
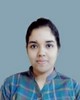
- Open Access
- Authors : Maria S Sebastian , Thahzin Rasha
- Paper ID : IJERTV10IS050043
- Volume & Issue : Volume 10, Issue 05 (May 2021)
- Published (First Online): 12-05-2021
- ISSN (Online) : 2278-0181
- Publisher Name : IJERT
- License:
This work is licensed under a Creative Commons Attribution 4.0 International License
Gyroscopic Transportation Roundabout
Maria S Sebastian, Thahzin Rasha
Civil Engineer
Sahrdaya College of Engineering and Technology Thrissur, India
AbstractOur work is based on the designing of a transportation and traffic system that supports the modern transportation facility like a gyroscope. It consists of lanes arranged around the roundabout for the gyroscope to move in a convenient manner without disturbing the road traffic. The gyroscopes have controllable legs that can raise and lower their height sensing the vehicles ahead and at the back preventing collisions and congestions. Around the roundabout, rails are provided for the wheels of the gyroscope to move.
Gyroscopic transport would see enormous, disk-shaped vehicles swarm through the streets on wheels, elevated above traffic, and overlapping to form multiple layers of travel. The designer argues that his proposed mode of transit would have huge potential to provide an efficient, economical, safe, environmentally friendly, comfortable, and manoeuvrable conveyance that is independent of the general traffic flows on arterial roads, while the mobile pods may seem unsuitable for everyday use, the proposed design is fully functional and is ready to build future cities with them.
This mode of transportation is compatible with the human habitat, with the spaces in which city dwellers recreate. It can pass alongside parks, squares, and pedestrian paths. The vehicles are elevated above traffic, overlapping each other to form multiple layers of travel. It is said that the gyroscopes would be initially powered by flywheels wound up in the morning, and would continue to be powered throughout the day from energy supplied by solar panels mounted on the roofs of the cars.
Pods are stilted on expandable legs that can both contract and enlarge depending on the context, meaning they can pass under bridges and vehicular overpasses with ease. Inside, passengers sit in rows just like they would on a subway or bus, or alternatively ride-in-style inside luxurious pods that include comfortable couches and TV sets.
Keywords Gyroscope; flywheels; mobile pods
-
INTRODUCTION
The paper is based on the design of the transportation system supporting gyroscope. A gyroscope is a vehicle that may come in future. The paper deals with the study of designing a transportation system that supports the gyroscope travelling on rails. The transportation system consists of the following:
-
Transportation planning
-
Geometric design
-
Pavement design
-
Traffic engineering
The paper is of designing a roundabout of gyroscopic rails at the intersection of four four-lane roads. Considering one out of four, the geometric design is to have 4 lanes, two lanes in one direction and two lanes in opposite direction. A rail is provided in between two directions for a gyroscopic vehicle
that moves on legs embedded in rails and the height of legs can be adjusted so that the nearby vehicles are not intersected.
-
-
TRANSPORTATION PLANNING
-
Transportation Survey, Data Collection and Analysis
We are planning to implement a gyroscopic transportation system in our country. Gyroscope is a huge mode of transport that can accommodate a lot of people. India is a highly populated country and this population creates crowd and rush in town areas. This rush can be reduced by providing gyroscope as a public mode of transportation so that the rush on the streets can be reduced. Since the gyroscope is provided with height adjustable legs they can be raised high above the other vehicles without disturbing them. Moreover, gyroscope is more spacious and modern compared to the ordinary public transportation system.
-
Use of Transportation Planning
The design consists of a rotary design. A rotary intersection is a specialized form of intersection-at-grade in which the traffic movies in one direction around a central island. For keep-to-the-left rule, vehicles approaching the intersection are forced to move around the central island in an orderly manner and weave out of the rotary into their respective desired directions.
-
Design elements of a rotary: A number of elements of a rotary are considered herein. The guidelines given are in accordance with the Recommended Practice for Traffic Rotaries, IRC: 65 1976, Indian Roads Congress, New-Delhi, 1976.
-
Design speed: Various elements such as radii and weaving lengths are governed by the design speed. This should be necessarily lower than the design speed of the intersecting highways so as to keep the dimensions within practical limits. The IRC recommended values are 40 km/h in rural areas and 30 km/h in urban areas.
-
Entry radius: This is determined by the design speed, super elevation and coefficient of pavement friction. This should be such as to result in the drivers lowering their speed to the design speed of the rotary.
IRC recommends an entry radius of 20 to 35 m for rural areas and 15 to 25 m for urban rotaries.
-
Exit radius: Delete the author and affiliation lines for the second affiliation. This should be larger than that of the rotary island for the drivers to leave the rotary rapidly. The recommended practice is to keep the exit radius 1.5 to 2 times more than that of the entry radius.
However, the exit radius may be kept similar to the entry radius in case the pedestrian traffic across the exit road is high, in order to limit the exit speed and allow for pedestrian safety.
-
Size of central island: The radius of the central island depends on the design speed of the rotary; theoretically, it
Where,
w = [ (e1 + e2) / 2] +3.5 (1)
should be the same as that of the entry radius. However, in practice, the radius of the central island is kept slightly more than the entry radius; this is meant to slow down the approaching traffic and give a little preference to the traffic already on the rotary.
This purpose is adequately served by making the radius of the central island 1 1/3 times that of the entry curve. (IRC: 651976).
-
Width of carriageway at entry and exit: This depends on the design traffic entering and leaving the intersection. A minimum of 5 m, with provision for extra width due to curvature, is recommended for the entry and exit. The recommendations of IRC are given:
-
Weaving length: The ease with which the traffic can merge and diverge will be dependent on the weaving length. This is decided based on entry width, the width of the weaving section, total traffic volume, and the proportion of weaving traffic in it. If the weaving length is made at least four times the weaving width, direct traffic cuts may be prevented.
Sl. No.
(IRC: 65 1976)
Carriageway width of approach road (m)
Entry radius (m)
Carriageway width of entry and exit (m)
1.
2.
3.
4.
5.
6.
7.
8.
07.0 (2 – lanes)
10.5 (3 – lanes)
14.0 (4 – lanes)
21.0 (6 – lanes)
07.0 (2 – lanes)
10.5 (6 lanes)
14.0 (4 lanes)
21.0 (6 lanes)
2535
1525
6.5
7.0
8.0
13.0
7.0
7.5
10.0
15.0
Sl. No.
(IRC: 65 1976)
Carriageway width of approach road (m)
Entry radius (m)
Carriageway width of entry and exit (m)
1.
2.
3.
4.
5.
6.
7.
8.
07.0 (2 – lanes)
10.5 (3 – lanes)
14.0 (4 – lanes)
21.0 (6 – lanes)
07.0 (2 – lanes)
10.5 (6 lanes)
14.0 (4 lanes)
21.0 (6 lanes)
2535
1525
6.5
7.0
8.0
13.0
7.0
7.5
10.0
15.0
TABLE I. WIDTH OF CARRIAGEWAY AT ENTRY AND EXIT OF A ROTARY
e1 = Entry width in meters
e2 = Width of non-weaving section in meters w = width of weaving section in meters
-
External kerb line: The external kerb line of a weaving section should be normally re-entrant either straight or a large radius curve, similar to exit curves. This tends to eliminate wastage of area near the middle of weaving sections, as it is unlikely to be used by traffic.
-
Sight distance: Stopping sight distance for the adopted design speed should be provided. A rotary should be preferably in a flat area, at any rate not steeper than 4 in 50. Barrier type kerbs are preferred at the outer edges of a rotary to discourage pedestrians from crossing over.
-
Super elevation and camber: The rotary curvature is opposite to that of entry and exit; so, the super-elevations will be opposite to each other. This causes difficulty in high and heavy vehicles. For the least discomfort, the algebraic difference in the cross-slopes should be limited to about 0.07; channelizing islands should be located at the neck. Slight adjustments may be made from the point of view of curvature and speed.
-
-
-
The capacity of a rotary: This is directly dependent on the capacity of each weaving section, which is governed by the geometry of the intersections including entrances and exit, and the percentage of the weaving traffic in relation to the total traffic volume.
-
The Transport and Road Research Laboratory, London, recommends the following formula based on extensive research, which is a modification of the Wardrop formula.
qp = [280w (1+ e/w) (1 p/3)] / (1 + w/l) (2)
Where,
qp = Practical capacity of the weaving section of the rotary (PCU/hour)
w = width of the weaving section in meters (6 to 18m) e = average entry of the rotary in meters
IRC: 65-1976 recommends a minimum weaving length of 45 m for a design speed of 40 km/h and 30 m for 30 km/h.
A maximum limit to weaving length is also considered desirable to discourage speeding near the rotary. For this, twice the above values can be taken to be the upper limits.
-
Entry and exit angles: A desirable value for entry angle is 60°; the exit angles should be small for a smooth exit from the rotary it can be 30° or less.
-
Width of rotary carriageway: Width at entry, the width of non-weaving section and width of the weaving section are the important elements of the rotary carriageway. The width of the non-weaving section should be at least equal to the widest single entry into the rotary. The width of the weaving section should be more than this. The general recommendation (IRC: 65-1976) is-
Fig. 1. Rotary intersections of highways
Where,
p = (b + c) / (a + b + c) (3)
commonly in India.Pavements are a conglomeration of materials.
l = Length of weaving section between the ends of the channelizing islands in meters
p = Proposition of weaving traffic, i.e., ratio of the sum of crossing streams to the total traffic on the weaving section
Fig. 2. Roundabout junction with gyroscopic rails
-
-
GEOMETRIC DESIGN
All geometrical parameters are determined as per IRC. Length of carriageway (overall)
14.30 m 3.5 m per lane x 4 = 14 (4 lanes)
-
30 cm for rails
-
30 cm covering with 10 cm hole in between for the legs of gyroscope and 10 cm covering on each of its sides.
Length of each lane – 3.5 m
Length of rails in middle – 30 cm including 10 cm covering on each side and 10 cm for legs in the middle to go below the ground level.
Length of shoulder – 1.5 m on each side.
Length of footpath provided after a barrier kerb on each side – 1.5m
Type of cross slope – combination of straight and parabolic Type of kerb – barrier (20 cm high)
Design of rotary intersection:
-
Since gyroscopes are designed at urban areas, design speed=30 km/h
-
Entry radius=20
-
Exit radius=35m
-
Weaving length=30 m
-
Entry angle=60 degree
-
Exit angle=30 degree
-
-
PAVEMENT DESIGN
Flexible bituminous roads are provided for the pavements around gyroscopic rails. They are more flexible and take up loads satisfactorily. It is more economical and used
Fig. 3. Cross section of pavement around gyroscopic rail
-
Subgrade Soil
Soil is an accumulation or deposit of earth material, derived naturally from the disintegration of rocks or decay of vegetation, that can be excavated readily with power equipment in the field or disintegrated by gentle mechanical means in the laboratory. The supporting soil beneath the pavement and its special under courses are called subgrade. Undisturbed soil beneath the pavement is called natural subgrade. Compacted subgrade is the soil compacted by the controlled movement of heavy compactors.
Desirable properties:
The desirable properties of subgrade soil as a highway material are
-
Stability
-
Incompressibility
-
Permanency of strength
-
Minimum changes in volume and stability under adverse conditions of weather and groundwater
-
Good drainage, and
-
Ease of compaction
The tests used to evaluate the strength properties of soils may be broadly divided into three groups:
-
Shear tests
-
Bearing tests
-
Penetration tests
-
-
Sub-base Course
A slab on ground and pavements normally are designed to be supported by a solid sub base, which needs to be uniform by nature to support the structure above it. A sub base will go on top of the subgrade, which typically is native soil or improved soil that has been compacted. It is important for a sub base to have solid edges and joints to prevent cracking and concrete spalling.
Sub-base Layer Advantages:
-
Provide strength and support to the overlying pavement
-
Provide drainage and frost protection
-
Prevent settlements to pavement and slab on grade
-
Be reusable if you decide to change your pavement surface
-
Keep workers out the mud
-
Create a workable surface prior to the placing of the finished pavement
-
Reduce construction costs
Some of the most used subbase materials include:
-
Recycled concrete
-
Granular fill
-
Manufactured aggregate
-
Crushed rock
-
Lean concrete
-
Recycled materials, such as crushed concrete or brick
-
-
Base Course
Aggregate base (AB) is typically made of a recipe of mixing different sizes of crushed rock together forming the aggregate which has certain desirable properties. 20 mm or 34 in Aggregate Base, Class 2, is used in roadways and is an aggregate made of a specific recipe of different sizes and quality of rock inclusive of 20 mm (34 in) to fine dust. An aggregate is normally made from newly quarried rock, or it is sometimes allowed to be made from recycled asphalt concrete and/or Portland cement concrete. The base course or base course in pavements is a layer of material in an asphalt roadway, race track, riding arena, or sporting field. It is located under the surface layer consisting of the wearing course and sometimes an extra binder course.
<>If there is a sub-base course, the base course is constructed directly above this layer. Otherwise, it is built directly on top of the subgrade. Typical base course thickness ranges from
100 to 150 millimetres (4 to 6 in) and is governed by underlying layer properties. Generally consisting of a specific type of construction aggregate, it is placed by means of attentive spreading and compacting to a minimum of 95% relative compaction, thus providing the stable foundation needed to support either additional layers of aggregates or the placement of an asphalt concrete wearing course which is applied directly on top of the base course.
-
Binder Course
This layer provides the bulk of the asphalt concrete structure. Its chief purpose is to distribute the load to the base course The binder course generally consists of aggregates
having less asphalt and doesn't require quality as high as the surface course, so replacing a part of the surface course by the binder course results in a more economical design.
-
Surface Course
Surface course is the layer directly in contact with traffic loads and generally contains superior quality materials. They are usually constructed with dense graded asphalt concrete(AC). The functions and requirements of this layer are:
-
It provides characteristics such as friction, smoothness, drainage, etc. Also, it will prevent the entrance of excessive quantities of surface water into the underlying base, sub-base and sub-grade.
-
It must be tough to resist the distortion under traffic and provide a smooth and skid-resistant riding surface.
-
It must be waterproof to protect the entire base and sub-grade from the weakening effect of water.
-
-
Seal coat: Seal coat is a thin surface treatment used to water-proof the surface and to provide skid resistance.
-
Tackcoat: Tack coat is a very light application of asphalt, usually, asphalt emulsion diluted with water. It provides proper bonding between two layers of binder course and must be thin, uniformly cover the entire surface, and set very fast.
-
Prime coat: Prime coat is an application of low viscous cutback bitumen to an absorbent surface like granular bases on which binder layer is placed. It provides bonding between two layers. Unlike tack coat, prime coat penetrates into the layer below, plugs the voids, and forms a watertight surface.
REFERENCES
-
Vittorio M. N. Passaro , Antonello Cuccovillo, Lorenzo Vaiani, Martino De Carlo and Carlo Edoardo Campanella, Gyroscope Technology and Applications: A Review in the Industrial Perspective, Sensors, Italy, pp. 4-20, April 2021.
-
Indian Road Congress, Guidelines for Planning and Design of Roundabouts (First Revision), IRC:65-2017, April 2021