
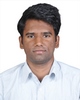
- Open Access
- Authors : Medichalam Srivinayak , , Dr. Md. Fakhruddin H. N
- Paper ID : IJERTV10IS100124
- Volume & Issue : Volume 10, Issue 10 (October 2021)
- Published (First Online): 25-10-2021
- ISSN (Online) : 2278-0181
- Publisher Name : IJERT
- License:
This work is licensed under a Creative Commons Attribution 4.0 International License
Design and Analysis of Fan Blade with Dual Natural Fibers and Al 7075
Medichalam Srivinayak
Student of Dept. of Mechanical Engineering, Methodist College of Engineering and Technology, Hyderabad, India.
Dr. Md. Fakhruddin H.N
Professor of Dept. of Mechanical Engineering, Methodist College of Engineering and Technology, Hyderabad, India.
Abstract Fan blades are one among the foremost common engineering parts which are employed by everyone in day to day life. The increasing energy and decreasing efficiency in the present and future generations of Industries have become the major issues. This can be achieved by minimizing the weight and increasing the efficiency of the fan blades. In this work, the design and analysis of fan blade which is made up of natural fibers (hemp fiber and basalt rock fiber) is carried out, and also a complete comparison of aluminium alloy 7075 and the blades made of natural fibers is achieved. The design of the fan blade is modeled in Solidworks 2016 and converted it into IGS format. The analysis of different materials is carried out using Ansys 2021 in which static analysis, fatigue analysis and model analysis were done. Through Static, Fatigue and Modal analysis of the materials, The Basalt rock fiber has shown better results than Aluminium alloy 7075 and Hemp fiber.
Keywords Efficiency, Fan blade, Fiber, Material .
-
INTRODUCTION
The ceiling fan has become a crucial appliance for domestic also as industrial purposes. As we knew that power consumed by the fans is less but as fans run continuously with minor breaks they consume a lot of power which leads to a high power consumption. Having low consumption of power with low weight and effective utilization of natural recourses is the main target of the electrical appliances companies these days. The mentioned goal can be achieved by implementing a better design, material, and manufacturing process. In spite of many benefits of Aluminium Alloy 7075, there are some limits mainly good strength to weight ratio, lower resistance to corrosion, higher cost etc. To replace Aluminium alloy 7075 we can use composite materials which can also contain natural fibers, where the directions of fibers affect the properties of the composite material. Natural Fibers have similar properties as Aluminium alloy 7075 and is also good in strength to weight ratio. The work on this project is to focuses on dual natural fibers that are hemp fiber and basalt rock fiber.
-
LITERATURE SURVEY
Sanjay M R et.al. [1]. This study proposes a definite review of the various sorts of retting measures, chemical and surface treatments and portrayal strategies for regular fibers. The following review talks about the reason for natural fiber and its potential, Advantages and burdens of utilizing a natural fiber, Extraction techniques: dew retting and water retting process, chemical treatment: by utilizing a synthetic treatment
on the natural fibers permits lessening its strands hydrophilic components, Surface treatment:The natural fibers require some surface chemicals to work on its surface performance. Characterisation method:This area is devoted to presents the most valuable portrayal techniques for the natural fibers. The characterisation strategies are exceptionally fundamental to choose the natural fibers appropriate as support for polymer composites.
Priyanka Dhurvey et.al. [2]. Complete examination of ceiling fan is accomplished for four distinct cutting edge materials. Underlying examination and optimal design investigation is finished utilizing ANSYS programming. COP examination is finished utilizing MATLAB Program and weight and power utilization examination is additionally presented.From the outcomes gotten from the current work, it can reason that the ceiling fan having sharp edges of PVC material outcomes in higher COP than the cutting edge of other material inside the scope of speed. Fan having sharp edges of PVC material is able to do reduce the force utilization than different sharp edges prompting higher effectiveness of fan and is energy saving.
Swaroop M P et.al. [3]. From the investigation that they have led, it very well may be seen that there is absolutely an impact on wind stream as the sharp edge point changes. What struck them the most is that the speed of air which gets through the power source continues to increment up to a specific sharp edge point and afterward the speed diminishes after the ideal cutting edge point is reached. From 4 unique examinations that they have directed, they have discovered the best cutting edge point to be at 8 degrees.
S Prabhakaran et.al. [4]. In this task the composite cutting edge has been planned and manufactured. This composite cutting edge has more strength over existing fan edge. The current fan cutting edge weighs about 295grams while the heaviness of composite fan edge is 215grams, which is 28% lesser than existing edge. It is tried that the force devoured by the current sharp edge (0.052units) is more when contrasted with composite blade(0.037units). So when we utilize composite fan implies we can decrease 30% of force devoured by the current roof fan. Cost of composite roof fan cutting edge is Rs. 279/ – which is 44% not exactly existing aluminum cutting edge. The strength of the composite cutting edge additionally high when we contrasted and aluminum sharp edge. From the review, it is presumed that fiber built up plastic material is an appropriate material for assembling the composite roof fan cutting edge.
Junjie Zhou et.al. [5]. The outcomes show that R40 pivotal stream fan runs stable under resounding working conditions, reverberation doesn't happen; the bigger turn speed can expand the regular frequencies of cutting edge; the edge has the greatest reaction of the thrilling power at 120Hz.
A. Shaniavski [6]. Air consumption has harms just from bombed fan cutting edges parts. There were no hints of any unfamiliar articles which might enter the air admission in flight and cause its failing and upset a motor activity. A deficiency of air admission in flight was brought about by disappointment of the multitude of screws which attach air admission to motor due to extremely high energy of flying pieces of broken fan edges.
Ebrahim Mustafa et.al. [7]. Four distinctive harmony length and five curving point of their sharp edges were examined. The fan was planned by utilizing NACA 5505 series. The primary examination is directed to the sharp edge plan in the variety of harmony length
Santosh Kumar Dahare1 et.al. [8]. In this plan of fan edge, material changed over from existing aluminum into Nylon66. Fan sharp edge plan strategy for an ideal outcome as indicated by FEM hypothesis is performed.
IV. METHODOLOGY
-
Summary
From the above literature review we can say that:
-
Less measure of work is accomplished For Vibration Analysis of fan edge.
-
Less consideration is given to the Resonance and normal Frequencies of Fan Blade
-
Most of the review in the field of fan edge is led for primary disappointment of the fan edge configuration utilizing FEA.
-
A. Materials
Fig. 1 Methodology
-
-
PROBLEM DEFINITION AND OBJECTIVES
-
Problem Definition
The Fan blade have been the most common engineering part which are used by everyone in everyday life. The increasing population and technology have made the use of fan blade a priority and the fan blades used today. The high energy consumption and decreasing efficiency in the present and future generations of Industries have become the major issues This can be addressed by minimizing the weight and increasing the efficiency of the fan blades. So, The main aim of this project would be get a best material which will save energy and have higher efficiency.
-
Objective of the Work
-
Replacement of Aluminium Alloy 7075 with Natural fibers
-
Calculating the properties of Aluminium Alloy 7075 and Natural fibers
-
Testing whether Natural Fibers are better Aluminium Alloy 7075.
-
-
Aluminium Alloy 7075: The 7000 sequence aluminium alloys are functional in a many applications. The low weight and robustness character of grade 7075 are cherished very much by manufacturers and end users. As a physically powerful machinable aluminium alloy, it is highly used in the aerospace industries, aircraft and automotive.
-
Hemp Fiber: Benefits of hemp is that, it can be full- grown without chemicals, it gives extensive fibers and it is fastest growing plant on the earth. The scientific name of the hemp is cannabis sativa.
-
Uses of hemp: The 7000 sequence aluminium alloys are functional in a many applications. The low weight and robustness character of grade 7075 are cherished very much by manufacturers and end users. As a physically powerful machinable aluminium alloy, it is highly used in the aerospace industries, aircraft and automotive.
Fig. 2 Hemp Fiber
-
Basalt Fiber: Basalt is an igneous rock formed by rapid cooling of lava from volcano. Crushed basalt rocks is used a raw material for manufacturing basalt fibers. Basalt fiber has a wider temperature range from -4520F to 12000F. when compared to carbon and armored fiber it has a higher oxidation resistance, higher compression strength, higher shear strength and higher radiation resistance. It has excellent shock resistance and can be used for ballistic purposes. Good fatigue and corrosion resistance. Easy to handle, environmentally friendly and can be recyclable. The chemical components include SiO2, Al2O3, CaO, MgO, Na2O + K2O, TiO2, Fe2O3 + FeO etc. The products on basalt fiber include basalt cloth, roving and yarn, chopped strands, needled felts and georgics.
The sequence of operations of basalt fiber includes:
-
Melting of basalt breads into basalt melt
-
Homogenization of basalt melt and its preparation for production
-
Forming of basalt melt through a platinum alloy bushing assembly
-
Extraction of initial fiber, lubrication and winding on bobbins.
-
Properties of Materials
TABLE I. PROPERTIES OF DIFFERENT NATURAL FIBERS
-
Modeled Using Solid Works
Fig. 3 2D Diagram of Fan Parts Ceiling Fan Blade
Fig. 4 3D Diagram of Fan Parts Ceiling Fan Blade
Geometric Attribute
Dimension
Fan Blade Length
483.17 mm
Fan Blade Thickness
0.8 mm
Fan Blade Bend Angle
10
Fan Blade Punch Hole Radius
6 mm
Fan Blade Tip Width
106.17 mm
Fan Blade Root Width
127 mm
Geometric Attribute
Dimension
Fan Blade Length
483.17 mm
Fan Blade Thickness
0.8 mm
Fan Blade Bend Angle
10
Fan Blade Punch Hole Radius
6 mm
Fan Blade Tip Width
106.17 mm
Fan Blade Root Width
127 mm
TABLE II. DIMENSIONS CEILING FAN BLADE
Properties
Hemp fiber
Basalt rock fiber
Aluminium alloy 7075
Tensile Strength (Mpa)
250
300
450
Youngs Modulus (Gpa)
70
110
71.7
Density (g/cc)
1.447
2.7
2.8
Fig. 5 2D Diagram of Fan Parts – Ceiling Fan Blade Shank
Fig. 6 3D Diagram of Fan Parts Shank
TABLE III. DIMENSIONS CEILING FAN BLADE SHANK
Geometric Attribute
Dimension
Shank Length
132.50 mm
Shank Width
44 mm
Punch Hole Radius
6 mm
Shank Thickness
1.5 mm
Fig. 7 2D Diagram of Fan Parts Rivet
Fig. 8 3D Diagram of Fan Parts Rivet
TABLE IV. DIMENSIONS RIVET
Geometric Attribute
Dimension
Rivet Diameter
6 mm
Rivet Grip Range
2.30 mm
Fig. 9 Assembly of all parts
2) Material: Hemp Fiber
a. Total deformation
Fig. 10 Assembly of all parts
-
-
Static Analysis Of Fan Blade
1) Material: Aluminium Alloy
-
Total deformation
-
Stress
Fig. 14 Total deformation of Hemp Fiber
Fig. 15 Stress of Hemp Fiber
-
Strain
Fig. 11 Total deformation of Aluminium Alloy
-
Stress
Fig. 12 Stress of Aluminium Alloy
-
Strain
Fig. 13 Strain of Aluminium Alloy
Fig. 16 Strain of Hemp Fiber
3) Material: Basalt Rock Fiber
-
Total deformation
Fig. 17 Total deformation of Basalt Rock Fiber
-
Stress
Fig. 18 Stress of Basalt Rock Fiber
-
Strain
Fig. 19 Strain of Basalt Rock Fiber
c. Safety Factor
Fig. 22 Safety Factor of Aluminium Alloy
2) Material Hemp Fiber
a. Life
-
-
Fatigue Analysis Of Fan Blade
1) Material: Aluminium Alloy
-
Life
-
Damage
Fig. 23 Life of Hemp Fiber
Fig. 20 Life of Aluminium Alloy
-
Damage
Fig. 21 Damage of Aluminium Alloy
Fig. 24 Damage of Hemp Fiber
-
Safety Factor
-
Fig. 25 Safety Factor of Hemp Fiber
3) Material: Aluminium Alloy
-
Life
Fig. 26 Life of Basalt Rock Fiber
-
Damage
Fig. 27 Damage of Basalt Rock Fiber
-
Safety Factor
Fig. 28 Safety Factor of Basalt Rock Fiber
-
-
Modal Analysis of Fan Blade:
-
Material: Aluminium Alloy
-
Total deformation 1
Fig. 29 Total deformation 1 of Aluminium Alloy
-
Total deformation 2
Fig. 30 Total deformation 2 of Aluminium Alloy
-
Total deformation 3
Fig. 31 Total deformation 3 of Aluminium Alloy
-
-
Material Hemp Fiber
-
Total deformation 1
Fig. 32 Total deformation 1 of Hemp Fiber
-
Total deformation 2
Fig. 33 Total deformation 2 of Hemp Fiber
-
Total deformation 3
Fig. 34 Total deformation 3 of Hemp Fiber
-
-
Material Basalt Rock Fiber
-
Total deformation 1
Fig. 35 Total deformation 1 of Basalt Rock Fiber
-
Total deformation 2
Fig. 36 Total deformation 2 of Basalt Rock Fiber
-
Total deformation 3
Fig. 37 Total deformation 3 of Basalt Rock Fiber
-
RESULTS
Static, Fatigue and Modal analysis were performed and the results are given in Table 5, Table 6 and Table 7.
TABLE V. STATIC ANALYSIS RESULTS
Materials
Total Deformation (mm)
Stress (N/mm2)
Strain
Aluminium alloy7075
8.8857
35.218
0.0005723
6
Hemp fiber
12.839
50.885
0.0008269
8
Basalt rock fiber
6.7572
26.782
0.0004352
5
TABLE VI. FATIGUE ANALYSIS RESULTS
Materials
Damage
Safety factor
Aluminium alloy 7075
2.5585e+05
0.24295
Hemp fiber
8.5834e+05
0.15879
Basalt rock fiber
1.2472e+04
0.58814
TABLE VII. MODAL ANALYSIS RESULTS
Materials
Mode1
Freque ncy
Mode2
Freque ncy
Mode3
Frequen cy
Aluminiu m alloy 7075
119.12
15.771
173.01
47.576
180.12
83.853
Hemp fiber
112.41
10.367
175.8
57.371
164.9
83.765
Basalt rock fiber
123.72
16.989
170.48
40.96
183.71
80.772
1.00E+06
9.00E+05
8.00E+05
7.00E+05
6.00E+05
5.00E+05
4.00E+05
3.00E+05
2.00E+05
1.00E+05
0.00E+00
1.00E+06
9.00E+05
8.00E+05
7.00E+05
6.00E+05
5.00E+05
4.00E+05
3.00E+05
2.00E+05
1.00E+05
0.00E+00
Al 7075
hemp fiber basalt rock fiber
materials
Al 7075
hemp fiber basalt rock fiber
materials
Damage
Damage
Fig. 38 Materials Vs Damage
14
12
10
8
6
4
2
0
Al 7075
hemp fiber
materials
basalt rock fiber
0.7
0.6
0.5
0.4
0.3
0.2
0.1
0
Al 7075
hemp fiber basalt rock fiber
materials
14
12
10
8
6
4
2
0
Al 7075
hemp fiber
materials
basalt rock fiber
0.7
0.6
0.5
0.4
0.3
0.2
0.1
0
Al 7075
hemp fiber basalt rock fiber
materials
Stress(N/mm2)
Stress(N/mm2)
total deformation(mm)
total deformation(mm)
Damage
Damage
Fig. 39 Materials Vs Deformation
60
50
40
30
20
10
0
60
50
40
30
20
10
0
Al 7075
hemp fiber
materials
basalt rock fiber
Al 7075
hemp fiber
materials
basalt rock fiber
strain
strain
Fig. 40 Materials Vs Stress
0.0009
0.0008
0.0007
0.0006
0.0005
0.0004
0.0003
0.0002
0.0001
0
0.0009
0.0008
0.0007
0.0006
0.0005
0.0004
0.0003
0.0002
0.0001
0
Al 7075
hemp fiber
materials
basalt rock fiber
Al 7075
hemp fiber
materials
basalt rock fiber
Fig. 41 Materials Vs Strain
Fig. 42 Materials Vs Safety factor
18
16
14
12
10
8
6
4
2
0
18
16
14
12
10
8
6
4
2
0
Al 7075
hemp fiber basalt rock fiber
materials
Al 7075
hemp fiber basalt rock fiber
materials
Frequencey (Hz)
Frequencey (Hz)
Fig. 43 Materials Vs Frequency
-
CONCLUSION
Through Static, Fatigue and Modal analysis of the materials, when comparing the stresses at Basalt fiber to aluminum alloy and hemp, the static analysis findings show that the stresses at Basalt fiber are lower. When comparing aluminum alloy and hemp fiber to the findings of the Fatigue analysis, the safety factor for Basalt fiber is the highest.
From the above experiment we have obtained the following results:
Total Deformation (mm):
Basalt fiber(6.7572 mm) > Aluminium Alloy 7075(8.8857 mm) > Hemp Fiber(12.839 mm)
Stress (N/mm2):
Basalt fiber(26.782 N/mm2) > Aluminium Alloy 7075(35.218 N/mm2) > Hemp Fiber(50.885 N/mm2)
Strain:
Basalt fiber(0.00043525) > Aluminium Alloy 7075(0.00057236) > Hemp Fiber(0.00082698)
Damage:
Basalt fiber(1.2472e+04) > Aluminium Alloy 7075(2.5585e+05) > Hemp Fiber(8.5834e+05)
Safety Factor:
Basalt fiber(0.58814) > Aluminium Alloy 7075(0.24295)
> Hemp Fiber(0.15879)
In modal analysis by comparison of Model-1, Model-2 and Model-3:
Basalt fiber> Aluminium Alloy 7075> Hemp Fiber
From the results we can conclude that the Basalt rock fiber has shown better results than Aluminium alloy 7075 and Hemp fiber. Basalt rock fiber gives better efficiency and can be obtained at low cost. Due to its light weight property the consumption of energy will also be decrease.
-
FUTURE SCOPE
-
The further extension of this project would be to make a composition of the natural fibers by using the data of this project, which can suit our environment and replace the materials used now.
REFERENCES
-
Sanjay M R, Siengchin S, Parameswaranpillai J, Jawaid M, Pruncu CI, Khan A. A comprehensive review of techniques for natural fibers as reinforcement in composites: Preparation, processing and characterization. Carbohydr Polym. 2019 Mar 1;207:108-121. doi: 10.1016/j.carbpol.2018.11.083. Epub 2018 Nov 26. PMID: 30599990.
-
Adeeb, Ehsan & Maqsood, Adnan & Mushtaq, Ammar & Sohn, Chang Hyun. (2016). Parametric Study and Optimization of Ceiling Fan Blades for Improved Aerodynamic Performance. Journal of Applied Fluid Mechanics. 9. 2905-2916. 10.29252/jafm.09.06.25808.
-
Swaroop M P Optimisation of Fan Blade Angle, Int. Journal of Engineering Research and Application ISSN: 2248-9622, January 2017.
-
S.Prabhakaran, M.Senthil kumar Development of Glass Fiber Reinforced Polymer Composite Ceiling Fan Blade IJERD eISSN: 2278-067X, pISSN: 2278-800X, (July 2012).
-
Junjie Zhou, Bo Liu, Dingbiao Wang, Xiaoqian li Dynamic Characteristics Analysis of Blade of Fan Based on Ansys Power and Energy Engineering Conference 2010.
-
A. A. Shaniavski Fatigue Failure Analysis of Fan Blade of D-L8 Engine of Ruslan Aircraft
-
Ebrahim Mustafa, Danardono, Triyono, Agus Dwi Anggono and Abdussalam Ali Ahmed Finite Element Analysis and Optimization Design of Aluminium Axial Fan Blade ARPN- ISSN 1819-6608 September 2015.
-
Santosh Kumar Dahare, Dr. Rohit Rajvaidya Design and Analysis of Nylon66 Ceiling Fan Blade Using Finite Element Method International Research Journal of Engineering & Applied Sciences ISSN: 2322-0821 2013.
AUTHORS PROFILE
Medichalam Srivinayak, He has completed Bachelor of Technology degree in Mechanical engineering in Sri Indu College of Engineering and Technology, Hyderabad, Telangana India. He is currently persuing Master of Engineering(M.E) in CAD/CAM in Methodist College of Engineering and Technology, Hyderabad, India.
Dr. Md. Fakhruddin H.N, Associate Professor in Department of Mechanical Engineering, Methodist College of Engineering Abids, Hyderabad 500001, India, having total experience of 25 years in which 5 years in industry, with 23 research papers published in reputed journals and a reviewer for
International Journal/Conference and a subject expert has delivered Invited Talk / guest lecture in many conferences and workshops and also inolved in state Govt. confidential work / APEAMCET & TSEAMCET.