
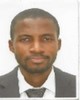
- Open Access
- Authors : Akinbomi J. G. , Obafaiye A. G , Akinyemi O. P , Salami L, Patinvoh R. J, Adesina A. A, Aminu K. A
- Paper ID : IJERTV11IS010195
- Volume & Issue : Volume 11, Issue 01 (January 2022)
- Published (First Online): 07-02-2022
- ISSN (Online) : 2278-0181
- Publisher Name : IJERT
- License:
This work is licensed under a Creative Commons Attribution 4.0 International License
Evaluation of Carbon Black Usage in Shoe Polish Production
1,*Akinbomi, J.G., 2 Obafaiye, A.G., 3Akinyemi, O.P., 4Salami, L.,
5Patinvoh, R. J., 6 Adesina, A.A. 7Aminu, K.A.
1Department of Chemical Engineering, Lagos State University, Epe Campus,
2Centre for Environmental Studies and Sustainable Development, Lagos State University, Ojo Campus,
Abstract:- Nonbiodegradable nature of plastics bottles, pure water nylon sachets, rubber tyres and battery wastes has made people to resort to non-environmental friendly techniques including unsanitary landfilling, burning and ocean dumping to dispose the polymeric wastes, which, consequently, have negative environmental and health impacts. However, conversion of the polymeric wastes into carbon black materials that can be used as pigments in shoe polish production is an effective and environmentally friendly disposal technique for the polymeric wastes. This study, therefore, aimed at examining the effects of using carbon black materials derived from polymeric wastes as black pigments in shoe polish. Distinctive process variables tested during the shoe polish production included type of water repellant, source and particle size of carbon black, as well as, process temperature. The shoe polish samples produced were applied on shoe leathers and the physical properties including wrinkle resistance, gloss, rub resistance; resistance to fading and dust absorption, of the shoe leathers were assessed. Based on the results, shoe polish samples produced using used vegetable oil, (p=0.374) as water repellant; carbon black from plastic bottle wastes (p value of 0.178) as dye; temperatures of 80 and 90C (p value of 0.178) and carbon particle size of 0.25mm (p value of 0.178) showed physical properties that were not significantly different from that of the commercial KIWI shoe polish.
Keywords: Carbon black, Polymeric wastes, Physical property, Shoe polish, Waste valorization
-
INTRODUCTION
Rubber tyres, pure water nylon sachets, polyethylene terephthalate (PET) bottles and batteries are valuable engineering and household materials due to their light weight, durability and strong qualities [1]. Moreover, most electronic devices are powered by batteries which will be disposed when they wear out. However, some of the attractive qualities of the polymeric materials including durability, resistance to light, acid, microbial attack, as well as, biological degradation, have created a challenge for effective management of the discarded polymeric wastes. The non-biodegradable nature of these polymers makes them to remain in the environment for long period of time after their disposal causing the littering of the discarded polymeric wastes which is a common phenomenon in most developing countries, especially, Nigeria. Unfortunately, indiscriminate disposal of wastes results in significant negative impacts on health and environment.
Disposal of discarded rubber tyres, pure water nylon sachets, polyethylene terephthalate (PET) bottles and batteries can be effectively managed by using carbon black materials from these polymeric wastes as pigments in shoe polishes[2-4]. Carbon black materials from batteries is got by open up the batteries while carbon black from tyres, pure water nylon sachets, polyethylene terephthalate (PET) bottles can be effectively got through pyrolysis process [5]. Besides employment generation, valorization of polymeric wastes through the usage of their carbon black pigments in shoe polishes will reduce, to a great extent, the level of environmental pollution and negative health impact from indiscriminate disposal of the polymeric wastes. Shoe polish is a surface coating material usually wax or cream based which is applied to the surface of a shoe material to protect, smoothen , shine and make it proof to water, solvents or dust, as well as improve performance and durability of the shoe material [6, 7]. A good shoe polish should be glossy, quick drying, adhesive, thin and prevent shoe surface from deterioration.
Various studies have been conducted on polymeric waste valorization through conversion to wax or carbon black pigments for shoe polish production [8, 9]. For example, Gumel and Uma[8] carried out a comparative study of performance of shoe polishes formulated from polyethylene and carbon black. Also, Ameh [9] conducted a study on thermophysical properties of shoe polish manufacture from pure water sachet. However, gap still exists in these studies as regards investigating the effects of experimental process variables including type of water repellant agent, source and particle size of carbon black, as well as, process temperature; on the quality of shoe polishes. Therefore, the aim of this study was to assess the effects of using carbon black from plastics, rubber, batteries and nylon wastes as black pigments in shoe polish production as re-processing of non- biodegradable wastes into value-added product such as shoe polish can greatly contribute to a greener environment. Investigation was carried out on effects of different process variables including temperature, carbon black particle size, carbon black source and type of water repelling agent, on the quality of shoe polish produced. The shoe polish produced was applied on finished black leather while physical properties such as wrinkle resistance, gloss, rub resistance, fading resistance and dust absorption resistance were evaluated and compared to KIWI commercial shoe polish
-
MATERIALS AND METHODS
-
Materials / Equipment
The materials and equipment used during the study included discarded PET bottles, rubber tyres, water sachets, batteries, fresh and used vegetable oils, isopropanol, paraffin oils, water baths, thermometer, canoe bar soap, candle was, gum Arabic, lime oranges, kerosene, carbon black, KIWI commercial shoe polish, leathered shoes, aluminum pots, stirrer, kerosene stove, shoe polish packaged containers, pouring utensils, cooling equipment for the polish to set, stop clock, thermometer, scale balance, as well as, pyrolysis system. The pyrolysis system comprised of gas-fired furnace, pyrolysis reactor, heavy oil condenser, two cyclones for light oil condensation, scrubber for gas cleaning, and gas storage bag (Figure 1). The pyrolysis reactor was a cylindrical steel vessel with thickness, internal diameter and capacity of 12 mm, 250 mm, and 25 kg of shredded polymeric waste, respectively. The reactor vessel was closed with two pairs of flanges (top and bottom). There was a hole in the center of the reactor vessel which served as the gas exit. The gas-fired furnace was made in such a way that it would provide uniform heat to the pyrolysis reactor. Solar-power temperature sensor was inserted in the reactor vessel to measure the temperature in the pyrolysis reactor (Figure 2).
The discarded PET bottles, rubber tyres, water sachets and batteries were collected from dumpsites around Lagos State University, Ojo, Lagos, Nigeria. Reinforced steel was removed from the waste tyres before they were shredded manually into chips, washed with clean water, and then spread under the sun for drying. Chemical balance, measuring cylinder, and stop clock were also used during the pyrolysis experiment for measuring feedstock weight, cooling water volume, and progressing reaction time, respectively. Empty containers were also prepared for the collection of condensed liquid oil and char.
-
Experimental Procedure
The experimental procedure was in two stages; the first stage was the conversion of polymeric wastes into carbon black while the second stage was the usage of the obtained carbonblack in shoe polish production. The first stage involved conversion of the polymeric wastes except batteries into carbon black materials and other products through pyrolysis process. The batteries were open up to obtain the carbon black. The pyrolysis reactor containing 9 kg each of the dried shredded polymeric wastes was placed inside liquefied petroleum (LPG) gas-fired furnace for batch pyrolysis process. Before starting the pyrolysis process, between 20 and 30 litres of clean water were measured into each of the two cyclones used for light oil condensation. The 9 kg of each of the shredded polymeric wastes was pyrolyzed separately at a temperature range between 236C and 488 C. The temperature was maintained for about 5 hours (residence time) at 488 C. At the end of the pyrolysis experiment, the non- condensable gas was collected in a gas storage bag while the condensable liquid oil was collected in containers. The furnace was left to cool down to room temperature (25C) before the char left in the reactor vessel was removed.
The second stage involved production of shoe polish samples using different components including the carbon black materials (Table 1). Specific amounts of the required feedstock materials (including candle wax, carbon black, vegetable oil, gum, lime oranges except the flammable alcohol and kerosene) were measured into the aluminum pot placed on electric cooker. The mixture inside the aluminum pot was stirred thoroughly until the temperature reached various degrees of temperature including 60oC, 70°C, 80oC, 90°C and 100oC.The mixture inside the aluminum pot was removed from the hot electric cooker and poured into a glass beaker. Isopropanol and kerosene were introduced into the mixture while stirring. The resulting mixture was divided into two equal parts (50ml). The two equal parts were put into separate glass containers while 30ml of each mixture was poured into the customized packaging steel container and allowed to cool. The remaining 20ml of each mixture was poured into a container for test analysis.
After production of the shoe polish, physical tests were conducted to determine the quality of the shoe polish samples produced. The parameters evaluated include gloss, rub resistance, fading resistance, dust absorption resistance and wrinkle resistance. The polished samples were examined for their gloss by comparing them with one another. To test for rub resistance, the polished leather samples were rubbed with white and clean cotton material for about 40 times. The change in hue and level of stain were examined. The polished leather samples were tested for fading resistance by exposing them to the sun for 74 hours. Finally change in hue and glosses were used to access the parameter. To test for dust absorption resistance, the polished leather samples were exposed to an open environment, where dust could get easy access to them for 24 hours. The level of dust adsorption was then examined. Regarding the wrinkle resistance, the polished leather samples were each held at both end and creased to see if the polish would peel off the leather.
-
-
RESULTS AND DISCUSSION
Table 3 shows the qualities of various shoe polish samples using varying experimental process variables including water repellant, source and particle size of carbon black and temperature. For the distinctive factor of water repellant, the three substances used which include paraffin oil, fresh and used vegetable oils exhibited very good gloss, wrinkle and fading resistance properties. This indicates that any of the three substances can be used as water repellant in shoe polish without change in these physical properties. However, in terms of rub resistance, used vegetable oil did not show very good performance and only fresh vegetable oil showed very good performance as regards dust absorption resistance.. Regarding the carbon black source, it was observed, after carrying out physical observations on the shoe polish samples, that shoe polish samples made with
carbon black from tyre had poor qualities of all the tested physical characteristics. The reason might not be unconnected with high mechanical strength due to rubber vulcanization with sulphur. Shoe polish samples with carbon black from battery demonstrated very good luster and dust absorption resistance properties. Shoe polish samples with carbon black from plastics bottle showed very good gloss property while those shoe samples with carbon black from water sachets indicated very good fading resistance quality.
Regarding distinctive factor of temperature, the results showed that producing shoe polish at 100C would give only very good wrinkle resistance; producing shoe polish at 90C would demonstrate very good properties of gloss, fading and wrinkle resistances while producing shoe polish at 80C would give very good properties of fading, dust absorption and wrinkle resistances. Shoe polish samples produced at 90 and 80C showed properties that were similar to commercial KIWI shoe polish. At 70 and 60C, shoe polish samples produced demonstrated very good rub resistance property besides very good dust absorption and wrinkle properties demonstrated by shoe samples produced at 70 and 60C, respectively. Concerning particle size of carbon black as distinctive factor, shoe polish samples produced using the smallest particle size of 0.25mm showed very good properties of gloss, fading resistance and wrinkle resistance. For the particle size of 0.045mm, the shoe polish samples showed very good rub and dust absorption resistance properties while the shoe polish samples with 0.08mm showed very good rub and wrinkle resistance properties.
Statistical analysis of the physical properties of the shoe polish samples in comparison with the commercial KIWI shoe polish was done to determine if there were significant differences between the physical properties of the shoe polish samples and that of the commercial KIWI shoe polish. The Minitab paired t-test was used to analyze if there was significant mean difference between the property value associated with each of the distinctive process variables of the shoe polish samples and that of the commercial KIWI shoe polish. Representative values were assigned to the quality level of the physical properties of shoe polish samples (Table 2). From the results presented in Table 3, it could be observed that all the distinctive process variables tested had associated p-values that were greater than -level = 0.05 which indicated the non-significant difference in physical properties when compared with that of commercial KIWI shoe polish. Only shoe polish samples produced at temperature of 100C had p- value of 0.016 which was less than -level = 0.05 indicating significant difference between the physical properties of the shoe polish sample and that of the commercial KIWI shoe polish. Based on the results of the statistical analysis for distinctive process variables; in comparison with commercial KIWI shoe polish; used vegetable oil (p value of 0.374), carbon black from plastics bottle wastes (p value of 0.178), temperatures of 80 and 90C (p value of 0.178), and carbon particle size of 0.25mm (p value of 0.178), seemed to be the best experimental process variable for shoe polish samples with physical properties that were not significantly different from that of the commercial KIWI shoe polish.
-
CONCLUSION
The study had focused on the evaluation of carbon black usage in shoe polish production while subjecting it to various experimental process variables including type of water repellant agent, process temperatures, as well as source and particle size of carbon black material.. The results showed that shoe polish samples produced using used vegetable oil, (p=0.374) as water repellant; carbon black from plastic bottle wastes (p value of 0.178) as dye; temperatures of 80 and 90C (p value of 0.178) and carbon particle size of 0.25mm (p value of 0.178) showed physical properties that were not significantly different from that of the commercial KIWI shoe polish. The sudy demonstrated that besides employment generation, valorization of polymeric wastes through the usage of their carbon black pigments in shoe polishes will reduce, to a great extent, the level of environmental pollution and negative health impact from indiscriminate disposal of the polymeric wastes, thereby contributing to a greener environment.
REFERENCES
-
Mastral, J.F., C. Berrueco, and J. Ceamanos, Pyrolysis of high-density polyethylene in free-fall reactors in series. Energy and Fuel, 2006. 20(4): p. 1365-1371.
-
Taiwo, A.J. and C.U. Ameh, Preliminary studies on properties of shoe polish formulated from wax produced from waste water sachets. International journal of engineering and innovative technology (IJEIT), 2013. 1-5(5): p. 120-123.
-
Roy, C., A. Chala, and H. Darmstadt, The vacuum pyrolysis of used tires End-uses for oil and carbon black products. Journal of Analytical and Applied Pyrolysis, 1999. 51: p. 201221.
-
Quek, A. and R. Balasubramanian, Liquefaction of Waste Tires by Pyrolysis for Oil and Chemicals-A Review. Journal of Analytical and Applied Pyrolysis,, 2013. 101: p. 1-16.
-
Martinez, J.D., N. Puy, R. Murillo, T. Garcia, M.V. Navarro, and A.M. Mastral, Waste Tyre PyrolysisA Review,. Renewable and Sustainable Energy Reviews,, 2013. 23: p. 179-213.
-
Guthrie, J.T. and I. Lin, Physical and Chemical Aspect of pigment Application. 1994, U.K: OCCA.
-
Turner, G.P.A., Introduction to Paint Chemistry and Principles of Paint Technology. 3rd ed. 1993, London: Chapman and Hall,.
-
Gumel, S.M. and A. Umar, COMPARATIVE STUDY OF PERFORMANCE OF SHOE POLISHES FORMULATED FROM POLYETHYLENE AND CARBON BLACK (C. I. BLACK PIGMENT 7). Chemsearch Journa, 2011. 2(1-2): p. 42 – 44.
-
Ameh, C.U., Thermophysical Properties of Shoe Polish Manufactured from Pure Water Sachet AU J.T. , 2011. 15(2).
-
Akinbomi, J.G., S.O. Asifat, A. Ajao, and O. Oladeji, eds. Asphalt Making Potential of Pyrolytic Bitumen from Waste Rubber Tyres: An Adaptive Measure to Climate Change. Handbook of Climate Change Resilience, ed. W. Leal-Filho. 2019, Springer: Cham.
Figure 1. Pyrolysis system setup[10]
Figure 2. Gas-fired furnace with attached solar-powered temperature sensor[10]
Table 1. Components of shoe polish samples
S/N |
Components |
Function |
Amount (g) |
1 |
Carbon blaack |
It acts as dye or colourant |
20 |
2 |
Candle wax |
It acts as softener and water repellant agent |
20 |
3 |
Paraffin wax |
It acts as a water repellant |
20 |
4 |
Isopropanol |
It acts as a softener for dissolving grease, wax and oil; as well as a volatilizer to give quick drying effect |
20 |
5 |
Gum arabic |
It acts as a thickener or adhesive |
5 |
6 |
Lime orange juice |
It acts as a Fragrance |
5 |
7 |
Kerosene |
It acts as a preservative |
10 |
Table 2, Representative values for the quality level of the physical properties of shoe polish samples
Physical Property |
Property Quality |
Representative Value of Property Quality |
Lustre/Gloss, Rub Reistance, Fading resistance, Dust Absorption Resistance, Grease/Wrinkle resistance |
Very good |
4 |
Good |
3 |
|
Fair |
2 |
|
Poor |
1 |
Published by : http://www.ijert.org
International Journal of Engineering Research & Technology (IJERT)
ISSN: 2278-0181
Vol. 11 Issue 01, January-2022
Table 3. Comparative analysis of shoe formulations with commercial KIWl shoe polish
S/N |
Shoe polish formulation with distinctivefactor |
Physical Properties of Shoe Polish |
||||||||||
Lustre/Gloss |
Rub Resistance |
Fading Resistance |
Dust Absorption Resistance |
Wrinkle Resistance |
P-Values |
|||||||
Quality |
Value |
Quality |
Value |
Quality |
Value |
Quality |
Value |
Quality |
Value |
|||
Standard: KIWI commercial shoe polish |
Very good |
4 |
Very good |
4 |
Very good |
4 |
Very good |
4 |
Very good |
4 |
||
1 |
Water repellant: fresh vegetable oil |
Very good |
4 |
Good |
3 |
Very good |
4 |
Good |
3 |
Very good |
4 |
0.178 |
2 |
Water repellant: used vegetable oil |
Very good |
4 |
Very good |
4 |
Very good |
4 |
Good |
3 |
Very good |
4 |
0.374 |
3 |
Water repellant: Paraffin oil |
Very good |
4 |
Good |
3 |
Very good |
4 |
Good |
3 |
Very good |
4 |
0.178 |
4 |
Dye (cabon black) from pyrolytic plastic bottle wastes |
Very good |
4 |
Good |
3 |
Very good |
4 |
Good |
3 |
Very good |
4 |
0.178 |
5 |
Dye (cabon black) from pyrolytic discarded vehicle rubber tyre |
Poor |
1 |
Poor |
1 |
Poor |
1 |
Poor |
1 |
Poor |
1 |
– |
6 |
Dye (cabon black) from pyrolytic pure water nylon sachet |
Good |
3 |
Good |
3 |
Very good |
4 |
Good |
3 |
Very good |
4 |
0.099 |
7 |
Dye (cabon black) from discarded Tigerhead battery (1.5V) |
Good |
3 |
Very good |
4 |
Good |
3 |
Very good |
4 |
Good |
3 |
0.070 |
8 |
Temperature at 100C |
Good |
3 |
Good |
3 |
Good |
3 |
Good |
3 |
Very good |
4 |
0.016 |
9 |
Temperature at 90C |
Very good |
4 |
Good |
3 |
Very good |
4 |
Good |
3 |
Very good |
4 |
0.178 |
10 |
Temperature at 80C |
Good |
3 |
Good |
3 |
Very good |
4 |
Very good |
4 |
Very good |
4 |
0.178 |
11 |
Temperature at 70C |
Good |
3 |
Very good |
4 |
Good |
3 |
Very good |
4 |
Good |
3 |
0.070 |
12 |
Temperature at 60C |
Good |
3 |
Very good |
4 |
Good |
3 |
Good |
3 |
Very good |
4 |
0.070 |
13 |
Dye (Carbon black) particle size of : 0.25 mm |
Very good |
4 |
Good |
3 |
Very good |
4 |
Good |
3 |
Very good |
4 |
0.178 |
14 |
Dye (Carbon black) particle size of : 0.45 mm |
Good |
3 |
Very good |
4 |
Good |
3 |
Very good |
4 |
Good |
3 |
0.070 |
15 |
Dye (Carbon black) particle size of : 0.80 mm |
Good |
3 |
Very good |
4 |
Good |
3 |
Good |
3 |
Very good |
4 |
0.070 |
IJERTV11IS010195
www.ijert.org
(This work is licensed under a Creative Commons Attribution 4.0 International License.)
495