
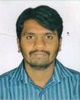
- Open Access
- Authors : Arunkumar K N , Dr. G B Krishnappa
- Paper ID : IJERTV11IS030111
- Volume & Issue : Volume 11, Issue 03 (March 2022)
- Published (First Online): 26-03-2022
- ISSN (Online) : 2278-0181
- Publisher Name : IJERT
- License:
This work is licensed under a Creative Commons Attribution 4.0 International License
Mechanical Properties of Aluminum Metal Matrix Composites – A Review
Arunkumar K N1, G B Krishnappa2
1Assistant Professor, Department of Mechanical Engineering, Vidyavardhaka college of Engineering, Mysuru, 570002, India
2 Dean(R&D) and Professor, Department of Mechanical Engineering, Vidyavardhaka college of Engineering, Mysuru,
570002, India
Abstract Current engineering applications require materials that are stronger, lighter and less expensive. Metal Matrix Composites (MMCs) are used for structural, electrical, thermal, tribological and environmental applications. Development of hybrid metal matrix composites has become an important area of research interest in Material Science. The research works on hybrid composite material containing Aluminum alloy as matrix and SiC, B4C, Alumina, TiO2, Gr etc., as reinforcements with varying weight percentages are considered for the review. This review also aims at studying the effect of reinforcement on mechanical properties of aluminum matrix composite with cryogenic treatment.
Key Words: Aluminum Metal Matrix Composites (AMMCs), Metal Matrix Composites (MMCs), Cryogenic treatment, Reinforcements.
1.INTRODUCTION
Composite materials gained importance because of their enhanced properties compared to alloys. Today composites are well occupied in the field of automotive, aeronautical and spacecrafts industry. Composite materials are present generation materials which are developed to meet the demands of fast-growing requirements of industry and market. The present investigation is concentrated on Aluminium Metal Matrix Composites (AMMCs). In AMMCs, the major phase of aluminium alloy act as matrix phase and another phase act as reinforcement phase which tightly binded the matrix phase, basically they are ceramic, non-metallic carbides or cemented carbide materials like alumina, SiC, B4C, Gr, CO etc., The major advantages of AMMCs compared to unreinforced materials are greater strength, improved stiffness, reduced weight, improved high temperature properties, improved abrasion and wear resistance as well as improved damping capabilities. Cryo treatment has successfully proved that it has improved material characteristics of MMC. This is possible by changes in the Microstructural of the material by change in the crystal structure with fine grains and it converts the chemical composition of the material by deep cryo treatment [-196oC].
-
Mechanical properties of AMMCs
The essence of research works concerning with the various properties of composite materials for different reinforcement materials with varied proportions along with cryogenic treatment are discussed in this section.
-
Tensile strength of AMMCs
The specimen fabricated by stir casting equipment which yields maximum tensile strength at 15% SiC reinforcement, then decreases from 15% till 30% SiC reinforcements [1]. Stir
casting and lost wax casting technique was used to fabricate the composites which show a significant improvement in the yield and ultimate tensile strengths of the composite with increasing the SiC content and/or decreasing the particle size of the reinforcement. [3,4,6,19,30,35]. The ultimate tensile strength was decreased by 5.88% by the addition of gr reinforcement in steps of 3% which varied from 0% to 12%. . This is due to the detrimental effect of Al4C3 at the interface of the graphite and the Al matrix [2, 5]. Tensile properties improvement has been observed for cryo treated specimens. The cryotreated Al 6061+5%SiC+2%Gr composite has shown optimum value. As the percentage of Gr increases above 2% decrease in tensile strength has been observed [7].The SiC varies from 2.5 % to 10% and Gr varies from 1% to 4% in four equal proportions. The cryotreated Al6061 reinforced with 2% Gr and Al6061 reinforced with 7.5% Sic has maximum value of tensile strength compared to untreated specimens [8]. Addition of SiC in Aluminum metal matrix above 10% leads to decrease in tensile strength and elongation which was fabricated by stir casting technique [9]. Tensile strength of prepared Al6061 hybrid composites is higher when
compared to base Al 6061 composite. Addition of 6% SiC and Gr varies from 3% to 9% increases the tensile strength considerably with respect to base matrix Al6061 [10]. The composite specimen was prepared with 66 grams (3.3%) of SiC, 66 grams (3.3%) of graphite and 2000 grams of Aluminium. The results indicate an improved tensile strength of around 9% compared to base Al alloy [11]. The tensile strength and yielding strength of the Al-4.5% Cu alloy increased with the addition of 6 wt. % of SiC and Graphite particulates [12]. AlSiC and AlGr composites required for the investigation are fabricated by stir casting. Al-SiC and Al- Gr composite shows considerable improvement in tensile strength compared to base Al 6063 alloy.. The Al-SiC exhibits higher tensile strength compared to Al-Gr composite [13]. The tensile strength of Al-Si alloy, Al-Si-Gr (3%) and Al-Si-Cu (2%) decreases were decreasing with increase in temperature from room temperature to 3000C [14]. The tensile strength will be the optimum at Al (90%) – Gr (2%) – SiC (2%) – B4C (6%) combination which was fabricated by stir casting method with a stirring speed of 450 rpm, stirring time 0f 5 min and preheat temperature of 4800C [15]. Fabrication of Al6061 hybrid composite reinforced with 6 wt.% of SiC and varying steps of graphite by 3 wt.%, 6 wt.%, and 9 wt.%. The tensile strength increases with the increase in Gr particulates with the influence of SiC particulates [16]. The Al6061 (95%) – SiC (3%) – TiB2 (2%) will exhibit higher tensile strength than Al6061 (90%) –
SiC (5%) – TiB2 (5%) [17]. Al 6061 +10% alumina and fly- ash, Al 6061 +15% alumina and fly-ash and Al 6061
+20%alumina and fly-ash are fabricated by using stir casting. The tensile strength increases with increasing % of alumina and fly-ash [18]. The matrix alloy 7072 exhibits lower ductility than the matrix alloy 6063. Adding of 5 wt. % TiO2 to the aluminum matrix and addition of 2 or 4 wt. % Gr to the Al- TiO2 composite increased the tensile strength [20]. The results showed that the yield stress, tensile strength and the modulus of elasticity were increased by 11%, 51%, and 51% respectively for 4% wt. reinforcement of boron carbide [21]. Increasing the content of graphite within the aluminum boron carbide matrix results in significant decrease in ductility and ultimate tensile strength [22]. Increase in the yield strength and ultimate tensile strength takes place with the increase in rice husk and SiC content. The strength improvement of hybrid composites can be attributed to the increase in the dislocation density [23]. With the addition of SiC (5%) + Flyash (5%) and SiC (5%) + Basalt (5%) to the base Al6082 alloy, the tensile strength increases [24]. For longer time and with higher speed it is recommended that the composite with 10 % Cu, for short run applications composite with 15 % Cu is the best and for structural applications the composite with 20 % Cu may be considered [25]. Addition of SiC particulates up to 20% has resulted in increased tensile strength with maximum value being at 15% of SiC as well as its addition yields weight reduction by a factor two [26]. Addition of Al2O3 has resulted in application of higher stress to initiate plastic deformation in matrix alloy of AA6061 composite [27]. Mechanical properties of the specimens shown increase up to 20% reinforcement of SiC beyond that no improvement found [28]. Tensile properties after mixing of Al2O3 and Graphite particulates are higher than Al6061 alloy [29,31,36]. Al6061/Al6063-wt. 15%/20% iC
exhibited higher UTS compared to unreinforced alloy [32,33]. The AlSiC rod can sustain axial stress of 23% over Von Mises yield stress in constant angle of twist tests, when the plastic strain was of the order of elastic strain [34].
-
Hardness of AMMCs
-
The material became harder due to increasing proportions of SiC results to decrease in elongation % of AlSiC metal matrix composites [1,4,6,9,24,28,32]. The hardness of the nano composites continuously decreases with the addition of graphite [2,5,22] but addition of boron carbide will contribute to increase in hardness to the base Al alloy. The low aspect ratio particle reinforcements are of much significant in imparting the hardness of the material than the other types of reinforcements. The higher hardness is due to the particulate reinforcements like SiC, Al2O3 and aluminide [9,37]. This is as shown in figure 1 and 2 [37]. The hardness of Al-SiC composite is greater than that of Al-Gr composite because of high hardness of SiC [13,38]. Hardness of hydrid composites (Al-SiC-Gr) shows significant improvement due to uniform distribution of reinforcement [11,39]. The hardness of the Al- 4.5% Cu alloy increased with the addition of 6 wt. % of SiC and Graphite particulates [12], Also, 5 wt.% SiC and 15 wt.% Copper will have increased hardness value [25]. Addition of boron carbide to Al-SiC improves the hardness of the hybrid composite [15]. Adding Gr above 3% to the Al-SiC/Alalloy will decrease the value of hardness [16,29]. On addition of SiC
and TiB2 to the Al6061 matrix, hardness value increases by considerable amount [17].
Fig. 1. Variation of Vickers Hardness of Al6061-SiC and Al7075-Al2O3 composites [37]
Figure 2. Variation of Brinells Hardness of Al6061-Al2O3 and Al7075-SiC Composites [37]
2.3 Wear strength of AMMCs
A Pin-On-Disc wear testing machine to check the wear rate. Wear rate reduces significantly in the composites due to the increasing proportions of SiC reinforcement till 15% [6]. The wear behavior on Pin-on-disc wear setup shown reduction in mass loss and wear rate due to the presence of SiC, Gr [11,13,29,35,50]. The addition of SiC (5%) + Flyash (5%) and SiC (5%) + Basalt (5%) to the base Al6082 alloy decreases the wear [24]. For longer time and with higher speed it is recommended that the composite with 10 % Cu, for short run applications composite with 15 % Cu is the best and for structural applications the composite with 20 % Cu may be considered [25]. Wear resistance properties are higher in case of composites compared to unreinforced 6061Al matrix. The graphite varied as 3%, 6% and 9%, alumina is maintained 10% as constant [29]. The composite shows better dry abrasive wear resistance when Aluminium reinforced with SiC and MWCNT [40]. The addition of fly ash up to certain level (20%) and graphite (4%) reinforcement to the base Al alloy decreases the specific wear rate [41]. The optimum conditions for wear volume loss of MMCs tested are observed at 5 wt % reinforcement of Gr with contact stress of 0.4 MPa and 1.6 MPa, sliding distance of 300 m and 1800 m, sliding velocity of 2 m/s and 0.5 m/s respectively [42]. Results showed that sliding distance is the most influential factor and load is the factor which affects the wear least. The Al6082/Gr composites were successfully fabricated by stir casting process and the wear resistance of composite has been improved as compared to conventional AA6082 matrix [43]. Increase in percentage of TiC from 2% to 10% to AA7075 matrix material, decreases the volume loss and coefficient of friction [44]. Alumina (Al2O3), Silicon Carbide (SiC) and Hybrid (Al2O3+SiC) reinforced with
Aluminum alloy (AL7075) will show improved wear resistant which will be used for automobile parts like disc brake, piston, cylinder liner, drive shaft etc. [45]. The addition of reinforcement particles B4C and MoS2 to the base Al 2219 alloy reduces the specific wear rate of composites [46]. The study reveals that the addition of Gr will enhance the wear properties of Al/SiC/Gr hybrid composites under optimum conditions [48]. The results indicate that 5% B4C reinforced with Al-Gr MMC is better applicable than the other B4C reinforced (2.5% and 7.5%) due to their superior characterization [49].
Fig.3. Weight loss values of different Al2O3/ SiC MMCs [47]
Fig.4. Cumulative volume loss values of different Al2O3/SiC MMCs [47]
2.4 AMMCs subjected to cryogenic treatment
The tensile, hardness of the Al6061 alloy reinforced with B4C and Gr shows marginal improvement after cryogenic treatment, but impact strength decreases [50]. The hardness of the LM25/SiC composites improves showed after the cryogenic treatment at -1960C due to the coarse eutectic phase present in the matrix as compared with cast samples. Deep cryogenic treatment of 0.2 wt. % Al2O3 showed great value of yield strength compared to other alloys [53]. Increasing cryogenic cycles will decrease the creep compliance as the matrix of the composite became brittle after cryogenic cycled [54]. The microstructure and hardness of the AL6061-Al2O3 metal matrix composites improves on effect of cryogenic treatment. Also, varying cryogenic treatment duration in hours increases the hardness is shown in figure 5 [55]. The Ultimate tensile strength, yield strength and compressive strength increases with increasing wt. % of reinforcement for the MMCs for the same cryogenic condition. The application of cryo treatment has increased the hardness further due to the presence of coarse eutectic phase [56]. The results revealed that cryogenic
treatment improves the wear resistant and hardness of Al6061/SiC/TiO2 hybrid composites [57]. The experimental results show that Compression Strengths increases as the duration of cryogenic treatment increases, but as the percentage of Copper increases in the Alloy the Compression Strength increases to some extent and then decreases [58]. The tensile strength increases and compressive strength, toughness & hardness of AlSi10Mg alloy increased drastically after cryogenic treatment. Ductile to brittle transition in between 12 hour to 24 hour cryogenic treatment takes place which was mainly due to the precipitation of second phase particles [59]. A marginal improvement in the mechanical properties was observed after cryogenic treatment for most of the alloys.
Fig.5. Effect of cryogenic treatment duration on microhardness of the Al and Al /Al2O3
Fig.6. Tensile behavior with and without cryo Treatment for different materials [60]
CONCLUSION
The review of investigations reveals that various parameters like Fabrication method, Microstructure and different combinations of reinforcements will lead to the several conclusions on the Hybrid Aluminum Metal Matrix Composites (HAMMCs). Firstly, the microstructures of the HAMMCs fabricated by stir casting method have been found to be stable with uniformed distribution of reinforcing particles. Consequently, the HAMMCs can be fabricated with different combinations of reinforcements to achieve desirable mechanical properties. The composition and type of the
reinforcements control the mechanical properties of the HAMMCs with respect to the strength. It has also been observed from the literature that the reinforcements like SiC, alumina, Gr, B4C can be combined with complementary reinforcements to obtain desirable properties for the composite. Also, from the review it is seen that the effect of cryogenic treatment will enhance the mechanical properties like Tensile strength, hardness and Wear resistance of HAMMCs. The study reveals that the HAMMCs can be considered as a replacement for conventional materials in recent advanced applications. The present review confirms that the utilization of HAMMCs in various structural, electrical, thermal, tribological and environmental applications seems to be feasible.
REFERENCES
[1] Surya Kumar, Earnest vinay Prakash, Prabhat kumar Sinha and Amit, Analysis and Testing of Aluminium Silicon Carbide Metal Matrix Composites Paripx – Indian Journal of Research, ISSN – 2250-1991, Volume 4, Issue 8, Aug 2015. [2] Syed Nasimul Alam and LaileshKumar Mechanical properties of aluminium based metal matrix composites reinforced with graphite nanoplatelets Materials Science&Engineering A667 (2016), pg.no.1632. [3] Yehia M. Youssef and M. A. El-Sayed, Effect of Reinforcement Particle Size and Weight Fraction on the Mechanical Properties of SiC Particle Reinforced Al Metal Matrix Composites, International Review of Mechanical Engineering (I.RE.M.E.), Vol. 10, No. 4, ISSN 1970 8734, July 2016. [4] K Karvanis , D Fasnakis , A Maropoulos and S Papanikolaou Production and mechanical properties of Al-SiC metal matrix composites IOP Conf. Series: Materials Science and Engineering 161 (2016) 012070 doi:10.1088/1757-899X/161/1/012070. [5] Pardeep Sharma, SatpalSharma and DineshKhanduja, Effect of graphite reinforcement on physical and mechanical properties of aluminum metal matrix composites, Taylor and fraancis group, particulate science and technology 2016, VOL.34, NO.1, pg.no.1722. [6] Rajesh Agnihotri and Santosh Dagar, Mechanical Properties of Al- SiC Metal Matrix Composites Fabricated by Stir Casting Route, Research in C Medical & Engineering Sciences CRIMSON PUBLISHER,S Wings to the Research ,December 05, 2017 [7] Arunkumar K N, G B Krishnappa, S Kasturirengan and Laxman B R An Experimental Investigation on Tensile and Compression Behavior of Aluminum, Silicon Carbide, and Graphite Hybrid Composite with and without Cryogenic Treatment, Elsevier Materials Today: Proceedings 5 (2018) 904910. [8] Arunkumar K. N., G. B. Krishnappa and Mohammed Salman Pasha, A Study on Tensile and Shear behaviour of Untreated and Cryogenically Treated Al-SiC and Al-Gr Metal Matrix Composite, MATEC Web of Conferences 144, 02019 (2018) [9] N.Subramani, M.Balamurugan and K.Vijayaraghavan Mechanical Behavior of Al-SiC Composites Prepared By Stir Casting Method, International Journal of Innovative Research in Science, Engineering and Technology (An ISO 3297: 2007 Certified Organization) Vol. 3, Issue 3, March 2014, ISSN: 2319-8753. [10] Pulkit Bajaj, Mechanical behaviour of aluminium based metal matrix composites reinforced with Sic and alumina, A thesis, master of Engineering in Production and Industrial Engineering, department of Mechanical Engineering, Thapur University, Patiala-147004, INDIA. [11] A. Karthikeyan, S. Nallusamy Investigation on Mechanical Properties and Wear Behavior of Al-Si-SiC-Graphite Composite using SEM and EDAX, IOP Conf. Series: Materials Science and Engineering 225 (2017) 012281. [12] Amarnath J S, Chris Edberg, Bharath G R, Girish B R, G L Chandrasekhar and Madeva Nagaral, Hardness and tensile behavior of AL-4.5%CU-SIC-Graphite particulates reinforced hybrid composites International Journal of Engineering Research, Volume No.5 Issue: Special 6, pp: 1129 1254, ISSN: 2319-6890)(online),2347-5013(print), 20 May 2016.
[13] Jaspreet Singh, Deepak Narang and N.K. Batra, Experimental Investigation of Mechanical and Tribological Properties of Al-Sic and Al-Gr Metal Matrix Composite, ISSN: 0975-5462, Vol. 5, No.06, June 2013, Pg.No.1205-1210. [14] G Rajaram, S Kumaran and T Srinivas Rao, Tensile behavior of Al-Si and Al-Si/graphite composites at elevated temperature Materials science forum, ISSN: 1662-9752, Vol.710, pp.457-462, 2012. [15] V. L. Kingston, M. John Prabhakar and N. Senthil Kumar A Study on Mechanical Characteristics of Hybrid Metal Matrix Composite, International Journal of Engineering Research and Technology, ISSN: 2278-0181, Vol.3, Isue 4, April 2014. [16] Niranjan K N, Shivaraj B N, Sunil kumar M, Deepak A R Study of mechanical properties on al 6061 hybrid composite by stir casting method, International Research Journal of Engineering and Technology (IRJET), e-ISSN: 2395 -0056, Volume: 04 Issue: 01 | Jan-2017.
[17] Elvin Raju. Chevvakula, Yeswanth Kumar P, S.Sivananthan and Dr. D.Vijayaganapathy Investigation of Mechanical Properties for Al- Sic-TiB2 Metal Matrix Composite, International Journal of Pure and Applied Mathematics, Volume 118 No. 24 2018. [18] Mr. Himanshu Chauhan, Mr. Irfan and Mr. Ashish Chauhan, Variation of Mechanical Properties (Tensile Strength&Microstructure) of Al6061/(Al2o3 And Fly-Ash), Hybrid Metal Matrix Composite Produced by Stir Casting, International Research Journal of Engineering and Technology (IRJET), e-ISSN: 2395-0056, Volume: 04 Issue: 07 | July -2017.
[19] A. Chennakesava Reddy, Evaluation of Mechanical Behavior of Al/Sic Metal Matrix Composites with respect to their Constituents by Taguchis Techniques, i-managers Journal on Mechanical Engineering, Vol.1, No.2. February April 2011. [20] Manickam Ravichandran and Sundaram Dineshkumar Experimental investigations of Al-TiO2-Gr hybrid composites fabricated by stir casting, https://www.researchgate.net/ publication/303370651. [21] Zahraa Fadhil and Haydar Al-Ethari Influence of Boron Carbide Reinforcement on Mechanical Properties of Aluminum Base Composite Prepared by Stir and Squeeze Casting Journal of Babylon Univ ersity/Engineering Sciences/ No.(5)/ Vol.(25): 2017. [22] C.Muthazhagan, A.Gnanavel babu, G.B.Bhaskar, K. and Rajkumar Influence of Graphite Reinforcement on Mechanical Properties of Aluminum-Boron Carbide Composites, Advanced Materials Research Vol. 845 (2014) pp. 398-402. [23] Dora Siva Prasad, Chintada Shoba, and Nallu Ramanaiah,Investigations on mechanical properties of aluminum hybrid composites Journal of Materials research and Technology, Brazilian Metallurgical, Materials and Mining Association. Published by Elsevier Editora Ltd., 2013. [24] G. Venkatachalam and A Kumaravel,Mechanical Behaviour of Aluminium Alloy Reinforced With SiC/Fly Ash/Basalt Composite for Brake Rotor, Polymers & Polymer Composites, Vol. 25, No. 3, 2017. [25] Antaryami Mishra 1 and Sandip.Kumar Nayak, Mechanical Behaviour and Wear Characteristics of Al-Cu- SiCP Hybrid Composites, SSRG International Journal of Mechanical Engineering (SSRG-IJME) volume 4 Issue 5 May 2017 [26] Neelima Devi. C, Mahesh.V and Selvaraj, N Mechanical characterization of Aluminium silicon carbide composite International journal of applied engineering research, Dindigul Vol. 1, No 4, 2011, pp.793-799. [27] Khalid Al – Dheylan and Syed Hafeez, Tensile failure micro mechanism of 6061 aluminum reinforced with submicron Al2O3 metal-matrix composites, The Arabian Journal for Science and Engineering, Vol. 31, Number 2C, 2006, pp. 89-98. [28] Khalid Mahmood Ghaur , Liaqat Ali, Akhlaq Ahmad, Rafiq Ahmad Synthesis and Characterization of Al/SiC Composite Made by Stir Casting Method J. Engg. & Appl. Sci. Vol. 12, Jan., 2013, pp. 102- 110. [29] Sudindra s & C Anil kumar Studies on al6061/al2o3 and graphite hybrid metal matrix composites International Journal of Metallurgical & Materials Science and Engineering (IJMMSE) ISSN 2278-2516 Vol. 3, Issue 3, Aug 2013, pp.35-42. [30] Mohan Vanarotti, S.A Kori, B.R Sridhar, Shrishail B. Padasalgi. Synthesis and Characterization of Aluminium Alloy A356 and Silicon Carbide Metal Matrix Composite, 2012 2nd International Conference on Industrial Technology and Management (ICITM 2012) IPCSIT vol. 49, pp. 11-15, 2012 IACSIT Press, Singapore. [31] Madeva Nagaral, V Auradi & Ravishankar M K, Mechanical behaviour of aluminium 6061 alloy reinforced with Al2O3 & graphite particulate hybrid metal matrix composites International Journal of Research in Engineering & Technology (IJRET) Vol. 1, Issue 2, July 2013, pp193-198. [32] Jebeen Moses, I.Dinaharan, S.Joseph Sekhar, Characterization of silicon carbide particulate reinforced AA6061 aluminium alloy composites produced via stir casting, Procedia Materials Science 5, 2014, pp.106 112. [33] K. L. Meena, DR. A. Manna, DR. S. S. Banwait, DR. Jaswanti, An Analysis of Mechanical Properties of the eveloped Al/SiC-MMCs, American Journal of Mechanical Engineering, 2013, Vol. 1, No. 1, pp.14-19. [34] R. Padmanabhan, B.J. MacDonald, and M.S.J. Hashmi, Elastic plastic behaviour of an AlSiC MMC rod under combined tension and torsion loading, Journal of Materials Processing Technology 155156, 2004, 17561759. [35] Md. Habibur Rahman, H. M. Mamun Al and Rashed, Characterization of silicon carbide reinforced aluminum matrix Composites, Procedia Engineering 90 (2014) 103 109. [36] P Balaji And Aniruddha V Muley Mechanical Properties of Al Matrix Hybrid Composites, International Journal of Mechanical And Production Engineering, ISSN: 2320-2092, Volume- 4, Issue-9, Sep.- 2016. [37] Mechanical behavior of Particulate Reinforced Aluminum Metal Matrix Composites A Review International Journal of Engineering Technology Science and Research (IJETSR),ISSN 2394 3386 Volume 4, Issue 12, December 2017. [38] Arunkumar K. N., G. B. Krishnappa and Mohammed Salman Pasha, A Study on Hardness and Wear behaviour of Untreated and Cryogenically Treated Al-SiC and Al-Gr Metal Matrix Composite, MATEC Web of Conferences 144, 02020 (2018) [39] An Experimental Investigation on Hardness and Shear Behavior ofAluminum, Silicon Carbide, and Graphite Hybrid Composite with and without Cryogenic Treatment, Materials Today: Proceedings 5 (2018) 916921. [40] K.R.Padmavathi and Dr. R.Ramakrishnan,Tribological behaviour of Aluminium Hybrid Metal Matrix Composite, Procedia Engineering 97 ( 2014 ) 660 667. [41] Viney Kumar, Rahul Dev GuptaandN K Batra, Comparison of Mechanical Properties and effect of sliding velocity on wear properties of Al 6061, Mg 4%, Fly ash and Al 6061, Mg 4%, Graphite 4%, Fly ash Hybrid Metal matrix composite, Procedia Materials Science 6 ( 2014 ) 1365 1375. [42] S. Rajesh, A. Gopala Krishna, P. Rama Murty Raju and M. Duraiselvam, Statistical Analysis of Dry Sliding Wear Behavior of Graphite Reinforced Aluminum MMCs, Procedia Materials Science 6 ( 2014 ) 1110 1120. [43] Pardeep Sharma, Dinesh Khanduja and Satpal Sharma, Dry sliding wear investigation of Al6082/Gr metal matrix composites by response surface methodology, jmaterrestechnol. 2016;5(1):2936. [44] V Ramakoteswara Rao, N.Ramanaiahb, and M M M Sarcar, Dry Sliding Wear Behavior of TiC AA7075 Metal Matrix, International Journal of Applied Science and Engineering 2016. 14, pg.no.27-37. [45] Raghavendra N and V S Ramamurthy, Tribological Characterization of Particulate MMMC Developed By Stir Casting Process, International Journal of Recent Advances in Mechanical Engineering (IJMECH) Vol.5, No.4, November 2016. [46] N.G.Siddesh kumar, G.S.Shiva Shankar and S Basavarajappa, A Study on Dry Sliding Wear Behaviour of Hybrid Metal Matrix Composites at Room Temperature, Applied Mechanics and Materials Vols 766-767 (2015) pp. 219-228. [47] N Altinkok, Ozsert and F Findik Dry Sliding Wear Behavior of Al2O3/SiC Particle Reinforced Aluminium Based MMCs Fabricated by Stir Casting Method, Acta Physica Polonica A, Vol. 124 (2013). [48] Fabrication characteristics and tribological behavior of Al/SiC/Gr hybrid aluminum matrix composites: A review, Friction 4(3): 191 207 (2016). [49] N. Senthilkumar1, T. Tamizharasan and M. Anbarasan Mechanical Characterization and Tribological Behaviour of Al-Gr-B4c Metal Matrix Composite prepared by Stir Casting Technique, Journal of Advanced Engineering Research ISSN: 2393-8447 Volume 1, Issue 1,2014, pp.48-59.
[50] E. Gewfiel , M A H E LMeniawi andY. Fouad, The effects of graphite and SiC formation on mechanical and wear properties of aluminumgraphite (Al/Gr) composites, 978-1-4673-4810-2/12/,2012 IEEE. [51] Varun Chandra M, Sudarshan M, Sumantha H and Harshith Gowda K I Effect of with and without cryogenic treatment on Tensile, hardness and impact on hybrid Aluminium-6061 metal matrix composites,International Journal of Engineering Research and General Science Volume 6, Issue 3, May-June, 2018.
[52] G Elango, BK Raghunathb and K ThamizhmaranEffect of Cryogenic Treatment on Microstructure and Micro Hardness of Aluminium (LM25) – SiC Metal Matrix Composite, TJER Vol. 11, No. 1, 64-68, 16 March 2014. [53] Al-Alkawi Hussain Jasim Mohammed, Abthal Abd Al-Rasiaq and Mamoon A A Al- Jaafari, Effect of Cryogenic Treatments on Mechanical Properties of 7075 Aluminum Alloy Matrix/Al2O3 Particles Reinforced Composites, International Journal of Engineering Research and Modern Education (IJERME), Volume 2, Issue 1, 2017. [54] Jiemin Feng, Hui Wang, Zhansheng Guo, Hongjiu Hu and Junqian Zhang Effect of Cryogenic Cycles on Mechanical Behavior of Glass/Epoxy Composite, Polymers & Polymer Composites, Vol. 22, No. 2, 2014. [55] Panchakshari H V and Dr. Girish D P, Effect of Cryogenic Treatment on Microstructure and Microhardness of Al6061-Al2o3 Metal Matrix Composites Journal of Engineering Research and Studies JERS/Vol. III/ Issue I/January-March, 2012/105-107. [56] Panchakshari H V, Girish D P and M Krishn, Effect of Deep Cryogenic Treatment on Microstructure, Mechanical And Fracture Properties of Aluminium-Al2O3 Metal Matrix Composites, International Journal of Soft Computing and Engineering (IJSCE), Volume-1, Issue-6, January 2012. [57] A jayachendran, Dr. K Velmurugan, Dr. V S K Venkatachalapathy and K Thamizhmaran, Effect of Cryogenic treatment on Microstructure and Tribological Properties of AL6061 Hybrid Metal Matrix Composite, International Journal of Engineering Research and Technology(IJRET), Vol.7, issue 5, May-2018. [58] G Ramanjaneya Yadav, N Harsha, V Durga Prasada Ra and S Rajesh, Effect of Cryogenic treatment on Compression Strength of Al-Cu alloys SSRG International Journal of Mechanical Engineering (SSRG-IJME) – Special Issue May – 2017. [59] Ramesh S. Desai, Ajith G Joshi and Sunil Kumar B V Study, On Influence of Cryogenic Treatment on Mechanical Properties of Alsi10Mg Alloy, IJRET: International Journal of Research in Engineering and Technology, Volume: 05, Special Issue: 21, ICRIET- 2016. [60] Pavan K M, Sachin L S , Mayur S, Chandrashekar.A and B S Ajaykumar, Effect of Cryogenic Treatment on the Mechanical and Microstructural Properties of Aluminium Alloys – A Brief Study, International Journal of Mechanical and Production Engineering, ISSN: 2320-2092, Volume- 2, Issue- 5, May-2014.