%, 0.2%, 0.3%, 0.4%, 0.5% and then varied the
proportion of rice husk ash as 10%, 20%, 30% replacement of cement. According to him 0.4% nylon fiber and 20% risk hush ash was the best proportion. At this proportion the compressive strength at 28 days curing was about 43.778 Mpa which was in accordance with IS: 5658:2006. Fig.
1 depicts the compressive strength pattern obtained.
-
Jangid and Darade, 2017 used lime, fly ash, coir and chemicals with concrete to enhance the strength of compressed earth blocks and found that on varying proportion of fly ash from 10% to 50% the compressive strength decreased from
146.67 Mpa to 33.33 Mpa. The addition of coir and lime resulted in increase of compressive strength; the maximum compressive strength obtained was about 300 Mpa. According to him t percentage of fiber should not be more than 3% as it will result in mixing difficulty and also adversely affect the compressive strength.
-
Shabiimam et.al, 2018 used plastic as partial replacement of aggregate in paver blocks and found it to be suitable in its use. The percentage replacement of aggregate was found in order 0%, 10%, 20%, 30% and 40%. The compressive strength at 28 days curing was found to be varying between 41.10 Mpa to 37.77 Mpa respectively, which was in accordance with IS: 5658:2006.
-
Rajkumar et.al, 2016 used bagasse ash as partial replacement of cement in paver blocks. He performed 4 trials at two different water cement ration i.e. of 0.38 and 0.45 and at two replacement compositions i.e. 0% and 50% of cement by bagassse ash and found that 28 days compressive strength varied between 45 Mpa to 42 Mpa which was in accordance with IS: 5658:2006.
-
Malinga et.al, made paver blocks using geopolymer concrete by partial replacement of cement and aggregate by fly ash and GGBS and found the compressive strength to be varying in the range of 35 Mpa which was in accordance with IS: 5658:2006.
-
Banupriya et.al, 2016 used GGBS and fly ash for the manufacture of paver blocks as replacement of concrete. He made mixtures in proportion of 80%, 75%, 70%, 65% of GGBS mixed with 20%, 25%, 30%, 35% fly ash respectively and found the compressive strength to be varying between 54 Mpa to 43.56 Mpa. The highest compressive strength obtained was at 75% GGBS and 25% fly ash mixture that was 60.5 Mpa.
Figure 1: Compressive strength pattern obtained by Reddy et.al (2015)
-
-
MANUFACTURING OF PAVER BLOCKS
BY COMPLETE REPLACEMENT OF CEMENT OR AGGREGATES
-
Kumar and Kumar, 2012 used red mud and fly ash for manufacturing of paver blocks. Both the materials are industrial waste. Red mud is obtained as a waste material during the extraction of aluminum in Bayerss process. 9 different trials were made by varying fly ash percentage from 100% to 60% at the interval of 5% and varying red mud from 0% to 40% respectively. Two combinations were found satisfactory to be used as paver blocks. Fig 9(a) summarizes the properties of the obtained two combinations. It can be clearly seen that the given two combination satisfy all parameter prescribed in IS 15658: 2006 to be used as paver blocks.
-
Tawalare et.al, 2018 used fly ash, recycled
aggregate as replacement of fine aggregate and slag as replacement of coarse aggregate in paver blocks. He made four trials varying different parameters listed in fig 3(b). It can be seen from the fig. 3(a) only one trial i.e. GPC4 (recycled aggregate) satisfies the criteria of compressive strength to be used as paver blocks.
-
Tempa et.al, 2020used plastic waste as replacement of cement for manufacturing of paver blocks. The plastic waste was made to vary between 40% to 70% by weight of total mix and it was obtained that the compressive strength varied from about 55 Mpa to 70 Mpa, which was in accordance with IS: 5658:2006.
Figure 2: (a) The paver block properties obtained by Kumar and Kumar (2012); (b) The paver blocks obtained using red mud and fly
Figure 3: (a) Compressive strength at different mixing obtained by Tawalare et.al (2018); (b) different trials considered by Tawalare et.al (2018)
-
-
CONCLUSION
-
CBP is a good alternative for conventional pavement in low and moderate traffic areas like parking, gardens etc.
-
The operating speed for CBP is typically 40 to 60 Kmph however researches are working on and it might be further possible that CBP in near future work as alternative for high speed roads.
-
The initial cost of CBP is higher but in long run CBP turns out to be cost efficient than conventional pavement design however this fact also depend on terrain conditions, availability of materials, weather conditions, traffic and loading
-
Proper checking of CBP is needed after completion of construction.
-
The excessive use of cement is leading to exploitation of natural lime whose sustainable use can ensure its availability for future generations. The manufacturing of cement leads to emission of greenhouse gases.
-
Aggregates are quarries from natural quarries, their stock is also limited.
The generation and proper handling of industrial, household waste is an issue of serious concern and thus ways are to be worked out to use these waste products in a wise manner.
-
Many of the waste materials like red mud, fly ash, plastic, slag have been found satisfactory as partial or complete replacement of cement and aggregate in construction industry.
-
The use of the waste material in concrete paver blocks has proved to be a significant revolution. The waste materials concrete paver blocks qualifies all strength criteria prescribed by IS: 5658:2006.
-
The use of waste material in concrete block pavements also results in significant decrease of the cost of pavement.
-
-
REFERENCES
-
1239-1244.
[4] Talesnick, Mark, and Rafi Geller. "Case Study of Premature Failure of a Concrete Block Pavement System at a Shipping Container Logistics Site." Journal of Performance of Constructed Facilities 34, no. 1 (2020): 04019093. [5] Huurman, M. "Rut development in concrete block pavements due to permanent strain in the substructure." In First International Conference on Concrete Block Paving, pp. 293- 303. 1996. [6] Tanu, H. M., Minakshi Mishra, M. Sunitha, T. V. Reshma, and-
S. Sankalpasri. "A Study On Cement Stabilized Laterite Paver Blocks."
[7] Reddy, A., Vishal Gupta, and Deepak Garg. "Effect of partial replacement of cement by rice husk ash using nylon fiber inconcrete paver block." IJSRD-International Journal for Scientific Research & Development, ISSN (online) (2015): 2321-0613.
[8] Harikumar, M., N. P. Firozemon, S. Rithika, S. Nipin, T. S. Shayifa, and K. M. Jini. "Experimental investigation on compressed stabilized earth block." International Journal of Scientific & Engineering Research 7, no. 4 (2016): 76-84. [9] Jangid, Shivnath, and Milind Darade. "Study on Compressed Stabilized Earth Block." (2017). [10] Udawattha, Chameera, Harsha Galabada, and Rangika Halwatura. "Mud concrete paving block for pedestrian pavements." Case studies in construction materials 7 (2017): 249-262. [11] Anbarasi, K., S. Southamirajan, S. Devaki, P. L. Sathyabalan, and M. Gokul Anish Kumar. "Plastic Paver Blocks of Waste Plastic By Analyzing Properties of Materials." Journal of Critical Reviews 7, no. 4 (2020): 1301-1306. [12] Hamdi, Abdessattar, Nejib Ben Jamaa, and Imen Kallel Kammoun. "Potential use of phosphogypsum in paving blocks." Green Materials (2020): 1-11. [13] Hossiney, Nabil, Hima Kiran Sepuri, Mothi Krishna Mohan, Sarath Chandra K, Srinidhi Lakshmish Kumar, and Thejas HK. "Geopolymer concrete paving blocks made with Recycled Asphalt Pavement (RAP) aggregates towards sustainable urban mobility development." Cogent Engineering 7, no. 1 (2020):1824572.
[14] Tawalare, Abhay, Rupali Kejkar, and Mahesh Kumar. "CoMParison of geopolymer paver block using natural aggregate and recycled aggregate as fine aggregate and slag as coarse aggregate." In IOP Conference Series: Materials Science and Engineering, vol. 431, no. 9, p. 092002. IOP Publishing, 2018. [15] Anupriya, B., T. Mohanasankari, and B. Saranya. "Experimental Investigation of Paver Block by using Municipal Solid Waste." [16] Jayakumar, P. T., V. R. Ram Kumar, R. Suresh Babu, and M. Mahesh Kumar. "Experimental investigation on paver blocks using steel slag as partial replacement of aggregate and sludge as partial replacement of cement." Int J Sci Res 2, no. 5 (2013): 87-91. [17] Yang, Sungchul. "A feasibility study of wood-plastic composite paver block for basic rest areas." Journal of the Korean Wood Science and Technology 47, no. 1 (2019): 51-65. [18] Shabiimam, M. A., Tehsin Kazi, Abhishek Pandey, Tajuddin Ansari, and Rahul Chaurasia. "Reusing Plastic Waste by Manufacturing of Paver and Solid Block." [19] Rajkumar, P. R., K. Divya Krishnan, P. T. Ravichandran, and -
Aarthi Harini. "Study on the use of bagasse ash paver blocks in low volume traffic road pavement." Indian Journal of Science and Technology 9, no. 5 (2016): 1-6.
XV, Issue No. 2, (Special Issue) April-2018, ISSN 2230-7540 [27] Waziri, Baba Shehu, and Zanna Alhaji Lawan. "Properties of
compressed stabilized earth blocks (CSEB) for low-cost housing construction: a preliminary investigation." International Journal of Sustainable Construction Engineering and Technology 4, no. 2 (2013): 39-
46.
[28] Bhatt, Arpita, Sharon Priyadarshini, Aiswarya Acharath Mohanakrishnan, Arash Abri, Melanie Sattler, and Sorakrich Techapaphawit. "Physical, chemical, and geotechnical properties of coal fly ash: A global review." Case Studies in Construction Materials 11 (2019): e00263. [29] Parson Ann, 2021, How paving with plastic could make a dent in the global waste problem, Yale E360 [30] Sharma S.D, (2004), Interlocking Concrete Paver Blocks,NBM&CW Infra construction and equipment magazine
[31] Vaiiukynien, Danut, Dalia Nizeviien, Aras Kantautas, Vytautas Bocullo, and Andrius Kiel. "Alkali Activated Paste and Concrete Based on of Biomass Bottom Ash with Phosphogypsum." Applied Sciences 10, no. 15 (2020): 5190. [32] Suresh P, Md. Azam , Harish B.,2019. Recycling Plastic Waste Into Paving Blocks, Journal Of Architecture & Technology, Volume XI, Issue XI, ISSN No : 1006-7930 [33] Lam, Charles Hoi King, John Patrick Barford, and Gordon McKay. "Utilization of municipal solid waste incineration ash in Portland cement clinker." Clean technologies and environmental policy 13, no. 4 (2011): 607-615. [34] Stephen Leni, Raji Amjad, Rajan Sachin, Visakh N V, 2019, Study on Failure of Interlocking Pavements , International Research Journal of Engineering and Technology (IRJET) e-ISSN: 2395-0056 Volume: 06 Issue: 04 Apr 2019
[35] Shen, Weiguo, Yi Liu, Bilan Yan, Jing Wang, Pengtao He, Congcong Zhou, Xujia Huo, Wuzong Zhang, Gelong Xu, and Qingjun Ding. "Cement industry of China: driving force, environment iMPact and sustainable development." Renewable and Sustainable Energy Reviews 75 (2017): 618-628. [36] Venkatarama Reddy, B. V., and Ajay Gupta. "Strength and elastic properties of stabilized mud block masonry using cement-soil mortars." Journal of materials in civil engineering 18, no. 3 (2006): 472-476. [37] IRC:SP:63-2004, Guidelines for the use of interlocking concrete block pavement [38] IS:15658-2006, Precast concrete blocks for paving- specification [39] The manufacturing of concrete paving block, Cement and concrete institute, South Africa