
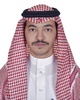
- Open Access
- Authors : Ahmed S. Al Jehani , Seraj Y. Abed
- Paper ID : IJERTV11IS070073
- Volume & Issue : Volume 11, Issue 07 (July 2022)
- Published (First Online): 20-07-2022
- ISSN (Online) : 2278-0181
- Publisher Name : IJERT
- License:
This work is licensed under a Creative Commons Attribution 4.0 International License
Reliability Centered Maintenance Applied on HVAC System
Ahmed S. Al Jehani
Department of Industrial Engineering King Abdulaziz University
Jeddah, Saudi Arabia
Seraj Y. Abed
Professor, Department of Industrial Engineering King Abdulaziz University
Jeddah, Saudi Arabia
Abstract- Reliability, availability, and maintainability are essential in nearly every endeavor that deals with providing services. Reliability Centered Maintenance (RCM) is a maintenance strategy that is implemented to optimize the maintenance program of a facility or system. Since failure cannot be prevented entirely, it is important to minimize its probability of occurrence, the impact of failures when they do occur, and the downtime. This paper is about Reliability Centered Maintenance (RCM) application on the HVAC system, especially on the Air Handling Unit. HVAC system information and failures data were collected and analyzed for one operation year at King Abdulaziz International Airport. Failure Mode and Effect Analysis (FMEA) was conducted on HVAC (AHU) system as its main part of the RCM analysis process. As a result of RCM analysis, a new preventive maintenance strategy and the total required activities were defined. Based on that monthly, quarterly, half-yearly, and yearly preventive maintenance activities and time of the Air Handling Unit were recommended, which improved the AHU system reliability, availability, and maintainability.
Keywords HVAC, RCM, Reliability, AHU, Maintenance, Airport
- INTRODUCTION
Air transport is an important enabler to achieving economic growth and development. Air transport facilitates integration into the global economy and provides vital connectivity on a national, regional, and international scale. It helps generate trade, promote tourism, and create employment opportunities. Airports has a significant impact in transportation system around the world, as it’s one of the main corners in the system. King Abdul-Aziz International Airport (KAIA) is considered one of the most ambitious, distinguished projects existing in the Kingdom and as a unique Airport in the area, as it is the air gate of the two Holy Mosques and the city of Jeddah which enjoys great economic weight and is witnessing steady growth in its air traffic.
HVAC System is considered one of the most important systems at the airports. Which has direct impact on passengers’ experience and directly effect on the Airport service quality level, Airport Environmental standards, and Safety, regulatory compliance, cost, and operational throughput.
Maintenance is an important factor in quality and performance of any systems and facilities. Optimize maintenance activities to ensure the availability and its readiness for proper operation play a key role on airport performance. It would also reduce the risk of failures and interruption that may affect passengers and stakeholders. Therefore, Reliability Centered Maintenance (RCM) was
applied to HVAC system especially on Air Handling Unit (AHU) to optimize the performance, availability, and reliability of the system at the Airport.
- LITERATURE REVIEW
Reliability Centered Maintenance (RCM) is a process to determine the maintenance requirements of any asset/machinery under its optimal operating conditions. It is a process that is completed to make sure that all the machinery and assets perform as desired by their users with optimum efficiency. RCM can be used to develop scheduled and proactive maintenance procedures, redesigning of equipment, improve troubleshooting procedures hence increasing the overall efficiency of the process and reducing its cost. Therefore, RCM is a structured process that is used to determine failure modes and develop strategies to overcome them, under operation requirements and effective cost. S. Ahmed, M. Asif and A. Zaidi (2020)
Reliability Centered Maintenance (RCM) integrates Preventive Maintenance (PM), Predictive Testing and Inspection (PT&I), reactive maintenance, and Proactive Maintenance to increase the probability that a machine or component will function in the required manner over its designed life cycle with a minimum amount of asset failure and downtime. These principal maintenance strategies, rather than being applied independently, are optimally integrated to take advantage of their respective strengths. The goal of this approach is to reduce the Life-Cycle Cost (LCC) of a facility to a minimum while continuing to allow the facility to function as intended with required reliability and availability. NASA (2008).
Reliability Centered Maintenance methodology that requires a combination of engineers and technical skills, as well as management awareness and motivation, offers the most systematic and efficient process to address an overall programmatic approach to optimization of HVAC systems. A solution to many of the problems associated with the HVAC systems will reduce sickness, create a better working environment, reduce energy consumption, and lower maintenance cost. Therefore, there is immediate need to develop an expert system to help owners and users optimize the function of HVAC system. Daniel Wong, B. Eng., M.B.A. (2000).
According to M. BUGAJ (2011), Implementation will (or should) usually begin during the Analysis Phase of an RCM project and may provide information for improvement of the analysis. Implementation involves many activities, such as:
Analysis of historical data, Identification of resources (time, manpower), Procedure writing, parts and consumables needed to carry out the procedures.
According to Ciani, Guidi, Patrizi, Galar (2021), Reliability-centered maintenance is an effective way to select the appropriate maintenance policies for every type of system. Classical RCM process is consists of five steps:
- Initiation and planning
- Functional failure analysis (identifying the failure modes, causes, effects and criticalities.)
- Task selectionselecting the appropriate maintenance task and interval
- Implementation
- Continuous improvementmonitor the effectiveness
In the same way, according to (Haidar Al Haiany, 2016), Failure Modes and Effect Criticality Analysis (FMEA & FMECA), is one of the main used methods for performing the reliability analysis. FMEA usually starts in early phase of system design.
- METHODOLOGY
The goal of an RCM approach is to determine the most applicable cost-effective maintenance technique to minimize the risk of impact and failure and to create a hazard-free working environment while protecting and preserving capital investments and their capability. This goal is accomplished through the identification of failure modes and their consequences for each system.
The following steps are followed to implement Reliability-Centered-Maintenance:
-
- Select the most critical equipment
- Identify the boundaries & functions of the equipment
- Define the failure modes
- Identify the root causes of the failure modes
- Enumerate consequences of failures
- Select a maintenance tactic for each failure mode
- Establish an overall maintenance plan
- Steps to impalement the methodology
The previous steps are associated by engineering and RCM tools for more clarifications of selected asset, scope of analysis, and resources planning for the recommended future maintenance plan.
- General information about the asset
- Scope of analysis
- p>Theory of operation
- Equipment/ system description
- Functions of the asset
- Functional failure
- Failure Mode
- Failure effect
- Failure consequence
- New Maintenance Plan
- Resources Planning
- Implementation
- Data Collection
Current system performance plays key role to improve analysis and study outputs. To get more accurate data and good analysis, data of HVAC failures in KAIA-Terminal (1) for 2 years was collected and analyzed. In the same way,
current preventive maintenance frequency collected and analyzed to get indication of the whole system performance.
- Data Analysis
To optimize the utilization of the RCM over all its phases, qualitative and quantitative analysis tools could be applied to improve the outputs accuracy, which aligned with the previous implementation steps of the RCM. The following methods and tools are considered a key to implement a proper RCM analysis.
- Historical Data Analysis
To improve the reliability of the selected asset, historical maintenance activities and failures data were collected and analyzed to get indication of the whole current system performance. the historical data contained on corrective maintenance historical data, current preventive maintenance plan, manpower utilization and spare parts usage, etc. The following analysis tools were applied to the historical data.
- Mean Time Between Failure (MTBF)
- Availability of spare parts
- Response time
- Incident resolution time
- Travel Time analysis
- Failure Mode and Effect Analysis (FMEA)
FMEA is one of the main used methods for performing the reliability analysis. FMEA is applied to each system, subsystem, and component identified in the boundary definition. For every function identified, there can be multiple failure modes. The FMEA addresses each system function, all possible failures and the dominant failure modes associated with each failure. The FMEA then examines the consequences of failure to determine what effect failure has on the mission or operation on the system and on the machine. In the FMEA analysis stage criticality assessment provides the means for quantifying how important a system function is relative to the identified mission. FMEA ranks the effects from lowest (1) to highest (10). The probability of occurrence (failure) will be determined aligned with the previous way of criticality assessment (ranking), which provides a method of quantifying the probability of failure. Historical data provides a powerful pre-request in establishing the ranking.
- Historical Data Analysis
-
- HVAC SYSTEM (AIR HANDLING UNIT)
Air Handling Unit is one of the most important equipment in the Heating, Ventilation, and Air Conditioning System. In the same way, it’s considered front of house equipment, that has direct impact on passengers’ experience. Failure and poor management of AHU will have an impact on the following:
-
- Adversely affect quality levels
- Environmental standards of the Airport facility.
- Safety, regulatory compliance, cost, or operational throughput.
Accordingly, provisions for any critical equipment must be accounted to support the sustainability of the business entity.
- AHU Functions
Air handling units are able to fan, heat, cool, filters and humidify. That serve all terminal and offices in the Airport.
In addition it takes outside air, recondition it and supply it as fresh air to the building, the AHU performs other functions:
- Filtration and control of the quality of the air that will reach the interior, using air purification filters, and depending on the retention of these filters, the air will be clean.
- Control of the air temperature that regulates the air conditioning system in cold or hot, so that the thermal sensation in the interior is the desired one maintained.
- Monitors the relative humidity monitoring for greater indoor comfort.
- AHU System Description
The system consists of a recirculating air handling unit (AHU) with:
- Supply fan with VFD.
- Modulating Outside, Return and field air dampers.
- Pre-filter.
- Bag filter.
- 2-way modulating valves
- Duct mounted temperature sensors.
- Duct mounted smoke detectors.
- Duct Pressure Sensor.
- Room CO2 Sensor.
- AHU Operation sequence & Operating tempo
Most of the equipment in the new terminal entered to the operation in 2019, with 24 Hour operating tempo. However, it can be in low utilization mode at the night in some sections in the terminal. The active operation mode shall be determined based in any of the following means:
- Automatically from the Building Management System (BMS), Based on a programmed time schedule.
- Manually from the BMS by an operator manually entered command.
- AHU Attributes
To maximize the accuracy of the outputs and build reliable maintenance strategy, the main equipment attributes has been analyzed and recorded. There are two main attributes for Air Handling Unit as shown in table (1):
Table 1. Main attributes for Air Handling Unit
In the same way, it’s important to understand equipment’ parts attributes. One of the main parts of the AHUs is the belt, which must be correctly tensioned to ensure good contact with the pulley. If the belt is insufficiently tensioned, the belts may slip, and if it excessively tensioned, the motor and fan bearings may be over-loaded.
Figure 1. Belt factors
When correctly tensioned, the belt deflection L will be 15 mm per meter of distance between centers c/c when a force P1 (N) is applied and P < P1 < 1.5P, where the force P is dependent on the belt type as shown in table (2). The
deflection should be measured preferable by means of tensiometer.
The second part is AHU’s bearing, normally fans are fitted with grease ball bearing series: SY and type UCP with minimum anticipated running life of:
Fan with speed up to 1000 RPM 25000 hrs Fan with speed between 1500/2000 RPM 20000 hrs Fan with speed between 2000/3000 RPM 15000 hrs Table 2. Bearing running life
-
- FAILURE MODE AND EFFECT ANALYSIS FOR AIR HANDLING UNIT
(FMEA) is one of the main used methods for performing the reliability analysis, which is considered an essential part of an RCM analysis process. The FMEA addresses each system function, all possible failures, and the dominant failure modes associated with each failure. The FMEA then examines the consequences of failure to determine the effects on the system functionality.
- Logic tree diagram
The basic (LTA) uses the decision tree structure shown in figure (2). From this figure, decision bins: 1) safety related,
2) outage-related, or 3) economic-related were noticed. Each failure mode is entered into the top box of the tree and the logic of the tree is to be followed. This will support the decision making of the required and possible maintenance strategy for each failure.
Attributes Unit of Measurement Min Recorded Max Recorded Volume M3/S 0.5 20 Static Pressure Pascals (Pa) 250 730 - Criticality of Occurrence
Figure 2. Logic tree diagram
Criticality assessment provides the means for quantifying how important a system function is relative to the identified mission. The following table provides a method for ranking system criticality.
- Probability of Occurrence
The probability of occurrence (failure), the following table provides one possible method of quantifying the probability of failure. Historical data provides a powerful tool in establishing the ranking.
R Effect Comment 1 None No reason to expect failure to have any effect on safety, health, environment, or mission. 2 Very Low Minor disruption to facility function. Repair to failure can be accomplished during trouble call. 3 Low Minor disruption to facility function. Repair to failure may be longer than trouble call but does not delay mission. 4 Low to Moderate Moderate disruption to facility function. Some portion of mission may need to be reworked or process delayed. 5 Moderate Moderate disruption to facility function. 100% of mission may need to be reworked or process delayed. 6 Moderate to High Moderate disruption to facility function. Some portion of Mission is lost. Moderate delay in restoring function. 7 High High disruption to facility function. Some portion of Mission is lost. Significant delay in restoring function. 8 Very High High disruption to facility function. All of Mission is lost. Significant delay in restoring function. 9 Hazard Potential Safety, Health, or Environmental issue. Failure will occur with warning. 10 Hazard Potential Safety, Health, or Environmental issue. Failure will occur without warning. Table 3. Criticality of Occurrence
R Effect Comment 1 1/5,000 Remote probability of occurrence; unreasonable to expect failure to occur. 2 1/5,000 Low failure rate. Similar to past design that has, in the past, had low failure rates for given volume/loads. 3 1/2,000 Low failure rate. Similar to past design that has, in the past, had low failure rates for given volume/loads. 4 1/1,000 Occasional failure rate. Similar to past design that has, in the past, had occasional failure rates for given volume/loads. 5 1/500 Moderate failure rate. Similar to past design that has, in the past, had moderate failure rates for given volume/loads. 6 1/200 Moderate to high failure rate. Similar to past design that has, in the past, had moderate failure rates for given volume/loads. 7 1/100 High failure rate. Similar to past design that has, in the past, had high failure rates that has caused problems. 8 1/50 High failure rate. Similar to past design that has, in the past, had high failure rates that has caused problems. 9 1/20 Very High failure rate. Almost certain to cause problems. 10 1/10+ Very High failure rate. Almost certain to cause problems. Table 4. Probability of Occurrence
- Failure Mode and Effect Analysis Table
Based on the collected data of the failures of HVAC System (Air Handling Unit) at King Abdulaziz International Airport for one year of operation, the following table showing the FMEA analysis of the selected system.
It cannot supply the required air flow to the space
2
4
Preventive Maintenance
It cannot supply the required air flow to the space
4
5
Condition Based (Building Management System BMS)
It cannot supply the required air flow to the space
3
4
Preventive Maintenance
4
5
Condition Based (Building Management System BMS)
+
Preventive Maintenance
FMEA Information Table Component Analyzed: AHU N Function Functional Failure Failure Mode (Cause of Failure) Failure Effect (What Happens when it Fails) Criticality Probability Proposed Maintenance Type 1 To Supply the required amount of conditioned air at acceptable noise level to meet the inside condition of the occupancy A Insufficient Air Flow 1 Fan 1 To Supply the required amount of conditioned air at acceptable noise level to meet the inside condition of the occupancy A Insufficient Air Flow 2 Duct System 1 To Supply the required amount of conditioned air at acceptable noise level to meet the inside condition of the occupancy A Insufficient Air Flow 3 Filters dirty or clogged It cannot supply the required air flow to the space 4 6 Preventive Maintenance 1 To Supply the required amount of conditioned air at acceptable noise level to meet the inside condition of the occupancy A Insufficient Air Flow 4 Coils dirty or clogged It cannot supply the required air flow to the space 4 7 Preventive Maintenance 1 To Supply the required amount of conditioned air at acceptable noise level to meet the inside condition of the occupancy A Insufficient Air Flow 5 Recirculation Internal cabinet leaks in bulkhead separating fan outlet (pressure zone) from fan inlet (suction zone) leak around fan outlet at connection through cabinet bulkhead It cannot supply the required air flow to the space 4 5 Preventive Maintenance 1 To Supply the required amount of conditioned air at acceptable noise level to meet the inside condition A Insufficient Air Flow 6 Obstructed Fan Inlets Elbows, cabinet walls or other obstructions restrict air flow inlet obstructions cause more restrictive systems but do not cause Increased negative pressure readings near the fan inlet(s). Fan speed may be increased to counteract the effected of restricted fan inlet (s) It cannot supply the required air flow to the space 2 4 Preventive Maintenance 1 To Supply the required amount of conditioned air at acceptable noise level to meet the inside condition A Insufficient Air Flow 7 No Straight Duct at Fan Outlet a) fans which are normally used in duct system are tested with a length of straight duct at the fan outlet. It there is no straight duct at the tan outlet, decreased performance will result if it is not practical to install a straight section of duct at the fan outlet, the fan speed may be Increased to overcome this pressure loss. It cannot supply the required air flow to the space 2 3 Run to Fail 1 To Supply the required amount of conditioned air at acceptable noise level to meet the inside condition A Insufficient Air Flow 8 Obstructions In High Velocity Air Stream 2 To Supply the required amount of conditioned air at acceptable noise level to meet the inside condition of the occupancy B Power High 1 Fan - forward curved impeller installed backwards
- fan running backwards
- cut-off missing or improperly Installed
- fan speed too slow
- actual system is more restrictive (more resistance to flow) than expected
- dampers closed
- registers closed
- leaks in supply ducts
- insulating duct liner loose
- obstruction near fan outlet
- sharp elbows near fan outlet
- improperly designed turning vanes
- projections, dampers, or other obstruction in part of system where air velocity Is high
- backward inclined impeller installed backwards
- fan speed too high
- High energy consumption
- Motor operates in overload condition
- Premature motor failure
3
5
Preventive Maintenance
3
4
Preventive Maintenance
4
1
Run to Fail
3
4
Condition Based (Building Management System BMS)
+
Preventive Maintenance
3
6
Condition Based (Building Management System BMS)
2 To Supply the required amount of conditioned air at acceptable noise level to meet the inside condition of the occupancy B Power High 2 System 2 To Supply the required amount of conditioned air at acceptable noise level to meet the inside condition of the occupancy B Power High 3 Gas Density a) calculated horsepower requirements based on light gas (e.g., high temperature but actual gas is heavy (e.g., cold start up) 2 To Supply the required amount of conditioned air at acceptable noise level to meet the inside condition of the occupancy B Power High 4 Fan Selection a) Fan not operating at efficient point of rating. Fan size or type may not be best for application. 3 To Supply the required amount of conditioned air at acceptable noise level to meet the inside condition C Fan Does Not Operate 1 Electrical Or Mechanical Mechanical and electrical problems are usually straight forward and are normally analyzed in a routine manner by service personnel. In this category are such item as: g) motor too small and overload protector has broken circuit
This will cause fan failure with no air flow to the system 6 7 Condition Based (Building Management System BMS/ I2BS) +
Preventive Maintenance
4 To Supply the required amount of conditioned air at acceptable noise level to meet the inside condition D Premature Failure 1 Belts, Bearings, Sheaves, Impeller, Hubs Etc. Each Fan component is designed to operate satisfactory for a reasonable lifetime. Fan intended for heavy duty service are made especially for the 1 types of service. For example, Class 1 fans are intended for operation below certain limits of pressure and. outlet velocity. Class II fans are designed for higher operating limits, not all components are limited by the same factors.
This will cause noise and air flow problem. That will cause fan failure prematurely. 6 8 Condition Based (Building Management System BMS) +
Preventive Maintenance
5 To Supply the required amount of conditioned air at acceptable noise level to meet the inside condition E Static Pressure Wrong 1 System It cannot supply the required air flow to the space 4 7 Condition Based (Building Management System BMS +I2BS)
+
Preventive Maintenance
5 To Supply the required amount of conditioned air at acceptable noise level to meet the inside condition of the occupancy E Static Pressure Wrong 2 System, Fan or Interpretation or Measurement The velocity pressure at any point of measurement is a function of the velocity of the air or gas and Its density. The static pressure at a point of measurement In the system Is a lucullan of system design (resistance to flow), air density and the amount of air flowing through the system. The static pressure measured in a ‘loose” or oversized system will be less than the static pressure in a ‘tight” or undersized system for the same flow rate. 5 To Supply the required amount of conditioned air at acceptable noise level to meet the inside condition of the occupancy E Static Pressure Wrong 3 System a) system has less resistance to flow than expected. This is a common occurrence. Fan speed may be reduced to obtain desired flow rate. This will reduce power (operating cost). It supplies too much air 2 6 Condition Based (Building Management System BMS) 5 To Supply the required amount of conditioned air at acceptable noise level to meet the inside condition of the occupancy Static Pressure Wrong 4 Gas Density Pressure will be less with high temperature gases or high attitudes - oversized duct work
- face and by-pass dampers oriented so coil dampers are open at the same time by-pass dampers are open
- filter(s) let out
- access door open
- High energy consumption
- Motor operates in overload condition
- Premature motor failure
- High energy consumption
- Motor operates in overload condition
- Premature motor failure
- High energy consumption
- Motor operates in overload condition
- Premature motor failure
- blow fuses c) loose pulleys
- broken belts
- electricity tuned off f) wrong voltage
- impeller touching scroll
- obstruction in system
- dirty filters
- Dirty coils.
It supplies too much air to the system
2
5
Condition Based (Building Management System BMS)
This will cause noise problem and possible physical damage to fan impeller and housing
3
7
Preventive Maintenance
5 To Supply the required amount of conditioned air at acceptable noise level to meet the inside condition E Static Pressure Wrong 5 Fan It supplies too much air 2 7 Condition Based (Building Management System BMS) 6 To Supply the required amount of conditioned air at acceptable noise level to meet the inside condition F Too Much Air Flow 1 System 6 To Supply the required amount of conditioned air at acceptable noise level to meet the inside condition F Too Much Air Flow 2 Fan backward inclined impeller installed backwards (power will be high) It supplies too much air to the system 3 4 Preventive Maintenance 7 To Supply the required amount of conditioned air at acceptable noise level to meet the inside condition of the occupancy G Noise 1 Impeller Hitting Inlet Ring 7 To Supply the required amount of conditioned air at acceptable noise level to meet the inside condition of the occupancy G Noise 2 Impeller Hitting Cut Off This will cause noise problem and possible catastrophic failure 6 6 Condition Based (Building Management System BMS) & Preventive Maintenance
7 To Supply the required amount of conditioned air at acceptable noise level to meet the inside condition of the occupancy G Noise 3 Drive Sheave not tight on shaft (motor and/or fan) belts hitting bell tube bells too loose. belts too tight belts wrong section belts not “matched” In length on multi-bell drive variable pitch sheaves not adjusted so each groove has same pitch diameter (multi-belt drives) misaligned sheaves belts, wrong motor, motor base or fan no securely anchored, belts oily or dirty Improper drive selection. This will cause noise problem 4 7 Preventive Maintenance 7 To Supply the required amount of conditioned air at acceptable noise level to meet the inside condition of the occupancy G Noise 4 Coupling coupling unbalanced, misaligned, loose or may need lubricant This will cause noise problem 3 7 Preventive Maintenance 7 To Supply the required amount of conditioned air at acceptable noise level to meet the inside condition of the occupancy G Noise 5 Bearing defective bearing need lubrication loose on bearing support loose on shaft seals misaligned foreign material inside bearing worn bearing fretting corrosion between inner race and shaft This will cause noise problem 4 8 Preventive Maintenance 7 To Supply the required amount of conditioned air at acceptable noise level to meet the inside condition of the occupancy G Noise 6 Shaft Seal Squeal This will cause noise problem 3 7 Preventive Maintenance 7 To Supply the required amount of conditioned air at acceptable noise level to meet the inside condition of the occupancy G Noise 7 Impeller a) loose of shaft b) defective impeller. Do not run the fan. Contact manufacturer c) unbalance d) coating loose e) worn as result of abrasive or corrosive material moving through flow passages This will cause noise problem 4 7 Preventive Maintenance 7 To Supply the required amount of conditioned air at acceptable noise level to meet the inside condition of the occupancy G Noise 8 Housing This will cause noise problem 3 4 Preventive Maintenance - Backward incident impeller installed backwards. Power will be high
- fan speed too high
- oversized duct work
- access door open
- registers or grilles not installed d) dampers set to by-pass coils e) filter (s) not in place
- impeller not centered in jet ring
- inlet ring damaged
- crooked or damaged Impeller
- shaft loose in bearing
- Impeller loose on shaft
- bearing loose in bearing support
- cut-off does not secure in housing
- cut-off damaged
- cut-of improperly positioned
- need lubrication
- misaligned
- foreign materials in housing
- cut-off other parts loose (rating during operation)
This will cause noise problem
4
5
Preventive Maintenance
This will cause noise problem
3
5
Preventive Maintenance
7 To Supply the required amount of conditioned air at acceptable noise level to meet the inside condition of the occupancy G Noise 9 Electrical a) lead-in cable not secure b) AC hum in motor or relay c) starting relay chatter d) noisy motor bearing e) single phasing a 3-phase motor
This will cause noise problem 3 5 Preventive Maintenance 7 To Supply the required amount of conditioned air at acceptable noise level to meet the inside condition of the occupancy G Noise 10 Shaft 7 To Supply the required amount of conditioned air at acceptable noise level to meet the inside condition of the occupancy G Noise 11 High Air Velocity 7 To Supply the required amount of conditioned air at acceptable noise level to meet the inside condition of the occupancy G Noise 12 Obstruction In High Velocity Gas Stream May Cause Rattle, Or Pure Tone Whistle a) dampers b) registers c) grilles d) sharp elbows This will cause noise problem 2 6 Preventive Maintenance 7 To Supply the required amount of conditioned air at acceptable noise level to meet the inside condition of the occupancy G Noise 13 Pulsation Or Surge restricted system causes to operate at poor point of rating fan too large for application ducts vibrate at same frequency as fan pulsation
This will cause noise problem 3 4 Preventive Maintenance 7 To Supply the required amount of conditioned air at acceptable noise level to meet the inside condition of the occupancy G Noise 14 Gas Velocity Through Cracks Holes or Past Obstructions a) leaks duct work b) fine on cols c) register or grills
This will cause noise problem 4 6 Preventive Maintenance 7 To Supply the required amount of conditioned air at acceptable noise level to meet the inside condition of the occupancy G Noise 15 Rattles And/or Rumbles a) vibrating duct work b) vibrating cabinets parts c) vibrating parts isolated from buildings This will cause noise problem 2 6 Preventive Maintenance - bent
- undersized. May cause noise at impeller, bearing or sheave.
- if more than two bearings are on shaft. they must be properly aligned.
- duct work too small for application
- fan selection too small for application
- register or grilles too small to application
- heating or cooling coils with insufficient face area for application
- sudden expansion in duct work
- sudden contraction in duct work
- turning vanes
Table 5. Failure Mode and Effect Analysis (AHU)
- Logic tree diagram
- DEVELOPED MAINTENANCE STRATEGY
Proper and regular maintenance must be comprehensively accomplished to preserve its safety, reliability, and operating life. To achieve these, new maintenance strategy developed based on the RCM analysis results and manufacture manual.
The maintenance manual must be carefully read before performing any maintenance task. Preventive Maintenance check lists must be carried out in line with the recommended frequency by teams of experienced and trained technicians. Maintenance management team shall ensure that regular, or required, training is received to update and improve their knowledge of the technologies/systems they are required to support. This fulfils the basic premise of the Quality ISO 9001 and Environmental ISO 14001. It is preferred that technicians have the appropriate certifications on systems for which they are responsible.
The new strategy of preventive maintenance is divided into two main scopes which are mechanical and electrical activities. The required activities are defined with the required time of each activity. The new maintenance program divided to monthly, quarterly, half-yearly, and yearly maintenance frequency.
- Preventive Maintenance Mechanical Activities
15.00
12.00
12.00
17.00
12.00
12.00
18.00
15.00
15.00
15.00
4.00
12.00
120.00
5.00
AHU Preventive Maintenance Mechanical Activities Sr. Task Monthly Quarterly Half Yearly Yearly Time (Min) 1 Use pressurized water to clean the panel filter, cleaning with solvents is not recommended. Replace if required. 2 Visually check by differential pressure gauges if the bag air filter is clogged. Tap it in designated area to clean it. 7.30 3 Check for unusual noise and vibration. Correct as required. 7.30 4 Check and record motor ampere and voltage. 3.00 5 Check internal insulation and air leakage. Correct as necessary. 8.00 6 Check and record inlet / outlet temperature and pressure of water and of air. 8.00 7 Check Damper Position and Correct if required 4.00 8 Replace the air filters. 9 Lubricate fan and motor bearings with specified lubricant. 10 Check for belt(s) tension. Replace if required. 11 Clean cooling coil and drain pan by pressurized water. Check the blower and body insulation.
60.00 12 Check the humidification / dehumidification system if provided. Correct if required. 13 Clean the chilled water strainer 14 Replace the Belt 15 Check unit controls and sensors for proper operation. Correct if required.
16 Clean control panel. Check contactors, connectors, terminals and wiring for loose connections and signs of overheating. Correct as necessary. 17 Check motor damper, guide vanes and hinges. Lubricate if required.
18 Check the function of heater if provided. 19 Check motor winding insulation. 20 Check and clean the inlet / outlet /drain pipe work, valves, and air vents. Lubricate the electrically controlled valves if provided. 21 Check and report if unit require repaint. Total Time (Min) 52.6 162.6 193.6 349.6 Table 6. Preventive Maintenance – Mechanical Activities
- Preventive Maintenance Electrical Activities
AHU Preventive Maintenance Electrical Activities | ||||||
Sr. | Task | Monthly | Quarterly | Half Yearly | Yearly | Time (Min) |
1 | Check the temperature, the humidity, the presence of corrosive or explosive gases and the presence of dust in the area electrical room doors and windows should be closed room temperature should not exceed 40 C | 5.00 | ||||
2 | Check for any abnormal sound or vibration of the reactor, transformer or cooling fans. | 5.00 | ||||
3 | Check abnormal odors such as the smell of burning insulating materials etc. | 3.00 | ||||
4 | Stop the equipment and check the motor has completely stopped | 3.00 | ||||
5 | Press the interlock switch on the operation panel, the switch should turn on and switch RED light has turn on | 2.00 | ||||
6 | Turn off and lock out the control power supply | 4.00 | ||||
7 | Turn off and lock out any other job specific power feeding the drive (panel space heater, SCADA) | 4.00 | ||||
8 | Before to start open any door wait for 15 minutes or more for the DC bus discharge All maintenance work on the board should be carried out at least 15 minutes after all power supplies are turned off to allow all capacitors on the board to discharge. | 15.00 | ||||
9 | Verify that all power is removed by measuring the main, the DC bus, the control and any other external source voltage levels with properly rated measuring equipment | 8.00 | ||||
10 | Ground the 3-Phase input power supply terminal at the main circuit input terminals | 5.00 | ||||
11 | Check to see if there is any abnormality with air flow, increased fan noise, etc. | 5.00 | ||||
12 | Visually check if the air filter is clogged. Tap it outside the room to remove the loose dust | 4.00 | ||||
13 | Use water to clean the filter, cleaning with solvents is not recommended | 8.00 | ||||
14 | Check to see that is no wires or mounted parts are broken, disconnected, loose or damaged (cable can be cleaned with isopropyl alcohol). | 5.00 | ||||
15 | The boards must be protected from dust, corrosive gases and extreme temperatures | 4.00 | ||||
16 | Use brush to carefully wipe off dust, inspect boards for signs of component damage, heating and corrosion | 10.00 | ||||
17 | When removing the board, disconnect all the connectors and wires and remove the mounting screws from the upper part of the board first At this time be careful not to drop the boards or screws, when setting the board down, place it on static free surface, be careful no to damage any components. | 3.00 | ||||
18 | When attaching the board, do so the order opposite to removing procedure. Be sure that all of the connectors and wires are connected correctly | 3.00 |
15.00
12.00
19 | Check the drive to make sure no tools or other foreign objects were left in the drive | 2.00 | ||||
20 | Remove the LOCKOUT and turn on the main supply and controls supply and verify the cooling fans operation of both banks. | 8.0 | ||||
21 | After safety checks, prepare for the operation. Press the interlock switch on the operation panel when the LED is turned off, the interlock is off. If the drive is ready, it will start if commanded | 8.00 | ||||
22 | Check to see if the dust is stuck to the cubicle interior or if there is any discoloration, heat generation, abnormal sound, leakage, odor or damage with the reactor, transformer, contactors, cables and bus bars connections, fuses, capacitors, disconnect switches and meter. | |||||
23 | Check the protection functions for proper operation (door switches and cooling fans) | |||||
Total Time (Min) | 114 | 114 | 114 | 141 |
Table 7. Preventive Maintenance – Electrical Activities
VII.CONCLUSION
This paper has presented the Reliability Centered Maintenance (RCM) methodology, steps, tools, and its application to the HVAC system, especially for the Air Handling Unit. Air Handling Unit systems functions, components, and attributes are presented and analyzed which provides a comprehensive understanding of the system and study scope.
Failure Mode and Effect Analysis (FMEA) is presented in the paper as the main tool of RCM. The ranking methodology of failures criticality and probability of occurrence was developed to classify the failures to select the proper maintenance strategy. FMEA was applied based on the collected historical data of the failures showed the AHUs failure mode, effect, and the consequences on the functionalities of the system.
As a result of the Failure Mode and Effects Analysis (FMEA), a new maintenance strategy has been proposed. The proposed maintenance strategy combined three maintenance methods in one strategy, which includes Run-to-Fail, Preventive Maintenance, and Condition-Based-Maintenance. The new strategy of preventive maintenance is divided into two main scopes which are mechanical and electrical activities. The total time required to perform mechanical activities is 52.6 Min Monthly, 162.6 min quarterly, 193.6 min half-yearly, and 349.6 min yearly. In the same way, the total time to perform electrical activities is 114 Min Monthly, 114 min quarterly, 114 min half-yearly, and 141 min yearly.
The study shows that the reliability, availability, and maintainability analysis is useful for decision-making about developing maintenance strategies. This helps in understanding system functions, failures, failure effects and selecting the proper maintenance strategy based on the failure type. To optimize the maintenance process, management
must continue the shift from a reactive to proactive maintenance approach. They must also continue to optimize the utilization of technologies such as Building Management System (BMS), Integrated Intelligent Building System (I2BS), and Computerized Maintenance Management System (CMMS) to identify the problems before failure.
VIII. REFERENCE:
[1] Ciani,L.;Guidi,G.;Patrizi, G.; Galar, D. Condition-Based Maintenance of HVAC on a High-Speed Train for Fault Detection. Electronics 2021,10,1418. https:// doi.org/10.3390/electronics10121418 [2] Abhishek Kumar, Puneet Sharma, Amit Agarwal. RAMS of HVAC for Rolling Stock Application. International Journal of Engineering Research & Technology (IJERT). Vol.10 Issue 08, August-2021.ISSN: 2278-0181
[3] Sohaib Ahmed, Muhammad Asif ,Asad A. Zaid, Reliability Centered Maintenance (RCM) of a Commercial HVAC Air Handling and Condensing Unit, European Journal of Advances in Engineering and Technology, 2020 [4] Gonzalo Sanchez-Barroso a, Justo Garcia Sanz-Calcedo, Application of Predictive Maintenance in Hospital Heating, Ventilation and Air Conditioning Facilities, Emerging Science Journal. Vol. 3, No. 5,October, 2019
[5] Dwi Priyanta1, Nurhadi Siswantoro2, Rizky Agung Sukandar, Determination of Maintenance Task on Rotary Equipment Using Reliability Centered Maintenance II Method, International Journal of Marine Engineering Innovation and Research, Vol. 4(3), Sept. 2019. 191-198 [6] G.Gupta, R.P.Mishra. Identification of Critical Components using ANP for Implementation of Reliability Centered Maintenance. 25th CIRP Life Cycle Engineering (LCE) Conference, 30 April-2 May 2018, Copenhagen, Denmark [7] Haidar Al Haiany (2016). RELIABILITY CENTEREDMAINTENANCE – Different Implementation Approaches. Division of Operation and Maintenance Engineering Lulea University of Technology.
[8] Filippo De Carlo, Maria Antonietta Arleo, Mario Tucci, Orlando Borgia. (2015). Condition Based Maintenance optimization for a service plant. * Department of Management, Economics, and Industrial Engineering, Polytechnic di Milano, via LA Bruschini, 4, 20156, Milano. [9] Au-Yong, C. P., Ali, A. S., & Ahmad, F. (2014). Improving Occupants’ Satisfaction with Effective Maintenance Management ofHVAC System in Office Buildings. Automation in Construction, 43, 31-37.
[10] Mariam Altaf Tarar, Study Reliability Centered Maintenance (RCM) of Rotating Equipment through Predictive Maintenance, 2nd International Conference on Research in Science, Engineering and Technology (ICRSET2014), March 21-22, 2014 Dubai (UAE) [11] Fischer, K.; Besnard, F.; Bertling, L.; , “Reliability-Centered Maintenance for Wind Turbines Based on Statistical Analysis and Practical Experience,” IEEE Transactions on Energy Conversion, , vol.PP, no.99, pp.1-12, doi: 10.1109/TEC.(2011).2176129 [12] M. BUGAJ, University of Zilina, Faculty of Transport and Communication, Air Transport Department Univer- zitna 8215/1, 010 26 Zilina, Slovak Republic. Vol 1. issue 1. Feberury 2011. [13] Alireza Ahmadi, Aircraft Scheduled Maintenance Programme Development Decision Support Methodologies and Tools, Division of Operation and Maintenance Engineering Lulea University of Technology June 2010 [14] NASA.(2008), Reliability-Centered Maintenance Guide For Facilities and Collateral Equipment. [15] Aditya Parida and Uday Kumar, APPLICATIONS AND CASE STUDIES Maintenance performance measurement (MPM): issues and challenges, Journal of Quality in Maintenance Engineering Vol. 12 No. 3, 2006 [16] Javad Barabady (2005). Improvement of System Availability Using Reliability and Maintainability Analysis. LuleÃ¥ University of Technology Division of Operation and Maintenance Engineering. 2005:92. [17] Richard Cassady, C., Pohl, E.A. (2004), Managing availability improvement efforts with importance measures and optimization, IMA Journal of Management Mathemat- ics, Vol. 15, No. 2, p. 161- 174 [18] Laura Swanson (2001), Linking maintenance strategies to performance. Int. J. Production Economics 70 (2001) 237}244. Department of Management, Southern Illinois University Edwardsville, Edwardsville, IL 62026-1100, USA. [19] Daniel Wong, B.Eng., M.B.A, 2000, A knwoledge-Based Decision Support System in Reliability-Centered Maintenance of HVAC System. Faculty of Engineering And AppliedScience, Memorial University of Newfoundland.