
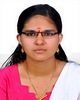
- Open Access
- Authors : Gopika Krishnan P , Husna M S , Neethu N S , Sreelekshmi M S, Kiran C J
- Paper ID : IJERTV10IS070161
- Volume & Issue : Volume 10, Issue 07 (July 2021)
- Published (First Online): 20-07-2021
- ISSN (Online) : 2278-0181
- Publisher Name : IJERT
- License:
This work is licensed under a Creative Commons Attribution 4.0 International License
Strength and Durability Assessment of Concrete with Fine Aggregate Replaced by Copper Slag
Gopika Krishnan P1, Husna M S2, Neethu N S3, Sreelekshmi M S4, Kiran C J5
Department of Civil Engineering Government Engineering College, Barton Hill
Thiruvananthapuram, India
Abstract The present work focuses on assessing the viability of applying blasted copper slag, an industrial by- product obtained during the manufacture of copper, as a replacement material for fine aggregate in concrete mixes. The chemical composition of copper slag including iron, silica and aluminum oxide, which makes it work efficiently as fine aggregate in concrete and also imparts pozzolanic activity in concrete. Mix design of concrete was done on weight basis by adding various percentages of copper slag. The replacement percentages focused on this study are 20%, 30%, 40%, 50% and 60%. Different tests were carried out on these mixes to investigate its strength, workability and durability properties, hence established the optimum percentage of copper slag that can be used as a replacement to fine aggregate in concrete. The change in trend of all these properties, with different replacement percentages was examined and the reason for the change is also investigated. The increase in concrete characteristics after 28 days, due to the pozzolanic property of copper slag has also been studied.
Keywords Concrete, Copper slag, Fine aggregates, Replacement, Strength, Durability, Workability
-
INTRODUCTION
The construction industry exhibits a rapid growth and is in constant need of natural resources for the development of the infrastructure. Simultaneously, the wastes generated from the industries are increasing rapidly. This research was performed to evaluate the potential use of copper slag, an industrial waste, as sand replacement in the production of concrete. Copper slag is a by-product of the manufacture of copper. It has various applications like blasting medium replacement in industrial cleaning, as a filler material and additive to Portland cement in construction industry etc. Copper slag is characterized by lower water absorption and comparable gradation of fine aggregate, at the same time producing a pozzolanic effect in concrete matrix when incorporated due to its chemical composition. These characteristics make copper slag to be a promising replacement material for fine aggregate without compromising the workability, strength and durability of conventional concrete.
-
MATERIAL PROPERTIES
-
Fine aggregate
Fine aggregate used for the preparation of control concrete and replaced concrete is Manufactured sand of zone II confirming to IS 383: 1970. It is observed to have a specific gravity of 2.69 and water absorption of 1.42 when tested according to the standard procedure mentioned in IS 2386 Part 2 (1963).
Sand grains are angular, shape of the grains approximating to spherical form, elongated and flattened grains being present only in very small or negligible quantities. Fig.1 shows the gradation curve for fine aggregates observed by sieve analysis.
-
Coarse Aggregates
The coarse aggregate having a nominal size of 20mm is used for the experimentation. The coarse aggregates used are tested for their gradation, specific gravity and water absorption as recommended in IS 2386 Part 1 (1963), IS 2386
Part 3 (1963), IS 2386 Part 3 (1963) respectively. It is observed from the testing that the coarse aggregates used have a specific gravity of 2.73 and water absorption 0.34. Fig.2 shows the gradation curve for coarse aggregates observed by sieve analysis.
Sl no.
Properties
Results
1
Grade
53
2
Specific Gravity
3.13
3
Initial Setting Time
150 minutes
4
Final Setting Time
225 minutes
TABLE I: PROPERTIES OF CEMENT
A. Cement
The Cement used for preparing specimens is Ultratech OPC 53 grade cement. Table I shows the physical properties of cement
Fig 1: Gradation curve of fine aggregates
Fig 2: Gradation curve of coarse aggregates
D. Copper Slag
The properties and chemical composition of copper slag are listed in Table II indicates the physical properties of copper slag and Table III shows the chemical composition of copper slag. Fig.3 emphasizes the gradation curve of copper slag obtained by conducting sieve analysis.
Sl. No.
Property
Results
1
Grain Shape
Angular, Multifaceted
2
Appearance
Black Glassy
3
Specific Gravity
3.50
4
Particle Size
0.075 to 4.75mm
5
Water absorption
0.16
Sl. No.
Property
Results
1
Grain Shape
Angular, Multifaceted
2
Appearance
Black Glassy
3
Specific Gravity
3.50
4
Particle Size
0.075 to 4.75mm
5
Water absorption
0.16
TABLE II: PHYSICAL PROPERTIES OF COPPER SLAG
Fig 3: Gradation curve of copper slag
-
-
METHODOLOGY
Mix proportions are worked out after attaining the material properties. According to the requirement, various specimens are cast to test for their characteristics. Fresh as well as hardened concrete are tested to attain properties like workability, durability and strength on various apparatus according to standard procedure given by specified IS codes or ASTM codes. Results are then analyzed and property variation with replacement is found.
-
Mix proportioning
Mix proportioning is done conforming to IS 10262: 2009 for M25 grade concrete. Percentage of copper slag replacement is taken as 20%, 30%, 40%, 50% and 60%. Table IV shows the mix proportioning worked out for the same for 1 m3 volume.
Mix
Cement (kg)
FA
(kg)
Copper slag(kg)
CA
(kg)
Water (kg)
Control Concrete (CC)
383.16
701.23
0
1161.24
205.50
20 % FA
replaced with copper slag (CS20)
383.16
560.98
140.25
1161.24
205.50
30 % FA
replaced with copper slag (CS30)
383.16
490.86
210.37
1161.24
205.50
40 % FA
replaced with copper slag (CS40)
383.16
420.74
280.49
1161.24
205.50
50 % FA
replaced with copper slag (CS50)
383.16
350.62
350.62
1161.24
205.50
60 % FA
replaced with copper slag (CS60)
383.16/p>
280.49
420.74
1161.24
205.50
Mix
Cement (kg)
FA
(kg)
Copper slag(kg)
CA
(kg)
Water (kg)
Control Concrete (CC)
383.16
701.23
0
1161.24
205.50
20 % FA
replaced with copper slag (CS20)
383.16
560.98
140.25
1161.24
205.50
30 % FA
replaced with copper slag (CS30)
383.16
490.86
210.37
1161.24
205.50
40 % FA
replaced with copper slag (CS40)
383.16
420.74
280.49
1161.24
205.50
50 % FA
replaced with copper slag (CS50)
383.16
350.62
350.62
1161.24
205.50
60 % FA
replaced with copper slag (CS60)
383.16
280.49
420.74
1161.24
205.50
TABLE IV: MIX PROPORTION FOR 1 m3
TABLE III: CHEMICAL COMPOSITION OF COPPER SLAG
Constituents
Weight
Silica (SiO) (Combined as Silicate)
26 30%
Free Silica
Less than 0.5%
Alumina (AlO)
2%
Iron Oxide as FeO
42 47%
Calcium Oxide CaO
1 2%
Magnesium Oxide MgO
1.04%
Copper Oxide CuO
6.1% max
Sulphates
0.13%
-
Specimen requirements
3 Cubes of size 150mm x 150mm x 150mm were cast for Compressive strength and Surface resistivity test for all the mixes. 3 Cylinders of height 300mm and diameter 150mm were cast for Split tensile strength test for all the mixes. For the Rapid Chloride Penetration test, 3 RCPT disc of diameter 100mm and height 50mm were cast for all the mixes.
-
-
TEST PROCEDURE
-
Slump Test
The test specimen is prepared by mixing the components of concrete in suitable proportions with a water-cement ratio of
0.5. The test is administered employing a metal mould within the sort of a conical frustum mentioned as Abrams cone with a height of 30cm, bottom diameter 20cm and top diameter 10cm. A tamping rod 16mm diameter and 60cm long was used.
-
Compressive Strength Test
Three cubes of size 15 cm x 15 cm x 15 cm are used for experimentation. Mixing of concrete was done in a laboratory batch mixer for preparation of cubes and are cured for 28 days. The specimens, after curing, are surface dried and placed centrally on the base plate of the machine with load applied continuously at the rate of 140kg/cm2/minute till the specimen fails. The maximum load at which the specimen failed is recorded.
-
Split tensile Strength Test
Three cylindrical specimens of 150 mm diameter and 300 mm height are tested in surface dry condition after curing for at least 28 days for each mix using a compression testing machine. The cylindrical specimen was placed such that the longitudinal axis is perpendicular to the load. Load was applied uniformly and continuously without shock at a nominal rate within the range 1.2 N/mm2/min to 2.4 N/mm2/min, until failure. The maximum applied load at failure was recorded.
-
Surface Resistivity Test
Three cubes of size 150 x 150 x 150 mm are used for the test. The Resipod proceq meter was made to come in contact with the levelled surface of the specimen which has undergone a curing of at least 28 days. The probes of the proceq meter were dipped into water in a tray immediately before taking measurement since it is completely dry and no measurement is possible since the current is carried by the ions in the pore liquid. Then the instrument is placed on the specimen and the screen will directly show the reading which was the measure of resistivity offered by the particular specimen against the flow of ions in kcm. Once a stable reading has been achieved, the reading was noted.
-
Rapid Chloride Penetration Test
Three cylindrical discs of diameter 100 mm and height 50 mm are used for testing. Cylindrical specimen, side coated with epoxy, was put in a vacuum chamber for 3 hours. Then the specimen was made to vacuum saturated for about 1 hour and then for about 18 hours allowed to soak in water. It is further placed in the test device where the left-hand side ()
of the test cell is filled with a 3% NaCl solution and the right- hand side (+) is filled with 0.3N NaOH solution. The system is connected and a 60-volt DC potential that is applied for 6 hours where readings are taken every 30 minutes.
-
-
RESULTS
-
Workability- Slump test
Slump test is conducted on all mixes for a desired slump of 75 mm corresponding to medium workability. Table V shows the slump obtained for various mixes. A graph is plotted with percentage of copper slag replaced v/s slump observed as shown in Fig.4. An equation is formed with the results obtained as y = 0.00667×2 +0.01667x +65
where, x = percentage of copper slag replaced y = slump in mm,
so that the corresponding slump can be predicted for any percentage replacement of fine aggregate with copper slag. From CC to CS 60, the slump observed shifts from 65 mm to 90 mm. Hence, a gradual increase can be seen in the slump value with an increase in the percentage replacement of fine aggregate with copper slag.
TABLE V: SLUMP OBSERVED
Mix
Slump observed
Workability result
CC
65 mm
Medium
CS20
68 mm
Medium
CS30
72 mm
Medium
CS40
75 mm
Medium
CS50
82 mm
Medium
CS60
90 mm
Medium
Fig 4: Graphical representation of slump observed
Fineness modulus of fine aggregates is 2.6 while that of copper slag is 2.7. This can result in a smaller specific surface area. Also, the surface texture of copper slag is glassy and smooth, which reduces its water absorption. Furthermore, the water absorption of fine aggregate is 1.42 % while that of copper slag is 0.46 %. These all result in increased free water content in the concrete matrix, that in turn may have increased the workability with increase in copper slag content in mixes.
-
Compressive strength
Compressive strength of CC and CS40 is found out after 28 days curing and is obtained as 40.57 MPa and 39.87 MPa respectively. All the remaining mixes were tested at 60 days due to inconveniences related to pandemic outbreaks.
A graph is drawn with the results obtained as in Fig.5 An equation is formed with the 60-day compressive strength curve in order to project the 28 days strength to 60 days strength for an efficient and accurate analysis, given by,
y = -0.0089×2 + 0.3913x + 40.63
where, x = percentage replacement by copper slag in % y = 60-day compressive strength in MPa
Hence, the approximate values for CC and CS 40 at 60 days as well as the results obtained for other mixes are tabulated in Table VI.
All observed values were above the target strength of 31.6 MPa of M25 concrete. Strength gain with age is also observed comparing the 28 day nd predicted 60-day compressive strength.
Maximum increase in compressive strength is observed at 30% replacement. Hence, optimum replacement of fine aggregate with copper slag can be attained at 30 % replacement, with an increase in strength than normal control concrete.
Fig 5: Graphical representation of compressive strength
TABLE VI: 60-DAY COMPRESSIVE STRENGTH OBSERVED
Mix
Approximate 60-day compressive strength (MPa)
% Increase in compressive strength
CC
40.63
–
CS20
43.72
+ 7.61
CS30
45.23
+ 11.32
CS40
42.04
+ 3.47
CS50
36.20
– 10.9
CS60
32.40
– 20.26
-
Split tensile strength
Split tensile strength of various concrete mixes including the control concrete (CC) as well as mixes with fine aggregate replaced by copper slag in various percentages is found out conforming to IS code recommendations and is expected to be near a target split tensile strength of 2.8 MPa as per ACI 318.
Split tensile strength of CC and CS 40 is observed at 28 days which is 3.37 and 3.35 respectively. All other mixes were tested at 60 days. A graph is plotted with percentage of copper slag replaced and observed split tensile values as shown in Fig.6.
An equation is formulated with the 60-day split tensile strength to find the approximate 60-day strength of specimens tested at 28 days for an impartial analysis given by,
y = -0.0002×2 + 0.004x + 3.35
where, x = percentage replacement of copper slag in % y = 60 day split tensile strength in MPa
The approximate values of the mixes hence found as well as the observed 60-day values of split tensile strength are tabulated in Table VII.
The values are above the target strength desired and a slight strength gain for 28-day samples is observed. Split tensile strength increased from CC to CS 30 and decreased further. Hence, an optimum replacement with copper slag can be achieved at 30 %, with a strength gain than CC.
Fig 6: Graphical representation of split tensile strength
TABLE VII: 60-DAY SPLIT TENSILE STRENGTH OBSERVED
Mix
Approximate 60 day split tensile strength (MPa)
% Increase in split tensile strength
CC
3.37
–
CS20
3.39
+ 0.59
CS30
3.41
+ 1.19
CS40
3.36
+ 0.29
CS50
3.25
– 3.56
CS60
3.20
– 5.04
-
Surface resistivity test
Surface resistivity of CC and CS 40 are found using non destructive testing methods at a curing period of 28 days for which value of 32.20 kcm and 31.16 kcm is obtained respectively.
Other mixes are tested at 60 days and a graph is plotted with these observations as y axis and percentage replacement of copper slag as X axis as given in Fig 7. The 28-day resistivity values are projected to 60-day values for approximate analysis with the help of equation formulated from the 60-day resistivity curve, given by,
y = -0.0066×2 + 0.287x + 32.218
where, x = percentage replacement of copper slag in % y = 60-day surface resistivity in kcm
The 60-day resistivity values are tabulated in table VIII.
The resistivity values when compared to standard values given in AASHTO TP 95 shows a low permeability, indicating high resistivity. Table IX indicates the standard values of surface resistivity as per AASHTO TP 95. Resistivity is observed to at a peak at 30% replacement indicating the optimum replacement percentage along with improved conditions of durability.
TABLE VIII: 60-DAY RESISTIVITY OBSERVED
Mix
Approximate resistivity observed (60 days) (kcm)
% Increase in resistivity
CC
32.22
–
CS20
34.47
+ 6.99
CS30
36.70
+ 13.91
CS40
33.13
+ 2.83
CS50
28.20
– 12.47
CS60
26.63
-17.34
TABLE IX: STANDARD VALUES OF SURFACE RESISTIVITY
Range
Penetrability
<12
High
12 TO 21
Moderate
21 TO 37
Low
37 TO 254
Very low
>254
Negligible
-
Rapid chloride penetration test
The permeability of chloride ions is measured using RCPT test where CC and CS 40 has amount of charge passed as 1570.28 coulombs and 1560.17 coulombs respectively after 28-day curing. All other mixes were tested at a period of 60 days curing for which values obtained are graphically represented in Fig. 8. An analytical equation is formulated using the 60-day values obtained to find approximate 60-day permeability of specimens tested at 28 days. The equation is given as,
Fig 7: Graphical representation of surface resistivity
y = 0.0449×2 2.1287x + 1573.5
where, x = percentage replacement of copper slag in % y = 60-day RCPT value in coulombs.
The values observed as well as approximated values for 28 days permeability are given in Table X.
Fig 8: Graphical representation of permeability
Mix
Approximate charge passed
-60days(coulomb)
% Decrease in permeability
CC
1573.50
–
CS20
1558.69
+ 0.94
CS30
1546.32
+ 1.73
CS40
1560.19
+ 0.85
CS50
1570.17
+ 0.21
CS60
1613.49
– 2.54
Mix
Approximate charge passed
-60days(coulomb)
% Decrease in permeability
CC
1573.50
–
CS20
1558.69
+ 0.94
CS30
1546.32
+ 1.73
CS40
1560.19
+ 0.85
CS50
1570.17
+ 0.21
CS60
1613.49
– 2.54
TABLE X: 60-DAY PERMEABILITY OBSERVED
Maximum decrease in permeability of chloride ions is observed at 30 % replacement. All the values are under the range of low permeability as per standard provisions in – ASTM C 1202, as given in Table XI.
Hence, optimum replacement of fine aggregates with copper slag can be done at 30 % with an increased durability than CC.
Current passing (Coulombs)
Chloride ion permeability
>4000
High
2000 to 4000
Moderate
1000 to 2000
Low
100 to 1000
Very low
<100
Negligible
Current passing (Coulombs)
Chloride ion permeability
>4000
High
2000 to 4000
Moderate
1000 to 2000
Low
100 to 1000
Very low
<100
Negligible
TABLE XI: STANDARD VALUES OF SURFACE RESISTIVITY
-
-
CONCLUSIONS
-
The slump value of concrete was found to increase from 65mm to 90mm from CC to CS60. However, slump for all the mixes were in the range of medium workability as per IS 456:2000.
-
Compressive strength of concrete increased from
40.57 MPa to 45.23 MPa from CC to CS30, which is 11.3% increase.
-
For all the mixes from CC to CS60, compressive strength and split tensile strength are greater than target strength.
-
Split tensile strength of concrete increased from 3.37 MPa to 3.41 MPa from CC to CS30, which is 1.19% increase.
-
Surface resistivity of concrete increased from 32.2 to
36.7 kcm from CC to CS30, which is 13.91% increase.
-
Chloride ion penetration of concrete decreased from 1570.28 to 1546.32 Coulomb from CC to CS30 depicting better durability. However, all the mixes from CC to CS60 lies in the range of low permeability.
-
Hence, the optimum percentage of copper slag replacement in concrete, with respect to its strength and durability characteristics was found to be 30%.
-
From the analytical relationship between concrete properties Vs. percentage of copper slag replaced, there is an increase in strength and durability aspects from 28 to 60 days. This is due to the pozzolanic property of copper slag
-
Scope for future research
Constant W/C ratio kept for all mixes was found to be a prime reason for decrease in strength and durability as the percentage replacement by copper slag increases. This is due to low water absorption of copper slag. Therefore, moisture correction factor can be worked out to reduce the extra water in the matrix and thereby the properties of replaced concrete such as workability, strength and durability can be effectively improved.
The strength of concrete is found to improve post 28 days, however the same needs to be studied in detail.
ACKNOWLEDGMENT
We are deeply indebted to Sankar V, Assistant Director, Kerala Highway Research Institute, Karyavattom, for providing us with lab facilities for conducting the experimental works related to this project.
REFERENCES
-
Chadalavada Teja, Divya Anusha Naidu, Dr. Dumpa Venkateswarlu, Performance of copper slag as replacement of fine aggregate, Journal of Critical Reviews, Volume 7, Issue 9, 2020.
-
Mansi M Soni, Jayesh R Mangroliya, Performance of copper slag on strength as partial replacement of fine aggregate in concrete, International Journal of Engineering Research & Technology, Volume 7, Issue 1, 2018.
-
Bhosale Mahesh Bhimarao, Sathe Akash Shrikanth, Dr. Santhosh K Patil, Replacement of copper slag with aggregate, International Research Journal of Engineering and Technology, Volume 7, Issue 3, 2020.
-
Mr. Suhas S Malkhare, Prof. Atul B Pujari, To study the performance of copper slag as partial or fully replacement to fine aggregates in concrete, International Journal of Research and Review, Volume 5, Issue 5, 2018.
-
Ambrish E, Dhavamani Doss S, Shanmugha Nathan N, Ganapathi Raj S, Partial replacement of copper slag as fine aggregate, SSRG International Journal of Civil Engineering, Volume 4, Issue 3, 2017.
-
R. Elamaran, K. Srinivasan, S. Vimala, Use of copper slag for partial replacement to fine aggregate in concrete, International Journal of Recent Technology and Engineering (IJRTE) ISSN: 2277 3878, Volume 7, Issue 5S3, 2019.
-
C. K. Madheswaran, P. S. Ambily, J. K. Dattatreya, N. P. Rajamane, Studies on use of copper slag as replacement material for river sand in building constructions, Journal of the Institution of Engineers (India): Series A, Volume 95, Issue 3, Page No. 169- 177, 2014.
-
O. Pavez, O. Rivera, I. Toledo, A. Nazer, Use of copper slag as fine aggregate and partial replacement of cement, Holos, ISSN: 1807- 1600, Volume 4, Issue 34, Page No. 31-45, 2018.
-
M.A.G. Dos Anjos, A.T.C. Sales, N. Andrade, Blasted copper slag as fine aggregate in Portland cement concrete, Journal of Environmental Management, ISSN: 0301 – 4797, Volume 196, Page No. 607 613, 2017.
-