
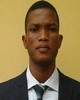
- Open Access
- Authors : Ogunsona Damilola Adesoga , Giwa Abdulgafar Babatunde , Familusi Timothy Oluwafemi
- Paper ID : IJERTV10IS100098
- Volume & Issue : Volume 10, Issue 10 (October 2021)
- Published (First Online): 25-10-2021
- ISSN (Online) : 2278-0181
- Publisher Name : IJERT
- License:
This work is licensed under a Creative Commons Attribution 4.0 International License
Design and Construction of 500 Watt PWM DC/AC 220V Power Inverter
Ogunsona Damilola Adesoga
Department of Physics,
Tai solarin University of Education Ijagun PMB 2118, Ijebu-Ode, Nigeria.
Giwa Abdulgafar Babatunde
Department of Physics,
Federal University of Technology Akure, PMB 704, Akure, Nigeria
Familusi Timothy Oluwafemi
Science, Laboratory and Technology Department, Osun State Polytechnic Iree, Nigeria
Abstract A 500 watt PWM DC/AC 220V Power Inverter which is designed to converts direct current DC to alternating current AC with the use of a transformer, switching and control circuit was designed and constructed using SG3524 which is an integrated switching regulator circuit that has all essential circuitry required for making a switching regulator in single- ended or push-pull mode. The built-in circuitries inside the SG3524 include pulse width modulator, oscillator, voltage reference, error amplifier, overload protection circuit, output drivers, etc. which processed the DC signal into AC signal and later sent the current signal into a driver transistor BC558. Acting as class B voltage amplifier, the resulting signal was further amplified using four MOSFET transistors mounted on a heat sink. The resulting alternating voltage to which a 12Vd.c is superimposed was fed into the middle of the primary coil of 500watt transformer windings producing alternating current AC in the secondary wind 220V AC.
KeywordsPWM; Power Inverter; DC/AC.
-
INTRODUCTION
Electrical power interruption is quite common in every place especially in our country Nigeria, after a heavy downpour of severe storms. To counter this power outage a researcher has carried out reliable and economical alternative sources of electricity supply. In Nigeria, a regular power supply is a dream that is yet to come true. Businesses are folding up and so much money is being lost, due to power failure.
Lately, there has been an expanding interest in elective fuel sources as worldwide oil saves wane and worries for the environment keep on developing. Today, we progressively rely upon gadgets that require power, however, in Nigeria, perhaps the most populated country in Africa; just 40% of individuals are associated with the energy network; those associated experience brownouts and complete power outages around 60% of the time. In the meantime, it is bright 43% of sunshine hours in Nigeria, which is normal of 1885 hours of daylight each year; this implies sun-powered as an elective
energy arrangement is a lot of doable in this piece of the world [1].
Inverters are utilized for some applications as in a circumstance where low voltage DC sources like batteries, sunlight-based boards, or energy components should be changed over so gadgets can run on AC power. One illustration of such a circumstance would change electrical force from a vehicle battery over to run a PC, TV, lighting, or PDA and more [2].
An inverter is an electronic gadget or hardware that changes direct current (DC) to substituting current (AC). The information voltage, yield voltage and recurrence, and in general force dealing with relies upon the plan of the particular gadget or hardware. The actual inverter doesn't produce any force; the force is created from a DC source like a battery. As a rule, when we talk about the inverter, it is by and large with a course of action of an inverter circuit and a battery. It can likewise be joined with different sources like the breeze or sun-oriented energy. Fundamentally, an inverter is utilized to supply continuous 220V AC to the heap associated with its yield attachment. It gives a steady AC supply at its yield attachment, in any event when the AC mains supply isn't free [3].
Previously, Pulse Width Modulation (PWM) strategies were utilized in voltage and current source Inverter alone however with the accessibility of self-drove gadgets, for example, power semiconductor, Metal Oxide Semiconductor Field Effect Transistor (MOSFET), Insulated Gate Bipolar Transistor (IGBT) and so on beat width balanced DC to AC converter is presently normal in numerous applications. The consistent state and dynamic execution of Inverters, AC to DC converters, and DC and AC drives are essentially reliant upon the beat width adjustment strategies. Pulse Width Modulation (PWM) of a sign or force source includes the balance of its obligation cycle, to either pass on data over a correspondence channel or control the measure of force shipped offload [4].
Vol. 10 Issue 10, October-2021
-
believed that in the advanced society, power has extraordinary command over most day-by-day exercises for example in homegrown and modern usage of electric force for tasks. Power can be produced from public stock to clients in various manners including the utilization of water, wind, or steam energy to drive the turbine just as much as of late the utilization of gas Generators, sunlight based energy, and thermal power are too wellspring of power. They planned and built a 1000Watts (1KW) 220 Volts Inverter at a recurrence of 50Hz. This gadget was built with privately sourced segments and materials of controlled norms. The essential rule of its activity is a straightforward transformation of 12V DC from a battery utilizing incorporated circuits and semiconductors at a recurrence of 50Hz, to a 220V AC across the windings of a transformer.
By and large, power inverters are utilized for some applications, for example, in AC drives, emergency clinic hardware, footholds, home and office gadgets [5][6]. There are various classes of inverters, for example, voltage source inverter, current source inverter, transformerless inverter, transformer-based inverter, buck inverter, support inverter, buck-help inverter, altered sine wave inverter, quasi-inverter, staggered inverter, square wave inverter, unadulterated sine wave inverter, and so forth [7][8][9][10][11][12].
-
-
METHODOLOGY
POWER AMPLIFIER
POWER AMPLIFIER
The methodology utilized for this research ascertains the equipment was designed to resist the desired rating of the equipment. The Pulse Width Modulated (PWM) inverter comprises of the following unit; switching circuit (oscillator), Driver circuit, Power amplification circuit, Output and Battery. The switching oscillating circuit supplies the PWM signal which is transmitted to the driver circuit following which the power amplification circuit amplifies the signal to the output. The active circuits of the equipment are powered by the battery.
OSCILLATOR
DRIVER
OSCILLATOR
DRIVER
BATTERY
AC OUTPUT
BATTERY
AC OUTPUT
Fig -1: Basic Block Diagram of a Pulse-Width-Modulated (PWM) Inverter
-
Oscillator stage
This consists of IC SG3524 which generates a signal at a frequency of 50HZ due to the resonance tank
created between a capacitor and resistor in pin 6 and 7, these two components cause the oscillator to oscillate at 50HZ, and output is spilled into two. These two outputs are 1800 out of phase they are in pin 11 and 14 i.e. the output of this IC is at 100mA maximum current. This current may not be sufficient to drive the power stage; hence need for drivers is required.
Fig- 2 Circuit of the oscillating section
-
Driver stage and Power Amplification stage
A driver is a component that can deliver more current than the signal source, the output from PWM SG3524 is amplified by the two transistors BC558; which is enough to open the gate of the four MOSFET transistors in the amplification stage. This is te main power section; this section comprises four MOSFET transistors mounted on an adequately sized heat sink to dissipate the generated heat. They serve to amplify the output signal generated. The output from the drains of the four transistors is fed to a step-up 500W transformer, at point A which is the middle of the primary coil a 12V DC supply is superimposed on the signal, thus generating a 220V AC signal at the second output of the transformer.
Fig-3 Driver stage and Power amplification stage
-
-
DESIGN AND MODE OF OPERATION
The complete circuit diagram of the PWM inverter circuit is shown in fig 4. This consists of IC SG3524 which generates a signal at the frequency of 50HZ due to the resonance tank created between a capacitor and resistor in pin 6 and 7 of the circuit resulting in square waves at pin 11 and 14 of the IC. These two are 1800 out of phase with each other; the two wave trains are fed to the driver stage which are the buffer transistors, which consist of two BC558 transistors, meant to amplify the voltage value of the signal from pin 11 and 14 of the oscillator IC, thus giving the signal enough energy to open the gate of the power transistors. The power transistors which are the four MOSFET transistors (with terminals such as gate, drain, and source) functions as energy amplifiers for the signal generated. In this power inverter circuit, DC power is connected to a transformer through the center tap of the
primary windings. A switch is rapidly switched back and forth to allow current to flow back to the DC source through two alternate paths from one end of the primary windings and then the other. The signal from the DC enters the input pins of the PWM (SG3524), where the oscillator processed it to alternating current (AC) and later sent the current signal out from its output pin i.e. pin 11 and 14 to the driver BC558 in which the signal is amplified with BC558 and sent it out to the power amplifier which is the four MOSFET transistor mounted on a heat sink. Thus the alternation of current in the primary winding of the transformer produces alternating current (AC) in the secondary windings.
Fig- 4 Circuit diagram of 500-watt PMW DC/AC 220V power inverter
-
IMPLEMENTING THE DESIGN
To actually implement the design of this 500 watt PWM DC/AC 220V power inverter, certain steps had to be taken to ensure that every unit of the project functions correctly. In order to do this the schematic diagram of the entire project was first designed using express schematic software and later designed the PCB layout using express PCB software. The following steps were considered for the designing process. Download express software which is a free version on the net (www.google.com). Design the circuit diagram with express schematic and the PCB layout of the schematic diagram with express PCB. The PCB layout circuit diagram was printed on an A4 glossary paper and the printed PCB diagram was placed on a neat copper board. Then ironing the PCB diagram on the copper board with pressing iron and ensure it is neatly placed together. The copper board to which the PCB was attached was dipped into a bucket of water to remove the glossary paper. Etching the copper board with lead chloride in order to make a pattern on the surface of the copper board after which the surface was clean with petrol. A hand drilling machine was used to make holes on the copper board to allow the components to fit into their respective holes for soldering.
Fig-5 PCB components layout of 500 watts PWM dc/ac 220v power inverter
-
Construction and Testing
The circuit was initially simulated using the downloaded software after which the components were temporarily placed on a Vero board to ascertain the project meeting the required conditions. The construction phase includes; final transfer of components, soldering the component, and coupling the active circuit following strictly the schematic diagram on the PCB. Below is the complete project of 500 watts PWM DC/AC 220V Power Inverter.
Fig-6 constructed 500watts PWM DC/AC 220V Power Inverter
-
Performance Evaluation
Firstly the device was switched on after it has been connected to a fully charged battery rating 12V as the input voltage, and then the output voltage of the power inverter was measured with a digital multi-meter, in which the meter reads the voltage to be approximately 220AC Volt as shown in fig. 7.
Fig-7 Testing the output of the constructed 500watts PWM DC/AC 220V Power Inverter
The inverter was further tested using electrical appliances of 500W power rating as indicated in fig 8, and it was observed that the equipment performs with the limit of its power rating, thus the device was capable enough without any deficiency to the power TV set, Radio set, and a house Lamp respectively.
Therefore this power inverter is a True Sine Wave Inverter that is able to meet the backup rules of electronic devices and is simple to control.
Fig-8 Performance evaluation of the output of the constructed 500watts PWM DC/AC 220V Power Inverter
VI. CONCLUSION AND RECOMMENDATION
The aim of this project was to produce a 500watts PWM DC/AC 220V power inverter, that would be easy to fabricate, and fairly efficient when tested. Taking a look at these goals and the end result it can be said that the result is inconsonant with the aim and objectives, the circuitry and total cost of all the components used in the construction of the circuit was around #20000 and it compared favorably in performance with imported inverter for the purpose of efficiency and keeping power losses to a minimum. This project is a stepping stone to a cheaper and efficient pure sine wave inverter, by using the data collected in this research work as well as the schematics and recommendations the product produced here can be improved upon, while the energy capacities can be increased.
This project is an eye-opener that alternative energy source can be developed locally using the solar panel as a constant DC energy source during the day time which can be used to charge a pull of batteries which can serve as a source of
energy for an inverter circuit which in turn can be useful when there is a power outage from public electricity. This electricity source can also be a useful energy source for rural communities that are far from the national grid.
V. ACKNOWLEDGMENT
The author is grateful to the electronics and instrumentation group, Department of Physics, Federal University of Technology, Akure.
REFERENCES
-
A Musa, G.S.M. Galadanci, 5KVA power inverter design and simulation-based on boost converter and H-bridge inverter topology,
Bajopas, vol. 2, June 2009
-
Roberto Faranda, Sonia Leva, Piazza Leonardo da Vinci, renewable energy resources for households, WSEAS transactions on power systems, issue 6, Vol. 3, June 2008.
-
O. O. Omitola, S. O. Olatinwo and T. R. Oyedare, Design and Construction of 1KW (1000VA) PowerInverter, Innovative Systems Design and Engineering vol.6 no. 2 pp.1 13, 2014
-
C. Anene., Design and Implementation of a 5 kVA Inverter, Journal of Electrical and Electronics Engineering 2016
-
A.Haider, R. Alam, N. Binte Yousuf and K. M. Salim, Design and Construction of Single Phase Pure Sine Wave Inverter for Photovoltaic Application, International Conf. IEEE, 2013
-
B.K. Bose, Modern Power Electronics, Evolution, Technology and Applications, NY, IEEE Press, 1992
-
C.U Eya and Agu, Solar-powered single-phase boost differential Inverter, Nigeria Journal of Technology Vol..34, 2014, pp.164-176
-
Daniel. W Hart, Power Electronics, McGraw-Hill, the McGraw-Hill Companies, Inc., 1221 Avenue of the Americas, New York, NY 10020. 2011
-
I. Mohan, T.M. Undeland and W.P. Robbins, Power Electronics
-
Muhammed. H. Rashid, Power Electronics Circuits, Devices and Application, 3rd Edition Prentice Hll India, 2004,
-
Sanjay Dixit, Ambreesh Tripathi, Vikas Chola, and Ankur Verma, 800VA Pure Sine Wave Inverters Reference Design, Texas Instrument SLAA602AJune 2013Revised August 2017
-
Olusegun O. Omitola1*, Segun O. Olatinwo1 and Taiwo R. Oyedare Design and Construction of 1KW Power Inverter, Innovative Systems Design and Engineering, Vol.5, No.2, 2014, pp.1-13