
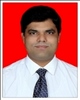
- Open Access
- Authors : Dr. Dattaji. K. Shinde , Shubhankar Ramdasi
- Paper ID : IJERTV10IS080113
- Volume & Issue : Volume 10, Issue 08 (August 2021)
- Published (First Online): 18-08-2021
- ISSN (Online) : 2278-0181
- Publisher Name : IJERT
- License:
This work is licensed under a Creative Commons Attribution 4.0 International License
Effect of FIFO Strategy Implementation on Warehouse Inventory Management in The Furniture Manufacturing Industry
Shubhankar Ramdasi
-
ech Student, Department of Production Engineering, Veermata Jijabai Technological Institute
Mumbai, India
Dr. Dattaji. K. Shinde
Associate Professor, Department of Production Engineering, Veermata Jijabai Technological Institute
Mumbai, India
Abstract Almost every industry requires inventory management. Inventory management is very important in the warehousing and e-commerce industry to ensure product availability. Warehousing & E-commerce industries are in tremendous pressure due to high competition in the marketplace. Hence, there is constant requirement to focus on inventory management technique and improve process efficiency, minimize the operational cost. Inventory holds a major portion for the expenses of the industry. This leads to focusing on improvement in inventory management model and streamlining the operations. Organizations need to have a strict adherence to inventory control and warehouse operations to continuously improve and increase the efficacy of the process, be it warehousing or E- commerce industry. Maintaining the inventory at optimum level with minimum obsolete or expiration of inventory and the lowest inventory management related expenses are the main attributes which help a company stay in the competition. In simple words, organizations need to put a continuous effort to improve their Efficiency and Effectiveness. This paper focuses on implementation of First In First Out inventory management model by redesigning the warehouse processes. The main aim of the study is to carefully analyze the existing system, identify the gaps and loopholes, concentrate on the most important areas for development, identify best practices, and ultimately propose action plans and proposals for their implementation and execution.
Keywords First In First Out (FIFO), Inventory Management, Warehouse Operations, GRN, Batch Number
-
INTRODUCTION
E-commerce industries are facing various challenges and pressure, especially the companies having their own finished product inventory to minimize the cost related with inventory handling because of day by day increasing market competition. Therefore, it is important for e-commerce industries to minimize the inventory management and operation expenses without affecting the efficiency of the process by adopting proper inventory management model. Proper inventory management aims at optimum inventory handling cost with maximum efficiency and effectiveness of the process. The study was conducted in one of the leading e- commerce industries dealing with home decor and furniture segment. The organization deals with two types of inventories, first one is 'marketplace' which is directly sold to the customers by vendors, the organizations act as a service platform & logistics partner for them. Another one is 'warehouse inventory'. This inventory is stored with the
organization in their warehouse. This study only aimed at warehouse inventory which is stored at warehouse. The material inflow in the warehouse is followed as per the Fig.1.
Fig. 1. Material Inflow at Warehouse
There are a variety of approaches that can be used in a single company, such as the just-in-time technique provided for merchandise to be delivered if it fell below a certain threshold, batch control is a mechanism that allows a firm to place an order at a predetermined time interval with a predetermined amount, the FIFO technique, which maintains stock depending on the date of receipt, is commonly used for perishable items or the items having warranty periods[1]. The general process flow at warehouse is adopted according to the Fig.2concept.
Fig.2. General Process Flow at Warehouse
First-In-First-Out (FIFO) is an acronym for "First-In, First-Out." The FIFO technique is a system for inventory control that keeps stock depending on the date (received & sale). The initial batch of products received must be sold or distributed to customers. In terms of inventory accounting models, FIFO is classified as a perpetual inventory system. The FIFO technique will ensure that the oldest stock gets flushed out and that the inventory in hand is fresh. The furniture industry year average sale for Mumbai warehouse is shown in the fig. 3.
Yearly Average sale at Mumbai Warehouse
Yearly Average sale at Mumbai Warehouse
27%
27%
Marketplace
BO SOR
Marketplace
BO SOR
17%
17%
56%
56%
Fig. 3. Category wise yearly sales
-
LITERATURE REVIEW
The FIFO method (first in, first out) is a technique of valuing First In First Out inventory based on the assumption that the first item purchased is the first thing utilized or sold, independent of physical flow[2]. The primary goal of inventory management is to improve customer service, increase buying and production efficiency, reduce inventory investment, and increase profit. The First in First Out (FIFO) approach should be utilized to improve the utilization of raw materials and reduce raw material loss owing to stock expiration. [3]. Because the first purchased item is the first one withdrawn from the inventory account, and the remaining balance comprises of goods at newer cost prices, the price put into the balance sheet becomes balanced. Equalizing the physical flow of products is one of FIFO's aims[2,4]. In the actual world, most managers adhere to the FIFO rule of inventory flow. According to studies, a FIFO issuing strategy is best for perishable and degrading inventory in a single warehouse with infinite capacity [5]. In a warehouse, an inventory information system is a system that manages transaction and inventory data. It has been observed that e- commerce businesses demand inventory management systems. Purchasing, receiving, storing, ordering, retrieving, delivering, and returning items are all part of the inventory system[6].Businesses have been using automated inventory management for a long time, and they haven't had any problems deciding which systems to employ for inventory accounting. According to the study, all companies in the industry should value and report their inventory using the FIFO approach in order to maintain consistency and uniformity[7]. The last bottleneck activity which was related to the development of Steelyard for systematic storage of steel inventory was successfully executed using a simple Load- Distance-Technique which is a handy technique of Facility Planning used to minimize material handling and travel time thereby improving your efficiency of operations [8]. The real secrete about inventory accuracy is that it is continuous improvement process. By improving inventory accuracy, the warehouse parameter like inventory turnover, inventory days, inventory value, idle time of workers etc. can be improve[9].
-
PROBLEM STATEMENT
The organization have two types of inventories first one is bought out (BO) inventory and the second one is sales or return (SOR). BO is the inventory that organization purchase from the market or from vendors and sell it, so it is inventory owned by organization itself. SOR type is somewhat different
than this. Basically, SOR inventory belongs to different vendors which is kept with organization for 90 days from the date of receiving. If the inventory is not sold in 90 days, then it will be returned to the vendor.
Ideally the inventory which is bought or received first should be dispatched first in orer to maintain the smooth flow of the inventory. The SOR inventory must be sold within 90 days of receiving to avoid the validity lapse. For this it is necessary to process the inventory is before its expiry timeline. To follow the expiry timeline there must be a strategy for inventory management. In the current scenario there are some loopholes in the system as well as processes followed. Due to these loopholes orders (inventory) are processed irrespective of its expiry which leads to expiration of validity period of SOR inventory. After the time frame of 90 days, we have to return the inventory to vendor, this will lead to potential loss to the company. The data available in the system is not sufficient to determine the foolproof picking strategy. As the system does not aware of ageing criteria and picking sequence, the picking is carried out from random locations. In such condition picking takes place irrespective of ageing of products this will lead to picking of fresh products instead of earlier received products. Also, there is lack of proper labeling on the products by which we can determine the ageing of products. All of these will lead to potential loss to the company. Thus, the main objectives of this paper is to study and implementation of Implement uniform labeling for the products, implement FIFO for warehouse inventory, and restructure the inward process for inventory to improve the warehouse management of furniture.
-
METHODOLOGY
To put together the aim employ two sorts of input: on the one hand, researchers with expertise on inventory management; and on the other hand, inventory management (related) literature. Plan-Do-Check-Act (PDCA) cycle as shown in Fig.4 is followed for the further study.
Fig. 4. PDCA Cycle
-
Plan
Before making any changes, it's important to write down what activity we're seeking to enhance and how you'll measure the change's impact.
-
Analyzing current process –
To analyze the current process, we need to collect data. During the data collection it was observed that we can see that
stock keeping units (SKUs) are stored are different locations having different inward date. But while picking the orders the inward date of the SKUs is not considered. Instead of picking older products, SKUs are picked from random locations. The current SKU transaction in the ERP is shown in the Fig.5
.
Fig. 7. Batch Number Format
As the GRN is done system will generate the batch no. and this is linked with SKU in the system so for the further processes system will consider Batch No as Ageing criteria. As the order is confirmed on website it will reflect in system & it will suggest the location for picking of SKU if there are multiple batch no available of same SKU software will suggest the SKU with earlier Batch No. and picker should pick the product from suggested location only.
-
Sequential Pallet Licensing
Pallet ID are given to pallet during inward process.
Th .
ese pallet ids are linked with Batch No So that we can
Fig. 5. SKU transaction in ERP software
The whole process from inward to dispatch, requires some basic things to be checked such as SKU, PO number, etc. This information is necessary for each product to execute the transactions. But currently there is no uniformity of information for SKUs. As each vendor follows their own labeling format which makes it difficult to track each detail required. Also the current labeling format and method are shown in the Fig.6.
Fig. 6. Current Labeling Format
track items pallet wise also it will be helpful for analyzing the pallet requirement for the warehouse operations.
There are two types of pallets are available in the warehouse. Pallet IDs for them are also different for small pallet, id will be started by PSM and for extended pallet it will start with PEX followed by 7-digit sequence number. Ex. PSM1234567
-
Label Items Clearly
It is also helpful to clearly label your items so that operators can easily identify the older items when there are multiple product choices in the same bin location. To make the labeling of items clear and uniform with required details a new template of label is introduced as per the fig. 8. Shown below.
-
-
Do
-
Implementing FIFO (Batch wise Picking)
Basic logic behind the batch wise picking is to firstly ageing criteria need to be linked with the SKU throughout the process. As the GRN is done the products are reflected in the
-
-
Check
Fig. 8. Proposed Labeling Format
AX software as inventory & the time period of 90 days will start. GRN Date is used as ageing criteria.
But only GRN date is not sufficient as after the 90 days time lapse we need to return the products to the vendor which might be received against different PO. So, to separate Batch No. is to be created. Batch No is the combination of GRN Date & PO No is shown in the Fig. 7
You should be able to measure the effect of the modification by looking at changes in the metrics once it has been implemented. Of course, you'll expect an improvement, but make sure to track it down. Many improvement measures will have little effect or possibly exacerbate the situation. The data collected after the implementation of FIFO shows that Batch No is available in the system and the picking is done according to the FIFO criteria i.e. if there are multiple batches
available in the inventory then the system will suggest the older batch available to be picked.
During the post implementation study, it is observed that if there is a SKU with same GRN date but different PO No. then the system will suggest the batch wise picking considering the older PO but in current process we are not sorting the SKUs according to the PO during inward, so it crates error during picking. To eliminate this problem inward and GRN process need to be redesigned.
-
Act
The next step will be determined by the outcome of the check phase. If the modification was successful, you should inform everyone, update documentation, or change the process description to make it permanent. To overcome issue found during verification, inward process is optimized. The inward process map before and after modification is followed and is shown in the Fig. 9. Earlier products are sorted SKU wise i.e. one pallet can be loaded only with one SKU irrespective of their PO no. But now in optimized process SKUs are sorted as one pallet-one SKU-one PO no.
Fig. 9. Inward process map before & after modification
-
-
RESULTS
From the analysis and modification of flow of inward and outward inventory and the effective labeling method and formats implementation in the warehousing management. SOR inventory we need to return to the vendor after validity lapse which results in potential sell loss to the company. But after implementation of FIFO we can clearly see the difference in the SOR RTV data as shown in the Fig.10. The quantity of products that are returned to vendor is reduced.
From Fig 10 indicated that the quantity that is returned to vendor due to validity lapse has been reduced after adopting the FIFO strategy. Batch wise picking eliminates the chances of picking a newer product even if there is an older product with valid ageing available in the inventory.
SOR RTV
30
25
20
15
10
5
0
SOR RTV
30
25
20
15
10
5
0
Months
Months
23
23
25
25
17
17
21
21
13
13
16
16
14
14
17
17
Quantity
Quantity
Fig.10. Month wise SOR RTV Data
The average SOR RTV during the period September-20 to December-20 was 21.5 which is reduced after implementation of FIFO to15 with 30% reduction in the return of item to the vendors. This means approximately 5 products are saved from returning to vendor. This results in small loss that would be occurred even if the products are returned back.
-
Elimination of Potential sale loss –
21
21
15
15
13
13
14
14
As we need to return the products to vendor after validity lapse, but in some cases, it happened if the FIFO should have been followed then we can avoid the RTV of some products. This is the potential sales loss to the company due to non- confirming the FIFO strategy is shown in the Fig. 11. This render the SOR RTV and potential sale los before and after FIFO implementation. The potential sale loss become to zero.
25
23
25
SOR RTV Potential Sale Loss
25
23
25
SOR RTV Potential Sale Loss
20
17
16
17
20
17
16
17
10
5
7
10
5
7
0
0
4
4
5
5
2
2
0 0 0 0
0 0 0 0
Fig. 11. SOR RTV & Potential Sale Loss Before & After FIFO Implementation
For a furniture warehouse business, it is important that every activity is to be checked whether it is profitable or not. In the following table 1, the details of potential sale loss before and after implementation of FIFO in terms of money has been shown this noticed that there is total elimination potential sales loss as the products purchased first are dispatched first.
Table 1 Potential Sale Loss in Rs.
Before
After
Month
Potential Sale Loss(Qty)
Amount (Rs)
Avg. Amount (Rs)
Month
Potential Sale Loss(Qty)
Amount (Rs)
Avg Amount
Sep- 2020
4
119000
89125
Jan- 2021
0
0
Rs.0
Oct- 2020
5
96000
Feb- 2021
0
0
Nov- 2020
7
137000
Mar- 2021
0
0
Dec- 2020
2
45000
Apr- 2021
0
0
The average potential sales loss for the time period September-2020 to December-2020was Rs.89,125 per month and after complete implementation of the FIFO warehouse management techniques in this project, the average potential sales loss reduced to zero rupees. Thus, the selling the products of worth Rs.89125 per month which would be returned to vendor in previous scenario has improved the product sale and profit for the furniture sale for the Furniture warehouse Mumbai.
-
-
CONCLUSION
-
The afore mentioned analysis and execution concluded that installing FIFO in your warehouse has several advantages. By sending the oldest things first, you can keep your products from deteriorating and your inventory from becoming obsolete. Because your items have spent less time in your warehouse, your consumers will get them in reasonably clean cartons. Obsolete inventory refers to items that have expired and are no longer valuable to customers. When items move swiftly in and out of the warehouse, the odds of an item becoming obsolete before it is sold to a consumer are reduced. When it sends out the oldest stock first, then likelihood to enhance the item will sell before it expires. This can help firms minimize the amount of unsold inventory, allowing them to increase revenues. Another advantage of FIFO is that quality monitoring is simplified. It's easier to trace delivery if you ship items in the order, you receive them. After complete implementation of the FIFO warehouse management techniques in this project, the average potential sales loss reduced to zero rupees. Thus, the selling the products of worth Rs.89125 per month which would be returned to vendor in previous scenario has improved the product sale and profit for the furniture sale.
ACKNOWLEDGEMENT
Author acknowledges the facilities provided by Production Department VJTI, Mumbai and furniture industry for conducting this research and design analysis.
REFERENCES
-
Reza Budiawan, Jodhy K. Simanjuntak (2019) "Inventory Management Application of Drug using FIFO Method" The 2019 International Conference on Engineering Technology and Technopreneurship (ICE2T 2019) Bandung, Indonesia.
-
Anita C Sembiring1, J Tampubolon, D Sitanggang, Mardi Turnip, Subash (2019) "Improvement of Inventory System Using First In First Out (FIFO) Method" 1st International Conference of SNIKOM 2018 Journal of Physics: Conference Series.
-
Deepa Sanjay Pandey and Niyati Raut (2016) " Inventory management by using fifo system" Asian Journal of Science and Technology Vol.07, Issue, 02.
-
Manohar H M, S Appaiah (2017) "Stabilization of FIFO system and Inventory Management" International Research Journal of Engineering and Technology (IRJET) Volume: 04 Issue: 06.
-
Chun Chen Lee (2006), "Two-warehouse inventory model with deterioration under FIFO dispatching policy" European Journal of Operational Research, 861873.
-
Meinarini Catur Utami, Dwi Rizki Sabarkhah, Elvi Fetrina, M, Qomarul Huda (2018) "The Use of FIFO Method For Analysing and Designing the Inventory Information System" The 6th International Conference on Cyber and IT Service Management (CITSM 2018), Medan.
-
Eissa A. Al-Homaidi, Amgad Saeed Dabwan, Dr. Anwar Ahmad (2018) "Valuation of Inventory Methods in the Industrial Companies in Yemen" IJSRD – International Journal for Scientific Research & Development Vol. 6, Issue 04, 2018 ISSN (online): 2321-0613.
-
Kothawade, A., D K Shinde. (2019). "Improvement of Bottleneck Operations using Facility Planning Techniques in a Major Electric Overhead Travelling Crane Manufacturing Organization." 5th International Conference on Industrial Engineering, Proceeding of ICIE 2019.
-
Pramod Nehe, D. K. Shinde. (2018). "Inventory Accuracy for Switchboard Manufacturing Plant using Cyclic Counting method." International Research Journal of Engineering and Technology, 5(9), 688-695.
-
Rahmat Nurcahy, Akhyar P Siddiq (2009) "Analysing And Improving Implementation of FIFO System at Warehouse" Proceeding of the 11th International Conference on QiR (Quality in Research), University of Indonesia, Depok, Indonesia.
-
Mark H. McElreath and Maria E. Mayorga, Laine Mears (2010) "Assigning Storage Locations in an Automated Warehouse" Proceedings of the 2010 Industrial Engineering Research Conference.
-
Neeraj Kumar, S R Singh (2009) "Two-Warehouse Inventory Model with Stock-Dependent Demand for Deteriorating Items with Shortages" The IUP Journal of Computational Mathematics, Vol. II, No.3