
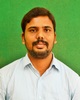
- Open Access
- Authors : Manu G. , Rajat Agrawal , Mandeep Singh , Kaushlendra Pratap Singh, Rahul Yadav
- Paper ID : IJERTV10IS080036
- Volume & Issue : Volume 10, Issue 08 (August 2021)
- Published (First Online): 12-08-2021
- ISSN (Online) : 2278-0181
- Publisher Name : IJERT
- License:
This work is licensed under a Creative Commons Attribution 4.0 International License
Numerical Investigation of Thermal Energy Storage System with Helical Coil using Phase Change Material
1Manu G.
Assistant Professor Mechanical Engineering JSSATE Noida, India
4Kaushlendra Pratap Singh
Student Mechanical Engineering JSSATE Noida, India
2Rajat Agrawal
Student Mechanical Engineering JSSATE Noida, India
3Mandeep Singh
Student Mechanical Engineering JSSATE Noida, India
5Rahul Yadav
Student Mechanical Engineering JSSATE Noida, India
Abstract In this study, a modified helical tube type heat exchanger was introduced and numerically investigated, to enhance the thermal performance of energy storage system using phase change material (PCM).
To evaluate the thermal performance of this heat exchanger, a geometric model of the thermal energy storage system is designed. It consists of an outer cylindrical tube with a helical heat pipe passing through it. The cylinder is filled with the phase change material i.e. paraffin wax. Two-dimensional numerical models were developed. The model enables us to stimulate conduction and natural convection heat transfer mechanisms. The assumptions used in numerical modeling are also discussed in the paper. The process of melting and solidification (discharging) was monitored during the simulation. The results showed that the PCM solidification process accelerates when utilizing the modified helical tube heat exchanger compared to straight tube heat exchanger.
Key words: Phase change material, helical coil, cylindrical shell.
Nomenclature:
Local liquid fraction (-)
g Gravitational acceleration (m/s2) Tm Melting point of the PCM (K)
H Fusion latent heat (kJ/kg) Thermal expansivity (1/K)
-
INTRODUCTION
Ever increase in the demand of power will causes greenhouse gas emissions and the increase in fuel prices are the main driving forces behind effort to more effectively utilize various sources of renewable energy. Solar energy is one of the primary source of renewable energy, but it is not available continuously unlike intermittent by nature. Thus, a need arises to develop thermal energy storage systems to store the available excess energy whenever available for later use. Energy storage system would be helpful to create a balance between the demand and supply and also improves the performance and reliability of the energy systems. So phase changing materials (PCMs) have been proposed to store the
latent heat energy. The use of a latent heat storage system using phase changing materials (PCMs) is an effective way of storing thermal energy and has the advantages of high- energy storage density and the isothermal nature of the storage process.
Many type of thermal energy storage (TES) system using phase changing materials (PCMs) have been studied. A straight copper tube and shell unit is one of the simplest design and among the most commonly used.
This project aims to design and analyze a thermal energy storage unit with phase change materials. We designed a helical tube heat exchanger with phase change materials (PCM) inside a shell unit.
-
PHASE CHANGE MATERIALS
Phase change materials (PCMs) are substances which absorb or release large amount of heat energy when they go through a change in their physical state, i.e. from solid to liquid and vice versa. During the phase transition, many materials are able to absorb a significant amount of heat energy. The opposition is true when the material freezes and solidifies: the material will give out the heat that it absorbed when it melted. Different materials will melt and solidify at different temperatures and are able to absorb different amount of energy.
Phase change materials are useful because they melt and solidify at specific, defined temperatures, making them suitable to control the temperature in range of diverse applications. By melting and solidifying at the phase change temperature (PCT), a PCM is capable of storing and releasing large amounts of energy compared to sensible heat storage. Heat is absorbed or released when the material changes from solid to liquid and vice-versa or when the internal structure of the material changes; PCMs are accordingly referred to as latent heat storage (LHS) materials.
A large variety of PCMs are available in the market. These are classified as Organic PCMs and Inorganic PCMs. In our study we use Paraffin wax as a PCM because it is chemically and physically stable, have high heat of fusion,
non-corrosive in nature, etc. Some other properties of Paraffin wax are shown in the Table-1.
Table 1: Thermo-physical properties of Paraffin Wax
Property
Value
Melting Temperature (Tm)
53.7oC
Specific Heat – Solid (Cps)
2.0 kJ/kg.K
Specific Heat Liquid (Cpl)
2.15 kJ/kg.K
Thermal Conductivity Solid (ks)
0.24 W/m.K
Thermal Conductivity Liquid (kl)
0.22 W/m.K
Density Solid (s)
910 kg/m3
Density Liquid (l)
790 kg/m3
Latent Heat of Fusion
190 kJ/kg
-
Literature Review
Zhao et al. [1] presented numerical results for shell tube latent thermal energy storage units. Results confirmed that using the optimized fin number can decrease the melting time by over 60%. Furthermore, the additional reduction of time can be obtained by appropriately modifying bottom fins lengths and intervals. What is more, in the result as of CFD calculations for PCM storage with three kinds of metal foams (nickel, aluminum, and copper). Finally, it was confirmed that by using optimized fins geometry it is possible to obtain comparable efficiency of the melting process as in the case of metal foam using.
Debojyoti Chakraborty et al [2] carried out an experiment on paraffin wax and concluded that at the vicinity of the wall of the inner pipe through which heat is supplied to shell side (annulus), the temperature difference is very steep. The phase change near wall is noted by the formation of a flat plateau regime on temperature v/s time plot. The radial variation of the temperature is noted in three different cases and also the natural convection was considered in liquid phase;
Chen et al. [3] numerically investigated the performance of the PCM thermal energy storage unit with metal foam enhancement. The metal foam was used to enhance heat transfer inside the PCM substance as well as at the side of fluid flow. The article presented a calculation procedure that was used to model the solidification/melting process during the discharging/charging process of the storage tank. The use of foam significantly increased heat transfer on both sides. The time of phase change decreased more than 84% using metal foam on both sides (at PCM and working fluid sides), compared to 40% in the case of using the metal foam only on the phase change material side. The increase of thermal efficiency of latent energy storage units can be achieved also by modification of PCM properties.
Anish et al. [4] experimentally investigated the performance of energy storage with erythritol/xylitol as PCM in a vertical double spiral coil unit. The authors presented an analysis of experimental data for the charging/discharging process at different operating conditions (flow rate of working fluid and different inlet temperature of it).The study concuded that a double coil storage unit provided good performance. Better heat transfer efficiency was obtained for the melting process. It was highlighted that this is the effect of bigger natural convention influence compare to solidification. In the same operation condition, the higher energy was stored in PCM
container filled with erythritol. However, the discharging process is diminished in the case of erythritol due to the appearance of subcooling phenomena.
-
-
NUMERICAL MODEL
The melting and solidification model of ANSYS (Fluent) software was used for modeling and simulation of the melting of PCM. ANSYS Fluent uses enthalpy porosity method for modeling the solidification and melting process. In this method the melting interface is not tracked explicitly. A quantity named as liquid fraction (fraction of cell volume which is in liquid form) is associated with each cell in the PCM domain. Based on enthalpy balance the liquid fraction is calculated after each iteration. In this method phase change interface is shown as mushy zone in which the value of liquid fraction changes from 0 to 1. Mushy zone is like a pseudo (porous zone) whose porosity decreases from 1 to 0. When the material solidifies the porosity becomes 0 and the velocity drops to zero in that zone.
-
Assumptions
The assumptions made during the numerical modeling are:
-
The flow is laminar.
-
Inlet fluid has constant velocity and constant temperature.
-
The ambient temperature is assured to be constant at 300K.
-
Solidification and mushy zone parameter is constant at 10000.
-
Viscous heating and volume expansion is ignored.
-
-
Boundary Conditions
-
Inlet velocity of the working fluid is set to 20 m/s.
-
Inlet temperature is 330K.
-
Outer wall of the cylinder is at an ambient temperature of 300K.
-
Helical coil is high thermal conductive material, assumed it is a copper
-
All the other contact regions and walls are coupled.
-
-
Model Description
A geometric model of the Thermal Energy Storage system used for simulation is shown in the Fig 2.1, it consists of an outer cylindrical tube with a helical heat pipe passing through it. The cylinder is filled with the phase change material i.e. paraffin wax and the helical heat pipe carries the working fluid i.e. water.
Fig 2.1: Diagram of model
-
Cylinder
The cylinder has a length of 510mm and the outer diameter is 142mm with a wall thickness of 1mm are shown in the fig-2.2 and fig-2.3. The material of the cylinder is chosen acrylic due to its insulating property and light weight.
Table 2: Dimension of the cylinder
DIMENSION
VALUE
Length
510 mm
Outer Diameter
142 mm
Inner Diameter
140 mm
Wall Thickness
1 mm
Hole Diameter
25 mm
Figure 2.2: Side view of the Cylinder shell with helical coil
Figure 2.3: Longitudinal view of cylinder with coil inside
-
Helical Heat Pipe
The helical heat pipe has a total length of 510mm with 400mm helix length, outer diameter of the pipe is 25 mm with a wall thickness of 1mm are shown in the fig-2.4 and fig-2.5. The material of the heat pipe is chosen copper due to its high thermal conductivity and easy availability.
Table 3: Dimensions of the Helical Heat Pipe
DIMENSION
VALUE
Total Length
510 mm
Helix Length
400 mm
Coil Diameter
125 mm
Pipe Outer Diameter
25 mm
Pipe Inner Diameter
23 mm
Pitch
50 mm
Outer Surface Area of Pipe
2810.2 mm2
Figure 2.5: Copper helical coil with transverse view
-
Mesh generation and simulation approach
The meshing of the model has been done in the ANSYS Mesh Editor. The physics preference has been set to CFD and the solver preference to Fluent while keeping the export format and element order to standard and linear respectively along with the default element size. For the sizing, the size function has been set to adaptive and relevance centre to fine while keeping the element size to default. Further, the smoothing has been set to high.
Edge sizing has been given to the outer cylinder and the helical pipe while keeping the definition type as Number of Divisions with no bias and behavior set to hard. The number of divisions for the cylinder and the pipe are 90 and 45 respectively.
The orthogonal quality depicts that the mesh has a standard quality of about 0.18, average quality of 0.71 and minimum quality of approximately 0.05. Also, the mesh has 190154 nodes and 1048701 elements.
Fig 2.6: Schematic diagram of the meshing
When meshing is complete, named selections are provided to the various parts of the model, outer walls of the cylinder and coil and the inlet and outlet for the working fluid. The named selections prove to be helpful when selecting specific parts or faces or while providing the boundary conditions.
The meshed model file is then loaded in the ANSYS Fluent interface for the simulation.
-
Governing equation
The general governing equations solved for the simulation of melting and solidifications include all conservation equations for mass, momentum, and energy. In this study, the enthalpy model is adopted, which is most commonly applied for modeling the PCM melting and solidification processes
-
Continuity Equation
()
+
t
(u)
x
(v)
+
y
(w)
+ = 0
z
-
Momentum Equation
(u)
(uu)
(uv)
P u
Figure 2.4: Copper helical coil in longitudinal view
+ +
t x
= + µ [
y x x x
+ y
u
µ
µ
[ ] + Auy
(v)
+
t
(vu)
x
(vv)
+
y
P
= +
y
v
µ [
x x
v
µ [
y y
] + Av + g(T Tm)
Time 315 min
Where , , , g and Tm are density, dynamic viscosity, volume thermal expansivity, gravitational acceleration and melting point of the PCM, respectively. Au and Av are momentum dissipation source items
-
Energy equation
Time 420 min
(h)
t
(uh)
+ +
x
(vh)
=
y
T ( ) +
x x x
T
( )
y
Fig 3.1: Contours of mass fraction
3.2 Contours of Temperature
3. RESULTS AND DISCUSSION
The numerical study of melting of paraffin wax in a close cylinder by a helical heat pipe is done. The results of the simulation were recorded at regular intervals of 105min for a complete melting cycle of 420 minutes (7 hrs). Those results are represented as contours of mass fraction, temperature and density.
3.1 Contours of mass fraction
Fig 3.1 represents the variation of mass fraction with time. We can easily examine the shape and motion of melting interface as the time passes. The red color represents the condition when material is completely liquid (=1) and blue color represents the condition material is completely solid (=0). The mushy zone represents the melting front; it separates the liquid and solid region. We can observe that at the initial stage time = 105 min of melting process the melting interface is almost around the surface of the heat pipe, whih indicates that in early stages the heat transfer is mainly by conduction.
Time – 1 min
Time 105 min
Time 210 min
Fig 3.2 represents the contours of temperature and the variation in temperature after regular interval of 105 min each. It can be analyzed that from the figure that the maximum temperature achieved is 320K during the initial stage and 330K at the later stages of the melting process. The blue color shows the low temperature zone. The shape of this zone resembles to that of the solid PCM in the PCM domain as shown in the Fig 3.1. There is a red zone developing in the PCM domain nearer to the surface of heat pipe after 105min, and it gradually increases in size. This is because of the turbulence effects present in the liquid PCM. At the end of the melting process all the PCM is in liquid phase and the properties becomes constant so constant temperature zones have been developed which can be clearly seen in Fig 5 for Time = 420 min.
Time 1 min
Time 105 min
Time 210 min
Time 315 min
Time 420 min
Fig 3.2: Contours of Temperature
-
Contours of Density
Fig 3.3 represents the contours of density and the variation in density after regular interval of 105 minutes each. The density of the PCM changes with increase in temperature. So as the temperature increases the density of the PCM decreases and it rises up, gets accumulated at the top and form a zone of low density PCM at the top; which is shown by blue color in the Fig 6. At the end of the melting process the density of the PCM domain is constant and the value of the density at time 420min is 998 kg/m3.
Time 1 min
Time 105 min
Time 210 min
Time 315 min
Time 420 min
Fig 3.3: Contours of density
-
-
CONCLUSIONS
After this numerical modeling and simulation of PCM melting process with constant heat flux condition the following conclusions can be drawn:
-
Numerical simulation of horizontal cylindrical shell with helical tube structure is carried out find the charging time of Phase change material (PCM). Simulation are carried out at inlet condition of mass flow rate is 0.1m/sec, and fallowing observation were made.
-
Low thermal conductive phase change material keep more temperature gradient due to lagging in heat transfer, helical tube can distribute the heat around the circumference at a certain radius.
-
Upper portion of cylinder melt faster than lower portion, due to rapid temperature distribution in upper part.
-
Charging enhancement can be achieved by adding certain high conductive nanoparticles in phase change material so the temperature can be distributed uniformly throughout the cylinder.
REFERENCES
-
Heat transfer enhancement of phase change materials for thermal storage applications: A critical review (Nasiru I. Ibrahim Ahmet Z. Sahin) Sciencedirect, July 2017.
-
Design and fabrication of Alternative energy storage device using PCM (Prabhu M. Ramalingam, R. Manivannan, G. Naveen, K. Balasubramaniam) Journal of Chemical and Pharmaceutical Sciences, Jan-March 2017.
-
Experimental Performance Enhancement of Thermal Storage with PCM (P. Sundaram) Journal of chemical and pharmaceutical sciences, Oct-Dec 2016.
-
Solar thermal energy storage with phase change material Heat exchanger Design and heat transfer analysis (Xi-li duan, Stephan Ryan, Josh Roul, John Stamp, Skylar Hodder) 2nd International Conference on Sustainable Development (ICSD 2016).
-
Review of phase change material with nanoparticle in engineering applications (C. Kaviarasu, D. Prakash) Journal of engineering science and technology review, 7 Sept 2016.
-
Nanoparticle enhanced phase change material in latent heat thermal energy storage system: An experimental study (Muath A. Alomar, Yazeed A. Alomar) proceeding of the international conference of energy harvesting, storage and transfer (EHST17) Paper no. 19.
-
Review on Phase Change Materials with Nanoparticle in engineering applications (C. Kaviarasu and D. Prakash) Journal of Engineering Science and Technology review 9.4 (2016) 26-386.
-
Dispersing different nanoparticles in paraffin wax as enhanced phase change materials: A study on the stability issueJune 2018 Journal of Thermal Analysis and Calorimeter.
-
ANSYS FLUENT 15.0 Users Guide.
-
Sharma, Atul, et al. Review on thermal energy storage with phase change materials and applications. Renewable and Substantial energy reviews 13.2 (2009): 318-345.