
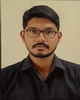
- Open Access
- Authors : Prashant D. Chaudhari , Gaurav S. Gajare
- Paper ID : IJERTV9IS040480
- Volume & Issue : Volume 09, Issue 04 (April 2020)
- Published (First Online): 27-04-2020
- ISSN (Online) : 2278-0181
- Publisher Name : IJERT
- License:
This work is licensed under a Creative Commons Attribution 4.0 International License
Design and Fabrication of Semi-Automated Drainage Cleaning System
Prashant D. Chaudhari
Department of Mechanical Engineering
Dr. Vithhalrao Vikhe Patil College of Engineeering Ahmednagar, Maharashtra
Gaurav S. Gajare
Department of Mechanical Engineering
Dr. Vithhalrao Vikhe Patil College of Engineering Ahmednagar, Maharashtra
Abstract The research paper focuses on replacing the manual method of cleaning the drainage system with the semi- automated mechanical drainage cleaner. The method followed nowadays is proving to be the health hazard for the worker undergoing the process of cleaning the drainage. Along with the drainage water some solid waste travels through the drainage line and at the junction points of drainage system these solid waste gets accumulated over time and thus causes the blockage of system. This urges the need of timely cleaning of drainage lines. So this system will help to resolve the problem and will thus help in ensuring the timely cleaning of the system by segregating the solid waste.
KeywordsDrainage system, solid waste, manual cleaning, health hazard
-
LITERATURE REVIEW
-
INTRODUCTION
Water running through a water drainage system usually carries along waste materials most of which are non- biodegradable which not only cause flooding but also climate change. Overflow of drainage water through drainage system occurs when there is a blockage at an end of the drainage system forcing the water to find its way elsewhere apart from the mapped out drainage system, therefore the running water spills over the horizontal height of the drainage systems spreading to regions alongside the drainage system, thereby causing problems such as pushing down of structures such as fences, water logging of farm lands and residential buildings etc. [1]
Drainage systems are blocked most times by garbage like nylon, plastic bottles and empty cans which cluster together and find their way into the drainage systems. If this garbage is allowed to flow, it blocks the system due to which water flow gets distracted and it comes out of the drainage cover [2]. The method followed nowadays to clear these blockages are either by using suction machine which is a costly method way or else by road sweeper and unskilled worker who has to enter the drainage hole and clean it manually which is dangerous for their health. The drainage systems are cleaned when there is no water in them i.e. when it is not raining. But when it is raining the drainage systems cannot be cleaned because of the severe conditions of the rain which no one would volunteer to endure to ensure garbage does not enter into the drainage systems [3]. These solid waste separated either by suction machine or manually are not properly disposed they are allowed to litter in the nearby areas. Also non uniform size of the drainage lines is one of the major issues for designing a universal cleaning machine [4].
Author
Research Work
Remark/Conclusion
Ndubuisi C. Daneils (2014)
Drainage System Cleaner: A solution to Environment Hazards
Developed a system that works on the flow of drainage line.
R. Sathiyakala P. Maheswari (2012)
Smart Sewage Cleaning System is the automatic functional network using smart arm extraction and E- Bucket heating.
Worked on the smart arm that can lift and be used for extraction of the blockages.
Shao Wu Zang (2016)
Drainage Cleaning Using Ceramic Filter.
Ceramic Filter is used to clean the drainage system.
Balachandra.G Karthikeyan.S Divya.N (2016)
Semi-automatic drain for sewage water treatment of floating materials.
Since the paper studied and designed the system for only uniform drainage line and holes, it lagged the study of non-uniform drainage hole.
Author
Research Work
Remark/Conclusion
Ndubuisi C. Daneils (2014)
Drainage System Cleaner: A solution to Environment Hazards
Developed a system that works on the flow of drainage line.
R. Sathiyakala P. Maheswari (2012)
Smart Sewage Cleaning System is the automatic functional network using smart arm extraction and E- Bucket heating.
Worked on the smart arm that can lift and be used for extraction of the blockages.
Shao Wu Zang (2016)
Drainage Cleaning Using Ceramic Filter.
Ceramic Filter is used to clean the drainage system.
Balachandra.G Karthikeyan.S Divya.N (2016)
Semi-automatic drain for sewage water treatment of floating materials.
Since the paper studied and designed the system for only uniform drainage line and holes, it lagged the study of non-uniform drainage hole.
-
-
OBJECTIVES
The major objectives of the project are as follows:
-
Basic safety of the labor and hygiene.
-
To replace the manual system by semi-automated system.
-
The system should be portable.
-
The system should be able to segregate solid waste from the drainage water.
Fig. 1: Methodology
Fig. 1: Methodology
-
-
METHODOLOGY
-
SYSTEM DESIGN AND WORKING
DCM consists of various parts which includes motor, chain & sprocket, belt & pulley, shaft, collector and lifter. Once the power is supplied to the motor the output shaft of motor starts rotating. The main shaft and output shaft of motor is connected with the help of belt and pulley arrangement. Chain and sprocket is mounted on the main shaft. And the lifter bucket is mounted on the chain. Once the chain starts rotating the lifter starts moving along with it [5]. All the solid waste including plastic bottles, cans, carry bags etc. gets lifted up through this bucket and it is collected in the collector.
-
Frame Calculations:
Fig. 2: Frame Dimensions
Fig. 2: Frame Dimensions
Assuming water pressure on frame is 2000 kg/m³ p = 2000 kg/m³
=
= 2000 0.35 0.6 0.005
= 2.1
=
= 2.1 9.81
= 20.601
= /
= 20.601/ (210 10³)
= 98.1
As its pressure limit is 5 kgf/cm² which is greater than calculated pressure 0.0010034 kgf/cm².
-
Calculation for Base Frame:
Assumptions
Total load on frame is about 10kg
=
= 10 × 9.81
= 98.1 N
This load is applied at the center as shown in fig
i.e. at 305mm
Fig. 4: Base Frame Dimensions in mm
Fig. 4: Base Frame Dimensions in mm
Fig. 5: Reaction on Frame
Fig. 5: Reaction on Frame
From fig.
R1 +R2 = F
And
MR1 = 0
F × 305 – R2 × 610 = 0
Fig. 3: Side View Dimensions
Fig. 3: Side View Dimensions
98.1 × 305 R2 × 610 = 0
Therefore, R2 = 49.05
R1 + 49.05 = 98.1
R1 = 49.05
Mb = 49.05 × 305
Mb = 14960.75
Y= b/2 . (b = width of square pipe of frame)
= 25/2
= 12.5mm
I = bd³ / 12
= d / 12 ..(b=d)
= (25) / 12
= 32552.333
Stress on frame, = Mb y / I
= (32552 × 10) / 14960.75
= 21.75 N / mm² = Syt / FOS Therefore,
Syt = × FOS
= 21.75 × 3 (Assming FOS = 3)
= 65.75 N / mm²
Selecting material GCI 15 having Tensile strength (min) = 150 N / mm²
For safer design considerations as 65.75 N / mm² Therefore all assumptions are in safer state.
-
Selection of Motor:
Speed (N) = 30 rpm
We suppose the weight of garbage = 4 kg Pulley size is = 320 mm
FOS = 1.5
Force = 4× 9.81
= 39.24N
Torque = Force × Distance
= 39.24 × 320
= 12556.8 N-mm
= 12.5568 N-m
Therefore,
Maximum Torque = 12.5568 × 1.5
= 18.8352 N-m
Now,
Power = (2NT)/60
= (2 × 30 ×18.8352)/60
= 59.1725 watts.
Therefore,
Selecting motor of power of 84 watts so losses can be avoided. Voltage: 12 volt
Current: 7 amp
Speed: 30 rpm
-
Shaft Calculations:
Designation
UTS
(N/mm²)
Yield Strength (N/mm²)
15C8
440
240
ASME code for design of shaft:
Since the loads on most shafts in connected machinery are not constant, it is necessary to make proper allowance for harmful effects of load fluctuation.
According to ASME code permissible values of shear stress may be calculated from various relations.
(allowable) = 0.18 x Sut
= 0.18×440
= 79.2 N/mm²
OR
(allowable) = 0.3 x Syt
= 0.3 × 240
= 72 N/mm²
Considering minimum of the above values
(allowable) = 72 N/mm²
This is allowable value of shear stress that can be induced in shaft material for safe operation
To Calculate Input Torque:
Selecting the motor of 84Watt i.e. 12v 7Amp Power= 2nt/60
T = 60 × P/2n
= 60 × 84/2 ×30
= 26.73 N-m
Assuming 100% overload T (design) = 2 × T
= 2 × 26.73 × 103
= 53.460 × 103 N-mm
Check for Torsional Shear Failure of Shaft
Assuming min section diameter on input shaft = 20mm d=20mm Td=16× (actual)×d³
(actual) = 16Td / d³
= (16 × 53.460 × 10³) / (20)³
(actual) = 34.0336 N/mm²
As (actual) is less than (allowable)
Input shaft is safe under torsional load. Hence we select shaft with diameter of 20 mm.
6. Calculation of Bearing:
Bearing selection completely depends on shaft diameter, here we have selected the perfectly safe shaft of diameter 20mm. Since the shaft is of diameter 20mm so we have used the bearing of 20 mm ID.
The bearing no.204 pedestal bearing is used because it is self- aligned bearing.
Material Selection:
-
Frame :
Frame is the crucial part of machine, all the forces, stresses and water pressure are calculated. After studying the results of calculations we have decided to use GCI15 material for fabricating the main frame as well as the base frame of the machine [6].
-
Motor :
The main purpose of motor is to covert electrical energy into mechanical energy. There are two types of motor viz. 1) AC motor and 2) DC motor. Our requirement of speed is not more than 30rpm and power not more than 70 Watts. This is satisfied by 12Volts and 7 amp wiper motor.
-
Shaft :
Shaft is the rotating element used to transmit the power. We will be using solid shaft. The shaft should have high strength, good machinability, high wear resistance and good heat treatment properties. The materials used for shaft are carbon steels of grade 40C8, 15C8, 50C4, 50C12. MS and EN8 can also be used. We have selected 15C8 for shaft.
-
Bearing :
The shaft diameter is 20mm. Therefore the ID of bearing needs to be 20mm. From the calculations we have decided to use RB204 pedestal bearing. Pedestal is nothing but the plumbing block. It is used to provide support for rotating shaft with the help of compatible bearing.
-
-
Chain and Sprocket :
We have used Pintle Chain and 6 inch Sprocket as per the standards available in the market satisfying our requirement.
-
-
CAD Model
Fig. 6: CAD Model
Fig. 6: CAD Model
-
FABRICATION
During Fabrication firstly the base frame was welded according to the dimensions and then the remaining pipes were welded on the base frame. After making the frame pedestal bearings were mounted on the frame and then the shafts of required diameter were engaged in the bearings. Also the chain and sprockets were mounted on the upper and lower shaft. Sheet metal and the net were welded on the front facing frame pipes.
Fig. 7: Rear View of Fabricated Model
Fig. 8: Front View of Fabricated Model
Lifter was prepared from the net like pipes. Also the collector bin was prepared separately it was provided with the handle to lift. Meanwhile the side flaps were created and mounted on the side pipes of the frame. Also the wiper motor was mounted on the position and by using belt and pulley arrangement drive was provided to the driving shaft.
-
TESTING
Testing of the final project was conducted by nearby water reservoir. The side flaps provided were properly working and help the water to pass through the net only. The lifters were able to lift maximum weight of 4kg at a time. The solid waste lifted by lifter was properly disposed in the collector bin during each rotation.
Fig. 9: Actual Position of the model
Fig. 10: Actual Position of the Model
-
ADVANTAGES
-
System works properly at given conditions and it is to be the most economical way of cleaning.
-
Easy to operate as no special skills are required.
-
Reduction of labour oriented method of cleaning, thus upgrading the dignity of labour.
-
System is light in weight and easily portable.
-
Efficient for residual removal.
-
Large amount of garbage will be collected, which can be recycled
-
-
CONCLUSION
From this project it is concluded that DCM is helpful for separating solid waste from the drainage water which will further avoid the blockage of drainage line and avoid flooding.
-
Due to continuous rotation of the chain the lifter timely collects all the waste and thus avoids the blockage by separating solid waste from the liquid.
-
Separation of these solid waste helps in treating the solid waste and thus converting it into degradable waste.
-
Being light in weight this kind of system can be placed at the junction points of the drainage system that are frequently subjected to blockages.
The system functions more effectively during the heavier rains which has more volume of garbage with high velocity running water through the drainage lines.
REFERENCES
-
Ganesh U L,et.al. Semi-Automatic Drain For Sewage Water Treatment Of Floating Materials, International Journal of Research in Engineering and Technology, Vol No- 05, Jul-2016
-
NDUBUISI C. Daniels, Drainage System Cleaner A Solution to Environmental Hazards, International Refered Journal of Engineering and Science, Vol No- 3, March 2014.
-
Yadav, D. (2009). Garbage disposal plant mired in controversy. India Times, TNN, 19 Feb 2009. 61 Bharat, K. and G.A. Mihaila, when experts agree: using non-a_liated experts to rank popular topics . ACM Trans. Inf.Syst., 20(1), (2002), pp.47-58.
-
S D Rahul Bharadwaj, Shraddha R Jogdhankar, Automatic Wastewater treatment process to reduce global warming International Journal of Environmental Science: Development and Monitoring, Vol No- 2 (2013)
-
Balachandra,et.al.Automatic Drainage Water Pump Monitoring and Control System Using turbine International Journal of Innovative Research in Technology, Vol No- 1, 2014.
-
Gnash U L,et.al. Semi-Automatic Drain For Sewage Water Treatment Of Floating Materials, International Journal of Research in Engineering and Technology, Vol No05, Jul-2016.
-
Dr .K.Kumaresanetal., Atomatic Sewage Cleaning Equipment, International Conference on Explorations and Innovations in Engineering and Technology , 2016.
-
R.Sathiyakalaet.al. Smart Sewage Cleaning System International Journal of Innovative Research in Computer and Communication Engineering, Vol No- 4, February 2016.
-
NitinSall, et.al., Drain Waste Water Cleaner, Global Journal of Researches in Engineering: J General Engineering Vol No- 16, 2016. Gregor Burger, et.al, Designing and Implementing a Multi-Core Capable Integrated Urban Drainage Modelling Toolkit: Lessons from CityDrain3, Advances in Engineering Software 100, 2016.
-
S S Rattan Department of Mechanical Engineering Regional Engineering College Kurukshetra (2004). Theory of machines Publication: Tata McGraw-Hill Publishing Company Limited.