
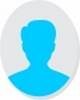
- Open Access
- Authors : Ranjeet Handibag , Dr. Umesh Potdar , Ajinkya Jadhav
- Paper ID : IJERTV9IS120224
- Volume & Issue : Volume 09, Issue 12 (December 2020)
- Published (First Online): 02-01-2021
- ISSN (Online) : 2278-0181
- Publisher Name : IJERT
- License:
This work is licensed under a Creative Commons Attribution 4.0 International License
Thermal Design of Tube and Shell Heat Exchanger and Verification by HTRI Software
Ranjeet Handibag
Mechanical Engineering Department Pimpri Chinchwad College of Engineering Pune, India
Dr. Umesh Potdar
Associate Professor Mechanical Engineering Department
Pimpri Chinchwad College of Engineering Pune, India
Ajinkya Jadhav
Mechanical Engineering Department Pimpri Chinchwad College of Engineering Pune, India
Abstract Heat exchangers are the devices used to transfer heat from one fluid to another. Fluids can be either gases or liquids. plate heat exchanger, Double pipe heat exchanger, shell and tube heat exchanger, condensers, evaporators and boilers are the most common types of heat exchangers. They are widely used in petroleum refineries, sewage treatment, air conditioning, power station, space heating and petrochemical plants. Tube and shell tube and shell heat exchanger is type of heat exchanger in which two fluids which are at different temperatures are separated by solid wall. this article includes thermal design calculation and verification of all the process parameters which are required for proper functioning of the compressor system as a whole. the design calculations of tube and shell heat exchanger are verified by HTRI(Heat Transfer Research Inc.) software. This is the software for the rating, design, and/or simulation of a wide variety of heat transfer equipment, including shell-and-tube and non-tubular exchangers, air coolers and economizers, and fired heaters.
Keywordstube and shell heat exchanger, HTRI, temparature, compressor.
-
INTRODUCTION
Industries often use compressed gases such as air, hydrogen, acetylene, oxygen, methane, etc. The volume required of these compressed gases is very high so it is required to compress these gases efficiently. For this reason intercoolers are used. Intercoolers are placed after compression or between two stages of compression. Intercoolers can be placed horizontally or vertically but horizontal intercoolers are more effective thus horizontal intercoolers generally used.
Intercoolers are generally placed in between two stages of compression as it cools down the hot fluid before sending it to second compression. Thus volume of fluid decreases which increases the volumetric capacity and decreases the work done by motor.
Fig 1: 2 stage compressor block diagram [6]
Fig 2: Tube and shell heat exchanger [12]
Following are the functions of an intercooler used in compressor:
-
Atmospheric air contains moisture, and furthermore, the air may pick up oil vapor as it passes through some parts of the compressors. Cooling air down to or below its initial temperature will remove moisture down to the dew point, improving the quality of the air.
-
Intercoolers improve the efficiency of compressor. As the volume of hot air reduces on cooling volumetric efficiency increases.
-
Every 4 °C rise in inlet air temperature results in higher energy consumption by 1 percent to achieve equivalent output. Thus lower the temperature of intake air, more is the energy efficiency of a compressor.
-
-
METHODOLOGY Problem identification
Selection of a heat exchanger
Thermal design
Verification of design
-
PROBLEM STATEMENT
To cool down the air from Thermal design of heat exchanger based on the input parameters which are given in the specification sheet and verification of design i.e. verification of the overall heat transfer coefficient also, finding out the acceptability of the pressure drop.
-
SELECTION OF HEAT EXCHANGER
Thermal design of the heat exchanger (intercooler) is according to the Kern's method. It is simple to apply, accurate enough for preliminary calculations. The selection criteria for the heat exchanger, design procedure and its calculations are discussed in the subsequent sections Selection Criteria for Shell and Tube Heat Exchanger
-
Materials of construction
-
Operating pressure and temperature
-
Flow rates
-
Flow arrangements
-
Fouling tendencies
-
Maintenance, inspection, cleaning, extension
-
Overall efficiency
-
Shell:
Shell is the cylindrical vessel container through which fluid flows and the tube bundle is placed inside the shell. Shells are usually casted from standard steel pipe with satisfactory corrosion allowance.
Fig 3: Shell Design [7]
BEW type shell type is selected. It is simple in construction and easy to clean as it has floating rare end head thus tube sheet can be easily removed for cleaning.
-
Tube and tube layout
The enough tube thickness ensures that it will bear the internal pressure along with the adequate corrosion allowance. Longer tube less is the shell diameter at the expense of higher shell pressure drop. Stainless steel, copper, bronze and alloys of copper- nickel are the commonly used tube materials.
The shortest center to center distance between the adjacent tubes is Pitch. The general pattern of tubes is square or triangular pattern. The tube count is the number of tubes that can be accommodated in a given shell ID.
Fig 4: Tube Layout [1]
For this application triangular layout is selected as it is more effective and easy to clean
-
No of passes
To obtain greater heat transfer co-efficient and also to reduce scale formation, number of passes is chosen to get the required tube side fluid velocity. The tube passes vary from 1 to 16. A single tube pass is selected for the design.
-
Baffle
Liquid is maintained in a state of turbulence ensures the higher heat transfer coefficients. The turbulence is induced outside the tubes which cause the liquid to flow at right angles to the axes of the tubes. This causes considerable turbulence even when a small amount of liquid flows through the shell.
One from the various types of baffles is used to increase the fluid velocity by diverting the flow across the tube bundle to obtain higher transfer co-efficient. The distance
Between adjacent baffles is called baffle-spacing. The segmental baffle used in design shown in the figure 4..
The % cut for segmental baffle refers to the cut away height from its diameter.
Fig 5: Segmental baffle [3]
-
-
-
PROBLEM IDENTIFICATION TABLE I. REQUIREMENT SHEET
DATA CONSIDERED
Gas Handled
Air
Capacity of compressor
M3/hr
736.2
Suction Temperature
°C
35-38
Relative humidity (Min / Max)
%
70
Suct. Pres. at compr. flange
Bar (g)
1.01
Cooling Water Temp: In / O
° C
32/40
HEAT EXCHANGERS DATA
Quantity required
Nos.
1 No.
Code of construction
TEMA C
Flow
Air
kg/hr
792.6
Fluid
Tube side
Air
Shell side
Water
Corrosion allowance
mm
Tube side
1.5
Shell side
1.5
Pressure
Bar (g)
Tube side
2.82
Shell side
3.965
Design Pressure
Kg/cm² (g)
Tube side
4
Shell side
3.3
Hydro Test Pressure
Kg/cm² (g)
Tube side
6.0
Shell side
5.0
Design Temperature
°C
Tube side
200
Shell side
75
Max.permissible Pr .Drop
Kg/cm² (g)
(By Vendor)
Tube side
0.1
Shell side
0.5
Water consumption
kg/hr
5000
Air (Gas) Temperature
°C
In
147
Out
40
No. of passes per Shell
Nos.
1
Material of construction
Tube
SA249TP304
Tube Sheets
C.S.
shell
C.S.
Baffle Plates
C.S.
Tie Rods
C.S.
Heads
C.S.
Fouling factor
M2.Hr.°C/Kca
Tube side
0.0002
Shell side
0.0004
Tube OD size
inch
3/8"
Tube thickness
SWAG
20G
Tube length
mm
1600
Tube pitch
mm
12.2
-
Outlet Condition Of Air (At Outlet Of intercooler) Pressure P2= 2.8806 kg/cm2
Temperature T2= 40.0 RH = 1.00
Saturated pressure of vapour PV2 = 0.0739 kg/cm2
Weight of air per kg of dry air
= (0.622*PV2*RH2)/(P2- PV2*RH2)
= (0.622*0.0739*1)/( 2.8806- 0.0739*1)
= 0.01637 kgs
-
Temperature of air at the inlet of the intercooler (adiabatic compression)
T2/T1 = (P2/P1)(-1)/ T2/38 = (2.8806/1.0269)(1.4-1)/1.4
T2 = 144.56
T1, T2 = temperature at the i/p and o/t of L.P. cylinder resp. P1, P2 = Pressure at the i/p and o/t of L.P. cylinder resp.
-
Weight of dry air;
= P*V/R*T kgs/hr
= ((1.026-0.7*0.06689)*736.2*104)/29.271*311.0
= 792.60 kgs/hr
Weight of vapour in = 0.0294*792.60 = 23.30 kg/hr
-
Heat duty = (flow rate * specific heat * temperature rise)
Dry air = 792.6*0.245(144.56-40) = 20304.19 kcal/hr Vapour = 23.30*0.45(144.56-40) = 1096.311 kcal/hr
Total = 21400.5 kcal/hr
Hot fluid
Cold fluid
Difference
High Temperature
Del t5=144.56
39.6
Del t2=104.56
Low temperature
40
Del t6=32.0
Del ta=8.0
Differen
ce
Del t3=104.56
Del t4=8.0
(Note- Temperatures in above table are in )
-
Thermo-Physical Properties Of Hot And Cold Fluids
-
Inlet Condition Of Air (To L.P. Cylinder) Pressure P1= 1.0269 kg/cm2
Temperature T1= 38.0 . RH = 0.7
Saturated pressure of vapour PV1= 0.06689 kg/cm2
-
LMTD
= (Del t2-Delt1)/ ln(Del t2(Del t1)
= (104.56-8.0)/ ln(104.568.0)
= 37.56
Weight of air per kg of dry air:
= (0.622*PV1*RH1)/(P1- PV1*RH1) (1)
= (0.622*0.06689*0.7)/( 1.0269- 0.06689*0.7)
= 0.0294 kg
-
-
-
Shell Side Calculations
-
Flow Area
As = (Ds*C*Bp)/(144*Pt)
= (6*0.105*3.590)/(144*0.4803)
= 0.0327 ft2
Ds = Diameter of shell = 6 inch Pt = Pitch of tubes = 0.480 inch
Do = outer diameter of tube = 0.375 inch Bp = baffle pitch = 3.59 inch
C = Pt-do = 0.480-0.375 = 0.105
-
Mass Velocity
Gs = W/As
= 11025/0.0327
= 337155.96 lbs/hr.ft2
W = weight of water = 5000*2.205 = 11025 lbs/hr
-
Reynolds No.
Res = Des*Gs/MYU
= 0.0248*337155.96/1.808
= 4624.70
Des = Equivalent Diameter
o
o
= 4*(Pt/2 * 0.86Pt 1/2 * d2 /4)1/2 * do
= 0.2977 inch = 0.0248 ft MYU = viscosity of water at 35
= 0.7191 cp = 1.808 lb/ft.hr
-
Shell Side Heat Transfer Coefficient Ho:
Ho = 0.36 * (K/Des) * (Des*Gs/MYU)0.55 * (C*MYU/K)0.33 * (MYU/MYUW)0.14
=0.36 * (0.3630/0.0248) * (4624.70)0.55 *
(1.0*1.808/0.3630)0.33 * 10.14
= 928.16 Btu/hr.ft2.
-
Shell side thermal resistance Ros = 1/Ho = 1/928.16 = 1.077*10-3
Shell side fouling factor, Rdo = 0.002 Thermal resistance Ro:
Ro = Ros + Rdo
= 1.077*10-3 + 0.002
= 3.077*10-3 hr..ft2
-
-
Tube Side Calculations
-
Flow area
At = (No of tubes * flow area per tube)/(No of passes
*144)
= (94 * 0.0730)/(1*144)
2
M= weight of air = weight of dry air + weight of vapour
= (792.6+23.3) * 2.205 = 1799.3 lbs/hr
-
Reynolds No :
Res = di * Gt/MYU
= 0.02541 * 37794.1/0.0505
= 19016.79
MYU = viscosity of air
= 0.0208 cp = 0.0505 lb/fthr
-
Tube Side Heat Transfer Coefficient Hi :
Hi = JH * (K/di) * (C*MYU/K)0.33 * (MYU/MYUW)
= 70 * (0.0183/0.02541) * (0.245*0.0505/0.0183)0.33 * 10.14
= 44.30 Btu/hr.ft2.
Referring to graph in Kerns book fig.24 page 834, JH corresponding to the Reynolds no 19016.79 is 70
-
Tube side thermal resistance Tube side fouling factor rdi = 0.001
ri = 1/ Hi
= 1/44.30 = 0.0225
Ri = ri + rdi
= 0.001 + 0.0225 = 0.0235
Tube wall resistance = rw
rw = d/(24*K) ln(d/(d-2*t))
= 0.375/(24*117) ln(0.375/(0.375-2*0.035))
= 2.75*10-5
-
Total resistance Rtotal :
= Ri * (Ao/Ai) + Ro + rw
= 0.0235 * (0.375/0.305) + 3.07*10-3 + 2.75*10-5
= 0.03199
-
-
Overall heat transfer coefficient U
U = 1/Total resistance
= 1/0.03199
=31.258 Btu/hr.ft2 = 152.61 kcal/hrm²°C
-
Pressure drop
-
Pressure drop shell side Ps
Refer the graph figure 29 of kern: corresponding to Reynolds No. friction factor F = 0.0025
Ps = F * G2s * Ds * (N+1)/(5.22 * 1010 * s * De * PHIs)
-
Mass velocity :
= 0.0476 ft
Gt = M/At
= 1799.3/0.0476
= 0.0025 * 337155.962 * 0.5 * 13/(5.22 * 1010 * 1* 0.0248 *1 )
= 1.45 psi = 0.09983 kg/cm2 F = friction factor
N = no of baffles
= 37794.1 lbs/hr.ft2
s = sp. Gravity
-
Pressure drop tube side Pt
-
Refer the graph figure 26 of kern: corresponding to Reynolds No. friction factor F = 0.0002
Pt = F * Gt 2 * L * N/(5.22 * 1010 * di * s * PHIt)
= 0.0002 * 37794.12 * 5.25 *1/(5.22 *1010 * 0.025*
0.0027*1)
= 0.4 psi
TABLE . COMPARISON OF PARAMETRS
Parameter
Calculated value
HTRI value
remark
Overall heat transfer coefficient
152.61
kcal/hrm°C
142.26
kcal/hrm²°C
Less than 10% of variation
Heat duty
21400.5 kcal/hr
21896 kcal/hr
Less than 10% of variation
Shell side pressure drop
0.09983 kg/cm2
0.049 kg/cm2
< 0.5 kg/cm2
Tube inside pressure drop
0.044 kg/cm2
0.053 kg/cm2
<0.1 kg/cm2
Parameter
Calculated value
HTRI value
remark
Overall heat transfer coefficient
152.61
kcal/hrm²°C
142.26
kcal/hrm²°C
Less than 10% of variation
Heat duty
21400.5 kcal/hr
21896 kcal/hr
Less than 10% of variation
Shell side pressure drop
0.09983 kg/cm2
0.049 kg/cm2
< 0.5 kg/cm2
Tube inside pressure drop
0.044 kg/cm2
0.053 kg/cm2
<0.1 kg/cm2
L = tube length per pass in ft N = no of baffles
PHIt = MYU/MYUW = 1
s = sp. Gravity
Pr = 4 * (N/s) * V2/(2 * g)
= 4 * 1/0.0027 * 0.162/(2 * 32.2 ) = 0.25 psi
PTt = Pt + Pr
= 0.4 + 0. 25
= 0.65 psi = 0.044 kg/cm2
-
-
DESIGN VERIFICATION
The software results look like figure no 6. The main parameter which will be verifies is the overall heat transfer coefficient, heat duty and pressure drop.
The difference between calculated value and HTRI value of overall heat transfer coefficient and Heat duty (heat exchanged) is less than 10% which is acceptable. Calculated value and HTRI value of shell side presure drop and tube inside presure drop are less than allowable pressure drop hence the values of the calculated parameters are varified.
-
CONCLUSION
At first thermal design is done by using kerns method. The input parameters are taken from specification sheet. The values of Overall heat transfer coefficient, Heat duty, pressure drop, are obtained.
HTRI software is used to verify analytical thermal design. It gaves close results as that of obtain from thermal design. The comparision between calculated values and software obtained values concludes the varification of the parameters.
The proven theoretical methods are in good agreement with the software results.
Fig 6: HTRI Result [13]
FUTURE SCOPE
HTRI incorporates a user-friendly interface that reduces time and increases efficiency. It can load a case from CD or a read only directory. If a user loads a case marked as read only, HTRI opens and runs the case. The results are given by the software are in less time as compared to manual calculations.
HTRI can estimate the shell weight. It has an approximation procedure for estimating the weight. It does not rigorously determine the material needed to construct the shell but rather divides the diameter into suitable portions. The values obtained are reasonable but not exact
Thus after all the input is put in the software, it generates the results which can further be used for analyzing them with required output. If found satisfactory user may move ahead with the design or he shall again change the input values and obtain the required results.
REFERENCES
-
Sadik kakac, Heat Exchangers Selection, Rating and Thermal Design, 2002. I.S. Jacobs and C.P. Bean, Fine particles, thin films and exchange anisotropy, in Magnetism, vol. III, G.T. Rado and H. Suhl, Eds. New York: Academic, 1963, pp. 271-350.
-
Fundamentals of Heat and Mass Transfer, by Theodorel L. Bergman and Adrienne S. Lavine. 7th edition page no. 705-748.
-
Process Heat Transfer, by D. Q. Kern, McGraw-Hill, 1950, the University of Michigan, 21 Nov 2007
-
G.N. Xie, Q.W. Wang , M. Zeng, L.Q. Luo, Heat transfer analysis for shell and tube heat exchanger with experimental data by artificial neural networks approach, Applied Thermal Engineering 27 (2007)
-
Jiangfeng Guo, Lin Cheng, Mingtian Xu, Optimization design of shell and tube heat exchanger by entropy generation minimization and genetic algorithm, Applied Thermal Engineering 29 (2009)
-
Ramesh K. Shah, Dusan P. Sekulic, Fundamentals Of Heat Exchanger Design, Rochester Institute of Technology, Rochester, New York Formerly at Delphi Harrison Thermal Systems, Lockport, New York &University of Kentucky, Lexington, Kentucky, 2003.
-
Standards of the Tubular Exchanger Manufacturers Association, Seventh edn., 1988, TEMA, Inc., 25 North Broadway, Tarrytown, New York 10591, USA
-
Andre L.H. Costa, Eduardo M. Queiroz, Design optimization of shell- and-tube heat exchangers, Applied Thermal Engineering 28 (2008 )
-
Paisarn Naphon and Tanapon Suchana et al. Heat transfer enhancement and pressure drop through the horizontal concentric tube
with twisted wire brush inserts, International Communications in Heat and Mass transfer, Volume 38
-
Arturo R L, Miguel T V & Pedro Q D. (2011) The Design Of Heat Exchanger, science research. Vol 3 pp 911-920
-
Leong kc & Toh kc (1998), shell and tube heat exchanger design software for educational applications, int.j.engng.ed. vol14 pp 217-234
-
Image of tube and shell heat exchanger https://images.app.goo.gl/f7bHtjLWKNNBACss6
-
Image genarated by Heat Transfer Research, Inc. , HTRI Xchanger Suite, [Online]. Available: https://www.htri.net/htri-xchanger-suite. [Accessed Jan 2019].
I want to learn HTRI software.plz share contact details and email id