
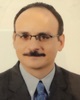
- Open Access
- Authors : Hesham A. Hegazi , Ahmed H. Mokhtar
- Paper ID : IJERTV9IS060813
- Volume & Issue : Volume 09, Issue 06 (June 2020)
- Published (First Online): 01-07-2020
- ISSN (Online) : 2278-0181
- Publisher Name : IJERT
- License:
This work is licensed under a Creative Commons Attribution 4.0 International License
Optimum Design of Hexagonal Cellular Structures Under Thermal and Mechanical Loads
Hesham A. Hegazi1, Ahmed H. Mokhtar2
1 Professor, Mechanical Design & Production Dept., Faculty of Engineering, Cairo University.
2 Associate Lecturer, Mechanical Design & Production Dept., Faculty of Engineering, Cairo University.
Cairo 12316, EGYPT.
AbstractThe concept of cellular materials is available long time ago in nature, examples of these cellular materials are, bones, wood, glass sponges, plant stems, and bird beaks. There must be good reasons for it. Researchers showed a great interest in a new class of materials with optimized properties. Two contradicting objectives are considered. A better mechanical, physical, thermal, and acoustic properties are required, as well as, low density. Sandwich structures deliver this combination of properties. They are light weight and compact structures that could be used in various applications.
In this paper, the concept of sandwich structures was investigated. They are consisted of a core sandwiched between two substrates. This compact combination can achieve lightness with relatively high rigidity and stiffness. Such structures could be metallic or composite. Sandwich structures are divided into three main groups; Metal foams, periodic cellular metals and lattice structures. The difference between each type is the core formation and orientation.
A hexagonal honeycomb cellular structure was studied as a compact heat exchanger that loaded with both thermal and mechanical loads. First, a comparison was carried out between different structure materials and cooling fluids. Then, optimum design curves were constructed to help for selecting the optimum cell size, cell thickness and structure height that maximize thermal and mechanical performances.
Keywords Optimization; cellular materials; sandwich panel structures; cross flow heat exchange; light metal.
-
INTRODUCTION
Nature Introduced cellular materials like bones, horns, wood, coral and bird peaks when it needs very light structures but can withstand the external forces applied. Cellular metals are a mimic for those natural materials. Intermittent cell metals are permeable structures with 20% or less of their inside volume involved by metals. A few, for example, hexagonal honeycomb, are generally used to empower the plan of a light sandwich panel structures, for making unidirectional liquid streams, for engrossing the vitality of effects. Layered metals are additionally a type of intermittent cell metal structure. They have their voids organized one-way empowering liquid stream one way yet not different headings. They are broadly utilized in structures and in transport development and for cross stream heat exchangers. Recently, critical intrigue has risen in cross section structures which have three-dimensional interconnected void spaces appropriate for permitting liquid course through them. The structures of which it is required to optimized is composed of similar unit cells with dimensions ranging from tens of micrometers to tens of millimeters [1].
The main concern of this paper is metallic sandwich structures especially with the corrugated hexagonal cores. They show promising performance as multifunction applications. When compared to regular solid sheet metal with same weight and material, corrugated sandwich structures performed better under controlled blast [2]. In this thesis, a further investigation of open celled corrugated structures was made to highlight their performance as compact heat exchangers. As they allow a continuous flow of fluid, corrugated structures are ideal when a rigid yet light heat exchanger needed.
For determining the optimum dimensions for a corrugated sandwich structure, an optimization procedure done using MATLAB toolbox on a model developed by Gu et al. [3]. The objective was maximizing both mechanical and thermal performance while maintaining the minimum weight. The design attributes were; structure height ), cell length ) and sheet thickness ) of which the structure made of. The structure material is also very important as well as cooling fluid. So, a study was made to show the effect of changing structure material and cooling fluid. Then design curves were introduced to help in selecting corrugated structure variables.
The least difficult kind of sandwich comprises of two slim, solid, solid sheets of thick material isolated by a thick layer of low-thickness material which might be substantially less hardened and solid. This will ensure that the bending stiffness of this sandwich is very much greater than that of a single solid plate of the same total weight made of the same material. The core must be stiff enough in the direction perpendicular to the faces. This will guarantee that they remain the correct distance apart and stiff enough in shear to ensure that when the panel is subjected to bending moment, the faces do not slide over each other.
It fills in as both an essential and optional load carrying element. Adding to this, it is fit for transmitting incredibly high loads when appropriately appended to the structure.
Sandwich panels have lots of applications in industry. A large list of components is used in different industries, this including but not limited to aircraft industry, aerospace industry, construction industry, and architectural projects [7]. Fig. 1, shows how honeycomb structure can improve the relative stiffness, relive strength, without sacrificing the relative weight.
Fig. 1. A striking example of how honeycomb stiffens a structure without materially increasing its weight. [4]
-
THEORETICAL BACKGROUD
-
Relative Density
The properties of a honeycomb or foam depend, above all, on its relative density ). Relative density is the ratio between array density ) to solid density ( ). The fraction of porous space in the structure is simple ( ). Every
structure has its specific relative density depending on cell type, orientation (Fig. 2) and cell dimensions. Generally speaking, cellular solids have relative density less than 0.3 and it is given as [19]:
(1)
where [19] for triangular, square and hexagonal cells, respectively.
Fig. 2. Examples of cell orientation. [19]
-
Heat Transfer Coefficient
The heat transfer coefficient in thermodynamics can be calculated as the proportionality between the heat flux and the thermodynamic driving force for the flow of heat (i.e., the temperature difference, T)
(2)
where is the total heat dissipated per unit area )
Thermal performance is described numerically by an effective heat transfer coefficient. The goal is to develop a cellular system with large that also has allowable pressure drops and occupies a small volume (compact). For heat exchangers, the overall heat transfer coefficient ) is given by [3]:
(3)
: The total heat dissipated from the sandwich structure ( )
: Structure Length
: Structure Width
: Logarithmic mean temperature difference
(4)
(5)
(6)
(7)
(8)
(9)
(10)
(11)
-
Pressure Drop
(12)
(12)
The pressure drop is irectly proportional to the heat transfer coefficient increases. In case of laminar flow, the pressure drop across the cellular array derived from the Hagen-Poiseuille solution of the momentum equation is given by the free stream velocity and the cell morphology by [14]:
Where, the frictional coefficient is, = 14.17; 13.3;
15.07 for square, triangular and hexagonal cells, respectively [3]. While the effect of cell shape on is small, the pressure drop is significantly affected by shape because ).
-
In-plane Shear Modulus
Fig. 3 shows a hexagonal honeycomb, by far the commonest kind. The in-plane stiffnesses and strengths (that is, those in the plane) are the lowest because stresses in this plane make the cell walls bend. The out-of-plane stiffnesses and strengths (those in the direction) are much larger because they require the axial extension or compression of the cell walls.
The direction of loading in honeycomb structures will affect its mechanical properties. The relative density and cell geometry are the main factors affecting the in-plane properties. (Fig. 4) shows the bending deformation will occur if a cell is compressed in-plane. This will cause a linear elastic type of deformation. Due to this, a reduced in-plane stiffnesses and strength are likely to occur.
Fig. 3. A honeycomb with hexagonal cells. [19]
Fig. 4. Hexagonal cell (a) undeformed, (b) upon in-plane compression initially deforms by bending. [19]
-
-
DESIGN OPTIMIZATION
-
Problem Definition
The intent of this paper is to provide to the designers of products using cellular materials a study and optimization of the cooling process and the structural load capacity (rigidity) of a two-dimensional hexagonal cellular structure (Fig. 5), with unit cell as shown in (Fig. 6). Afterwards, the
performance of the model will be analyzed for various materials and cooling fluids.
Fig. 5. A design of compact heat sink with two-dimensional metal hexagonal honeycombs for cooling by forced convection. [3]
Following [3], They have introduced a dimensionless Thermo-mechanical index (equation 13). the ratio of total heat transfer rate to the pumping power needed to force the fluid through ), will affect the heat transfer performance of a heat sink. The higher this ratio, the better the heat sink performance. This ratio is then multiplied by the in-plane shear stiffness ) as it is used for a n indicative measure of the structural utility.
Fig. 6. A unit cell of the structure
The objective function is defined by these two steps. First: to predict and compare the thermo-mechanical performance of hexagonal cellular structure with three different materials (Aluminum, Copper and Iron) and three different cooling fluids (Air, Water and Freon). Second: to maximize heat dissipation ) and Shear Stiffness (G) at specified pressure drop (p) for Hexagonal honeycomb.
(13)
The in-plane shear modulus for the case of hexagonal honeycomb is given by:
(14)
By substituting by (equations 11, 12) and from (Equation 14) we get:
(15)
The main variables in this index are cell size ), sheet thickness ) and structure height ). Then, the objective is to find these variables that maximize thermo-mechanical performance.
-
Cell Topology
There are three basic distinctive features that differ between periodic corrugated sandwich structures. The first and most visual feature is cell type. Corrugated structures could be hexagonal, square, triangular cells. The second feature is stacking order. For example, structures with triangular or square cells (Fig. 7) are different in performance due to different connectivity points. Stacking order mainly depends on fabrication method. The third feature is porosity. Its defined as the ratio of void volume to total volume of the cellular material.
Fig. 7. Different stacking orders for 2D cellular solids having: (a)(c) rectangular cells; (d)(f) equilaterally triangular cells. [20]
The difference in cell topology would affect structures mechanical and thermal performances while maintaining every other aspect constant. For instance, if mechanical tests were made on two corrugated sandwich structures with same material, cell size, sheet thickness, structure height, width
and length but different cell topology, the results would be significantly different. Such difference is due to cellular materials are load bearing so that shear modulus ) is of interest. Porosity also is an important aspect when utilizing
sandwich structures as compact heat sinks.
To find the optimal cell topology that maximizes both thermal and mechanical performance equation (13) was used [3]. Fig. 8 and 9 show Thermal performance index and thermo-mechanical performance index ) vs. structure thickness ) for hexagonal, triangular (four and six connectivity) and square (three and four connectivity) cells at optimum relative density ) with =1 mm, =100,
=200 W/m K and =0.026 W/m K. The implication of Figure 18 is that for designing thin cores ), panels with triangular cells (with six-point crossing point) outflank every single other structure, as a result of their modified load- bearing attributes. The situation changes for thicker structures ), the hexagonal cells outflank all others in view of their superior thermal performance. It is very clear from Fig. 8, that the hexagonal honeycomb has the highest thermal performance index with respect to the relative density, compared to other different structures. In Fig. 9 it is shown that the hexagonal structure has a superior thermo- mechanical performance index with respect to relative thickness over other structures. So that hexagonal structures were selected to be used in this research due to its superior performance over other structures available.
Fig. 8. Thermal performance index I1 plotted as a function of relative density for triangular, square and hexagonal structures. [3]
Fig. 9. Thermomechanical performance index plotted as a function of core thickness [3]
-
Optimization Tool
The method used to find the optimum of equation 4.2 is fmincon Interior-Point Algorithm from MATLAB optimization toolbox. The problem is defined as a single objective, constrained problem. A deterministic optimization method is used for finding the optimum dimensions.
The Interior-Point algorithm applied in case of constrained minimization problem is used to solve a sequence of approximate minimization problems. The original problem is
(16)
For each > 0, the approximate problem is
(17)
subject to ,
In order to solve the given optimization problem, the used algorithm performs one of two main types of steps at each iteration [22]:
-
A direct step in (x, s). This step attempts to solve the Karush-Kuhn-Tucker (KKT) equations for the optimization problem via a linear approximation. This is also called a Newton step.
-
A CG (conjugate gradient) step, using a trust region.
-
By default, the algorithm first attempts to take a direct step. If it cannot, it attempts a CG step. One case where it does not take a direct step is when the approximate problem is not locally convex near the current iteration.
-
-
RESULT AND DISCUSSION Comparison bar charts were developed to show the
difference in performance of three different hexagonal cellular structures. These three structures are made from Aluminum, Copper and Iron. They differ in thermal
conductivity and density ). The idea is to show which structure has the best structural rigidity and heat dissipation while maintaining the minimum weight. As the cooling fluid is also very important in heat dissipation, three different fluids were used; Air, Water and Freon. The difference in the thermal conductivity f each fluid ) will highlight the best fluid to use with each structure material.
Fig. 10 shows that when using air as cooling fluid, the optimum number of rows (H/a) will be maximum for any material relative to Freon and water. The optimum number of rows for aluminum sandwich structure is almost 50 and 25 percent lower when using water and freon respectively relative to air as a cooling fluid. Optimum thermal performance (Fig. 10) varied dramatically with changing cooling fluids as expected. Water + Iron were the winning selection as they outperformed by far all other cooling fluids and materials even with water. Air is not recommended as a cooling fluid.
Fig. 11 shows that sandwich structures should be made with aluminum when minimum weight is needed. Using water with aluminum structure would reduce total weight by 20 and 40 percent compared to freon and air respectively. In case of copper structure, water reduces structure weight by almost 30% compared to both air and freon. And in case of iron structure, water would reduce weight by 40 and 50 percent for freon and air respectively.
Fig. 10. of Air, Water and Freon vs. Optimum structure number of rows (H/a) for every structure material.
Fig. 11. Cooling fluids (Air, Water and Freon) vs. Optimum Thermal performance for every structure material.
Fig. 12. Kf vs Optimum (H/a)
Fig. 13. Cooling fluids (Air, Water and Freon) vs. Optimum Weight for every structure material.
The purpose of this section is to introduce design charts that help optimizing hexagonal structures. These charts can improve selection of hexagonal structure main dimensions. Based on cell size , a designer can select optimum wall thickness and structure height . Hence, he would be able to maximize both mechanical and thermal performances of the structure. The optimization is done using interior point algorithm in MATLAB toolbox.
To expand the range of selection, three materials were investigated; Aluminum ( ), Copper
() and Iron ( ). Since not only air is used as a cooling fluid, three different fluids are studied to cover many applications. The investigated fluids are: Air , Water
and Freon . These varieties give the
designer 9 possible combinations to choose from. The selection process should be now easier and quicker than before.
-
Aluminum
Fig. 14 shows the variation of the optimum sheet thickness that maximizes the thermal performance, for the three cooling fluids. Fig. 15 shows the variation of the optimum sheet thickness that maximizes thermo-mechanical performance, for the three cooling fluids. Fig. 16 shows the variation of the optimum structure hight with relative to the cell length for the three cooling fluids that maximize the thermal and thermo- mechanical performance.
Fig. 14. Cell length ) vs. Optimum sheet thickness ) that maximizes Thermal performance for every cooling fluid.
Fig. 15. Cell length ( ) vs. Optimum sheet thickness ( ) that maximizes Thermo-mechanical (TM) performance for every cooling fluid.
Fig. 16. Cell length ( ) vs. Optimum Structure height (Hopt) that maximizes Thermal performance and Thermo-mechanical (TM) for every cooling fluid.
Fig. 17 shows the variation of the optimum cell thickness with relative to the cell length for copper, for the three cooling fluids that maximize the thermal performance. Fig. 18 shows the variation of the optimum cell thickness with relative to the cell length for copper also, for the three cooling fluids that maximize the thermo-mechanical performance. In case of Iron, the variation in shown in Fig. 19 and Fig. 20. A comparison of the optimum performance for the three materials is shown in Fig. 21, 22, 23, and 24.
-
Copper
Fig. 17. Cell length ( ) vs. Optimum sheet thickness ( ) that maximizes Thermal performance for every cooling fluid.
Fig. 18. Cell length ) vs. Optimum sheet thickness ) that maximizes Thermo-mechanical (TM) performance for every cooling fluid.
-
Iron
Fig. 19 Cell length ( ) vs. Optimum sheet thickness ( ) that maximizes Thermal performance for every cooling fluid.
Fig. 20. Cell length ( ) vs. Optimum sheet thickness ( ) that maximizes Thermo-mechanical (TM) performance for every cooling fluid.
Fig. 21. kf vs optimum performance
Fig. 22. ks vs optimum performance
Fig. 23. kf vs optimum weight
Fig. 24. ks vs optimum weight
-
-
CONCLUSION
The aim of this paper was to highlight the importance of sandwich structures and to study the corrugated ones even further. The main parameters that characterize corrugated structures are; structure height ( ), cell length ( ) and sheet
thickness ) of which the structure made of. These parameters control not only structure stiffness and center deflection under mechanical loads, but also how the structure exchange heat loads with the cooling fluid by forced convection. So the objective is to know the values of , and ) that maximize stiffness and heat exchange while minimizing weight.
First, a study was made on hexagonal corrugated structure to show the effect of altering cooling fluid and structure material. A model was used from [4] as an objective function. An optimization procedure was made using MATLAB toolbox. Obviously, Aluminum did great when weight or structure height is important. On the other hand, iron was better than aluminum and copper in thermal performance. Significantly, Water was the perfect cooling fluid for optimum thermal performance and structure height ). There was almost no difference between cooling fluids and optimum weight. The second section was about design curves. These curves enabled the designer to select optimum thickness ) and structure height ) for every cell length ) and for every material (Aluminum, Copper and Iron) and cooling fluids also (Water, Air and Freon).
REFERENCES
-
H. N. G. Wadley, Multifunctional periodic cellular metals., Philos. Trans. A. Math. Phys. Eng. Sci., vol. 364, no. 1838, pp. 3168, 2006.
-
A. G. Evans, J. W. Hutchinson, and M. F. Ashby, Multifunctionality of cellular metal systems, Prog. Mater. Sci., vol. 43, no. 3, pp. 171 221, 1998.
-
S. Gu, T. J. Lu, and a. G. Evans, On the design of two-dimensional cellular metals for combined heat dissipation and structural load capacity, Int. J. Heat Mass Transf., vol. 44, no. 11, pp. 21632175, 2001.
-
Hexcel Composites, Honeycomb Attributes and Properties, pp. 140, 2000.
-
H. N. G. Wadley and D. T. Queheillalt, Thermal Applications of Cellular Lattice Structures, Mater. Sci. Forum, vol. 539543, pp. 242 247, 2007.
-
T. Liu, Z. C. Deng, and T. J. Lu, Bi-functional optimization of actively cooled, pressurized hollow sandwich cylinders with prismatic cores, J. Mech. Phys. Solids, vol. 55, no. 12, pp. 25652602, 2007.
-
S. Milton and S.M. Grove, Composite Sandwich Panel Manufacturing Concepts for a Lightweight Vehicle Chassis, Proc. Of the 30th Inter. Symp. Of Automotive Tech. and Automation, ISATA, Florence, June 1997.
-
C. L. Yeh, Y. F. Chen, C. Y. Wen, and K. T. Li, Measurement of thermal contact resistance of aluminum honeycombs, vol. 27, pp. 271 281, 2003.
-
J. Tian, T. J. Lu, and H. P. Hodson, Thermal Hydraulic Performance of Sandwich Structures With Crossed Tube Truss Core and Embedded Heat Pipes, 13th International Heat Pipe Cont., Shanghai, Chaina, 2004.
-
N. A. Fleck and V. S. Deshpande, The Resistance of Clamped Sandwich Beams to Shock Loading, vol. 71, no. May, 2004.
-
B. A. Gama, T. A. Bogetti, B. K. Fink, C. J. Yu, T. Dennis Claar, H. H. Eifert, and J. W. Gillespie, Aluminum foam integral armor: A new dimension in armor design, Compos. Struct., vol. 52, no. 34, pp. 381395, 2001.
-
W. Goldsmith and D. L. Louie, Axial perforation of aluminum honeycombs by projectiles, Int. J. Solids Struct., vol. 32, no. 89, pp. 10171046, 1995.
-
C. J Yungwirth, H. N. G. Wadley, J. H. OConnor, A. J. Zakraysek, and V. S. Deshpande, Impact response of sandwich plates with a pyramidal lattice core, Int. J. Impact Eng., vol. 35, no. 8, pp. 920936, 2008.
-
M. F. Ashby, A. Evans, N. a Fleck, L. J. Gibson, J. W. Hutchinson, and
H. N. . Wadley, Metal foams: a design guide, Mater. Des., vol. 23, no. 1, p. 119, 2002.
-
S. S. RAO, Engineering Optimization, Theory and Practice, Third Edition.
-
Hegazi, H.A., Nassef, A.O., Metwalli, S.M., Shape Optimization of NURBS Modeled 3D C-Frames Using Hybrid Genetic Algorithm, 2002 ASME Des. Aut. Conf., Paper Number DETC2002/DAC-34107, Montreal, Canada, 2002.
-
E. Sandgren, E. Jensen, and J. W. Welton, Topological design of structural components using genetic optimization methods, vol. 115. pp. 3143, 1990.
-
S. M. Metwalli and H. A. Hegazi, Computer-based design of disc brakes by multi-objective form optimization, ASME Design Engg. Tech. Conf., Paper No. DETC2001/CIE-21680, Sept., 9-12, Pittsburgh, Pennsylvania,USA, 2001.
-
L. Gibson and M. Ashby, Cellular solids Structures and properties Second edition, Cambridge University Press. 1997.
-
T. Wen, F. Xu, and T. J. Lu, Structural optimization of two- dimensional cellular metals cooled by forced convection, Int. J. Heat Mass Transf., vol. 50, no. 1314, pp. 25902604, 2007.
-
R. H. Byrd, J. C. Gilbert, and J. Nocedal, A trust region method based on interior point techniques for nonlinear programming, Math. Program., vol. 89, no. 1, p. 149, 2000.
-
A. H. Mokhtar, Optimum Design of Hexagonal Cellular Structure Under Thermal and Mechanical Loads, MSc Thesis, Cairo University, Cairo, 2016.
NOMENCLARURE
Biot number
proportional factor for surface area density proportional factor for pressure drop proportional factor for solid wall length
proportional factor for total number of slices over width W
specific heat
proportional factor for cell wall thickness proportional factor for cell wall ends hydraulic diameter
Young's modulus
in-plane shear modulus
h local heat transfer coefficient
h- overall heat transfer coefficient H heat sink height
thermal conductivity thermal performance
thermomechanical performance index cell wall length
heat sink length
L* the characteristic length mass flow rate
heat sink weight
proportional factor for fin attachments total number of slices over width W
Nu Nusselt number pressure drop
Prandtl number heat flux
total heat transfer rate Reynolds number cell wall thickness temperature
logarithmic mean temperature difference velocity
heat sink width shear viscosity kinematic viscosity relative density shear stress
density Subscripts
exit of heat sink fluid
solid substrate
inlet of heat sink