
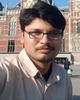
- Open Access
- Authors : Bilal Ahmad , Safdar Abbas Zaidi , Muhammad Arsalan Saeed
- Paper ID : IJERTV9IS060730
- Volume & Issue : Volume 09, Issue 06 (June 2020)
- Published (First Online): 01-07-2020
- ISSN (Online) : 2278-0181
- Publisher Name : IJERT
- License:
This work is licensed under a Creative Commons Attribution 4.0 International License
Experimental Study on True Stress-Strain Relations and Poissons Ratio Evaluation of Particular Areas of Welded Connections
Bilal Ahmad1, Safdar Abbas Zaidi1* & Muhammad Arsalan Saeed2
1 Student, Natural Hazards & Risks in Structural Engineering, Bauhaus University-Weimar 99423, Germany
2 Lecturer, Department of Civil Engineering, Sir Syed University of Engineering & Technology-Karachi 75300, Pakistan
AbstractThis article presents the experimental evaluation of properties of a welded connection joint in steel structures. Three different joint areas are taken under consideration namely the base material, filler material and the heat affected zone. Stress strain relation has been conducted using miniature tensile testing and for this Digital Image Technology has been incorporated in this experiment. DIC results are manipulated using GOM Correlate software and MS-Excel tools. Observing overall experimental results properties and conclusion for each studied joint area has been made and using these results Poisson ratio for each component is determined.
KeywordsPoisson ratio, welded connection, True stress strain curve, experimental DIC
-
INTRODUCTION
The elasticity and ductility of steel has made it most reliable and resistant in lateral loads of wind and seismic actions in viewpoint of construction industry. Since first successful incorporation of steel in 19th century to the construction industry, the development of steel construction has brought a revolution in the development of material properties and their method of productions. Some noticeable milestones in terms of structure strength, economy, versatility in architecture, fabrication and erection technology, serviceability and others are introduced in construction industry and these achievements cannot be delivered without implementing steel in structural design [1]. Thermo-mechanical rolling and the quenching and tempering process, steel with a high construction strength hut guaranteeing also good fabrication properties such as weld-ability was introduced into the construction market [1]
According to [2], S460M & S690Q steel are the most common practiced structural steel material in European construction industry. There are three different ways to make HSS. The first and oldest method is QT (quenched and tempered) followed by the TMCP (thermomechanical controlled process) and DQ (direct quenching) methods. The common goal of all of these above mentioned production methods is to create a steel of high yield strength and good ductility.
Today, the application of these grades is driven by some major requirements of Architecture, Economy, Environment and structural safety [3]. Materials exhibiting good mechanical characteristics such as yield strength and toughness as well as excellent fabrication properties are always been a preference for structural engineers [4]. The two major ways of increasing yield strength of steel are alloying elements or using heat treatment. Keeping in mind that alloying elements in some cases also worsens the fabrication properties of steel especially the welding ability on contrary heat treatment has a major advantage on microscopic crystalline structure of material and results in a fine grained steel with higher strength and toughness [5]. Table 1 shows all the types of available steel grades according to Euro code 2007 and all these materials are now in practice of European construction for steel structures.
Table 1: Steel Grades Available in Market [6]
Standards
Steel Grade
EN 10025-2
Non Alloy structural steel
S275, S355
EN10025-3
Normalized rolled weld able f i n e grain structural steels
S275, S355 S420,S460
EN 100025-4
Thermomechanical rolled weld bale fine grained structural steels
S275, S355 S420,S460
EN10025-6
Flat products of high yield strength steel in the quenched and tempered condition
S460, S500 S550, S620 S690, S890
One of the most important property of any material is the measure of its strength. Strength of material can be expressed in many categories of compression, tension, flexure etc. however tensile test provides a lot of information about the strength and mechanical behavior of material. The basic idea of tensile test is to place the sample between two grips and make sure these grips must be fixed. The material sample has some known geometrical feature which are the standard ones. Load is applied in such a way that one end remains fixed and load increases on the other end. Keep increasing the load till fracture and meanwhile measure the change in length with respect to original length.
Engineering stress and strain data is commonly used because it is easier to generate the data and the tensile properties are adequate for engineering calculations but engineering stress-strain curve does not give a true indication of the deformation characteristics of a metal because it is based entirely on the original dimensions of the specimen, and these dimensions change continuously during the testing used to generate the data. True stress and strain measures account for changes in cross- sectional area by using the instantaneous values for the area as defined in ASTM [7].
Tensile properties indicate how the material will react to forces being applied in tension. A tensile test is a fundamental mechanical test where a carefully prepared specimen is loaded in a very controlled manner while measuring the applied load and the elongation of the specimen over some distance. Tensile tests are used to determine the modulus of elasticity, elastic limit, elongation, proportional limit, and reduction in area, tensile strength, yield point, yield strength and other tensile properties [8].
-
EXPERIMENTAL STUDY
Commercial software GOM Correlate has been used for DIC analysis of the miniature tensile tests in free version for students. It only allows to analyze 2D surface using one camera only. The basic principal of DIC is the tracking of the same image points located in the two digital images of the test specimen surface taken before and after deformation. Local strain analysis using DIC technique requires the test specimen surface to be painted with a pattern. For this sprinkled with white paint and black paint to ensure a good contrast (optional any paint can be used. The given sets of data, or images are imported into GOM Correlate for DIC analysis.
Longitudinal extensometers in the length L of 10 mm are created on the image sets taken by camera 1 for longitudinal technical strain identification. Transverse extensometers are created on image data sets taken by camera 2 in the section that presents the necking and fracture, to get the cross-section change which is needed for true stress strain curve. Finally, the image taken time is matched with the test machine sampling time, using Excel programming function and tools to obtain the corresponding force to each image.
Once the images are imported into the software, surface component are created for DIC analysis within the surface throughout the complete image dataset. Facet size and point distance must be chosen when a surface component is created, the first step is determining how many pixels the software uses to find the points, the value is small it will trace closer strain values. Facet size should be kept as low as possible but large enough to track all the oints over the whole sample test.
The image sets of data, or images are imported into GOM Correlate for DIC analysis. The red dot in figure 7 shows poor quality as stochastic pattern, in some samples the surface components created in the software disappears just after 100-150 images. Depending upon the quality of pattern the results of DIC analysis vary in accuracy and problems can be observed in plastic areas when pattern is highly distorted as shows in figure 1. The red Dotes that were painted in the test specimen are not properly matched by the software where the surface components were created this can be observed in the below figure
8 where after 144 image the methodology of strain measurement does not work and we do have any stain data for further manipulation. This distorted pattern and strain measurements can be seen in
below figure 2. After taken the strain measurements from the Software it is then matched with the force which is recorded during the test. Somehow some stress stain curve is not complete due to missed data. The reason has been discussed earlier
Table 2: Test Specimen Geometry Description
Sample ID
Gauge Width (mm)
Gauge Thickness (mm)
Cross section Area (mm)
3SN012
2.14
3.23
6.85
3WEZ012
2.14
3.03
6.48
3GW012
2.13
3.23
6.88
The size of existing miniature tensile test specimen is mentioned in below table 2. For the calculation of engineering stress stain curve we take the value of cross-section area given in same table. To obtain a true stress strain curve an engineering approach is applied using other software tool (Autodesk Auto CAD). As the miniature test was carried out by orthogonal arrangement of Cameras. Camera 1 gives us the width and rear camera 2 gives us the thickness of the sample by manipulating and comparing images on selected points on the curve the actual cross-section area for calculating stress has been obtained. A sample figure 1 is shown below.
Figure 1: Actual thickness of sample obtained from AutoCAD setting scale
-
ANALYTICAL RESULTS
-
Stress Strain Curves
Stress strain curves for all three welded connection element of base metal, filler material and heat affected zone are produced. For base material a sample from S690Q steel is taken whose dimensions are tabulated in Table 2. For filler material G46 material is used. This all combination makes studied joint under matched in its welding properties. Also a small specimen is taken from the center core of heat affected zone.
Using GOM student software version, miniature test images are analyzed. The analysis has been made for engineering stress strain as well as true stress strain relationship. For true stress strain, AutoCAD software is used to examine the dimension changes gives by GOM. A transverse extension-meter is marked on modelled specimen in GOM and the transverse length at each interaction point has been measured. This technique is applied in both the images side of specimen thickness and its width in order to obtain an actual stressed area for cross section at any instant of loading. Thus stress strain curves are plotted and their results are shown in figure 3, 4 and 5 for base material, filler and heat affected zone respectively. In case of true stress strain curve the abrupt change is due to the reduction of cross-sectional area which results the curve to go in upward direction
B. Poissons Ratio
Poisson's ratio is the ratio of transverse contraction strain to longitudinal extension strain in the direction of stretching force Tensile deformation is considered positive and compressive deformation is considered negative. The definition of Poisson's ratio contains a minus sign so that normal materials have a positive ratio.
= – trans / longitudinal
Poissons ratio for all studied samples are determined and negative sign from the equation above is neglected in calculation. The results for Poisson ratios are shown in a graphical way from figure 6 to figure 8.
In figure 3, it is clearly observed that yield strength is same for both engineering stress and true stress plot and after that true stress strain shows more strength till its maximum tensile strength which is due to the process of necking in specimen length. Yield strength for bas material (approximately 727 MPa) is found to be slightly higher than the designated strength of 690 MPa. Figure 4 shows the same plot for filler material of G46 and its strength is found approximately 500 MPa which is again a bit higher than designated 460 MPa. The joint remains under matched as filler material strength is less than base material.
From figure 5, the strength of heat affected zone is observed much higher among all the three specimen and yield strength is found more than 800 MPa which is approximately 830 MPa. The increase is yield strength of heat affected zone may be due to the excessive heating process during welding of joint and it may change the microscopic crystalline structure of material resulting in a new chemical composition of steel.
Above in figure 6, Poisson ratio of base material is plotted as the scattered graph showing the values at each image, longitudinal and transverse strains are obtained from the DIC image analysis. To obtain stains values extensometers are places in horizontal and traverse directions. By taking average of all the values it can be concluded the resultant value is -0.35297 which is close or nearly equal to the value of the Stainless steel which is assumed to be 0.3[9]. And the minus shows the contraction of the material
The average value of Poisson ratio of weld material / filler is minus 0.304, as observed from figure 7, which is comparable to the value of the stainless steel is taken as -0.30. The fluctuations in scattered graph is due the undesired slippage caused by lack of proper gripping of specimen during the tensile test. Similarly, the graph of Poisson ratio of heat effected zone is shown in figure 8. The scattered graph shows values of Poisson ratio at each image and the average value is minus -0.8588. This value is slightly large compared to base material and filling material and due to the transformation in the micro structure of the heat effected zone due to the thermal welding process the recrystallization of the grains leads to higher strength value.
Figure 2: GOM Correlate software processed image Sample BM 3WG004, longitudinal extensometer for Strain measurement. Distorted Image from number 144
Figure 3: Stress Strain results for base material
Figure 4: Stress Strain results for filler material
Figure 5: Stress Strain results for heat affected zone
Figure 6: Poisson ratio for base material
Figure 7: Poisson ratio for filler material
Figure 8: Poisson ratio for heat affected zone
-
-
CONCLUSION
The stress strain curves are not too much consistent due to the loss of surface components in DIC analysis. Most of data is missing at fracture point. But in general all the stress strain relationships show a fine agreement between engineering and true stress strain properties.
The strength of all the welded connection components are found slightly higher than their designated standard values. In addition, heat affected zone shows highest strength even more than its parent material. This is due to the change in its micro structure and chemical properties due to the application of excessive heat temperature during welding process. It is strongly recommended for further research to study the effect of welding heat on steel microscopic crystallography and its chemistry to obtain a much fine results for heat affected zone in welding joint.
Poisson ratios are determined for each component. For ase material it is approximately averaged to -0.352, for filler material it is -0.304, and for heat affected zone its averaged to -0.85 approximately. The negative sign just showing the effect of contraction and is plotted with negative region in graphs.
For further research, it is suggested to study some more specimen especially of heat affected zone to evaluate the chemical and materialistic properties and their Poisson ratios can be assessed with more precise values.
ACKNOWLEDGMENT
The Authors would like to acknowledge all the supports and guidelines provided by Department of steel and hybrid structures at Bauhaus University-Weimer in Germany. The consistent guidelines regarding research and writing has made this work completed and comprehensive to be presented to international forum.
REFERENCES
-
Samuelsson A. and Schroter F. Chapter 5.1 – Production processes, mechanical and chemical properties, fabrication properties in Use and application of high-performance steels for steel structures. International Association for Bridge and Structural Engineering (IABSE), (2005).
-
Khoshaba, S a m i r a n d W. Heinrich. (2014). Problems w i t h W e l d e d j o i n t s in S t e e l Structures. Conference proceedings
-
Basu, B. Raman, R. Microstructural Variations in a High-Strength Structural Steel Weld under Isoheat Input Conditions. Welding Journal, 2002, pp. 239- 248
-
Galambos TV, Hajjar JF, Earls CJ, Gross JL. Required properties of high performance steels. Report NISTIR 6004. Building and Fire Research Laboratory, National Institute of Standards and Technology; 1997.
-
G¨unther H-P, editor. Use and application of high-performance steels for steel structures. Structural Engineering Documents. International Association for Bridge and Structural Engineering (IABSE), vol. 8; 2005.
-
Eurocode 2004, EN 1993-1-1: European standard for hot-rolled structural steel.
-
American Society for Testing & Materials (ASTM) Manual guidelines
-
Woong Lim & Ho-Kyung Kim. (2013). Design and development of miniaturized tensile testing machine. Global Journal of Engineering Education, 15(1), pp: 48-53
-
D. E. Gray, American Institute of Physics Handbook, 3rd Ed., Chapter 3, McGraw Hills, New York, 1973