
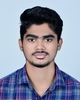
- Open Access
- Authors : Rashad Bin Aboobacker K. E , Dr. Rakesh K. N
- Paper ID : IJERTV11IS070258
- Volume & Issue : Volume 11, Issue 07 (July 2022)
- Published (First Online): 06-08-2022
- ISSN (Online) : 2278-0181
- Publisher Name : IJERT
- License:
This work is licensed under a Creative Commons Attribution 4.0 International License
Numerical Analysis of Hybrid Sinusoidal Corrugated Steel Beam
Rashad Bin Aboobacker K.E Post Graduate Student, Department of Civil Engineering
Government College of Engineering Kannur, Kerala, India
Dr. Rakesh K.N
Professor, Department of Civil Engineering
Government College of Engineering Kannur, Kerala, India
AbstractThe Corrugated web steel beams (CWSBs) have great engineering applications and advantages due to their excellent strength, reduced weight and aesthetic appearances. This work studies different parameters on the sinusoidal corrugated plate girder. Finite element analysis software ABAQUS® CAE was used to conduct the numerical investigations. An existing experimental study on sinusoidal corrugated plate girders was used for conducting numerical models. The numerical models generated were validated against the results obtained experimentally. Following satisfactory validation, extensive parametric investigations were carried out. The parametric studies were carried out on the effect of using different grades of steel in plates and the effect of web slenderness ratio. Hybrid steel beams have different steel grades for flange and web. Changing the steel grades used in flange and web, the hybrid effect on sinusoidal corrugated plate girder was investigated. Using high-strength steel in the flange and low- strength steel in the web shows improvements in stiffness and plasticity than plate girders with high-strength steel in the web and low-strength steel in the flange. The variation in the ultimate strength of different sets on hybrid steel plate girders was investigated. The slenderness effect on hybrid girder was evaluated. The web slenderness ratio effects on ultimate load- carrying capacity with different ratios with varying web thickness were evaluated.
Keywords Sinusoidal Corrugation; Plate Girder; Hybrid; sinusoidal; Numerical; ABAQUS
-
INTRODUCTION
The plate girder is a built-up beam with plates in the web and flange. These were designed to bear immense loads over long spans. James Mill Holland constructed the first plate girder bridge for the Baltimore and Ohio Railroad in 1846-47, made from tubular wrought iron. Plate girders gained popularity in the late nineteen century when they were used to build railroad bridges. The common types of plate girders include riveted plate girders, bolted plate girders and welded plate girders. Welded plate girders had supplanted riveted and bolted plate girders by the 1950s due to their superior quality, aesthetic appearances, and reduced construction cost. A plate girder fails mainly by web buckling, flange buckling, or fatigue failure. The main components of a plate girder include flange, web plate, stiffeners (vertical, horizontal, inclined), flange and web splices and end connections. Due to the advantage of large loads for longer spans, these are often used in ships, oil and platforms, cranes, elevators, and gantry beams.
A corrugated web plate girders are plate girders with corrugated web instead of flat web. Due to the corrugated web, beams have more shear stability than ordinary flat web beams,
so the stiffeners and thicker web plates required can be reduced. These structures have a unique design in which the corrugated steel in the web is optimised to achieve maximum stability and load-carrying capacity. The corrugations in the web prevent the beam from failure due to loss of stability before the web yields. The corrugated web in girder has more material than the girder of the same size with a flat web. Compared to hot-rolled beams, corrugated web beams offer a substantial weight reduction due to the thin web. The corrugated web beams are a novel constructional system that has arisen in many structural designs. It provides an intelligent approach to minimising the requirement of web stiffeners for post-loading performance issues linked with ordinary flat webs were studied in the works of Abbas et al. [1]. Because of the corrugated web profile, this type of structural element can withstand large loads before buckling, making researchers more interested in corrugated- web beams and designers. The corrugation geometries of rectangular, trapezoidal, triangular, and sinusoidal are possible.
Furthermore, the shape of the corrugation, such as trapezoidal or sinusoidal forms, has been shown to boost the capacities of steel beams with corrugation under flexural and shear stresses were studied in the works of Elchalakani et al. [2]. However, in recent years, the corrugation of the trapezoidal and sinusoidal has become a more and more popular choice of corrugations among structural designers. The corrugated steel web in bridges results in lower seismic stresses and lighter substructures, leading to a cost-effective and easy construction. According to Ashrawi et al. [3], the corrugated web beams have been used as principal bearing components in large steel structures and girders in highway or railway bridges since they do not require web stiffeners and have lighter beam characteristics. Even with the lesser need for stiffeners, the corrugated steel web has better out-of-plane stiffness and shear buckling resistance than the flat steel web, which helps in saving the material and labour costs for fabrication significantly. The performance of corrugated-web girders was proven to be improved from that of ordinary beams, with CWBs having enhanced stability against shear buckling, less weight, and longer service life Inaam et al. [4]. According to Zhang et al. [5], the corrugation profile in corrugated-web beams can significantly reduce the steel used in bridge girders. According to Haydar et al. [6], even though corrugated-web beams were widely used in many design areas, critical features such as post- buckling strength, defections, and shear capacities must be studied. Nikoomanesh et al. [7] studied the inelastic shear buckling capacity of the sinusoidal corrugated web (SCW) girders numerically and experimentally. Formulas were
proposed to determine the inelastic capacity of the SCWs and to determine nonlinear buckling capacities. The effect of patch load and eccentric patch load on trapezoidal corrugated web beams was studied by Inaam et al. [5].
A hybrid plate girder has steels of different grades on the web and flanges. This type of structure is used extensively in construction and fabrication nowadays. Since the 1960s, hybrid steel girders have been used throughout North America. Since the web of a plate girder contributes little to the bending strength of the girder, the web shear strength depends on the depth/thickness ratio. Therefore, in hybrid plate girders, high strength steel (HSS) was used in the flange and low strength steel (LSS) in the web, making the web thick and more stable and economical.
In the present study, the ultimate load capacities of hybrid sinusoidal corrugated web beams are numerically evaluated. At first sinusoidal corrugated web beams with homogenous material were modelled and validated against the experimental model of Gorecki et al. [8]. After validation, the effect of the hybrid girder was studied by changing the material properties in the web and flange. In addition, the effect of web slenderness ratio on hybrid corrugated web beam was also studied.
-
NUMERICAL EVALUATION
The numerical analysis is done using finite element analysis software ABAQUS® CAE. The linear analysis was done using eigenvalue buckling analysis, and the nonlinear analysis was done using the Static Riks method. Finally, the modelling was done according to the experiment conducted by Gorecki et al. [8].
-
Description of Experiment
p>The four-point bending test was conducted by Gorecki et al. [1]. The loading was done in load-unload cycles. Each cycle, the force increased by 50 kN till failure. Fig.1 shows the schematic loading diagram used for modelling. One end of the girder was hinge supported, and the other end roller supported
55 mm peak to peak (a). The span was 2500 mm with the 8 mm
and 180 mm flange thickness () and width () respectively.
All the components of the beams have the same material
property. The material properties determined from the tensile coupon test are shown in Table 2. A bilinear isotropic hardening model was used to define the stress-strain characteristics, as shown in Fig. 2.
Table 1 Model geometry of BS200/3
Web height, (mm)
250
Flange width, (mm)
180
Flange thickness, (mm)
8
Web thickness, (mm)
3
Stiffener thickness, (mm)
5
Peak to Peak, a (mm)
55
Wave period, w (mm)
200
Span (mm)
2500
Table 2 Model geometry
Yield Stress (MPa)
Ultimate Stress (MPa)
Youngs Modulus (GPa)
Poisons Ratio
415
660
197820
0.29
700
600
Stress (MPa)
500
400
with the load was applied 636 mm from either end and loading
distance of 1228 mm. The vertical displacement was measured
200
in the middle of the girder using LVDT, and inclinometers were used to calculate the lateral deflections and rotations.
100
300
Loading
Fig. 1. Schematic loading diagram
-
Material and Geometrical Modelling
The plate girders with corrugation of sinusoidal geometry web were tested. The model dimensions are given in Table 1, conducted by Gorecki et al. [8]. The corrugated web thickness
() of 3 mm with height of 250 mm. the sinusoidal
corrugation has the geometry of 200 mm wave period (w) and
0
0 0.05 0.1 0.15
Strain
Fig. 2. Bilinear stress-strain curve
-
Meshing
A 4-noded S4R shell element was used for modelling. Geometric imperfections are taken into consideration while modelling. A mesh convergence study was conducted, and a mesh size of 15 mm was considered for meshing. The mesh convergence study conducted are shown in Fig. 3, and the meshed model is shown in Fig. 4.
418
413
Load (kN)
408
403
398
393
388
7000 17000 27000 37000 47000
Number of elements Fig. 3. Mesh convergence
450
400
350
300
Load (kN)
250
200
150
100
50
0
FEM
Test
0 5 10 15 20
Deflection (mm)
Fig. 5. Load-deflection curve of BS200/3
-
-
PARAMETRIC STUDY
Figure 4. Meshed model in ABAQUS® CAE
-
Boundary Condition and Buckling Analysis
The beam is horizontally placed at one end with hinged support, and other end roller support was provided. The boundary condition adopted are shown in Table 3, where the U1, U2, and U3 are the displacements along the x, y, and z directions, and UR1, UR2, and UR3 are the corresponding rotations about x, y, and z directions. In Table 3, the 1 implies movements are fixed, and 0 implies free movement.
For the linear analysis, the eigenvalue buckling analysis was performed where a unit load was applied to obtained buckling modes, and buckling modes were taken as output for imperfections applied for nonlinear buckling analysis. For the nonlinear analysis, the Static-Riks method was performed. The load-controlled analysis was carried out, and the peak load was compared with Gorecki et al. [8]. The numerical results were validated against the experimental results. Fig. 5 compared the numerical and experimental load versus displacement, showing considerable agreement.
Support
U1
U2
U3
UR1
UR2
UR3
A
1
1
1
0
1
1
B
0
1
1
0
1
1
Table 3. Boundary conditions
Detailed parametric studies were conducted on the validated numerical model. The studies on the effect of varying the grade of steel in flange and web, the effect of web slenderness ratio and the effect of vertical stiffeners. For studying the effect of the hybrid girder, the six cases of varying the steel grade combinations used in flange and web are considered. In addition, the effect of web slenderness is studied by varying the web thickness, and web height and the effect of stiffeners are studied by changing the positions of vertical stiffeners.
-
Effect of changing the steel grade
The varying steel grade used in the web and flange and the effect on the ultimate load capacity of the beam were studied. Six cases were considered for the study, by changing the steel grade in flange and web to study the effect of changing steel yield strength. For three cases, HSS was used in the flange and LSS in the web; for the other three cases, LSS was used in the flange and LSS in the web. Using HSS in flange and LSS in web improves the load capacity of the beam [9]. The combinations used for studying the hybrid girder are shown in Table 4.
Table.5 shows the ultimate load and corresponding percentage variations for the different flange to web yield
strength ratios (/). The load-deflection curve of different
cases are shown in Fig. 6. Using HSS in flange and LSS in the
web of beam shows improvements in load carrying capacity. Using this combination, the ultimate load increased from 250 kN to 380kN, a 52% increase ultimate load. Using the LSS in flange and LSS in the web also shows improvements in the ultimate load capacity. The ultimate load increased from 269 kN to 394 kN, a 45% increase in ultimate load by using this combination. It was seen that the cases of 1,2,3 where the HSS was used in the flange and LSS were used in the web show no sudden drop after the ultimate load. Instead, the curve follows a plastic nature and has more deflection.
Table 4 Models used for hybrid analysis
Case No.
The steel used in
flange ()
The steel used in
web ()
1
S355
S275
2
S460
S275
3
S690
S275
4
S275
S355
5
S275
S460
6
S275
S690
in load was only 4%, and for 150 to 200 for the 5 mm web, it was only 18%.
700
600
500
Slenderness = 83
Slenderness = 167
Slenderness = 250
Slenderness = 333
Table 5. Comparison of ultimate load against various yield ratios
Load (kN)
400
300
200
100
0
0 5 10 15 20
Deflection (mm)
/
Ultimate load (kN)
Percentage variation (%)
2.5
380
52
1.8
305
22
1.3
250
–
0.8
269
–
0.6
332
23
0.4
394
45
Figure 7 Load-deflection curve for slenderness ratios of = 3 mm
450
400
350
300
Load (kN)
250
200
150
100
50
case 1
case 2
case 3
case 4
case 5
900
800
700
600
Load (kN)
500
400
300
200
100
0
Slenderness = 200
Slenderness = 150
Slenderness = 100
Slenderness = 50
0 10 20 30
Deflection (mm)
case 6
0
0 5 10 15 20 25 30
Deflection (mm)
Fig. 6. Load-deflection curve of different cases
-
Effect of web slenderness ratio
Web slenderness ratio is the ratio of web height to web thickness. The web heights of 250 mm, 500 mm, 750 mm and 1000 mm and the web thickness of 3 mm and 5 mm were considered with HSS in flange and LSS in the web. The slenderness ratios of 50, 100, 150, and 200 were considered. For the 5 mm thick web and the 3 mm thick web, the slenderness ratio of 83, 167, 250 and 333 was considered. Deflection at the middle of the beam was taken for the study.
From Fig. 7 and Fig. 8, for each web thickness of 3 mm and 5 mm, the ultimate load-carrying capacity increases with an increase in the slenderness ratio. Tables 6 and 7 show the percentage variation in peak load for different web slenderness ratios. For the 3 mm web thickness, as the slenderness ratio increased by 164%, the ultimate load increase occurred, and for the 5 mm web thickness 210% increase occurred. For higher slenderness ratios, the plastic region is lesser compared with lower slenderness ratios. The increase in ultimate decreases for higher slenderness ratios. When the slenderness ratio value changed from 250 to 333, the percentage variation
Figure 8 Load-deflection curve for slenderness ratios of = 5 mm
Table 6 Comparison of ultimate load against various
Slenderness ratio
Ultimate Load (kN)
Percentage Variation (%)
83
250
–
167
507
103
250
633
153
333
659
164
slenderness ratios of = 3 mm
Table 7 Comparison of ultimate load against various
Slenderness ratio
Ultimate load (kN)
Percentage variation (%)
50
255
–
100
683
167
150
744
192
200
791
210
slenderness ratios of = 3 mm
-
-
CONCLUSION
The behaviour of hybrid sinusoidal corrugated steel girder was studied. A four-point bending configuration is adopted for analysis of the behaviour of the girder. The numerical model constructed in ABAQUS® CAE software was validated against the experimental conducted by Gorecki et al. [8]. The validated model was used for the parametric study. The parameters adopted for the parametric study include changing the steel grade in flange and web and the effect of the slenderness ratio.
The conclusions derived from the parametric studies are as follows:
-
The load-carrying capacity improved when the yield strength of the steel used in the web or flange increased
-
Using the HSS in flange and LSS in web improves the load-carrying capacity by improving overall weight reduction and material reduction.
-
Using HSS in the flange and LSS in the web, the ductility was increased, and the plastic deformation capacity was improved.
-
As the web slenderness ratio increased, the ultimate load-carrying capacity increased, but the improvement in load capacity diminished for a higher web slenderness ratio. After a slenderness ratio greater than 333 increasing the web height has a negligible effect on the load-carrying capacity of the girder.
-
When the web slenderness ratio increased, the initial stiffness increased, but the plasticity decreased. Conversely, the elastic-plastic deformation capacity decreases as the web height increases, but the initial stiffness improves.
REFERENCES
[1] Abbas, H. H., Sause, R., Driver, R. G. & Asce, M. The behaviour of corrugated web I-girders under in-plane loads. Journal of Engineering Mechanics, 132(8), 806814J. Clerk Maxwell, A Treatise on Electricity and Magnetism, 3rd ed., vol. 2. Oxford: Clarendon, 1892, pp.68-73, 2006. [2] Elchalakani, M., Elkawas, A. A., & Hassanein, M. F.. Lateral torsional buckling strength and behaviour of high-strength steel corrugated web girders for bridge construction. Thin-Walled Structures, 122, 112123, 2018. [3] Ashrawi, M. A., Sunitha, C. M., & Smitha, K. K. The load-carrying capacity of corrugated web beams. International Research Journal of Engineering and Technology, 03(09), 135138, 2016. [4] Inaam, Q., & Upadhyay, A. The behaviour of corrugated steel I-girder webs subjected to patch loading: Parametric study. Journal of Constructional Steel Research, 165, 884896, 2019. [5] Zhang, B., Yu, J., Chen, W., Wang, W., & Xu, J.. Stress states and shear failure mechanisms of girders with corrugated steel webs. Thin-Walled Structures, 157, 106858, 2020. [6] Haydar, H., Far, H., & Saleh, A.. Portal steel trusses vs portal steel frames for long-span industrial buildings. Steel Construction, 11(3), 205217, 2018. [7] M.R. Nikoomanesh & M.A. Goudarz. Patch loading capacity for sinusoidal corrugated web girders. Thin-Walled Structures 169 108445, 2021. [8] Górecki, M., & ledziewski, K. Influence of corrugated web geometry on mechanical properties of i-beam: Laboratory tests. Materials, 15(1), 277, 2021. [9] Veljkovic, M., & Jojansson B. "Design of hybrid steel girders". Journal of Constructional Steel Research, 60(3-5), 535-547, 2004. [10] ABAQUS® CAE 2017, ABAQUS Inc