
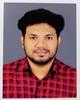
- Open Access
- Authors : Sangeeth Sulphi
- Paper ID : IJERTV10IS050413
- Volume & Issue : Volume 10, Issue 05 (May 2021)
- Published (First Online): 04-06-2021
- ISSN (Online) : 2278-0181
- Publisher Name : IJERT
- License:
This work is licensed under a Creative Commons Attribution 4.0 International License
Finite Element Assessment of Crack Potency in Deep Beams with Varying Shear Span to Depth Ratio and Location of Opening
Sangeeth Sulphi
M-tech in structural Engineering Kollam, India
Abstract Cracks in concrete beams are due to an increase in shear stress appearing near the support such as wall or column. These cracks are called shear crack and are inclined at 45 degrees with the horizontal. These cracks in beams can be avoided by providing additional shear reinforcements near the support where the shear stress is maximum. Deep beams are structural elements loaded as simple beams in which a significant amount of the load is carried to the supports by a compression force combining the load and the reaction. As a result, the strain distribution is no longer considered linear, and the shear deformations become significant when compared to pure flexure. Deep beam is a beam having large depth/thickness ratio and shear span depth ratio less than 2.5 for concentrated load and less than 5.0 for distributed load. The study intended to investigate the crack development, propagation, and merging behaviour of critical shear cracks. For this, certain parameters like shear span to depth ratio, location of opening (if provided), presence of skin reinforcement and shear reinforcement should be varied. For the purpose of analysing crack concentration in deep beam, ABAQUS Finite element Analysis software is suited.
Keywords Reinforced Concrete Deep Beam, Crack potency, Shear span to depth ratio, stiffened opening, ABAQUS
-
INTRODUCTION
becomes different than the conventional beam which intern makes the load transfer mechanism through these beams altogether different. Such a beam is also referred to as a Deep Beam (transfer beam).
As per code provisions given by Bureau of Indian Standards, a beam shall be considered as deep beam when the ratio of effective span to overall depth ratio is less than 2.0 for simply supported beam and 2.5 for continuous beams. Theory of simple bending criteria is not applicable in case of deep beams and they must be designed by considering non-linear stress distribution along the depth of the member because deep Beams possess two- dimensional action in compared with conventional beams and the assumption where the plane section remains plane before and after bending is not applicable as the strain is not distributed linearly. The applied pressure will have more effect on the stress rather than strain, also shear deformation in normal beams can be neglected but in deep beams, the failure is mainly due to shear which cannot be neglected. Due to larger depths, like in traditional method stress is not linear in elastic stage and the parabolic shape at ultimate stress is not achieved which is also a major reason for shear failure in deep beams. Many Researchers in the past had done research on shear strength parameter in deep beams since shear failure is the primary concern
-
General
High-rise buildings are characterized by their high susceptibility to lateral drift under the effects of lateral loads such as wind and earthquake loads. Therefore, in order to achieve architectural and functional requirements of large column-free space in high-rise buildings, the RC columns are placed at the periphery of the built-up plan area. With a view to develop high flexural and torsional stiffness, these columns are very closely spaced and interconnected through very stiff beams, called as Spandrel beams. These closely spaced columns at the periphery, however, pose hindrance to the free flow of people and goods at the ground floor and basement levels. To fulfil this requirement, the columns at these floor levels have to be placed at larger spacing. As a result, an interface has to be provided between the closely spaced columns of upper floors and the widely spaced columns at the ground/basement floor level. This interface has to be a horizontal RC element and hence is referred to as Beam. Conventionally, a beam is a flexural member of a structural system. The above-mentioned interface beam, however, does not behave as a flexural member since it gets sandwiched between closely spaced upper columns and a little widely spaced supporting columns below it. Also, to transfer the high magnitude of loads collected from all the upper floors of a high-rise building, the depth of the interface beams has to be kept much higher than the conventional beams, ranging from 1 m to 4.5 m. As a result of this, span to depth ratio of such beams
Figure 1.1: Typical deep beam (transfer beam) [42]
Reinforced concrete deep beams are more utilitarian for structural applications such as pile- caps, water tanks and tall buildings. Because of their proportion they develop mechanism of force transfer quite different from that in slender beams and their strength is likely to be controlled by shear rather than flexure provided with nominal amount of longitudinal reinforcement. Deep Beams are used for the structure where there are no intermediate columns and for long spans. In bridges, deep beams are used as girders to support the carriageway. Deep Beams are also used in RCC water tanks as side walls and Pile
foundation they are used as connections for pile caps. Types of deep beams may be classified as Simply Supported Deep Beams, Continuous Deep Beam & Deep Beams with and without opening. Variety of application for Deep beam is found that can be used in situations where other type of beams or structural components cannot be used such as in bridges where long spans are required. In large halls or building where no column is to be used. R. C. C. side walls of water tank may act as deep beams. Pile caps can also act as deep beams in case of smaller spans. Raft foundation may contain deep beams in some cases. Bunkers and Silos of such structures may act as deep beam.
Figure 1.2: Deep beams in bridge [41]
-
Behaviour of Deep beams
Early analysis of reinforced concrete deep beams was based on the classical theory of elasticity with the beam assumed as homogenous. Reinforcement was placed in regions where tensile stresses exceed the estimated strength of the concrete. The elastic approach, which is applicable for conventional beams, did not adequately describe the stress distributions of deep beams. An actual stress exceeds theoretical stresses of the sections near supports, and theoretical stresses exceeded actual stresses at sections near the centre of the span.
In deep beams subjected to concentrated loads, the distribution of principal tension and compression stresses is as shown in Figure 1.3, where the compression stresses at the centre of line joining load with support are approximately in the same direction of this line while the tension stresses are perpendicular to this line
Figure 1.3: Principle stress trajectories in deep beams [3]
In the middle of beam span, the bottom face is subjected to pure tension stresses while the top face is subjected to pure compression stresses. The cracks appear in direction normal to the tensile stress trajectories. As the load increases, the cracks widen and propagate and more cracks open. Because the shear span is small, the compressive stresses at the support region affect the magnitude and direction of the principal tensile stresses. Therefore, the crack pattern of a deep beam is totally different from that of a conventional beam.
There are many factors that could influence the shear strength of a deep beam, specifically method of load application, shear span to depth ratio, length to depth ratio, tension reinforcement, size effect, location of openings (if proided), compressive strength, aggregate interlock and side cover. The present study focusses on the numerical analysis of impact of variation of three of the above mentioned parameters namely, method of load application, shear span to depth ratio and location of openings in deep beams. Furthermore, with the objective, as a safeguard to reduce the intensity of crack concentration around the opening, an internal strengthening of opening has been done by the provision of circular steel plates around the opening. The proposed software used is ABAQUS
6.14 and the types of analysis are Dynamic Explicit Analysis, Modal Analysis and Static Non-Linear Analysis.
-
Direct and Indirect loading
-
ANALYSIS
The crack analysis in a deep beam is indispensable to clarify the various mechanisms by which cracks occur and evaluate the damaging effects that these cracks inflict on the corresponding models. In this study, the following types of cracks and their concentration has been analysed.
-
Tensile cracks
-
Compressive cracks
-
Maximum principle plastic strain (shear cracks)
-
-
Dynamic Explicit Analysis
Dynamic Explicit Analysis is computationally efficient for the analysis of large models with relatively short dynamic response times and for the analysis of extremely discontinuous events or process. The analysis allows for the definition of very general contact conditions and uses a consistent, large deformation theory- strains and rotations are assumed to be small
-
Modal Analysis
Modal Analysis is the study of the dynamic properties of systems in the frequency domain. The approach uses the overall mass and stiffness of a structure to find the various periods at which it will naturally resonate. The study actually assists this analysis to employ the validity of the result from Dynamic Explicit Analysis. The cracked and uncracked frequency of the models are analysed to check the intensity of crack concentration, as crack pattern depends on the extension of variation of cracked frequency from uncracked frequency. Higher the difference between the frequencies, higher will be the crack pattern.
-
Static No- Linear Analysis
There is a non-linearity of strain distribution inside deep beams, and the corresponding analysis have been done in the study to
check that non linear relation between the applied load and displacement. The final output of the analysis is the force displacement curve and if it shows sudden rise and fall in the curve, it states that the corresponding model is liable to high distortion thereby cracking.
1.5 Scope of the present study
Modelling and analysis of deep beam models with varying shear span to depth ratio and varying locations of opening in the web of the beam, subjected to Direct loading and Indirect loading by using the software ABAQUS 6.14 and determination of their crack concentration effects. Determination of the most economic model from the above-mentioned parameter analysis. Finally, reduction of crack concentration around the openings through internal strengthening by using circular steel plates.
-
-
LITERATURE REVIEW
2.1 General
Any structural member is designed based on the major criteria like safety & serviceability conditions where the ultimate load and its corresponding deflections are the main constraints. Beams are designed to transfer loads from slabs to columns where deep beams appear in the case of longer spans. Theory of simple bending criteria is not applicable in case of deep beams and they must be designed by considering non-linear stress distribution along the depth of the member. Many Researchers in the past had done research on shear strength parameter in deep beams since shear failure is the primary concern. Deep Beams possess two-dimensional action in compared with normal beams and the assumption where the plane section remains plane before and after bending is not applicable as the strain is not distributed linearly. The applied pressure will have more effect on the stress rather than strain, also shear deformation in normal beams can be neglected but in deep beams, the failure is mainly due to shear which cannot be neglected. Due to larger depths, like in traditional method stress is not linear in elastic stage and the parabolic shape at ultimate stress is not achieved which is also a major reason for shear failure in deep beams.
Deep Beams are used for the structure where there are no intermediate columns and for long spans. In bridges, deep beams are used as girders to support the carriageway. Deep Beams are also used in RCC water tanks as side walls and Pile foundation they are used as connections for pile caps. Deep beams are those whose depth is more when compared to the normally used beams, but they are categorized based on their shear span to depth ratio. Shear forces in beams are caused when the applied momentum changes along its length, thus shear cracks would propagate in the shear span region. Deep beams normally fail in shear. Shear tension failure occurring due to the loss of the bond strength in flexural reinforcement caused by the horizontal cracks and shear compression failure occurring due to crushing of concrete at the point of application of the load. This shear failure is fragile in nature and results in sudden damage or collapse.
Jun hong Zhang, Shusa Lang (2020), Experimental study of shear capacity of high strengthened reinforced concrete deep beams with small shear span depth ratio: This study aimed to investigate the shear capacity performance for eight deep beams with HTRB600 reinforced high strength concrete under concentrated load to enable a better understanding of the effects of shear spandepth ratio, longitudinal reinforcement ratio, vertical stirrup ratio and in order to improve design procedures.
The dimension of eight test specimens is 1600 mm x 200 mm x 600 mm. The effective span to height ratio is 2.0, the shear span depth ratio is 0.3,0.6 and 0.9 respectively. In addition, the longitudinal reinforcement ratio is set to 0.67%, 1.05%, 1.27%, and the vertical stirrup ratio is taken to be 0%, 0.25%, 0.33%, 0.5%. Through measuring the strain of steel bar, the strain of concrete and the deflection of mid-span, the characteristics of the full process of shear capacity, the failure mode and the load deflection deformation curve were examined. The test results showed that the failure mode of deep beams with small shear spandepth ratio is diagonal compression failure, which is influenced by the layout and quantity of web reinforcement. The diagonal compression failure could be classified into two forms: crushing-strut and diagonal splitting. With decreasing of shear spandepth ratio and increasing longitudinal reinforcement ratio, the shear capacity of deep beams increases obviously, while the influence of vertical web reinforcement ratio on shear capacity is negligible. Finally, the shear capacity of eight deep beams based on GB 50010-2010 is calculated and compared with the calculation results of ACI 318-14, EN 1992-1-1:2004 and CSA A23.3-04, which are based on strut-and-tie model. The obtained results in this paper show a very good agreement with GB50010-2010 and ACI 318-14, while the results of EN 1992- 1-1:2004 and CSA A23.3-04 are approved to be conservative.
Hassen Falah Hassen, Yaarub Gatna Abtan (2020), A review of behaviour of reinforced concrete deep beams with shear: Reinforced concrete deep beams are structural members having depth much greater than normal in relation to their span, while the thickness in the perpendicular direction is much smaller than either span or depth. The strength of deep beams is usually controlled by shear, rather than flexure. In this study, the previous researches related to reinforced concrete deep beams will be reviewed. These researches approximately started in the second half of the past century. Large numbers of researchers studied the behaviou of concrete deep beams and the determination of their capacity. Some of these researches are experimental investigations carried out by testing a number of deep beams with variation in some parameters, while the others are theoretical to estimate deep beam capacity by developing some theories and suggestion of equations for calculating its capacity and comparisons were made with those adopted by some codes. Because of the large number of these researches, their review requires large part of this study, and because the prior studies elaborately reviewed the pioneer researches, only the researches made since year 2000 will be reviewed in this study.
G Harsha, P Polu Raju (2019), Shear strength of deep beams: A comprehensive literature study has been reviewed on shear strength of deep beams. The shear behaviour of deep beams must be understood by varying various parameters such as web reinforcement, shear span to depth ratio, size of the beam, depth of the beam, vertical reinforcement, side face reinforcement, percentage of reinforcement, Crack width criteria, Shear span deflection. Comparison of various international codes for the design of reinforced concrete deep beam is reviewed. This study provides preliminary support for proposing a new shear strengthening technique during the design of the member. Any structural member is designed based on the major criteria like safety & serviceability conditions where the ultimate load and its corresponding deflections are the main constraints. Beams are designed to transfer loads from slabs to columns where deep beams appear in the case of longer spans.
Theory of simple bending criteria is not applicable in case of deep beams and they must be designed by considering non- linear stress distribution along the depth of the member. Many Researchers in the past had done research on shear strength parameter in deep beams since shear failure is the primary concern.
Sayed H Sayed, Ahmed M Mostafa (2018), Effect of loading and supporting area on shear strength and size effect of concrete deep beams: A theoretical and an experimental program consisting of nine concrete deep beams specimens were carried out to investigate the effect of loading and supporting area on shear strength and size effect phenomenon of concrete deep beams. As shear strength rather than flexural usually dominates the strength of deep beams, and size effect phenomenon typically represented by reduction in shear strength as beam depth increases, its of a great importance to understand the shear behavior of such elements. It is generally agreed that whatever controls the strength of the diagonal strut governs the strength of the deep beam. As one of the main factors affecting the strut strength, loading and supporting area will be the focus of this research. Thought the research evidence will be provided that by proper configuration of loading and supporting areas, shear strength of concrete deep beams can be increased, and size effect phenomenon can be mitigated.
Mahar A Adam, Mohammed Sayid (2016), Shear performance of fibre reinforced self-compacting concrete deep beams: The self-compacting concrete (SCC) is the newest innovating category of high performance concrete. The shear behaviour of Fibre Reinforced Self-Compacted Concrete (FRSCC) deep beams was investigated. The experimental program consisted of twelve simply supported beams tested up to failure under four-point load. The key parameters covered in this investigation were steel fibres ratios (0.0, 0.50, 0.75 & 1.00%) and the effective shear span to depth ratio that varied from 0.6 to 1.0. Also, the main flexure reinforcement ratio was variable (1.0, 1.60 and 2.20 percent). In addition, vertical and horizontal web reinforcement effect was investigated. The mid- span deflection, cracks, reinforcement and concrete strains of the tested beams were recorded and compared. Test results pointed out that the steel fibres enhanced the cracking load, ultimate capacity, displacement and energy absorption of the tested FRSCC deep beams. The utmost enhancement in the performance of deep beams was achieved with steel fibres content of 1.0% within the range of the test parameters. The enhancement in the ultimate capacity was 40%. The test results indicated that both vertical and horizontal web reinforcement are efficient in shear capacity enhancement of FRSCC deep beams. The ultimate shear capacity was increased by about 47% with increasing the longitudinal steel ratio from 1.0% to 2.2%. Maximum strain in the extreme compression fires of concrete section was 0.0019 and achieved at specimen tested at a/d ratio of 0.6. A non-linear finite element analysis (NLFEA) model was constructed to simulate the shear behaviour of tested beams, in terms of crack pattern and load deflection behaviour. It can be concluded that a good agreement between the experimental and numerical results was achieved. The ratio of the predicted to the experimental ultimate strength ranged between 0.98 and 1.04.
Abhijith Pabale, A J Mehatra (2015), Evaluation of effectiveness of deep beams in shear: The rapid ascent of fibre reinforced concrete to the main stream construction material has been spectacular and paralleled by no other construction material. In spite of coming a long way, there still exist a number
of areas where fibre reinforcement has shown promise but an extensive use has not been transpired. One of such areas is Structural Concrete. Deep beam is such a structural element whose span to depth ratio is comparatively very small. They are often used as transfer girders in tall buildings, long span construction etc. which may catastrophically fail in shear. Behaviour of normal reinforced concrete deep beams and steel fibre reinforced concrete deep beams subjected to predominant shear with or without stirrups and web reinforcement is presented to evaluate the effectiveness of steel fibres in deep beams. The review of research work shows that the inclusion of steel fibres in reinforced concrete deep beams result in enhancing their deformation characteristics at all stages of loading up to failure as well as improving their shear resistance. Therefore, the use of steel fibres is an attractive alternative to test for deep beams for different parameters.
Leon raj, G Appa Rao (2014), Shear strength of deep beam panels: Behaviour of RC beam panels is influenced by several factors. An alternative for conventional beam is 3D steel wire precast panel to behave as deep beam in various locations of RC building systems. Understanding the influence of factors involved on behaviour and strength is needed. The factors to be discussed include; compressive strength of concrete, percentage of tension reinforcement, quantity and distribution of vertical and horizontal web reinforcement, aggregate interlock, shear span-to-depth ratio, distribution of loading, side cover, and depth of beam. The influence of above parameters on the shear strength of reinforced concrete deep beams has been reviewed. A major challenge in every tall building construction is to achieve adequate column free space in the lowermost storey either for parking or storage facility. To achieve sufficient dwelling room size as per architectural design in the upper stories, vertical element so-called floating column is endowed. Its terminal level rests on the transfer girder which acts as a point load. In view of ample shear strength, deep beams are primarily recommended as transfer girders. These members transfer loads through loading face to supports in the transverse direction. The deep horizontal members predominantly fail in shear rather than flexure. These beams are characterized with small span-to-depth ratio. Pile caps, corbel, brackets, foundation walls and off-shore structures are few examples of RC deep beams.
Wael Kasseem (2014), Shear strength of deep beams with mathematical modelling and design formula: A proposal for estimating the shear capacity of reinforced concrete deep beams is presented in this paper. The proposed model is based on the fixed-ngle softened truss model and utilizes a newly proposed formula for the effective transverse compressive stress acting on the beam web. The proposed formula is developed using a stepwise multiple linear regression analysis of the reported shear capacity values of 445 experimental deep beams. The validity of the mathematical model is examined by comparing its response with the experimental results as well as predictions of other formulas available in the literature, and it results as the one best fitting the measured shear strengths. The mathematical model leads to an explicit single closed-form expression for computing the shear strength of deep beams. The proposed expression is dimensionless and contains four variables that express the horizontal and vertical reinforcement ratios, the concrete strength, and the shear span ratio. On the basis of results of this paper, a design formula is proposed with predictions more consistent and reliable than the ACI Code and Eurocode.
Reza Aghayari, Ali Reza Rahai (2011), Investigation on experimental and analytical shear strength of reinforced concrete deep beams: An experimental-analytical investigation was conducted to study the behaviour of high-strength RC deep beams; a total of sixteen reinforced concrete deep beams with compressive strength in range of 59 MPa-65 MPa were tested under two-point top loading. The shear span-to-effective depth ratio a/d was 1.10; all the specimens were simply supported and reinforced by vertical, horizontal and orthogonal steel bars in various arrangements. The test specimens were composed of five series based on their arrangement of shear reinforcing. The general behaviour of tested beams was investigated. Observations were made on mid-span and loading point deflections, cracks form, failure modes and shear strengths. The test results indicated that both vertical and horizontal web reinforcement are efficient in shear capacity of deep beams, also the orthogonal shear reinforcement was the most efficient when placed perpendicular to major axis of diagonal crack. Concentrating of shear reinforcement within middle region of shear span can improve the ultimate shear strength of deep beam. The test results were then compared with the predicted ultimate strengths using the ACI 318-08 provisions; ACI code tended to either unsafe or scattered results. The performed investigations deduced that the ACI code provisions need to be revised.
Ir. R. Sarkhosh, Ir. J. A. den uijl (2010), Shear capacity of concrete beams without shear reinforcement under sustained loads: When a concrete beam is under sustained high loads, a flexural cracking pattern appears along the span. Here, various shear-carrying mechanisms may be developed by a beam, e.g. aggregate-interlock and dowel action. These mechanisms induce tensile stresses in concrete near the crack tip and at the level of the reinforcement. Once the tensile strength of the concrete in these regions is reached, the existing flexural cracks progress in a diagonal direction or new ones are created. The development of the critical shear crack, however, does not necessarily imply the collapse of the member but in case of sustained high loads, the crack width and therefore the crack length will be increased. The aim of this research is to predict the time-dependent mechanical behaviour of cracked concrete beams subjected to sustained shear loads. The results should enable the designer to quantify the failure load (ULS) and deformations and the propagation of the cracks (SLS) of beams under sustained shear loads.
S K Madan, G Rajesh Kumar (2007), Steel fibres as web reinforcement for RCC deep beams in shear: Test data are presented on the shear strength of a series of reinforced cement concrete (RCC) deep beams with three steel fibre volume fractions (0, 1.0 and 1.25%), three shear span to effective depth ratios (0.75, 1.0 and 1.25) and three combinations of web reinforcement. A total of 18 beams were tested to failure under two-point top loading. The test results indicate that the fibres have significant influence on the shear strength of a longitudinally reinforced concrete beams. Shear strength increases with increasing fibre volume and decreasing shear span to-effective depth ratio. Steel fibres can replace the conventional web reinforcement in RCC deep beams. The theoretical prediction of ultimate shear strength on the basis of methods used in the study gives results close to the observed values in most of the beams tested. Maximum increase of 56 percent in first cracking load for beam containing 1.25 percent of fibres was observed when compared with beam containing no web reinforcement. Also for all with steel fibres followed by
beams containing web reinforcement. These results support the use of steel fibres as an alternative to conventional web reinforcement is deep beams.
-
Summary
Generally, Reinforced concrete (RC) deep beams are common structural elements that are often appear in pile caps, tanks, folded plates, foundation walls, bins, folded plate roof structures and offshore structures as well as in tall buildings as transfer girders. They are identified as being relatively short and deep, having a thickness that is small relative to their span or depth. Due to the relatively small value of span-to-depth ratio, a complex state of strain is developed in deep beams and hence traditional sectional design approaches that are based on the plane sections theory are violated and unsuitable for their design. The ultimate strength and diagonal cracking capacity of deep beams are not significantly influenced by span to depth ratio (L/d). Where the ultimate shear strength is slightly decreases with increasing (L/d) ratio. The ultimate strength and diagonal cracking capacity are significantly influenced by shear span to depth ratio (s/d) which is considered as one of the important parameters that govern failure of deep beams by shear mode or flexural mode. The increase in this ratio decreases the deep beam shear capacity. The concrete compressive strength has a significant influence on shear capacity of deep beams whereas the behaviour of them does not much differ when using high strength concrete from using normal strength concrete. The presence of openings in deep beams negatively affects their shear capacity especially when these openings are close to the strut region that joins between the load and support positions. The vertical shear reinforcement has a significant effect on shear capacity of deep beams, while the horizontal reinforcement has little effect on it especially when the value of (s/d) is large. The strength of beams with 250 mm shear span is less than that of 200 mm shear span. It is clear from these results that the strength of deep beam is inversely proportional to the shear span for the constant depth of the beam. Shear strength increases with fibre content and decreasing s/d ratio. Maximum increase in first cracking load for beam containing minute percentage of fibre was observed when compared with beam containing no web reinforcement.
Diagonal Tensile Stresses will increase rapidly if proper care is not taken for the stresses criteria while designing the beam. Major Failure is diagonal cracking in Deep Beams, with the increase in span to depth ratio, the inclination of cracks increases. The portions of uncracked concrete depth resist the shear stress and the transfer of shear at cracked portion is negligible. Concentrating of shear reinforcement within middle region of shear span can improve the ultimate shear strength of deep beam. Shear strength decreases with the increase in the depth of the beam.
-
-
OBJECTIVES The objectives of the present study are:
-
To study different parameters causing crack concentration in deep beams
-
To model and analyse the effect of shear crack concentration in deep beam models
-
To determine the optimized model with most economic shear span to depth ratio and location of opening
-
To model and assess the internal strengthening of openings provided in the deep beams through the provision of circular steel plates
-
To model and assess the substitution of 3D panels and steel fibres as web reinforcement in deep beams
-
-
METHODOLOGY
-
Studying the literature reviews for understanding the concept
-
Choosing the software and its validation
-
Assigning material properties and modelling the deep beam models in ABAQUS 6.14
-
Analysis of the proposed models based on their:
-
Dynamic response- Dynamic Explicit Analysis
-
Frequency modes- Modal Analysis
-
Static response- Static Non-linear Analysis
-
-
Observation of results and discussions
-
-
VALIDATION
5.2.1 Material properties
Concrete (M25) and steel (Fe415) are the most basic components used for the construction of a typical deep beam. Here the model is assigned with the following material properties.
Table 5.1: Concrete and rebar details [1]
Material properties
Density (kg/m³)
Youngs modulus of elasticity (MPa)
Poisons ratio
Concrete
2548.538
25000
0.20
Rebar
7849.047
200000
0.30
-
General
Software Validation is a process of evaluating software product, so as to ensure that the software meets the pre-defined and specified business requirements as well as the end users/customers' demands and expectations. It is also defined as the process of checking or proving the validity or accuracy of something.
-
Numerical analysis
In order to determine the maximum displacement of the deep beam model, the following properties and load conditions are assigned:
-
The length of the beam is 10m
-
The width and depth of the cross section is 1m × 1m
-
A load of 400 KN is imparted at the centre span of the beam as shown in the figure 5.1
Figure 5.1: Model inputs
Table 5.2: Section details of model [1]
Width
1000 mm
Xu max/d
0.479
Minimum depth
452 mm
Clear cover
20 mm
Minimum total depth
500 mm
Total depth
1000 mm
Effective depth
952 mm
Factored shear
325 KN
Normal shear stress
0.341 MPa
Permissible shear stress
3.1 MPa
Concrete shear strength
0.406 MPa
Stirrup diameter
10 mm
Minimum spacing
100 mm
Maximum spacing
300 mm
Provided spacing
140 mm
Factored shear
325 KN
Normal shear stress
0.341 MPa
Permissible shear stress
3.1 MPa
Concrete shear strength
0.406 MPa
Stirrup diameter
10 mm
Minimum spacing
100 mm
Maximum spacing
300 mm
Provided spacing
140 mm
Table 5.3: Main bar details [1]
Tensile strength
0.781 MPa
Area of steel required
2140 mm2
Minimum area of steel
1950 mm2
Area of steel provided
3054 mm2
Main bar diameter
36 mm
Bars required
3
Clear spacing
416 mm
Tensile strength
0.781 MPa
Area of steel required
2140 mm2
Minimum area of steel
1950 mm2
Area of steel provided
3054 mm2
Main bar diameter
36 mm
Bars required
3
Clear spacing
416 mm
Table 5.4: Stirrup bar details [1]
:
Figure 5.2: Reinforcement details in the model
Figure 5.3: Deep beam model
Figure 5.4: Meshing of deep beam model
Figure 5.5: Assigning loading and support conditions
Figure 5.6: Displacement shown in ABAQUS (2-D view)
Figure 5.7: Displacement shown in ABAQUS (3-D view)
-
-
Analytical method
The maximum displacement of a deep beam is given by
Where, W is the load applied on the deep beam (400 KN) L is the length of the deep beam (10 m)
E is the modulus of elasticity (25000 MPa) I is the moment of inertia (8.33×1010 mm4)
The maximum displacement, max = 1.004 mm
-
Comparison of result
Table 5.5 shows the results obtained from both numerical method and analytical method. Comparing the manual and software results, almost same results were obtained, the software value is 0.49% higher than analytical method. According to
Abaqus manual, the maximum percentage of variation is limited up to 10%. Hence the value is less than 10%, the software was validated.
Parameter
Analytical method
Numerical method
Percentage of error
Maximum displacement
1.004 mm
1.009 mm
0.49 %
Table 5.5: Comparison of numerical and analytical results
-
-
MODELLING
-
Model details
An eight node linear brick, reduced integration, hourglass control, solid homogenous element is used to model beam. Two node linear displacement element is used to model rebars. A discrete rigid element is used to model bearing plates and loading plates. General contact is done for all exterior faces, feature edges, beam segments and analytical rigid surfaces. Penalty method, rather known as penetration method is used for friction, which permits only some relative motion of the surfaces
Figure 6.1: Deep beam model with supporting and bearing plate
Figure 6.2: Provision of horizontal reinforcement and stirrups in the model
Figure 6.3: Rebars embedded in the model
-
Characteristics assigned to the model
The following characteristics/features have been assigned to the proposed models to know whether the crack concentration can be reduced:
-
Method of load application
Load may be applied to beams on the extreme compression or tension fibres. The main effect of applying loads on the compression face to a deep beam without web reinforcement is to increase the ultimate shear capacity above the shear causing inclined cracking. Two loading cases are encountered by simply supported deep beams, namely, direct and indirect loading. External loads are applied perpendicular to the surface of a member in the direction of the member centroid (for example, traffic load acting to deck units). External loads are applied to the sides of members and away from the centroid, as denoted by the headstocks that support beams on the side faces of nibs. Deep RC beams have been widely used in high-rise buildings as load- distributing structural parts of transfer girders, wall footing, foundaton pile caps, floor diaphragms, and shear walls, among others. Nonetheless, the performance of indirectly loaded deep RC beams is rarely investigated. External loads are generally, placed via shear brackets on the sides of the beams. Crack widths and deflections are more rarely encountered in direct loading than in indirect loading. Moreover, these widths and deflections are more often experienced during indirectly loading near the bottom than near the top. Beams with web reinforcement generally exhibited narrow cracks, as well as few deflections and mild tensile steel strain.
Figure 6.4: Indirect and Direct loading [6]
-
Shear span to depth ratio
Shear span is the distance from the point of application of concentrated load to its respective reaction forces. Shear span to depth ratio is the ratio of the span length to its depth (vertical height). The shear failure of a concrete beam is greatly influenced by shear span to depth ratio. When s/d ratio is between 1-2.5, under this load condition, flexural cracks develops and propagate in the compression zone. This behaviour extends towards the tension reinforcement and propagate along the reinforcement. The eventual failure will be due to the anchorage failure of tension reinforcement. Failure can also take place due to crushing of concrete in the compression zone adjacent to point load. When s/d ratio is between 2.5-6, in the initial stage, few flexural cracks with high shear cracks propagate towards compression zone. Therefore, openings should be given, without interrupting the force path.
Table 6.1: Effect of Shear span to depth ratio
s/d = 1-2.5
Compression failure
s/d = 1-2.5
Tension failure
s/d = 2.5-6
Diagonal shear failure
In the present study, the shear span to depth ratio has been given in four varying manner, that is:
s/d= 1
s/d= 2
s/d= 3
s/d= 4
Figure 6.5: Deep beam models with varying shear span to depth ratios
-
Location of openings in web
Openings are inevitably installed in deep beams to create conduits for civil plants like air conditioning, electricity or a computer network. Openings are generally provided in web of the deep beam. Accommodation of such openings cause reduction in beam strength, stiffness and causes excessive deflection and cracking. Location of openings play a vital role in the design of deep beams with openings. When the opening is placed within the interior shear span, the highest load capacity reduction takes place. In the present study, three different
locations of opening have been given for the models and they are at the midpoint (5m from the edge), in between the mid-point (2.5m from the edge) and closer to the edge (0.5m from the edge).
5m from edge
2.5 from edge
0.5m from edge
Figure 6.6: Deep beam model with varying location of openings
-
Internal strengthening of openings through circular steel plates
-
Several techniques for internal strengthening are available now a days, like lamination of fibre reinforced polymer sheets, circular steel plating etc. In the present study, the circular steel plate is used for the internal strengthening of openings. Steel frame box or steel circular ring created by welded bent plates was under compression and confinement to the surrounding concrete. The technique of internal strengthening of openings by using steel plates gave a noteworthy increase in the ultimate shear strength by 9-11%. With the steel plate provision, the main diagonal shear cracks have not passed through the openings, but around them. Thus, the interruption degree on the inclined compressive strut remains undisturbed. Solid homogeneous discrete element is used to model the circular steel plate.
Figure 6.7: Circular steel plate model
Figure 6.8: Dimension of circular steel plate
Figure 6.9: Deep beam models with stiffened steel plates
Figure 6.10: Meshing of deep beam models with stiffened plates
-
Loading condition assigned to the model
The deep beam model is simply supported on the edges. Two point loading of 200kN each is applied on both the loading plates. The mesh size adopted for the models is 100 × 100 mm.
Figure 6.11: Loading in the models
-
Model designations
The Dynamic Explicit Analysis of the model with following characteristics are given model designations.
-
Varying shear span to depth ratio
-
Varying location of openings
-
Internal strengthening of openings
-
Since there are two kinds of loading, namely Direct loading and Indirect loading, the following are the corresponding model designations:
Table 6.2: Model designations of models with varying shear span to depth ratio under Dynamic Explicit Analysis
Parameter analysing
Direct loading
Indirect loading
Tensile cracks
DDTs1
IDDTs1
DDTs2
IDDTs2
DDTs3
IDDTs3
DDTs4
IDDTs4
Compressive cracks
DDCs1
IDDCs1
DDCs2
IDDCs2
DDCs3
IDDCs3
DDCs4
IDDCs4
Maximum principle plastic strain
DDPs1
IDDPs1
DDPs2
IDDPs2
DDPs3
IDDPs3
DDPs4
IDDPs4
Table 6.3: Model designations of models with varying location of openings under Dynamic Explicit Analysis
Parameter analysing
Direct loading
Indirect loading
Tensile cracks
DDTO1
IDDTO1
DDTO2
IDDTO2
DDTO3
IDDTO3
DDTO4
IDDTO4
Compressive cracks
DDCO1
IDDCO1
DDCO2
IDDCO2
DDCO3
IDDCO3
DDCO4
IDDCO4
Maximum principle plastic strain
DDPO1
IDDPO1
DDPO2
IDDP02
DDPO3
IDDPO3
DDPO4
IDDPO4
Parameter analysing
Direct loading
Indirect loading
Tensile cracks
DTOSP1
IDTOSP1
DTOSP2
IDTOSP2
DTOSP3
IDTOSP3
Compressive cracks
DCOSP1
IDCOSP1
DCOSP2
IDCOSP2
DCOSP3
IDCOSP3
Maximum principle plastic strain
DPOSP1
IDPOSP1
DPOSP2
IDPOSP2
DPOSP3
IDPOSP3
Parameter analysing
Direct loading
Indirect loading
Tensile cracks
DTOSP1
IDTOSP1
DTOSP2
IDTOSP2
DTOSP3
IDTOSP3
Compressive cracks
DCOSP1
IDCOSP1
DCOSP2
IDCOSP2
DCOSP3
IDCOSP3
Maximum principle plastic strain
DPOSP1
IDPOSP1
DPOSP2
IDPOSP2
DPOSP3
IDPOSP3
Table 6.4: Model designations of models with stiffened plate around the opening under Dynamic Explicit Analysis
Figure 7.3: DDTs3
-
-
ANALYSIS
-
General
The deep beam models with varying characteristics as shear span to depth ratio and location of openings have been analysed. In this session, the results observed from different analysis like Dynamic Explicit Analysis, Modal Analysis and Static Non- linear analysis are discussed in detail.
-
Deep beam models with varying shear span to depth ratio subjected to Direct loading
-
Dynamic Explicit Analysis
-
Tensile cracks
Figure 7.1: DDTs1
Figure 7.2: DDTs2
Figure 7.4: DDTs4
-
Compressive cracks
Figure 7.5: DDCs1
Figure 7.6: DDCs2
Figure 7.7: DDCs3
Figure 7.8: DDCs4
-
Maximum principle plastic strain
Figure 7.11: DDPs3
Figure 7.12: DDPs4
-
-
Modal analysis
Figure 7.9: DDPs1
Figure 7.10: DDPs2
15.00
10.00
5.00
0.00
20.00
10.00
0.00
20.00
10.00
0.00
MODE 1
s/d = 4 s/d = 3 s/d =2 s/d =1 UNCRACKED FREQUENCY
CRACKED FREQUENCY
Figure (a)
MODE 2
MODE 2
s/d = 4
s/d = 3
s/d =2
s/d =1
s/d = 4
s/d = 3
s/d =2
s/d =1
UNCRACKED FREQUENCY
CRACKED FREQUENCY
UNCRACKED FREQUENCY
CRACKED FREQUENCY
Figure (b)
MODE 3
MODE 3
30.00
28.00
26.00
24.00
22.00
30.00
28.00
26.00
24.00
22.00
s/d = 4
s/d = 3
s/d =2
s/d =1
s/d = 4
s/d = 3
s/d =2
s/d =1
UNCRACKED FREQUENCY
CRACKED FREQUENCY
UNCRACKED FREQUENCY
CRACKED FREQUENCY
Figure (c)
Figure 7.13 (a) (b) (c): Modal analysis of first three mode shapes
STATIC NONLINEAR CURVE
2000
1500
s/d = 1
1000
s/d = 2
STATIC NONLINEAR CURVE
2000
1500
s/d = 1
1000
s/d = 2
Force (kN)
Force (kN)
-
Static Non-linear Analysis
0
0
0
100
200 300
0
100
200 300
Displacement (mm)
Displacement (mm)
500
500
s/d = 3
s/d = 4
s/d = 3
s/d = 4
Figure 7.14: Force displacement curve in varying shear span to depth ratio subjected to Direct loading
-
Results and discussions Dynamic Explicit Analysis
-
From the results, it is observed that the propagation of tensile cracks and compressive cracks are maximum at the edges of the deep beam models. The above-mentioned crack action is high for first two models in both tensile and compressive cracks namely, DDTs1, DDTs2, DDCs1 and DDCs2 and evidently undergoes a subsequent reduction in propagation when the shear span to depth ratio has been increased that is for the models DDTs3, DDTs4, DDCs3 and DDCs4. The fourth models in each case derives economy in terms of less sagging. Therefore, higher the shear span to depth ratio, lesser will be the propagation of tensile cracks and compressive cracks.
But the ideology of crack reduction on the high shear span to depth ratio have been contradicted in the case of third parameter, that is, maximum principle plastic strain. Since plastic strain is regarded as an indicator of shear cracking, it will be on rapid
propagation at higher shear span to depth ratio. Hence, for plastic strain less shear span to depth ratio is economical.
Modal Analysis
The Modal Analysis of first three mode shapes have been analysed. The frequency exhibited by the corresponding models before and after cracking are termed as uncracked and cracked frequency respectively. The probability of crack propagation is high when there is high difference between the cracked frequency and uncracked frequency. For all of the three mode shapes it is observed that for s/d ratios 1 and 2, there is comparatively quite high difference between cracked frequency and uncracked frequency and less difference is seen in the case high s/d ratios especially for s/d = 4. Therefore, it is concluded that higher the shear span to depth ratio, lesser will be the difference between the frequencies and lesser will be the crack propagation thereby lesser will be the damage. Thus, the result of Dynamic Explicit Analysis is furthermore validated.
Static Non-linear Analysis
The force displacement curve of the models is provided to seek the abnormality in the non-linearity. If the curve shows any sudden rise and fall in axial load, it states that the corresponding model is liable to high crack propagation. For s/d ratio 1, the maximum displacement takes place when loaded with high axial force but the corresponding curve possess a number of sudden rise and falls which results in the distortion of the deep beam model. Thus, the crack propagation is enhanced. The second shear span to depth ratio (2) also comes up with quite unsatisfactory rise and falls in the curve. In the case of s/d ratios 3 and 4, it is observed that even if the maximum displacement is reached in comparatively less axial loads, the curve remains as normal that is in the normal mode of a force displacement curve and hence the corresponding nature can be called as optimum. It is the ductile property exhibited by the corresponding model makes it to displace for lower axial load since the ductility allows bending and deformation to some extent without rupturing.
-
Deep beam model with varying location of openings subjected to Direct loading
-
Dynamic Explicit Analysis
-
Tensile cracks
Figure 7.15: DDTO1
Figure 7.16: DDTO2
Figure 7.17: DDTO3
Figure 7.18: DDTO4
-
Compressive cracks
Figure 7.19: DDCO1
Figure 7.20: DDCO2
Figure 7.21: DDCO3
Figure 7.22: DDCO4
-
Maximum principle plastic strain
Figure 7.23: DDPO1
Figure 7.24: DDPO2
MODE 2
20.00
15.00
10.00
5.00
0.00
No Opening Opening at Opening at Opening at
5m 2.5m 0.5m
UNCRACKED FREQUENCY
CRACKED FREQUENCY
MODE 2
20.00
15.00
10.00
5.00
0.00
No Opening Opening at Opening at Opening at
5m 2.5m 0.5m
UNCRACKED FREQUENCY
CRACKED FREQUENCY
Figure (b)
Figure 7.25: DDPO3
40.00
30.00
20.00
10.00
0.00
MODE 3
No Opening Opening at
5m
Opening at 2.5m
Opening at 0.5m
Figure 7.26: DDPO4
STATIC NONLINEAR CURVE
500
STATIC NONLINEAR CURVE
500
-
-
Modal Analysis
UNCRACKED FREQUENCY CRACKED FREQUENCY
Figure (c)
Figure 7.27 (a) (b) (c): Modal analysis of first three mode shapes
-
Static Non-linear Analysis
12.00
10.00
8.00
6.00
4.00
2.00
0.00
MODE 1
400
No Opening
400
No Opening
300
200
Opening at
5m
300
200
Opening at
5m
Force (kN)
Force (kN)
No Opening Opening at
Opening at
0.5m
Opening at
0.5m
5m
Opening at 2.5m
Opening at 0.5m
UNCRACKED FREQUENCY CRACKED FREQUENCY
Figure (a)
0 100 200 300
0 100 200 300
Displacement (mm)
Displacement (mm)
Opening at
100 2.5m
0
Opening at
100 2.5m
0
Figure 7.28: Force displacement curve in varying locations of opening subjected to Direct loading
-
Results and Discussions Dynamic Explicit Analysis
For the purpose of comparing the deep beam with opening and without opening, the first models in each session that is, DDTO1,DDCO1 and DDPO1 has been modelled without opening and the remaining models DDTO2, DDTO3, DDTO4, DDCO2, DDCO3, DDCO4, DDPO2, DDPO3 and DDPO4 are
with openings at mid-point (5m from edge), in between the midpoint and edge (2.5m from edge) and closer to the edge (0.5m from edge) respectively. It was observed that diagonal cracks were initially formed around the opening which then propagated towards support and loading points respectively. With a further increment of the load, the cracks get further widened around the opening resulting in the spalling. Openings are evidently influenced by crack concentration due to tension and compression.
Opening near the edge and midpoint contribute to high tensile cracks and compressive cracks, that is models DDTO2, DDTO4, DDCO2, DDCO4, DDPO2, DDPO4. Shear Crack
probability is higher for beam models with opening at midpoint. So it is concluded that location of opening at 2.5m from edge, that is models DDTO3, DDCO3 and DDPO3 possess comparatively less cracking around the opening. Thus, the most economic location of opening in a deep beam is estimated as in between the midpoint and the edge.
Modal Analysis
There is larger reduction in frequency when opening is provided at the center of the beam. Opening at the center adds up distortion, because there is already higher mid-point bending moment. Opening near the edge causes more damage than opening at 2.5m. This was due to instability of the beam by mass and stiffness change due to opening. It is better to provide opening somewhere between center and the edge.
Static Non-linear Analysis
In this case, the crack displacements as explicit functions of external displacement. Beam with opening shows a fall in axial force, it indicates more cracking. Beam with opening at midpoint shows more displacement at lower loads, so its stiffness is less and cracking will be more.
-
-
Deep beam model with varying shear span to depth ratio subjected to Indirect loading
-
Dynamic Explicit Analysis
-
Tensile cracks
Figure 7.29: IDDTs1
Figure 7.30: IDDTs2
Figure 7.31: IIDTs3
Figure 7.32: IDDTs4
-
Compressive cracks
Figure 7.33: IDDCs1
Figure 7.34: IDDCs2
Figure 7.35: IDDCs3
Figure 7.36: IDDCs4
-
Maximum principle plastic strain
Figure 7.37: IDDPs1
Figure 7.38: IDDPs2
Figure 7.39: IDDPs3
Figure 7.40: IDDPs4
-
-
Modal Analysis
MODE 1
MODE 1
10.50
10.00
9.50
9.00
8.50
10.50
10.00
9.50
9.00
8.50
s/d = 4
s/d = 3
s/d =2
s/d =1
s/d = 4
s/d = 3
s/d =2
s/d =1
UNCRACKED FREQUENCY
CRACKED FREQUENCY
UNCRACKED FREQUENCY
CRACKED FREQUENCY
Figure (a)
MODE 2
MODE 2
19.00
18.00
17.00
16.00
15.00
19.00
18.00
17.00
16.00
15.00
s/d = 4
s/d = 3
s/d =2
s/d =1
s/d = 4
s/d = 3
s/d =2
s/d =1
UNCRACKED FREQUENCY
CRACKED FREQUENCY
UNCRACKED FREQUENCY
CRACKED FREQUENCY
Figure (b)
MODE 3
MODE 3
31.00
30.00
29.00
28.00
27.00
26.00
31.00
30.00
29.00
28.00
27.00
26.00
s/d = 4
s/d = 3
s/d =2
s/d =1
s/d = 4
s/d = 3
s/d =2
s/d =1
UNCRACKED FREQUENCY
CRACKED FREQUENCY
UNCRACKED FREQUENCY
CRACKED FREQUENCY
Figure (c)
Figure 7.41 (a) (b) (c): Modal analysis of first three mode shapes
STATIC NONLINEAR CURVE
800
600
s/d=1
400
s/d=2
STATIC NONLINEAR CURVE
800
600
s/d=1
400
s/d=2
FORCE (kN)
FORCE (kN)
-
Static Non-linear Analysis
200
0
200
0
s/d=3
s/d=4
s/d=3
s/d=4
0 50 100 150
0 50 100 150
-200
-200
DISPLACEMENT (mm)
DISPLACEMENT (mm)
Figure 7.42: Force displacement curve in varying shear span to depth ratio subjected to Indirect loading
-
Results and discussions Dynamic Explicit Analysis
-
The main aim of this session is to know what variation would the type of loading could cause in terms of crack propagation in a deep beam. As stated earlier in the study, the amount of deflection varies, based on the stiffness of the deep beam, the span between supports and the load it which carries. On comparing the results with Direct loading, the crack reduction pattern holds same for indirect loading. Shear span to depth ratio closer to 1 and 2 resulted in cracking mainly, at the edge of the deep beam. Shear span to depth ratio closer to 2 and 3 resulted in cracking at the bottom whereas Shear span to depth ratio closer to 4 resulted in cracking at the top center.
The models IDDTs1, IDDTs2, IDDCs1 and IDDCs2 are liable to comparatively more tensile crack and compressive crack propagation respectively. The shear span to depth ratio 3 and 4 that is, IDDTs3, IDDTs4, IDDCs3 and IDDCs4 seems more economical especially, s/d = 4. Therefore, for indirect loading also, propagation of tensile and compressive cracks goes on reduction at higher shear span to depth ratio.
As observed for Direct loading, in Indirect loading too, the ideology of reduction of tensile and compressive cracks on high shear span to depth ratio is again violated in the case of shear cracks, that is, plastic strain. The plastic strain is maximum at higher shear span to depth ratio. The model IDDPs1 is the most economic model in terms of minimum plastic strain. The impart of Indirect loading had resulted in the increase of only one parameter and that is tensile cracks. The action of tensile cracking is more when indirect loading is provided, while Compressive cracks and shear cracks get reduced under indirect loading. Midpoint sagging, which is being regarded as a drawback for direct loading, is get reduced for indirect loading.
Modal Analysis
The modal analysis result of Indirect loading is almost similar to result of Direct loading. More difference between the cracked frequency and uncracked frequency is seen for less shear span to depth ratios and less difference for high shear span to depth ratio. Hence, higher shear span to depth ratio possess less damage. On comparing, Frequency under indirect loading get reduced from 1% to 6% than direct loading.
Static Non-linear analysis
Non-linear strain distribution in deep beams are caused by sudden changes in loading and geometry. s/d ratio 1 shows a sudden fall in axial force, it indicates more cracking. Shear span to depth ratio 2, 3 and 4 showed a normal force displacement curve and the shear span to depth ratio 1 showed a sudden fall in axial force, it indicates more cracking. For indirect loading, the beam fails at lower displacements and lower loads, Therefore, cracking occurs quickly.
-
Deep beam model with varying locations of openings subjected to Indirect loading
-
Dynamic Explicit Analysis
-
Tensile cracks
Figure 7.43: IDDTO1
Figure 7.44: IDDTO2
Figure 7.45: IDDTO3
Figure 7.46: IDDTO4
-
Compressive cracks
Figure 7.47: IDDCO1
Figure 7.48: IDDCO2
Figure 7.49: IDDCO3
Figure 7.50: IDDCO4
-
Maximum principle plastic strain
Figure 7.51: IDDPO1
Figure 7.52: IDDPO2
Figure 7.53: IDDPO3
-
-
Modal Analysis
MODE 1
9.20
9.00
8.80
8.60
8.40
No Opening Opening at Opening at Opening at
5m 2.5m 0.5m
UNCRACKED FREQUENCY CRACKED FREQUENCY
MODE 1
9.20
9.00
8.80
8.60
8.40
No Opening Opening at Opening at Opening at
5m 2.5m 0.5m
UNCRACKED FREQUENCY CRACKED FREQUENCY
Figure (a)
MODE 2
16.60
16.40
16.20
16.00
15.80
15.60
15.40
15.20
15.00
No Opening Opening at Opening at Opening at
5m 2.5m 0.5m
UNCRACKED FREQUENCY CRACKED FREQUENCY
MODE 2
16.60
16.40
16.20
16.00
15.80
15.60
15.40
15.20
15.00
No Opening Opening at Opening at Opening at
5m 2.5m 0.5m
UNCRACKED FREQUENCY CRACKED FREQUENCY
MODE 3
28.00
27.80
27.60
27.40
27.20
27.00
26.80
26.60
26.40
26.20
No Opening Opening at Opening at Opening at
5m 2.5m 0.5m
UNCRACKED FREQUENCY CRACKED FREQUENCY
MODE 3
28.00
27.80
27.60
27.40
27.20
27.00
26.80
26.60
26.40
26.20
No Opening Opening at Opening at Opening at
5m 2.5m 0.5m
UNCRACKED FREQUENCY CRACKED FREQUENCY
Figure (b)
Figure 7.54: IDDPO4
Figure (c)
Figure 7.55 (a) (b) (c): Modal analysis of first three mode shapes
200
150
200
150
NO
OPENING
NO
OPENING
OPENING AT
100 5m
OPENING AT
100 5m
FORCE (kN)
FORCE (kN)
-
Static Non-linear Analysis
STATIC NONLINEAR CURVE
250
STATIC NONLINEAR CURVE
250
0
0
50 100
150
OPENING AT
0.5m
0
0
50 100
150
OPENING AT
0.5m
-50
DISPLACEMENT (mm)
-50
DISPLACEMENT (mm)
50
50
OPENING AT
2.5m
OPENING AT
2.5m
Figure 7.56: Force displacement curve in varying locations of opening subjected to Indirect loading
-
Results and Discussions Dynamic Explicit Analysis
Openings influence crack concentration due to tension and compression. The models IDDTO2, IDDTO4, IDDCO2, IDDCO4, IDDPO2, IDDPO4 undergoes high crack propagation and the model with opening in between the mid-point and the edge that is IDDTO3, IDDCO3 and IDDPO3 seems satisfactory with comparatively less intensity of crack propagation around the opening. Cracks due to opening are almost similar for direct and indirect loading. Indirect loading through secondary beam results in less compressive cracks. On comparing with the Direct loading, Shear Crack probability is higher for beam with opening at the midpoint. Shear cracks get reduced when the beam is loaded indirectly, very small extra shear cracks are generated at the locations of secondary beams.
Modal Analysis
Less difference between the cracked frequency and the uncracked frequency is shown for the opening at 2.5m from edge therefore, it is concluded that in order to reduce the amount of cracking, opening should be provided somewhere between midpoint and edge. For indirect loading, the frequency got reduced from 4% to 6% than direct loading, which implies, secondary beams add up more cracks on the primary beam than cracks formed due to direct loading.
Static Non-linear Analysis
The non-linearity nature in the force displacement curve and sudden rises and falls in axial load are more seen in Direct loading than Indirect loading. Opening at 2.5m shows similar curve of beam without opening for Indirect loading. Deep beam with opening at midpoint shows sudden fall in axial force, so it indicates more cracking. For indirect loading, the beam fails at lower displacements and lower loads, therefore cracking occurs quickly.
-
-
Deep beam model with stiffened circular plate around the opening
-
Dynamic Explicit Analysis
-
Tensile cracks
Figure 7.57: DTOSP1
Figure 7.58: DTOSP2
Figure 7.59: DTOSP3
-
Compressive cracks
Figure 7.60: DCOSP1
Figure 7.61: DCOSP2
Figure 7.62: DCOSP3
-
Maximum principle plastic strain
Figure 7.63: DPOSP1
Figure 7.64: DPOSP2
Figure 65: DPOSP3
-
-
Modal Analysis
MODE 1
Opening at 5m Opening at 2.5m Opening at 0.5m
MODE 1
Opening at 5m Opening at 2.5m Opening at 0.5m
9.619.709.64 9.639.789.69
9.619.709.64 9.639.789.69
7.92
8.29
7.92
8.29
6.82
6.87
6.82
6.87
5.41
5.77
5.41
5.77
No steel plate Steel Plate No steel plate Steel Plate
UNCRACKED FREQUENCY CRACKED FREQUENCY
No steel plate Steel Plate No steel plate Steel Plate
UNCRACKED FREQUENCY CRACKED FREQUENCY
Figure (a)
MODE 2
Opening at 5m Opening at 2.5m Opening at 0.5m
17.5117.3317.15 17.5517.4517.23
MODE 2
Opening at 5m Opening at 2.5m Opening at 0.5m
17.5117.3317.15 17.5517.4517.23
13.65
12.56
10.41
14.06
12.61
11.02
13.65
12.56
10.41
14.06
12.61
11.02
No steel plate Steel Plate No steel plate Steel Plate
UNCRACKED FREQUENCY CRACKED FREQUENCY
No steel plate Steel Plate No steel plate Steel Plate
UNCRACKED FREQUENCY CRACKED FREQUENCY
Figure (b)
MODE 3
Opening at 5m Opening at 2.5m Opening at 0.5m
MODE 3
Opening at 5m Opening at 2.5m Opening at 0.5m
28.9828.5428.99 29.0028.6329.04
26.84
24.71
21.56
26.88
24.75
22.64
28.9828.5428.99 29.0028.6329.04
26.84
24.71
21.56
26.88
24.75
22.64
No steel plate Steel Plate No steel plate Steel Plate
UNCRACKED FREQUENCY CRACKED FREQUENCY
No steel plate Steel Plate No steel plate Steel Plate
UNCRACKED FREQUENCY CRACKED FREQUENCY
Figure (c)
Figure7.66(a) (b) (c): Comparison of cracked and uncracked frequency of stiffened and non-stiffened plate
-
Static Non-linear Analysis
-
NON-STIFFENED OPENING
500
400
NON-STIFFENED OPENING
500
400
[1] Results and Discussions Dynamic Explicit AnalysisThe main objective behind the internal strengthening of opening is to avoid the interruption degree of openings along the force path and to distribute the load around the opening. The technique of internal strengthening discussed in the study has seen satisfactory results regarding the reduction of concentration of cracks around the opening. Cracks near the opening gets reduced when opening is stiffened by using circular steel plate. For midpoint opening, that is, model DTOSP1, DCOSP1 and DPOSP1, when stiffened with steel plate, plastic strain got reduced to 3.45%. For opening at 2.5m, that is, DTOSP2, DCOSP2 and DPOSP2, when stiffened with steel plate, plastic strain got reduced to 12.88%. For opening near the edge, that is, DTOSP1, DCOSP1 and DPOSP1, when stiffened with steel plate, plastic strain got reduced 7.95%. Hence, the maximum reduction of plastic strain happened for the opening provided between the mid-point and the edge. The openings at the mid- point and close to the edge, with the aid of internal strengthening, can seek quite good applications.
Modal Analysis
The increase in un-cracked and cracked frequency for opening at midpoint, when steel plate stiffening is provided, are from 0.1% to 0.2% and 1.44% to 3.88% respectively. The increase in un-cracked and cracked frequency for opening at 2.5m, when steel plate stiffening is provided, are from 0.3% to 0.8% and 3.0% to 4.7% respectively. The increase in un-cracked and cracked frequency for opening at the edge, when steel plate stiffening is provided, are from 0.16% to 0.54% and 0.44% to 0.77% respectively.
Static Non-linear Analysis
300
200
100
300
200
100
Opening at
5m
Opening at 2.5m
Opening at
5m
Opening at 2.5m
Force (kN)
Force (kN)
The non-linear nature of models with stiffened plate and
w
Opening at
0 0.5m
0 100 200 300
Displacement (mm)
Opening at
0 0.5m
0 100 200 300
Displacement (mm)
ithout stiffened plate is plotted. Same displacement is observed for higher loads in stiffened beams, it indicates that the ability of the beam to resist cracking is increased. When openings are stiffened, the pattern of load displacement curve observed is similar.
400
400
Opening at
5m
Opening at
5m
Force (kN)
Force (kN)
Figure 7.67: Non stiffened opening
STIFFENED OPENING
STIFFENED OPENING
800
600
800
600
0
0
100 200
300
Opening at
0.5m
0
0
100 200
300
Opening at
0.5m
-200
Displacement (mm)
-200
Displacement (mm)
200
200
Opening at
2.5m
Opening at
2.5m
Figure 7.68: Stiffened opening
-
-
CONCLUSION
The three types of analysis namely Dynamic Explicit Analysis, Modal Analysis and Static Non-linear Analysis has done for the models and showed almost similar results. In order to avoid cracking in simply supported deep beams, higher shear span to depth ratio is strictly preferrable (s/d > 2). In order to provide opening in simply supported deep beam, most appropriate location is in between the midpoint and edges. When indirect loading is provided, the cracks developed are more due to the reduction of torsional stiffness. Indirect loading induces more tensile cracks but less compressive cracks and shear cracks. When openings are stiffened using steel plates, cracking gets reduced. When openings at 2.5m are stiffened with steel plates, they behave almost similar to the deep beam without opening.
REFERENCES
-
Thamer Hussein Amer Alhussein, Jamal Abdul Samad Khudhair, (2020), Experimental and Numerical Evaluation of Shear Strength of Directly and Indirectly Loaded Flanged Recycled Self-Compacted Reinforced Concrete Deep Beams, Hindawi Journal of Engineering Volume 2020, Article ID 3462010, 20 pages.
-
V Revilla-Cuesta, M Skaf, F Faleschini, J M Manso and V Ortega-L´opez, (2020), Self-compacting concrete manufactured with recycled concrete aggregate: an overview, Journal of Cleaner Production, vol. 262, Article ID 121362.
-
Hasan Falah Hassan, Yarub Gatna Abtan, (2020), A Review of Behaviour of Reinforced Concrete Deep beams, Journal of Engineering and Sustainable Development.
-
G Wardeh, E Ghorbel, (2019), Shear strength of reinforced concrete beams with recycled aggregates, Advances in Structural Engineering, vol. 22, no. 8, pp. 19381951.
-
C Roy, T U Mohammed, R Hasan, (2019) Experimental analysis on self-compacting concrete (SCC) made with locally available materials incorporating different W/C ratio, in Proceedings of International Conference on Planning, Architecture and Civil Engineering, Bangladesh, February.
-
K N Rahal and Y T Alrefaei, (2017), Shear strength of longitudinally reinforced recycled aggregate concrete beams, Engineering Structures, vol. 145, pp. 273282.
-
Haleem K Hussain, (2017), Finite Element Analysis of Deep Beams under Direct and Indirect load, Kufa Journal of Engineering Vol. 9, No. 2, PP. 152-167.
-
Said M, Adam M A, Mahmoud A, Shanour A S, (2016), Experimental and analytical shear evaluation of concrete beams reinforced with glass fiber reinforced polymers bars, Construction and Build. Material. V. 102. pp. 574-591.
-
Wael Kassem, (2015), Shear strength of deep beams: a mathematical model and design formula, Struct Concrete.
-
Abdul-Razzaq, (2015), Effect of Heating on Simply Supported Reinforced Concrete Deep Beams, Diyala Journal of Engineering Sciences, 8(2), p.116-133.
-
Hassan F Hassan, (2015), Behaviour of Hybrid Deep Beams Containing Ultra High Performance and Conventional Concretes, Engineering and Technology Journal, Vol.33, Part A, No.1, 2015, pp.30-50.
-
Mohamad N, Khalil I, Abdul Samad and Goh W I, (2014), Structural Behaviour of Precast Lightweight Foam Concrete Sandwich Panel with Double Shear Truss Connectors under Flexural Load, ISRN Civil Engineering, 17.
-
ACI Committee, (2014), Building Code Requirements for Structural Concrete (ACI 318-14) and Commentary, American Concrete Institute, Indianapolis, IN, USA.
-
Syroka Korol, and J Tejchman, (2014), Experimental investigations of size effect in reinforced concrete beams
failing by shear, Engineering Structures, 2014. 58: p. 63-
78.
-
Mohammad Hassani M, Akib S, Shariati M, Suhatril M and Arabnejad Khanouki M M, (2014), An experimental study on the failure modes of high strength concrete beams with particular references to variation of the tensile reinforcement ratio. Engineering Failure Analysis, Elsevier Ltd, 41, 7380.
-
Al-Khafaji, J, Al-haarbaf, I, Wisam W H, (2014), Shear behaviour of self-compacting concrete deep beams, Journal of Engineering and Development, Vol. 18, No.2.
-
Andermatt M F, Lubell A S, (2013), Behaviour of Concrete Deep Beams Reinforced with Internal Fibre-Reinforced Polymer Experimental Study, ACI Structural Journal, 47(110), 585594.
-
Sultan W H, (2013), Behavior of steel fibers reinforced self- compacting concrete deep beams under shear effect, PhD Thesis, University of Al-Mustansirya, Civil Department, Baghdad, Iraq, pp. 240.
-
Lu, W Y Lin, (2013), Shear strength of reinforced concrete deep beams, ACI Struct. J, 110, 671680.
-
Birrcher D B, Tuchscherer R G, Huizinga M, and Bayrak O (2013), Minimum Web Reinforcement in Deep Beams, ACI Structural Journal, 26(110), 297306.
-
Haider M, Alsaeq, (2013), Effects of Opening Shape and Location on the Structural Strength of R.C. Deep Beams with Openings, World Academy of Science, Engineering and Technology 78.
-
Nilesh, Saksena, Prof. P G patel, (2013), Experimental Study of Reinforced Concrete Beam with Web Openings, International journal of advanced engineering research and studies.i/Jaers/vol. ii/ issue, iii/April-June, 2013/66- 68.
-
Gara F, Ragni L, Roia D and Dezi L, (2012), Experimental behaviour and numerical analysis of floor sandwich panels, Engineering Structures, Elsevier Ltd, 36, 258269.
-
Omar Qarani Aziz, Ramzi B and Abdul-Ahad, (2012), Shear Strength Prediction of Crushed Stone Reinforced Concrete Deep Beams without Stirrups.
-
Campione G, (2012), Flexural behaviour of steel fibrous reinforced concrete deep beams, ASCE Journal of Structural Engineering. V.138, No.2, 2012, pp. 235-246.
-
Hassan S A, (2012), Behaviour of reinforced concrete deep beams using self-compacting concrete, PhD Thesis, University of Baghdad, Civil Department, Baghdad, Iraq, pp. 164.
-
Amiri S, Masoudnia, (2011), Investigation of the Opening Effects on the Behaviour of Concrete Beams Without Additional Reinforcement in Opening Region Using Fem Method, Australian Journal of Basic and Applied Sciences,5(5),617-624.Hanson, J.M., Square openings in webs of continuous joists, Portland Cement Association, 1969, pp: l-14.
-
Arabzadeh A, Aghayari R, Rahai A R, (2011), Investigation of experimental and analytical shear strength of reinforced concrete deep beams, International Journal of Civil Engineering. V. 9. No. 3. pp. 207-214.
-
Mohammad hassani M, et al, (2011), Failure modes and serviceability of high strength self-compacting concrete deep beams, Engineering Failure Analysis, 18(8): p. 2272- 2281.
-
Ray S P, (2011), Behaviour and ultimate shear strength of reinforced concrete deep beams with and without opening in web, PhD thesis, Indian Institute of Technology, Kharagpur, India.
-
Tae Min Yoo, (2011), Strength and Behaviour of High Strength Concrete Deep Beam with Web Opening. Griffith school of Engineering- PhD thesis- Griffith University.
-
Shah D L, Modhera C D, (2010), Evaluation of shear Strength of Self Compacting Concrete Deep Beam, International Journal of Advanced Engineering and Technology. V.I, Issue II, pp. 292-305.
-
CHEN Hui-rong, (2009), Finite Element Analysis on Hole Radius of Circular Web Opening Steel Beams. Journal of Qingdao Technological University China, Vol. 30 No. 3 2009.
-
Zhang N, K H Tan, (2007), Size effect in RC deep beams: Experimental investigation and STM verification, Engineering structures, 29(12): pp 3241-3254.
-
Kong, F K, (2006), Reinforced concrete deep beams: CRC Press.
-
Kosa K, Wakiyama T, Nishioka T, Kobayashi H, (2006), Effect of Shear Span Ratio on The Fracture of Deep Beams, Earthquake Disaster Prevention Research Group, Public Works Research Institute, 9 pp.
-
Shah R H, Mishra S V, (2004), Crack and Deformation of SFRC Deep Beams, IE (I) journal CV, July, 2004, pp. 44- 48.
-
Okamura H, (1999), Self-compacting high-performance concrete, Tokyo: Social System Institute.
-
Okamura H, Maekawa K, Ozawa, K, (1998), High performance concrete, Tokyo: Gihoudou Publication.
-
https://images.app.goo.gl/UqpXniHxuz1C6ANQ7
-
https://images.app.goo.gl/g15bSPUR3C7pG1SKA
-
Abaqus 6.14/ CAE users manual [44] IS 456: 2000