
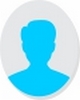
- Open Access
- Authors : V. V. Vijetha Inti , Ch. Rajya Lakshmi , G. Rama Swamy , D. Mamatha, B. Kiran
- Paper ID : IJERTV9IS120120
- Volume & Issue : Volume 09, Issue 12 (December 2020)
- Published (First Online): 21-12-2020
- ISSN (Online) : 2278-0181
- Publisher Name : IJERT
- License:
This work is licensed under a Creative Commons Attribution 4.0 International License
Design of Automated Solar Lawn Mover
1V. V. Vijetha Inti, 2 Ch. Rajya Lakshmi,3 D. Mamatha, 4 G. Rama Swamy, 5B. Kiran
1Assistant Professor, Department of EEE, Vishnu Institute of Technology,Bhimavaram, A.P., India 2Associate Professor, Department of Chemistry, Vishnu Institute of Technology,Bhimavaram, A.P., India 3Assistant Professor, Department of EEE, Vishnu Institute of Technology,Bhimavaram, A.P., India 4Assistant Professor, Department of Chemistry, Vishnu Institute of Technology,Bhimavaram, A.P., India Assistant Professor, Department of Physics, B.V.Raju College, Bhimavaram, A.P., India
Abstract:- Automation is rising quickly in the present technology. So mechanization assumes an imperative part in the horticultural field which is useful for the ranchers. In the previous days, the grass cutters utilized were physically handheld gadgets. Along these lines, there was contamination and loss of energy as they utilized gas and petroleum motors. So the old grass cutters should be supplanted via mechanized ones, where the framework will work for direction and hindrance discovery utilizing sunlight based energy as a force source.
Keywords: Automation, Solar energy, Grass cutter, Arduino
-
INTRODUCTION
In this paper we present an automated grass trimmer, fueled with sun based energy and ready to work just with the perfect energy from the sun; this one is an extraordinary contrast from the business ventures having a robot needing a charging station associated with the electrical matrix. It utilized Arduino UNO microcontroller board as the principle regulator of the framework, Ultrasonic sensor for object location, a NODE MCU for Wi-Fi association, a straight sharp edge for cutting the grass, and an engine drive for the wheels of the Robot. This is completely robotized and sustainable power based project.In Subsisting framework the gas or petroleum motors are used for the working of the grass cutting machines, yet in our plan we are made a grass shaper robot [1]which works by giving sunlight based energy as the source and the principle disadvantage of the remaining alive framework is it need a different individual to work the robot[2][3], to conquer this downside we are planning the robot with programmed block recognize and shirking by using the finish to stop switch , for the programming of the arduino microcontroller board we used the arduino programming and disentangled variant of c++ language as the programming language to indite the code.
In this paper we present a robotic lawn mower, fueled with sun powered energy and ready to work just with the perfect energy from the sun; this one is an incredible contrast from the business ventures having a robot[4] needing a charging station associated with the electrical matrix. When planning a grass cutter fueled by sun based energy, it is basic that the majority of the energy comes from the sun, and obviously a definitive outcome would be acquired if sun oriented energy were sufficient to totally control up the robot: this one is anyway a target that will be extremely hard to get, given the low effectiveness of existing sun based boards. In our venture the entire surface of the robot is bound to sunlight based boards, acting likewise as a cover: just the sides have been left free, and at any rate they wouldn't assume an unequivocal function in providing energy. Clearly, this decision represents a genuine imperative to the remainder of the undertaking, since in this way we previously characterized the greatest force accessible.
We need to consider that sunlight based power[5] won't generally be accessible, the same number of nursery territories are frequently in shade, or at any rate not straightforwardly hit by the sun, so we need to consider extensive misfortunes of influence. These misfortunes can be made up just if the robot has a gatherer fit for providing energy when it is missing from the sun. In this circumstance the battery functions as a cushion, collecting energy when it is bounty, and providing it when the robot, in actuality, is in shade. Starting here of view lead batteries are the most appropriate ones, however nothing restricts us to utilize batteries that can be performing more as far as weight and limit, similar to lithium ones. In full sun, the sun oriented board is equipped for reviving the inner battery with a flow at about 0,6A, adding up to about 8W, well under the force utilized by even the most proficient electric yard trimmer, fueled at 220Vac. This causes us to see as of now that an item like the one we're depicting in these pages can't substitute a physically worked yard trimmer totally, as this last one should be utilized from time to time, when the grass is excessively tall. Or maybe, the mechanical grass cutter can be utilized for a nonstop and consistent trimming of the grass.
These arrangements likewise offers a further bit of leeway, since the persistent taking care of guarantees that the lawn is consistently youthful and soft[6], and as it is cut in tiny pieces it is expected to decay itself in a brief timeframe, consequently filling in as preparation for the grass. You shouldn't expect the grass that has been sliced to be accumulated: in actuality, it will store itself among the grass cutting edges that have quite recently been cut.
For this sort of use, less force is required, and can be handily dealt with a battery fueled system[7]. The feeble force in play persuaded us to pick footing and a cutting motor with diminished force. Most likely, they may not totally suit the requirements of our perusers, who may in any case get the motors and the structure they like, contingent upon their spending plan and individual exigencies. To characterize the cutting zones in a yard, the underground wiring framework ends up being
simultaneously straightforward, precise and solid. It is additionally the best framework to characterize the work region of the robot.
Everything depends on the use of a straightforward electric wire, laid on the ground or somewhat under it, and associated with a control unit controlling the wire itself with a rotating electric sign at around 10 V and a recurrence of 34KHz. In the lower part of the body of the robot four little wheels are introduced, two on the front side, the other two on the rear, both alluding to an electric circuit shaped by a capacitor in equal. The circuit shaped by the equal inductance and the capacitor is called equal reverberating circuit and is determined with the goal that the strain at its closures, prompted by the outer attractive field, is at a most extreme when the attractive field shifts.
An reduced switch inverter [8]a can be used if the motor used for the lawn mover is an AC motor. But the cost of the equipment and the process for the conversion of electrical energy will become high for the design of a specific inverter and the motor. A low cost inverter with less number of switches has bee presented in [9].Because of all these disadvantages a DC motors are used for the movement of grass cutter in lawn.
-
BLOCK DIAGRAM &WORKING:
Solar Panel Battery DC-DC Converter Voltage Regulator
Motor Drive Motor Drive
Motor1
Microcontroller
Motor1
Motor
Motor
End Switch
IR Sensor
End Switch
Figure 1.Block Diagram of Solar Lawn Mover
The square portrayal of our undertaking is appeared previously. It contains a few squares, for example, Micro Controller, Battery, Solar Panel, IR Sensor and 4-Channel Motor Driver IC, Solar board unit, voltage controller . At the point when we charge our battery through Buck-converter it goes about as a charge regulator which charges our battery to 13V in corresponding to that we will have connect rectifier to change tainted dc over to unadulterated dc structure. The voltage currently get controlled by utilizing two voltage controllers, utilizing 7805 we can keep up voltage level to 5 volts which is needed for the activity of nano and by utilizing 7812 we can keep up voltage level to 12 volts to work transfers and engine drivers. Normal producer semiconductor which is utilized here assumes a vital function for our whole activity, as a typical producer semiconductor producer is grounded and the base is associated with aurdino nano through 1k resistor, and authority is associated with the transfer where as opposite finish of hand-off is associated with Vcc pin of nano. At the point when voltage goes through the base of semiconductor producer and authority gets because of that momentum move through transfer and there by our controlling of our robot can be accomplished through driver circuit.
The plan contains a microcontroller, IR sensor, DC engine, end to stop switch all these together consolidated we get a grass shaper robot. End to stop switch and IR sensor to distinguish if the robot was going into an article. Security is the fundamental concern when planning a robot with cutting edges. Figuring out where to put our sensor and switch is pivotal to the general adequacy of our plan. The chip should be in the robot to shield it from the regular components. End to stop will be mounted straightforwardly before the robot for most extreme discovery. Batteries are use for power age for the robot development and the battery is battery-powered.
The driver circuits makes the engines to run by directions unloaded by a client in Arduino nano. At first when the switch of our grass trimmer is set to on then it begins to move in a straight manner until it is upset by any obstruction then the finish to stop switch is changed its state whether it to on or off it gives the sign to driver circuits to move in back dependent on the postpone given by the client in a nano and it take right bearing for a total turn then it begins to move straight until it upsets by any snag if that happens it again move back for a similar deferral however now it will move left way for complete pivot which is conceivable through aurdino regulator.
Turning on the strength button the engines pivoting forward way and the grass cutting engine withal enacts, the sharp edge which is adjusted to the grass cutting engine cut the grass, on the off chance that any check comes in the manner, at that point the infra red sensor recognizes the obstacle and imparts the sign to the microcontroller then according to the given program the miniature regulator change the revolution of one of the engine then two engines pivots in absolute opposite ways with one another then the hindrance is dodged. It used to charge the Battery which supplies Power to the Controller that coordinates all the parts in this Project Atmega328p-pu: It is the primary Micro Controller utilized n Arduino Uno Micro Controller Board. It is
a result of Atmel and most Advanced chip it is a 8-cycle miniature regulator dependent on the CMOS Technology, it has the 32k of blaze memory, 1k EEPROM, 2k of internal.
-
CONTROLLING EQUIPMENT
Figure 2.Arduino nano microcontroller boardpin diagram
The Arduino board is planned so that it is simple for fledglings to begin with microcontrollers. This board particularly is breadboard neighborly is extremely simple to deal with the associations
USB Jack: Connect the small USB jack to a telephone charger or PC through a link and it will draw power needed for the board to work
Vin Pin: The Vin pin can be provided with an unregulated 6-12V to control the board. The on-board voltage controller directs it to +5V
+5V Pin: If you have a controlled +5V supply then you can straightforwardly give this o the +5V pin of the Arduino Information/yield:
There are absolutely 14 advanced Pins and 8 Analog pins on your Nano board. The advanced pins can be utilized to interface sensors by utilizing them as information pins or drive loads by utilizing them as yield pins. A basic capacity like pinMode() and digitalWrite() can be utilized to control their activity. The working voltage is 0V and 5V for computerized pins. The simple pins can gauge simple voltage from 0V to 5V utilizing any of the 8 Analog pins utilizing a basic capacity compare analogRead() These pins separated from filling their need can likewise be utilized for specific purposes which are examined underneath:
-
Serial Pins 0 (Rx) and 1 (Tx): Rx and Tx pins are utilized to get and communicate TTL sequential information. They are associated with the relating ATmega328P USB to TTL sequential chip.
-
External Interrupt Pins 2 and 3: These pins can be arranged to trigger a hinder on a low worth, a rising or falling edge, or an adjustment in worth.
-
PWM Pins 3, 5, 6, 9 and 11: These pins give a 8-cycle PWM yield by utilizing analogWrite() work.
-
SPI Pins 10 (SS), 11 (MOSI), 12 (MISO) and 13 (SCK): These pins are utilized for SPI correspondence.
-
In-fabricated LED Pin 13: This pin is associated with an implicit LED, when pin 13 is HIGH LED is on and when pin 13 is LOW, its off.
-
I2C A4 (SDA) and A5 (SCA): Used for IIC correspondence utilizing Wire library.
-
AREF: Used to give reference voltage to simple contributions with analogReference() work
-
Reset Pin: Making this pin LOW, resets the microcontroller.
-
END TO STOP SWITCHES
Figure 3. End to stop switch
A breaking point switch identifies the actual development of an item by direct contact with that object. An illustration of a cutoff switch is the switch that distinguishes the vacant situation of a vehicle entryway, naturally initiating the lodge light when the entryway is opened.
Recollect that the "ordinary" condition of a switch is the state of the base improvement. A breaking point switch will be in its "ordinary" state when it isn't in contact with anything (ie nothing that contacts the switch actuator instrument).
Cutoff switches find numerous utilizations in the business, especially in automated control and CNC machine device frameworks (Computer Numerical Control). In many movement control frameworks, versatile components have "homegrown" positions where the PC appoints a position estimation of zero. For instance, the controls of the hub of a CNC machine apparatus, for example, a machine or factory re-visitation of their "beginning" positions at the hour of dispatching, so the PC can know with certainty the underlying areas of each piece. These underlying positions are identified by limit switches. The PC
arranges that every servo engine voyages totally one way until a breaking point switch on every hub is set off. The position counter for every hub is reset to zero when as far as possible switch identifies that the underlying position has been reached.
An ordinary cutoff switch configuration utilizes a switch with a roller tip to connect with the moving part. The screw terminals on the switch body give association focuses the NC and NO contacts inside the switch. The majority of the breaking point switches in this plan share a "typical" terminal between the NC and NO contacts this way:
This switch contact plan is now and then alluded to as a structure C contact set, since it joins both a structure A contact (ordinarily open) just as a structure B contact (typically shut).
A nearby perspective on a few cutoff switches (utilized on a drum sequencer) shows the game plan of association terminals for structure C contacts. Each cutoff switch has its own "NO" (typically open), "NC" (ordinarily shut), and "C" (normal) screw terminal for wires to append.
Cutoff switches are utilized in an assortmen of uses and conditions on account of their roughness, simplicity of establishment, and dependability of activity. They can decide the presence or nonattendance, passing, situating, and end of movement of an item. They were first used to characterize the restriction of movement of an item; thus "Limit Switch".
-
Battery(12V-7.2Ah)
3.2.1 Working of Battery:
A battery is a gadget, which comprises of a different voltaic cells. Every voltaic cell comprises of two half cells associated in arrangement by a conductive electrolyte holding anions and feline particles. One half-cell incorporates electrolyte and the terminal to which anions move, for example the anode or negative terminal; the other half-cell incorporates electrolyte and the cathode to which feline particles move, for example the cathode or positive anode.
In the redox response that controls the battery, decrease happens to cations at the cathode, while oxidation happens to anions at the anode. The cathodes don't contact each other however are electrically associated by the electrolyte. Generally the half cells have various electrolytes. Everything considered each half-cell is encased in a holder and a separator that is permeable to particles however not the heft of the electrolytes forestall blending.
3.3 Working of Lithium Ion Battery
Lithium Ion batteries are currently mainstream in lion's share of electronic compact gadgets like Mobile telephone, Laptop, Digital Camera, and so forth because of their enduring force effectiveness. These are the most mainstream battery-powered batteries with preferences like best energy thickness, irrelevant charge misfortune and no memory impact. Li-Ion battery utilizes Lithium particles as the charge transporters which move from the negative cathode to the positive terminal during release and back while charging. During charging, the outside current from the charger applies an over voltage than that in the battery. This powers the current to pass the opposite way from the positive to the negative terminal where the lithium particles get installed in the permeable anode material through a cycle called Intercalation. The Li-Ions go through the non fluid electrolyte and a separator stomach. The cathode material is intercalated lithium compound.
The negative cathode of the Li-Ion battery is comprised of carbon and the positive terminal is a metal oxide. The most ordinarily utilized material in the negative terminal is Graphite while that in the positive cathode might be Lithium cobalt oxide, Lithium particle phosphate or Lithium manganese oxide. Lithium salt in a natural dissolvable is utilized as the electrolyte. The electrolyte is regularly a combination of natural carbonates like Ethylene carbonate or Diethyl carbonate containing lithium particles. The electrolyte utilizes anion salts like Lithium hexafluoro phosphate, Lithium hexafluoro arsenate monohydrate, Lithium per chlorate, Lithium hexafluoro borate and so on Contingent on the salt utilized, the voltage, limit and life of the battery fluctuates. Unadulterated lithium responds with water energetically to frame lithium hydroxide and hydrogen particles. So the electrolyte utilized is non watery natural dissolvable. The electrochemical function of the terminals charge among anode and cathode relies upon the heading of current stream.
3.3.2 Li Ion Battery Reaction
In the Li-Ion battery, both the terminals can acknowledge and deliver lithium particles. During the Intercalation cycle, the lithium particles move into the terminal. During the opposite cycle called de intercalation, the lithium particles move back. During releasing, the positive lithium particles will be removed from the negative terminals and embedded into the positive cathode. During the charging cycle, the converse development of lithium particles happens.
-
SOLAR PANEL
Figure 4. Solar Panel
Consistently, the sun emanates (conveys) a colossal measure of energycalled sunlight based energy. It transmits more energy in one day than the world uses in a single year. This energy comes from inside the sun itself. Like most stars, the sun is a major gas ball made up generally of hydrogen and helium gas. The sun makes energy in its internal center in a cycle called atomic combination. It takes the sun's energy simply barely eight minutes to venture to every part of the 93 million miles to Earth. Sun oriented energy goes at the speed of light, or 186,000 miles for every second, or 3.0 x 108 meters for each second. Just a li ttle
piece of the obvious brilliant energy (light) that the sun emanates into space actually arrives at the Earth, yet that is an excess. Consistently sun based energy arrives at the Earth to supply our country's energy needs for a year! Sun powered energy is viewed as a sustainable power source because of this reality. Today, individuals utilize sunlight based energy to warm structures and water and to produce power. Sunlight based energy represents an exceptionally little level of U.S. energyshort of what one percent. Sunlight based energy is generally utilized by habitations and to create power.
Sun oriented energy can likewise be utilized to deliver power. Two different ways to make power from sun based energy are photograph voltaics and sun oriented warm frameworks. Photovoltaic Electricity Photovoltaic comes from the words photograph, which means light, and volt, an estimation of power. In some cases photovoltaic cells are called PV cells or sun powered cells for short. You are most likely acquainted with photovoltaic cells. Sun oriented controlled toys, number crunchers, and side of the road call boxes all utilization sun powered cells to change over daylight into power. Sun powered cells are comprised of silicon, the very substance that makes up sand. Silicon is the second generally normal substance on Earth. Sunlight based cells can supply energy to anything that is fueled by batteries or electric force. Power is delivered when brilliant energy from the sun strikes the sun based cell, making the electrons move around. The activity of the electrons begins an electric flow. The transformation of daylight into power happens quietly and immediately. There are no mechanical parts to wear out. Contrasted with alternate methods of making power, photovoltaic frameworks are costly and numerous boards are expected to rise to the power created at different kinds of plants.
-
Dc Motor:
Figure 5. DC Motor
This Johnson Geared Motor from Robu.in gives force which falls moderate to the forces by focus shaft gear engines and side shaft dc gear engines, at a sensible expense.
It is a straightforward DC engine including metal gearbox for driving the shaft of the engine, so it is a precisely commutated electric engine which is fueled from DC supply. The Johnson Geared Motors are known for their reduced size and enormous force speed trademark.
The Johnson Motor accompanies side shaft otherwise called a helter-skelter shaft and six M3 mounting openings. The shaft of the engine prepares metal brambles which makes these DC gear engines Shaft wear safe. The shaft of the engine has an opening for better coupling.
The engine will run easily between the voltage range 6 to 18 V DC and give you 200 RPM at 12V inventory. It gives the force of 3.9 kg-cm at 200 RPM.
-
Working model of lawn mover
Figure 6(a)Solar Lawn mover Figure 6 (b) Switching Circuit
The above figures 6(a) and 6(b) shows the working model of the sun based yard mover where the grass trimmer works freely with no outside help .Just on the off chance that we switch on the engine this yard mover will move all around the ground which cuts the additional grass in the grass and on the off chance that any outer aggravation happened, at that point the mover will turn back utilizing the finish to stop switch. Hence can move freely without any help of man.
CONCLUSION
Fundamental Drawback of the Subsistng System is it need a different individual to work the Robot, so to conquer this downside a framework was actualized for completely robotized battery controlled grass shaper. As the innovation is getting progressed, highlights of grass cutters are additionally upgraded. The planned Model is profoundly effective and exact as it distinguishes the items and stops the development. Hence, the Design and execution of the task has been fruitful. Since there is no expense of fuel
and any sort of contamination as the current framework utilizes battery as a force source, the planned Robot will address the Difficulty of minimal effort of activity and an environmentally friendly power.
REFERENCES :
-
Vishal Danve, Anindu Bose and Varun Dhawan Solar powered gardener International Journal of Technical Research and Applications e-ISSN: 2320- 8163, www.ijtra.com Special Issue 39 (KCCEMSR) (March 2016),PP. 39-43
-
Mohammad Baloch, Taj; Timothy Thien Ching Kae; , "Design and modelling a prototype of a robotic lawn mower," Information Technology, 2008. ITSim 2008. International Symposium on , vol.4, no., pp.1-5, 26-28 Aug. 2008.
-
Yu Zhiqiang; Gao Meng; Deng Xiaoyan; Du Liqiang; He Chaofeng; Di Jianhong; Yang Yong; Shi Yanhui; Hu Liqiang; , "APF obstacle avoidance in polar coordinates for mobile robot based on laser radar,"Advanced Computer Control (ICACC), 2010 2nd International Conference on , vol.1, no., pp.549-552, 27-29 March 2010.
-
Tsubata, K.; Suzuki, K.; Mikami, S.; Osawa, E.-I.; , "Recognition of lawn information for mowing robots," Autonomous Robots and Agents, 2009. ICARA 2009. 4th International Conference on , vol., no., pp.15- 20, 10-12 Feb. 2009.
-
Pratik Adhav,ShivajiKolekar Manufacturing Of Solar Operated Grass Cutter Machine,International Engineering Research Journal (IERJ), Volume 2 Issue 8 Page 2785-2788, 2017 ISSN 2395-1621
-
Muhammad Wasif Design and Implementation of Autonomous Lawn-Mower Robot Controller 7th International Conference on Emerging Technologies … 978-1-4577-0768-1/11/$26.00 ©2011 IEEE
-
BibekanandaPatra,SambhunathNandy Lawn Mower Trajectory Tracking By Wheeled Mobile Robot: Its Consequences, 2017, 978-1-5386-1703-8/17, 2017 IEEE
-
Design and Implementation of Dual Switch Inverter Fed from Renewable Energy Sources, Mrs.V.V.Vijetha Inti, Dr.V.S.Vakula, TEST Engineering and Management,Volume 83,Page Number: 13993 13999,Publication Issue:March – April 2020
-
Design And Matlab/Simulink Implementation Of Four Switch Inverter For Microgrid Utilities,Mrs.V.V.Vijetha Inti, Dr.V.S.Vakula, Energy Procedia, vol 117,pages: 615-625,2017
-