
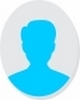
- Open Access
- Authors : O. M. Elhefny , R. A. Aboelnasr , F. R. Gomaa
- Paper ID : IJERTV11IS010076
- Volume & Issue : Volume 11, Issue 01 (January 2022)
- Published (First Online): 01-02-2022
- ISSN (Online) : 2278-0181
- Publisher Name : IJERT
- License:
This work is licensed under a Creative Commons Attribution 4.0 International License
Study Dynamic Characteristics of Milling Tool Holder by Experimental and Theoretical Work
O.M. Elhefny
Instructor,
High Institute for Engineering and Technology, Elmahalla Alkobra, Egypt.
R.A. Aboelnasr
Assistant Professor,
Production Engineering and Mechanical Design Department, Faculty of Engineering, Menoufia University, Shebin El Kom, Egypt
F.R. Gomaa
Professor,
Production Engineering and Mechanical Design Department, Faculty of Engineering, Menoufia University, Shebin El Kom, Egypt.
Abstract: Vibration problems often occur in manufacturing processes during metal cutting. vibration level depends upon many parameters such as design of machine and tool structure, material of work piece and tool and fixture of (tool tool holder) structure. As a result of vibration, the tool life is reduced, noise appears, and the surface is poorly finished. In this paper an assessment of dynamic characteristics was carried out by experimental modal analysis and Theoretical modal analysis by simulated data using ANSYS program. A comparison was made between the two methods and the difference in the results of both of them was clarified.
Keywords: Vibration -modal analysis -dynamic characteristics finite element method machine tool.
-
INTRODUCTION
In order to obtain a high surface quality and precision of the workpiece, the problems of vibration caused during the cutting operations in the manufacturing operations must be overcome. Hung J et al. Suggested that the machining performance of a machine tools jointly determined by the structure of the machine tool, the tool spindle and the dynamic characteristics of machine tools are expressed in different forms and with different frequency ranges, such as the low-frequency structural mode and the high-frequency instrument mode [1- 3]. Occurrence of chattering has an initial occurrence condition. Chatter generates during cutting and its values increase continuously Therefore, it is feasible to discover and control the chatter in the initial period of its occurrence. The machine tool has multiple degrees of freedom vibration system and chatter occurs at the natural frequency of one of the two final execution parts. the system is transformed into a single-degree-of-freedom chatter model with executing components to simplify the model. One or two chatter active bodies can be analyzed according to specific conditions in actual engineering applications. The cutting chatter system can have two chatter active bodies. With different cutting parameters, chatter can occur at different natural frequencies. Therefore, combined with the actual situation at the scene, we should pay enough attention to the optimization of machine vibration resistance and chatter monitoring [4].The holder is an affective parameter in cutting process so that Fleischel et al estimated the dynamic behavior of the whole cutting system
consisting of spindle, tool holder, tool and work piece. Therefore modal and operational vibration analyses were performed to describe the damping and operational characteristics of two competing tool holder technologies, namely heat shrink (HS) and hydraulic expansion (HE). A modal and operational vibration analysis on three different machining centers showed that HE technology has better damping properties which implies lower operational vibrations and reduced noise emission compared to HS [5].
By the way Benattia et al analyzed the influence of the perpendicularity of the spindle of the milling machine on the machined surface. The study was conducted by computer simulation tests and experimental part using surface condition monitoring instruments, and showed that the presented model could thus be integrated into systems computer-aided design and computer-aided manufacturing. Finally, the physical and statistical parameters of roughness during milling at position 90 confirmed that when the defect of the perpendicularity is eliminated to the maximum, the best surface conditions are obtained. They Recommended that it is better to use the vertical spindle milling machines as the effect of the angle of inclination of the spindle axis influences the surface quality generated and the roughness of the surface obtained by this process must be improved. The change in run out sizes should be limited to a short interval. The modeling of the vibrations is also possible from these data and the dynamic behavior of the active part (tool, tool holder of the spindle, and angle of inclination) can be analyzed. The vibration effect of the machine can be explained by superimposing the vibratory motion on the nominal peripheral of the milling operation [6]. In order to estimate the dynamic characteristics of system, modal analysis technique can be effectively used. Estimation of machine tools modal parameters is very important in service. the parameter estimation is carried out by experimental Modal Analysis (EMA), under artificial excitation using an impact hammer or shaker tests, at rest to control machining stability more efficiently [7-8]. The input and output data are measured from the frequency response functions (FRFs) of the structure, which represents the relationship between the excitation and vibrational response of the structure, Conditional parameters are specified [9-11]. Maamar et al developed a robust modal identification
procedure of a machine tool, during machining. In service, structural modes are weakly present and masked by strongly dominant harmonic components, which can induce a large error in the estimated values. The transmissibility Function- Based (TFB) method has been carried out in order to identify modal parameters of a machine tool, in machining conditions. Results demonstrate that the TBF method is a particular OMA approach by its original ability to eliminate spurious poles and to provide an accurate prediction of modal parameters in the presence of preponderant harmonic components. The modified Enhanced Frequency Domain Decomposition method (EFDD), which is based on white noise excitation assumption, is considered for a comparison purpose. The presence of harmonics is reduced when considering information about the
Fig. (1) Experimental setup and data acquisition system for holder only.
applied cutting force and the distinction between harmonics and structural poles is performed using three selection criteria [12]. Recently, Devriendt et al proposed the Transmissibility Function-Based (TFB) method. The authors demonstrated its original ability to eliminate harmonic components and its independence from the excitation nature [13-15]
From the theoretical stand point finite element method plays a vital rule in modal analysis. The FEM can be applied in solving the mathematical models of many engineering problems, from stress analysis of truss and frame structures or complicated machines, to dynamic responses of automobiles, trains, or airplanes under different mechanical, or electromagnetic loading. The finite element method (FEM), or finite element analysis (FEA), is based on dividing a complicated object into smaller and manageable pieces. computer-aided design (CAD) using computer graphics is used to design a product instead of hand drawing and computer simulations using computer-aided engineering (CAE) software is also nowadays used to analysis the design instead of hand calculations. Many commercial programs have become available for conducting the FEA like ANSYS work bench [16-19].
-
EXPERIMENTAL PROCEDURE AND SET UP:
To get the experimental data, an accelerometer of type B&K Tri-Axial Piezoelectric Type 4506 was used. the system wasexcited though an impact hammer of type B&K Type (8202). The function FRF was obtained by data acquisition B&K Data Acquisition Type 3160 using enhanced domain decomposition technique to estimate the dynamic characteristics of the tool holder (natural frequency and
[(m/ s² )/N ] [(m/ s² )/3.6
3.2
2.8
2.4
2
1.6
1.2
800m
400m
0
[(m/ s² )/3.6
3.2
2.8
2.4
2
1.6
1.2
800m
400m
0
N] Frequency Response H 1(R esponce,Force) – Input1 (M agnit ude)
Working : Input : Input : F FT A nalyzer
N] Frequency Response H 1(R esponce,Force) – Input1 (M agnit ude)
Working : Input : Input : F FT A nalyzer
3.6
3.2
2.8
2.4
2
1.6
1.2
800m
400m
5 10 20 50 100 200 500 1k 2k 5k 10k 20k
[Hz]5 10 20 50 100 200 500 1k 2k 5k 10k 20k
[Hz]0
[dB /1.00-4
-8
-12
-16
-20
-24
-28
-32
-36
-40
[dB /1.00-4
-8
-12
-16
-20
-24
-28
-32
-36
-40
] Coherence(R esponce,Force) – Input Working : Input : Input : F FT A nalyzer
] Coherence(R esponce,Force) – Input Working : Input : Input : F FT A nalyzer
-4
-8
-12
-16
-20
-24
-28
-32
-36
5 10 20 50 100 200 500 1k 2k 5k 10k 20k
[Hz]5 10 20 50 100 200 500 1k 2k 5k 10k 20k
[Hz]-40
Frequency Response H 1(R esponce,Force) – Input1 (M agnit ude) Working : Input : Input : F FT A nalyzer
5 10 20 50 100 200 500 1k 2k 5k 10k 20k
[Hz]Fig. (2) FRF Results for holder only.
Coherence(R esponce,Force) – Input Working : Input : Input : F FT A nalyzer
5 10 20 50 100 200 500 1k 2k 5k 10k 20k
[Hz]Fig. (3) Coherence diagram for the holder only.
damping ratio). The measurements were made for holder only and also (tool- tool holder) structure.
-
Experimental Set up for the Holder only:
The measurement was carried out on the MT3 ER32Taper holder which consists of three components (main shaft, collar and stopper) as shown in fig 1 according to the following procedure:
The too holder was hanged by a spring on a stand Let the system fixed from the holder shank and free from tool direction
An accelerometer was fixed on the stopper.
An impact hammer is used to give the excitation to the system.
Measurements were obtained by data acquisition.
Table (1) Damping natural frequency results and vibration
amplitude for holder only from experimental work.
Modal test result
Mode no
Damped frequency (Hz)
Vibration amplitude [(m/)/]
Damping ratio
%
1
2750
1.7
0.82
2
3050
3.8
0.71
3
3800
4
0.412
4
5150
3.3
0.518
5
5600
1.9
0.432
-
Experimental Procedure for the (Tool Tool Holder) Structure:
-
The measurements were taken like the holder only procedure where (the tool-tool holder) structure was hanged
Let the system fixed from the holder shank and free from tool direction as shown in fig 4.
-
The accelerometer was fixed on the stopper.
-
System excitation by the impact hammer.
-
Results taken by data acquisition.
-
-
Fig. (4) experimental setup and data acquisition system for (tool-tool holder) assembly.
-
Modeling for Holder Only:
For the used tool holder type is MT3 ER32Taper. alloy steel was used for toolholder component material.
-
Modeling Procedure:
-
Construction 3D model by geometry using solid work software as fig. 7.
-
Input Material properties of holder components as table 4
-
Selection Boundary conditions (fixed top of main shaft).
-
Automatic Mesh selection for all component of tool holder.
-
Give solution order to the program
[(m / s² )/7
6
5
4
3
2
1
0
[(m / s² )/7
6
5
4
3
2
1
0
N ] Frequency R espo nse H 1(R espo nce,Fo rce) – Input1 (M agnit ude)
Wo rking : Input : Input : F FT A nalyzer
N ] Frequency R espo nse H 1(R espo nce,Fo rce) – Input1 (M agnit ude)
Wo rking : Input : Input : F FT A nalyzer
[(m / s² )/N ]Frequency R espo nse H 1(R espo nce,Fo rce) – Input1 (M agnit ude) Wo rking : Input : Input : F FT A nalyzer
7
6
5
4
3
2
1
5 10 20 50 100 200 500 1k 2k 5k 10k 20k
[H z]5 10 20 50 100 200 500 1k 2k 5k 10k 20k
[H z]0
5 10 20 50 100 200 500 1k 2k 5k 10k 20k
[H z]Fig. (5) Frequency vs Amplitude for tool- holder assembly
[dB /1.000
-4
-8
-12
-16
-20
-24
-28
-32
-36
-40
[dB /1.000
-4
-8
-12
-16
-20
-24
-28
-32
-36
-40
] Coherenc e(R esponce,Force) – Input Working : Input : Input : F FT A nalyzer
] Coherenc e(R esponce,Force) – Input Working : Input : Input : F FT A nalyzer
-4
-8
-12
-16
-20
-24
-28
Coherenc e(R esponce,Force) – Input Working : Input : Input : F FT A nalyzer
Fig. (7) tool holder geometry.
The modal analysis has been done to estimate natural frequencies to find time consuming when damping ratio is constant and equal 0.09. A sample of mode shape result from the model is shown in fig. (8).
Table (3) Mechanical properties of alloy steel.
Mechanical Property
Value
Density (kg/m^3)
7600kg/m^3
Modulus of elasticity(MPa)
233000
Poissons ratio
0.3
Bulk modulus (Mpa)
/td>
194100
Shear modulus(Mpa)
896000
Mechanical Property
Value
Density (kg/m^3)
7600kg/m^3
Modulus of elasticity(MPa)
233000
Poissons ratio
0.3
Bulk modulus (Mpa)
194100
Shear modulus(Mpa)
896000
-32
-36
-40
5 10 20 50 100 200 500 1k 2k 5k 10k 20k
[Hz]5 10 20 50 100 200 500 1k 2k 5k 10k 20k
[Hz]5 10 20 50 100 200 500 1k 2k 5k 10k 20k
[Hz]Fig. (6) Coherence measurements for tool- holder assembly.
Table (2) Damping natural frequency and vibration amplitude for (tool-tool holder) assembly from experimental work.
Modal test result
Mode no
Damped frequency (Hz)
Vibration amplitude [(m/)/]
Damping ratio%
1
1900
2.5
0.78
2
2500
1.3
0.67
3
2750
1.9
0.528
4
2900
7.5
0.517
5
3050
4.5
0.804
-
-
-
-
FINITE ELEMENT MODELING USING ANSYS
SOFTWARE:
The modelling was carried out for the holder only and tool-tool holder assembly
.
Fig. (8) sample of mode shapes of holder.
Fig. (9) Amplitude of the first ten modes shapes for holder.
Table (4) damped natural frequency, damping ratio and maximum deflection of holder only.
ANSYS results
Mode No.
Damped Frequency
(Hz)
Damping Ratio%
Maximum deflection (mm)
1
5639.9
9.9877e-003
16.216
2
5662.1
9.9876e-003
82.13
3
6087.
9.9661e-003
235.3
4
6208.7
9.9668e-003
244.6
6
6230.8
9.9537e-003
409.1
7
6250.4
9.9498e-003
392.5
8
6317.7
9.9119e-003
385.79
9
6344.
9.9389e-003
109.51
10
6369.2
9.925e-003
251.02
-
Modeling for Tool – Tool Holder Assembly:
By adding the tool to the last system and repeat the same procedure. Geometric model for the tool-tool holder assembly is shown in the fig. (10). The used material for the tool was high speed steel (HSS). Tool material properties are shown in table (5).
Table (5) Mechanical properties of highspeed steel.
Mechanical Property
Value
Density (kg/m^3)
7700kg/m^3
Modulus of elasticity (MPa)
210000
Poissons ratio
0.28
Bulk modulus (Mpa)
159000
Shear modulus (Mpa)
820000
Fig. (10) tool holder assembly.
After carrying the model analysis at constant damping ratio equal 0.09 to estimate natural frequencies and damping ratio as in table 4 and a sample of mode shapes as in fig 11.
Fig. (11) A sample of mode shapes of tool-holder system
Fig. (12) Amplitude of the first ten modes shapes for Tool holder assembly.
Table (6) Damped natural frequency, damping ratio and maximum deflection for tool holder assembly.
ANSYS results
Mode No.
Damped Frequency [Hz]
Modal Damping Ratio
Maximum deflection (mm)
1.
2424.8
9.9625e-003
238.39
2.
2464.3
9.9591e-003
128.18
3.
5639.5
9.9731e-003
33.207
4.
5663.6
9.9733e-003
63.112
5.
6515.7
9.9432e-003
193.4
6.
6561.3
9.8961e-003
119.24
7.
6567.6
9.8959e-003
329.32
8.
6589.5
9.897e-003
327.10
9.
6606.6
9.8976e-003
43.716
10.
6615.7
9.9003e-003
427.29
-
-
RESULTS AND DISCUSSION:
-
From experimental modal analysis results its found that in the case of carrying the analysis out on the holder only, a group of peaks and frequencies values appear as in the fig 2, and the damping ratio was found to be equal as in the table 1. And when assembling the holder and the tool, it was found that the values of frequencies decreased, as in the fig 5, as well as the decrease in the existing damping ratios, as in the table 2. And all mods are about bending modes.
-
It was also observed that at the frequency of the fourth mode which equal 2900 Hz has an amplitude of 7.5mm. this high amplitude indicates that machining must be avoided at this frequency.
-
When comparing the dynamic characteristics of the holder only and the tool- holder assembly, it was found that the natural frequencies decreased
approximately from 2750 Hz to 1900 Hz for the first mode, as well as the damping ratio decreased in the case of the holder and the tool more than the holder only.
-
The high damping ratio of the holder is considered an influential factor, and this is expected from the characteristics of the holder that it has an effective effect on cutting operations.
-
From the theoretical point of view, when the analysis was carried out using the ANSYS software for both the holder only and the tool- holder assembly, the values of the natural frequencies and the damping ratio for the holder as in a table 4. and also for the tool- holder assembly as in a table 6. and also a sample of the mod for each of the holder and the tool- holder assembly appeared as in the fig. 8 and fig 12 respectively. Mode shapes showed the places maximum deformation for each mode, where the red region indicates the maximum deformation that occurs.
-
It was observed that There is a difference in the number of mods resulting from the experimental and the theoretical analysis, because the experimental work measure bending only, but the theoretical measures both of bending and torsion modes so the comparison was made between the mods that have bending only in the two cases.
-
A comparison between the modal test and ANSYS results for the holder only was carried as in table7 and for tool-holder assembly as in table 8. Deviation error was estimated by this relationship :
error (%) = (ANSYS result -modal test result)/ ANSYS result.
Table (7) comparison bet. Modal test and ANSYS results and error percentage for holder only.
Mode No.
Natural Frequency (Hz)
(Modal Test)
Natural Frequency (Hz)
(Theoretical – ANSYS)
Deviation Error (%)
1
5150
5639.9
8.6%
2
5600
5662.1
1.09%
3
–
6087.
–
4
–
6208.7
–
5
–
6213.
–
6
–
6230.8
–
7
–
6250.4
–
8
–
6317.7
–
9
–
6344.
–
10
–
6369.2
–
VII. REFRENCES
Table (8) comparison bet. Modal test and ANSYS results and error percentage for tool-holder assembly.
Mode No.
Natural Frequency (Hz)
(Modal Test)
Natural Frequency (Hz)
(Theoretical – ANSYS)
Deviation Error (%)
1
1900
2424.8
21.6%
2
2500
2464.3
-1%
3
–
5639.5
–
4
–
5663.6
–
5
–
6515.7
–
6
–
6561.3
–
7
–
6567.6
–
8
–
6589.5
–
9
–
6606.6
–
10
–
6615.7
–
-
From table 7 its observed that there is a small difference between the data obtained by modal test and ANSYS and error percentage is illustrated above in case of holder only when comparing the bending modes from the two methods and in tool-holder assembly as table 8. this difference due to many different factors such as surroundings conditions, measuring accuracy and instruments sensitivity.
-
This approach in results indicates to the validity of experimental model analysis.
-
-
-
CONCLUSION:
-
Results show that good agreement between experimental and analytical data from ANSYS.
-
Theoretical analysis using ANSYS program help in identification dynamic characteristics (damped ratio natural frequency mode shapes).
-
ANSYS software is a powerful tool for modal analysis that can rely on in cases that no instruments available and can calculate tool holder damping.
-
Damping in holder is an affecting parameter in improving cutting process.
-
Modal analysis technique is avital method for estimating dynamic characteristics of system.
-
-
RECOMMENDATION:
Its recommended to pay attention to damping and adding materials that help to increase the damping of the holder in order to obtain a high surface finish and high accuracy in cutting operations.
-
Hung, J.; Lai, Y.; Luo, T.; Su, H.-C (2013) Analysis of the machining stability of a milling machine considering the effect of machine frame structure and spindle bearings: Experimental and finite element approaches. Int. J. Adv. Manuf. Tech.
-
Davies m. a., pratt j. r., dutterer b. s., burns t. J (1992) chatter recognition and control system manufacturing laboratories. Inc. Gainesville. Florida, U.S, patent nr 5 170 358; 117-
-
Emad Al-Regib, Jun Ni, and Soo-Hun Lee(2003) Programming spindle speed variation for machine tool chatter suppression. International Journal of Machine Tools and Manufacture, 43(12):1229 1240.
-
Linxi Li1 , Jianlin Zhong1 , Hongjun Wang1,2,3 , Yangjie Gao(2018) Machine tool chatter test and analysis.journal of engineering 9134.
-
A J. Fleischer, V.Schulze,M.Klaiber,J.Bauer,F.Zanger(2016) The influence of tool holder technologies on milling performance CIRP 46( 226 229).
-
Benattia Bloul1 , Abdelghafour Bourdim2, said Hamou,Bourdim Mokhtar (2017) Geometric analysis of the influence of perpendicularity of a spindle axis of the milling machine on the surface quality. In : Advances in Mechanical Engineering, Vol. 9(4) 18 .
-
Chen G, Li Y, Liu X (2018) Pose-dependent tool tip dynamics prediction using transfer learning. Int J Mach Tools Manuf 137:3041.
-
Kiss A-K, Hajdu D, Bachrathy D, Stepan G (2018) Operational stability prediction in milling based on impact tests. Mech Syst Signal Process 103:327339.
-
Deng C, Miao J, Wei B, Feng Y, Zhao Y (2018) Evaluation of machine tools with position-dependent milling stability based on Kriging model. Int J Mach Tools Manuf 124:3342.
-
Albertelli P, Goletti M, Monno M (2013) A new receptance coupling substructure analysis methodology to improve chatter free cutting conditions prediction. Int J Mach Tools Manuf 72:1624.
-
Y, Bi Q, Zhang S, Wang Y (2018) A new receptance coupling substructure analysis methodology to predict tool tip dynamics. Int J Mach Tools Manuf 126:1826.
-
Maamar A, Bouzgarrou B-C, Gagnol V, Fathallah R (2017) Time domain stability analysis for machining processes. Advances inAcoustics and Vibration: 7788.
-
Devriendt C, Guillaume P (2007) The use of transmissibility measurements in output-only modal analysis. Mech Syst Signal Process 21:26892696.
-
Devriendt C, Guillaume P (2008) Identification of modal parameters from transmissibility measurements. J Sound Vib 314:343356
-
Devriendt C, De Sitter G, Vanlanduit S, Guillaume P (2009) Operational modal analysis in the presence of harmonic excitations by the use of transmissibility measurements. Mech Syst Signal Process 23:621635.
-
Xiaolin Chen, Yijun Liu. (2015) Finite element modelling and simulation with ANSYS workbench. International Standard Book Number-13: 978-1-4398-7385-4 (eBook – PDF).
-
KINS/RR-685 (2009) Seismic Analysis of Mechanical Components ANSYS. Korean institute of nuclear safety.
- [18] Darrell W. Pepper Juan C. Heinrich (2017) The Finite Element Method Basic Concepts and Applications with MATLAB®, MAPLE, and COMSOL,Taylor and Francis Group, LIC.
-
Bofang Zhu (2018) Fundamentals and Applications in Civil, Hydraulic, Mechanical and Aeronautical Engineering. Tsinghua University Press.