
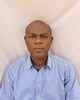
- Open Access
- Authors : Osita O. Obiukwu , John E. Igboekwe
- Paper ID : IJERTV9IS020150
- Volume & Issue : Volume 09, Issue 02 (February 2020)
- Published (First Online): 26-02-2020
- ISSN (Online) : 2278-0181
- Publisher Name : IJERT
- License:
This work is licensed under a Creative Commons Attribution 4.0 International License
Investigations on the Thermal and Dynamic-Mechanical Properties of Rattan Cane Fibre (Calamus Deeratus) Filled Epoxy Composites
Osita O. Obiukwu Department of Mechanical Engineering, Federal University of Technology, Owerri,
Imo State, Nigeria
John E. Igboekwe Department of Mechanical Engineering, Federal University of Technology, Owerri,
Imo State, Nigeria
AbstractIn this study, the dynamic-mechanical and thermal properties of rattan cane fibre reinforced epoxy were investigated. Varying fractions of the composites with 5 30 wt% fibre content and stoichiometric ratio of the epoxy/hardener (2:1) were fabricated using a compression moulding machine at 130 0C for about 10 minutes. The laminates were cut to square shapes (15 X 15 cm2) as test samples. FTIR Agilent technology was used to characterize the chemical structure; PerkinElmer TGA 4000 was used to study the heat flow characteristics, SEM model Phenon Prox. was used to study the surface morphology. The results showed that the treated fibre had improved facial adhesion, TGA results showed a decomposition temperature for filler to be at 310 0C. SEM shows best micro structure at 10 and 15 Wt.% of fibre, while DMA results depicts best combined values at 25 Wt.% fibre loading for storage & loss moduli and tan delta.
KeywordsCalamus deeratus, epoxy, DMA, thermal properties, dynamic-mechanical properties
-
INTRODUCTION
Composites of natural fibres and polymers are finding places in many industries, particularly in the automotive industry that demand materials that have low density, low cost, thermal and dynamic stability. Since many polymer matrices as well as most natural fibres have these characteristics, composites based on them usually show excellent specific properties [1]. Various types of lignocelluloses fillers have been exploited including wood flour, henequen, kenaf, hemp, sisal, flax, rice husk, jute and others [2, 3, and 4]. Fibre-reinforced composite materials use fibre materials to mechanically enhance the strength, elasticity and physical appeal of polymer composites. The extent to which strength and elasticity are enhanced in a fibre-reinforced polymer depends on the mechanical properties of fibre and matrix, their volumes relative to one another and the fibre length and orientation within the matrix [5]. A great variety of organic fibres obtained from cellulose- rich plants have in recent years not just being investigated but effectively employed in varying engineering composites [6]. Despite the advantage of organic fibres, the use of organic fibres as reinforcement agents, particularly in hydrophobic polymeric matrices, have several drawbacks such as poor wettability, incompatibility with some polymeric matrices and high moisture absorption by the fibres because of the hydrophilic nature of organic fibres. Other factors bedevilling the proper and effective harnessing and utilization of organic fibres is its degradation at relatively low temperature due to the presence of cellulose and hemicellulose. This early thermal
degradation limits the allowed processing temperature to less than 200 °C and restricts the type of thermoplastics that can be used with organic fibres to some commodity plastics such as pe, pp, pvc and ps [7]. They get sticky, crack, and shiny and melt in heat and humidity. Fibres-reinforced composite materials undergo various types of dynamic stressing during service, mainly in automotive products and the dynamic mechanical properties of these materials need to be investigated. The organic fibre used in this research is the rattan canes fibre. Rattan has thirteen genera with over 600 species; four of these genera are endemic to Africa in the tropical rainforest regions. The species in Nigeria in descending order of availability are calamus deeratus, eremospatha macrocarpa, oncocalamus manni and laccosperma secondiflorum. l. secundiflorum, c. deerratus, e. macrocarpa and o. manni having average stock densities per plot of 100 square metres of 6, 22, 12 and 18 clumps respectively. Calamus deeratus is the most abundant specie in Nigeria with small stemmed diameter ranging from 7.2 17.8 mm. Rattan canes are mainly from wild stocks and cane furniture/handicraft weavers form the bulk of cane users. Other uses of cane within the study area include: as cane for flogging, ropes for tying hides to drum frames, fish traps, loop for climbing palm trees, as food sources, and in medicinal applications for making artificial bones [8]. This paper examines the properties of rattan calamus deeratus and its application as organic fibre. The determination of the properties of rattan was conducted according to ASTM standard with a suitable modification. Composites were developed from epoxy and rattan cane fibre (treated with NAOH), using compression moulding process.
-
MATERIALS AND METHODS
-
Materials.
Epoxy LY 556 (bisphenol A diglycidyl ether) resin is used in this study due to its wider range of applications, its characteristic high adhesion, mechanical strength, heat and corrosion resistant abilities [9]. Hardener used is HY- 951(IUPAC name: NN bis (2 aminoethylene 1, 2-diamine. Sodium hydroxide (NaOH), Distilled water and processing oil were obtained from Rovet Chemicals, Lagos State, Nigeria. Rattan Cane was obtained from the surroundings of Owerri in Imo state while foil paper was obtained from Pascal Scientific, Lagos.
-
Preparation of the Composites.
The cane fibres (figure 1) were soaked for 4 hours and washed in water to remove the adhering dirt and peel the bark, they were dried in an oven at 70 OC for 6 hours. After drying, they were cut with Warring Blender to reduce the length of the fibre to 2 – 4 mm. Fibres were pre-treated with alkali using 5
% NaOH solution for four hours (4 hours). After pre- treatment, the fibres were washed with distilled water until all untreated sodium hydroxide was removed. After washing, the fibres were pre-dried, and oven dried at 80 OC for 4 hours. The fibres were bow milled for 12 hours to get a sieve size of 70
µm prior to compounding. The bio filler (rattan cane) was mixed with the epoxy by stirring at room temperature in a glass beaker with the help of suitable glass rod. Hardener was added into the beaker containing mixture at a time of stirring. With proper stirring for ten minutes, uniform mixing of the reinforcing agent and the polymer matrix was ensured and they were poured into a suitable mould. The fibre content of the composition was varied from 5-30 Wt.% at 5 Wt.% interval while the matrix (epoxy and hardener) content of the composition used was in a ratio of 2:1 as shown in the Table 1 below.
Fig. 1. Rattan cane (calamus deeratus)
TABLE I. FORMULATION OF EPOXY / HARDENER
/RATTAN CANE FIBRE RATIOS
Filler Wt.%
Epoxy Wt.%
Hardener Wt.%
00
05
10
15
20
25
30
66.66
63.33
60.00
56.67
53.33
50.67
46.67
33.34
31.67
30.00
28.33
26.67
25.33
23.33
-
Characterization.
The FTIR spectra of fibre were recorded in the range of 4000 to 600 cm1 at a resolution of 4 cm-1 using an FTIR Agilent technology Spectrometer. Thermo- Gravimetric Analysis (TGA) of the Bio filler samples were studied using PerkinElmer TGA 4000 (Netherlands). The morphology of the samples was studied using Scanning Electron Microscope model Phenon Prox. Manufactured by Phenonworld Eindhoven, the Netherlands. Sptter coater used is Q15ORES manufactured by Quonum, England using 7600F at an
accelerating voltage of 5.0kV and magnification of 1000. The dynamic mechanical properties of the samples were studied using Model DMA 242EArtemis. Specimens approximately 1 mm thick, 3 mm wide and 20 mm long were machined from a larger sample of cured laminate to evaluate the stiffness and damping properties of the samples.
III RESULTS AND DISCUSSION
-
Characterization.
The FTIR spectra analysis of the untreated and treated samples are shown in figures 2 and 3. Untreated rattan fibre spectrum in Figure 2(a) shows OH-stretching vibration of cellulosic structure with peak intensity of 3302.4 cm-1 indicating the presence of OH, Hbonded stretch of the alcohols, phenols compounds. This peak intensity tends to shift after Sodium hydroxide treatment to 3377.0 cm-1. The peak that appeared at frequency of 2970.0 cm-1 indicated the presence of CH stretching vibration of cellulose/hemicellulose which changed to 2922.2 cm-1 after sodium hydroxide treatment [10]. The C=O linkage of hemicellulose in the raw rattan fibre is exhibited by band of 1699.7 cm-1 which changes after sodium hydroxide treatment to 1707.1 cm-1. Peaking bands at 1602.8 cm-1 and 1509 cm-1 of untreated rattan fibre related to C=C aromatic stretching vibration due to lignin which peaks at 1606.5 after treatment. The peak that appeared at frequency of 1360.5 cm-1 indicated the presence of CH of alkanes. The peak that appeared at frequency of 1230 cm-1 indicated the presence of CH, (CHX) stretch of alkyl halides. The peak that appeared at frequency of 1028.7cm-1 indicated presence of CN stretch of aliphatic amines.
Fig. 2. FT-IR crystallography of the untreated rattan cane fibre
Fig. 3. FT-IR crystallography of the treated rattan cane fibre
-
Thermo Gravimetric Analysis.
Thermo gravimetric analysis (TGA) determines the thermal degradation behaviour of fibre by measuring the change in the weight of the composites sample when heated in air. When the filler/compound is heated at low temperature, moisture and other volatile components is evaporated first
(48.62 OC -194-29 OC. Further heating of the filler will get part of it degraded and converted into gaseous product with corresponding weight loss which is reflected in TGA curves [11]. On further heating, all organic matter will be removed leaving behind inorganic components in the compound. The TGA curve from the Fig. 4 and 5 for the bio fillers indicated a melting point of 194-210 OC which also overlaps with the distortion of water. The decomposition temperature for the fibres was indicated to be at 310 ºC. It may be observed that the decomposition peak is relatively a lower temperature as compared to that of native starch and other plants fibres [12]. Biofillers are wider in size covering more temperature range for complete decomposition of thermoplastic fibres confirming the better thermal stability of thermoplastic as compared to native fillers (not mix with matrix). The decomposition temperature is at 310 OC which appears as a glass transition (Tg), this behaviour may be related by the TGA curve between 194 – 220 OC, the decomposition temperature was shown between 310 – 410 OC. Degradation of all polymer composites first degrade at the temperature peak started at 220 OC, which is similar to the degradation of lignin materials, hemicelluloses, cellulose and lignin. Degradation temperatures are approximately 180 OC, 190 OC and 200 OC respectively as stated by the following investigations: [13]; [14]; [15]. The decomposition temperature peak gives the highest decomposition temperature at 512 OC. It is known that degradation takes place at this temperature.
Fig. 4. TGA of rattan cane fibre
1µm of diameter. The presence of pits and global marks after chemical treatment is important for increase in the effective surface area. This also increases the roughness of the fibre surface and consequently improving mechanical bonding with the polymer matrix. The composites show more or less even distribution of the filler on the matrix as the filler is not so viscous but tacky; as it spreads within the matrix it tends to stick. The physical appearance of the composites is ash black/brown black and brittle. The brittleness properties increases with increase in the filler content, it may be suggested that as the filler was spread by mechanical agitation, it goes in between the epoxy molecular chains and branches and stuck, thereby destructing the hydrogen bonding between the intermolecular chains/branches of the matrix, This phenomenon is prominent as filler load increases. It is observed that they all have better physical and morphological appearances in terms of surface flatness and homogeneity than 5 Wt.%, while the reverse is the case for higher ratios, thus it will be expected that the mechanical properties will have a similar effect. The bio-composites of plant origin are more hydrophilic.
-
Morphology.
Fig. 5. TGA of rattan cane fibre
The SEM micrographs in Fig. 6 (a-d) show the percentage of fillers and its effects on the bio-composites. It can be seen that micrograph showed various level of adhesion. It can be observed that the samples have a smooth adhesion. It is very clear that the filler weight of 10- 25 Wt.% increases the effective surface area available for wetting by the polymer matrix. It is achieved by increasing the fibre aspect ratio (ratio of length to diameter) by reducing the fibre diameter. The micrographs with a rough surface are a consequence of the matrix having higher surface energy and can improve the interface adhesion with the polymer matrix. The rough surface is made up of pits which are circular holes of about
Fig. 6. (a) Micrograph of 5 wt % fibre Composite (b) Micrograph of 10 wt % fibre Composite (c) Micrograph of 15 wt % (d)Micrograph of 25 wt % fibre Composite
-
Dynamic mechanical analysis (dma).
Fig. 7 (a-g) shows the outcome of the DMA/DTMA Results. The dynamic mechanical analysis (DMA) depicts the stiffness stability of the composite with the increasing temperature, its glass transition temperature and its visco-elastic nature when stimulated by dynamic loading. The tests were carried out under the load stress of 150 KN/m2slightly above atmospheric pressure. The amplitude of 60.00 nm, smoothing of 3e,005/0.1 m and P.F of 1.10 were maintained during the investigations. The curve shows the composite is stable under the dynamic loading (having zero strain) with increasing temperature at frequencies of 2.5 Hz, 5 Hz, and 10 Hz up to 80 OC. before the onset glass temperature of 37.4 – 54.4 OC.
Fig. 7 (a) Thermogram of control sample, (b) Thermogram of 5 % wt composite, (c) 10 % wt, (d) 15 % wt, (e) 20 % wt, (f) 25 % wt and (g) 30 % wt..
The results of the investigations showed that Fig. 7 (filler samples of 5.0-30wt% filler loading (composites)) give a good outcome in their performances. It showed the most outstanding Storage Modulus result at the Onset of 56.2 OC and inflation of 59.0 (Storage modulus or In-phase component is the measure of elastic modulus of a material but not the same as Youngs modulus). It has the second to the highest Storage modulus at the temperature of 59.2 OC and though with a lower Mpa of 239. It also has a glass transition temperature of 56.2 OC. (Glass transition temperature; sample become less hard as storage modulus decreases and tan delta peaks. Tan delta peak height is typically between 0.1 and 1.2. The onset can be taken to be the Tg). The Tangent Delta75.6 OC and peak of 0.910 while the change in length fall at 72.0 OC and -536 µm. Figure 14 (filler sample 5.00) has an outstanding Tangent delta at temperature 7596.6 OC at peak of 0.910. tan delta or damping is the loss of mechanical energy. Modeled by a dashpot. It has a change in length of 72.0 OC and -536.4 µm. The variation in change in length may be attributed to the content of the filler introduced to the matrix or sometimes may occur as result of the thermal history.From the thermographs, the Onset of storage modulus of the composite fall within the range of 37.4 -56.2, while the Inflation of the storage modulus of all composite investigated fall within the range of 41.4 58.2. The temperature of the Loss modulus fall within the range 35.7 OC 56.6 OC, while the strength the samples fall within the range of 175 -315 Mpa. In tangent delta, the temperature range for all the investigated sample fall within 67.4 OC 75.7 OC while the peak of the samples fall within 0.718 1.388. The change in length of the composites samples investigated fall within the range of 65.5 72.0 OC and –374.4 to -536.4 µm. While, the glass transition temperature of the samples fall within the range of 37.4 OC 56.2 OC. From the results obtained, it can be noted that, the combination of the thermoset matrix and the biofiller with the additives can yield a composites for domestic materials.
4 CONCLUSION
A study has been carried out to determine the effects of rattan fibre reinforcement on dynamic-mechanical and thermal properties of the composite. The FT-IR spectra suggest replacement of Hydroxyl bonds between the composites and partial ester formation for the fibre studied. The bio- composites were shown to have improved thermal stability with the application of suitable dual coupling agent than in their respective pure states. There is better adhesion of smaller particle size, which implies that particle size can affect adhesion and better filler performance as indicated by SEM micrographs. There is better enhancement in dynamic – mechanical properties for the treated composites samples compared to the untreated samples. The DMA curve also showed that the composites have higher glass transition temperature and better mechanical (stiffness) stability in high temperature under dynamic loading.
ACKNOWLEDGEMENTS
The authors thank to Dr, Henry and his team of technologists in NILEST Zaria and Mr. Fidelis Nwanya for their supports in varying proportions and different capacities.
REFERENCES
-
Kvien, I. & Oksman, K. Appl. Phys. A (2007) 87: 641. https://doi.org/10.1007/s00339-007-3882-3
-
K. Begum & M.A. Islam , Natural Fiber as a substitute to Synthetic Fiber in Polymer Composites:A Review, Res. J. Engineering Sci., Volume 2, Issue (4), Pages 46-53, April,26 (2013)
-
Han, Y.H., Han, S.O., Cho, D. et al. Macromol. Res. (2008) 16: 253. https://doi.org/10.1007/BF03218861
-
Wambua, P.; Ivens, J.; Verpoest, I. Natural fibers: Can they replace glass in fiber reinforced plastics? Compos. Sci. Technol. 2003, 63, 1259-1264.
-
Masuelli, Martin. (2013). Introduction of Fibre-Reinforced Polymers
Polymers and Composites: Concepts, Properties and Processes. 10.5772/54629.
-
Satyanarayana, K.G. & Guimarães, J.L. & Wypych, Fernando. (2007). Studies on lignocellulosic fibers of Brazil. Part I: Source, production, morphology, properties and applications. Composites Part A: Applied Science and Manufacturing. 38. 1694-1709. 10.1016/j.compositesa.2007.02.006.
-
Silva, R. V., & Aquino, E. M. F. (2008). Curaua Fiber: A New Alternative to Polymeric Composites. Journal of Reinforced Plastics and Composites, 27(1), 103112.
https://doi.org/10.1177/07316844080270010301.
-
E.B, Lucas & Dahunsi, B. I. O.. (2004). Characteristics of three western Nigerian rattan species in relation to their utilisation as construction material. Journal of Bamboo and Rattan. 3. 45-56. 10.1163/156915904772875635.
-
H. Lee and K. Neville, Hand book of Epoxy resins, Newyork; McGraw- Hill, 1967.
-
Abdullah,. A.H,. Russell,. D.S, and. Abdulwahab, A.S. (2011) Particle reinforced polymers, J. Bas. Res (Sci),. 37(3A), 36-42).
-
Gabbot, P. (2008). Principle and Application of Thermal Analysis. Oxford, UK. Blackwell Publisher.
-
Musa, M.B., Yakubu, M.K. & Akuso, S.L. (2013). The Study of Degradation Properties of Maize Starch – Filled Linear Low Density Polyethylene Composites. Journal of Research in Agriculture 8: 78- 82.
-
Xie, H.Z.&Xie,D.(2005). Effects of Coupling Agent on Properties of Polypropylene/Glass Journal of Applied Polymer Science, 97, 2254.
-
Xu, S.A., (2008). Effect of Compatibilizers Content on the Tensile Properties and Fracture Toughness of HDPE/Polystyrene Blends, Journal of Polymer Science, 32(3), 208-214.
-