
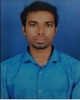
- Open Access
- Authors : Mohammed Imran , Syed Abdul Moeed
- Paper ID : IJERTV10IS060362
- Volume & Issue : Volume 10, Issue 06 (June 2021)
- Published (First Online): 29-06-2021
- ISSN (Online) : 2278-0181
- Publisher Name : IJERT
- License:
This work is licensed under a Creative Commons Attribution 4.0 International License
Design and Simulation of Heat Sink for Different Components Geometry with Various Heat Capacities
Mohammed Imran
Mechanical Engineering Department (M.E) Muffakhamjah College Of Engineering And Technology, Hyderabad, India
Syed Abdul Moeed
Mechanical Engineering Department (M.E) Muffakhamjah College Of Engineering And Technology, Hyderabad, India
AbstractThis Electronic device cooling system is capable of satisfying required capacity electronic device. This paper details the results of a study to develop a geometry based optimization tool for heat sink design. Variation in the design aspects of the heat sink components, the cooling of electronic devices is possible. Geometry of heat sink, effect heat convention capability, size and weight of the component. Electronic warfare devices, obviously uses electronic chips. These components generate Power as they function. This power generation goes hand in hand with the generation of heat. Heat generated can be quite harmful to this electronic equipment & may also decrease the efficiency. The problem is even greater when the electronic set up is placed in a hot environment.
This high temperatures, decreases the life span of the component, might even cause permanent damage to the equipment. Hence, it becomes necessary to manage the thermal issues by designing suitable heat sinks, such that the power is efficiently dissipated. This project involves designing a heat sink, for an electronic chip of area (80mm * 60mm) that is placed in the environment in which the temperatures reaches up to 55 degree Celsius. Steps were taken to solve the problem using design formulas with respect to the given specifications & the ambient temperature.
Keywords Optimal spacing, Convective heat transfer coefficient, Thermal diffusivity, kinematic viscosity, Height of fin
-
INTRODUCTION
Electronic Warfare device has an issue of electronic over heating which can damage the entire set up. Hence, the heat dissipation is eminent. With the increase in heat dissipation from microelectronic devices and the reduction in overall form factors, thermal management becomes a more and more important element of electronic product design. Both the performance reliability and life expectancy of electronic equipment are inversely related to the component temperature of the equipment. Long life and reliable performance of a component may be achieved by effectively controlling the device operating temperature within the limits set by the device design engineers. Heat sinks are devices that enhance heat dissipation from a hot surface, usually the case of a heat generating component, to a cooler ambient, usually air. For the following discussions, air is assumed to be the cooling fluid. In most situations, heat transfer across the interface between the solid surface and the coolant air is the lead
efficient within the system, and the solid-air interface represents the greatest barrier for heat dissipation. A heat sink lowers this barrier mainly by increasing the surface area that is in direct contact with the coolant. This allows more heat to be dissipated and/or lowers the device operating temperature. The primary purpose of a heat sink is to maintain the device temperature below the maximum allowable temperature specified by the device manufacturer.
Arularasan and Velraj (2008) have selected an optimal heat sink design in their research work, preliminary studies on the fluid flow and heat transfer characteristics of a parallel plate heat sink have been carried through CFD modeling and simulations. The geometric parameters fin height, fin thickness and fin pitch have been considered in this work. In this research work, optimal design of the heat sink is carried out on a parallel plate heat sink using CFD study. Experimental studies have been performed with a parallel plate heat sink to validate the heat sink model. These results and conclusions drawn in this paper benefit the design engineers involved in electronics cooling.
Abdullah H. et al. compared solid and perforated horizontal rectangular fin in natural convection by using finite element technique. They keep the same dimensions, thermal conductivity, base temperature and ambient temperature for both fins and studied the effect of the perforation on heat transfer rate. They found that, perforated horizontal rectangular fin has more heat transfer and less weight compared to equivalent solid fins. The heat transfer enhancement of the perforated fins are depends on fin thickness and thermal conductivity of material.
-
MATERIALS AND METHODS
The most common heat sink materials are aluminum alloys. Aluminium alloy 1050A has one of the higher thermal conductivity values at 229 W/m.K but is mechanically soft. Aluminium alloys 6060 and 6063 are commonly used, with thermal conductivity values of 166 and 201 W/m.K, respectively. The values depend on the temper of the alloy. Copper has around twice the conductivity of aluminium, but is three times as dense and, depending on the market, around four to six times more expensive than aluminium. Aluminium can be extruded, but copper cannot. Copper heat sinks are machined and skived. Another method of manufacture is to
solder the fins into the heat sink base. The high temperatures, decreases the life span of the component, & might even cause permanent damage to the equipment. Hence, it becomes necessary to manage the thermal issues by designing suitable heat sinks, such that the power is efficiently dissipated.
Diamond is another heat sink material, and its thermal conductivity of 2000 W/m.K exceeds copper five-fold. In contrast to metals, where heat is conducted by delocalized electrons, lattice vibrations are responsible for diamond's very high thermal conductivity. For thermal management applications, the outstanding thermal conductivity and diffusivity of diamond is an essential. Nowadays synthetic diamond is used as sub mounts for high-power integrated circuits and laser diodes.
Composite materials can be used. Examples are a copper- tungsten pseudo alloy, AlSiC (silicon carbide in aluminium matrix), Dym alloy (diamond in copper-silver alloy matrix), and E-Material (beryllium oxide in beryllium matrix). Such materials are often used as substrates for chips, as their thermal expansion coefficient can be matched to ceramics and semiconductors.
II. NUMERICAL CALCULATION:
In order to reduce the complexity of the calculations the following assumptions will be made:
-
The surface area due to the thickness of the fins t, and thickness of the base b are much much smaller than the total surface area of the heat sink
-
The thermal conductivity of the heat sink is high enough so that the temperature of the surface of heat sink is uniform and approximately equal to the temperature of the heat source
-
The heat source has the same length and width of the heat sink and is centered on the base of the heat sink
-
The source is in perfect contact with the base of the heat sink
The above assumptions will introduce some errors in your calculations. However the purpose of conducting this calculation is to get a rough estimate of the size of the required heat sink. More sophisticated calculation methods, software or testing can then be used to refine the design.
This analysis is for a heat sink whose base is oriented vertically with cooling via natural convection only. The first step of the calculation is to select values for L and H based on your design constraints. The optimum spacing between the fins s that produces the maximu heat transfer due to natural convection is given by equation 1. A detailed explanation of how this equation was derived can be found in .
= 1/Tavg
Tavg = Ts + Tamb
2
Sopt = 2.71[g(TsTamb)]
Lµ
hconv = 1.31k
Sopt
The thermal conductivity of air evaluated at T avg . It is a measure of how well heat is removed from the surface of the heat sink via convection.
The law of conservation of energy dictates that the heat generated by the heat source Q must be equal to the heat dissipated by the heat sink under steady state conditions. This is represented in equation 3. The right hand side of equation 3 which accounts for the heat dissipated by the heat sink is derived from Newtons law of cooling. The surface area A of the heat sink is given by equation 4. The thickness of the fins, t and base, b are not included in the surface area calculation since one of the assumptions made is that these dimensions are negligible. The number of fins, N is calculated by combining equations 3 and 4. The width, W of the heat sink is then calculated using equation
Q = hconv A ( Ts T amb ) A = N x (H b ) x L
W = (N 1 )Sopt +N t
Using this formula we can determine the heat generation in base component of electrical circuit. The number of fins required for the heat sink and optimal spacing between fins also calculated.
CACULATION:
This project involves designing a heat sink, for an electronic chip of area (80mm * 60mm) that is placed in the environment in which the temperatures reaches up to 55 degree Celsius. Steps were taken to solve the problem using design formulas with respect to the given specifications & the ambient temperature.
Sopt = 2.71 [ ( 9.81 x 0.014 x (85 55) ]
0.06 x 20.02 x 10-6 x 48.556 x 10-6
= 4.58 x 10-3 m
hconv = 1.31×0.02966
4.58 x 10 -3
= 8.483 N/m2 K N = 80 .
4.58+1
= 15
10 = 8.483 x (14 x (H-0.005) x 0.06 x ( 85 55 ) H = 41.79 mm
This calculation provides some insight into what dimensions should be varied to optimize the size of the heat sink. If you are trying to minimize the volume of the heat sink the length should be made a small as possible. This will maximize the heat transfer from the heat sink as such reducing the surface area required to limit the source temperature below the required value
III. DESIGN AND SIMULATION:
A heat sink usually consists of a base with one or more flat surfaces and an array of comb or fin-like protrusions to increase the heat sink's surface area contacting the air, and thus increasing the heat dissipation rate. While a heat sink is a static object, a fan often aids a heat sink by providing increased airflow over the heat sink The heat sink's contact surface (the base) must be flat and smooth to ensure the best thermal contact with the object needing cooling. Frequently a thermally conductive grease is used to ensure optimal thermal contact; such compounds often contain colloidal silver. Further, a clamping mechanism, screws, or thermal adhesive hold the heat sink tightly onto the component, but specifically without pressure that would crush the component
When selecting or designing a heat sink the following factors must be considered Thermal resistance, Material, Fin efficiency, Spreading resistance, Fin arrangements, Surface color.
Fig.1 heat sink design using uni graphics NX
Table 2.Dimensions of heat sink
S,no
Dimensioned part
Dimensions (mm)
1
Span gap
4.58
2
Component width
40
3
Component height
10
4
Fin thickness
1
5
Fin height
41.58
6
Number of fins
15
Thermal simulations give engineers a visual representation of the temperature and airflow inside the equipment. Thermal simulations enable engineers to design the cooling system; to optimize a design to reduce power consumption, weight and cost; and to verify the thermal design to ensure there are no issues when the equipment is built. Thermal simulation is often required to determine how
to effectively cool components within design constraints. Simulation enables the design and verification of the thermal design of the equipment at a very early stage and throughout the design of the electronic and mechanical parts Thermal simulation allows experimentation with optimization, such as modifying heat sink geometry or reducing fan speeds in a virtual environment, which is faster, cheaper and safer than physical experiment and measurement. We are using uni graphics NX for design of heat sink. All the dimensions of heat sink achieved as per given heat capacity dissipation.
Simulation of heat sink design performed in Ansys workbench steady state thermal. Initial conditions, boundary conditions are as per given geometry. As per given heat dissipation we can analyze and design the geometry dimensions and check whether the heat sink efficiency is better. Increases in number of fins in heat sink increases the heat loss from given component. Heat flow also depend on properties of the material like heat transfer coeffient and thermal conductivity i.e., selection of material also plays important role in design of heat sink.
Fig 2.Temperature analysis
Fig 3.Total heat flow analysis
Fig 4.Directional heat flux analysis
As per given heat dissipation, temperatures and given conditions heat sink is analyzed and output are examined. After the simulation the given results are drawn
Table3. Simulation of heat sink design output
S.no
Name of the property
Values
1
Heat ambient Temp
550 k
2
Heat source Temp
780 k
3
Heat capacity
10 watts
4
Total Heat flow
5.3 watts
5
Directional heat flow
4.7 watts
6
Heat transfer coeffient
12 w/m2k
RESULTS AND DISCUSIONS:
In this project work using the formulas we can design and optimize heat sink geometry dimensions. Heat dissipation of the circuit will decide the size and geometry of the heat sink. By varying heat dissipation no of fins, optimum distance of the fins and height of the changes as follows.
Table 4: variation heat dissipation vs height of fin
s.no
Heat dissipation (J)
Height of fin (mm)
1
5
26.26
2
10
41.58
3
15
68.78
4
20
90.04
5
25
111.13
As per the results we observed that increasing in the heat dissipation will leads to increases the fin height where the number of fins and optimum spacing between fins are not changed. Thickness of the fin is 1mm also not varied.
CONCLUSIONS:
Different components with different materials having various heat capacities we design heat sink with varying geometry and no.of fins. Numerical calculations and
simulation are performed as per dimensions. Heat dissipation, temperatures will decide geometry of the model, selection of material and no of fins. This report gives the all information regarding design of heat sink geometry and heat sink materials.
REFRENCES:
-
Arularasan and Velraj. Optimization of the geomery of a heat sink, university of Virginia, Charlottes ville.
-
Kim D., Jung J., Kim S., Thermal optimization of plate-fin heat sinks with variable fin thickness, International Journal of Hear and Mass Transfer 53(2010) 5988-5995,Elseveir,2010.
-
S.A. Nada Natural convection heat transfer in horizontal and vertical closed narrow enclosures with heated rectangular finned base plate International Journal of Heat and Mass Transfer 50 (2007) pp. 667 679.
-
Yue-Tzu Yang , Huan-Sen Peng Numerical study of pin-fin heat sink with un-uniform fin height design International Journal of Heat and Mass Transfer 51 (2008) pp.
-
M. Dogan , M. Sivrioglu Experimental investigation of mixed convection heat transfer from longitudinal fins in a horizontal rectangular channel International Journal of Heat and Mass Transfer 53 (2010) pp.
-
Abdullah H. AlEssa, Ayman M. Maqableh and Shatha Ammourah, Enhancement of Natural Convection Heat Transfer from a Fin by Rectangular Perforations with Aspect Ratio of Two, International Journal of Physical Sciences, volume 4 (10), Oct. 2009,
-
Journal of Electronics Cooling and Thermal Control.
-
Dave s Steinberg , Cooling Techniques of Electronic Equipments.
-
H.S Lee , Thermal Design: Heat Sinks, Thermo electrics, Heat Pipes, Heat Exchangers and Solar cells.
-
Kyoungwoo., Park-Kyoun., The application of the CFD and Kringing method to an optimization of heat sink, International Journal of Heat and Mass Transfer .
-
Kumar M., Kumar A., Kumar S., Optimum design and selection of heat sink (IJAIEM) . 12.Ralph Remsburg, Advanced Thermal Design of Electronic Equipments.
-