
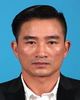
- Open Access
- Authors : Hoang Thanh Dat
- Paper ID : IJERTV9IS060081
- Volume & Issue : Volume 09, Issue 06 (June 2020)
- Published (First Online): 12-06-2020
- ISSN (Online) : 2278-0181
- Publisher Name : IJERT
- License:
This work is licensed under a Creative Commons Attribution 4.0 International License
Experimental Study on The Heating Performance of R32 Heat Pump using Natural Cold Source
Hoang Thanh Dat
The University of Da Nang – University of Technology and Education 48 Cao Thang, Danang City, Vietnam
Abstract: The compression heat pump has high exhaust temperature when evaporation temperature is low, which seriously affects the stability of the operation of the unit, especially the R32 engineering quality. This paper presented a method to improve the thermal performance of low temperature and established the experimental table. In this paper, the compression heat pump refrigerant is R32. The heat pump was studied under sub-cooling and normal conditions, exhaust temperature, heat production, the change rule of the parameters such as heat COP.
Keywords: Heat pump; Sub-cooling; R32; COP.
-
INTRODUCTION
Energy is an important material foundation for the survival and development of human society [1]. Global economic growth and population growth have led to a growing demand for energy. Heat pump technology is a new energy technology that has attracted worldwide attention in recent years. The heat pump technology can save a great deal of high grade energy. Air conditioning is an indispensable part of human life and work environment. According to the literature, global average building energy consumption accounts for about 37% of the total energy consumption [2], and China's building energy consumption is about 40%[3] of total energy consumption [4]. In total energy consumption, air conditioning system consumes the largest proportion. In order to improve the efficiency of refrigeration and thermal energy efficiency, the over-cooling technology is widely used in the steam compression refrigeration system in low-temperature fields [5]. There are several main types of cold weather: cooling of the environment, cooling of the suction pipe and the use of external mechanical cooling [6-7]. According to the national conditions of China, an R32 refrigerant alternative is proposed, but the excessive exhaust temperature restricts its promotion, especially in the field of heating. In this paper, the heat pump system with R32 is adopted to improve the thermal performance of heat pump, and its theoretical analysis and experimental research are carried out. Experimental results presentation, in evaporation temperature -20 ~ 5 respectively and the sub-cooling flow mass increase 0.005m3/h. In the evaporation temperature is -20 ~ 5, sub-cooling flow mass increase 0.005m3/h each protection the heat flow average 2.5% lower. At the same evaporation temperature, the heating COP decreases with the increase of the sub-cooling flow mass.
-
MATERIALS AND METHODS
-
How the system works
The working principle of heat pump system using natural cold source is shown in figure 1. Compared with the single stage, the cooling device is added, and the cold source is from the low temperature environment. When it is cold running, it is used to introduce some cold source medium from the low temperature environment to improve the heat making, especially in low ambient temperature.
Fig. 1. Sub-cooling cycle and lgp-h diagram
-
Calculation model
Calculation process conditions:
-
The system works under steady state conditions;
-
Condensation temperature 40, the Evaporating temperature range – 20 ~ 0 ;
-
The degree of superheat 0 ~ 10 ;
-
Indicate the efficiency of 0.8;
Fig. 1 shows the lgp-h diagram of the sub – cooling cycle 1'-2s -3-4-5'-5-1'. Processs 3-4 in order to liquid refrigerant
the temperature of the throttle super cooler, 4-5' for throttling process.
The heating Qsubheat
Qsubheat cmt cvt
(18)
-
No sub – cooling cycle Unit quality refrigerating quantity
-
q0 p p =p p
Unit volume refrigerating capacity
(1)
The performance coefficient of the hot COPsubheat cycle
COP
COP
Qsubheat
W
W
subheat
sub
(19)
Theory than work
qzv (p
p )/v1' =q0 / v1'
(2)
Fig. 2 shows the change of the exhaust temperature with the degree of sub-cooling. It can be seen from figure 2 that the lower the temperature of the exhaust temperature, the
W0 ps p (3)
Indicating specific work
lower the temperature of evaporation and the higher the exhaust temperature. In the evaporation temperature at 0, –
W W /
(4)
10 and -20, every increase 1 degree of sub-cooling,
i 0 i
exhaust temperature drop an average of 1.19. The effect of
Unit heat load of condenser
qk ps p
Performance coefficients of the refrigeration cycle The theoretical value
(5)
sub-cooling on the exhaust temperature is more obvious when the evaporation temperature is lower.
105
Exhaust temperature/
Exhaust temperature/
100
q h h 95
t0 = -20
COP 0 1 5
t0 = -15
0 W h h
(6) 90
Indicated value
0 2s 1
85
t0 = -10
t0 = -5
i
i
COP q0
80
75 t0 = 0
Wi
The heating
(7) 70
65
t0 = 5
Type in the:
Qheat cmt cvt
(8)
60
4 6 8 10 12
Degree of sub – cooling /, t = 40
c The specific heat of waterJ/(kg.K)
The density of waterkg/m3
v Volume flow in water unit timem3/s
t The temperature difference of the cooling water
k
Fig. 2. The variation of discharge temperature with Sub – cooling of suction vapor
Fig. 3 shows the change of the thermal COPsubheat with evaporation temperature. Can be seen from figure 3, the
t=t
mout tmin
(9)
evaporating temperature increased when heating COPsubheat, evaporation temperature when -20 ~ 0 with super-cooling
tm-inAverage temperature of cooling water inlet
tm-outAverage temperature of cooling water outlet.
The performance coefficient of the heat cycle of the heating COPheat
degree is 8 when heating COPsubheat increased by an average of 53.8%.
4.1
3.8 t0 = -20
COP
Qheat
3.5
t0 = -15
heat W
(10)
i
COPsubheat
COPsubheat
3.2
t0 = -10
(2) the heat pump cycle that is sub – cooling t0 = -5
Unit quality refrigerating quantity
2.9
t0 = 0
q0-sub p p' =p h4
Unit volume refrigerating capacity
(11)
2.6
2.3
t0 = 5
Theory than work
qzv
(p
p' )/v1' =q0-sub
/ v1'
(12)
2.0
2 4 6 8 10 12
Degree of sub – cooling /, tk = 40
Wsub W0 ps p (13) Instructions than work
Fig. 3. The heat COP with of sub-cooling system
-
-
Experimental study
Wi Wsub /i
Unit heat load of condenser
(14)
Fig. 4 shows a diagram of the experimental installation of a sub-cooling heat pump system using natural cold source.
q h h
System includes: 1 – the scroll compressor, 2 – oil separator, 3
k -sub 2' 3
The thermal load of the coolers
qgl p h4
The performance coefficient of the loop The theoretical value
(15)
(16)
– condenser, 4 – depending on the liquid mirror, 5 – dry filters, 6 super cooler, 7 – expansion valve, 8 – evaporator, 9 – chilled water flow meter, 10 – freezer water tank,11 – 14 and electric heater, 12 – cooling water pump, 13- condenser cooling water tank 15 – cooling water pump, 16 – cooling water flow meter. When the system is running, the cold
COPsub
q0-sub p p'
W h h
circulation can be achieved by introducing a portion of chilled water from the freezing water to refrigerant liquid.
sub 2s 1 (17)
Fig. 4. Experimental testing bench
125
120
Exhaust temperature /
Exhaust temperature /
115
110
105
100
95
90
85
80
75
70
to= -20 to= -15 to= -10 to= -5 to= 0 to= 5
0.005 0.01 0.015 0.02 0.025 0.03 0.035
Sub-cooling flow mass /m3/h
In this paper, R32 is used to study the experiment and
Fig. 5. The variation of discharge temperature with sub-cooling flow
compare the performance of the single-stage mode with the to= -20 to= -15 to= -10
cold mode. In order to better evaluate the performance of the prototype system, the instrument was calibrated. The boot process is as follows: firstly, connect the power of the control cabinet, start and adjust the cooling water system, and open the compressor when the water system is adjusted, and open the data acquisition system. During the experiment, the single- stage compression cycle experiment was carried out after a period of stable working condition. After the unit has been stable for a period of time under the experimental setting conditions, it has been turned on separately. Need to direct measurement parameters include: suction temperature, pressure, exhaust temperature, pressure, condenser import and export, import and export temperature and pressure, cooling
4.0
Heating capacity/kW
Heating capacity/kW
3.5
3.0
2.5
2.0
1.5
to= -5 to= 0 to= 5
0.005 0.01 0.015 0.02 0.025 0.03 0.035
Sub-cooling flow mass /m3/h
water temperature, cooling water flow, sub-cooling temperature and pressure, compressor power. To the amount of indirect measurement for: t import and export of cooling water temperature difference and heat Q, heating COP.
-
Results and discussions
Fig. 5 shows the change of the exhaust temperature with the sub-cooling flow mass. It can be seen from figure 5 that under the same evaporation temperature, the sub-cooling flow mass increases and the exhaust temperature decreases. The evaporation temperature lower, the more obvious the decreasing trend of the sub-cooling flow. In evaporation
temperature -20 ~ 5 respectively and the sub-cooling flow mass increase 0.005m3/h. Average reduce exhaust
temperature corresponding 1.7 to 3.
Fig. 6 shows the variation of heat flow with sub-cooling flow mass. It can be seen from figure 6 that, under the same evaporation temperature, the increase of sub-cooling flow mass will decrease the heat production. In the evaporation
temperature is -20 ~ 5, sub-cooling flow mass increase 0.005m3/h each protection the heat flow average 2.5% lower. In the evaporation temperature for -10, sub-cooling flow mass increase of the heating flow mass to most reduce. Evaporation temperature within the range -10 ~ 5, the best sub-cooling flow mass is 0.015m3/h; Evaporation temperature in the -20 ~ -15, the heat flow with the change of sub-cooling flow mass effect is not obvious.
Fig. 6. The variation of heating capacity with sub-cooling flow mass
Fig. 7 shows the change in the sub-cooling flow mass of the heating COP. It can be seen from figure 7 that the change trend of COP is basically in line with the change trend of heat production. At the same evaporation temperature, the heating COP decreases with the increase of the sub-cooling flow mass. In evaporation temperature at -10, the increase of the sub-cooling flow mass to reduce impact on the heating COP, the largest in the evaporation temperature is -20 to -15 and sub-cooling flow mass when the heating COP of minimal impact. In the evaporation temperature for -10 ~ -5 condition, best too sub-cooling flow mass is 0.015m3/h, at – 15 and -20 condition, heating COP does not change significantly with the too sub-cooling flow mass. The reason is that the sub-cooling flow mass increases, the liquid sub- cooling increases, but at the same time the condensing pressure decreases, the production heat decreases, the compressor power increases, and the heating COP decreases.
to= -20 to= -15 to= -10 3.0 to= -5 to= 0 to= 5
COPsubheat
COPsubheat
2.5
2.0
1.5
1.0
4.4
Heating capacity/kW
Heating capacity/kW
3.9
3.4
2.9
2.4
1.9
1.4
Single-stage
Sub-cooling sytem
-20 -15 -10 -5 0 5
Evaporating temperature/
0.005 0.01 0.015 0.02 0.025 0.03 0.035
Sub-cooling flow mass /m3/h
Fig. 7. The variation of heating COP with sub-cooling flow mass
Fig. 8 shows the variation of the exhaust temperature with the evaporation temperature. The figure 8 shows that the evaporation temperature is lower exhaust temperature higher, when the low evaporation temperature below -20, single
stage compressor system and overheating exhaust temperature is too high, the system run deterioration can't even run, only in extreme sub-cooling system mode to the safe operation, and after sub-cooling exhaust temperature of 120.6 . In the
Fig. 9. The variation of heating capacity with evaporating temperature
Fig. 10 shows the change rule of the heat COP with evaporation temperature. It can be seen from figure 10 that, with the increase of evaporation temperature, the single-stage operation and the sub-cooling running system heat COP is on the rise. But compared with single-stage operation, the sub- cooling running mode is heat COP lower. In the evaporation
temperature of -15 ~ 5, after sub-cooling heating COP decrease average 3.2%. when the evaporation temperature -10
and -15 , sub-cooling of heating COP is the average decreases correspondingly 7.3%, 10.6%.
evaporation temperature of -15 ~ 5, sub-cooling system
of exhaust temperature than ordinary single-stage run by 4
~ 6, the evaporating temperature 5, sub-cooling system of exhaust gas temperature most decrease, the most obvious exhaust temperature is 68 only. After the condenser has
been added, it has obvious effect on the high exhaust temperature when the system is running at low temperature.
125
120
3.0
COPsubheat
COPsubheat
2.5
2.0
1.5
Single-stage
Sub-cooling sytem
Exhaust temperature/
Exhaust temperature/
115
110
105
Single-stage
Sub-cooling sytem
1.0
-20 -15 -10 -5 0 5
Evaporating temperature/
100
95
90
85
80
75
70
65
-20 -15 -10 -5 0 5
Evaporating temperature/
Fig. 10. The variation of heating COP with evaporating temperature
-
-
CONCLUSION
In this paper, the thermal performance of heat pump using natural cold source is studied. The results are as follows:
-
It is obvious that the exhaust temperature of the system is lower than that of the sub-cooling system, which is suitable for high exhaust temperature system and operation of the refrigerant such as R32. With the increase of sub-cooling flow
Fig. 8. The variation of discharge temperature with evaporating temperature
Fig. 9 shows the change rule of heat control with evaporation temperature. It can be seen from figure 9 that in the same operation mode, the heat production increases with the increase of evaporation temperature. However, when the system is in sub-cooling operation mode, compared with ordinary single-stage operation mode at different evaporative temperatures, the heat production is reduced. In evaporation temperature -15 ~ 5, sub-cooling of heating is the
average 5% Whe the evaporation temperature -10 and –
15, sub-cooling of heating is the average decreases correspondingly 6.6%, 12%.
mass, the exhaust temperature decrease more and more.
-
The optimal sub-cooling flow mass value of natural cold source is in sub-cooling operation. Evaporation temperature within the range -10 ~ 5, sub-cooling flow
mass is 0.015m3/h when the heating and heating COP to obtain the maximum; Evaporation temperature in the -20 ~
-15, the heating and heating COP along with the change of sub-cooling flow mass effect is not obvious.
-
Under the same conditions, the heating and heating COP of the sub-cooling system compared with the single- stage system is slightly reduced. When the evaporation temperature of -15 to reduce, the most obvious decrease by
12% and 10.6%, respectively.
REFERENCES
-
Leng Tianjiu, Han leitao, Ma huang (2008). Development and utilization of unconventional energy [J]. Agricultural engineering technology: new energy industry, (6):26-29.
-
Xie Yingbai (2002). Theoretical analysis and experimental study of total energy system of gas engine heat pump [D]. Thesis of doctoral dissertation of north China electric power university.
-
Zhang Zhiying (2006). Building energy saving is the only way to achieve sustainable development of the construction industry [J]. China engineering consulting, (7): 18-19.
-
Cai Weiguang (2011). Analysis model and empirical study on the influence factors of energy consumption in Chinese buildings [D]. Chongqing: doctoral dissertation of Chong Qing University.
-
Du Xiaotong (2012). Research on energy efficiency optimization of buildings [D]. Doctoral dissertation of Shan dongong University.
-
Bilal Ahmed Qureshi B AZubair S M (2013)Mechanical sub-
cooling vapor compression systems-current status and future directions. International Journal of Refrigeration [J]. 36 (8): 2097-2110.
-
Bilal Ahmed QureshiSyed M Zubair (2012). The effect of refrigerant
combinations on performance of a vapor compression refrigeration system with dedicated mechanical sub-cooling. International Journal of Refrigeration [J]. (35): 4757