
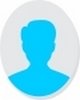
- Open Access
- Authors : C. Nivedhitha , B. Durga , E. Suneka , G. Ancelin Teena, E. Priya
- Paper ID : IJERTV10IS070304
- Volume & Issue : Volume 10, Issue 07 (July 2021)
- Published (First Online): 13-08-2021
- ISSN (Online) : 2278-0181
- Publisher Name : IJERT
- License:
This work is licensed under a Creative Commons Attribution 4.0 International License
Experimental study on Partial Replacement of Cement by Hyposludge in Concrete with Chemical Admixture
Ms. C. Nivedhitha, M.E, Assistant Professor Dept. of Civil Engineering
Saranathan College of Engineering Trichy, India
G. Ancelin Teena, E. Priya,
E. Suneka, B. Durga,
Student
Dept. of Civil Engineering Saranathan College of Engineering Trichy, India.
Abstract The global cement industry contributes about 9% of greenhouse gas emission to the earths atmosphere.Paper industry wastes are being produced by 420 million tonnes per annum by chemical process in India. In order to reduce cement
-
Cement
-
MATERIALS AND PROPERTIES
manufacturing and disposal problem of paper waste, there is a need to develop alternative binders in construction field. Utilization of industrial waste products as Supplementary Cementitious Material in concrete is very important aspect in view of economical, environmental and technical reasons. It is directed towards developing low cost concrete and light weight concrete from paper industry waste. From the test results,10 % replacement of hyposludge with cement attained good strength and when superplasticizer is added good strength is obtained on
20 % replacement of hyposludge with cement. Hence by replacing hyposludge in the concrete structures that will conserve resources and avoid environmental and ecological damages caused by cement production.
Keywords Cement, hypo sludge, chemical admixture, M30 grade concrete, compressive strength, spilt tensile
-
INTRODUCTION
This work examines by using paper waste (hypo sludge) as partial replacement of cement & it is most essential to develop profitable building materials from hypo sludge. Carbon dioxide is emitted as a by-product of clinker production, a intermediate product in cement manufacture, in which calcium carbonate is calcinated and converted to lime, the primary component of cement. Carbon dioxide is also emitted during cement production by fosil fuel combustion, that causes environmental damages. Concrete is a material which is the most widely used in construction of the buildings in the world.There is an increasing demand for concrete worldwide at low cost, by producing this hyposludge concrete it will reduces the demand of concrete and reduces the emissions of CO2 from cement industry. Hypo sludge is used as a replacement in producing concrete and was investigated on its physical and mechanical properties. There is an increasing demand for concrete worldwide at low cost, by producing this concrete it will reduces the demand of concrete and reduces the emissions of CO2 from cement industry. This project concisely explains the technical and environmental benefits of supplementary cementitious materials use and study the deign parameters of concrete on inclusion of paper waste as partial replacement of cement with and without using superplasticizers.
Cement is formed by grinding calcined limestone and clay
into a very fine, grey powder. Cement is one of the binding agent in this project. The cement and water forms a paste and binds the other materials together. The Ordinary Portland Cement (53 grade) conforming to IS:8112-1989 is being used. Tests were conducted on cement.
TABLE I. PROPERTY OF 53 GRADE CEMENT
S.no.
Property
Result
1.
Specific gravity
3.15
2.
Consistency
33%
3.
Initial setting time
30 min
4.
Final setting time
600 min
-
-
-
Fine Aggregate
Fine aggregate is the essential ingredient in concrete that consists of natural sand or crushed stone.Fine aggregate used throughout the work comprised of M-sand with maximum size of 4.75mm conforming to Zone I as per IS 383-1970. The physical properties of fine aggregate like specifc gravity and water absorption are tested in accordance with IS:2386.
TABLE II. PROPERTY OF FINE AGGREGATE
S.no.
Property
Result
1.
Specific gravity
2.6
2.
Water absorption
2%
-
Coarse Aggregate
Coarse aggregate consists of crushed granite or basalt rock,conforming to IS:383. Coarse aggregate are used in the size of 20mm.The physical properties of coarse aggregate like specific gravity, impact strength and crushing strength are tested in accordance with IS:2386.
TABLE III. PROPERTY OF COARSE AGGREGATE
S.no.
Property
Result
1.
Specific gravity
2.45
2.
Impact strength
26.75%
3.
Crushing strength
28%
-
Hyposludge
Hyposludge is a waste material collected from the paper industry. Hyposludge is used in concrete with the replacement of cement of 10%,20%, and 30% by using superplasticizers and also in absence of superplasticizers. The compressive strength and spilt tensile strength was determined in 7 and 28days.
TABLE IV. PROPERTY OF HYPOSLUDGE
S.no. |
Property |
Result |
1. |
Consistency |
31% |
2. |
Initial setting time |
36 miin |
3. |
Final setting time |
595 min |
E.Chemical Admixture
Admixtures are ingredients other than basic ingredients cement, water and aggregates that are added to concrete batch immediately before or during mixing to modify one or more of the specific properties of concrete in fresh and hardened state.Added in small quantity in liquid form. Dr. Fixit Pidiproof LW+ was used. It is used as an additive for cement concrete.It makes concrete cohesive and prevents segregation.
F.Water
Water is the essential ingredient to mix all the components in concrete. The pH of water used should be from a range of 6.0 to 8.5.Water is required for preparation of cement mix and curing work.
-
DESIGN MIX METHODOLOGY
The concrete mix design was proposed by using IS10262:2009.The grade of concrete used was M30 with water to cement ratio 0.45. Superplasticizer was added about 4 % of cement.The mix design proportions for 1m3of concrete were tabulated.
TABLE V. MIX DESIGN PROPORTIONS
Hypo sludge(%)
W/C ratio
Cement (Kg/)
F.A
(Kg/)
C.A
(Kg/)
0
0.45
440
717
1130
10
0.45
390
717
1130
20
0.45
354
717
1130
30
0.45
310
717
1130
-
EXPERIMENTAL INVESTIGATION
-
Test on Fresh Concrete
Slump cone test determines the workability and consistency of various concrete mixes.By using a metallic slump mould,The differenc in level between the height of the mould and that of the highest point of the subsided concrete is measured.
-
Casting of moulds
Casting of conventional concrete of M30 mix ratio and also casting of 10%,15%,20%,25% and 30% replacement of cement by hypo sludge. We casted conventional concrete with M30 mix design, we casted 24 cubes and 24 cyclinders of around for conventional concrete of cube size 150mm×150mm×150mm.and cylinder size 150mm ×300 mm has been casted for the determination of compressive strength and spilt tensile strength respectively. The concrete specimens were cured under normal conditions as per IS 516-1979 and were tested at 7 days and 28 days for determining compressive strength and spiltting tensile strength.
-
Compressive strength Test
In this test, the cubes are subjected to compressive force in a compression testing machine and the ultimate load at which the failure occurs is noted.Then the compressive stress is ultimate load by area exposed to load and stress value is obtained in N/mm2.
Fig 1. Compressive strength test
TABLE VI. COMPRESSIVE STRENGTH TEST RESULTS
S.no
Hypo Sludge (%)
Compressive Strength at 7 days (N/mm2)
Compressive Strength at 28 days (N/mm2)
1.
0%
24.3
35.7
2.
10%
25.6
37.6
4.
20%
26
38.1
6.
30%
21.9
29.7
-
Split Tensile strength test
In this test,the cylindrical specimen is placed horizontally between the loading surface of a compression- testing machine and the load is applied until failure of cylinder occurs along the vertical diameter. The split tensile strength is given by the formula 2P/ (DL) and the stress value is obtained in N/mm2.
Fig 2. Split tensile strength test
TABLE VII.SPLIT TENSILE STRENGTH TEST RESULTS
S.no
Hypo Sludge (%)
Split tensile Strength at 7 days (N/mm2)
Split tensile Strength at 28 days (N/mm2)
1.
0%
2.15
2.56
2.
10%
1.8
2.61
4.
20%
1.37
1.62
6.
30%
1.1
1.9
-
-
CONCLUSION
we conclude our project with various mixes with curing periods of 7 and 28 days by partial replacement of cement with hypo sludge.Testing of cubes and cylinder in compression testing machine with capacity of 1000 kN were carried out.The compressive strength of concrete increases as the curing period for M30 grade concrete and the replacement of hypo sludge is done from The maximum strength of concrete is attained in 20% replacement of hyposludge with cement as compared to Conventional concrete.
0%,10%,20%, and 30%.The maximum compressive strength for 7 days and 28 days is achieved for 20% replacement of cement with use of superplasticizers and starts decreasing on 30%.
REFERENCES
-
An Exploration Study On Stone Waste As Fore going Alternatives For Green Concrete Ankit Nileshchandra Patel, Prof.JayeshkumarPitroda,IJAERS/Vol. II/Issue III/April-June, 2013/35-38
-
Utilization Of Waste Paper Pulp By Partial ReplacementOf Cement In Concrete Sumit A Balwaik; S P Raut Vol.1, Issue 2, pp.300-309
-
Durability Of Concrete With Partial Replacement Of Cement By Paper Industry Waste (Hypo Sludge) Jayeshkumar Pitroda, L.B.Zala, F S Umrigar, ISSN: 22783075, Volume-2, Issue-3, February 2013
-
Structural performance of concrete in partial replacement of paper waste.Rampanth,Sureshg.patil.(IJETE).Volume1,Issue 7,August 2014
-
Study of concrete involving useof waste paper sludge ash aspartial replacement of cement.SajadAhmad,Rafiq Ahmad (ISOR).Vol 3,Issue 11,November 2013.
-
Structural performance and durablitity of concrete by partial replacement of hyposludgeHariKrishnan,vidyasagarlal, (ISJOR)Vol4, Issue no 12 ISSN:2319- 6890,Dec 2015.
-
Experimental investigation of partial replacement by industrial waste.Balamurgan,karthickraja,IJERA,ISSN:2248-9622,Vol 4,Issue 4,April 2014.
-
Flexural Strength of Beams by Partial Replacement of Cement With Fly ash and Hyposludge in Concrete.Jayraj vinodsinhsolanki,Jayeshkumar Pitroda, IJESIT,Vol 2,Issue1,January 2013.
-
Experimental study on partial replacement of Cement by Hyposludge in concrete Priya R,Hepzibah A,Indhuja N,Madhavan D,Manikandan R, IJISET ,Vol. 4, Issue 3, March 2017.
-
Indian Standard code of Practicefor plain and reinforced concrete,IS 456:2000,fourth revision,Bureau of Indian Standard, New Delhi.
-
Indian Standard recommended guidelines for concrete mix design, IS 10262-2009 Bureau of Indian Standards, New Delhi.
-
Indian Standard Specification For coarse aggregate and Fineaggregate from natural sources for concrete,IS 383:1970,Bureau of Indian Standards,New Delhi.J. Clerk Maxwell, A Treatise on Electricity and Magnetism, 3rd ed., vol. 2. Oxford: Clarendon, 1892, pp.68-73.