
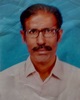
- Open Access
- Authors : Sabapathi. T , Aishwarya K , Pavithra M
- Paper ID : IJERTV9IS030106
- Volume & Issue : Volume 09, Issue 03 (March 2020)
- Published (First Online): 11-03-2020
- ISSN (Online) : 2278-0181
- Publisher Name : IJERT
- License:
This work is licensed under a Creative Commons Attribution 4.0 International License
Tunnel Fire Detection using FBG
Sabapathi. T Associate Professor (Sr. Grade) Department of Electronics and
Communication Engg.
Mepco Schlenk Engineering College, Sivakasi
Aishwarya K
Department of Electronics and Communication Engg.
Mepco Schlenk Engineering College,Sivakasi
Pavithra M
Department of Electronics and Communication Engg.
Mepco Schlenk Engineering College,Sivakasi
AbstractTunnel fires are not common but they can cause a great damage to lives and properties if happen. Detecting the presence of a fire inside the lengthy and curved tunnel is a tedious process. Detection using Fiber Bragg Grating (FBG) Sensor technique provides a novel methodology by finding not only the presence but also locating the fire inside the tunnel. FBG Sensors are distributed across the inner sides of the tunnel and they are monitored by the Optical Spectrum Analyser (OSA) or Wavelength Division Multiplexing (WDM)Sensor Interrogator at the exit. The change in the center wavelength from the original spectrum at the output denotes the temperature change (fire occurrence) inside the tunnel. The FBG provides output with more accuracy and it can withstand very high temperature values.
Keywords Center wavelength, Fiber Bragg Grating Sensor, Optical Spectrum Analyser, Tunnel Fire, WDM Sensor Interrogator.
-
INTRODUCTION
The project Tunnel Fire Detection comes under Structural Health Monitoring (SHM), which involves the process of collecting the information and analyzing it for evaluating the performance of the structure under monitor. The factors that contribute to tunnel fire are tunnel length and its volume. The major tunnel fire accidents are due to ventilation problems, collision of two or more vehicles and lack of information about the number of vehicles inside the tunnel. These along with fuel spillage cause the fire to spread throughout the tunnel in a faster way leading to a catastrophic disaster.
may safeguard the public and properties from massive accident.
The process of sensing and locating is efficiently done by the FBG sensor. The gratings in the FBG sensor cause a narrow range of wavelength to shift and the rest of it to transmit through it [3]. The center of the reflected wavelength is the Braggs Wavelength. These characteristics of FBG sensor is utilized to measure temperature or strain changes in the structures. They have the greater temperature withstanding capability, more immune to EMI (Electro Magnetic Interferences), longer life time, explosion safe and it can be multiplexed. The FBG sensors are designed and simulated here using OptiGrating and OptiSystem software. Also, the temperature changes inside the tunnel are visualized using COMSOL Multiphysics Software.
-
FBG SENSOR
FBG is short segment of optical fiber that reflects particular wavelength of light and transmits all other wavelengths [6]. It acts as an optical notch filter. The reflection is due to the grating patterns inside the fiber. FBGs are built by using holographic interference or a phase mask to expose small length of fiber to a periodic distribution of light intensity. The wavelength is reflected based on the Braggs equation,
B = 2 neff (1)
The conditions are even more serious when the length of the tunnel is too long or the tunnel has bends. Because the visibility of the tunnel from one end to the other end is less. Hence the fire occurrence at one end cannot be sensed through the other. Hence many more vehicles may enter the tunnel causing a massive accident.
The fire can be detected using a no. of ways like using of temperature sensor inside the tunnel or monitoring the tunnel through camera. All these can sense the fire inside the tunnel but locating them becomes difficult. The temperature sensor like thermistor cannot withstand very high temperature (say 1000C). Also, they have the problem of self-heating. The image processing using cameras inside the tunnel may detect and alert the people outside the tunnel but eventually the camera may get damaged due to the fire itself. If we could locate the position of fire in an effective way, we
Where B is the Braggs wavelength, neff is the effective refractive index of the grating inside the core of the fiber, is the grating period. Only the wavelength of light that satisfies this Braggs equation gets reflected.
The value of the reflected wavelength changes based on changes in the temperature. When there in an increase in temperature (as in fire conditions), the fiber elongates causing the grating pattern to vary. Hence the effective refractive index of the grating increases leading to change in wavelength shift at the reflected port of the FBG sensor. This indicates the intensity of fire inside the tunnel structure. And when the temperature reaches back to normal, the wavelength shift comes back to its center wavelength. There is no process of hysteresis.
The change in refractive index is induced by the thermo-optic coefficient and the thermal expansion coefficient.
B = B (+) T (2)
Where is the thermo-optic coefficient of the grating of the fiber and is the thermal expansion coefficient of the fiber.
The output from each sensor will be the same i.e. the reflected spectrum of all the sensors are at the same center wavelength [6].
But during the condition of fire as in Fig.2, the temperature reading at each sensor will be varied, so as their reflected spectrum shifts away from that of the output obtained to the ideal reference value (25C).
= 1
= 1
(3)
(4)
In this paper, the FBG sensor is designed using the OptiGrating software and a setup is made in OptiSystem where 3 of the designed sensors are arranged in a distributed manner across a tunnel of length 4 km [9]. Each sensor is provided with a varying temperature (fire conditions) and is simulated.
-
METHODOLOGY
Here a tunnel like setup is being assumed and 3 FBG sensors are placed in a distance of 1 km apart each other. Initially these FBG sensors are designed for same temperature (25C).They all are provided with a same center wavelength of 1550 nm. The input is provided to the 3 FBG sensors through 3 light sources simultaneously and the reflected spectrums of the 3 sensors are individually monitored through 3 OSA or WDM Sensor Interrogator as illustrated in Fig.1.
In practical conditions, instead of using 3 separate input sources, single source can be used which can feed all the FBG Sensors.
Fig.1. Block Diagram (Ideal condition)
Fig.2. Block Diagram (Fire condition)
Now the reflected spectrum is more shifted for sensor 2 than sensor 1. Whereas the sensor 3 has the least shift as it is away from the place of fire. By calculating the shift between any two sensors, we could be able to locate the position of fire inside the tunnel.
-
COMSOL
The virtual tunnel model has been simulated in the COMSOL Multiphysics Software. The tunnel structure is designed using SOLIDWORKS 2019, a CAD based software. The tunnel in this model is erected using bricks in order to withstand high temperature range of 1000C.
Fig.3. Tunnel model designed in Solidworks
The designed tunnel structure is then imported into COMSOL Multiphysics Software. Here the FBG sensor is first separately designed using the parameters [10] as shown in Table.1.
TABLE I FBG PARAMETERS
Name
Expression
Description
n1
1.4457
Core Refractive Index
n2
1.425
Cladding Refractive Index
n3
1.446
Step index grating Refractive Index
N
5
No. of periods
P
536[nm]
Grating period
L
N*10*P
Length of the fiber
neff
(n1+n2)/2
Effective Refractive Index
lambda
2*neff*P
Incident light wavelength
f0
c_const/ lambda
Frequency of light
r_core
10[um]
Core Radius
r_cladding
62.5[um]
Cladding Radius
Now the designed FBG sensor is placed at 3 different locations in the Tunnel structure. Heat is generated inside the structure using the Heat Transfer Module in COMSOL as shown in Fig. 4. This provides tabulation for temperature at each sensor during different time instants [5]. The values are then plotted to obtain temperature vs. time graph for each of the 3 sensors (Fig.5).
Fig.4. Heat Transfer in the Tunnel using COMSOL
Fig.5. Plot of Temperature vs. Time for 3 Sensors
-
SIMULATION
-
OptiGrating section
OptiGrating is specialized software from Optiwave that has a module for designing Fiber Bragg Grating Sensor. The physical parameters like temperature and strain can be modified based on the requirement and its reflected and transmitted spectrum can be analyzed.
Here 3 FBG Sensors with 1550 nm center frequency, 2 nm linear chirp and no apodization are designed. The reflected and transmitted spectrum is obtained for normal condition 25C as shown in Fig.6. The temperature is varied for multiple values (up to 1000C) and the results are saved in the format that can be exported to OptiSystem Software.
Reflected spectrum Transmitted spectrum
Fig.6. OptiGrating output for FBG Reflected and Transmitted Spectrum
-
OptiSystem Section
The OptiSystem tool provides the facility to simulate various optical as well as electrical components. The files can also be imported from other Optiwave Software, MATLAB, etc.
Here the FBG sensors designed in OptiGrating are imported as a reflection spectrum text files and they are placed at three different positions P1, P2, P3. Overall distance taken for consideration is 4 km.
Optical fiber of 1 km is placed between each sensor. The input to the FBG Sensor is provided through the Mach- Zehnder Modulator. The pulse launched to the sensor is Non- Return to Zero. The simulated setup is illustrated as in Fig.7.
Fig.7. Model Setup
During normal conditions the output at OSA is same from all 3 Sensors. But at fire situation, consider the temperature of Sensor 1 is 600C, Sensor 2 is 900C and Sensor 3 is 100C. The outputs are obtained as shown in Fig.8. (Blue colour denotes Reference Spectrum and Red colour denotes Shifted Spectrum)
-
Results
Fig.8.1 Sensor 1 Fig.8.2 Sensor 2
Fig.8.3 Sensor 3
Fig.8. OSA Output for 3 FBG Sensors at different temperature
The simulation result as illustrated in Fig.8 shows that a major shift in Braggs wavelength is provided by the FBG Sensor 2. The new center wavelength is 1556 nm that is
shifted from 1550 nm. Sensor 1is shifted to 1553.8 nm which is less than the shift provided by the Sensor 2. The Sensor 3 which has the least change in temperature has a new value of 1550.41 nm.
From the output values we would locate the position of the fire in the sensing area. Since the shift is more in Sensor 2, the fire accident must be near the location of the FBG Sensor 2.
Also, the Sensor 1 has a considerable change in the reflected output spectrum than Sensor 3. So, the fire must be between Sensor 1 and Sensor 2 and Sensor 3 must be away from the fire incident.
The temperature is varied for different values in an FBG Sensor and its corresponding change in wavelength pattern is studied. The reference temperature is taken as 25C. The readings are given in Table.2 and it is plotted for Change in Temperature vs. Change in Wavelength as shown is Fig.9.
TABLE II CHANGE IN BRAGGS WAVELENGTH
T (C)
B (nm)
25
0.36
75
1.0358
175
2.478
275
3.898
375
5.316
475
6.808
575
8.162
675
9.618
775
10.996
875
12.418
975
13.824
Fig.9. Plot for Change in Temperature vs. Change in Braggs Wavelength
-
-
CONCLUSION
The simulation result shows sensitivity value of FBG Sensor as 20 pm/C. Locating the fire inside the tunnel can be made still more precise when the number of FBG Sensors is increased for the considered tunnel length of 4 km.
This can also help rescuing operations very fast and can safeguard many lives and properties.
The future work requires hardware implementation of the simulation setup and compares both the hardware and software results.
-
REFERENCES
-
Baoqiang Yan, Jian Li, Mingjiang Zhang, Jianzhong Zhang, Lijun Qiao and Tao Wang, Raman distributed temperature sensor with optical dynamic difference compensation and visual localization technology for tunnel fire detection, MDPI Sensors, 2019.
-
L.A. Ribeiro, S.F. Quirino, A.O. Toledo, C.L. Barbosa, O. Lisboa, and J.U. Aeeuda, Spontaneous Raman Scattering in Optical Fiber,AIP Conference Proceedings, pp 159-162, October 2008.
-
Igor Miklosik, Peter Kello, Juraj Spalek, Fiber Laser fire detection in the Tunnel simulator, IEEE Access, pp 429-434, 2016.
-
Erwan Capitaine, Nawel Ould Moussa, Chrisophe Louot, Claire Lefort, Dominique Pagnoux, Jean- Rene Duvlere,Junya
F. Kaneyasu, Hideaki Kano, Ludovic Duponchel, Vincemt Couderc and Phlippe Leproux, Coherent Anti-Stokes Raman scattering under electric field stimulation, Phys. Rev. B, 2016
-
S.V. Shruthi and S. Sundaravadivelu, High Temperature Measurement using Fiber Bragg Grating Sensor, Indian J.Sci.Res.14 (1), pp 284- 289, 2017.
-
Mohamed. Elgaud, Ahmed.M. Elshirkasi, M.S.D. Zan, A.G. Abushagur, A. AshrifA. Bakar, Analysis and Simulation of TDM Fiber Bragg Sensing Array using Optigrating and Optisystem, International Conference on Advances in Electrical, Electronic and System Engineering,pp 301-305, 2016.
-
HamidAle Mohammad, Superstructure Fiber Bragg Grating under Temperature Variations, Opto-Mechanical Fiber Optic Sensor, pp 27-47, 2018.
-
Palli Mishra, Kanhu Charan Bhuyan, Hemanta Kumar Sethi, Development of FBG Sensors using Optiwave system software for structural health monitoring, International Journal of Engineering Science Invention, pp 157-163, 2017.
-
P.Mahalakshmi, S. Kalaiselvi, Design and Analysis of temperature sensor array by using COMSOL Multiphysics 4.3, IJSR, vol.3, no.3, pp 304-309, March 2014.
-
C. Gavrila, I. Lancranjan, A Study of Optical Sensor based on Fiber Bragg Grating using COMSOL Multiphysics, Proceedings of the COMSOL Conference, 2009.