
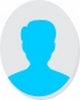
- Open Access
- Authors : Rahul V Huded
- Paper ID : IJERTV9IS120243
- Volume & Issue : Volume 09, Issue 12 (December 2020)
- Published (First Online): 11-01-2021
- ISSN (Online) : 2278-0181
- Publisher Name : IJERT
- License:
This work is licensed under a Creative Commons Attribution 4.0 International License
Thermal based Energy Recovery System Fuelled by Urban Waste
Rahul V Huded
(Jan. – Dec. 2019) Under Department of Mechanical Engineering, PES University Bengaluru-560085
AbstractThe main purpose of this work is to analyse the incinerator for burning municipal solid waste (MSW) to obtain the value of total heat transferred to the water flowing in the copper tube. This incinerator would be capable of burning solid waste including plastic materials and other stationery wastes produced in the locality. Optimum working conditions for the efficacy of incinerator are obtained as results from the steady state simulation of the incinerator using ANSYS Fluent. To achieve this control volume analysis was conducted, and various calculations were performed to find the waste characteristic properties, outlet temperature of water, pressure and velocity variations taking place because of controlled combustion of the MSW. This project work comprises study of the stages involved in the combustion of MSW; the potentiality of waste as a fuel from the knowledge of its analysis, heating value and quantity; selection of appropriate materials which have anti-corrosive and heat protective properties; economic considerations on the fabrication of the proposed unit; the combustion characteristics of MSW; heat recovery from the burning waste; control of waste incineration particulate emissions and techniques for the safe release of exhaust gases.
KeywordsWaste heat recovery, calorific value, Incineration, Gasification, meshing, grid independence test, natural convection.
-
INTRODUCTION
Plastics are astonishing materials made by mankind; they are lightweight, flexible and strong. If we thought that all of the plastic waste which is being collected from our homes ended up being recycled then we are substantially wrong. On a global scale, 78 million tonnes of plastic packaging gets produced every year and after a very short use, only 14% of it gets collected for recycling; another 14% is burnt in open air; 40% gets landfilled and the remaining 30% piles up polluting the environment. In an increasingly urbanized world, the price we pay to sustain our modern lifestyle is the generation of a colossal amount of disposable waste. Most of this waste traverses a small, unenviable journey, beginning from our dustbins and lying forgotten in a landfill on the outskirts of the city. In our country of India especially, methods of waste disposal are still quite old fashioned, and very nearly obsolete. Municipal Solid Waste (MSW) in India is first segregated, and then very little is rudimentarily recycled. But recycling is a dated process, as soon a recycled material is no longer fit for usage or further processing. A much larger fraction of the total garbage produced heads towards a landfill, where they are merely dumped away from the public eye. In some cases, they also undergo open air incineration, which is not only uncontrolled and unmoderated, but also hazardous and ineffective in the crude and rural manner in which it is
done. In such a scenario, consider this. The waste that we deem to be just an unwanted by-product of the contemporary lifestyle actually becomes a fuel to further it [4]. The fabled concept of waste to energy is actually already in practice in some parts of the world.This project will mainly deal with the design and analysis of an incineration unit on a smaller scale, which is a suitable representation of the energy harvester present in most WTE plants. It will produce quantifiable heat energy which can further be converted into useful forms. We have chosen this project as it directly deals with two pressing issues – the effective disposal of waste and meeting the energy needs of a typical large urban community.
-
SPECIFICATIONS
-
Waste Heat Recovery system
Waste heat recovery system A waste heat recovery unit is an energy recovery heat exchanger that recovers heat from hot flue gases or steam. The waste heat released from the combustion of polymeric/plastic waste is used for the purpose of heating water. One of the key areas for potential energy saving in existing systems is waste heat recovery. Waste heat recovery is so important because by reducing the amount of fuel used to produce heat in a boiler installation, heating efficiency increases, resulting in decreased fuel use [16]. By convective heat transfer the flue gas temperature reduces as it increases the feed water temperature. The key to efficient heat transfer rate however is the design of the chamber and heating tube, which needs to maximize total thermal contact with hot exhaust gases.
-
HVAF Chromium carbide coating
Cr2C2-NiCr coatings combat high-temperature wear due to the high wear resistance imparted by the hard carbide particles and the high temperature oxidation resistant nature of the Cr2O3 oxide formed over both phases [6]. High velocity sprayed chromium carbide ceramic coatings mitigate abrasive and erosive wear at temperatures up to 750°C. Solid waste incinerators typically emit hazardous air pollutants, including dioxin, furan, mercury, lead, cadmium, and other heavy metals. For this reason, incinerators are generally fitted with air pollution controls, such as afterburners to reduce carbon monoxide emissions, scrubbers to remove particulates and acid gases, filters (e.g., electrostatic precipitators, cyclones, or baghouses) to remove particulates [7]. A disadvantage is that the incinerator flue gas is a secondary source of pollution, which must be purified to remove a variety of harmful pollutants. The types of pollution controls used depend on the composition of the
wastes burned and on the design of the solid waste incinerator.
-
Purification system
The emission abatement of polychlorinated dioxins, furans and nitrogen oxides issued from MSW incineration is the major concern. These substances cannot be separated by conventional gas clean-up processes but are successfully removed through adsorption onto carbonaceous materials; many investigations for this purpose are still being carried out in the recent trends. Our ideology for purification and safe release of the exhaust gases involves a freely rotating ventilator induced with active carbon filter. Coriolis forces inside the cylindrical chamber rises the exhaust gases in a curved path line, thus heating the water flowing inside the copper helix tubing. The free to rotate ventilator affixed with carbon scrubbers adsorb the toxic impurities (furans, dioxins, CO), while providing a free flow for the flue gases. Carbon filtering is a method of filtering that uses a bed of activated carbon to remove contaminants and impurities, using chemical absorption. The ventilator ensures that over pressure is not built up in the chamber by maintaining proper aeration to the incinerator. Based on our survey, an overall cost estimation of our proposed incineration unit was obtained (Table 1.2).
-
Calorific value estimation
In this study, the potential for energy production and reduction of toxic greenhouse gas (GHG) emissions from municipal solid waste (MSW) was evaluated. In this paperwork, energy recovery from municipal solid wastes is examined. The fuel characteristics of solid waste components are reviewed. The energy potential of the solid waste sample collected from plastic recyclers in Nayandahalli, Bengaluru was then estimated. After lab experimentation, the gross calorific value is calculated at about 46.32MJ/kg. As an outcome, energy generation from MSW is shown to be environmentally beneficial and an economic alternative.
-
Definition of Boussinesq Approximation/p>
The model is observed to be a natural convection problem involving viscous compressible fluid flow. The density variation of the fluid at steady state temperature is negligible. The Boussinesq approximation is applied to the problem where the fluid varies in temperature from one place to another, driving a flow of fluid and heat transfer. The fluid satisfies conservation of mass, conservation of momentum and conservation of energy. In the Boussinesq approximation, variations in fluid properties other than density are ignored, and density only appears when it is multiplied by g, the gravitational acceleration. The Navier stokes equations govern the motion of fluids.
-
-
MATERIALS
Suitable materials are used for the inside wall of incinerator. The material should have high resistance to heat flow and should be able to withstand high temperatures of 8000C temperature and higher. (Clay materials made and fired into refractory bricks (fire bricks) are one of the best alternative materials suitable as lining for inside incinerator walls.)
The combustion chamber material is made up of steel (carbon steel, max 0.25% carbon) because it is readily available and has lower thermal conductivity. Mild steel is selected for the fabrication of many components in the incinerator. The material belongs to the group of low carbon steels which are relatively cheap and possesses good formability and weldability properties. As an alternative, to reduce heat losses from the burning waste, the combustion chamber can be properly insulated with clay of 70mm thickness, [9] the thermal conductivity of clay is 0.25W/m-
K. Other commercially used materials to build incineration chamber: TYPE 309 Stainless Steel; RA333 is a high chromium nickel base super alloy with outstanding resistance to high temperature oxidation and carburization.
Highly corrosive conditions are encountered in many industrial incineration and combustion processes. In plants for waste incineration, the charges contain high quantities of chlorine and sulphur compounds that have a strong corrosive effect. [5] The methods for protection against corrosion used so far, such as galvanic nickel-plating, overlay welding or thermal spraying of nickel-based alloys do not allow a significant increase of the process temperature above 400°C. Hence, the coating being applied in the interiors of the incineration chamber has to be given significance. Cold spray coating process uses high velocity metal particles which due to adiabatic shearing stability get plated onto the substrate. This is one good method which can be used for coating the incineration chamber.
-
Steady state simulation
To visualize the operation of the incinerator importantly the fluid flow inside the chamber at steady state and the temperature variations along the combustion process, simulation of a proportionate model was made using Ansys Fluent. Mesh on subparts has been depicted in section 3.3.2.
Best fit meshed models and residual plots for varied mesh inputs and parameter variations, showing convergence are shown in Figure 3.18. Information about boundary conditions and solution parameters are given in Table 3.1. The finite element mesh is used to discretize the CAD model into smaller elements or cells, over which the set of equations are solved. CFD preference was selected with cutcell method meshing to obtain a structured polyhedral mesh of the heat recovery system. Meshing influences the accuracy, convergence and speed of the solution, hence sufficient number of elements were imparted perpendicular to the wall surface in the direction of the flow to obtain the first element length as 0.249mm from the boundary layer surface. Mesh sizing was varied to perform grid independency test, residual behavior (Fig 3.18) was studied to check for continuity of the equations. Most consistent result parameters were evaluated in calculation of the heat recovery efficiency. To avert discretization errors, model was successfully meshed at over 0.25 million elements, the solver showed converging residuals. The components involved in the heat recovery system are named in figures
3.10 to 3.17. As meshing every component of the system was essential, the parts were named to imply boundary conditions for the convection process.
A cylindrical enclosure of the range 0.5-2m was created to observe the operation of incinerator and its effects on the surrounding fluid domain. Solid contours of the fluid domain showing variation in temperature, pressure and velocity of the gas spreading in the domain due to incineration process are depicted. The control volume was analysed by changing maximum element size up to 10mm for scaling the grid variations, face sizing was done to capture the proximities and curvature of the fluid domain for the resolution of fine meshing.
-
Boundary conditions and analysis
Taking all the mass balances in the fluid and thermal characteristics required for the actual combustion process into consideration, the model was meshed to subdivide it into 2,52,964 elements with 2,13,591 nodes. The solver is given with air and mass flow rate inlet, chamber wall, pipe wall conditions and all operating conditions. For the steady state analysis of the unit, air inlet (1m/s) and operating Boussinesq temperature were specified in the fluid domain boundary conditions. Aiding the convection at 8500C, mass flow rate for water entering the tube inlet is given as input: k-omega model with standard wall functions and SIMPLE first order upwind solution was used for the analysis. Cylindrical control volume was enlarged until 2m around the incinerator for carrying out parametric and grid analysis. The model operating conditions were specified and solver is standard initialized from air intake slits for green gauss cell based solution and the simulation is processed. As it is a natural convection process with negligibly varying fluid density, bouyancy driven flow(Boussinesq approximation) is being used for analysis. Results show that the output parameters do not vary after approximately 0.4 million elements. Air inlet velocity and mass flow rate of water (15-30 lpm) were varied to get optimum conditions at the water outlet. The results obtained from the solver are used to calculate the total heat transferred to the flowing water.
Successively smaller cell sizes for the fluid domain for the improvement of solution, the grid size was considered as the calculations approached convergence. The resultant monitor values (Fig 3.21 to 3.23) affecting the performance of the incinerator are plotted against total number of elements to establish independence of the mesh resolution. By increasing the domain (Fig 3.24) and mesh size further we can observe that the 4 million cell simulation results in a value that is within the acceptable range. Our values of interest are essentially the main outputs from the simulation, so pressure gradient, mass flow rates, maximum temperature etc. The refined mesh (Fig 3.18) gave converging and steady values after repeated iterations, residual RMS error values are typically less than 10- 5 and the monitor points of air intake velocity were tested for different input values (Fig 3.19 and 3.20) which reached a steady solution.
After extending and varying the fluid domain size, to reduce the influence of the number of grid size on the computational results, parametric study was performed. The important boundary conditions parameters pertaining to the incinerator were tested to see the effects of input conditions on the results. The simulation was run on progressively
finer grids by reducing the element size, parameters including flue gas temperature, chamber wall temperature and mass flow rate of air at the exhaust outlet were plotted against number of elements, the graph shows horizontal behaviour at over 0.25 million cells to give negligible differences between the solutions. The numerical solution was converging for the enlarged fluid domain; critical entities were evaluated in the calculatons as the mesh was seen to be grid independent. Mesh sizing and refinement was done to resolve the flow in the designed model such that boundary conditions are not affected by grid changes.
In the parametric analysis, studying of each operational parameters effect was required in order to determine the optimum scenario for achieving high energy efficiency. In this work, parametric analysis has been carried out for the designed incinerator. Two parameters were considered: mass flow rate of flue gas at exhaust outlet and incineration temperature. The effect of these parameters predicted by the simulation is presented in Figure 3.25 and 3.26.
An increase of air flow rate would be disadvantageous in most of the cases, mainly due to the dilution of the produced gas with the nitrogen introduced by air. This should be avoided as it leads to a substantial reduction in the heating value of the synthesis gas .It was observed that 1148K (8750 C) was the optimum operating temperature at which, the toxic dioxins formed in the exhaust gases due to waste incineration escape out from the composition and it was apparent that lowest moisture content in feed is desirable for maximum efficiency, thereby shredding and pre-treatment of the MSW is essential.
-
Equations
The The incineration (combustion) of carbon-based materials in an oxygen-rich environment (greater than stoichiometric), typically at temperatures higher than 8500C, produces a waste gas composed primarily of carbon dioxide (CO2) and water (H2O). Other air emissions are sulphur dioxide and nitrogen oxides. The inorganic content of the waste is reduced to ash. This is the most common and well-proven thermal process using a wide variety of fuels [3]. During the full combustion there is oxygen in excess and, consequently, the stoichiometric coefficient of oxygen in the combustion reaction is higher than the value 1. In theory, if the coefficient is equal to 1, no carbon monoxide (CO) is produced and the average gas temperature is 1,200K. The reactions that are then taking place are: C
+ O2 CO2 …(1.1) CxHy + (x+ y/4) O2 xCO2 +
y/2 H2O …(1.2) In the case of lack of oxygen, the reactions are characterized as incomplete combustion ones, where the produced CO2 reacts with C that has not been consumed yet and is converted to CO at higher temperatures. C + CO2
+ heat energy (J) 2CO (1.3).
-
Results and Discussion
Steady improvements of manufacturing techniques have led to an abundance of economic and powerful processing resources that are available to many different fields. Therefore numerical simulation methods that can be used
to model physical processes have gained high importance in the context of research and development. This is especially true for cases where relying on experimentation and measurements is either infeasible or prohibitively expensive. The species mass fractions at the fluid inlets and temperature conditions for the incineration process were setup. After refined meshing of the model, the input velocity and the thermal shell conduction conditions for the convection process were given to the solver, using k- omega model and standard wall conditions with cell zone conditions been specified, the solver was reinitialised and the calculation for steady state flow field was processed for more than 1000 iterations. The sectional view of the designed heat recovery system is shown in figure 4.1. To produce a more realistic image, ANSYS solver is moved past the traditional surface to renderings inside of a flow- field via temperature volume rendering (Fig 4.2) with which temperature variations and gradients can be visualized in one diagram. For instance, in the simulation results of the combustion chamber we not only see the temperature concentration based on colour; we see that areas majorly exposed to convection have a high gradient while open areas have low gradients.
Besides statistics and data collection techniques visualization is crucial for gaining insight into the data sets. The visualization presented in this thesis are primarily applicable to the results generated by computational fluid dynamics (CFD) simulations in Ansys that are used to predict the physical behavior of fluids and flue gases produced from the incineration of MSW. For each cell, physical properties are simulated by defining initial boundary conditions and solving partial differential equations that represent basic physical laws such as conservation of mass or energy. Fig 4.3 shows the pressure variation inside the incinerator chamber along its height caused due to the convection, interior pressure tends to gradually increase near the base of the incinerator.
Visualization techniques used to explore CFD simulation results are scalable with respect to different data set properties. So, to obtain higher resolution meshes which in turn increase the accuracy of a simulation, mesh sizing were made flexible by trying out coarser to finer cell geometries.
Therefore, visualization methods have to cope with higher geometric complexity when dealing with grids containing such cells. Increasingly complex physical phenomena can be simulated due to the development of new modeling methods [15]. The resulting data sets contain solutions not only for fluid flow but also for different kinds of thermal reactions. Again CFD data visualization methods have to be scalable, this time with respect to the number of physical attributes that are simulated for each grid cell. For the improvement of results, mesh refinement with successive smaller sizes is demonstrated in Fig 3.24, the fluid domain was enlarged around the incinerator and the parameters are analyzed.
As the mesh was made finer the solution approached convergence, graphs depicted in 3.2.6 show output parameters such as exhaust gas temperature (K), wall temperature (K), total mass flow rate of air (kg/s)
advancing to convergence at over 0.25 million cells for the incinerator model. This project work presents the gas flow of the waste incinerator using a simulation approach that incorporates Fluent for the turbulent reacting flow of gas plenum. Because the gas flow in the incinerator is created by the combustion gas released from the bed due to incineration of MSW, the computation was initialized by giving reliable data on the air velocity, burning temperature and gas composition. . The aforementioned simulation allows various parametric studies (Fig 3.25 and Fig 3.26) including variation of the parameters for the waste bed. With the development in the computational modelling of the waste bed, new simulation method has been reported (Ryu et al., 2002), which combines the models for waste combustion and for the gas plenum to evaluate the flow inlet/outlet conditions above the waste bed from the model predictions A possible reason for the fluctuations is the different ignition temperature for the variety of different wastes in the feed. This causes an uneven temperature distribution in the incinerator chamber during the initial stages of combustion. Figure 4.4 shows the calculated process rates in the combustion chamber as functions of distance from the fuel entrance. It is seen that during the first 0.45m along the length, only moisture evaporation occurs in the incinerator. At a location near the 0.45m position, a sharp rise in the devolatilization rate occurs as the bed temperature is raised above the threshold and volatile gases start to be released from the solid wastes. At this point, the moisture evaporation rate also rises sharply to a higher level as the bed is heated up by the ignition of the released volatile gases. The devolatilization rate, however, returns to a stable level (lower than the peak value) after a very short transient period; Fig 4.6 shows the calculated gas temperature distribution for the whole computation domain.
Fig 4.4 and Fig 4.5 show the intermediate results for each update of the input boundary conditions during the simulation. They depict the incident convection on the wall surface expressed i terms of temperature (K).The incineration temperature was initially assumed to be constant at 1124K (Boussinesq temperature).The temperature on chamber wall and due to gas emission(maximum 1148K) are determined by the flow pattern (Fig 4.5),the temperature profiles along the length of the incinerator are shown below in Figure 4.6. The measurements show a sharp temperature rise of the wall surface at a distance of 0.45m above the waste-fuel entrance.
To conceptualize the gas flow and determine the velocity effects in the varied control volume around the incinerator, air inlet velocity at the slits location present in the incineration chamber was analyzed over a range 0-1m/s. The average mass flow rate of the flue gas at the exhaust outlet of the incinerator was observed to be 2.64*10-4kg/s. In the Fig 4.6, the representation of the gas flow velocity vectors near the surface wall regions due to change in temperature inside the incinerator chamber is shown. Subsequently, the velocity profile of the fluid extending in the whole domain, the flow pattern and velocity path lines is observed in Fig 4.10. It includes gas velocity plane section, which asserts an average gas velocity of 0.384m/s.
Furthermore, the specific heat of the fluid and density are tabulated in table 4.1, the final temperature at the water outlet was seen to be 340.56K, and the results obtained from the simulation are used in the calculation of heat recovery caused due to thermal conductivity of the copper helix tubing. The results indicate that the gas flow and mixing inside the chamber is very complicated. Fig 4.9 shows 3-dimensional gas flow representation which will help to better understand the heterogeneous temperature distribution inside the incinerator as they will affect significantly the surrounding behavior and refractory coating wear. The temperature gradient creates negligible density difference between different layers of the fluid, buoyancy driven force becomes greater than viscous forces and fluid layer with lower density travels out through exhaust, to establish a natural convection circulation Rayleighs number for the gas is calculated as 35.067×106 which predicts the critical temperature gradient in the incinerator chamber.
This work illustrates the gas flow and temperature behavior in a small-scale utility incinerator for disposing hazardous solid wastes. In the future, heat transfer within the chamber will be included in this research. The numerical predictions and optimization will provide useful information for improved process control. The maximum effective chamber wall temperature was obtained as 1126K. The results are in comparison with the experimental results foreseen in our literature survey. The coefficient of thermal conductivity for the flue gas was seen to be 0.0145W/m-K.
-
Conclusions
In this paper, an attempt has been made to define and analyse the various functional operational and design parameters that control the effectiveness of solid waste disposal by incineration. The careful consideration of these system parameters by incinerator designers can lead to the installation and operation of incinerators for disposal of solid wastes without causing objectionable air, water or land pollution.
-
The model predicted quite satisfactorily the upper and average integral values of both the temperature and velocity fluctuations and allowed the interpretation of the observed oscillations.
-
After successive refinement of meshing quality, a steady state thermal and fluid flow analysis of the designed incineration unit, accompanied by calculation of Rayleigh number, interior pressure and temperature distribution due to the buoyancy driven
flow for the model is achieved with a valid approximation.
-
Improving the secondary air by the incorporation of ventilator is necessary to reduce the particle carryover to the boiler tubes by the high-speed gas stream and to increase the efficiency of heat transfer.
-
-
-
USE FOR FUTURE WORK
Incineration of municipal solid waste (MSW) has been well established for several decades. It mainly reduces the volume of the waste into inert ash and recovers energy for heat and electricity. It is currently the most popular technology for waste disposal in many countries. However, driven by increasing public concern and consolidated regulations on pollution, incineration technology still needs an extensive scientific approach in many areas of combustion and flue gas treatment.New methodologies can be incorporated as there is intense concern about the emissions of chemicals from incinerators, and the possible effects on humans and other organisms that result on exposure to these emissions. The central competent authority in Taiwan is currently planning a promotion policy for combining the district heating and cooling system with waste heat from all MSW incineration plants, which aims at a 30 % increase in the overall energy efficiency [18]. Modern incinerators are equipped with rigorous pollution control technologies. Most importantly, injection of fine activated carbon into flue gases helps in absorption of toxic pollutants like mercury, dioxin and furan. During the incineration, small particulates are entrained into the flue gases which can prove to be toxic at large exposures. Usage of electrostatic precipitators; Baghouse filters; Cyclone filters remove toxic particulates. By reaction of the flue gas with ammonia, oxides of nitrogen can be controlled. Flue-gas desulfurization and HCl removal can be achieved by the reaction of sulfur dioxide with finely powdered limestone (CaCO3) or lime [Ca(OH) 2] to form sludge containing gypsum.
12.Figures and Tables
ACKNOWLEDGMENT
This project would not have been possible without the kind support and help of many individuals and the faculty of our University. We would like to extend our sincere thanks to all of them. We consider ourselves privileged and would like to express our gratitude, and respect towards all those who guided us during our term at PES University. We are highly indebted to our guide Prof. Meghana Athadkar, Assistant Professor, Department of Mechanical Engineering, PES University, for the guidance and constant supervision. Prof.Meghana Athadkar, and our professors at PES University have been great role models both technically and morally. We thank Dr. K.S Sridhar, Chairperson, Department of Mechanical Engineering, PES University for his constant support and for providing a platform to carry out and conduct our work. I thank Dr. K.N Seetharamu and Dr.V.Krishna for their inestimable time and valuable inputs which were vital in completing our project. We also extend our profound gratitude to the faculty of PES University; without the knowledge they imparted over the semesters, the completion of this project would not have been possible. We are thankful to all the members of PES University for their cooperation and assistance. Finally, we would like to convey our regards to our family and friends for standing by us throughout the period of our project completion. Thank you for the unconditional support and guidance you have given us.
REFERENCES
With rapid urbanization and industrialization, affordable energy supply from fossil fuels has become a problem of great extent, due to the rising fuel prices and greenhouse gas emissions. Refuse plastic fuel (RPF) is becoming the center of research as it is a waste-to energy conversion concept and provides an alternative energy source. The minimum activation energy value for RPF blend was found out to be 15.753 kJ mol1 with a heating increment of 5
°C min1. Synthesized RPF found to require approximately 12 times less activation energy in comparison with PET and 410 times less than coal depending upon the coal type [21].
For Pakistan, PET and food waste can provide daily 11,550 RPF energy blocks each of 1 ton with 256 Million MJ of energy which give 71,000 MW of electricity daily that could fulfill energy gap in the country Energ from waste
(EfW) is a suitable method of waste management and is important for renewable energy production. South Korea currently recycles 57% of household waste and landfills 26%. The remaining 17% is incinerated, mainly for heat production. 3.4.1 Waste types and characteristics Solid wastes including HDPE plastic refuse from the municipality is collected by the recycling units, a sample of which was submitted for experimentation to obtain the gross calorific value. The different kinds of wastes include: Domestic-old papers, packaging, bottles, crockery wares, furnishing materials, garden trimmings. Institutional-schools, colleges, hospitals, large hotels and restaurants dumped plastic packaging bottles, containers, rubbish bins, old crates and some garbage and shopping bags.
The testing and estimation of waste properties is something that must be carried out, we did extensive research as most estimation of calorific values and other fuel properties are for conventional fuels. The calculation of calorific value of the waste to determine the heat contents can be carried out using Dulongs formula.
-
William.M.Vatavuk, Donald.R.van der Vaart, James.J.Spivey.2000.Incinerators, Research Triangle Institute.
-
Marie Elena Diaz, Prof. Nickolas J Themelis.2011. Cost/Benefit Analysis of Waste to Energy plant for Montevideo. Columbia:
Dept. of Earth and Environmental Engineering
-
Konstantinos Moustakas and Maria Loizidou;2010. Solid Waste Management through the Application of Thermal Methods.
National Technical University of Athens
-
Rohith BR. 2017.Times of India Article Bengalurus daily garbage generation.
/timesofindia.indiatimes.com/articleshow/61873003.cms?utm_source
=contentofinte rest&utm_medium=text&utm_campaign=cppst
-
Caterina Rusu, Malin Brodin. 2018.Coatings, (8) 353
-
Hindawi Publishing Corporation,2014 International Journal of Corrosion (2)306-505
-
A.Bosmans, I.Vandeeydt, D.Geysen, L.Helsen. 2012 Journal of Cleaner Production. (55) 10-23
-
S. Unnikrishnan, A. Singh.2010. Resources, Conservation and Recycling
-
A.J Ujam and F Eboh.2012 Thermal Analysis of Small Scale Municipal Solid Waste Fired Steam Generator, Journal of Energy Technologies and Policy (2)
-
S. Chattopadhyay.2009. Waste Management (2) 14491458
-
David A. Tillman, Amadeo J. Rossi, Katherine M. Vick.1981. Incineration of municipal and hazardous solid wastes.3rd ed. San Diego: Academic Press
-
Robert E.Zinn,Walter R.Niessen,1975.Commercial Incinerator Design criteria. Cambridge, Massachusetts.Arthur D. Little.Inc.
-
A. Mountouris .2006. Energy Conversion and Management (47) 17231737
-
C. Ryu, Y.B.Yang, V.Nasserzadeh & J.Swithenbank.2004.Themal reaction modeling of a large municipal solid waste incinerator, Journal of the air & waste management association. (52)1891- 1907,
-
Y.Yang, J.Rakhorst, M.A.Reuter, J.H.L.Voncken,1999 Analysis of gas flow and mixing in a rotary kiln waste incinerator.TU Delft,
Dept of Applied earth sciences
-
Waste heat recovery. 2008.Technology and opportunities, US industry 7-11
-
F. Ayaa, P. Mtui, N. Banadda, J. Van Impe. 2014 Design and Computational Fluid Dynamic Modeling of a Municipal Solid Waste Incinerator for Kampala City, Uganda. American Journal of Energy Engineering. (2) 80-86.
-
W.T. Tsai, Y.H. Chou .2006. Renewable and Sustainable Energy Reviews
-
Report on Waste to Energy by the World Energy Council, 2016
-
Janusz Wojtkowiak, Czeslaw Oleskowicz-Popiel. 2017.Investigations on hot water temperature changes at the pipe outflow, Poland,4th ed.