
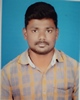
- Open Access
- Authors : Chappa Suresh , Chelapaka Venkata Lakshmi
- Paper ID : IJERTV10IS050158
- Volume & Issue : Volume 10, Issue 05 (May 2021)
- Published (First Online): 22-05-2021
- ISSN (Online) : 2278-0181
- Publisher Name : IJERT
- License:
This work is licensed under a Creative Commons Attribution 4.0 International License
Numerical Analysis of Heat Transfer Enhancement in the Single Pipe Heat Exchanger with Helical Enclosure (He) Under Constant Wall Temperature
¹Chappa Suresh
¹Department of Mechanical Engineering
¹Satya Institute of Technology And Management, JNTUK
Vizianagaram. AP. India
²Chelapaka Venkata Lakshmi
²Department of Mechanical Engineering
²Satya Institute of Technology And Management, JNTUK
Vizianagaram. AP. India
Abstract In this investigation the heat transfer mechanism based on the temperature slope among two dissimilar geometry of helical inserts with both cases of distinct nominal pitch lengths& angels and latitudinal lengths at the condition of constant wall temperature. Enhancement of inter changing of heat between wall to flowing fluid in the SPHE.in most of cases generally heat transfer done between two fluids but here its self-wall surface and fluid interface. The outlet temperature of the fluid drops suddenly when the Reynolds number increases rapidly 6500 with HI-B compared to HI-A. un predictable of first case through length and other case middle portion of inserts prescribed size of pitch length and pitch angle at preeminent temperature. also, the Nusselt number and heat transfer coefficients are significantly changed due to the constant wall temperature condition in the continues heat exchanging mechanism.
Keywords Single pipe heat exchanger (SPHE), Reynolds number (Re), Nusselt number (Nu), heat transfer coefficient (HTC), helical inserts (HI).
NOMENCLATURE
Symbol
C T Ai di L
T
(T-T) (Ti+Te)/2 Re
Pr Nu V
heat transfer coefficient [W/m². ] mass flow rate [kg/sec]
specific heat of water [ J/kg. K]
cold water temperature difference [] inside area of tube [m]
inner diameter of tube [mm] length of the pipe [mm]
wall surface temperature [] average temperature gradient [] Bulk mean temperature [] Reynolds number [-]
Prandtl number [-] Nusselt number velocity of fluid [m/sec]
pitch angle [-]
Symbol
C T Ai di L
T
(T-T) (Ti+Te)/2 Re
Pr Nu V
heat transfer coefficient [W/m². ] mass flow rate [kg/sec]
specific heat of water [ J/kg. K]
cold water temperature difference [] inside area of tube [m]
inner diameter of tube [mm] length of the pipe [mm]
wall surface temperature [] average temperature gradient [] Bulk mean temperature [] Reynolds number [-]
Prandtl number [-] Nusselt number velocity of fluid [m/sec]
pitch angle [-]
-
INTRODUCTION
Significant increase in efficiency of heat exchangers, can be realized with enhancement in heat transfer coefficient of fluid. The augmentation is classified into three main techniques: active, passive, and compound. The active techniques require
an external force such as electric field, acoustic or surface vibration. The passive technique involves fluid additives, special surface geometries, or swirl flow devices, that is, twisted tape inserts. On the other hand, the compound techniques are created by a combination of two or more passive and/or active. Many researchers used the passive device to achieve enhancement in heat transfer by its hassle-free use. Inserts increase residence time and generate swirl effect of fluid flow in the test section of tube causing vortex mixing of fluid particles. An attempt is made in the present study investigate enhancement of heat transfer in a single pipe with helical inserts of different diameter and length in the laminar to turbulent fluid flow region. Detailed experimentation was carried out with single and double strip helical screw tapes in a copper by Shashank Ranjan Chaurasia [3] they conducted that combining the effect of nanofluids and the effect of swirl created by insert would cumulatively augment the heat transfer coefficient. M.R. Salem et al [4] investigated heat transfer enhancement using continues helical tape inserts with varying pitch to diameter ratios and ratio of height to clearance between two pipes. Heat transfer enhancement with inserts was observed to be 70 to 164%when clearance was 0.275 to 1. Nusselt number increases of 1.77 times with helical inserts as compared to plain double pipe heat exchanger was indicated by Khashayar Sharifi [5]. Anas El Maakoul [6] carried out experimentation at varying Reynolds number and baffle plate spacing in a double pipe heat exchanger. Their results showed increased heat transfer from 5 to 45%when baffle spacing is reduced from 100to 25mm.multi objective optimization, NSGA- is utilised by M. Sheikholeslami et [7] for forced convection heat transfer analysis using thermal performance was maximum i.e., 1.59for Re 6000and open air ratio of 0.05. Niwat Piriyarungroj [8] investigated numerically the heat transfer enhancement and friction factor is a tube under constant wall temperature. It was observed that heat transfer and pressure loss increase with open air ratio when inserts one inserted in the fit tube. Sami D. Salman [9] carried out numerical analysis of heat transfer in a circulated tube with twisted tape inserts under constant wall heat flux and laminar flow condition. Their results indicated increased heat transfer with decreases tube ratios and increase of Reynolds number.
M.M.K. Bhuiya [10] in the double helical inserts under
turbulent flow condition at double helix angle of 9º and highest Reynolds number51000, while that condition achieved 215% of increased in thermal performance.
-
MODELLING
A circular pipe of 40mm internal diameter and overall length of 3meters with 2mm wall thickness is consider for heat transfer enhancement using passive devices such as helical inserts in the fluid domain. The Reynolds number of the fluid flowing in the tube is varied from 800 to 5000.the CAD model of the pipe with inserts is imported in to geometry module of Ansys CFX18.1 software. after meshing the required fluid domain with relevant boundary conditions is incorporated in the setup module of the CFX software. The outer wall of the circular pipe is surrounded by hot fluid flowing over the tube as to keep the outside wall temperature constant at 373K. the Reynolds number of the fluid is varying the velocity of the fluid entering the inlet boundary, the pressure outlet boundary condition is zero average state pressure is maintained at the outlet boundary. Two types of helical inserts are used with 14mm & 9mm diameter and lengths of 2900mm and 1600mm respectively. The CAD modelling the pipe along with the helical inserts are given figure1.
Fig:1 Helical enclosure inside pipe
Fig:2 Mesh generation
In this figure 2 the Grid convergence study is carried out by varying the mesh from coarse to fine mesh and the model with one nodes are considered for all the simulations.
-
METHODOLOGY
In the single pipe heat exchanger is numerically investigated with helical tape inserts are placed inside the tube, in the case of HI-A twisted tapes are insert throughout pipe length and another case of HI-B twisted tapes are some extend of muddle of the pipe only placed. So, in this both cases flow should same operationally conditions like (1) flow is incompressible and velocity of the flow is constant for each operating condition in both laminar and turbulent regimes. (2) assumed to flow should be three dimensional steady and uniform throughout the length.
(3) fluid properties are constant and abandoned gravity &viscous forces.
Q= h. A. = h. As.(T-T) (1)
=**/Ai*(T-Te) (2) = i+ e/2 =(Ts-Ti) + (Ts-Te)/2=T-(Ti+Te/2))
=Ts-Tb. (3)
Nu=3.657+0.067*(Re*Pr((di/L) ^1.33))
/(1+0.1*Pr*(Re*di/L))
if Re<2300 for laminar flow condition. (4) Nu=0.023*(Re)^0.8*(Pr)^0.33 if Re>2300 for turbulent flow condition. (5)
-
REESULTS AND DISCUSSIONS
Table:4.1 Numerical information of with HI-A
Velocity m/sec
Reynolds number (Re)
Nu
HTC
W/m². K
0.0025
430
54
8.5
125
0.005
842
43
9.4
139
0.01
1670
38
14
162
0.02
3330
32
19
243
0.03
5000
30
23
307
0.04
6674
28
28
386
Table:4.2 Numerical information of with HI-B
Velocity m/sec
Reynolds number (Re)
Nu
HTC
W/m². K
0.0025
394
45
5.6
65
0.005
782
39
8
91
0.01
1555
33
11
121
0.02
3100
27
15
182
0.03
4658
25
21
242
0.4
6222
23
25
303
Fig.3 Re Versus Te with HI-A
Fig.4 Re Versus Te with HI-B
In this study of figures 3&4, it is observed that the outlet temperature of the fluid leaving the pipe continuously drops at a rapid rate with Reynolds increasing from 500 to 6500, the flow regime being partly laminar up to 2300 and there after entering the transition zone. In case of HI- A, initially the temperature increases by 38K at 500Re with reference to without any insert and thereafter the temperature difference decreases rapidly in the transition zone and eventually becoming almost negligible at Re exceeding 5000.On the other hand with HI-B, the temperature difference is 26K at 500Re and finally it becomes zero at Re3500.it is also seen that at Re exceeding 3500,the temperature with HI-B takes a further difference even below the temperature without HI-B indicating that the convective heat transferred to the fluid is rapidly lost in heating the metallic insert inside the tube which is not seen with HI-A which could be due to stretching of the insert throughout the length causing gradual heating of the metallic insert from inlet end itself.
Fig.5 Re Versus Nu with HI-A
Fig.6 Re Versus Nu with HI-B
Fig:7 Re Versus HTC with HI-A
Referring to figures 5 to 8, it is the seen the heat transfer coefficient as well as Nusselt number rapidly increases with increases in Re for all four cases, is cases with HI-A HI-B & without inserts.
Fig:8 Re Versus HTC with HI-B
However as seen earlier for the temperature alterations, the initial increase of HTC as well as Nusselt number is much smaller for the case with HI-B when compared to HI-A. At 5000 Re, the HTC is seen to be same for both and thereafter dropping below the HTC value without HI-B with further increase in Re greater than 5000.
Fig:9 Te Versus L with HI-A
Fig: 10 Te Versus L with HI-B
With esteem to rise of fluid temperature raising along the extent of the pipe from inlet end, the figures 9&10 indicate similar trend for the cases with HI-A & HI-B i.e increasing rapidly initially up to length of 2500 mm and there after temperature raising very slowly from 2500 mm to the full length of the pipe, the reason for slow increase of temperature beyond 2500 could be due to loss of convective heat transfer to the metallic inserts
as conversed above. On the other hand, it is seen that the temperature for the cases without insert A or B continuously raises linearly up to the end of the pipe.
Fig:11 Temperature contour with HI-A
Fig:12 Temperature contour with HI-B
Fig.11 With HI-A case of long inserts the heat transfer mechanism and improvement is purely transferred by more surface area in the means of twisted helical inserts having large area compared to a Fig12 with HI-B, the temperature difference in higher to lower body heat bartering of 70 in the first case (HI-A) and same way 64 second case (HI-B) here the temperature gradient 6. The contour image indication of temperature ranges from 303 to 373 (HI-A) & 303 to 364 (HI-B).
Fig:14 Temperature contour without HI
In fig. 14 concludes the without- HI there is no excess amount of heat transfer between working fluid and bulk wall surface, it is nominal heat transfer to be optimized at elevated flow and temperature conditions. Along tube of the surface is maximized at most of saturated condition of employed fluid.
-
CONCLUENCES
-
When compared to nano fluids with consideration of various volume and weight concentration of proportions, here is a less effectiveness in the enhancement in the rising temperature at wall interface due to HT phenomena in the desired experimentation.
-
At elevated temperature conditions means maximum temperature gradient to be optimized 373K up to above normal temperature existing in the operating of pre-determined mass of flow through in pipe SPHE.
-
Plodding increment in the Nusselt number (Nu= 28 with HI-A) & (Nu= 25 with HI-B) and heat transfer coefficient with HI-A higher383 W/m². than the helical supplements of HI-B 322 W/m². K regarding conclusive data.
-
The confines in the possible mass flow rate through prescribed channel means 0.00025kg/sec to 0.04kg/sec admitted only because of heightened heat transfer time period among interfaces of both solid and liquid phases sufficiently for the flowing medium, if there is any transformation this mass flow rate beyond this value or else no significant HT mechanism occurred.
-
The optimized outlet temperature of the working fluids such convertible of heat carrying capacity over this analysis only up to 373K, whereas the critically approached value there is no scope in further incremental of (Te).
REFERENCES
-
J.D.Moya-Ricoa, A.E.Molina, J.F.Belmonte, J.I.CórcolesTendero, J.A.AlmendroIbáñeza, Experimental characterization of a double tube heat exchanger with inserted twisted tape elements. Applied thermal engineering 174(2020)115234.
-
Khashayar Sharifi, Morteza Sabeti, Mehdi Rafiei, Amir H. Mohammadi, Ali Ghaffari, Masoud Haghighi Asl, Hamidreza Yousefi, A good contribution of computational fluid dynamics (CFD) and GA- ANN methods to find the best type of helical wire inserted tube in heat exchangers. International journal of thermal science 154(2020)106398.
-
Shashank Ranjan Chaurasia, R.M. Sarviya, Thermal Performance Analysis of CuO/water Nanofluid Flow in a Pipe with Single and Double Strip Helical Screw Tape. S1359-4311(19)33911-0.
-
M.R. Salem, M.B. Eltoukhey, R.K. Ali, K.M. Elshazly, Experimental investigation on the hydrothermal performance of a doublepipe heat
exchanger using helical tape insert. International journal of thermal science124(2018)496-507.
-
Mehedi Tusar, Kazi Ahmed, Muhammad Bhuiya, Palash Bhowmik, Mohammad Rasul, Nanjappa Ashwath, CFD study of heat transfer enhancement and fluid flow characteristics of laminar flow through tube with helical screw tape insert. Energy Procedia 160 (2019) 699 706.
-
Khashayar Sharifi,Morteza Sabeti, Mehdi Rafiei, Amir H Mohammadi, Laleh Shirazi, Computational Fluid Dynamics (CFD) Technique to Study the Effects of Helical Wire Inserts on Heat Transfer and Pressure Drop in a Double Pipe Heat Exchanger.S1359- 4311(17)32304-9.
-
Anas El Maakoul, Azzeddine Laknizi , Said Saadeddine , Abdellatif Ben Abdellah, Mohamed Meziane, Mustapha El Metoui, Numerical design and investigation of heat transfer enhancement and performance for an annulus with continuous helical baffles in a double-pipe heat exchanger. Energy Conversion and Management 133 (2017) 7686.
-
M. Sheikholeslami, D.D. Ganji, Heat transfer improvement in a double pipe heat exchanger by means of perforated turbulators. Energy Conversion and Management 127 (2016) 112123.
Turbulent Heat Transfer in a Tube Fitted with Twisted Tape Placed Separately from the Tube Walls. Applied Mechanics and Materials 1662-7482, Vol. 751, pp 245-250.
-
Sami D. Salman, Abdul Amir H. Kadhum, Mohd S. Takriff, and Abu Bakar Mohamad, CFD Simulation of Heat Transfer Augmentation in a Circular Tube Fitted with Alternative Axis Twisted Tape in Laminar Flow under a Constant Heat Flux. Heat Transfer Asian Research, 43 (4), 2014.
-
M.M.K. Bhuiya, M.S.U. Chowdhury, J.U. Ahamed, M.J.H. Khan,
-
M.A.R. Sarkar, M.A. Kalam, H.H. Masjuki, M. Shahabuddin, Heat transfer performance for turbulent flow through a tube using double helical tape inserts. International Communications in Heat and Mass Transfer 39 (2012) 818825.
.