
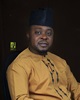
- Open Access
- Authors : Shittu N. Olawale , Job O. Fredrick , Edeh E. Ochayi , Pam Miriam
- Paper ID : IJERTV10IS080156
- Volume & Issue : Volume 10, Issue 08 (August 2021)
- Published (First Online): 28-08-2021
- ISSN (Online) : 2278-0181
- Publisher Name : IJERT
- License:
This work is licensed under a Creative Commons Attribution 4.0 International License
Effect of Nanosilica on the Concrete Subjected to Physical Sulphate Attack (PSA)
Shittu N. Olawale, Job O. Fredrick, Edeh E. Ochayi, Pam Miriam
Department of Building, University of Jos, Nigeria
Abstract:- There are still research gaps regarding the effects of nano particles such as nano silica (NS) on the response of concrete to special forms of sulphate attack: physical salt attack (PSA). Hence, this study aims at developing an innovative type of concrete: nano- modified concrete, incorporating various dosages of nano-silica (NS), and explores its efficiency in resisting deterioration of concrete caused by physical sulphate attack. PSA on concrete is a distress caused by the crystallization of salts in pores near drying faces or evaporative zones, which leads to progressive scaling and flaking of the concrete surface. Although numerous concrete structures are at risk of PSA during service, there is currently no standard test method for PSA of cement-based materials. Therefore, an accelerated laboratory test was developed in this research to assess the resistance of nano-modified concrete to PSA. The effects of 0%, 2%, 4%, and 6% addition of nano-silica by mass of cement on the resistance of concrete to PSA were investigated. The assessment criteria were based on mechanical properties (Compressive, Split Tensile and Flexural strength tests), durability property (Water Absorption Test), and physical properties (visual appearance and mass loss). Results showed that overall performance of concrete was significantly improved with the addition of variable dosages of nano-silica. At all curing ages, the strength generally increased with the addition of nano-silica up to 6%. In particular, at 28 days of curing, the compressive strength was considerably improved for mixtures containing 6% nano-silica (i.e. 27 N/mm²). The Split tensile strength was improved especially for concrete mixtures containing 6% nano-silica (i.e.
-
N/mm²). The flexural strength was also improved particularly for the concrete mixtures containing 4% nano-silica (4.00 N/mm²). Air-content of freshly produced concrete incorporating 6% NS was reduced due to filler effect of nano-silica particles. The water absorption tests showed that concrete mixtures containing different dosages of nano-silica had low water absorption, this might be due to the filler effect of nano-silica particles. Damage manifestations and mass loss results showed that the proposed test procedure was capable of replicating PSA on concrete within a short time interval (60 days), and hence it might be used to prequalify concrete mixtures for exposures conducive to PSA. The results of both visual assessment and mass loss showed that concrete mixtures incorporating nano- silica at different dosages had better sulphate resistance considerably when compared with the control concrete mixtures. It can be concluded that the overall performance of concrete was significantly improved with the addition of variable dosages of nano-silica, and concrete mixtures containing nano-silica at different dosages had better resistance in PSA exposure than ordinary Portland cement concrete.
-
INTRODUCTION
The deterioration of concrete structures can be linked to various sources, such as temperature, solution concentration and exposure of concrete to salts. But the most prominent is the attack of concrete by sulphate. Oxides of sulphur, especially sulphate SO4, are injurious to concrete; while chlorides are harmful to the reinforcing steel [1]. Sulfate attack is a severe and rapid degradation mechanism that may cause critical damage to concrete structures. The driving force of sulfate attack may have a physical and chemical nature [2]. Chemical sulfate attack, which involves chemical interaction between sulfate salts and cement minerals, is distinguished from physical sulfate attack (PSA), which is caused by crystallization and phase transitions of sulfate salts [3]. Such terms as salt scaling, salt weathering, or salt hydration are often used to designate the deterioration by PSA [4].
According to Thanos et al. [5], there are different types of sulphate attack, and the most common sulfate that attack or interact with concrete are Calcium, Sodium, and Magnesium sulphate, which are listed in order of their aggressiveness. The ensuing damage to concrete structures depends on the concentration levels of these species, the water permeability of the soil surrounding the structures and the amount of solution in contact with the surface of concrete elements [6]. Although, several studies during the formative years of investigation on sulphate attack have explored the associated mechanisms and how they can be mitigated since sulphate attack is a major threat to historical monuments and buildings, but it appears that the deterioration of concrete due to salt crystallization (i.e. PSA), has been over-looked and often confused with chemical sulphate attack [3, 7, 8].
In a bid to investigate the concrete resistance to physical sulphate attack (PSA), there are different exposure conditions for concrete testing reported in the open literature, and Zhutovsky & Hooton [9] classified these exposure conditions into three groups in regard to the interaction of the tested specimens with sulphate solution: (a) specimens subjected to immersion and drying cycles [10, 11] (b) partially immersed specimens [12, 13], and (c) fully immersed specimens [9, 13].
According to [9], in the first group, the crystallization and phase changes between mirabilite and thenardite are triggered by alterations in internal relative humidity (RH) that are produced by wetting and drying cycles. The problem with this approach is that a long time is required to reach RH equilibrium inside a specimen and there will be always a gradient of moisture across the specimen section. This results in slow and partial conversion of thenardite to mirabilite. For this reason, the time of testing needed to reach the level of damage necessary to quantify resistance of concrete to PSA is relatively long. In the approach with partial immersion of specimens, capillary action pulls the sulfate solution from the submerged part upward and crystallization of sulfate salts inside pores is induced by the increase of sulfate concentration due to evaporation. If this approach is combined with thermal
cycling the rate of deterioration may be high, but the localization of the damage to the zone of evaporation makes quantitative evaluation of the resistance to PSA difficult.
Folliard & Sandberg [14], stated that the most promising exposure condition for accelerated testing of concrete resistance to PSA seems to be thermal cycling of fully immersed specimens in concentrated sodium sulfate solution. This exposure condition is the most rapid and severe in comparison with other two approaches. Using the exposure condition of thermal cycling between 5oC and 30oC in 30 wt% sodium sulfate solution, [14] attained complete disintegration of 25 mm concrete cubic specimens with w/b ratio of 0.50 after just 30 cycles. The thermal equilibrium through a specimens cross-section can be achieved easily and rapidly. Thus, the reduction of temperature causes consistent crystallization of thenardite absorbed inside the specimen with further conversion to mirabilite. The significant crystallization pressure generated by such thermal cycles result in accelerated deterioration. Because the whole specimen is immersed in sulfate solution, the entire surface of the specimen is subjected to the process of deterioration, so the extent of damage is high, and thus easy to characterize quantitatively. Consequently, becaue the thermal cycling between 5 and 30oC in 30 wt% sodium sulfate solution resulted in the most extensive and rapid deterioration, these exposure conditions were adopted in the current research as the basis for accelerated testing of cementitious materials for PSA resistance.
-
MATERIALS
In this study, Dangote cement and nanosilica particles are utilized as binding materials in concrete. Locally available natural gravel (max. size of 10 mm) was used as coarse aggregate; its specific gravity and bulk density were 2.92 and 1488.6kg/m3, respectively. The fine aggregate was well graded river sand with a specific gravity and bulk density of 2.58 and 1454kg/m3 respectively. Both aggregates were procured at the various deposits within Jos, Plateau state of Nigeria. The cement was obtained from open market in Jos, which was produced by the Obajana factory of Dangote cement in Kogi state, since their products conform to the requirements of BS 812 (1991) for ordinary Portland cement. Its specific gravity was 3.15. Tap potable water available in the laboratory was used for mixing and curing of the concrete.
Nanosilica particles was processed and obtained from the Chemistry department of University of Jos, Nigeria, with specific gravity of 2.63 and particle size of 49.7nm.
Table 1. Chemical Composition of the Cementitious and Nanosilica Materials.
Chemicals Composition/ Proportions
Cement
Nano-Silica
SiO2 (%)
20.62
99.8
Al2O3 (%)
6.01
Fe2O3 (%)
3.22
CaO (%)
59.6
MgO (%)
3.65
SO3 (%)
2.46
K2O (%)
0.71
Specific Gravity (%)
3.15
2.63
Loss on Ignition-LOI (%)
8.5
6.0
Insoluble Residue-IR (%)
4.7
Specific Surface Area-SSA (m²/kg &
nm)
358
49.7
-
METHODS
To assess the strength and durability characteristics of the nano-modified concrete, this study was split into three experimental phases. Firstly, plastic properties (i.e., slump and compaction factor), secondly mechanical properties (i.e. compressive, split tensile, and flexural strengths), and lastly water absorption test and resistance of concretes exposed to accelerated PSA condition were evaluated. In this research work, four different concrete mixtures (i.e. 0%, 2%, 4% and 6% NS replacement of cement) were evaluated, and total concrete specimens cast were 56 cubes, 20 cylinders and 12 beams.
At the end of initial and final curing, concrete specimens from each concrete mixtures were tested for compressive (3, 7, 14, & 28 days), flexural and split tensile (i.e., 28 days) strengths in accordance with BS 12390 parts 1-7 (2000-2002: Testing of hardened concrete). Secondly, an accelerated laboratory test procedure was designed to evaluate the resistance of concrete to PSA. Therefore, based on this exposure, concrete prepared from 0%, 2%, 4%, and 6% of nano-silica (NS) particles replacement by mass of cement content at constant w/cm ratio of 0.45 were evaluated by visual assessment and mass change.
For compressive strength test, the concrete cubes of 100mm size were cast for finding the compressive strength. The prepared cubes were cured in water for 3, 7, 14, and 28 days respectively. The cured specimens were taken out and dried after each curing
age. After drying, the specimen is loaded using compression testing machine. The compressive strength of concrete cube specimens was investigated by measuring the load and it was calculated by using the equation
Fc = P/A.
For split tensile strength test, concrete cylinders of 100mm diameter and 300mm height were cast and cured in water for 28 days for finding the split tensile strength and it was calculated by using the equation
Split tensile strength =0.637P/DL.
Where P=Load applied, D=diameter of cylinder, L=Length of cylinder.
For flexural strength test, the concrete beams of 100x100x500mm size were cast and cured in water for 28 days for finding the flexural strength. After the specimens were taken out and dried, they were loaded one after the other using Universal testing machine. The flexural strength of beam was investigated by measuring the load and it was calculated by using the equation
Fcr = PL/bd^2. Where Fcr = Flexural strength, P =Applied load, b= Measured width d = Measured depth.
For durability test, water absorption and accelerated PSA tests were carried out, since the performance of concrete subjected to many aggressive environments is a function, to a large extent, of the penetrability of the pore system. In unsaturated concrete, the rate of ingress of water or other liquids is largely controlled by absorption due to capillary rise. For water absorption test, after 28 days curing, the specimen was taken out from the curing tank. The specimen were dried for 24 hours. The dried specimens were weighed accurately and noted as dry weight. The dried specimens were immersed in water. Weight of the specimen at pre- determent intervals was taken after wiping the surface with dry cloth. This process was continued not less than 48 hours or up to constant weight is obtained in two successive observations. Water absorption was calculated as follow;
% water absorption = [(w2w1) / w1] x 100
Where, w1= oven dry weight of cubes in grams, w2= wet weight of cubes after immersion in water at a pre-determine intervals. For PSA exposure testing, the test program involved totally immersing 8 concrete cylinders in 30wt% sodium sulphate solution (i.e., two replicate of each of the 4 tested concrete mixtures), while temperature and relative humidity are changed in repetitive cycles. Following a standard moist curing period of 28 days, the specimens were air dried for 48 hours before measuring the initial weights. To achieve the total immersion and prevent excessive evaporation of the solution, separate container was used for each specimen with air-tight lid. The containers and the specimens were placed inside a thermally controlled chamber. The solution was replaced after every 5 cycles. The highest and lowest target temperatures of the cycles were set at 50oC and 20oC respectively. The approximate duration of a complete thermal cycle was about 24hrs. In order to evaluate the damage caused by the PSA deterioration, visual inspection and mass loss were carried out. Before each measurement, all loose scale flakes and deposits were removed from the surface of specimens using a brass bristled brush. The measurements were taken every 10 cycles. Mass loss was measured using balances with a capacity of 100 kg and resolution of 0.01g.
Table 2. Specifications Test Specimens (Strengths and Durability).
S/No
Test
Size of specimens
Curing period (Days)
Total Specimens Used
1.
Cube compressive strength
100x100x100mm Cubes
3,7,14, & 28 days
48
2.
Split tensile strength
100mm diameter & 300mm height Cylinders
28 days
12
3.
Flexural strength of prism
100x100x500mm Beams
28 days
12
4.
Water Absorption Test
100x100x100mm Cubes
21 days
8
5.
PSA Test
100x300mm Cylinders
60 days
8
-
RESULTS AND DISCUSSION
-
Slump Test and Compaction Factor
The results of the slump test and compaction factor are shown in the table 3 below:
Table 3. Fresh properties of concrete (Slump and Compaction factor)
SN
Mix Id
Slump(mm)
Measured Air- content (%)
Uncompacted (kg)
Compacted (kg)
1
CC
17.00
10.86
15.10
16.94
2.
2% NS
40.00
7.02
15.90
17.10
3.
4% NS
7.00
10.42
15.48
17.28
4.
6% NS
15.20
6.47
16.20
17.32
From the table above, Air-content of freshly produced concrete incorporating 6% NS was reduced due to filler effect of nano- silica particles. The consistency of the fresh concrete produced with 6% of nano-silica was improved when compared with the control samples.
-
Compressive Strength Test
The compressive strength of concrete cubes were found for the control and concrete cubes incorporated with NS at different doses of 2%, 4% and 6% respectively. Table 4 shows the compressive strength of cubes with and without nano-silica particles.
Table 4. Average Compressive Strength of Cubes.
S/N
Mix Id ( % )
Compressive strength (N/mm2)
3 Days
Compressive strength (N/mm2)
7 Days
Compressive strength (N/mm2) 14 Days
Compressive strength (N/mm2) 28 Days
1
CC
14.5
20.3
24.5
27.0
2
2% NC
14.0
18.5
21.8
23.6
3
4% NC
14.0
18.5
20.8
22.8
4
6% NS
13.5
14.8
18.3
27.0
As shown in the table 4, at all curing ages, the strength generally increased with the addition of nano-silica up to 6%. In particular, at 28 days of curing, the compressive strength was considerably improved for mixtures containing 6% nano-silica (i.e. 27 N/mm2).
-
Split Tensile Strength Test
The Split tensile strength of concrete cylinders were found for the control concrete and concretes incorporated with NS at different doses of 2%, 4% and 6% respectively. From the table 5 below, the Split tensile strength was improved especially for concrete mixtures containing 6% nano-silica (i.e. 3.93 N/mm2).
Table 5. Average Split Tensile Strength Test of Concrete Cylinders in 28 days curing.
S/N
Mix Id (%)
Split tensile strength (N/mm2)
1
CC
3.08
2
2% NS
3.08
3
4% NS
2.97
4
6% NS
3.93
-
Flexural Strength Test
The flexural strength of concrete beams were found for the control concrete and concrete beams incorporated with NS at different doses of 2%, 4% and 6% respectively. Table 6 shows the flexural strength of concrete beams with and without nanosilica particles.
Table 6. Average Flexural Strength Test of Concrete Beams in 28 days curing.
S/N
Mix Id (%)
flexural strength (N/mm2)
1
CC
4.00
2
2% NS
3.75
3
4% NS
4.00
4
6% NS
3.25
As shown in the table 6, the flexural strength was also improved especially for the concrete mixtures containing 4% nano-silica (4.00 N/mm2).
-
Water Absorption Test
The rate of absorption was evaluated for the four mixtures to explore the relationship between PSA and the capillary rise in concrete. Table 7 below show the results of water absorption test carried out on concrete mixtures.
Table 7. Percentage Water Absorption Test for Concrete Mixtures.
S/N
Mixture Id
Dry weight (Kg)
Wet weight (Kg)
% Water Absorption
1
0%
6.46
6.70
3.72
2
2%
6.48
6.66
2.78
3
4%
6.50
6.67
2.62
4
6%
6.48
6.64
2.47
The water absorption test showed that concrete mixtures containing different dosages of nano-silica had low water absorption, this might be due to the filler effect of nano-silica particles.
-
Visual Inspection of Concrete specimens Subjected to PSA
The visual ratings of specimens at different ages of exposure are shown in Table 8 below:
Table 8. Visual rating of Damage at different ages of exposure.
Mixture Id
0 Days
10 Days
20 Days
30 Days
40 Days
50 Days
60 Days
0%
0
1
2
3
4
5
5
2%
0
0
1
2
4
5
5
4%
0
0
1
2
3
4
5
6%
0
0
1
1
2
4
5
The Visual assessment result above showed that almost all the specimens suffered from PSA distress. The specimens had slight to moderate deterioration (visual rating between 1 and 3) after 30 days, which was aggravated to moderate-to-severe deterioration (visual rating between 3 and 5) after 60 days of exposure. Eventually, all the mixtures had a visual rating of 5 (severe scaling) at the end of exposure. The NS addition reduced the amount of scaling at the early stage of exposure but starting from 55 days of exposure, all the specimens were severely deteriorated (visual rating of 5).
-
Mass Loss of Concrete specimens Subjected to PSA
The result of mass loss of concrete specimens subjected to PSA exposure was determined at different ages of exposure as shown in Table 9 below. For most of the mixtures, the rate of mass loss was low up to 20 cycles, and then it significantly increased to the end of exposure confirming to the visual assessment trend.
Table 9. % Mass Loss of Specimens at different ages of PSA exposure.
Mixture Id
Percentage Mass Loss (%)
1 Day
10 Days
20 Days
30 Days
40 Days
50 Days
60 Days
0%
0
2.7
3.2
6.7
13.5
20.3
25.0
2%
0
2.2
2.7
5.2
10.3
16.4
22.0
4%
0
1.8
2.5
4.0
8.6
10.5
13.0
6%
0
1.6
2.4
3.5
6.4
8.2
10.0
It can be noted that the specimens without NS had higher surface scaling compared to those specimens incorporated with NS Addition. At 60 days exposure, specimens containing 6% NS had better resistance to PSA (mass loss of 10%), relative to specimens from the control mixture (mass loss of 25%). All the specimens comprising NS had comparable mass loss (average of 15%) after 60 days. However, the highest percentage of mass loss (22%) was recorded for specimens with 2% NS dosage.
-
-
CONCLUSION
-
The overall performance of concrete was significantly improved with the addition of variable dosages of nano-silica particles. Damage manifestations and mass loss results showed that the proposed test procedure was capable of replicating PSA on concrete within a short time interval (60 days), and hence it might be used to prequalify concrete mixtures for exposures conducive to PSA. The results of both visual assessment and mass loss showed that concrete mixtures incorporating nano-silica at different dosages had better sulphate resistance in PSA exposure than ordinary Portland cement concrete.
REFERENCES
-
O.A. Joseph, P.A. Adekunle, A.I. Modupe, N.I. Priscilia, The effects of varying water-cement ratio on the degradation of concrete by sulphate salts, FUOYE Journal of Engineering and Technology 3 (1) (2018).
-
R.D. Hoolon, Current developments and future needs in standards for cementitous materials, Cem. Concr. Res. (78) (2015) 165177.
-
H. Haynes, R.O. Neill, P.K. Mehta, Concrete deterioration from physical attack by salts, Concr. Int. (18) (1996) 6368.
-
P.K. Mehta, P.J.M. Montteiro, Concrete Microstructure, Properties and Materials, Mc Gra W-Hill (2006).
-
D. Thanos, C.C. John, J.F. Kelvin, D. Raj, D.A.T Micheal, Laboratory and Field Evaluation of External Sulphate Attach in Concrete, Center for Transportation Research, The University of Texas (2011).
-
J. Skalny, J. Marchand, I. Older, Sulphate attack on concrete. Modern concrete Technology series, spoon press, London (2002).
-
H. Haynes, R. ONeill, N. Micheal, P.K. Mehta, Salt Weathering Distress on Concrete Exposed to Sodium Sulphate Environment, ACI Materials Journal 105(1) (2008) 3534.
-
P.K Mehta, Sulphate Attack on Concrete Separating myths from reality, Concr. Int. 22(8) (2000) 5761.
-
S. Zhutovsky, D. Hooton, Accelerated testing of cementitious materials for resistance to physical sulphate attack, Construction and Building materials (145) (2017) 98106.
-
M.T. Bossuoni, M.L. Nehdi, Durability of self-consolidating concrete to sulphate attack under combined cyclic environments and flexural loading, Cem. Concr. Res (39) (2009) 206226.
-
M.T. Bassuoni, M.L. Nehdi, Durability of self-consolidating concrete to different exposure regimes of sodium sulphate attack, Major struct. (42) (2009) 10391057.
-
M.T. Nehdi, A.R.R. Suleiman, A.M.M. Soliman, Investigation of concrete exposure to dual sulphate attack, Cem. Concr. Res (79) (2014) 395408.
-
M.T. Bossuoni, M.M. Rahman, Response of concrete to accelerated physical salt attack exposure, Cem. Conct. Res. (79) (2016) 395408.
-
K.J. Folliard, P. Sandberg, Mechanism of concrete deterioration by sodium sulphate crystallization, in: V.M Malhotra (Ed), Durab. Concr. Pro. Third CANMET-ACI Int. Conf. ACI SP1 (45) (1994) 933945.