
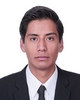
- Open Access
- Authors : M. Morales, R. Perea, C. Vasquez, O. Zempoalteca, E. Vargas, J. L. Hernandez, J. Carmona, M. Sanchez
- Paper ID : IJERTV9IS110017
- Volume & Issue : Volume 09, Issue 11 (November 2020)
- Published (First Online): 09-11-2020
- ISSN (Online) : 2278-0181
- Publisher Name : IJERT
- License:
This work is licensed under a Creative Commons Attribution 4.0 International License
Improvement of the Mechanical System of a
Winch
J. L. Hernandez, J. Carmona, M. Sanchez
Professor
Department of Industrial Maintenance Engineering
Universidad Tecnologica De Tlaxcala, Mexico
Abstract— This article shows the research work and activities carried out to improve the mechanical system of a winch by means of a thermic treatment that will give it hardness, resistance and elasticity. Solidworks was used for the simulation of the resistance and the structure of the mechanical components finite element method. Two simulations were carried out, one of them in the original state of the mechanical system. In order to determine which are the pieces that generated major resistance in the mechanism. Once thermic treatment was carried out, the second simulation was done that showed that the material resistance changed. The results showed that the parts this thermic process was applied to is more resistant fatigue, in order to the mechanism improving the useful life and its efficiency. In all greenhouses one of the important aspects is the winch, this equipment is essential in ventilation, to control the passage of air and temperature.
INTRODUCTION
Mechanical systems are essential in industry and in daily life as they lead to efficient work. The mechanical characteristics of a material depend on both its chemical composition and its crystalline structure. Thermic treatments modify this structure without the chemical composition, by means of a successive heating and cooling process until the desired crystalline structure is achieved. These systems are found throughout our environment, in our case we will use a winch to facilitate the work that is done in the curtain of a greenhouse, thus determining the analysis of the improvement of the mechanical system of the manual winch. Among the most important characteristics is the resistance to wear, which offers a material that is allowed to erode when in contact with another material by friction. That is why the thermic treatment was chosen in the foreground. This project is based on an improvement of the winch, the gears will be heated and cooled in water to increase the hardness of the steel, this is a thermic treatment called tempering.
Solidworks is a 3D CAD design software (computer aided design) for modeling 3D parts and assemblies and 2D drawings. It offers the possibility to create, design, simulate, manufacture, publish and manage the data of the design process.
Finite element method was used within the work that was done, to determine the fatigue to which the gear of the winch
M. Morales, R. Perea, C. Vasquez,
O. Zempoalteca, E. Vargas Students
Department of industrial maintenance Engineering
Universidad tecnologica de Tlaxcala, Mexico
Finite element analysis is a numerical method widely used in engineering to solve problems described by a series of partial differential equations. These types of problems are commonly found in mechanical design, acoustics, electromagnetism, fluid mechanics, among other studies and specifically in mechanical
THERMIC TREATMENT
Thermic treatment is essential to improve both the surface and hardness of the gear core, enhancing its ability to withstand tensile stress, improve strength and reduce wear. [1] TEMPERED
Its purpose is to increase the hardness and resistance of steel. Hardening produces a fine granular structure that increases tensile strength and decreases ductility. Steel can be hardened by heating to its critical temperature, which is approximately 790 to 830 °C, which is identified when the metal turns a bright cherry red color. Important factors in heat treatment are temperature, dwell time and cooling rate. [1] TEMPERATE COOLED IN WATER
Pieces to be cooled in water that have already been heated and maintained at 820 ºC during the calculated time (t), will be removed with pliers heated with to the torch or in a pre-heating muffle and quickly immersed in a brine bath (salt dissolved in the water until saturation). The quenching water must be clean and at a nearby temperature of 20 ºC. The specimens are shaken in the cooling bath until their temperature drops to about 100 ºC. [1] HARDNESS TEST – VICKERS
Vickers hardness (HV) is calculated by optically measuring the diagonal lengths of the impression left by the penetrator. The measurements are converted into HV by means of a formula: D= (D1+D2) / 2,
HV = (1,854*P) / D.
FINITE ELEMENT METHOD
is exposed, by means of a weight that was applied in the
Application of the finite element method by means of
simulation in Solidworks.
Solidworks Simulation allows the minimization or
IJERTV9IS110017 www.ijert.org
Published by : International Journal of Engineering Research & Technology (IJERT)
http://www.ijert.org ISSN: 2278-0181
Vol. 9 Issue 11, November-2020
maximization of mass, volume, tensile energy, tensile stress, force, displacement, speed, etc. As load conditions can be applied to the system point loads, pressure, thermal, gravity, static centrifuges, dynamic gravities. [5] GEAR TEMPERING
For the realization of the tempered of the winch gears, cooling was carried out in water as it was more efficient to achieve greater hardness. Using the temperature that was calculated and verified with table 1. [4]
Figure 3 Gear heating
Table 1. Steel 1018
The gear used for the test has the dimensions shown in Fig. 2, With a center diameter of 5.04 cm, a primitive diameter of 7 cm and with a number of teeth of 41. These measures were taken to calculate the ramps and use it in the execution of the tempered. The heating time for the gears depends on the size and shape of the part.
Figure 2 Gear dimensions
A furnace was used to carry out the tempering process. The gears were introduced into the furnace when the temperature increased to 850°C. Once this temperature was reached, the gears were left inside for 10 minutes so that the Steel could reach thermal equilibrium. In the fig. 3, the gear is shown in heating.
With the necessary safety equipment (tweezers, mask, gloves, dungarees and boots) the gears were removed after the mentioned time.
Figure 4 Gear Retreat
The cooling was done by putting the gears in clean water at a temperature required, these gears stirred in the cooling bath until its temperature decreases to about 100°C. As shown in fig. 5.
IJERTV9IS110017 www.ijert.org
Published by : International Journal of Engineering Research & Technology (IJERT)
http://www.ijert.org ISSN: 2278-0181
Vol. 9 Issue 11, November-2020
Figure 5 Gear Cooling
HARDNESS TEST
For know the hardness of the gear was used a Vickers durometer whose unit of measure is HV (Vickers), the penetrator that was used was a diamond pyramid with angle of 136°, when applying the load, left a square footprint on the material of the piece, as shown in Fig. 6.
Figure 6: Load application.
The load that is used to press the penetrator against the piece varies between 1 and 120 Kp, mainly load values of 1, 2, 3, 5, 10, 20, 30, 50, 100 and 120 Kp are used. However, the load used was 30 Kp. As shown in fig. 7, the time of application of the load during the Vickers hardness measurement ranges from 10 to 30 seconds, 15 seconds being the most used time for the duration of the measurement.
Figure 7: Application of load for 15 seconds
Once the application of the load was removed, the diagonals of the square penetration that resulted on the surface of the piece were measured as shown in figure 8, calculating the average of the measurements obtained.
Figure 8: square penetration
The Vickers hardness (HV) was obtained by dividing the load P (Kp) applied by the surface of the footprint S (mm2) left on the part.
𝐻𝑉 = 𝑃/𝑆 = 1,854 · 𝑃/𝑑2
Being:
•
P the load applied in the test (Kp)
•
S is the surface of the footprint (mm2)
•
D is the average value of the diagonal of the print on the specimen (mm).
Once obtained the value of the Vickers hardness was observed in table 2, the equivalence in Rockwell hardness.
IJERTV9IS110017 www.ijert.org
Published by : International Journal of Engineering Research & Technology (IJERT)
http://www.ijert.org ISSN: 2278-0181
Vol. 9 Issue 11, November-2020
Hardness table
Table 2.
SOLIDWORKS SIMULATION
A drawing was made that will serve to represent the mechanical parts of the winch, shown in fig. 9 and 10, to make a simulation in finite analysis in SolidWorks, to make the drawing of the pieces were measured with a Vernier once having the measures were it was used the sheet metal tool, rounding, extruding and extruding cut.
Once the pieces were drawn, we created the simulation by joining the gears, we added fixed geometry, fastenings, torsion, a mesh and a torsion force in order to have a finite analysis result, in one simulation the 1020 steel was used and in the other simulation the 1020 steel was used to visualize the resistance differences with the help of the colors code stress forces in each of the simulations. As shown in fig. 11 and 12.
IJERTV9IS110017 www.ijert.org
Published by : International Journal of Engineering Research & Technology (IJERT)
http://www.ijert.org ISSN: 2278-0181
Vol. 9 Issue 11, November-2020
RESULTS OBTAINED
The obtained values of hardness are the following:
Experimental Theory
Hardness
Before
tempering -2HRC -5HRC
Hardness
After
tempering 51,7HRC 50-60HRC
Table 3.
These values were obtained by performing the Vickers hardness test and converting them into rockwell hardness (HRC). As can be seen in table 3. The Tempered was successfully performed, increasing the gear hardness.
In the solidworks simulations in figure 11, a high torsional force scale is obtained while in figure 12. The scale of torsional force received by the gears is smaller, arguing that the resistance increases when the material is subjected to a thermal process, which in this case was tempered.
CONCLUSION
The heat treatments serve to improve the mechanical properties according to the application which is required, as reflected in the heat treatment performed on the piece, to be made successfully increases its hardness significantly and their functions. The simulation shows that there is less gear wear after heat treatment, the hardness test showed the increase in tolerance fatigue, concluding that it was a successful tempered.
AUTHORS AND AFFILIATIONS
José Luis Hernández Corona
Candidate for a Doctor from the Autonomous University of Tlaxcala, Research Professor in the area of Industrial Maintenance, Desirable Profile before the PROMEP, responsible for the CA of Industrial Maintenance at the Technological
University of Tlaxcala
Jonny Carmona Reyes graduated from the Technological Institute of Apizaco in 2010 with a bachelor´s degree in Electronic Engineering, specialty in automation and instrumentation. He worked as an electronic engineer in MIF company, developing electronic projects for the steel industry from 2010 to 2015. Since to 2013, he has been working as a teacher in the Technological University of Tlaxcala in the industrial
maintenance career.
Moisés Sánchez Moredia earned a Bachelor of Arts in Applied Modern Languages, specialized in English as a second language teaching by Universidad Autónoma de Tlaxcala. He holds a Master´s Degree in School Administration and Management by Universidad Internacional de la Rioja (UNIR). From 2016 to 2018, He was the coordinator of the English area in Universidad Tecnologica de Tlaxcala where he currently teaches
English in Industrial Maintenance Engineering.
Mauricio Morales Castañeda
graduated from the Technological University of Tlaxcala in 2019 with a degree of Higher University Technician in Maintenance Industrial Area He completed his stay process at Tecnosuelo S.A C. V, is currently studying Industrial Maintenance Engineering at the Technological
University of Tlaxcala.
Rogelio Perea Garcia graduated from the Technological University of Tlaxcala in 2019 with a degree of Higher University Technician in Maintenance Industrial Area He completed his stay process at Grúas Diaz Hnos. S.A C. V, is currently studying Industrial Maintenance Engineering at the Technological University of Tlaxcala.
IJERTV9IS110017 www.ijert.org
Published by : International Journal of Engineering Research & Technology (IJERT)
http://www.ijert.org ISSN: 2278-0181
Vol. 9 Issue 11, November-2020
Luis Orlando Zempoalteca Lima
graduated from the Technological University of Tlaxcala in 2019 with a degree of Higher University Technician in Maintenance Industrial Area He completed his stay process at SAGEMIC S.A.S, is currently studying Industrial Maintenance Engineering at the Technological University of Tlaxcala.
Cesar Vazquez Arenas graduated from the Technological University of Tlaxcala in 2017 with a degree of Higher University Technician in Maintenance Industrial Area he completed his stay process at REMSI, is currently studying Industrial Maintenance Engineering at the Technological University of Tlaxcala.
Edwin Vargas Flores graduated from the Technological University of Tlaxcala in 2019 with a degree of Higher University Technician in Maintenance Industrial Area He completed his stay process at SERVIMECI S.A, is currently studying Industrial Maintenance Engineering at the Technological University of Tlaxcala.
REFERENCES
[2] G.Orozco “Pruebasdel aceroAISI-SAE1018”, Ciencias de la ingeniería y mecánica, 2014.
[3] H. William, “Introducción a Solid Modelado”, Mc Graw Hill, 13 edición, 2017.
[4] I. Sacero “Propiedades mecánicasdeacero 1018”,2010
[5] J.Jiménez,“IntroducciónaSolidworks Simulationyanálisis de elemento finito” DITLAG ingeniería y capacitación, 2018.
[6] R. Hermenegildo “Ensayo de dureza en los materiales”, Ingemecánica, 2018.
[7] W. F. Smith “Fundamentos de la ciencia e ingeniería de materiales”3 edición,1999.
IJERTV9IS110017 www.ijert.org