
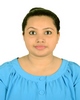
- Open Access
- Authors : Dhanshree V Damre , Tushar A Jadhav
- Paper ID : IJERTV9IS070603
- Volume & Issue : Volume 09, Issue 07 (July 2020)
- Published (First Online): 30-07-2020
- ISSN (Online) : 2278-0181
- Publisher Name : IJERT
- License:
This work is licensed under a Creative Commons Attribution 4.0 International License
Structural and Experimental Analysis of Lift Hook Bracket
Dhanshree V Damre(1)
-
Final (1) Year Student, Department of Mechanical Engineering,
Sinhgad College of Engineering, Pune 411041, India.
Tushar A Jadhav (2)
Professor (2),
Department of Mechanical Engineering, Sinhgad College of Engineering,
Pune 411041, India.
AbstractThis Lifting attachment for excessive exhaust system of diesel engine needs special considerations, such that during lifting their outer body do not over stress the components assemble inside the packaging of system. Lift brackets has wide applications in industries, it mainly used in power train transmission for lifting assemblies and transporting this excessive system from one location to another location. In this work, static structural analysis of lift hook bracket is carried out using analysis software ANSYS workbench to obtain the deformation value at various loading condition. Further, experimental analysis is performed to compare the results obtained in analysis.
Keywords Exhaust System, Lift Hook Bracket, Modes of Failures, Pull Testing, Quadratic Mesh, Static Structural Analysis.
-
INTRODUCTION
Lift hook bracket is attached to the exhaust system. It supports the master hook of crane; such that system can move from one location to another location. Lift brackets are classified into three categories; bolted, welded and strapped brackets. Among all types of bracket, the advantage of welded bracket over bolted and strapped bracket is that, the welding creates low stress concentration at weld location, while bolting creates high stress concentration at each bolt location. In case of strap bracket, it creates damage to outer body of system and unbalance of an assembly while lifting. The strength of welded joint is more as compared to bolted joint. Due to functional requirement of bolted joint there is a hole and gap is in between fasteners and base plate however, in welding joint such gap is not existing, thus such a structure would be more recommended in lifting applications. Hence, for exhaust system of diesel engines, the weld bracket is proposed for lifting and moving arrangements. A crane is used to lift a load by using ropes, wires and chains such that the load must be properly balanced using a rigging system.
Sling is one of the prominent components in power train, which acts as connector between master hook of crane and hook attach to bracket of exhaust system. Slings are classified in three types such as synthetic, chain and wire. Chain slings are typically suited for more demanding lifting operations and are made up of steel with appropriate mechanical properties for heavy lifting applications. Sling chain is considered extremely strong and durable. Excessive heat can influence the working load limit of a sling chain typically suited to more demanding lifting operations. Synthetic and wire slings are not recommended for heavy lifting applications due to high lifting of loads, wire rope exceeds the elastic limit, thus there would be permanent deformation in a rope and wire which is undesirable for design prospective. In addition to
this, bracket is widely used for lifting ships, pressure vessels, tank and supporting engines. During lifting process, the brackets fails at various locations depends upon loading configurations. There are four modes of failure such as, bearing failure, tension failure across net section, shear failure along single plane and cleavage tension failure on single plane. Bearing failure causes due to improper handling and installation or overloading. While, tension failure occurs when entire net cross section reaches to ultimate stress. In brittle crystalline materials, failure occurs due to cleavage as the result of tensile stress. In order to avoid above mentioned failures, the appropriate material and the size of bracket and weld is to be selected.
Several researchers have carried out simulation, experimental and analytical work on failure of lift bracket system. L. P. Antalffy et al. [1] have illustrated the various types of lifting brackets and suggested design criteria for bracket used in pressure vessels application with the intention of provide safe, cost effective and effective solution for lifting heavy pressure vessels at site. While, S. Boljanovic et al. [2] mentioned the fatigue behavior of failure of critical pin-loaded lug through the thickness crack at a hole. Stress intensity factor was calculated using analytical and numerical approaches. The stress ratio dependent on crack growth was considered to assess the fatigue strength of damage bracket. Experimental data was used to demonstrate the compatibility of developed model. J. Park et al. [3] mentioned influence on properties of base metal and dissimilar welding between steel base and steel lifting bracket. The effect was observed through microstructures. And hardness of sectional surface of the lifting bracket was determined through material properties. Design criteria was explained in Basic Rigging Workbook [4], it explains lifting safety, effect of asymmetrical load, critical lifts, pre-engineered lift and selection of appropriate rigging equipments including slings, shackles, turnbuckles and crane. Similarly, in ASME BTH-1 Design of Below- the -Hook Lifting Devices [5] the structural and mechanical design of lift bracket along with lifting conditions and modes of failure are explained. It also described the design criteria of lift hook bracket thoroughly. While, Bechtel Rigging Handbook [6] described preparations of rigging plans, design of heavy lift equipment support. The finite element analysis of bracket is explained in EDF-5595 [7], in which the tank lifting analysis was carried out. This analysis required lift brackets with the base plates to distribute the loading and associated stresses to the tank shell. However, it also discussed importance of lifting and tailing devices. The failures in such devices can results into loss or
damage of property, lives and huge economical loss. In this work, model of lift hook bracket is developed in modeling software PTC Creo 4.1 and the static structural analysis of welded lift bracket is carried out using analysis software ANSYS workbench 2019 R1 in order to obtain the deformation due to varying lifting load. Further, experimental analysis is carried out to simulate the result obtained in analysis.
-
ANALYSIS OF LIFT HOOK BRACKET Modeling of the lift hook bracket is carried out in PTC
Creo 4.1. Further, model is imported in ANSYS Workbench for analysis. Materials are assigned to model of exhaust system. The structural steel material is selected for lift hook bracket and weld filler, as it has high ultimate tensile strength and yield strength at room temperature. The properties of material are mention in Table 1.
Table 1 Material Property of Bracket and Weld Filler
Property
Value
Bracket
Weld
Density (kg/m3)
7850
7850
Yield Strength (MPa)
250
250
Ultimate Tensile Strength (MPa)
460
460
Poissons Ratio
0.3
0.3
Youngs Modulus (MPa)
2×105
2×105
-
Modeling of Bracket
Lift bracket is crucial component in the lifting devices and the performance of lifting depends upon the loading condition, such as liftng with spreader bar, lifting without spreader bar and single hook lifting in which lifting of system is carried out using one lift hook bracket. Number of brackets and mounting of brackets are decided based on weight, material density and center of gravity of system. In this analysis two brackets are considered for lifting single module exhaust system. Analysis is carried out for lifting with spreader bar that is vertical pull using spreader bar.
There are three methods to design the bracket such as simplified analysis method, air force method, ASME BTH method [5]. Initial CAD model of bracket and weld is model in PTC Creo 4.1 using ASME BTH method for initial dimensions as per customer requirement shown in fig.1. In which weld thickness is taken as 3 mm from acceptance criteria. In ANSYS workbench static structural analysis is selected. Model of the bracket with weld is imported for pre- processing. After importing the model material is assigned for weld filler and bracket along with exhaust system. Meshing is very important part in analysis, as it optimizes time. Here, for meshing the entire exhaust system along with weld and bracket quadratic element is used. As quadratic elements cover the corners of geometry and provides the precise results as compared to linear element. Failure in analysis can be possible if the weld and mounted plate is not attached. To increase accuracy, contact tool is run to check the connections between bracket and base system due to weld. In Fig. 2 proper connections are given between weld and surface of exhaust system shown by the highlighted pink line.
Fig. 1. CAD model of lift hook bracket
-
Static Structural Analysis
Static structural analysis is the study of the steady loading conditions on a structure. It ignores the damping effect and determines the stresses and deformation due to steady load condition. In order to decide the applied force, static gravitational load, analysis is carried out and resultant reaction force acts on each bracket is calculated. This resultant force then applies to bracket to determine the deformation.
The analysis consists of three steps, pre-processing, processing and post processing. In pre-processing the geometry is imported in .stp file from Creo to ANSYS workbench, the material properties are assigned to weld filler and bracket, quadratic element is used for meshing, then loading and boundary conditions are applied. After that the geometry is mesh. The body sizing mesh is used for analysis of bracket as it refines fine mesh at weld and bracket mounting location or heat affected zone. The total numbers of elements are 34600 and total numbers of nodes are 188885 with body sizing and global element size 1mm shown in Fig.2.
Fig. 2. Mesh model of lift hook bracket
-
Applied Resultant Reaction Forces
Mass of exhaust system (m) = 59.88 kg
Total weight of exhaust system (W) = 587.422 N Total length of exhaust system (L) =1210 mm
The resultant reaction forces on brackets of exhaust system are calculated by considering simply supported beam approach. Gravitational load is applied on the exhaust system and fixed support is given at brackets. Hence, the resultant reaction forces at fixed support F1 and F2 are calculated by equilibrium equations and its free body diagram shown in Fig.3.
Fig. 3. Free body diagram
Resultant reaction force on bracket-1 is; F1=294.1 N
Resultant reaction force on bracket-2 is; F2=294.1 N
Total reaction force is; F=588.2N
The boundary conditions applied for analysis are as follows.Resultant forces applied on bracket are calculated using analytical approach in which brackets are fixed and gravitational load is applied. These resultant forces are further applied on the edge of brackets and fixed support is given at strap locations shown in boundary conditions on exhaust system in Fig.4.
Fig. 4. Boundary conditions on exhaust system
In ANSYS post processing is the process in which results are analyzed and conclusions are derived from results. The analysis results such as total deformation on exhaust system is given for maximum load value 588.2N shown in Fig.5.
Fig. 5. Total deformation of exhaust system
Total deformation is 0.0959mm maximum on the top edge of bracket and 0.0426mm near weld location. It is observed that in most of the cases failure of bracket occurs near weld location due to varying loads. So, deformation is analyzed for various load cases.
Table 2 Lifting Conditions
Lifting Conditions
Low Load Case
High Load Case
Spreader Bar Lifting
X
2X
The criteria of selection of load cases are based on the lifting conditions. Lifting conditions for spreader bar lifting are shown in Table 2. Where X is the resultant reaction force calculated by analytical method.The boundary conditions applied such as, force 294.1N (X) and 588.2N (2X) applied on the top edge of the bracket-1 and fixed support is given at strap locations. The analysis results of total deformation at low load case is shown in Fig.6.
Fig. 6. Total deformation at low load case
The analysis results of total deformation at high load case is shown in Fig.7.
Fig. 7. Total deformation at high load case Fig. 8.
From Fig.6 , it is observed that, the total deformation in case of low load lifting condition maximum 0.0479mm on top edge of bracket-1 and minimum 0.0053mm near weld location. In high load lifting condition the maximum value of deformation is 0.0959mm on top edge of lift bracket-1 and minimum 0.01mm near weld location as shown in Fig.7.
Fig. 9. Load versus total deformation of static structural analysis
Load versus total deformation result of static structural analysis shown in Fig.8. It is observed that deformation increases gradually as load increases. At high load 588.2N deformation is 0.0959mm. While at 294.1N load, deformation is 0.043mm.
-
Experimental Analysis
Experimental analysis was carried out to verify the results of finite element analysis for actual working conditions. In this work, pull testing was used to perform the experiment. This experiment was carried out to calculate deformation when load increases. Schematic of experimental setup is shown in Fig.9.
The experiment was conducted for spreader bar lifting condition in which axial loading plays measure parameter. The input force was applied on the arm of actuator connected
with the lift hook bracket-1 of exhaust system in vertical direction. This force gradually increases by using servo hydraulic actuator, have 25kN capacity. To support the exhaust system, fixture plate was attached to the exhaust system, which was supported by base plate of setup machine. Results were calculated using strain gauges placed on bracket-1 and on bracket-1 mounted surface. These strain gauges were attached to the data acquisition device and data was converted into load versus total deformation result shown in Fig.10.
Fig. 10. Schematic of experimental setup
Fig. 11. Load versus total deformation of experimental analysis
An experimental result states that the rate of deformation is high up to 30N. After that, as load increases the deformation also increases gradually. Maximum deformation was
measured 0.0932mm at high load value and 0.067mm at low load value.
-
-
RESULT
The simulation results of lift hook bracket on varying load condition shows the maximum deformation. This simulation result of load versus total deformation of finite element analysis and experimental analysis shown in Fig.11. In which finite element analysis result is shown by blue curve and experimental result shown by orange curve. It is observe that deformation is increases suddenly due to self- weight in initial state of experimental curve.
Fig. 12. Simulation result of load versus total deformation
-
CONCLUSION
-
This paper represents the static structural analysis and experimental analysis of lift hook bracket of exhaust system. In static structural analysis total deformation due to axial loading was calculated at varying load and experimental analysis has been carried out to compare finite element analysis result. The finite element analysis result shows maximum deformation at top edge of the bracket for low load and high load condition. There was no deformation seen near weld and bracket mounting surface. So, it concludes that selected weld material was appropriate for this case. The simulation result was closest match, having 2.81% error at high load condition. While in case of low load condition the difference is 37.81% and it was neglected because the deformation value was less than 0.1 mm in both analytical and experimental analysis. This difference generally occurs due to setup error or improper orientation of the gauge on the testing surface.
ACKNOWLEDGMENT
The authors wish to thank Amar A. Mali, Sandip S. Patil and Kiran A. Kadam, Applied Mechanics Engineer, CES, Cummins Technical Center India, Pune, for providing the technical support for this work.
REFERENCES
-
Leslie P. Antalffy, George A. Miller III, Kenneth D. Kirkpatrick, Anil Rajguru, Yong Zhu, The design of lifting attachments for the erection of large diameter and heavy wall pressure vessels, International Journal of Pressure Vessels and Piping, pp. 12-21, 2016.
-
Slobodanka Boljanovic, Stevan Maksimovic, Fatigue damage analysis of wing-fuselage attachment lug, Procedia Structural Integrity5, pp. 801-808, 2017.
-
Jeongung Park, Gyubaek An, Haewoo Lee, Influence on properties of base metal after elimination of lifting lug member in a dissimilar welding between steel base and steel lifting lug, International Journal of Naval Architecture and Ocean Engineering 11, pp. 858-864, 2019.
-
Basic Rigging Work book, Training and Qualifications Program office, 2008.
-
ASME BTH-1, "Design of Below-the-Hook Lifting Devices," The American Society of Mechanical Engineers, 2014.
-
Bechtel Rigging Handbook, The Bechtel Equipment Operations Rigging Department.
-
EDF-5595, V-Tanks Remediation Tank Lifting Design, TSF, pp.09-18, 2005.