
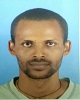
- Open Access
- Authors : Asefa Robsan Abebe , Liu Chao Hua
- Paper ID : IJERTV9IS040260
- Volume & Issue : Volume 09, Issue 04 (April 2020)
- Published (First Online): 16-04-2020
- ISSN (Online) : 2278-0181
- Publisher Name : IJERT
- License:
This work is licensed under a Creative Commons Attribution 4.0 International License
Study of Simulation Technology for Gas Metal Arc welding Robot using Robot Studio
Asefa Robsan Abebe 1*
School of Mechanical Engineering Tianjin University of Technology and Education, Tianjin 300222, P.R. China.
Liu Chao Hua 2
School of Mechanical Engineering Tianjin University of Technology and Education, Tianjin 300222, P.R. China.
Abstract: – This paper works on the” Study of simulation technology for gas metal arc welding robot using robot studio” on addressing some arc welding defects. The stated problems must be solved by deeply studying the parameters like arc travel speed, arc length, and arc time which to be observed from the simulation of virtual robot studio software.
The simulation will be done by importing solid work geometries which are table and workpiece for taking output data during virtual welding. After the simulation, each parameter value visualized in the MATLAB smart land welding software for remedies of lack of penetration, weld width, and lack of fusion defects specifically.
Finally, the two-software result integration should give the solution for the problem aforementioned and the virtual arc welding robot output solves the shop floor tasks.
Keywords:- Arc welding Robot, Welding Defects, Simulation, Parameters
- INTRODUCTIONWelding is the latest and intelligent industrial process used to save time, energy and money in the production automation line.[1][2] Whatever the first welding is innovated in 1960, the Arc welding usage was based on experience than science wise which is applicable in automotive, structural and bridge construction.[3][4] To fill the gap of lack of scientific welding and a few professional operator welding skill the well mechanized and equipped machine should have to implemented like robot arc welding. [1] Robot gas metal arc welding is usually known as a metal inert gas (MIG) or metal active gas (MAG) that sophisticate the base metal to coalescence by filler electrode melted at high heat concentration which drops as reel due to gravity into joint of parts and shield by a gas. [5]To more sophisticated, offline programming is necessary than manual welding. Robot studio is an offline-programming that uses an integrated technique in shop virtual welding floor depend on the level of automation with additional auxiliary.[6][7] Researchers used the teaching program for the reduction of reworking time and lack of skill how much the job is tedious using the conventional teaching method.[8] The offline programming is where the real environment job is going to be pursued using the editable and programmable language as a text file.[9] In this progress, the all activities performed is assisted by the auxiliaries of the robot system like Flex pendent-used for jogging and editing, IRC5 controller -the driver monitoring and controlling unit, Robot ware-ensure the performance of ABB robot and it is the heart for path configuration.[10]The industrial arc welding applicability due to the intensity and metal deposition rate which resume worn parts. Indeed, it
can restore the stress to weld while the parameters influencing the quality.[11][12] This welding used to adequately control geometry and defect welding like fusion, zone, profile, and properties. However, getting the welding quality difficult relative to another manufacturing process but the adaptability of gas metal arc welding robot with offline simulation made it applicable to the try trial and test traditional method. [13]
The metal gas arc welding process model, the droplets causing finger penetration based on the radius and the height of the molten pool.[14] The volume droplets of the molten pool inverse to velocity as doing for penetration.[15] For a case of fast production, welding increasing the speed that leads hump and undercut which another post fixing.[16]-[18]
For the source of current increases the penetration deep or shallow as the arc travel and voltage decrease.[19][20] Consideration of time in welding operation saves the economy through the weld line form starting to the endpoint, and the efficiency of time maintains the joint endurances. [21][22]. As stated, the real-time of the weld liquid to detect the seam gap many techniques have been used whereby the penetration reduced while the time is control.[23][24]
Near the welding point due to the strong arc, the droplets, partial liquid sink causing penetration while the remaining blow over form weld width. [25] The study stated, the metal transfer due to initial heat and temperature affect the weld width. [26] and it influences the shape of the pool width. [27][28] Generally, the paper contains the rest tasks: Related works based on review exists, the detailed explanation of each result and conclusion.
- RELATED WORKSSome related works have been researched to fix the usual problems with robot welding with different methods. Some of them stated: Suppose, the wire chemical composition and heat affected zone is taken as root to solve welding quality, for a valuable monitor of weld pool drop, and blow. [29] In the same manner, for the stability of welding and seam quality, the multi-frequency wave control has been used by peaking trailing two-wire current and the orthogonal experiments at mathematical analysis have been optimized. [30] As usual, the arc welding robot design system and analysis are researched for the propose of 3D simulation by theoretical based on OPEN-GL in C++. The robot simulation establishment is by the mathematical straight equation to a real-time robot. [31] For general knowledge the comparison selection of the industrial robot, different systems, and education-wise has been stated. Those are between Robot Guide-FANUC k.k., Robot Studio- AG, Rob Sim AG and CODESYS based onexperience and diverse decisive factors to analyze and evaluate.[32] There is also the study performed through a vision image processing camera that automates and intelligent seam tracking on gas arc welding robot for improving the quality of beads.[5] In the welding process industrial robot welding sometimes control the feature of the welding, penetration, joint of edge detection and welding size; arc welding sensor and program are used when the process is subject to excessive heat and fumes covers. [33] Obviously, Robot studio software is flexible in manufacturing CNC-machine and the transport system; the offline- programming helps the robot to load and unload jobs into the machine and essential to clarify the layout of the real floor.[34] The features of the robot studio affect the job of researchers by their characteristics and tool flexibility in the manufacturing process and in the education value they have. The automatic and integration it let for technology make the software easier.[35]Eventually, this paper simulates the virtual weld controlling the Arc Travel speed, Arc length, and Arc Time, then, the data will be taken as input for smart land welding results.
- SIMULATION OF VIRTUAL WELDINGThe simulation will be pursued by robot studio from the initial job of importing geometry from solid work software to robot studio station. At the station, from the library of ABB the IRC5 controller of 10 kg selected with My tool nozzle used for creating a virtual welding path. Since the programming is on PC (personal computer) the task offline is starts from workpiece adjustment, Robot ware system which controls the drive unit and Rapid language, creating work object which identifies the specific job, creating a path on workpiece prepared and change tool0 to My tool. Synchronizing the path configuration lets the simulation run and the control module to display for Rapid language that going to be edited as a text file format.
- Rapid Module DataThe main issue to be considered in this virtual welding simulation particularly through three parameters mentioned above study as the real robot system; the data of those parameters observe by changing per the simulation period. Accordingly, the data clarifies the phenomena per the value changed while the change is simultaneous or interchangeable between speed and arc length as shown in Table-I.
- Robot Studio Simulation Results
The Arc Travel speed magnitude affects as it reduces the lag of time as its fast time consumption occurs. The arc length matters the arc voltage depends on the position of the z-axis, as the too near or far; both positions are adjusted in the RAPID module.
Fig.1. Illustrates the robot simulation configuration which moves along the welding path to have an output of data on the RAPID Module while Fig.2. Shows at -2mm causes sticky and resistance to moving forward which is a reason for high time to small and fast speed. Fig.3. and Fig.4. At a datum (+1mm and +2mm) of my tool nozzle shows time lag and slow gun nozzle motion; the relation of speed and arc voltage is proportional.
Fig.1.Robot Simulation
Fig.2. Too near virtual nozzle to part.
TABLE I. WELDING SIMULATION DATA
S.No. Speed (v) Zone (z) Time (s) Arc-Len Z-axis (h) Speed/ TCP (deg/s)
Acc. m/s 1 5 5 223.2 -2 0.49 204.76 2 5 5 620.2 +1 1.19 200.1 3 5 5 619.8 +2 1.19 202.13 4 10 10 245.4 -2 2.39 322.66 5 10 10 309.1 +1 2.39 528.08 6 10 10 308.9 +2 2.39 529.04 7 30 30 101.7 -2 7.16 1722.28 8 30 30 102 +1 7.16 2744.67 9 30 30 101 +2 7.16 2745.54 10 50 50 60.3 -2 11.93 2480.59 11 50 50 61 +1 11.93 2610.66 12 50 50 60.1 +2 11.93 4988.74 Fig.3. Appropriate Arc Length
Fig.4. Too wide the virtual nozzle from a part.
- THE RESULT OF MATLAB SIMULATIONAs stated in abstract the next task is observing the three parameters of data taken in the simulation of smart land welding MATLAB to observe the factors. It will be pursued after the magnitude of the arc travel speed, Arc time and position of my tool or pointed to the welding joint. As mentioned in Table-I the movement of the tool along the path, the position of the nozzle too near or too far, the arc voltage magnitude, and the too lag or too fast of time matters the welded parts bead geometry.
- Arc Travel speed and Arc Voltage powerFig.5a and Fig.5b. shows the red color point is mid contour and the yellow color line shows the desired depth between two parameters while the arc voltage is too high as it is moving from blue color line to red color line along the gun nozzle moving direction.Fig.5a. Travel speed vs Arc voltage powerFig.5b. Travel speed vs Arc voltage power
- Arc Travel Speed and Arc Voltage vs PenetrationHence, as the speed of tool movement and the arcthe voltage which is known as arc length decrease and near respectively, the penetration of workpiece is deep whereby the speed of nozzle too fast and power is too small due to the arc length too far from the base metals, the penetration is too shallow as of Fig.6a and Fig.6b and the surface 3D show the penetration is too deep as it moves from blue color surface to the red color surface end high power 2500 J arc length.Fig.6a. Penetration Depth
Fig.6b. Penetration Depth
- Width welding vs Arc Travel speed and Arc Voltage Even though the width of weld is affected by the travel speed and power of arc voltage as doing for penetration, too flat width weld formed while the time slag or travel speed is slow and arc voltage or the arc length is too far. Fig.7a. Vice versa during the value of time, travel speed and arc length are increasing the width weld created is the slim shape and Fig.7b. shows, the width weld determined for speed 5m/s, arc voltage 2000J and melting temperature looks like flat. As shown in the Fig.7c. with the value of speed 60m/s, arc length 2000J, and melting efficiency of temperature 23 looks like needle shape. Considerably, the causes of those three parameters tested even if they are a reason for lack of fusion between two fillets going to be welded.Fig.7a. Width weld to travel Speed and Arc voltageFig.7b. Flat Shape Width Weld SizeFig.7c. Slim Shape Width Weld Size
- Melting Efficiency
While the paper concluding the results of the simulation, robot studio and the smart land welding MATLAB output, the three parameters effect have been seen and they have their events during the welding process. Causing of over penetration or lack penetration, blow of weld pool that being a reason for lack of fusion and weld width. Due to too high magnitude or too small magnitude of input added now, their efficient product will be re-filled for better melting efficiency.
Fig.8. Shows, the yellow line color indicates the desired depth, the white dot circle contour mid-point of the desired depth, and the 3D surface show as the desired travel speed and arc voltage or the appropriate arc length is set, the melting efficiency of the part to be welded is looks better from the blue color surface to the red color surface inward. And, the Fig.9. shows, the maximum fusion at the essential penetration, required fusion and arc blow, form the necessary bead geometry.
Fig.8. Melting Efficiency
Fig.9. Maximum Fusion Zone
TABLE II. WELDING EFFICIENCY SIMULATION DATA
s.n Thick. M.eff. Arc.V/w Arc.Tr/mm/s Sens./um/w 1 1mm 0.42 467 20.7 2.68 2 3mm 0.47 3702 20.6 0.85 3 6mm 0.48 11005 15.5 0.56 4 9mm 0.47 11005 7 0.83 5 12mm 0.46 11005 3.9 1.13 6 15mm 0.46 12004 3.3 1.08 The table and Fig.10 detail about, the influence of the arc voltage and arc travel while the robot is moving along the desired path accurately. The melting efficiency (M.eff.) of the base metal that negligibly changes incorporate the thickness of weldable, beside of those objectives; meanwhile, the thickness increase to the redline, the parameters robot arc welding provided speed(arc.Tr) decrements and the arc power(arc.V) increments. The sensitivity(sens.) of fusion on the seam tracking as doing as the arc Travel speed while opposites to arc length.
Fig.10. Melting Efficiency Simulation
- CONCLUSION
Generally, in this paper, the whole work presented which concerned with the factors that have been stated on the first page with their remedies to overcome the problems. The integration of the two-software provided to set easily the variables influencing the bead geometry and help to manage the problems along the seam path. Besides, the three parameters factor they have also observed; the proportionality of arc travel speed and arc length inversely matter arc time. Through the study of the performance from the simulation of robot studio to the MATLAB smart land welding virtual welding perspectives the figure, the result has been proven.
REFERENCES
- Complete Guide To Robotic Welding, What Is Robotic Welding, By Brian Reed On December 13, 2017.
- A Welding Quality Detection Method For Arc Welding Robot Based On 3d Reconstruction With Sfs Algorithm Int J Adv Manuf Technol 94:12091220, 2018.
- Theoretical Investigation Of Penetration Characteristics In Gas Metal- Arc Welding Using Finite Element Method, Subodh Kumar, And S.C. Bahadur, Volume 26b, June 1995-611.
- Applications Of Robotics In Welding Tanveer Majeed, Mohd Atif Wahid, Faizan Ali International Journal Of Emerging Research In Management &Technology Issn: 2278-9359 (Volume-7, Issue-3).
- Seam Tracking Of Intelligent Arc Welding Robot Khadijah Daeinabi, Mohammad Teshnehlab Proceedings Of The 6th Wseas Int. Conf. On Systems Theory & Scientific Computation, Elounda, Greece, August 21-23, 2006 (Pp161-166).
- The Corporate Technical Journal Of The Abb Group Special Robotics Report,30 Years In Robotics Page 6, Applications Stories Page 10, Virtual Technology Page 62.
- Programming Abb Industrial Robot For An Accurate Handwriting, Abigo Izabo, Tarig Faisal Mahmud Iwan, Hm Aa Al-Assadi2, Hanif Ramli; Isbn: 978-1-61804-094-7,2012.
- Direct Off-Line Robot Programming Via A Common Cad Package Pedro Neto, Nuno Mendes, 3030-708, 2013.
- Research And Realization Of Assistant Off-Line Programming System For Thermal Spraying, Chaoyue Chen, 11 Sep 2018.
- Robot Ware Industrial Robot Controller Software Irc5 Pr10259en_R2 Care Of. Printed In Sweden By Westerås Media Produktion, Västerås,2004.
- An Evolutionary Approach To Parameter Optimization Of Submerged Arc Welding In The Hard Facing Process, Patnaik, Amar Biswas, Sandhyarani Mahapatra, S.S., Vol. 2, No. 4,(2007) Pp.462483.
- Real-Time Measurement Of Width And Height Of Weld Beads In Gmaw Processes Jesús Emilio Pinto-Lopera, José Mauricio S. T. Motta And Sadek Crisostomo Absi Alfaro, 2016, 16, 1500.
- Through-Arc” Process Monitoring Techniques For Control Of Automated Gas Metal Arc Welding, Damn Barborak, Chris Conrardy, Bruce Madigan, And Troy Paskell, May 1999.
- Theoretical Investigation Of Penetration Characteristics In Gas Metal- Arc Welding Using Finite Element Method, Subodh Kumar, And S.C. Bahadur, Volume 26b, June 1995 -611.
- Effects Of Welding Velocity On The Impact Behavior Of Droplets In Gas Metal Arc Welding Jiecai Feng, Liqun Li , Yanbin Chen, Zhenglong Li, Hao Qin, Ying Li, 212(2012) 21632172.
- Predicting Of Bead Undercut Defects In High-Speed Gas Metal Arc Welding (Gmaw) Wen-Jing Xu, Chuan-Song Wu, De-Gang Zou, 2008, 2(4): 402408.
- Understanding Bead Hump Formation In Gas Metal Arc Welding Using A Numerical Simulation. Metallurgical And Materials Transactions Cho M H, Farson D F. B, 2007, 38(2): 305319
- Prevention Of Humping Bead Associated With High Welding Speed By Double-Electrode Gas Metal Arc Welding, C. S. Wu Z. H. HuL. M. Zhong, (2012) 63:573581.
- Microstructural Characteristics On Bead On Plate Welding Of Aisi 904 L Super Austenitic Stainless Steel Using Gas Metal Arc Welding Process, P.Sathiya, S.Aravinda, P.M. Ajith, B.Arivazhagan And A.Noorul Haq, Vol.2, No.6, 2010, Pp. 189-199.
- The Effect Of Gas Metal Arc Welding (Gmaw) Processes On Different Welding Parameters Izzatul Aini Ibrahim1, Syarul Asraf Mohamat,Amalina Amir, Abdul Ghalib, 41 ( 2012 ) 1502 1506
- Scheduling For An Arc-Welding Robot Considering Heat-Caused Distortion H-J Kim, Y-D Kim, And D-H Lee, (2005) 56, 3950.
- Heuristics For Single-Pass Welding Task Sequencing. Int J Prod Res,Kim K-Y, Norman Ba And Nnaji Bo 40: (2002) 27692788
- Research On Weld Pool Control Of Welding Robot With Computer Vision H.Y. Shen, H.B. Ma, T. Lin, And S.B. Chen, 34/6 (2007) 467 475.
- A Study On A Vision Sensor-Based Laser Welding System For Bellows Lee, S.K., Chang, W.S., Yoo, W.S. And Na, S.J. (2007), Vol. 19 No. 4, Pp. 249-55
- Detection Of Weld Pool Width During Strong Arc Disturbance Environment, Liangzheng Jiang And Xiangdong Gao Vols. 201-202 (2012) Pp 379-382.
- Study On Dc Welding Parameters Of Al-Alloy Shaping Based On The Arc-Welding Robot, Du Naicheng, Hu Shengsun, Yang Xuemei, And Feng Sheng Qian 2009-03-11 Pp 43-46
- Weld Pool Weld Width Prediction Based On Artificial Neural Network Liu Xiaogang, Liu Leting, Vols 462-463 (2014) Pp 171-174.
- Theoretical And Experimental Investigation Of The Gas Metal Arc Weld Pool In Commercially Pure Aluminum: Effect Of Welding Current On Geometry Farzadi A, Morakabiyan Esfahani M, Alavi Zaree Sr, (2017) 24: 25562564.
- Weld Control Possibilities In Arc Welding Journal Of Vibroengineering. Volume 15, Issue 1. Issn 1392-8716. March 2013.
- Research Of A Multi-Frequency Waveform Control Method On Double-Wire Mig Arc Welding Ping Yao And Kang Zhou Appl. Sci. 2017, 7, 171.
- Design Of Simulation For Arc Welding Robot Based On Opengl, By Chen Su-Li, Vols. 602-605 (2014) Pp 125-127.
- Comparative Selection Of Industrial Robot Simulation Systems For Educational Purposes, Duko Luka, Vogel Sanger Strasse 295, 50825, Vol. 15, March 2016.
- Robotics Arc Welding Sensor And Programming In Industrial Application International Journal Of Mechanical And Materials Engineering (2015)
- Off-Line Programming And Functioning Simulation Of Robotic Flexible Manufacturing Cell For Part’s Turning By Ivan Andrei Mario1, Nicolescu Florin Adrian, Avram Georgia Cezara, And Mantea Theodor Adrian Vol. 760 (2015) Pp 213-218.
- Technology And Applications Of Abb Robotstudio By Christine Connolly, 36/6 (2009) 540545.