
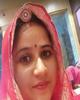
- Open Access
- Authors : Jyoti Kanwar , Bhaskar Shrivastava
- Paper ID : IJERTV11IS070068
- Volume & Issue : Volume 11, Issue 07 (July 2022)
- Published (First Online): 16-07-2022
- ISSN (Online) : 2278-0181
- Publisher Name : IJERT
- License:
This work is licensed under a Creative Commons Attribution 4.0 International License
Simulation of Crane Hook Eye using Finite Element Analysis
Jyoti Kanwar, Bhaskar Shrivastava
Department of Mechanical Engineering Yagyavalkya Institute of Technology, Jaipur, Rajasthan, India
Abstract:- The failure of crane hook eye happens attributable to the strain iatrogenic because of repetitive loading and unloading conditions. To reduce the failure of crane hook eye, the strain within the crane hook eye is studied and reduced the maximum stress than existing (trapezoidal) crane hook eye. By modifying the cross section the strain of the hook eye is reduced. During this study, the cross section has been chosen as a basic parameter to optimize the hook style that carries 4.5-tons load. Here, there square measure four forms of cross-sectional for crane hook eye specifically design-3, design-1, Design-2 and trapezoidal (standard). These crane hook eyes modelled and analyzed using SOLIDWORK and ANSYS software, and also the results of every changed crane hook eyes compared with trapezoidal hook results supported totally different criterias that square measure maximum stress, maximum deformation, fatigue life and weight of the hooks. Finally supported the comparisons of every changed modeling crane hook eyes with the quality crane hook eye, design-2 is chosen. The maximum Von-Misses stress and weight of design-2 crane hook eye is reduced from trapezoidal (standard) crane hook eye by 3.461 MPa (4.133%) and 0.354 Kg (2.49%). Therefore, model -3 crane hook eye is taken into account as optimum results.
Key words: Crane hook eye, Finite Element Method, Weight Optimization, Fatigue Analysis
INTRODUCTION
Crane hook eye could be a wiggly bar and is employed for lifting masses in cranes. Crane hook eye is that the element that is usually wont to elevate the significant load and transfer it from one place to a different in industries, factories and constructional sites. Crane hook eye is one in every of the maximum and necessary parts of crane primarily a hoisting fixture designed to interact a hoop or link of a lifting chain or the pin of a shackle or cable socket and should follow the health and safety tips. [2, 3] Cranes are classified as weight handling instrumentation (WHE). Theyre primarily designed to perform weight lifting and, with the right attachment, excavating operations underneath varied conditions. A framework crane features a hoist in a very mounted machinery house or on a tramcar that runs horizontally on rails, typically fitted on one beam (mono-girder) or 2 beams (twin- girder).
Figure 1 Crane with all components [4]
Single Crane hook eyes square measure the correct selection if the machinery deals with numerous up to seventy five tons; this lifting hook is extremely easy and simple to use.
Figure 2 Single Crane hook eyes
Double (Ramshorn) Crane hook eye is analogous in conception, however their style provides superior bearing that is appropriate for heavier different over seventy five tons.
Figure 3 Double (Ramshorn) Crane hook eye
Generally, crane hook eyes are made of iron or steel. For significant duty crane hook eyes low alloy steels are used however material isn't the sole issue behind its huge load bearing capability. Steel grade, heat treatment and shaping are equally necessary to create a sturdy crane hook eye. Correct shaping is incredibly necessary. Shaping provides higher structural integrity than the other metal operating processes. It eliminates any reasonably defect like gas pockets or voids within the hook which may have an effect on its long run performance; therefore increasing its strength, toughness, load bearing capability and fatigue resistance.
A crane is subjected to continuous loading and unloading condition. These can cause fatigue failure of Grus hook eye and cause serious accidents. Because of continuous loading cycle the life (the ability to resist the applied load) of crane hook eye can cut back. Therefore, the fatigue life and fatigue injury Grus hook eye should be analyzed (estimated).
To reduce the failure of crane hook eye, the strain elicited within the hook should be analyzed and reduced the strain the maximum amount as attainable with having higher alternative results. Actually, the analysis of optimized hook stress is reduced compared to the quality hook by suggests that of accelerating the contact space (high stress concentration space of cross section) and on purpose idea this implies indirectly strength rising of crane hook eye. By modifying the crosswise stress and weight of Grus hook eye will cut back with scrutiny the quality crane hook eye, and therefore the fatigue life even be higher than the quality crane hook eye.
FEM is used to optimize the overall weight and fatigue study of the crane hook eye. The first stage is to do a literature review using various sources such as journals, books, websites, and other resources. The gap in the literature (problem) is then identified. SolidWorks software is used to create the 2D and 3D models of the crane hook eyes, and ANSYS Workbench 17.2 is used to do the FEM simulation. The findings of numerical methods are compared to those of analytical approaches. Based on the FEM analysis, the new modified crane hook eye models are compared to the trapezoidal (existing) crane hook eye and the best crane hook eye is chosen.
The importance of this study is to cut back the load of Grus hook eye which suggests to form lightweight weight of crane hook eye still on save the waste of fabric for Manufacturer Company. The load reduction of crane hook eye is indirectly creating lightweight to the weight of crane. This helps to save lots of (reduce) fuel consumption of Grus. The manufacturer company made Grus hook eyes by mass; thus, it'll save a lot of materials and it's smart saving in terms of value. The opposite necessary of this study is to cut back the maximum stress iatrogenic on Grus hook eye (make having higher fatigue life than the prevailing crane hook eye). The fatigue life is checked by analysis fatigue sensitivity of Grus hook eyes and this analysis helps to estimate the fatigue life with the applied over load. If the maximum stress is reduced the sturdiness of Grus hook eye can improve.
LITERATURE REVIEW
Gopichand A.et al. (2013) has worked optimization of style parameters is applied victimization Taguchi methodology. Analytical methodology for stress calculation arched beam flexure formula is employed once the curvature of the member is pronounced as in cases of hooks and rings for various cross sections mathematical analysis of stress. [8] Nishant soni .et al. (2013) has worked with objective of the optimization of the mass for cane hook-under the result of static load comprising the height pressure load. He used finite part analysis for the form optimizations of crane hook eye furthermore as for validation of ultimate pure mathematics. [9]
Rashmi Uddanwadiker.et al. (2011) has calculated the strain pattern made because of the load on hook by victimization arched beam theory. For the planning improvement if the inner facet of hook at the portion of maximum stress is widened then the strain can get reduced. [10] Pradyumnakeshri maharana .et al. (2012) has calculable hook dimensions for varied cross section and topology by keeping the depth and cross section space. [11] Shaban M.et al. has studied the strain pattern of crane hook eye in its loaded condition. They investigated if the inner curvature of hook is widened the strain are going to be reduced. [12] Patel A.et al. (2013) has worked on reduction of weight of beam that has reduced the value and hyperbolic lifetime of beam. [13] Takuma Nisimura.et al. (2010) has studied injury issue estimation of crane hook eyes to recognize the tendency of the load condition. Its been calculable that loading conditions were crucial to the crane-hook damages. [14]
Chetan N. Benkar.et al. (2014) worked on crane hook eye for calculable the strain pattern in its loaded condition by getting ready a 3D solid model with the assistance of ANSYS fourteen bench. And he found that rectangular cross sectional space offers minimum stress and deformation level. [16] E. Narvydas.et al. (2012) calculated the strain concentration at shallow
notches and sleek lifting hook. And he thought-about for the sturdiness analysis and machine part the strain concentration issue is extremely vital. [17] Tripathi Yogesh .et al. (2013) has conducted FEM analysis to check the strain pattern of crane hook eye in its loaded condition, [18]
MATERIALS AND METHODS
According to [20] the proportional dimensions of single shank hook square measure indicated below. In figure 5 and table 1 shows all parameters of the shank crane hook eye square measure delineated and therefore the customary (proportional) dimensions square measure listed. The high and low stress concentration space of cross section square measure indicated; that square measure modification space of crane hook eye to induce higher results of weight and maximum stress of constellation hook eye.
Figure 4 dimensions cross sectional view of the standard (trapezoidal cross section crane hook eye) [20]
Table 1 the overall dimensions of the trapezoidal (standard) crane hook eye [20]
Distance from top to the load applied portion (L1) = 308 |
Length of the shank (B) = 113 |
Inner width of cross section at load applied portion b2 = 65 |
Total height of the crane hook eye (L) = 383 |
Distance from lock pin to applied load surface (e3) = 175 |
Distance from bottom of the shank to the load applied portion (e2) = 205 |
The height of nose part of the crane hook eye (a3) = 97 |
Inner width of high stress concentration area of cross section (bi) = 79 |
Gap of the curvature (a2) = 67 |
Height of high stress concentration area of cross section (h) = 96 |
The diameter of inner curvature of the crane hook eye (a1) = 83 |
Height of cross section at load applied portion (p) =81 |
For analytical stress analysis methodology used solely the high concentration stress space dimensions that square measure height of the cross section (h), inner and outer dimension of the cross section (bi) and (bo). As a result of the analytical stress analysis methodology is completed exploitation recurved beam flexure formula (Winkler-Bach formula for recurved beam).
Table 2 Comparison of the materials based on their mechanical properties [21, 22]
Properties |
Structural Steel |
AISI 4340 Steel, Normalized |
AISI 4340 Steel, Annealed |
AISI 4130 Steel, Normalized |
Units |
Elastic modulus |
200000 |
205000 |
205000 |
205000 |
N/mm2 |
Poissons ratio |
0.3 |
0.32 |
0.285 |
0.285 |
N/A |
Shear modulus |
76923 |
80000 |
80000 |
80000 |
N/mm2 |
Mass density |
7850 |
7850 |
7850 |
7850 |
Kg/m3 |
Ultimate Tensile strength |
460 |
1110 |
745 |
670 |
N/mm2 |
Yield strength |
250 |
710 |
470 |
436 |
N/mm2 |
The above table is compared four completely different materials that area unit steel, AISI 4340 Steel normalized, AISI4340 Steel tempered and AISI 4130 steel normalized supported their mechanical properties. The steel isn't heat treated and additionally the strength the fabric is extremely tiny with comparison the others. As mentioned within the higher than the normalized material is healthier than the tempered material because of the fatigue resistance. Therefore, rely upon the higher than comparison criterias AISI 4340 Steel is healthier than the others. Therefore, for this study chosen AISI 4340 steel normalized by thought of the higher than steel criterias.
-
Analysis and optimization Methods of crane hook eye
Design improvement is a very important engineering style activity. The method of crucial the simplest style is named improvement. In general, style improvement determines values for style variables specified AN objective perform is optimized whereas performance and different constraints are glad. The utilization of style improvement in engineering style continues to
extend, driven by additional powerful computer code packages and therefore the formulation of recent style improvement issues motivated by the decision-based style (DBD) framework. Style improvement model may be a subjective method that needs engineering judgment and technical skills. In a very given style scenario, there ar seemingly to be several variables, parameters, constraints, and criteria associated with completely different performance attributes. Thus, there are a spread of relevant improvement models from that to settle on. [19]
The design and analysis of crane hook eye is finished by thought of as serpentine beam. Crane hook eyes with tetragon, circular, rectangular and triangular cross section ar unremarkably used. From literatures conferred during this paper tetragon cross section hook is healthier than the opposite cross sections. This study deals with the study of crane hook eye consists the tetragon cross sections still because the modification of ordinary hook during which the load improvement is finished by ever-changing cross section. During this study there are 3 changed cross sectional hooks. Generally AN accident could occur because of stress concentration consider it thus stress analysis is critical before create it applicable. And stress analysis is studied in ANSYS bench seventeen.2. Currently the model and analysis each are distributed by softwares. So; it should be designed to deliver maximum performance while not failure.
In this study there are four sort of crosswise for crane hook eye particularly design-3, design-1, Design-2 and tetragon (standard). The theoretical stress calculation is finished rely upon the crosswise kind. All four cross-sections are modelled in SOLIDWORK seventeen computer code. Then, saving. igs file is employed more for analysis. Once modelling the four varieties of crane hook eye cross- sections its. igs file that is saved in SOLIDWORK is foreign in ANSYS bench computer code and by applying load and correct boundary constraints its analysis is obtained. The results of stress obtained in ANSYS are compared with theoretical calculations and supported the result section having least stress concentration is taken for more improvement.
For this methodology of improvement, pure mathematics improvement is employed as a tool. And supported high and fewer stress concentration the cross-sectional dimensions are modified. Here there are 3 new modelled (modified) cross sections that are model one, model a pair of and model three. Within the methodology of model one by reduced and adjusted the high stress concentration space of cross section. That are by variable the inner and outer dimension of the cross sections and keep the peak of cross section is constant. Within the methodology of model a pair of the pure mathematics is changed by reducing the either side of the serpentin member of hook cross section. Within the case of model three by increase the cross section of high stress concentration space. And cut back and alter the cross section of low stress concentration space. Finally, the new changed crane hook eye models are compared with the tetragon (existing) crane hook eye supported the FEM analysis and chosen the simplest one crane hook eye.
For this study used 3 varieties of geometric modifications to optimize the load and maximum stress of the hook. That are design-3, design-1 and design-2. And therefore the results of every changed hooks are compared with tetragon hook results supported completely different criterias that are soap stress, maximum equivalent strain, maximum deformation, weight and fatigue lifetime of the hooks. The applied load for all cross section is that the same that is four.5 tons. And compared the changed hooks every to different then chosen the simplest (better) model.
-
Methods of Modified Geometry 1 (Model -1)
For this changed hook (Design-3) the freelance parameters of high stressed space of cross section square measure breadth of inner aspect (bi) and breadth of outer aspect (bo). There square measure 3 Iterations having totally different breadth of inner aspect (bi) and breadth of outer aspect (bo) however the cross sectional square measures are constant for all Iterations. By alter (varying) these parameters analyzed the strain and hand-picked cross section having higher maximum equivalent stress that is Iteration two to match with alternative model hooks (design-1 and design-2).
-
Trapezoidal (b) Design-3
(c). Design-1 (d). Design-2
Figure 5 the 3D models of different cross sectional hooks which are trapezoidal, Design-3, Design-1 and Design-2
Figure 6 The mesh generating for the different cross section hooks
Table 3 indicated the mesh generating properties (number of elements and nodes)
Model of crane hook eye
Number of elements
Number of nodes
Trapezoidal
272408
391074
Design-3
270811
387911
Design-1
256997
369467
Design-2
266904
383795
-
-
Load condition of the crane hook eye
The load condition for all cross section is that the same in magnitude and direction as a result of the direction of applied load is that the same for all cross sections. Its applied vertically to downward direction as shown within the figure eleven. For these hooks the applied load is four.5 tons (44145 N) and also the results of total deflection, equivalent strain and Von-Mises stress is respectful rely upon the cross section. The force is distributed on the red colors of the hooks and it's identical for all cross- sectional hooks.
-
Design-3 cross section (b) Design-1 cross section
-
-
(c) Design-2 cross section (d).Trapezoidal (standard) cross section
Figure 7 Applied force on the trapezoidal, Design-3, Design-1, and Design-2 cross section hooks
RESULT AND DISCUSSION
In this portion is mentioned regarding the full results of constellation hook eyes. To realize the target of this paper stress and fatigue analysis area unit done on the various modelled crane hook eyes. Then ought to have discuss regarding these results and compare the results every to different.
Static structural analysis of trapezoidal crane hook eye
This section discusses the static structural analysis of trapezoidal crane hook eye. Figure twelve (d) shows the von-misses stress, total deformation and equivalent elastic strain of trapezoidal (existing) crane hook eye by applied load of 4.5 tons. The strain analysis has been done by ANSYS software, wherever the results are given by contours and numerical values. For the trapezoidal crane hook eye the maximum von-misses stress result from ANSYS is 84.149 MPa. And also, the maximum total deformation and equivalent elastic strain results area unit 0.2755 millimeter and 0.0004105. The load of trapezoidal (standard) hook indicated within the ANSYS workbench properties of pure mathematics is 14.233 Kg.
Static structural analysis of Design-3crane hook eye
The ANSYS analysis results of the model one crane hook eye as follow conferred by contours and numerical values. For this crane hook eye the utmaximum von-misses stress, total deformation and equivalent elastic strain is 85.563 MPa, 0.2785 millimeter and 0.0004174 severally. And also the weight of design-3 hook indicated within the ANSYS workbench is 13.984 Kg.
In the table six the design-3 is compared with trapezoidal counting on criteria of maximum stress, strain, deformation and weight of the hooks. The overall deformation and maximum equivalent elastic strain nearly a similar. Slightly design-3 is magnified than trapezoidal. The overall deformation and equivalent elastic strain of design-3 are magnified by 0.003mm and 0.000007.
The basic comparison should be supported the strain and weight of the hooks. As a result of the protection of the hook is counting on the strain iatrogenic on the hook. The magnified stress of design-3 from trapezoidal is 1.414 MPa (1.68%) however it's below safe condition. and also the reduced weight design-3 from trapezoidal is 0.249 kg (1.75%).
Table 4 Comparison of static structural analysis of design-3 crane hook eye with trapezoidal crane hook eye
Cross section of hook |
Load (tons) |
Maximum Total deformation (mm) |
Max Equivalent elastic strain (m/m) |
Max Equivalent (von- mises) stress (N/m2) |
Weight (kg) |
Design-3 |
4.5 |
0.2785 |
0.4174×10-3 |
85.563 x106 |
13.984 |
Trapezoidal |
4.5 |
0.2755 |
0.4105×10-3 |
84.149 x106 |
14.233 |
Static structural analysis of Design-1 crane hook eye
Results are obtained from analysis of Crane hook eye victimization ANSYS for 4.5tons load engaged on Crane hook eye. The maximum Von-Mises stress is 87.682 MPa, total deformation is 0.28443 metric linear unit and also the maximum equivalent elastic strain is 4.277 x 10-4. And also the weight of model two crane hook eye is 13.426 Kg.
The table seven is compared trapezoidal hook and design-1 with totally different results that are total deformation, equivalent elastic strain and von-mises stress. the load of design-1 is reduced by 0.807 kg (5.716%) compared to the trapezoidal hook that are shows the load on the on top of table seven. really the strain on the design-1 is larger than the trapezoidal by 3.533 MPa (4.2%) with an equivalent applied load. however its at intervals the limit stress of the fabric, then it's safe as thought of style.
Table 5 Comparison of static structural analysis of design-1 crane hook eye with trapezoidal crane hook eye
Cross section of hook |
Load (tons) |
Maximum Total deformation (mm) |
Maximum Equivalent elastic strain (m/m) |
Maximum Equivalent (von- mises) stress (N/m2) |
Weight (kg) |
Design-1 |
4.5 |
0.2844 |
0.4277×10-3 |
87.682×106 |
13.426 |
Trapezoidal |
4.5 |
0.2755 |
0.4105×10-3 |
84.149 x106 |
14.233 |
Static structural analysis of Design-2 crane hook eye
From the results of ANSYS the maximum von-misses stress performing on the inner fiber of the Design-2 crane hook eye is
80.93 MPa. Maximum total deformation and aso the maximum equivalent elastic strain are 0.30225 metric linear unit and 0.3989.
In the table 6 the design-2 is compared with trapezoidal with criteria of maximum stress, maximum equivalent elastic strain, total deformation and weight of the hooks. The maximum equivalent elastic strain of design-2 crane hook eye is a smaller amount than the trapezoidal. However total deformation of design-2 is bigger than trapezoidal. The entire deformation of design-2 redoubled by 0.0267mm and also the maximum equivalent elastic strain reduced by 0.0000116 from trapezoidal. The strain of model three is healthier than the trapezoidal stress. The reduced stress and weight of design-2 from trapezoidal is 3.22 MPa (3.825%) and 0.354 kg (2.487%).
Figure 8 shows the results of maximum stresses of the all modelled crane hook eyes. Design-2 has higher results of stress with scrutiny the others. And also the results of design-1 is bigger than the opposite modelled crane hook eyes.
Table 6 comparison of trapezoidal and design-2 hooks
Cross section of hook |
Load (tons) |
Maximum Total deformation (mm) |
Maximum Equivalent elastic strain (m/m) |
Maximum Equivalent (von-mises) stress (N/m2) |
Weight (kg) |
Design-2 |
4.5 |
0.3022 |
0.3989×10-3 |
80.93 x106 |
13.879 |
Trapezoidal |
4.5 |
0.2755 |
0.4105×10-3 |
84.149 x106 |
14.233 |
-
Equivalent (Von-Misses) stress model -1 (b). Equivalent (Von-Misses) stress model -2
-
Equivalent (Von-Misses) stress model -3 (d). Equivalent (Von-Misses) stress Trapezoidal
Figure 8 Maximum equivalent (Von-Misses) stress of modelled crane hook eyes by the maximum applied load
Stress and Weight Comparison of the modelled crane hook eyes
This portion discusses regarding the comparison of weight and maximum stress of recent modelled crane hook eyes (design-3, design-1 and design-2) and also the customary (trapezoidal). As we all know the reduction of weight of any mechanical half has a lot of blessings and increasing of stress is reversely as a result of it'll decrease the life time of the fabric (hook). The protection of the hook is betting on the strain induced on the hook and also the main objective of this study is weight optimization with safe life condition. Therefore, the comparison should be supported stress and weight of the hooks. Then here compare the hooks supported the on top of 2 things.
The table 7 and figure 9 shows the comparison of stress and weight of the modelled crane hook eyes. Once every optimization models are comparison with the trapezoidal (standard) crane hook eye;
The weight of design-3 crane hook eye is reduced by 0.249 kilogram and also the maximum Von-Misses stress induced on the design-3 crane hook eye is enlarged by 1.414 MPa with comparison the trapezoidal (standard) crane hook eye.
Based on the weight comparison the weight of Design-1 is smaller than the trapezoidal (standard) and different models of crane hook eyes however its maximum Von-Misses stress is larger than the all models of crane hook eyes. The weight is reduced by 0.807 kilogram and also the maximum Von- Misses stress is enlarged by 3.533 MPa from trapezoidal (standard) crane hook eye. Design-2 crane hook eye has higher results of weight and stress than trapezoidal (standard). The weight and stress of design-2 crane hook eye reduced by 0.354 Kg (2.49%) and 3.461 MPa (4.133%). Therefore, supported the FEM analysis of weight and maximum Von-Misses stress of design-2 is better than the opposite crane hook eyes.
Table 7 Comparison of hooks depending on maximum stress and weight of the crane hook eyes
Type of crane hook eye
Maximum von-Misses stress in (MPa)
Weight of the crane hook eye
In (Kg)
Design-3
85.563
13.984
Design-1
87.682
13.426
Design-2
80.93
13.879
Trapezoidal
84.149
14.233
-
Weight comparison of crane hook eyes
-
Comparison of Maximum Von-Misses stress of the hooks
-
-
Figure 9 Maximum Von-Misses stress and weight comparison of the modelled crane hook eyes
CONCLUSION
To conclude the results of each modified modelling crane hook eyes with the standard crane hook eye, the maximum Von- Misses stress and total deformation of model -1 and model -2 are increased. The fatigue life of both design-3 and design-1 crane hook eye is less than the standard crane hook eye. The maximum Von-Misses stress of model -3 is reduced and total deformation is increased. The fatigue life of design-2 crane hook eye is greater than the standard crane hook eye. Then design-2 crane hook eye has been selected as a best crane hook eye model.
From design-2 crane hook eye analysis get the following result which is achieved the objective of the thesis.
-
The maximum stress of design-2 crane hook eye is reduced by 3.461 MPa (4.133%) from the standard crane hook eye.
-
The total deformation induced on design-2 crane hook eye is greater than the standard crane hook eye by 0.035 mm. But the increased value is very small with comparing the overall dimension of the crane hook eye. And it has no effect on the life of the crane hook eye, because still life of design-2 is better than standard crane hook eye at any applied load.
-
The weight of design-2 crane hook eye is reduced by 0.354 Kg (2.487%) from thestandard crane hook eye. This means the mass and volume of the crane hook eye is optimized.
Therefore design-2 crane hook eye is considered as optimized result.
REFERENCE
[1] K. Ashok Babu, D.V. Subba Rao, Dr. P H V Sesha Talpa Sai, Design Optimization and Contact Analysis on Dual Joint. International Journal of Science, Engineering and Technology Research, vol. 4, pp. 2485-2493, July 2015. [2] Mr. Y.S.Mundada, Mr. S.J.Parihar, Review of Finite Element Analysis of Crane hook eye. in proc. CONVERGENCE 2016, April 2016, pp. 378- 381. [3] B. Nagaraju, M. RajaRoy, P. Venkatesh Reddy, K Satyanarayana, Stress Analysis of crane hook eye Using FEA. International Journal of Current Engineering and Scientific Research, vol. 2, pp. 126-131, February 2015. [4] Zaiyi Pana, Hongling Guoa, Yan Lia, Automated Method for OptimizingFeasible Locations of Mobile Cranes Based on 3D Visualization pp. 19-22 June 2017. [5] G.R.Dinesh, P.NaveenChandran, Analysis of Crane hook eye using ANSYS Simulation Tool. International Journal of Advances in Engineering, pp.434-438, April 2015.
[6] Dr. Daniel Kitaw, Pulleys, Sprockets, Drums and Load Handling Attachements in Material Handling Equipment, Ed. Ethiopia: Addis Ababa University, 2001, pp.76- 80. [7] Vivek Mahadev Thakur, Vaibhav Pawar, Dr. M.D. Nadar, Sanjay Ghorpade, Sahil Patil, Study and Analysis of Crane hook eye in Loading Area.International Journal of Advanced Research in Education & Technology, vol. 3, pp. 88-89, March 2016.
[8] A. Gopichand, R. V. S. Lakshmi, B. Maheshkrishna Optimization of design parameter for crane hook eye using taguchi method. International Journal of Innovative Research in Science, Engineering and Technology, vol.2, pp. 7780-7784, December 2013. [9] Nishant soni, crane-hook shapes optimization and thermal analysis using finite element too. IJAIR, PP. 51-55, 2013. [10] Rasmi Uddanwadikar Stress Analysis of Crane hook eye and Validation by Photo- Elasticity. Scientific Research, pp. 935-941, August 2011. [11] Pradyumnakesharimaharana, Computer Aided Analysis and Design of oisting Mechanism of an EOT Crane. Thesis, National Institute of Technology Rourkela, May 2012. [12] M. Shaban, M. I. Mohamed, A. E. Abuelezz and T. Khalifa, Determination of Stress Distribution in Crane hook eye by Caustic. International Journal of Innovative Research in Science, Engineering and Technology, vol. 2, pp. 1834-1840, May 2013. [13] Patel A.K, Jani V.K, Design and Dynamic Analysis of 70T Double Girder Electrical Overhead Crane. Journal of Information, Knowledge andResearch in Mechanical Engineering, vol. 2, pp. 496-503, October 2013.
[14] Takuma Nishimura, Takao Muromaki, Kazuyuki Hanahara, Damage factor Estimation of Crane hook eye (A database approach with Image, Knowledge and simulation), in pro. 4th International Workshop on Reliable Engineering Computing, 2010, pp. 623-632. [15] Santosh Sahu, Ritesh Dewangan, Manas Patnaik, Narendra Yadav,Study of Crane hook eye Having Trapezoidal Section by Finite Element Method& Design Experiments. International Journal of Modern Engineering Research, vol. 2, pp. 2779-2781, August 2012. [16] Chetan N. Benkar, Dr. N. A. Wankhade Finite Element Stress Analysis of Crane hook eye with Different Cross Sections. International Journal for Technological Research in Engineering, vol. 1, pp. 868-872, May 2014. [17] E.Narvydas, N.Puodziuniene, Circumferential Stress Concentration Factor at the Asymmetric shallow Notches of The lifting hook of trapezoidal cross-section. vol. 18, pp. 152-157, April 2012. [18] Yogesh Tripathi, K. Joshi, Comparison between Winker-Batch Theory and Finite Element Method in Crane hook eye for Trapezoidal Cross- Sectional Area. International Journal of Research in Engineering and Technology, vol. 2, pp. 26-31, September 2013. [19] Jeffrey W. Herrmann, Evaluating Design Optimization Models. Institute for Systems Research, 2007 [20] Columbus McKinnon Corporation (CM), Shank Crane hook eyes and Rigging Products, pp. 1-12, 2017. [21] ASM aerospace specification metals inc, AISI 4340 Steel.Internet:http://asm.matweb.com/search/SpecificMaterial.asp?bassnum=m434ae [22] Steven R. Schmid, Bernard J. Hamrock, Bo O. Jacobson, Fundamentals of machine element SI version 3rd edition, 2014.